微合金化對(duì)高錳奧氏體鋼在酸性鹽霧環(huán)境下的耐蝕性能影響研究
液化天然氣(LNG)作為一種清潔、高效、優(yōu)質(zhì)的能源,其燃燒產(chǎn)生的CO2排放量最高可減少20%[1]。我國(guó)明確提出2030年前碳達(dá)峰、努力爭(zhēng)取2060年前碳中和。《中華人民共和國(guó)國(guó)民經(jīng)濟(jì)和社會(huì)發(fā)展第十四個(gè)五年規(guī)劃和2035年遠(yuǎn)景目標(biāo)綱要》中指出,要大力發(fā)展清潔可再生能源,推進(jìn)LNG接收站規(guī)劃建設(shè),盡可能用非碳能源替代化石能源,加快能源綠色低碳轉(zhuǎn)型,持續(xù)提高清潔能源利用水平[2]。
天然氣在-160℃下液化后,體積縮小為原來(lái)氣態(tài)時(shí)的1/625左右,密度也較低,僅為同體積水的45%左右,非常便于運(yùn)輸[3]。天然氣中含有85%~95%的甲烷,且在LNG中甲烷純度更高。相較于包括石油在內(nèi)的其他化石燃料,LNG在減少排放方面效果更顯著,據(jù)有關(guān)數(shù)據(jù)表明[4, 5],全球LNG平均排放強(qiáng)度為0.35% CO2/噸。目前常用的LNG儲(chǔ)罐材料為9%Ni鋼,其合金成本昂貴,在加工及運(yùn)輸過(guò)程中易被磁化,焊接困難[6]。為節(jié)省成本,浦項(xiàng)鋼鐵公司與韓國(guó)科學(xué)技術(shù)院聯(lián)合研發(fā)出新型LNG儲(chǔ)罐超低溫奧氏體高錳鋼,該鋼在-196℃下的韌性、抗疲勞性及耐腐蝕性相當(dāng)于廣泛使用的9%Ni鋼,但其塑性約為9%Ni鋼的3倍[7]。此外,Mn的價(jià)格為Ni的1/10左右,高錳鋼的成本價(jià)格比因合金、9Ni鋼、不銹鋼低70%~80%,極大降低了制造LNG儲(chǔ)罐成本[8],并具有強(qiáng)度高、加工方便等特點(diǎn)。因此,高錳鋼在用作LNG儲(chǔ)罐方向上具有極大應(yīng)用前景與價(jià)值,其塑性、耐蝕性以及抗疲勞性引起許多低溫鋼研究者關(guān)注[9]。
合金化處理是改善鋼鐵各項(xiàng)性能的有效方法之一,在處理鋼樣過(guò)程中通常加入少量合金元素,都會(huì)對(duì)鋼鐵的組織和各項(xiàng)性能產(chǎn)生顯著影響[10]。Li等[11]通過(guò)低溫拉伸試驗(yàn)研究了Fe-20/27Mn-4Al-0.3C(20Mn、27Mn)鋼的力學(xué)性能,表明20Mn鋼在低溫下存在變形誘發(fā)馬氏體效應(yīng),伸長(zhǎng)率為77.4%;27Mn鋼未形成變形誘發(fā)馬氏體,且伸長(zhǎng)率為68.3%,相對(duì)較低。Mn影響了鋼樣的加工硬化率和伸長(zhǎng)率。Tang等[12]研究表明,高錳鋼中少量的Al能夠影響鋼樣的微觀組織,通過(guò)改變樣品表面氧化膜的成分,提高Al2O3膜的完整性,從而提高耐蝕性。Fajardo等[13]研究表明,TWIP奧氏體鋼Fe-Mn-3Al-3Si中,Mn含量越高,腐蝕敏感性越強(qiáng),耐蝕性越差。張丹丹等[14]研究表明,Mn含量為12.5%的固溶高錳鋼達(dá)到最大電荷傳輸電阻,表現(xiàn)出優(yōu)異的耐蝕性,證明了過(guò)高過(guò)低的Mn含量在高錳鋼中均對(duì)耐蝕性不利。Su等[15]對(duì)中錳鋼在NaCl溶液噴霧中形成的腐蝕產(chǎn)物層分析表明,腐蝕產(chǎn)物中存在Cr增加、Mn減少的現(xiàn)象,這些合金元素有利于形成腐蝕防護(hù)層,從而優(yōu)化耐蝕性能,因而鋼材自身受元素影響的耐蝕性能對(duì)于服役穩(wěn)定性至為重要。
