概述 根據工業發達國家統計,每年因鋼材腐蝕造成的經濟損失約為GDP的2%~4%。目前,全球鋼材腐蝕造成的經濟損失高達萬億美元。近年來,我國因鋼結構腐蝕造成的不安全事故約占橋梁安全事故的25%~30%。因此,學者們在鋼結構的腐蝕、檢測和防腐技術等方面開展了廣泛研究。 橋梁鋼結構腐蝕與 腐蝕疲勞損傷機理 鋼材的腐蝕類型多種多樣,包括均勻腐蝕、點腐蝕、縫隙腐蝕、晶間腐蝕和應力腐蝕等。均勻腐蝕是指鋼材表面全面均勻發生的腐蝕現象,導致材料整體逐漸變薄。點腐蝕則在局部區域發生,形成小面積的快速腐蝕,通常在應力集中或保護層缺陷處出現。縫隙腐蝕多發生在金屬連接處,如焊縫或緊固件接縫處,由于縫隙中電解質的滲透而形成。晶間腐蝕和應力腐蝕則分別由材料的晶粒邊界和外部應力作用引起,它們都可能導致材料的突然斷裂。 2.1 橋梁鋼構件腐蝕疲勞損傷 圖1 Q690D腐蝕樣本的S-N曲線:C0無腐蝕,C1,C2,C3腐蝕 Jiang等研究腐蝕效應對正交異型鋼橋面板疲勞性能的影響和疲勞裂紋擴展的規律,利用元胞自動機腐蝕模型獲取了在不同質量損失率(w)下典型正交異型鋼橋面板構件的三維腐蝕形態,并建立了具有毫米級腐蝕坑和裂紋的長跨度橋梁的多尺度有限元模型。結果顯示,與通過均勻厚度減小來表征腐蝕效應的方法相比,元胞自動機腐蝕模型獲得的極限承載能力更符合實驗結果。與未考慮腐蝕效應時相比,當U肋的w分別為6%、8%和10%時,U肋焊腳的裂紋起始處的峰值應力強度因子增加了32%、49%和86%,U肋-隔板的疲勞裂縫壽命分別降低了6.5%、18.9%和50%。根據U肋焊腳處裂紋起始的應變能釋放率,裂紋是以張開型裂紋為主,滑開型裂紋和撕開型裂紋為輔的復合裂紋。 羅霞飛等采用自主設計的海水間歇供水循環系統模擬干濕比為1:1的海水干濕交替環境,研究了空氣環境、全浸環境、干濕交替環境和應力比0.1、0.3和0.5對高強度鋼EH690鋼疲勞裂紋擴展的影響。基于試驗獲得的a-N曲線(a裂紋長度,N為疲勞周期)和da/dN-ΔK曲線(da/dN為裂紋擴展速率,裂紋尖端應力強度因子幅值),發現在裂紋擴展前期,EH690鋼在干濕交替環境與全浸環境中的裂紋擴展速率為空氣中的三倍左右,呈現出顯著的疲勞裂紋擴展加速現象。對于給定的應力強度因子,疲勞裂紋擴展速率隨著應力比的增大而增大。研究還擬合得到了不同環境和應力比下標準緊湊拉伸試件的Pairs常數,并通過掃描電鏡從微觀角度分析EH690高強鋼的腐蝕疲勞裂紋擴展機理,為實際海洋平臺的腐蝕疲勞壽命評估提供了可靠的試驗數據參考。 胡春建等基于濰萊鐵路線一座全焊接免涂裝耐候鋼橋,開展了列車動力作用下的關鍵構件和焊接節點疲勞損傷分析,并進行考慮腐蝕劣化影響下的疲勞壽命評估。基于列車-軌道-橋梁耦合系統模型,研究了在高速列車動力荷載下橋梁主桁關鍵構件動力響應,并得到結構中最不利構件位置,分析了關鍵構件在列車通行振動效應下的疲勞損傷度。