中國兵器工業集團公司成立以來,熱處理工藝技術歷經了從落后到先進,從以手工操作為主到機械化、半自動化和部分實現自動化的發展過程,工藝參數和產品質量也由不完全可控發展到完全可控,數字化模擬技術的引進也已納入規劃,且指日可待。伴隨著行業的發展現狀,本公司的熱處理工藝技術也發生了翻天覆地的變化,但仍然存在著不足。“十二五”乃至今后更長的期間,本公司熱處理工藝技術應不斷補充和發展,向國內外先進水平邁進。
1 表面強化技術
1.1表面熔敷技術
表面熔敷技術是利用激光、電磁感應或等離子弧,將自熔合金粉末在工件表面加熱到半熔融狀態,與工件表面層形成半冶金接合層,從而形成具有抗磨、抗氧化、耐熱、耐低應力和耐沖擊性好的表面熔敷層。常用的熔敷層有鎳基、鈷基、銅基及含WC型粉末等,硬度為35~67HRC。在數控機床上熔敷時,可獲得厚度均勻的熔敷層,對于非配合尺寸的表面一般無需磨削加工。
1.2激光表面非晶態處理
用激光將金屬表面加熱到熔融狀態后,急速(1×106℃/s)冷卻到某一溫度以下,使金屬成為非晶態結構。非晶態是沒有晶粒邊界的,結晶時不會出現成分偏析,獲得的硬度較高,可達到1000HV以上;同時,耐蝕性和耐磨性也較高。該技術被較多應用在汽車凸輪軸和柴油機鑄鋼套等的激光表面非晶態處理中。
1.3激光沖擊強化技術
激光沖擊強化技術也稱激光噴丸技術,是由高功率密度(GW/cm2量級)、短脈沖(10~30ns)的激光,通過沖擊工件表面的黑漆和鋁箔鍍層時,形成高壓等離子體,并產生高壓沖擊波,進而在金屬表面產生塑變,最終形成殘余壓應力,使金屬表面的抗疲勞性能大幅提高。7075-T6鋁合金構件表面經激光沖擊后的抗腐蝕疲勞壽命可提高2個數量級,Ti6A14V壓氣機葉片激光沖擊后的強度由206MPa提高到412MPa。
1.4表面機械強化技術
通過在材料或工件表面使用機械滾壓和噴丸等手段,使其產生一層殘余壓應力,常用于軸的表面噴丸和滾壓強化、彈簧和齒輪的噴丸強化、螺紋和花鍵齒的滾壓強化、扭力軸的扭轉+表面噴丸強化以及奧氏體鋼的加工硬化強化。
1.5表面熱處理強化數字化技術
隨著熱處理工藝軟件和計算機技術工程化應用的深入,表面熱處理強化數字化技術的應用越來越廣泛,主要包括電磁感應淬火回火,激光表面淬火回火,電子束表面淬火回火,激光沖擊表面強化,滲碳、滲氮和碳氮共滲等表面熱處理。該技術不但使熱處理工藝參數能通過模擬仿真實現優化,而且也使工藝過程及質量特性實現數字化控制。
2 新工藝技術
2.1低真空變壓滲氮技術的應用
通常滲氮都是在爐氣和爐壓不變的情況下進行的,對于一些細小的盲孔很難滲上氮。采用真空抽氣-負壓-保壓-充氣-保壓-抽氣的變壓換氣方法,提高了工件表面氮的活性和對氮的吸附能力,使滲層滲速能力加快,再加上稀土催滲劑催滲,滲氮時間將更短。
2.2離子氮化+氧化復合處理新工藝(對軟氮化工藝的改進)
該工藝先用離子氮化處理,獲得硬化層后,在離子爐內進行1次離子氧化處理,既解決了QPQ處理鹽浴氰化物污染環境的問題,又提高了零件的耐磨和耐蝕性。可以嘗試用氣體氮化+普通化學氧化的工藝方法,提高氮化層的耐磨和耐蝕性。研究表明,絕大多數零件氮化后進行油冷,既不影響變形,又能有效提高氮化層的耐磨和耐蝕性。
2.3液相等離子電解滲碳和滲氮技術
和普通電解技術原理類似,將被滲金屬作為陰極,石墨或不銹鋼作為陽極,在NaCl電解液中加入含C和N的有機物,如甲醇胺和尿素等,施加的直流電流要足夠高,使電解液中正離子在陰極富集,獲得具有納米尺寸的富碳層的晶粒,尺寸為50~70nm,使20#滲碳硬度達到1200HV,H13鋼滲氮硬度達到870HV,所需時間僅為25min左右。
2.4等離子體增強電化學表面陶瓷化技術
將Al、Ti、Mg和Zr的有色合金零件接電解液的陽極,并施加較高的電壓,就會在零件表面產生微區等離子弧光放電,足以使零件表面形成的氧化膜和界面層的電解質等物質被熔融和燒結,形成1層性能優異且硬度很高的Al2O3陶瓷氧化膜層。纖維硬度達1000~3000HV,相當于硬質合金,其耐磨性、耐蝕性和耐高溫性能均比較優良。
2.5回歸處理工藝的應用(RRA工藝)
固溶處理的Al-Zn-Mg-Cu系7055-T77鋁合金,在時效過程中隨著時效溫度的升高,GP區和合金相回熔,當達到回歸溫度的短時內,強度降低,抗蝕性強,可進行快速校正和形變加工;當達到T6的峰值時效時,晶內的GP區密度更高,強度更高。本公司的Al-Mg-Cu系鑄鋁件的校正也可以采用回歸處理的方法進行校正,回歸處理已成為進一步提高鋁合金熱處理強化的推薦技術。