此外銹層結(jié)構(gòu)、形貌還受外界環(huán)境和處理工藝的影響,例如:溫度[16]、離子濃度[17~19]及種類(lèi)[12,20]、冷軋[21]、焊接[22]等,銹層結(jié)構(gòu)不同導(dǎo)致鋼樣耐蝕性的差異。明男希等[23]研究表明,溫度通過(guò)影響X70鋼表面FeCO3膜的過(guò)飽和度、晶粒形核率和長(zhǎng)大速率,進(jìn)而影響其腐蝕速率。Cheng等[24]研究表明,高錳高氮奧氏體鋼(QN1803)在激光焊接后,由于高錳阻礙了相變,過(guò)飽和氮導(dǎo)致氮的流失,使QN1803殘留更多的
-鐵素體,從而整體耐蝕性降低。Yan等[25]研究了高錳鋼在模擬海洋飛濺區(qū)環(huán)境中的腐蝕行為,腐蝕速率與腐蝕過(guò)程中形成的氧化物有關(guān),研究證明腐蝕產(chǎn)物膜的保護(hù)作用逐漸顯著。腐蝕初期生成的Mn氧化物促進(jìn)了腐蝕進(jìn)程,后期腐蝕產(chǎn)物中Fe3O4、
-FeOOH和FeCr2O4的穩(wěn)定性和致密性抑制了錳鐵氧化物的腐蝕作用,減緩了腐蝕速率。Zhang等[26]探討了7B04鋁合金在酸浸和鹽霧環(huán)境(pH = 3.5)下的初始腐蝕行為,認(rèn)為鹽霧環(huán)境下腐蝕產(chǎn)物層生成速率比酸浸環(huán)境下大,腐蝕電流密度顯著低于酸浸環(huán)境下試樣,證明了腐蝕產(chǎn)物層越厚,對(duì)腐蝕反應(yīng)的抑制作用越強(qiáng)。Wang等[27]研究表明,新型含Al奧氏體耐熱鋼(AFA)在氧飽和的鉛鉍共晶(LBE)中,形成分層且不具保護(hù)性的氧化層,而在低氧濃度的LBE中,形成完整且具有保護(hù)性的富Al氧化層。降低LBE中的氧濃度會(huì)減緩界面向內(nèi)通氧量,使更多的Al向外擴(kuò)散,這有利于形成富Al氧化層,提高耐蝕性。因而鋼材服役環(huán)境也影響著其耐蝕性能。
本文選用添加了微合金化元素的高錳鋼和普通25Mn高錳鋼,通過(guò)酸性鹽霧試驗(yàn)探究其在模擬海洋大氣中的腐蝕行為,利用掃描電子顯微鏡、白光干涉儀、失重法分析兩種高錳鋼銹層以及腐蝕形貌的差異,同時(shí)通過(guò)動(dòng)電位極化和交流阻抗譜分析鋼樣的腐蝕過(guò)程,研究Cr、N、Al等微合金化元素對(duì)高錳鋼耐蝕性的影響,為進(jìn)一步提升高錳鋼耐蝕性提供支持。
1 實(shí)驗(yàn)方法
實(shí)驗(yàn)材料為國(guó)內(nèi)某鋼廠生產(chǎn)的兩種25Mn高錳鋼(HMS),使用濕法分析測(cè)得微合金化處理后的高錳鋼實(shí)際化學(xué)成分(質(zhì)量分?jǐn)?shù),%)為:C 0.45、Si 0.33、Mn 23.82、P 0.016、S 0.003、Cr 3.53、Cu 0.51、B 0.002、N 0.023、Al 0.032;未處理高錳鋼化學(xué)成分(質(zhì)量分?jǐn)?shù),%)為:C 0.46、Si 0.23、Mn 24.31、P 0.021、S 0.003、Cr 4.04、Cu 0.46、B 0.007、N 0.01、Al 0.005。