結合考慮局部節點板精細化的多尺度耦合有限元模型,考慮軌道不平順和列車運行速度的影響,得到橋梁節點板在不同速度下的疲勞損傷度;考慮環境腐蝕對橋梁疲勞壽命的影響,結合橋梁列車年運營量進行腐蝕環境下橋梁關鍵桿件和節點的疲勞使用壽命評估。研究結果表明,鐵路鋼桁梁橋在列車動力作用下,不同構件的疲勞損傷不同,剛度較小以及應力響應影響線較短的構件疲勞損傷度更大,其中疲勞損傷度由大到小依次為節點橫梁、腹桿、下弦桿、上弦桿。軌道不平順和列車運行速度對橋梁節點板應力響應最大值影響并不顯著,列車運行速度為120 km/h時與所分析橋梁共振更明顯。環境腐蝕會降低鐵路橋梁疲勞壽命,且對橋梁不同構件壽命影響程度不同。 2.2 高強鋼絲、纜索的 腐蝕/腐蝕疲勞損傷 王鑫等研究了含裂紋高強鋼絲在不同腐蝕周期后的力學性能變化及腐蝕機理。通過對1770MPa高強鍍鋅鋼絲進行人工加工刻痕模擬微裂紋狀態,在中性鹽霧環境下進行了不同時間(120,240,360,480,720小時)的腐蝕試驗。拉伸試驗結果顯示,隨著腐蝕時間的增加,鋼絲的極限強度、斷后伸長率逐漸降低,但彈性模量基本不變。有限元分析表明,蝕坑剛形成時裂紋底部會發生應力集中,更易在此處斷裂。斷口分析顯示,腐蝕會促進裂紋擴展,但不改變鋼絲微觀結構;隨腐蝕時間增加,斷口由韌窩轉為脆性斷裂。 Li等研究了腐蝕時間、應力水平、應力范圍對鋼絲失效模式、疲勞壽命和S-N曲線的影響。通過SEM掃描電鏡掃描分析了不同腐蝕程度鋼絲疲勞斷裂和裂縫增長速率,揭示了腐蝕鋼絲的裂紋萌生和擴展機制。圖3展示了不同腐蝕程度下鋼絲斷裂形態。研究表明,鋼絲疲勞壽命隨腐蝕程度的增加而減少。這個腐蝕程度對鋼絲疲勞壽命的影響是從敏感到不敏感。隨著腐蝕程度的增加,晶體間距和裂紋增加速率也會增加,裂紋萌生比例和裂紋擴展區從纜索直徑的45%減少到直徑的28%。腐蝕深度越大、表面越銳利,越容易成為疲勞裂紋源。 圖3 不同腐蝕程度下鋼絲斷裂形態圖試件 (F20-d90-ε2000-1/2/3/4中F20代表第20個疲勞試件,d90代表腐蝕齡期為90天,ε2000表示應變水平為2000 με,1/2/3/4代表4個不同的應力范圍) Xu等基于腐蝕壽命逆等階假設,考慮斜拉索的腐蝕及其變化,建立了平行鋼絲斜拉索中鋼絲連續失效過程的等效循環次數遞推公式。通過分別對鋼絲的腐蝕程度和疲勞壽命進行兩次階次統計,估算了斜拉索疲勞壽命累積分布函數(CDF)的界限,但沒考慮未斷絲的荷載重分布。基于Bai的腐蝕程度從0.18%到18.67%的腐蝕鋼絲的腐蝕應力壽命模型,通過蒙特卡羅模擬獲得了腐蝕及其變化對斜拉索疲勞壽命的影響。結果顯示,斜拉索的疲勞壽命受腐蝕程度較大的鋼絲影響,一旦考慮了腐蝕及其變異性,斜拉索應在5%的鋼絲斷裂時視為失效。此外,隨著腐蝕程度和及其變異性的增加,斜拉索的疲勞壽命會急劇下降,而鋼絲和斜拉索的疲勞壽命的變異性也會增加。 