鋁合金中鉻的質量分數一般不超過0.35%。如超過該成分范圍,則會發生包晶反應,形成極粗大的初生相 Al7Cr。商用合金中的合金元素和雜質元素可能會降低鉻在鋁中的固溶度,使Al7Cr初生相在包晶反應中形成。鋁合金中鉻的上限值取決于其他合金和雜質元素的數量和性質。如鑄造鋁合金含有過量的鉻,則會因其在包晶反應過程中停留而產生殘存的相。 在AI-Mg、AI-Mg-Si和Al-Mg-Zn合金體系的許多合金中,鉻是常用的合金元素。鉻形成細小顆粒相,在不可熱處理強化鋁合金中,有利于細化晶粒,提高合金的強度;在可熱處理強化鋁合金中,可控制晶粒尺寸和再結晶程度。由于鉻的擴散速度慢,在變形鋁合金中形成了細小彌散相。對5xxx系列合金,在(鑄)鍛錠預熱過程中形成面心立方的 AlsMg;Cr彌散相;在7xxx合金中,彌散相的成分則更接近于Al1MgzCr。這些細小彌散相抑制了 A1-Mg合金中的形核和晶粒長大,并阻礙了Al-Mg-Si合金和Al-Zn合金在熱加工或熱處理過程中發生再結晶。在可熱處理強化鋁合金中,鉻的主要缺點是增加了強化相在已存在的鉻顆粒處的析出傾向,由此增加了合金的淬火敏感性。 銅在鋁中具有相當大的固溶度,具有明顯的析出強化作用,因此,銅是鋁合金中最重要的合金元素之一。二元鋁-銅合金體系是典型的析出強化例子,是最受關注的研究系統之一。盡管如此,實際上很少看到商用二元鋁-銅合金。大多數商用鋁-銅合金都含有其他合金元素。通常,鋁-銅合金體系含有銅(質量分數為2%~10%)和其他合金元素,包括2xxx變形鋁合金系列和2xx.x鑄造鋁合金系列。此外,許多其他可熱處理強化鋁合金中也含有銅。根據合金中其他成分的不同,銅的質量分數為4%~6%時對鋁合金的強化效果達到最大。不同熱處理條件下鋁-銅合金薄板的性能如圖 1所示。 圖1 高純度變形鋁-銅合金的拉伸性能 注:薄板試樣寬13mm(0.5in)寬,厚1.59mm(0.06in)。0-退火;W一固溶水淬后立即測試;T4-固溶水淬后在室溫下時效;T6-在 T4后高溫時效。 與其他合金體系相比,對二元鋁-銅合金的時效特性已進行了較為詳細的研究,但很少有商用的二元鋁-銅合金。大多數鋁-銅合金都含有鎂等其他合金元素。在鋁-銅合金中加入鎂的主要優點是,通過固溶淬火能進一步提高合金的強度。如對某些變形鋁合金進行室溫時效,在提高合金強度的同時還能提高其塑性。如對合金進行人工時效,則可獲得更高的強度,但塑性會有所降低。在鑄造和變形鋁合金中,添加質量分數約為0.05%的鎂,能有效提高合金的時效強化性能。 在精煉鐵釩土和熔煉生成氧化鋁后,鐵作為雜質元素殘存于鋁合金中,因此,實際上所有鋁合金中都會殘存一定的鐵元素。鋁-鐵二元合金體系的共晶成分為w(Fe)=1.8%,在共晶溫度655℃(1211℉)下,鐵在鋁中最大的固溶度為0.05%。盡管可能存在其他相,在固溶度極限溫度出現的平衡相是Al3Fe(θ)。根據凝固速率和存在錳等其他合金元素,合金中可能出現亞穩相。如采用適中的速率淬火冷卻,則出現FeAl6相;快速火冷卻時出現 Fe2Al9相。鋁中鐵的固溶度非常有限,因此常用作導電材料。固溶的鐵使鋁的強度略有提高,在溫度略有升高的條件下,將具有更好的抗蠕變性能。