隨著全球化進程的不斷推進,海洋逐漸成為國際工業領域、軍事戰略的焦點。然而,海洋大氣環境中的極端環境和復雜工況,如高濕度、鹽分、溫度及應力載荷等特殊條件對航空發動機的服役性能與壽命提出了嚴峻的考驗。尤其是壓氣機及渦輪機的葉盤和葉片在該環境下的腐蝕問題都極為嚴重,其在海洋環境下的使用壽命也由于腐蝕問題而大大縮短[1]。隨著全球經濟發展及軍事戰略的需求,該類問題日漸突出,亟待解決。
海洋環境大氣中含有的大量鹽分(主要是NaCl)及水蒸汽會隨著海洋空氣進入壓氣機內部。通常,飛機發動機的壓氣機服役溫度為300~600℃(中溫),該溫度遠低于NaCl的熔點,因此,NaCl通常以固態鹽的形式沉積在葉片表面,形成沉積鹽膜,由此構成了中溫環境下固態NaCl及水蒸汽共存的腐蝕環境。針對金屬材料受含氯固態鹽加速的中高溫腐蝕行為的研究表明純金屬[2,3]、Fe-Cr系合金[4,5]、Ti合金[6,7]以及不銹鋼[8,9]的腐蝕均受到了不同程度的促進;合金表面原有的保護性氧化膜(如Cr2O3)在中、高溫環境下被破壞,并失去了對合金的保護性。針對上述的腐蝕現象,有研究提出了“動態水膜理論”,利用電偶腐蝕測量技術,首次證實在中溫NaCl鹽膜+水蒸汽環境的金屬腐蝕過程中存在電化學反應,揭示電化學反應催化加速氧化反應[10,11]。由此,該系列研究創新性地提出了中溫固態NaCl環境中金屬腐蝕的化學-電化學交互作用機制,并初步構建了腐蝕模型[12]。此外,也有研究針對于合金表面保護性氧化膜破壞及氧化膜/基體界面的腐蝕化學反應提出了“活化氧化”(Active oxidation mechanism)[2,13,14]的腐蝕機制,該理論認為在中高溫的(非)潮濕環境下,NaCl與氧化物發生破壞化學反應并產生氣態的金屬氯化物,該產物向合金側擴散至氧化膜/金屬界面,與氧發生反應而產生Cl,由于該處氧分壓較低,Cl將進一步與金屬反應,并再次生成金屬氯化物而循環參與到腐蝕過程中,由此持續性破壞金屬材料。
服役于海洋大氣環境下的飛機發動機葉片材料的腐蝕失效行為一直是受到廣泛關注的問題。一方面,在上述環境下服役的材料面臨的是多因素耦合作用下的腐蝕,包括溫度、水汽、沉積鹽以及在發動機運行過程中,葉片及葉盤所受的應力載荷。有研究針對氧化條件下材料的加速開裂及加速氧化行為提出了“Dynamic embrittlement”[15~17]和“Stress-assisted grain boundary oxidation”[17~19]的材料開裂理論,并認為在應力載荷影響下,受氧化過程影響的合金內氧化楔入將導致裂紋的萌生,氧由此可在裂紋尖端處通過晶界擴散并與金屬反應,并降低了晶界的強度,從而加速裂紋的擴展[20~22]。目前涉海飛機發動機等熱端部件材料在服役環境下的腐蝕有別于傳統氧化過程,該過程存在著Cl循環參與腐蝕反應并加速材料腐蝕的特點。當考慮到應力載荷同時也作用于服役材料上時,其腐蝕行為也將有別于傳統氧化-開裂過程。
基于以上問題,本研究以標準熱處理制度和固溶熱處理之后的GH4169合金為對象,深入研究兩種含有不同程度δ相析出的GH4169合金在潮濕環境中受600℃中溫、應力載荷和固態NaCl共同影響下的腐蝕行為。利用掃描電鏡(SEM)、X射線衍射儀(XRD)、能譜成分分析(EDS)等手段詳細分析腐蝕后腐蝕產物的成分和結構,在此基礎上進一步探索彈性應力載荷對中溫水蒸汽環境耦合固態NaCl條件下GH4169合金腐蝕失效的影響,以期為涉海航空發動機高溫合金的設計提供理論數據和參考。