Yan等基于鋼絲實驗數據,確立了鋼絲的均勻腐蝕深度的均值和標準偏差之間的關系,獲得了拉索中鋼絲的質量損失率的分布。隨后基于Miner線性累積損傷準則和平行系統理論去計算考慮鋼絲腐蝕變化的疲勞壽命。 Yu研究了腐蝕和活載共同作用下鋼絲耐久性。通過鋼絲斷面形態和不同樣本腐蝕特征去分析鋼絲的每種類型的失效模式。研究發現,在低應力幅下,鋼絲的疲勞壽命主要受環境的影響。但隨著應力幅的增加,疲勞壽命由應力幅決定。鋼絲斷裂形態分為單源斷裂和多源斷裂(圖4)。腐蝕程度低的鋼絲裂紋起源于單個疲勞源,隨著疲勞程度增加,腐蝕坑的深度增加,裂紋從不同的疲勞源擴展。隨著鋼絲嚴重腐蝕,擴展區減少,斷裂區域增加。 圖6 鋼絲裂紋失效模式 劉佳偉等為了評估在役滿20年后拱橋吊桿鋼絲的剩余疲勞壽命,基于某服役滿20年拱橋更換下來的吊桿,以吊桿內部高強度鋼絲為研究對象,對鋼絲進行不同時間的加速腐蝕,獲得不同腐蝕程度的鋼絲試件。對試件鋼絲進行表觀檢測、稱重、疲勞實驗和斷口形貌分析,得到了不同腐蝕程度下鋼絲的表面粗糙度、質量損失率、斷裂機理和疲勞壽命。通過Weibull模型對疲勞壽命數據分析,得到了不同失效概率下吊桿鋼絲的剩余疲勞壽命公式。研究結果表明,隨著腐蝕程度的增加,吊桿鋼絲表面粗糙度和質量損失率的數值不斷增加,疲勞壽命降低且疲勞斷口均為脆性破壞。打磨后的鋼絲疲勞壽命有所提升;相同失效概率下,吊桿鋼絲剩余疲勞壽命將隨著應力比的增加或腐蝕程度的增加而減少。通過實驗得到了在役滿20年后拱橋吊桿鋼絲的Pf-S-N曲線,為吊桿鋼絲的服役狀態和疲勞壽命預測提供了參考。 2.3 鋼橋連接腐蝕/腐蝕疲勞損傷 Jiang等研究了腐蝕對鋼塔角焊縫的疲勞壽命的影響,并提出了一種基于斷裂力學方法的非承載角焊縫疲勞壽命預測方法。研究考慮了初始裂紋處的點蝕、初始裂紋附近的點蝕和腐蝕疲勞裂紋擴展三種腐蝕效應,并定義了不同腐蝕環境下的輕度、中度和重度三種腐蝕等級。結果表明,當點蝕發生在角焊縫初始裂紋處時,疲勞壽命會隨著腐蝕深度增加而降低。在中等和嚴重腐蝕水平下,疲勞性能不滿足Eurocode 3(圖8);當點蝕發生在初始裂縫附近時,由于點蝕降低了焊趾附近裂縫前端的拉應力,角焊縫的疲勞性能會有所提升。 (a) CFCB-1 (b) CFCB-2 (c) CFCB-3 Kuang等研究了腐蝕栓釘的疲勞性能,并根據疲勞裂紋擴展理論和腐蝕栓釘疲勞失效機理,提出了腐蝕栓釘疲勞壽命預測模型。研究發現,隨著栓釘腐蝕率的增加,疲勞壽命迅速降低。當栓釘的腐蝕率從5%增加到50%時,栓釘的疲勞壽命分別從20%下降到90%(圖10)。 Guo等研究了軸向受力的高強度螺栓在腐蝕后的疲勞性能,對螺栓進行長達300天的中性鹽霧試驗,以模擬長期腐蝕。基于螺栓的宏觀形態和微觀形態,揭示了螺栓螺紋及銹蝕成分的演化規律,并建立了腐蝕時間對腐蝕坑的期望和方差影響的量化公式,獲得了螺栓剪壞和斷裂的失效模式。此外,失效模式轉變時的臨界腐蝕時間為150天,平均質量損失率為7.12%。