雖然鋁合金中存在少量的鐵可減少壓鑄過程中出現的焊合危害,但通常在鋁-硅鑄造合金中,鐵會形成粗大的富鐵相,因此通常不希望鋁-硅合金中含有鐵。 由于鋁合金中總是會殘存少量的鐵,鐵在鋁中的影響應根據三元或四元相圖來分析。隨著添加其他合金元素,鐵在鋁合金中的固溶度會進一步降低在大多數鋁合金中,鐵的最大固溶度可降低到w(Fe)=0.01%或以下。由于鐵和硅是工業純鋁中常見的雜質元素,因此,人們非常注重對A1-Fe-Si三元相圖的富鋁角的研究。在硅含量低的情況下幾乎所有的鐵元素都形成 Al3Fe 相。 鋁-鎂合金是變形5xxx系列和鑄造5xxx系列中,不可熱處理強化鋁合金。合金中的鎂能提高固溶強化效果,而不會過度降低合金的塑性。鋁-鎂合金具有優異的固溶強化和耐蝕綜合性能,通過形變強化,變形鋁合金的強度得到了進一步提高。目前,5xxx變形鋁合金系列中鎂的質量分數不超過5.5%,而鑄造鋁合金中鎂的質量分數為4%~10%。當鑄造鋁合金中鎂的質量分數達到10%時,在室溫下會形成第二相。當鑄造鋁合金中鎂的質量分數小于7%時,在室溫下合金是穩定的,在高于室溫時則是不穩定的。 為控制晶粒或亞晶結構,以及殘存鐵和硅雜質元素形成的金屬間化合物顆粒,通常在鋁-鎂合金中添加少量鉻、錳、鋯等過渡族元素。雖然鎂在鋁中的最大固溶度約為17%,但之前的冷加工工序會加速 Mg2Al;相的析出,因此,目前變形鋁合金中鎂的質量分數一般不超過5.5%。相對于鋁-鎂合金基體而言,這種析出相呈高度陽極電位,并沿晶界呈連續網狀分布,由此在長期室溫環境或短時間高溫環境下,合金具有很高的應力腐蝕開裂(SCC)敏感性。在正常情況下,由于5182、5083、5086、5154、5356和5456合金中鎂的質量分數約為3%,因此易受到應力腐蝕開裂的影響。一般來說,對于經嚴重冷變形的合金,大多數有害析出相是在室溫下長年累月形成的,或者持續暴露在65~180℃(150~350℉)的溫度下而形成。在較高的溫度下析出相會發生粗化,在晶界呈不連續析出,此時會降低或去除應力腐蝕開裂。 在鋁-鎂合金中添加錳,可提高合金強度。添加錳主要有兩個優點:第一,促進鎂析出相在組織中更加均勻地析出;第二,在達到合金所要求強度的條件下,添加錳可降低合金中鎂的含量,從而確保合金的穩定性更高,使變形鋁合金具有更高的強度和耐蝕性。在鑄造鋁-鎂合金中添加質量分數為0.75%的錳,對合金耐蝕性的影響很小,但提高了合金的硬度且降低了塑性。 硅和鐵一樣,是工業鋁合金中常見的雜質元素。電解鋁中雜質硅的質量分數為0.01%~0.15%,當鋁中存在鐵時,硅在鋁中的固溶度將極大地下降。隨著硅含量的增加,工業鋁中先形成六角晶系的α相(Al8Fe2Si),然后形成單斜晶系的β相(以化學計量的 Al5FeSi或 Al9Fe2Si2)。 作為合金元素,硅加入鋁或鋁合金中,能顯著改善合金的鑄造性能。不含銅的鋁-硅合金具有良好的鑄造性能和耐蝕性。二元鋁-硅合金體系是一個簡單的共晶體系,其共晶點硅的質量分數為12.6%。在共晶溫度577℃(1071℉),硅在鋁中的最大固溶度為w(Si)=1.65%。在很大程度上,硅提高了鋁合金的鑄造性能和流動性能。因此,合金元素硅在4xxx鋁合金釬焊薄板和3xx.x4xx.x鑄造鋁合金中應用廣泛。