可將微合金化處理后的高錳鋼命名為WH-HMS,未處理的高錳鋼命名為PT-HMS,采用電火花線切割(EDM)設(shè)備分別從兩種高錳鋼切割50 mm × 20 mm × 16 mm、10 mm × 10 mm × 3 mm的塊狀試樣用于失重分析和電化學(xué)分析,進(jìn)行電化學(xué)測(cè)試的樣品使用環(huán)氧樹(shù)脂與固化劑呈1∶1比例進(jìn)行混合,將銅導(dǎo)線在10 mm × 10 mm鋼材背面焊接并使用環(huán)氧樹(shù)脂密封。每個(gè)腐蝕周期使用3個(gè)平行試樣以確保實(shí)驗(yàn)的可靠與客觀。所有試樣的工作面,依次使用水磨砂紙180#、400#、800#、1200#、1500#及2000#對(duì)鋼樣6個(gè)面進(jìn)行逐級(jí)打磨,除去鋼板原始銹層,接著用2.5 μm金剛石膏拋光至鏡面,使用酒精超聲清洗3 min,去離子水沖洗后低溫干燥2 h封存?zhèn)溆谩?/span>
對(duì)鋼樣拋光處理后,采用4% HNO3和96%無(wú)水乙醇(體積分?jǐn)?shù))配置金相腐蝕液對(duì)高錳鋼進(jìn)行刻蝕。使用去離子水、無(wú)水乙醇洗凈后干燥,采用Leica DM2700M型金相顯微鏡觀察鋼樣金相組織。圖1a為WH-HMS金相組織,其中可見(jiàn)部分晶粒較大,晶界較直,少量析出碳化物在晶界和晶內(nèi),呈彌散分布,對(duì)其耐蝕性影響不大,所得組織為奧氏體和少量的沿晶網(wǎng)狀碳化物。圖1b為PT-HMS的組織形貌,大量析出碳化物分布在晶界和晶內(nèi)[28, 29]。
圖1 微合金化處理后高錳鋼及未處理高錳鋼金相形貌
Fig.1 Metallographic photos of WH-HMS (a) and PT-HMS (b)
根據(jù)ASTM B117標(biāo)準(zhǔn),酸性鹽霧試驗(yàn)在YWX/YH-60鹽霧試驗(yàn)箱中進(jìn)行,溶液配置為50 g/L NaCl溶液,實(shí)驗(yàn)溫度為(35 ± 2)℃,沉降量為1.65 mL/(80 cm2·h),鹽霧沉降的速率應(yīng)在連續(xù)噴霧至少24 h后測(cè)量。為了模擬酸性大氣環(huán)境,用稀鹽酸將溶液的pH調(diào)整為3.1~3.3,實(shí)驗(yàn)時(shí)間持續(xù)12、48、96、168和240 h后,分別取出3個(gè)失重試樣和3個(gè)電化學(xué)試樣。實(shí)驗(yàn)前需清除試樣表面的沉積鹽,以減少對(duì)腐蝕產(chǎn)物的影響。
將腐蝕后試樣用去腐蝕液(500 mL HCl + 500 mL H2O + 3~10 g六次甲基四胺)超聲波清洗1 min去除腐蝕產(chǎn)物,再用去離子水、無(wú)水乙醇清洗、充分干燥后,最后使用高精度天平測(cè)量酸性鹽霧腐蝕不同時(shí)間的失重試樣質(zhì)量。每組失重?cái)?shù)據(jù)均取3個(gè)平行試樣的平均值。
采用HV-1000STA場(chǎng)發(fā)射掃描電子顯微鏡(SEM)觀察鹽霧腐蝕不同時(shí)間后試樣表面形貌及清除腐蝕層后試樣表面形貌。使用Bruker Contour GT-1型白光干涉儀對(duì)試樣進(jìn)行三維形貌拍攝,截取其腐蝕軌跡,3D腐蝕形貌通過(guò)Vision64 Bruker 軟件進(jìn)行分析。