如果腐蝕時間短于臨界時間時,螺栓斷裂變得更加明顯;否則,螺栓螺紋剪切會變得更明顯(圖11)。分別針對螺栓斷裂和螺栓螺紋剪切失效模式建立了疲勞壽命和腐蝕周期之間的指數和線性關系。同時,在中性鹽性噴霧環境下的S-N曲線被提出,為腐蝕螺栓的疲勞壽命預測奠定了基礎。 圖11 高強度螺栓疲勞壽命與腐蝕時間的關系 蘆燕等對G20Mn5QT/Q355異種鋼對接焊接接頭在模擬海水環境下的腐蝕疲勞性能進行了研究,開展了其在NaCl溶液中腐蝕疲勞試驗(圖13),并對腐蝕疲勞斷口進行了掃描電子顯微鏡試驗,分析了其腐蝕疲勞失效機理。研究揭示了在較大應力水平(>220 MPa)下,母材缺陷及焊接缺陷是導致裂紋成核的主要原因;而在較小應力水平(≤220 MPa)下,表面蝕坑是導致裂紋成核的主要原因。對腐蝕疲勞試驗數據分別采用Stromeyer公式與基于三參數威布爾分布模型建立了對接焊接接頭的腐蝕疲勞壽命預測方法,結果表明采用三參數威布爾分布的腐蝕疲勞S-N曲線擬合精度更高。 馬燕等為了給解決耐候鋼橋在應用和發展中所面臨的腐蝕問題提供理論方法與對策,針對耐候鋼在大氣環境中的腐蝕損傷演化特性,通過編制MATLAB程序,建立了基于三維元胞自動機技術的耐候鋼焊接節點大氣腐蝕經時演化模型。該模型根據耐候鋼在大氣腐蝕過程中發生的化學反應,將大氣腐蝕系統中的關鍵元素抽象成4種元胞類型,并離散成元胞網格。對母材和焊縫分別定義了不同的元胞鄰居類型,模擬了耐候鋼焊接節點代表性體元在介觀尺度上的腐蝕演化過程,并通過大氣暴露試驗驗證了所提出方法的可行性和有效性,揭示了耐候鋼焊接節點腐蝕動力學及蝕坑演化規律,分析了溶解氧濃度和溶解概率對腐蝕損傷的影響。在此基礎上提出了耐候鋼大氣腐蝕經時演化預測方法。 腐蝕檢測與評估 3.1 橋梁鋼構件腐蝕監測技術 目前全球范圍內橋梁“老齡化”問題凸顯,受腐蝕損害嚴重,橋梁的服役性能劣化及橋梁倒塌等災禍在全球范圍內出現了逐年上升的趨勢。因此,加大橋梁養護和檢測勢在必行。目前檢測橋梁腐蝕狀況的檢測技術主要是基于計算機視覺和機器學習的損傷識別方法和基于傳感器檢測技術的無損檢測方法。 3.2 基于計算機視覺和機器學習 的損傷識別方法 馮東明等為了實現懸索橋主纜的自動化、智能化檢查,開展了基于無人機的主纜巡檢路徑規劃和小樣本數據下的主纜病害識別研究(圖14)。首先,利用無人機傾斜攝影測量技術快速建立懸索橋的三維模型,提出主纜無人機自動巡檢路徑的規劃方法;然后,采用Faster RCNN網絡模型識別主纜圖像中的表觀病害;最后,采用基于圖像融合的數據增強方法,提高小樣本數據集下目標檢測的準確率。在Faster RCNN網絡模型訓練過程中,隨著訓練輪次的增加,測試集中裂紋、銹蝕和劃痕三類病害的平均精確率得到提升,并在第15個訓練輪次后逐漸穩定,經過100個訓練輪次后,測試集中所有類別的平均精確率為0.723。