現已有硅的質量分數低至2%的鑄造鋁合金,但通常鑄造鋁合金中硅的質量分數在5%~13%范圍內,有時硅的質量分數高達 20%,為過共晶合金。 含銅量高的鋁-銅合金[w(Cu)=7%~8%],是最早的常用鑄造鋁合金,現已完全被Al-Si-Cu/Mg(3xx.x)合金所取代。Al-Cu-Si合金系列是使用最廣泛的鑄造鋁合金之一,不同合金牌號中銅和硅兩種元素的含量在很大范圍內變化,其中一部分合金中銅占主導地位,而另一部分合金中硅為主要合金成分。在這類合金中,銅有助于提高合金的強度,硅則可提高合金的鑄造性能和降低其熱脆性。在Al-Cu-Si合金系列中,銅的質量分數達到3%~4%時為可熱處理強化鋁合金,通常這部分合金中還含有一定量的鎂,以進一步提高合金的熱處理強化效果。 多年來鋁-鋅合金早已為人所知,但是鋁-鋅鑄造鋁合金的熱裂問題,以及變形鋁合金的應力腐蝕開裂敏感性問題限制了它們的使用。鋅的固溶強化和形變強化作用很小,因此,單獨在鋁中添加鋅沒有明顯的作用。然而,在添加銅和/或鎂的同時添加鋅以及少量的鉻,則鋁合金可以進行熱處理強化或自然時效。 在鋁-鋅合金,特別是在w(Zn)=3%~7.5%的鋁合金中添加鎂,可以有效提高該系列合金的強度。合金中的鎂和鋅形成MgZn2,其熱處理強化效果明顯大于鋁-鋅二元合金體系。Al-Zn-Mg合金體系中的析出相是7xxx變形鋁合金系列和7xx.x鑄造鋁合金系列的強化基礎。在商用Al-Zn-Mg合金的共晶分解過程中,可以形成六方晶系的MgZn2相和體心立方的Al2Mg3Zn3相。根據合金中的鋅鎂比,不含銅的鋁合金通過析出MgZn2或Al2Mg3Zn3亞穩態過渡相來實現強化。在Al-Zn-Mg-Cu合金體系中,銅和鋁置換了MgZn2相中的鋅,形成了Mg(Zn,Cu,AI)相。在這類合金中也可以通過共晶分解和固相析出形成Al2CuMg顆粒。 在A1-Zn-Mg合金體系中添加銅和少量且重要的鉻和錳,可得到商用高強度鋁合金。在該合金體系中,銅的作用是提高固溶體的過飽和度,在時效時提高CuMgAl2相的形核速率,從而提高時效速率鋅和鎂的作用是控制時效進程。在熱處理過程中銅也會提高淬火敏感度。一般來說,銅降低了Al-Zn-Mg合金的耐蝕性,但能提高合金抗應力腐蝕的能力。鉻、鋯等附加合金元素對提高合金的力學性能和耐蝕性有顯著的影響。 鋰可以降低鋁合金的密度,提高其模量。在鋁-鋰二元合金中,鋰以亞穩態Al3Li相析出。在Al-Cu-Li合金中,形成了大量的 Al-Cu-Li 相。與其他合金元素相比,鋰的成本較高,因此迄今為止,鋁-鋰合金主要在航天航空和軍工等領域得到了應用。 鈧是鋁合金中新的合金元素。鋁-鈧合金在凝固或過飽和固溶體分解過程中,形成立方結構的Al3Sc相,由此使鋁-鈧合金具有獨特的性能組合。Al3Sc立方相屬Ll2晶體結構,晶格參數與鋁的參數略有不同,比任何其他平衡相與基體的匹配都要好,與鋁基體保持共格。此外,Al3Sc相能有效地阻礙晶界遷移和再結晶過程。 由于鈧的價格非常昂貴,現在的生產原料基本來源于蘇聯的Sc203儲備,而且該資源還在不斷減少,因此僅限應用于特定的場合。目前,絕大多數鈧的生產都來自于稀土生產過程中的副產品,鈧的主要生產國是中國、俄羅斯、烏克蘭和哈薩克斯坦。