1 實驗方法
本研究以常用的鎳基高溫合金GH4169為研究對象,探索了其在固態NaCl、潮濕環境及應力耦合作用下的中溫腐蝕行為,其名義成分(質量分數,%)為:C 0.04,Mn 0.08,Si 0.07,Fe 17.87,Cr 18.19,Nb + Ta 5.28,Mo 3.04,Al 0.53,Ti 0.98,Co 0.24,Cu 0.07,P < 0.01,S < 0.01,Ni余量。為了適應不同的性能需求,該合金通常通過熱處理的方式控制晶粒度、δ相的形貌、數量和分布[30,31]。由此,研究中所使用的兩種GH4169合金分別經固溶熱處理(((1010~1065) ± 10)℃,1 h;空冷至(720 ± 5)℃,8 h;以50℃/h爐冷至(620 ± 5)℃,8 h,空冷)和標準熱處理制度(((950~980) ± 10)℃,1 h;空冷至(720 ± 5)℃,8 h;以50℃/h爐冷至(620 ± 5)℃,8 h,空冷)[32]。圖1a為經標準熱處理制度后的GH4169合金組織形貌,經此制度處理的材料有δ相沿晶界析出;經固溶熱處理之后的GH4169合金(圖1b)相較于標準熱處理制度下的合金具有更少的δ相析出。經過統計(圖1c),二者的晶粒尺寸較為相近,分別為11.41和11.94 μm。
圖1
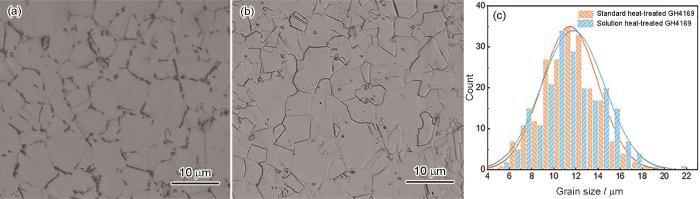
圖1 經標準熱處理和固溶熱處理后GH4169合金的金相組織及晶粒尺寸統計
Fig.1 Metallographic structure of GH4169 alloys treated by standard heat treatment (a) and solution heat treatment (b), and grain size statistics (c)
上述兩種材料被進一步加工為20 mm × 10 mm × 2 mm的薄片。樣品在酒精-丙酮溶液進行超聲清洗,以除去試樣表面的油污;而后,片狀樣品經SiC水砂紙逐級打磨至2000#后,對樣品進行倒角、倒邊處理;隨即,對樣品的表面進行拋光處理,以避免由粗糙的表面狀態導致不均勻或加速腐蝕;最后經過拋光后的樣品放置于酒精-丙酮溶液中進行清洗,而后冷風吹干,放入干燥器中備用。
為模擬飛機發動機葉片材料在實際海洋大氣環境下服役的條件,本研究首先搭建了潮濕中溫(600℃)環境,如圖2a所示,包括經由恒溫水浴實現的水蒸汽發生裝置、恒溫管式爐以及載氣源(氣路)。其中,水蒸汽是通過循環的(75 ± 2)℃的恒溫水浴產生。根據Magnus經驗方程[33,34],可推算此時水浴液面之上所產生的水蒸汽含量為386.54 hPa;由于實驗在敞開的環境(101.325 kPa)下展開的,故而水蒸汽的含量可計算為38.1%(體積分數),接近于實際海洋大氣環境中的水蒸汽含量[4]。而后,以空氣為載氣(流速為310 mL/min),從水浴的底部通入,將產生的水蒸汽攜帶并進入爐腔內的石英管中,并與實驗樣品接觸而發生腐蝕反應。
圖2
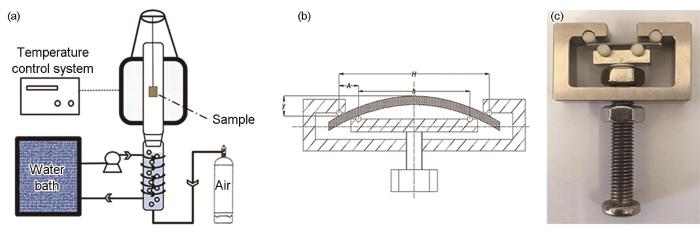
其中,σ、t和y分別為樣品受到的應力(MPa)、樣品的厚度(mm)以及樣品的變形量(mm);E為材料的Young's模量,在本研究中取值為150 GPa,對應于GH4169合金在600℃時的Young's模量[32];A及H分別為四點彎梁夾具的內外支點之間的距離及兩外支點之間的距離(圖2b)。根據