以小龍灣橋為研究對象,進行了主纜的現場檢查試驗。研究結果表明,基于懸索橋三維模型進行主纜無人機自動巡檢路徑規劃具有實際可行性;基于Faster RCNN網絡模型能較準確地識別主纜的裂紋、銹蝕和劃痕病害;利用圖像融合方法生成病害數據能有效克服數據樣本少的問題,并提高識別的準確性。 圖15表明,所提出的自適應光照預處理方法有效改善了實橋腐蝕圖像的光照不均和低光照問題,修復和增強了細節和紋理特征信息,顏色保真度較高;所提出的數據標注方法能夠精準標注腐蝕區域,減少邊緣描繪工作;與原始圖像相比,該方法預處理后的圖像訓練的模型在準確率、精確率、召回率、F1-score、交并比IoU和AUC上分別提高了5.2%、2.7%、22.5%、19.4%、25.4%和10.5%;對于光照良好的均勻腐蝕圖像,預處理對分割精度提高有限,對于點蝕圖像,分割精度有較大的提高,對于低光照或光照均勻性較差的圖像,分割精度得到了大幅提高。 Gao等采用了基于視覺圖像特征的準確檢測方法。無人機技術用于收集鋼橋的腐蝕圖像。考慮到圖像的復雜性,利用深度神經網絡對圖像進行卷積運算。根據銹跡圖像的明顯特征構建了一個深度神經網絡模型。監督學習的深度神經網絡與無監督學習的稀疏自編碼相結合,通過無監督學習的稀疏自編碼對深度神經網絡進行自編碼來減少重構偏差。在此基礎上,實現了對銹蝕狀態的準確檢測。 3.3 基于傳感器檢測技術的 無損檢測方法
耐腐蝕材料 陳繼林采用腐蝕失重法、宏觀形貌觀察、掃描掃描電子顯微鏡、X射線衍射及電化學測試,對耐候冷鐓鋼在模擬海洋大氣環境中的腐蝕行為進行了研究。圖18顯示,在模擬海洋大氣腐蝕環境下,耐候鋼表面銹層隨腐蝕時間由淺黃色依次向棕黃色、紅棕色轉變;銹層截面形貌從薄而疏松、不連續演變為厚而致密、均勻分布;銹層微觀形貌顯示,表面銹層存在相對平滑、不規則圓形花狀結構、閉環的環形巢結構、毛絨狀結構等4個演變狀態,但致密的毛絨狀結構銹層對基體的保護能力明顯提高;腐蝕產物主要由Fe3O4、γ-FeOOH、α-FeOOH組成,腐蝕初期主要是致密的Fe3O4,腐蝕中期開始形成γ-FeOOH,腐蝕后期γ-FeOOH逐漸溶解并還原形成穩定的α-FeOOH,對基體提供良好的保護作用;電化學分析顯示,腐蝕24~72 h,耐候鋼的陰極電流密度呈線性增大,且趨于穩定。耐候鋼的腐蝕深度損失與腐蝕時間呈冪函數關系;受腐蝕過程不同腐蝕產物的影響,腐蝕速率呈現先增長后下降的變化規律。 張宇等考慮免涂裝耐候鋼橋面臨著腐蝕環境的巨大挑戰,基于ISO規范對環境腐蝕的分類,回顧和討論金屬材料和耐候鋼腐蝕評價方法。依據我國《橋梁用結構鋼》和《耐候結構鋼》的規定,采用指數線性模型得到《橋梁用結構鋼》規定耐候鋼腐蝕上限模型。對比結果表明,我國耐候鋼具有較好的抗腐蝕性能,并且在各環境腐蝕等級中,抗腐蝕性能與歐洲耐候鋼基本相當。通過耐候鋼腐蝕試驗數據驗證了腐蝕模型的準確性,表明基于耐候鋼腐蝕上限模型可作為免涂裝耐候鋼橋梁的設計依據。