由于缺乏可靠性、安全性和穩定的長期生產,因此限制了鈧在工業中的廣泛應用。 同時添加鈧和鋯,可以將合金中鈧的質量分數減少到0.15%~0.20%,由此可在提高力學性能、服役性能和熱穩定性的情況下,降低合金的成本。在這種情況下,形成了致密晶體結構立方相(Al3Sc平衡相和亞穩態立方Al3Zr相),在300~400℃(570~750℉)范圍內,這兩種析出相都為共格析出。 鋁合金材料的研發主要是圍繞提高材料的強度、塑性、韌性、耐蝕性以及疲勞性能等綜合性能來開展的,而合金的性能又是由其組織決定的,熱處理是鋁合金性能優化的關鍵手段,通過控制溫度、時間和冷卻速度等工藝參數,可以顯著改變合金的內部微觀結構,從而增強其強度、硬度和耐腐蝕性等性能。熱處理不僅影響合金的晶粒大小和析出相的分布,還能促使強化相的形成和轉變,為不同使用環境和力學要求提供精準的性能調控。基于此,針對鋁合金的強化方法,如固溶強化、時效強化和細晶強化等,成為提升合金性能的核心手段。 鋁合金在常溫和中等應力作用下產生塑性變形,主要由位錯滑移所致,而高溫和低應力作用下產生塑性變形則由位錯蠕動和擴散流變產生。總的來說,不管工作溫度高低,合金抵抗變形能力主要由位錯運動難易所決定。因而,把增加鋁合金對位錯運動的抗力稱為鋁合金強化。 鋁合金的強化及其分類方法很多,一般將其分為加工硬化和合金化強化兩大類。鋁合金強化方法可細分為加工硬化、固溶強化、異相強化、彌散強化、沉淀強化、晶界強化和復合強化七類。在實際應用過程中往往是幾種強化方法同時起作用。 通過塑性變形(軋制、擠壓、鍛造、拉伸等)使合金獲得高強度的方法,稱為加工硬化。塑性變形時增加位錯密度是合金加工硬化的本質。據統計,金屬強烈變形后,位錯密度可由106根/cm2增至1012根/cm2以上。因為合金中位錯密度越大,繼續變形時位錯在滑移過程中相互交割的機會越多,相互間的阻力也越大,因而變形抗力也越大,合金即被強化。 金屬材料加工強化的原因是:金屬變形時產生了位錯不均勻分布,先是較紛亂地成群糾纏,形成位錯纏結,隨變形量增大和變形溫度升高,由散亂分布位錯纏結轉變為胞狀亞結構組織,這時變形晶粒由許多稱為“胞”的小單元組成;高密度位錯纏結集中在胞周圍形成包壁,胞內則位錯密度甚低。這些胞狀結構阻礙位錯運動,使不能運動的位錯數量劇增,以至需要更大的力才能使位錯克服障礙而運動。變形越大,亞結構組織越細小,抵抗繼續變形的能力越大,加工硬化效果越明顯,強度越高。由于產生亞結構,故也稱亞結構強化。 加工強化的程度因變形率、變形溫度及合金本身的性質不同而異。同一種合金材料在同一溫度下冷變形時,變形率越大則強度越高,但塑性隨變形率的增加而降低。合金變形條件不同,位錯分布亦有所不同。當變形溫度較低(如冷軋)時,位錯活動性較差,變形后位錯大多呈紊亂無規則分布,形成位錯纏結,這時合金強化效果好,但塑性也強烈降低。當變形溫度較高時,位錯活動性較大,并進行交滑移,位錯可局部集聚、糾結、形成位錯團,出現亞結構及其強化,屆時強化效果不及冷變形,但塑性損失較少。 加工硬化或亞結構強化在常溫時是十分有效的強化方法,適用于工業純鋁、固溶體型合金和熱處理不可強化的多相鋁合金,但在高溫時通常因回復和再結晶而對強度的貢獻顯著變小。 