電化學(xué)測(cè)試在CHI660電化學(xué)工作站上進(jìn)行,采用三電極測(cè)試系統(tǒng),工作電極(WE)為鹽霧腐蝕后的高錳鋼、參比電極(RE)為Ag/AgCl電極、鉑片(Pt)為輔助電極(CE)。連接接通后,為保證測(cè)試體系穩(wěn)定,先將鋼樣放在3.5%(質(zhì)量分?jǐn)?shù)) NaCl溶液中分別靜置30 min,穩(wěn)定后依次測(cè)量開(kāi)路電位(OCP)、電化學(xué)阻抗譜(EIS)和極化曲線(PC)。EIS測(cè)量在OCP下進(jìn)行,測(cè)量頻率為105~10-2 Hz,振幅為5 mV。動(dòng)電位極化曲線測(cè)試范圍為-300~500 mV,電位掃描速率為1 mV/s。點(diǎn)蝕電位(Ep)是在正向掃描期間電流密度突然增加的點(diǎn)測(cè)定的。測(cè)試結(jié)束后使用ZsimpWin軟件對(duì)相關(guān)數(shù)據(jù)進(jìn)行分析。所有測(cè)試均在環(huán)境溫度(25 ± 1)℃下進(jìn)行,并重復(fù)至少3次以確保數(shù)據(jù)的可靠性。
2 結(jié)果與討論
2.1 腐蝕行為及形貌分析
圖2為兩種高錳鋼在酸性鹽霧環(huán)境腐蝕不同周期后腐蝕產(chǎn)物的SEM像。WH-HMS在腐蝕12 h后(圖2a),腐蝕產(chǎn)物較少,較薄的腐蝕產(chǎn)物疏松分散在基體表面,表面仍有裸鋼露出。48 h(圖2c)后腐蝕產(chǎn)物呈棉球狀,腐蝕96 h(圖2e)時(shí)腐蝕產(chǎn)物呈棉球狀和團(tuán)簇狀。在腐蝕168~240 h后(圖2g和i),腐蝕產(chǎn)物呈團(tuán)簇狀和針狀,且存在大量孔洞,有利于Cl-穿過(guò)銹層進(jìn)入基體與銹層界面,促進(jìn)鋼基體的腐蝕,使腐蝕產(chǎn)物逐漸變得均勻、致密。PT-HMS腐蝕12 h后(圖2b),表面腐蝕產(chǎn)物呈疏松的團(tuán)簇狀,有較多的孔洞存在。腐蝕48 h(圖2d)時(shí),腐蝕產(chǎn)物主要呈棉球狀,大塊腐蝕產(chǎn)物不再出現(xiàn),腐蝕較為均勻。腐蝕96 h(圖2f)時(shí),“棉球”形態(tài)的腐蝕產(chǎn)物變得細(xì)小,且呈團(tuán)簇狀,存在大量孔洞。腐蝕168~240 h (圖2h和j)后,腐蝕產(chǎn)物逐漸均勻,呈棉球狀和針狀。隨著腐蝕時(shí)間的增加,銹層逐漸加厚,腐蝕產(chǎn)物特征顯著。研究表明[30~32],γ-FeO(OH)通常呈棉球狀、不規(guī)則顆粒狀和團(tuán)簇狀,α-FeOOH通常呈針狀或須狀。研究[33, 34]普遍認(rèn)為高錳鋼表面優(yōu)先形成γ-FeO(OH),隨著腐蝕產(chǎn)物的積累,活性的γ-FeOOH轉(zhuǎn)變?yōu)榉€(wěn)定的α-FeOOH,二者相互依附,使銹層更加致密。
圖2 兩種高錳鋼鹽霧腐蝕不同時(shí)間后表面銹層微觀形貌
Fig.2 Surface morphology of WH-HMS for 12 h (a), 48 h (c), 96 h (e), 168 h (g), 240 h (i) and PT-HMS for 12 h (b), 48 h (d), 96 h (f), 168 h (h), 240 h (j) after salt spray corrosion