圖3

圖3 ANSYS模擬計算的受力及應變狀態
Fig.3 Stress and strain state calculated by ANSYS simulation: (a) front view of strain state, (b) oblique view of stress state, (c) top view of strain state, (d) oblique view of stress state
為了解兩種GH4169合金在上述環境下的腐蝕行為,采用光學顯微鏡和掃描電子顯微鏡(SEM)對腐蝕后樣品表、截面上的腐蝕產物形貌進行觀察;通過X射線衍射(XRD, X'Pert Pro Panalytica Co.)和能譜(EDS, INCA, X-Max)分析了合金表面的腐蝕產物成分。將樣品垂直鑲嵌于環氧樹脂中,通過精細打磨及拋光獲得GH4169合金在上述環境下腐蝕后的截面,使用背散射電子成像的方式分析了合金的內腐蝕形貌以及在樣品截面上的成分分布。
為了解GH4169合金在受到腐蝕過程影響之后結構的穩定性,本研究還基于第一性原理的計算方法展開了受擴散影響導致的空位形成對合金結構影響的模擬計算。本研究借助Materials Studio軟件的CASTEP模塊對Ni-Cr-Fe模型合金及含有Cr及Fe空位的該合金結構展開了計算。根據該合金主要元素的原子比(Ni∶Cr∶Fe = 0.902∶0.390∶0.332),建立了含有64個原子的立方晶系晶胞模型;其中,Ni、Cr及Fe原子比為9∶4∶3??紤]晶胞對稱性,通過枚舉法列舉了3381個可能的晶胞,而后根據能量最低原則篩選出了最適晶胞;隨后,以此模型為基礎建立含有Cr空位、Fe空位及Fe、Cr共存空位的晶胞,由此模擬受腐蝕擴散過程影響而在合金基體中形成了空位的合金結構。計算過程中,使用了超軟贗勢(Ultrasoft pseudopotentials)來描述電子-離子相互作用[35,36];為了描述交換相關能,我們采用了Perdew等[37]的廣義梯度近似(GGA);在幾何優化和能量優化的過程中,最適的截斷能經收斂測試后選擇為310 eV;根據Monkhorst-Pack方法[38],k-point經測試后選擇為4 × 4 × 4;在整個的計算過程中,結構收斂的判據確定為:臨界能量不高于2.0 × 10-6 eV/atom,原子間最大相互作用力不高于0.06 eV/nm,另外原子位移不大于2.0 × 10-5 nm。
2 結果及討論
2.1 表面腐蝕形貌及成分分析
圖4為兩種熱處理狀態下的GH4169合金在不同應力載荷水平下的表面宏觀形貌。由圖4a~c可以看出,標準熱處理狀態下的GH4169合金表面產生了大量的紅褐色腐蝕產物,且局部區域的腐蝕產物發生了剝落;而經固溶熱處理之后的GH4169合金表面同樣生成了紅褐色的腐蝕產物,該腐蝕產物雖然未發生剝落,但是存在明顯的皺褶形貌特征(圖4d~f),說明該合金表面的腐蝕產物同樣是較為疏松的結構。另外,隨著應力的增大,合金表面的腐蝕狀態趨于惡化。經固溶熱處理之后的合金腐蝕產物的褶皺狀態也隨應力載荷的施加和增大逐漸明顯。由此可以初步判斷,兩種熱處理制度下的GH4169合金在固態NaCl耦合潮濕中溫環境中,應力載荷都將加速其表面的腐蝕。
圖4
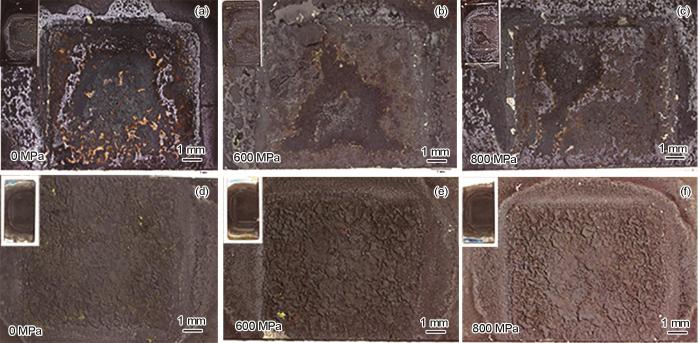