某些鋁合金冷變形時能形成較好的織構而在一定方向上強化,稱為織構強化。 合金元素固溶到基體金屬(溶劑)中形成固溶體時,合金的強度、硬度一般都會得到提高,稱為固溶強化。所有可溶性合金化組元甚至雜質都能產生固溶強化。特別可貴的是,對合金進行固溶強化時,在強度、硬度得到提高的同時,塑性還能保持在良好的水平上,但僅用這一種方法不能獲得特別高的強度。 合金元素溶入基體金屬后,使基體金屬的位錯密度增大,同時晶格發生畸變。畸變所產生的應力場與位錯周圍的彈性應力場交互作用,使合金元素的原子聚集到位錯線附近,形成所謂“氣團”,位錯要運動就必須克服氣團的釘扎作用,帶著氣團一起移動,或者從氣團中掙脫出來,因而需要更大的切應力。另外,合金元素的原子還會改變固溶體的彈性系數、擴散系數、內聚力和原子的排列缺陷,使位錯線變彎,位錯運動阻力增大,包括位錯與溶質原子間的長程交互作用和短程交互作用,從而使材料得到強化。 固溶強化作用大小取決于溶質原子濃度、原子相對尺寸、固溶體類型、電子因素和彈性模量。一般來說,溶質原子濃度越高,強化效果越大;原子尺寸差別越大,對置換固溶體的強化效果亦可能越大;溶質原子與鋁原子的價電子數相差越大,固溶強化作用亦越大;彈性模量大小的差異度越大,往往強化效果越好。 在采用固溶強化的合金化時,要挑選那些強化效果高的元素作為合金元素。但更重要的是要選那些在基體金屬中固溶度大的元素作為合金元素,因為固溶體的強化效果隨固溶元素含量的增大而增加。只有那些在基體金屬中固溶度大的元素才能大量加入。例如,銅、鎂是鋁合金的主要合金元素;鋁、鋅是鎂合金的主要合金元素,都是因為這些元素在基體金屬中的固溶度較大的緣故。 進行固溶強化時,往往采用多元少量的復雜合金化原則(即多種合金元素同時加入,但每種元素加入量少),使固溶體的成分復雜化,這樣可以使固溶體的強化效果更高,并能保持到較高的溫度。 圖3 原子尺寸對強化的影響 圖4 固溶體中鎂對退火鋁-鎂合金拉伸性能的影響 過量的合金元素加入到基體金屬中去,一部分溶入固溶體,超過極限溶解度的部分不能溶入,形成過剩的第二相,簡稱過剩相。過剩相對合金一般都有強化作用,其強化效果與過剩相本身的性能有關,過剩相的強度、硬度越高,強化效果越大。但硬脆的過剩相含量超過一定限度后,合金變脆,力學性能反而降低。此外,強化效果還與過剩相的形態、大小、數量和分布有關。第二相呈等軸狀、細小和均勻分布時,強化效果最好。第二相很大、沿晶界分布或呈針狀,特別是呈粗大針狀時,合金變脆,合金塑性損失大,而且強度也不高,常溫下不宜大量采用過剩強化,但高溫下的使用效果可以很好。另外,強化效果還與基體相與過剩相之間的界面有關。 過剩相強化與沉淀強化有相似之處,只不過沉淀強化時,強化相極為細小,彌散度大,在光學顯微鏡下觀察不到;而在利用過剩相強化合金時,強化相粗大,用光學顯微鏡的低倍即能清楚看到。過剩和強化在鋁合金中應用廣泛,幾乎所有在退火狀態使用的兩相合金都應用了過剩相強化。或者更準確地說,是固溶強化與過剩相強化的聯合應用。過剩相強化有時亦稱復相強化或異相強化。 非共格硬顆粒彌散物對鋁合金的強化稱彌散強化。為取得好的強化效果,要求彌散物在鋁基體中有低的溶解度和擴散速率、高硬度(不可變形)和小的顆粒(0.1μm左右)。