元素 | 質(zhì)量分數(shù)/% | |||||||||
---|---|---|---|---|---|---|---|---|---|---|
Al | Mo | Zr | Si | Fe | C | N | H | O | Ti | |
TC11鈦合金 | 6.31 | 3.34 | 1.59 | 0.27 | 0.071 | 0.027 | 0.002 1 | 0.001 7 | 0.15 | 余量 |
標準值 | 5.8~7.0 | 2.8~3.8 | 0.8~2.0 | 0.2~0.35 | ≤0.25 | ≤0.10 | ≤0.05 | ≤0.012 | ≤0.15 | 余量 |
鈦合金具有密度小,質(zhì)量輕,比強度和比剛度高,耐蝕性好,韌塑性和加工性能良好等優(yōu)點,在海洋油氣開發(fā)中具有廣闊的應(yīng)用前景。但鈦合金存在摩擦因數(shù)大,硬度低,耐磨性能差,高溫條件下氧化嚴重等缺點,這又限制了鈦合金在摩擦磨損場合的應(yīng)用[1-7]。海洋油氣開發(fā)中,由鈦合金、鈹青銅制造的隨鉆儀器零件,服役時在擠壓、剪切以及交變接觸應(yīng)力的作用下易發(fā)生磨粒磨損、黏著磨損、接觸疲勞等機械損傷[8];而在鉆井液中腐蝕介質(zhì)的作用下,隨鉆儀器零件還會發(fā)生化學損傷。實施表面改性是提升鈦合金、鈹青銅等隨鉆儀器零件耐磨性的有效途徑之一,常用的表面改性技術(shù)包括化學熱處理、離子注入、超聲速火焰噴涂(HVOF)、激光熔覆等。其中,HVOF具有加工效率高、熱影響區(qū)小、涂層與基材為機械結(jié)合、涂層厚度可控等優(yōu)點,通過調(diào)控噴涂工藝參數(shù)以及涂層材料體系設(shè)計,可在鈦合金等金屬表面制備出耐磨性優(yōu)異的涂層。
王成[9]采用HVOF在TC18鈦合金試片上制備WC-12Co和WC-10Co4Cr涂層。結(jié)果表明,兩種涂層無明顯缺陷,孔隙率低,涂層與基體結(jié)合良好,以機械結(jié)合為主;摩擦磨損測試表明,兩種涂層均顯著改善了基體的耐磨性,其中WC-10Co4Cr涂層相對更優(yōu)。張業(yè)勤等[10]采用兩種不同粉末在TC27鈦合金試片上噴涂耐磨涂層,對比分析了不同粉末對耐磨涂層的顯微組織、孔隙率、顯微硬度、結(jié)合強度及彎曲性能的影響。DU等[11]研究了噴丸、噴砂和HVOF制備的WC-17Co涂層的表面完整性對TC18鈦合金疲勞性能的影響。關(guān)于HVOF金屬陶瓷涂層的研究論文很多,研究方向多集中在涂層顯微組織,涂層與基體的結(jié)合性,以及涂層的耐摩擦磨損性能和耐蝕性方面[12-17]。但是,在鈦合金基材上采用HVOF制備陶瓷涂層,研究表面改性對基材組織和性能的影響較為少見。另外,發(fā)生過一起經(jīng)激光熔覆處理的鈹青銅隨鉆儀器零件早期疲勞斷裂事件,而疲勞失效又與基體組織和性能受到激光熔覆的熱輸入影響密切相關(guān)。基于這兩方面原因,有必要系統(tǒng)研究表面改性對鈦合金基材組織和性能影響。
筆者采用HVOF在TC11鈦合金試樣和隨鉆儀器零件上制備WC-10Co4Cr金屬陶瓷涂層,通過顯微組織和顯微硬度、沖擊韌性和斷口分析、濕砂膠輪磨粒磨損試驗和電化學測試,系統(tǒng)研究了涂層的性能,以及HVOF工藝對基材組織和性能可能造成的影響,為后續(xù)隨鉆儀器零件表面強化的規(guī)模應(yīng)用提供技術(shù)支持。