圖4 表面沉積NaCl的GH4169合金在潮濕的600℃環境下受0、600和800 MPa應力載荷影響腐蝕20 h后的宏觀表面形貌
Fig.4 Macro surface morphologies of GH4169 alloys treated by standard heat treatment (a-c) and solution heat treatment (d-f), and deposited with NaCl after corrosion in a humid 600oC environment for 20 h under a stress load of 0 MPa (a, d), 600 MPa (b, e) and 800 MPa (c, f)
圖5為經標準制度熱處理的GH4169合金在受不同水平應力載荷影響腐蝕20 h后的表面形貌。在不受應力載荷影響時,合金表面腐蝕產物膜較為平整,局部存在顆粒狀腐蝕產物(圖5a和b);同時,表面存在立方結構的NaCl的殘余(圖5c)。應力載荷的施加促使顆粒狀腐蝕產物增多并覆蓋整個合金的表面(圖5d和e);此外,腐蝕膜層上還存在少量孔洞(圖5f)。當合金受800 MPa的應力載荷時,合金表面出現了被針狀腐蝕產物包裹的顆粒狀腐蝕產物(圖5g),該層腐蝕產物膜上存在著裂紋,如圖5h和i所示。上述結果表明,隨著應力載荷的施加及增大,經標準熱處理后的GH4169合金表面腐蝕產物的構成逐漸復雜,同時還伴隨著NaCl的加速消耗,加重了合金表面的腐蝕反應。
圖5

圖5 標準制度熱處理的GH4169合金在含有固態NaCl的潮濕的600℃環境下受不同應力載荷影響腐蝕20 h后的表面形貌
Fig.5 Surface morphologies of GH4169 alloy treated by standard heat treatment after corrosion in a humid 600oC environment containing solid NaCl for 20 h under a stress load of 0 MPa (a-c), 600 MPa (d-f) and 800 MPa (g-i)
圖6為固溶熱處理制度下GH4169合金在潮濕600℃環境下受不同水平應力載荷影響腐蝕20 h后的表面形貌??梢钥闯?,合金表面生成了相對較厚的腐蝕產物層,然而如圖6a,d和g所示,該層腐蝕產物局部發生了開裂及剝落,并不完全具備致密的結構。當合金不受應力載荷影響時(圖6b),該層膜由上層的顆粒狀腐蝕及底層的多孔膜構成(圖6c)。當合金受600 MPa應力載荷影響時,腐蝕產物膜發生了大面積剝落使基體再次裸露于腐蝕環境中(圖6e);此時的外腐蝕膜由尺寸較大且表面覆有針(片)狀的腐蝕產物的顆粒構成,結構較為疏松(圖6f)。當合金所受的應力載荷增至800 MPa時,合金表面腐蝕產物膜更嚴重剝落,且其表面的顆粒狀腐蝕產物尺寸增大。由此可判斷,GH4169合金經固溶熱處理之后與其在標準熱處理制度之下的腐蝕情況相類似,應力載荷加速了合金的表面腐蝕,致使腐蝕產物膜傾向于開裂并發生剝落。
圖6

圖6 固溶熱處理的GH4169合金在含有固態NaCl的潮濕的600℃環境下受不同應力載荷影響腐蝕20 h后的表面形貌