這種彌散物可用粉末冶金法制取或由高溫析出獲得,產生粉末冶金強化和高溫析出強化。 由彌散質點引起的強化包括兩個方面:彌散質點阻礙位錯運動的直接作用,彌散質點為不可變形質點,位錯運動受阻后,必須繞越通過質點,產生強化,彌散物越密集,強化效果就越好;彌散質點影響最終熱處理時半成品的再結晶過程,部分或完全抑制再結晶(對彌散粒子的大小和其間距有一定要求),使強度提高。彌散強化對常溫或高溫下均適用,特別是粉末冶金法生產的燒結鋁合金,工作溫度可達350℃。彌散強化型合金的應變不太均勻,在強度提高的同時,塑性損失要比固溶強化或沉淀強化的大。熔鑄冶金鋁合金中采用高溫處理,獲得彌散質點使合金強化,越來越得到人們關注。在鋁合金中添加非常低的溶解度和擴散速率的過渡族金屬和稀土金屬元素,如含Mn、Cr、Zr、Sc、Ti、V等,鑄造時快速冷卻,使這些元素保留在α(Al)固溶體中,隨后高溫加熱析出非常穩定的0.5μm以下非共格第二相彌散粒子,即第二類質點。其顯微硬度可大于5000MPa,使合金獲得彌散強化效果。 這些質點一旦析出,很難繼續溶解或聚集,故有較大的彌散強化效果。以Al-Mg-Si系合金為例,加入不同量的過渡元素可使抗拉強度增加6%~29%,屈服強度提高最多,達52%。此外,彌散質點阻止再結晶即提高再結晶溫度,使冷作硬化效果最大限度保留,尤以Zr和Sc提高Al的再結晶溫度最顯著。 從過飽和固溶體中析出穩定的第二相,形成溶質原子富集亞穩區的過渡相的過程,稱為沉淀。凡有固溶度變化的合金從單相區進入兩相區時都會發生沉淀。鋁合金固溶處理時獲得過飽和固溶體,再在一定溫度下加熱,發生沉淀生成共格的亞穩相質點,這一過程稱為時效。由沉淀或時效引起的強化稱沉淀強化或時效強化。第二相的沉淀過程也稱析出,其強化稱析出強化。鋁合金時效析出的質點一般為G.P區,共格或半共格過渡相,尺寸為0.001~0.1μm,屬第三類質點。這些軟質點有三種強化作用即應變強化、彌散強化和化學強化。時效強化的質點在基體中均勻分布,使變形趨于均勻,因而時效強化引起塑性損失都比加工硬化、彌散強化和異相強化的要小。通過沉淀強化,合金的強度可以提高百分之幾十至幾百倍。因此,沉淀強化是Ag、Mg、Al、Cu等有色金屬材料常用的有效強化手段。 沉淀強化的效果取決于合金的成分、淬火后固溶體的過飽和度、強化相的特性、分布及彌散度以及熱處理制度等因素。強化效果最好的合金位于極限溶解度成分,在此成分下可獲得最大的沉淀相體積分數。 鋁合金晶粒細化,晶界增多,由于晶界運動的阻力大于晶內且相鄰晶粒不同取向使晶粒內滑移相互干涉而受阻,變形抗力增加,即合金強化。晶粒細化可以提高材料在室溫下的強度、塑性和韌性,是金屬材料最常用的強韌化方法之一。晶界上原子排列錯誤,雜志腹肌 晶界上原子排列錯亂,雜質富集,并有大量的位錯、孔洞等缺陷,而且晶界兩側的晶粒位向不同,所有這些都阻礙位錯從一個晶粒向另一個晶粒的運動。晶粒越細,單位體積內的晶界面積就越大,對位錯運動的阻力也越大,因而合金的強度越高。晶界自身強度取決于合金元素在晶界處的存在形式和分布形態,化合物的優于單質原子吸附的,化合物為不連續、細小彌散點狀時,晶界強化效果最好。