對(duì)比兩種高錳鋼的腐蝕產(chǎn)物形貌,可以看出經(jīng)過(guò)微合金化處理后的高錳鋼表面腐蝕產(chǎn)物的致密性得到明顯提高,顯著減小了其腐蝕程度。WH-HMS在初始時(shí)腐蝕程度就相對(duì)較輕,腐蝕240 h后銹層更加致密,這說(shuō)明適量的Cr可在鋼表面細(xì)化銹層結(jié)構(gòu),形成更致密的氧化膜。Cu的添加可有效促進(jìn)α-FeOOH穩(wěn)定化銹層的形成[35],鈍化膜中Si和Cr的分布幾乎同步,這種協(xié)同作用增強(qiáng)了鋼樣表面膜的鈍化能力[36],進(jìn)而提高鋼樣耐腐蝕性能。經(jīng)過(guò)鹽霧不同腐蝕時(shí)間后三維輪廓圖如圖3和4所示。兩種高錳鋼腐蝕產(chǎn)物隨著腐蝕時(shí)間增加,腐蝕產(chǎn)物逐漸積累,在初始階段WH-HMS的腐蝕產(chǎn)物厚度最高約20.4385 μm,略大于PT-HMS。腐蝕240 h后,多處點(diǎn)蝕連接形成不規(guī)則形狀的腐蝕區(qū)域,且WH高錳鋼相較于PT高錳鋼腐蝕得更加均勻,與觀察到的表面形貌結(jié)果一致,表明WH高錳鋼在腐蝕后期,腐蝕產(chǎn)物更加均勻,耐腐蝕性更好。
圖3 微合金化高錳鋼鹽霧腐蝕不同時(shí)間后的三維輪廓圖
Fig.3 3D morphologies of WH-HMS after salt spray corrosion for 0 h (a), 12 h (b), 48 h (c), 96 h (d), 168 h (e) and 240 h (f)
圖4 普通高錳鋼鹽霧腐蝕不同時(shí)間后的三維輪廓圖
Fig.4 3D morphologies of PT-HMS after salt spray corrosion for 0 h (a), 12 h (b), 48 h (c), 96 h (d), 168 h (e) and 240 h (f)
圖5為兩種高錳鋼去除腐蝕產(chǎn)物后表面微觀形貌。由圖(5a, c, e, g和i)可見(jiàn),WH高錳鋼試樣表面形成了少量局部點(diǎn)腐蝕坑,在腐蝕48 h后,有析出物質(zhì)生成。腐蝕96 h后,出現(xiàn)一些凸起的線狀?yuàn)W氏體型組織,而并沒(méi)有出現(xiàn)明顯的點(diǎn)蝕坑,局部腐蝕并未加劇,這也進(jìn)一步證實(shí)了點(diǎn)蝕特征不會(huì)隨著腐蝕時(shí)間的增加而發(fā)生顯著變化。同樣,PT高錳鋼出現(xiàn)類(lèi)似現(xiàn)象,在腐蝕48 h后,出現(xiàn)線狀?yuàn)W氏體組織,且有大量析出物生成。在腐蝕168和240 h后,出現(xiàn)裂紋,點(diǎn)蝕坑變多,局部腐蝕加重,如圖5g和j所示。結(jié)果表明,高錳鋼表面均表現(xiàn)為局部點(diǎn)腐蝕、有析出物生成和局部裂紋形貌,且PT高錳鋼的表面腐蝕更為嚴(yán)重,說(shuō)明微合金化元素的添加大大提升了高錳鋼的耐蝕性能。
圖5 兩種高錳鋼鹽霧腐蝕不同時(shí)間后去除銹層表面微觀形貌
Fig.5 Surface morphology of the rust removal layer of WH-HMS for 12 h (a), 48 h (c), 96 h (e), 168 h (g), 240 h (i) and PT-HMS for 12 h (b), 48 h (d), 96 h (f), 168 h (h), 240 h (j) after salt spray corrosion