結合《鐵路橋梁鋼結構設計規范》與《公路鋼結構橋梁設計規范》,提出基于腐蝕量模型的免涂裝耐候鋼橋梁強度和穩定設計方法,為我國免涂裝耐候鋼橋梁設計提供理論依據。為簡化設計,還提出容許腐蝕厚度設計方法用于超低,低和中度腐蝕環境,其中,超低和低腐蝕環境容許腐蝕厚度取500 μm,中度腐蝕環境容許腐蝕厚度取1000 μm。 朱桂琴以Q500Qenh鋼為基材,利用二氧化碳氣體保護焊方法,制作了兩種含不同耐候元素的焊接接頭試樣(圖19)。利用干濕交替加速腐蝕試驗考察了兩種試樣的耐蝕性及其元素富集情況。結果表明,相比于2號焊接接頭試樣,耐候元素含量較多的1號焊接接頭試樣經腐蝕后,銹層更加致密、穩定,且耐候元素出現明顯富集,腐蝕率與腐蝕深度均較低。 李偉偉等采用中性鹽霧加速腐蝕試驗,使試件處于較高濃度的氯離子環境中,模擬鋼材在海洋大氣環境中的長期腐蝕行為,對Q355NH,Q355鋼的腐蝕形貌,以及腐蝕后的力學性能進行了研究分析。得出了Q355NH鋼和Q355鋼的均勻腐蝕厚度、蝕坑深度與質量損失率的冪函數定量關系。相比Q355鋼,Q355NH鋼在腐蝕早期的腐蝕速率更大,但在長期腐蝕作用下,Q355NH鋼的耐腐蝕性更好。 圖21 未穩定化處理和穩定化處理的Q420NH鋼的銹層截面元素分布圖
防腐技術 橋梁中鋼結構的防腐技術涉及多個層面,包括使用專門的防腐涂料來隔絕腐蝕介質、采用陰極保護等電化學方法來減緩腐蝕、依據環境特點設計合理的涂層體系、進行嚴格的表面處理以增強涂層附著力、執行定期的檢查和必要的維護工作、控制腐蝕環境的溫濕度、應用耐候鋼以提高耐大氣腐蝕性能、遵循防腐涂裝養護技術指南和標準,以及在設計和施工階段就綜合考慮防腐措施。這些技術的綜合應用有助于延長橋梁鋼結構的使用壽命,確保橋梁的安全性和耐久性。 任玉苓等采用平板、切口、劃線、杯突、折彎等不同制樣方式,對不同種類鋅鋁鎂鍍層彩涂鋼板在連續鹽霧試驗中的涂層起泡等級、切口和劃線擴蝕寬度、不同試樣部位的紅銹出現時間等進行檢測,獲得了不同鋅鋁鎂鍍層種類、不同鍍層質量、不同涂層種類、不同加工方式彩涂鋼板的耐鹽霧性能。同時與鋅鋁鎂鍍層鹽霧試驗數據進行對比,找到了涂鍍層鋼板耐鹽霧性能的規律,為評估不同鍍層彩涂產品耐蝕性能奠定基礎。 張澤靈等采用基于硫氰酸銨溶液的試驗和電化學方法,研究了強度等級和表面質量對熱鍍鋼絲應力腐蝕敏感性的影響,并分析了應力腐蝕斷口形貌。圖22表明,1860 MPa級和2060 MPa級橋梁纜索用熱鍍鋼絲的應力腐蝕斷裂時間相當,但2060 MPa級鋼絲的應力腐蝕時間更加離散;鋼絲表面越粗糙,應力腐蝕敏感性越強;2060 MPa級鋼絲表面采用800目砂紙打磨后,應力腐蝕斷裂時間明顯縮短。應力腐蝕斷口形貌分為裂紋源區、裂紋擴展區和瞬斷區,裂紋主要起源于表面。 