晶界強化對合金的塑性損失較少,常溫下強化效果好,但高溫下不宜采用晶界強化,因高溫下晶界滑移為重要形變方式,使合金趨向沿晶界斷裂。 鋁合金的晶粒細化的方法主要有三種。 (1)細化鑄造組織晶粒 熔鑄時采用變質處理,在熔體中加入適當的難溶質點(或與基體金屬能形成難熔化合物質點的元素)作為非自發晶核,由于晶核數目大量增加,熔體即結晶為細晶粒。例如,添加Ti、Ti-B、Zr、Sc、V等都有很好的細化晶粒的作用;另外,在熔體中加入微量的,對初生晶體有化學作用從而改變其結晶性能的物質,可以使初生晶體的形狀改變,如Al-Si合金的Na變質處理就是一個很好的例子。用變質處理方法,不僅能細化初生晶粒,而且能細化共晶體和粗大的過剩相,或改變它們的形狀。此外,在熔鑄時,采取增加一級優質廢料比例、避免熔體過熱、攪動、降低鑄造溫度、增大冷卻速度、改進鑄造工具等措施,也可以(或有利于)獲得細晶粒鑄錠。 (2)控制彌散相細化再結晶晶粒 抑制再結晶的彌散相MnAl?、CrAl?、TiAl?、ScAl?、VAl?和ZrAl?質點,在顯微組織中它們有許多都是釘扎在晶界上,使晶界遷移困難,這不僅阻礙了再結晶,而且增加了晶界的界面強度,它們可以明顯細化再結晶晶粒。這些彌散相的大小和分布,是影響細化效果的主要因素,越細小越彌散,細化效果越好。彌散相的大小和分布主要受高溫熱處理和熱加工的影響。獲得細小彌散相的方法主要有:在均勻化時先進行低溫預處理形核,然后在進行正常熱處理;對含Sc的合金采用低溫均勻化處理;對含Mn、Cr的合金采用較高溫度均勻化處理;還可以采用熱機械加工熱處理的方法獲得細小彌散相,即對熱加工后的鋁合金進行高溫預處理,然后再進行正常的熱加工,如7175-T74合金鍛件就采用過這種工藝;此外,也可以通過熱加工的加熱過程和固溶處理過程來調控彌散相。 (3)采用變形及再結晶方法細化再結晶晶粒 采用強冷變形后進行再結晶,可以獲得較細的晶粒組織;采用中溫加工可以獲得含有大量亞結構的組織;采用適當的熱擠壓并與合理的再結晶熱處理相結合,可以獲得含有大量亞結構的組織,得到良好的擠壓效應;在再結晶處理時,采用高溫短時,或多次高溫短時固溶處理均可以獲得細小的晶粒組織。 采用高強度的粉、絲和片狀材料和壓、焊、噴涂、溶浸等方法與鋁基體復合,使基體獲得高的強度,稱為復合強化。按復合材料形狀,復合強化可分為纖維強化型、粒子強化型和包覆材料三種。晶須和連續纖維常作纖維強化原料,粒子強化型有粉末冶金和混合鑄造兩類。對燒結鋁合金屬粒子復合強化合金,多數學者認為是彌散強化的典型合金。復合強化的機理與異相強化相近。這種強化在高溫下強化效果最佳,在常溫下也可顯著強化,但塑性損失大。可以用作增強纖維的材料有碳纖維、硼纖維、難熔化合物(Al3O2、SiC、BN、TiB2等)纖維和難熔金屬(W、Mo、Be等)細絲等。這些纖維或細絲的強度一般為2500~3500MPa。此外,還可用金屬單晶須或Al3O2、B4C等陶瓷單晶須作為增強纖維,它們的強度就更高。但晶須的生產很困難,成本很高。 鋁合金是一種典型的基體材料。以硼纖維增強和可熱處理強化的合金(如Al-Cu-Mg、Al-Mg-Si)或彌散硬化的Al-Al3O2系為基的金屬復合材料,其比強度和比剛度為標準鋁合金的2~3.5倍,已被用于航空及航天工業。 