2.2 動(dòng)電位極化曲線
經(jīng)過(guò)不同鹽霧腐蝕時(shí)間的兩種高錳鋼在模擬海水溶液中的動(dòng)電位極化曲線如圖6所示。結(jié)果表明,不同腐蝕時(shí)間后,兩種高錳鋼銹層的陰極極化曲線基本相似,陽(yáng)極極化曲線表現(xiàn)出不同的腐蝕行為。陽(yáng)極極化曲線顯示,在-0.6~-0.4 V范圍內(nèi),各個(gè)腐蝕階段的銹層都有不同程度的鈍化,即隨著電位的升高,電流密度基本保持不變。微合金化高錳鋼在腐蝕240 h后出現(xiàn)的點(diǎn)蝕電位明顯升高,這也與研究[37]得出的結(jié)論一致,隨著N含量的提高,試樣的腐蝕沒(méi)有明顯變化,但是點(diǎn)蝕電位顯著提高,表明N含量的提高改善了腐蝕產(chǎn)物膜層的保護(hù)性能,耐點(diǎn)蝕性能增強(qiáng)。
圖6 微合金化高錳鋼、普通高錳鋼鹽霧腐蝕不同時(shí)間后極化曲線
Fig.6 Potentiodynamic polarization curves of WH-HMS (a) and PT-HMS (b) after salt spray corrosion for different time
對(duì)極化曲線進(jìn)行Tafel曲線擬合可以得到腐蝕電位(Ecorr)、腐蝕電流密度(Icorr),進(jìn)而判斷工作電極的腐蝕速率,擬合結(jié)果如表1、2所示。從表中可以看出,鹽霧240 h后,WH-HMS腐蝕電流密度由5.328 μA/cm2降低至1.962 μA/cm2,腐蝕速率由5.230 × 10-3 mm/a降低至1.925 × 10-3 mm/a;PT-HMS腐蝕電流密度先由5.310 μA/cm2降低至2.754 μA/cm2,又逐漸增加到4.038 μA/cm2,腐蝕速率也先減小后增加,由5.212 × 10-3 mm/a降低至2.703 × 10-3 mm/a,再增加到3.964 × 10-3 mm/a。這些數(shù)據(jù)進(jìn)一步證明微合金化處理后的高錳鋼的耐腐蝕性最好,與形貌表征分析出的結(jié)果相符。
表1 微合金化高錳鋼極化曲線擬合結(jié)果
Table1 Polarization curve fitting results of WH-HMS
表2 普通高錳鋼極化曲線擬合結(jié)果
Table2 Polarization curve fitting results of PT-HMS
2.3 EIS分析
圖7為經(jīng)鹽霧各腐蝕周期下兩種高錳鋼在3.5%NaCl溶液中的電化學(xué)阻抗譜測(cè)試結(jié)果。耐腐蝕性能可以通過(guò)電容性半圓弧直徑來(lái)體現(xiàn),半圓弧直徑的增大表明耐腐蝕性能的提高[38]。隨著腐蝕時(shí)間的增加,WH-HMS的容抗弧半徑腐蝕96 h后略微增大,在腐蝕240 h時(shí)容抗弧半徑達(dá)到最大。PT-HMS在腐蝕96 h時(shí)達(dá)到最大容抗弧半徑,后隨著腐蝕時(shí)間延長(zhǎng)而逐漸減小,且PT-HMS的最大容抗弧半徑遠(yuǎn)小于WH-HMS,表明WH-HMS的耐蝕性更好,說(shuō)明Cr、N、Al等微合金化元素的添加明顯提高了高錳鋼的耐蝕性。Bode圖頻率與阻抗的關(guān)系表明,隨著腐蝕時(shí)間的增加,低頻總阻抗模量逐漸增大。結(jié)果表明,在腐蝕過(guò)程中,銹層的耐蝕性逐漸增強(qiáng)。