Fig. 6 Surface morphologies of GH4169 alloy treated by solution heat treatment after corrosion in a humid 600oC environment containing solid NaCl for 20 h under a stress load of 0 MPa (a-c), 600 MPa (d-f) and 800 MPa (g-i)
圖7為標準制度熱處理和固溶熱處理下的GH4169合金表面腐蝕產物的XRD譜。由結果可以看出,應力載荷及熱處理制度并未導致合金表面的腐蝕產物種類產生差異,在本研究中主要包括NiCr2O4、NaNbO3、Fe2O3、NiO、Cr2O3、Al2O3及NiFe2O4。
圖7

圖7 GH4169合金在含有固態NaCl的潮濕的600℃環境下受不同應力載荷影響下腐蝕20 h后表面腐蝕產物的XRD譜
Fig.7 XRD patterns of surface corrosion products of NaCl-deposited GH4169 alloys treated by standard heat treatment (a) and solution heat treatment (b) after corrosion in a humid 600oC environment for 20 h under different stress loads
2.2 合金內腐蝕及成分分析
圖8為兩種熱處理制度下的GH4169合金在潮濕的600℃環境下受不同應力載荷影響下腐蝕20 h后的截面形貌。經標準熱處理之后的GH4169合金在不受應力載荷影響時,其外腐蝕層厚度平均約為3.06 ± 0.50 μm,該腐蝕產物膜較薄、不連續且存在大量的孔洞(圖8a);隨著應力載荷的施加,該腐蝕產物層逐漸增厚,其厚度平均約為3.55 ± 0.50 μm(圖8b);當應力載荷增加至800 MPa時,合金表面的腐蝕產物膜厚度平均約為4.98 ± 0.50 μm(圖8c),該腐蝕產物膜層較為疏松,且由連續的內層以及疏松的外層構成。固溶熱處理的GH4169合金經20 h腐蝕后,其表面產生的膜層雖同樣存在著孔洞,但相對于經標準熱處理的GH4169合金表面腐蝕產物膜則更為連續和致密,如圖8d~f所示。合金在不受應力載荷以及受600和800 MPa應力影響時,合金表面生成的腐蝕產物膜平均厚度分別約為2.63、3.83和4.72 ± 0.50 μm;在應力載荷的影響下,表面腐蝕產物膜同樣包含連續的內層和疏松的外層結構。
圖8

圖8 表面沉積NaCl的GH4169合金在潮濕的600℃環境下受不同應力載荷影響腐蝕20 h后的截面形貌
Fig.8 Cross-sectional morphologies of NaCl-deposited GH4169 alloys treated by standard heat treatment (a-c) and solution heat treatment (d-f) after corrosion in a humid 600oC environment for 20 h under a stress load of 0 MPa (a, d), 600 MPa (b, e) and 800 MPa (c, f)