1. 試驗
1.1 試樣和涂層制備
委托試制工廠按照設(shè)計要求,完成鈦合金試樣和涂層制備。將?50 mm的TC11棒材加工成尺寸為75 mm×25 mm×10 mm的TC11鈦合金試樣,共加工6件,其中3件采用HVOF工藝制備涂層。棒材為退火態(tài),熱處理制度是950 ℃×2 h,空冷+530 ℃×6 h,空冷,TC11鈦合金成分見表1。
試樣經(jīng)過清洗和烘干、表面噴砂粗化和預(yù)熱200 ℃,再進行HVOF。HVOF以航空煤油作為燃料,氧氣作為助燃氣,氮氣作為載氣,工藝參數(shù)為:煤油流量22 L/h,氧氣流量52 m3/h,送粉量60 g/min,噴涂距離360 mm,最終涂層厚度200~250 μm。金屬陶瓷粉末化學成分見表2。
粉末名稱 | 質(zhì)量分數(shù)/% | |||
---|---|---|---|---|
C | Co | Cr | W | |
WC-10Co4Cr | 3.5~4.5 | 9~11 | 3.5~4.5 | 余量 |
1.2 測試分析
有無涂層的鈦合金試樣(以下簡稱帶涂層試樣和無涂層試樣)各取1件進行切割,制成尺寸為20 mm×25 mm×10 mm的試樣,用于金相檢驗和硬度測試;試樣經(jīng)打磨和拋光后用HF+HNO3浸蝕劑顯示組織,使用光學顯微鏡(OM)和掃描電鏡(SEM)觀察涂層和基體的顯微組織,采用圖像分析軟件測量涂層的孔隙率。
利用能譜儀(EDS)和X射線衍射儀(XRD)分別測定涂層的化學成分和相組成,X射線源為Cu鈀Kα射線,管壓40 kV,管流40 mA,連續(xù)掃描,衍射角范圍為20°~90°。
按照ASTM E384-2017《材料顯微壓痕硬度的標準試驗方法》標準,使用維氏硬度計在2.94 N載荷下測定涂層和基體的顯微硬度,結(jié)果取5個點的平均值,基體硬度測量始于涂層界面,近界面處每間距100 μm進行測量,之后間距1 mm測量;無涂層鈦合金試樣的硬度從近表面往芯部測量,間距1 mm。
將有無涂層試樣各加工3件帶“V”型缺口的標準沖擊試樣,尺寸為10 mm×10 mm×55 mm,使用擺錘沖擊試驗機進行沖擊韌性試驗,用SEM觀察斷口形貌。
使用濕砂膠輪磨粒磨損試驗機測涂層的耐磨性,測試設(shè)備及測試參數(shù)見表3。參照ASTM G105-2020《進行濕砂/橡膠輪磨損試驗的標準試驗方法》,用稱量法測定試樣噴涂前后的磨損量,用SEM觀察試樣的磨損形貌。
設(shè)備 | 膠輪-濕砂磨粒磨損試驗機 |
---|---|
膠輪 | 硬度60 HD,直徑177.4 mm,寬度13 mm |
試樣尺寸/mm | 75.6×25.4×10.4 |
砂 | 50~70目(212~270 μm)石英砂,平均粒徑260 μm |
砂漿 | 1 500 g石英砂+940 g純凈水 |
膠輪輪速/(r·min-1) | 240 |
載荷/N | 240 |
磨程/m | 3 355 |
1.3 電化學測試
采用電化學工作站測試試樣的耐蝕性,試樣尺寸為10 mm×10 mm,采用標準三電極體系,用環(huán)氧樹脂封裝后的試樣作為工作電極,鉑片作為輔助電極,飽和甘汞電極(SCE)作為參比電極,在25 ℃的3.5%(質(zhì)量分數(shù))NaCl溶液中進行動電位極化曲線測試。動電位掃描范圍為-700~100 mV,掃描速率為2 mV/s,自腐蝕電位的測試時間為3 600 s。無特殊說明,本文中的電位均相對于SCE。