圖7 微合金化高錳鋼、普通高錳鋼鹽霧腐蝕不同時(shí)間后的電化學(xué)阻抗譜圖及等效電路圖
Fig.7 EIS of WH-HMS (a, c,e) and PT-HMS (b, d, f) and electrochemical equivalent circuit (g) after salt spray corrosion for different time
為了評(píng)估腐蝕產(chǎn)物在不同腐蝕時(shí)間后在試樣表面形成的保護(hù)膜的阻抗能力,采用圖7g所示的等效電路(EEC)模型擬合阻抗譜,其中,Rs表示溶液電阻,Rf和Qf為腐蝕產(chǎn)物膜層電阻和恒相元件(CPE),Rct和Qdl為雙電層間的電荷轉(zhuǎn)移電阻和恒相元件,n為彌散指數(shù),表示“彌散效應(yīng)”的偏離程度,當(dāng)n = 1時(shí),Q相當(dāng)于純電容。得到的最佳擬合參數(shù)如表3和4所示。從表中擬合結(jié)果可知,腐蝕240 h后WH-HMS的Rct值遠(yuǎn)大于PT-HMS,說(shuō)明微合金化處理的高錳鋼耐蝕性更優(yōu)。
表3 鹽霧腐蝕不同時(shí)間后微合金化高錳鋼等效電路擬合結(jié)果
Table 3 Equivalent circuit fitting results of WH-HMS after salt spray corrosion with different corrosion time
表4 鹽霧腐蝕不同時(shí)間后普通高錳鋼等效電路擬合結(jié)果
Table 4 Equivalent circuit fitting results of PT-HMS after salt spray corrosion with different corrosion time
2.4 腐蝕動(dòng)力學(xué)分析
高錳鋼酸性鹽霧腐蝕不同時(shí)間后單位面積失重曲線及擬合曲線如圖8a所示。已有研究表明,金屬材料的腐蝕失重ΔW與腐蝕時(shí)間t之間存在冪函數(shù)關(guān)系,公式如下[39,40]:
式中:A和n為常數(shù),反映銹層對(duì)金屬基體的保護(hù)作用[41]。若n < 1,銹層起保護(hù)作用;若n > 1,銹層加速腐蝕。由表5的擬合結(jié)果可知,兩種高錳鋼的n值均 < 1,說(shuō)明隨著腐蝕時(shí)間的增加,兩種高錳鋼的銹層厚度逐漸增加,均具有保護(hù)作用。而ΔWWH-HMS = 4.44202 × 10-4t0.9618 < ΔWPT-HMS = 8.74985 × 10-4t0.67759,說(shuō)明微合金化后高錳鋼銹層的保護(hù)性高于普通高錳鋼。
圖8 兩種高錳鋼鹽霧腐蝕不同時(shí)間后腐蝕失重?cái)M合曲線和腐蝕速率變化趨勢(shì)
Fig.8 Variations of mass loss fitting curve (a) and corrosion rate (b) of WH-HMS and PT-HMS with time
表5 兩種高錳鋼腐蝕動(dòng)力學(xué)擬合結(jié)果
Table 5 Fitting results of corrosion kinetic curves of two experimental steels