此外,在上述的環境下,兩種合金也發生了明顯的內腐蝕,內腐蝕產物均為不連續的顆粒,二者的內腐蝕深度隨應力水平的提高而逐漸變深,如圖8a~c所示。對于經標準熱處理的GH4169合金,在3種應力狀態下的最大內腐蝕深度分別約為5.47 ± 0.50、12.77 ± 0.50和23.52 ± 0.50 μm,其內腐蝕在局部區域會發生較深的內腐蝕,該現象在應力載荷的作用下尤為明顯。然而在上述環境下,經固溶熱處理的GH4169合金內腐蝕形貌則與之不同,表現為由尺寸較小且相對均勻的內腐蝕顆粒構成的深度均勻的“內腐蝕帶”(圖8d~f)。該“內腐蝕帶”在3種應力狀態下的深度分別約為7.91 ± 0.50、8.51 ± 0.50和9.33 ± 0.50 μm。根據上述結果可以看出,GH4169合金的內腐蝕雖然在不同的熱處理狀態下存在著形貌和深度的差異,但內腐蝕的生長都不同程度受到了應力載荷的促進。由此可以判斷應力載荷將促進GH4169合金在該環境下發生內腐蝕。
圖9

圖9 振動拋光后的標準制度熱處理GH4169合金內腐蝕形貌
Fig.9 Internal corrosion morphologies of standard heat-treated GH4169 alloy under a stress load of 0 MPa (a, d), 600 MPa (b, e) and 800 MPa (c, f) after shock polishing: (a-c) backscattered electron image of the internal corrosion morphologies, (d-f) internal corrosion morphologies with high contrast
兩種合金在600 MPa應力影響下,經20 h腐蝕后的內、外腐蝕產物中元素分布如圖10所示。標準制度熱處理的GH4169合金腐蝕20 h后(圖10a, b),其外腐蝕層主要由Ni、Fe、Nb、Cr、Al及O構成,根據圖7的XRD結果可知,上述元素對NiCr2O4、NaNbO3、Fe2O3、NiO、Cr2O3、Al2O3及NiFe2O4的形成有明顯的貢獻;此外合金的外腐蝕產物層還含有Ti,然而可能由于其含量較低,并未通過XRD檢測到該元素所對應的產物。另外,在合金的腐蝕產物膜層與基體之間還檢測到了Cl的分布,這表明該處可能發生了活化腐蝕[13]。圖10c為標準制度熱處理的GH4169合金腐蝕20 h后的內腐蝕區元素分布,根據Cr及O的分布可以判斷,內腐蝕產物主要由Cr的氧化物構成,即Cr2O3;此外,還有少量的Fe氧化物;在內腐蝕區還可以觀察到Ni的富集,然而該區域并不與其他元素存在明顯的重疊,因此可以判斷腐蝕過程導致了富Ni區的形成。值得一提的是,在內腐蝕區還檢測到了Cl的富集,同時該區域也為O的富集區,該結果表明Cl及O向合金內發生了擴散,由此在合金內構成了活化腐蝕的條件,進而引發合金的內活化腐蝕。
圖10
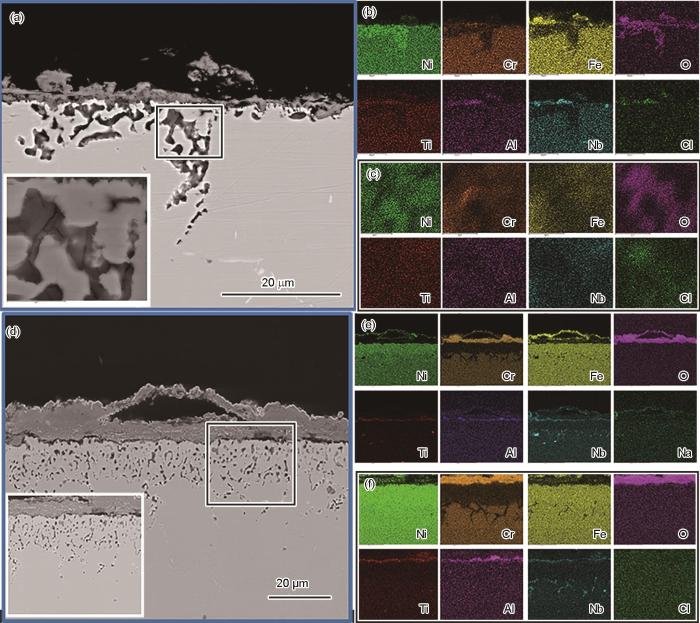
圖10 GH4169合金在潮濕的600℃環境下受600 MPa應力載荷影響下腐蝕20 h后的截面元素分布
Fig.10 Cross-sectional morphologies (a, d) and corresponding elemental distribution on the cross-section (b, e) and internal corrosion region (c, f) of GH4169 alloys treated by standard heat treatment (a-c) and solution heat treatment (d-f) after corrosion in a humid 600 °C environment for 20 h under a stress load of 600 MPa