3齒輪熱處理變形控制技術
1)齒輪在切削加工過程中存在著內應力,去應力退火雖然能釋放應力,使金屬組織內歪扭的晶格得到回復;但值得注意的是,回復過程也會引起變形。如滲碳淬火前易變形的齒輪,多次去應力精加工后再淬火,比1次去應力后直接淬火引起的變形小。
2)對于齒輪在淬火過程中的變形,采取的控制措施是保證加熱均勻和冷卻均勻。加熱爐配備有攪拌風扇,加熱過程要慢,結構薄厚不均時,應采取厚處先冷或薄處加厚套的措施。冷卻過程能采用氣淬的方法,就不采用油淬;能采用硝鹽淬的方法,就不采用油淬;能采用水基淬火劑淬火的方法,就不采用油冷。
4提高模具壽命的技術
目前,國內外模具熱處理技術發展較快的領域是真空熱處理、表面強化和材料預硬化技術。真空熱處理主要用來解決模具的淬火變形;表面強化是對成型模具進行滲氮、滲硼+淬火、電子束表面淬火、激光表面淬火和表面離子注入(即將模具和要注入的物質C、N、Ti和B等置入真空室,在高壓電場的作用下,上述物質被激化成高速離子注入模具表面,形成高度彌散的TiC和TiN等耐磨層)等強化手段;材料預硬化技術是指模具淬火后,再經預先機械滾壓和噴丸強化等。
5大型鍛件熱處理清潔節能技術
5.1加熱爐和裝爐方式的改進
中國一重大型鍛件廠生產的鍛件重達十幾噸至上百噸,熱處理井式爐深>20m,爐溫溫差均能保證±5℃,大型轉子的性能差達到10MPa。為克服廠房高度限制和爐溫不均勻,爐子采用開合式井式爐,如圖1所示。裝爐方式改進如下:
1)爐子側面開門用折疊式,工件從側面吊入;
2)工件由吊掛方式改為支承座支承,法蘭盤在爐頂上方;
3)吊具不加熱,出爐時使用專用冷吊具,吊出爐后淬火,此方法既省去了大型吊具加熱,又減小了工件掛頭和夾頭質量,有效解決了大鍛件熱處理加熱的問題,并且節能效果非常顯著。開合式淬火設備如圖2所示。
5.2大鍛件冷卻方式的改變
通常大鍛件的冷卻介質包括水和油,為解決高合金鋼油淬污染和水淬易裂的問題,采用噴霧或噴水淬火,水或霧的噴射速度適時可控,這是大鍛件淬火冷速可控的一大特點。
5.3擴氫退火
大鍛件退火耗時較長的是擴氫退火,以往非真空方法鋼液中的氫含量>2×10-6,臨界點以下的擴氫時間一般需要幾百至幾千小時。真空除氣后鋼液中的氫含量均控制在1×10-6左右,大部分碳鋼大鍛件無需擴氫處理,只需普通退火即可解決。
6非晶態材料
高強韌性耐蝕、耐磨、軟磁性非晶態合金(俗稱金屬玻璃)與玻璃的原子結構形態一樣,大體上是無序的,為了提高其強度和硬度,以獲得高的韌度及軟磁性,添加了P、C、B、Zr和Ti等可改善性能的元素,使其相對于金屬具有更高的強度、硬度和斷裂韌度。當鋼液以1×105℃/s急速冷卻到凝固點(近于玻璃熔點)時,仍呈現液態。隨著溫度降低,鋼液逐漸凝固,呈現出非晶態結構。可見,只有達到如此高的冷卻速度,并且在<-100℃的液氮中,才能得到塊狀非晶結構。
利用非晶態金屬制作原理現已研制出了超高強度納米非晶態鋁合金材料,并在航天航空領域得到了應用,其抗拉強度可達1000~1500MPa,遠超出了超硬鋁合金材料的強度,與鈦合金材料的強度相當,而且回歸時間變得更長,從而使構件的成型修復成為可能。
7碳纖維和增強碳基復合材料
碳-碳復合材料是以碳纖維為增強體,碳為基體的復合材料,國內外對其做了大量的應用研究。火炮身管采用以纏繞成型陶瓷為內襯的碳-碳復合材料制成,其質量減輕了30%~50%。在裝甲防護上做成輕質復合裝甲,破甲厚度可達到700mm,極大地減輕了炮塔的質量。
8結論
采用等離子無氧化熱處理的普及程度是衡量一個企業或地區熱處理先進程度的主要標準。采用真空、感應、激光、多用爐熱處理以及氣淬火、壓力淬火是減少工件熱處理畸變和綠色環保的有效方法。采用數字化熱處理技術是發展趨勢,能實現對熱處理參數和質量的精確控制。利用鑄鍛件余熱等溫退火、淬火以及余熱的回收利用,進一步減小變形和校正后回火是熱處理節能的一個有效途徑。高強度或超高強度功能材料的推廣應用是實現構件輕量化的重要手段。表面淬火、表面涂層、表面合金化以及表面離子注入、涂鍍技術的普及為工件耐磨和耐蝕提供了技術保障。
免責聲明:本網站所轉載的文字、圖片與視頻資料版權歸原創作者所有,如果涉及侵權,請第一時間聯系本網刪除。
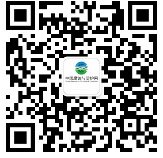
官方微信
《腐蝕與防護網電子期刊》征訂啟事
- 投稿聯系:編輯部
- 電話:010-62316606
- 郵箱:fsfhzy666@163.com
- 腐蝕與防護網官方QQ群:140808414