圖22 橋梁纜索用熱鍍鋼絲的應力腐蝕開裂斷口形貌 盧道勝等使用3種鈍化工藝對9Cr1Mo鋼進行表面鈍化處理,通過電化學測試、FeCl3腐蝕試驗、鹽霧腐蝕試驗、高溫高壓腐蝕試驗測試3鈍化工藝對9Cr1Mo合金耐腐蝕性能的提升。結果表明,通過鈍化處理,在9Cr1Mo鋼表面形成保護性好的鈍化膜,可有效降低鋼基體的腐蝕速率使得耐電化學腐蝕性能和耐鹽霧腐蝕性能顯著提升。在高溫高壓腐蝕試驗中未鈍化和鈍化后的9Cr1Mo鋼的腐蝕過程由CO2和H2S腐蝕共同控制,鈍化處理有利于鋼基體發生更為均勻的腐蝕,對9Cr1Mo鋼表面腐蝕膜的形成過程產生一定影響,但不會改變其腐蝕機理。 徐攀等采用電鍍鋅和熱鍍鋅鋁對Ф4.3 mm SWRS82B鋼絲進行表面處理,對電鍍鋅和熱鍍鋅鋁鋼絲在0.1 mol/L HCl溶液中進行耐腐蝕性能研究,對腐蝕后的形貌進行觀察并分析腐蝕機理。結果表明,電鍍鋅后鋼絲表面粗糙度Ra=1.024 μm,熱鍍鋅鋁后鋼絲表面粗糙度Ra=0.637 μm,熱鍍鋅鋁試樣表面粗糙度明顯小于電鍍鋅試樣;電鍍鋅的鋅層厚度約為15 μm,擴散層為35 μm,熱鍍鋅鋁合金的鍍鋅層約為24 μm,擴散層為50 μm,熱鍍鋅鋁試樣的耐腐蝕性能明顯優于電鍍鋅試樣。 王海洋等為提高大橋主纜防腐效果,開發研制了S形精密熱鍍鋅鋼絲。選用可加工性強的低碳鋼盤條,對酸洗、開坯、連續冷軋、熱鍍、精整等工序進行優化,完成產品尺寸精度和表面質量的控制(圖23)。試驗結果滿足預期的性能指標要求:S形熱鍍鋅鋼絲抗拉強度650~700 Mpa,扭轉20次以上,彎曲8~12次,鋅層面質量300~330 g/m2,纏繞試驗8圈不斷,鋼絲表面鋅鍍層平整光滑,纏絲應用良好。 圖24 溫州東歐大橋吊桿防水套包覆防腐方案效果 圖25 舟山官山大橋吊桿防水套包覆防腐方案效果 姚迪等依托某海港LNG碼頭工程,從分析海水腐蝕環境出發,結合碼頭結構耐久性要求,介紹了鋼管樁犧牲陽極陰極保護系統(圖28)的設計過程、犧牲陽極材料及類型的選取、各參數的計算方法、施工工藝流程、焊接施工質量檢驗及系統保護效果檢測。闡述了通過減小犧牲陽極與被保護鋼結構之間的距離、適當增加小規格犧牲陽極重量的設計優化方式,達到滿足設計年限要求、節省工程投資、方便安全施工的目的。 圖29 不同干濕態時間比下犧牲陽極的活化溶解形貌
結論與展望 隨著橋梁鋼結構在各種環境條件下的廣泛應用,其面臨的腐蝕問題日益突出,對橋梁的安全運營和耐久性構成了嚴重威脅。腐蝕環境顯著影響橋梁鋼結構的疲勞壽命,而腐蝕與疲勞的耦合作用會進一步加速結構損傷的進程。為了應對這些挑戰,研究人員已經開展了多方面的研究工作,包括腐蝕疲勞損傷機理的深入分析、腐蝕監測技術的創新、以及耐候鋼和其他耐腐蝕材料的開發與應用等。此外,智能監測技術的應用、基于數據驅動的維護策略的提出,以及綜合防腐措施的實施,都表明了橋梁鋼結構防腐技術正朝著更加智能化、系統化和環保化的方向發展。對2023年橋梁鋼結構腐蝕進展總結與展望如下: (1)研究發現腐蝕環境對鋼橋的疲勞壽命和性能有顯著影響,腐蝕疲勞耦合作用下,結構的損傷發展速率加快,疲勞壽命降低。