圖10d~f為固溶熱處理的GH4169合金腐蝕經20 h后的截面形貌及元素分布。可以看出,該合金的最外層疏松腐蝕產物膜由Fe、Ni、Cr、Nb及Na、O構成,中間層主要由Cr及O構成,另外還包括了Ti及Al構成的內層腐蝕產物膜。相較于圖10b所示的經標準制度熱處理的GH4169的元素分布,固溶熱處理未使元素的整體分布發生明顯的改變,然而卻生成了相對連續的Al及Ti的內層腐蝕產物,這可能是由于致密的中間層Cr2O3導致了相對低的氧分壓,此條件將利于TiO2及Al2O3的生成。另外,由圖10f所示的內腐蝕區的元素分布可以看出,合金內腐蝕區的前端生成了Nb的內腐蝕產物及貧Cr和貧Fe區。而由于在均勻“內腐蝕帶”生成的顆粒狀內腐蝕產物體積較小,其成分并不能得到明晰的判定。根據以往研究,推斷該腐蝕產物可能包含Cr2O3、Fe2O3及Al2O3[17,39,40]。
2.3 潮濕中溫環境耦合固態NaCl及應力載荷作用下GH4169合金腐蝕機制
在上述中溫環境下,GH4169合金發生了加重的表面腐蝕及內腐蝕。與之類似,固態含Cl鹽和水蒸汽協同作用也導致了其他含Cr鎳基和鐵基合金的腐蝕[4,5,8,41]。在含Cl鹽和濕氧環境下,合金的腐蝕速率和質量增重遠大于其僅在潮濕大氣或在僅含Cl環境下的腐蝕速率和質量增重。在含固態含Cl鹽和潮濕大氣的雙重作用下,合金的內腐蝕也得到了證實[8,23,40]。氯的存在會降低氧在合金中的體擴散及晶界擴散的活化能,導致加速外腐蝕和內腐蝕[5, 8]。應力的存在將加速晶間腐蝕的擴展[42]。由此可以判斷,在中溫條件下,氧與固態NaCl的協同作用是直接導致內腐蝕的關鍵因素;而水蒸汽和應力載荷等因素又加速了這一過程。
圖11
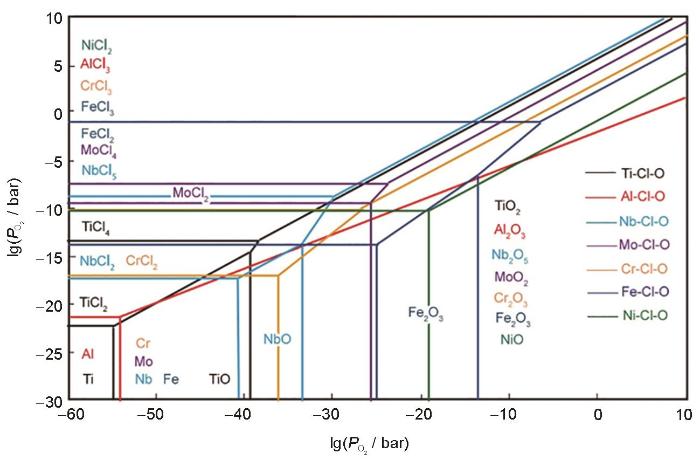
考慮上述腐蝕過程是伴隨金屬元素向外擴散發生的,因此導致了合金中部分金屬如Cr、Fe發生了貧化,如圖10所示,進而導致了合金中以Cr及Fe為主的空位形成。通過第一性原理的計算方法研究了與該腐蝕過程相關的空位形成對合金體系的影響,搭建的模型如圖12所示。晶體結構優化后,原始Ni-Cr-Fe合金的晶格常數為0.723 nm,當產生不同數量及種類的Cr/Fe空位后,晶格常數發生了較小的變化,產生1~3個Cr空位、一個Fe空位以及一個Fe及Cr共存的空位時,晶格常數分別為0.7238、0.7230、0.7217、0.7238和0.7270 nm。該結果表明,當固溶于Ni基體中的Cr及Fe受腐蝕過程影響而發生向外的擴散時,合金的晶胞并未發生較大的畸變。然而空位的形成卻使體系的穩定性發生了較大程度的下降,如圖13a所示,隨著Cr空位的數量增多,晶胞的體系能量逐漸升高,即晶胞穩定性下降;另外,從結果還可以看出,Fe擴散所導致形成的含Fe空位的晶胞穩定性要高于含有Cr空位的晶胞。
圖12
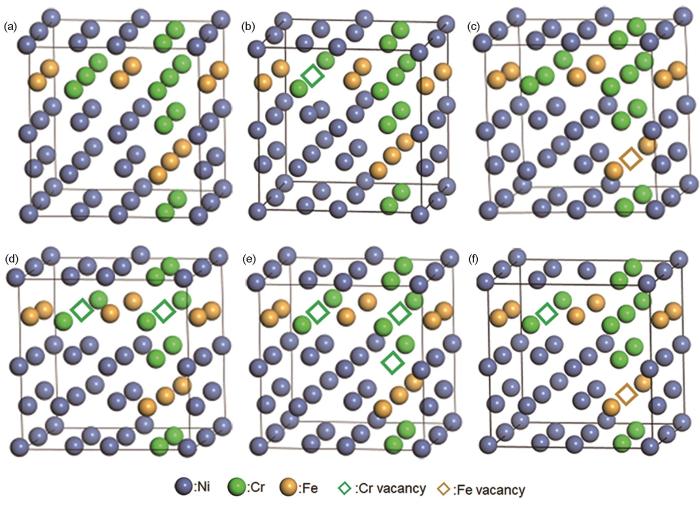
圖12 基于GH4169合金元素含量建立的Ni-Cr-Fe及含空位的合金晶胞