根據(jù)鋼樣的原始質(zhì)量與去除腐蝕產(chǎn)物后的質(zhì)量之差來(lái)測(cè)定高錳鋼的質(zhì)量變化(Δm)。通過(guò)確定平均腐蝕速率值,如表6所示,表征了腐蝕動(dòng)力學(xué)曲線,如圖8b所示。根據(jù) 式(2)[40,42]計(jì)算平均腐蝕速率ACR:
其中,Δm為質(zhì)量變化(g);t為腐蝕時(shí)間(h);ρ是被測(cè)試鋼材的物理密度(0.8 g/cm3);S為鋼板最大表面的面積(cm2)。兩種高錳鋼腐蝕曲線均呈不斷下降的趨勢(shì),其中PT-HMS在初始階段,平均腐蝕速率有急劇下降的趨勢(shì),在下一個(gè)浸泡時(shí)間節(jié)點(diǎn)后,平均腐蝕速率略有下降。80~240 h的腐蝕曲線較為穩(wěn)定,腐蝕速率的相對(duì)穩(wěn)定值為0.3745 × 10-3 mm/a;WH-HMS平均腐蝕速率下降相對(duì)較為顯著,腐蝕240 h后穩(wěn)定值不明顯。微合金化后高錳鋼的腐蝕速率整體均小于未處理高錳鋼,且失重量相對(duì)較大,說(shuō)明微合金化后高錳鋼的耐蝕性更優(yōu)。
表6 兩種高錳鋼鹽霧腐蝕不同時(shí)間后平均腐蝕速率及失重量
Table 6 Average corrosion rate and mass loss of two experimental steel
3 結(jié)論
(1) 微合金化工藝通過(guò)致密化鈍化膜有效提升了高錳鋼的耐蝕性,兩種高錳鋼在腐蝕初期,疏松銹層為腐蝕的發(fā)生提供了通道,腐蝕速率較快,腐蝕電流密度較大;隨著腐蝕時(shí)間的增加,銹層覆蓋率、致密度逐漸增加,腐蝕速率也逐漸減緩,腐蝕電流密度減小,耐腐蝕性提高。WH-HMS在腐蝕240 h后,其EIS譜線形成最大容抗弧半徑,且遠(yuǎn)遠(yuǎn)大于PT-HMS;腐蝕電流密度也在240 h后達(dá)到最小值,且小于普通高錳鋼,進(jìn)一步證明微合金化后的高錳鋼耐腐蝕性能優(yōu)于普通高錳鋼。
(2) 普通25Mn高錳鋼的腐蝕速率約為0.8982 × 10-3 mm/a,微合金化后約為0.3745 × 10-3 mm/a,兩種高錳鋼腐蝕行為均由點(diǎn)蝕逐漸發(fā)展為均勻腐蝕,且腐蝕動(dòng)力學(xué)特性均符合冪函數(shù)規(guī)律。其中,未處理高錳鋼擬合結(jié)果為ΔWPT= 4.44202 × 10-4t0.9618;微合金化后高錳鋼擬合結(jié)果為ΔWWH= 8.74985 × 10-4t0.67759。
免責(zé)聲明:本網(wǎng)站所轉(zhuǎn)載的文字、圖片與視頻資料版權(quán)歸原創(chuàng)作者所有,如果涉及侵權(quán),請(qǐng)第一時(shí)間聯(lián)系本網(wǎng)刪除。
相關(guān)文章
無(wú)相關(guān)信息
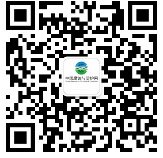
官方微信
《腐蝕與防護(hù)網(wǎng)電子期刊》征訂啟事
- 投稿聯(lián)系:編輯部
- 電話:010-62316606
- 郵箱:fsfhzy666@163.com
- 腐蝕與防護(hù)網(wǎng)官方QQ群:140808414
文章推薦
點(diǎn)擊排行
PPT新聞
“海洋金屬”——鈦合金在艦船的
點(diǎn)擊數(shù):9189
腐蝕與“海上絲綢之路”
點(diǎn)擊數(shù):7306