研究者們通過建立模型、進行實驗和理論分析,提出了不同的預測和評估方法,以提高鋼橋的耐腐蝕性能和延長其使用壽命。未來的研究可進一步探索和完善腐蝕疲勞損傷的預測模型,以更準確地預測鋼橋在不同環境和載荷條件下的使用壽命。此外考慮到實際應用中腐蝕環境的復雜性,未來的研究還應包括多因素耦合作用下的腐蝕疲勞行為,如溫度、濕度、鹽分等環境因素與多載荷的交互影響。 (2)橋梁的腐蝕監測技術主要是采用基于計算機視覺和機器學習的損傷識別方法,以及基于傳感器的無損檢測技術。利用無人機技術結合三維模型自動規劃巡檢路徑,并通過深度學習模型來識別橋梁主纜的病害。此外,尤其是在光照條件不佳的情況下,可以通過自適應光照預處理結合深度學習的方法可以改善腐蝕區域檢測的難題。結合無人機采集的高清圖像和深度學習網絡,能夠有效地建立鋼橋病害圖像庫,實現病害的自動識別。在無損檢測方面,MsS超聲導波檢測系統能夠快速檢測橋梁纜索的內部損傷,具有較高的檢測靈敏度和效率。在未來應該繼續優化深度學習和機器學習算法,以提高病害識別的準確性;結合物聯網(IoT)技術,實現橋梁狀態的實時監測和數據收集,為橋梁管理和維護提供更準確的信息;在數據分析方面,開發更復雜的數據處理和模式識別算法,以便從大量監測數據中提取有用信息,預測橋梁的腐蝕趨勢和潛在風險。 (3)耐候鋼的研究集中在理解其腐蝕行為、銹層結構與性能、表面處理技術、焊接技術、腐蝕疲勞性能,以及在設計方法與規范、免涂裝橋梁設計、全壽命周期評估、新材料開發和智能監測等方面的應用。未來應該給予更多關注在耐候鋼性能提升和在復雜環境下耐候鋼的開發。并進一步對鋼材中添加金屬元素含量的改良,逐步提高耐候鋼的防腐性能指標。 (4)橋梁鋼結構的主要防腐方法包括使用防腐涂料隔絕腐蝕介質、陰極保護等電化學方法減緩腐蝕、設計合理的涂層體系、進行表面處理以增強涂層附著力、執行定期檢查和維護、控制腐蝕環境的溫濕度、遵循防腐涂裝養護技術指南和標準,以及在設計和施工階段綜合考慮防腐措施。在未來應該深入探索和開發先進的防腐材料與技術,以實現更高效和持久的腐蝕防護效果;其次,開發和優化新型環保防腐涂料和合金材料,以提高橋梁鋼構件的耐久性;此外,研究應更多地考慮耐久性設計,通過標準化施工工藝和高質量的表面處理技術來增強涂層的附著力和防腐性能;最后,探索不同環境條件下的防腐技術,并開發適應這些環境的高性能防腐系統。
免責聲明:本網站所轉載的文字、圖片與視頻資料版權歸原創作者所有,如果涉及侵權,請第一時間聯系本網刪除。
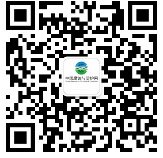
官方微信
《腐蝕與防護網電子期刊》征訂啟事
- 投稿聯系:編輯部
- 電話:010-62316606
- 郵箱:fsfhzy666@163.com
- 腐蝕與防護網官方QQ群:140808414