Fig.12 Ni-Cr-Fe model alloy cells and that with vacancy contained established based on GH4169 alloying element content: (a) original Ni-Cr-Fe cell, (b) a cell containing one Cr vacancy, (c) a cell containing one Fe vacancy, (d) a cell containing two Cr vacancies, (e) a cell containing three Cr vacancies, (f) a cell containing one Cr vacancy and one Fe vacancy
圖13
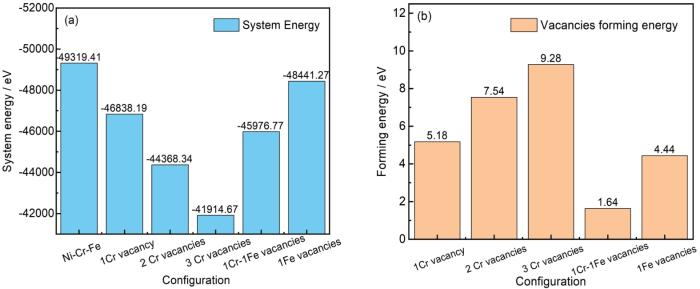
圖13 Ni-Cr-Fe模型合金晶胞及含有Cr、Fe空位的合金晶胞的穩定性
Fig.13 Stability of Ni-Cr-Fe model alloy cells and that with Cr and Fe vacancies: (a) system energy, (b) vacancy formation energy
從圖13b所示的不同空位的形成能可以看出,在所搭建的Ni-Cr-Fe晶胞中,Cr、Fe空位均不傾向于自發產生,這是由于其相應的空位形成能均為正值。然而,Cr、Fe與Cl反應的Gibbs自由能經計算分別為-323.84和-236.52 J/mol,這表明活化氧化過程促進了Cr、Fe與Cl之間的反應,消耗了基體中的Cr、Fe,進而導致了Cr及Fe空位的形成,其中Cr的反應傾向性更高。此外,Fe空位的形成相對于Cr空位更容易,這是由于Fe具有更高的擴散速率,即在合金中移動的能力更強。這使得在高溫條件下,Fe更容易從晶格中遷移到表面而生成含Fe的外層腐蝕產物,如圖10b和d所示。相比之下,Cr的擴散速率較低,在相同條件下形成空位的概率較?。挥纱?,合金中貧Cr區的形成可歸因于Cr與Cl之間的自發性活化腐蝕反應。
3 結論
(1) GH4169合金在含固態NaCl的潮濕600°C環境中發生了加速的腐蝕反應,致使合金表面生成了包含NiCr2O4、NaNbO3、Fe2O3、NiO、Cr2O3、Al2O3及NiFe2O4在內的復雜腐蝕產物。彈性拉伸應力載荷加速了表面腐蝕過程,導致了腐蝕產物層發生開裂和剝落。
(2) GH4169合金在含固態NaCl的潮濕600℃環境中發生了活化內腐蝕,內腐蝕產物為不連續顆粒狀,主要由Cr2O3、少量Fe2O3及NbO構成。其中,經標準制度熱處理之后的GH4169合金傾向于發生不均勻的沿晶內腐蝕,而經固溶熱處理之后的GH4169合金則在基體淺層產生了相對均勻的內腐蝕帶。
(3) 活化腐蝕過程導致合金基體中產生了貧Cr及貧Fe區,在該區域中Cr及Fe空位的存在導致了Ni-Cr-Fe晶胞的穩定性下降。
免責聲明:本網站所轉載的文字、圖片與視頻資料版權歸原創作者所有,如果涉及侵權,請第一時間聯系本網刪除。
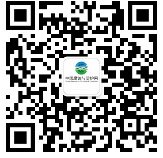
官方微信
《腐蝕與防護網電子期刊》征訂啟事
- 投稿聯系:編輯部
- 電話:010-62316606
- 郵箱:fsfhzy666@163.com
- 腐蝕與防護網官方QQ群:140808414