金屬基體復合材料的強化機理與上述固溶強化及彌散強化等機理不同,這種強化主要不是靠阻礙位錯運動,而是靠纖維與基體間良好的浸潤性緊密粘結,使纖維與基體之間獲得良好的結合強度。這樣,由于基體材料有良好的塑性和韌性,增強纖維又有很高的強度,能承受很大的軸向負荷,所以整個材料具有很高的抗拉強度及優異的韌性。此外,這種材料還能獲得很高的比強度、很高的耐熱性及抗腐蝕性,是目前材料發展的一個新方向。 不可熱處理強化鋁合金的強化 純鋁、Al-Mg、Al-Mg-Sc、Al-Mn合金屬于不可熱處理強化鋁合金,主要靠加工硬化和晶界強化獲得高強度,輔助強化機制還有固溶強化、過剩相強化、彌散相強化等。加工硬化可通過熱變形、冷變形、冷變形后部分退火而不同程度地獲得。熱變形產生亞結構強化,變形溫度越高,亞晶尺寸越粗大,強化效果越差,但塑性相當高。經完全退火的材料進行不同程度的冷變形,冷變形率越大,制品強度越高,但塑性也越低。冷變形的加工硬化效果最大。充分冷變形的制品在不同溫度下退火,控制回復和再結晶階段,可保留不同程度的加工硬化量即不同的強化效果。 可熱處理強化鋁合金的強化 工業生產的可熱處理強化鋁合金有Al-Cu-Mg、Al-Cu-Mn、Al-Mg-Si、Al-Zn-Mg和Al-Zn-Mg-Cu合金,以及開發中的Al-Cu-Li和Al-Mg-Li合金等。這些合金普遍采用淬火時效,并主要通過沉淀強化方法來獲得很高的強度,輔助強化機制也有固溶強化、過剩相強化、彌散相強化、晶界強化等。自然時效時G.P區為主要強化相,人工時效主要是G.P區加過渡相起強化作用,過時效時才出現穩定相,出現穩定相后強度降低。 形變時效與擠壓效應強化 在Al-Cu系和Al-Mg-Si系合金中,較多采用形變時效方法獲得高強度,該方法包括T3、T8和T9三種狀態,都是利用時效強化和冷作硬化的交互作用及強化在一定程度上的疊加作用。2124-T8厚板因冷變形產生的大量滑移線,滑移線上成排分布著時效析出相,二者的聯合作用使塑性變形更為困難,即強度進一步提高。 可熱處理強化鋁合金擠壓制品淬火時效后的強度比其他方法生產的同一合金相同熱處理狀態下的強度高,這一現象稱為擠壓效應。其組織觀察發現全部或部分保留了冷作硬化效應,基體中保留了大量亞結構,故強化是時效強化和亞結構強化的疊加。 Al-Si合金的強化 Al-Si系變形鋁合金,特別適合于生產活塞等模鍛件,合金中硅含量ω(Si)=12%~13%,還含有一定量的Cu、Mg、Ni等。組織中有較多的結晶時生成的共晶硅,均布在軟的α(Al)基體上,尺寸大都在5μm左右,硬且脆。這種共晶硅是鋁合金中異相強化的典型例子。由于異相強化具有耐高溫、耐磨和中強等特點,故特別適合于制作活塞。 來源:《鋁合金的熱處理》、《簡明鋁合金加工手冊》、網絡
免責聲明:本網站所轉載的文字、圖片與視頻資料版權歸原創作者所有,如果涉及侵權,請第一時間聯系本網刪除。
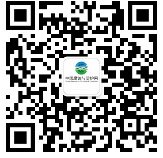
官方微信
《腐蝕與防護網電子期刊》征訂啟事
- 投稿聯系:編輯部
- 電話:010-62316606
- 郵箱:fsfhzy666@163.com
- 腐蝕與防護網官方QQ群:140808414