2. 結(jié)果與討論
2.1 顯微組織
由圖1可見:涂層平均厚度為230 μm,涂層截面呈較致密的層狀結(jié)構(gòu),有零星分布的孔隙,孔隙率為2.55%,屬于較低水平,涂層與基體為機械結(jié)合;涂層內(nèi)部有斷續(xù)分布的微裂紋,這在一定程度上降低了涂層與基體的結(jié)合力;界面處的TC11鈦合金基體組織為暗黑色β相基體+白色等軸α相再結(jié)晶晶粒的雙相組織,在涂層界面處有少量的白色細針狀α相,β相內(nèi)的α相呈片層結(jié)構(gòu);與未經(jīng)噴涂的鈦合金組織相比,涂層界面處的α+β雙相組織形貌和比例沒有明顯差別。
與等離子噴涂、電弧噴涂、火焰噴涂等其他改性技術(shù)相比較,HVOF技術(shù)具有低熱源溫度和極高噴射速度,能夠防止碳化物過分氧化和蒸發(fā)分解。工件預(yù)熱溫度不超過200 ℃,HVOF時基材的表面溫度測量值不超過150 ℃,遠低于TC11鈦合金的退火溫度530 ℃及β/(α+β)轉(zhuǎn)變溫度(約1 000 ℃)。因此,HVOF的熱輸入不會導致鈦合金基體發(fā)生組織轉(zhuǎn)變,影響材料性能。但需控制涂層內(nèi)部裂紋的產(chǎn)生,裂紋容易造成涂層在使用過程中剝落,從而影響零件使用壽命。
2.2 涂層元素及相組成
由圖2可見,涂層中各元素含量與WC+10Co4Cr基本一致。由圖3可見,涂層含大量WC增強相及少量W2C和Co25Cr25W8C2相。涂層的性能在一定程度上取決于熱噴涂過程中發(fā)生的物理化學過程。C在金屬黏結(jié)相中的溶解將導致C含量的降低,WC相部分分解為W2C相,C進入黏結(jié)相形成含碳的金屬固溶體基體,基體硬度升高;黏結(jié)相進入碳化物相,形成Mx Wy C型復(fù)合碳化物相(η相)。兩者都將提高WC-金屬陶瓷的脆性[18-19]。所以理想的WC-金屬陶瓷涂層相結(jié)構(gòu)應(yīng)以WC相為主,并含有一定量的W2C相、CoCr黏結(jié)相和少量的η相,這樣結(jié)構(gòu)的涂層更致密、耐磨,同時具有較高的韌性。
2.3 顯微硬度
測得WC-10Co4Cr涂層的顯微硬度均值為1 391 H V,涂層表現(xiàn)出極高硬度。無涂層試樣的硬度見圖4,為343~363 HV,帶涂層試樣的鈦合金基體硬度為336~360 H V,可見采用HVOF工藝沒有使近界面的基體硬度發(fā)生顯著改變,這一測試結(jié)果與顯微組織的觀察結(jié)果相一致。
2.4 沖擊韌性與斷口形貌
由表4可見,無涂層試樣的沖擊功為20.0 J,帶涂層試樣的沖擊功為24.5 J,即經(jīng)過HVOF制備涂層后的鈦合金的沖擊功略高于未經(jīng)處理的鈦合金。由圖5可見:噴涂涂層前后試樣的沖擊斷口形貌無差別,均為塑性斷口,呈剪切韌窩的形貌特征;帶涂層試樣的沖擊斷口在涂層界面兩側(cè)呈現(xiàn)完全不同的斷裂形貌,涂層斷口表現(xiàn)為脆性斷口,有許多的二次裂紋,解理小平面和層狀結(jié)構(gòu),鈦合金斷口表現(xiàn)為塑性斷口,呈剪切韌窩特征。
試樣 | 沖擊功/J | 沖擊功平均值/J |
---|---|---|
無涂層試樣 | 18.7 18.0 23.3 | 20.0 |
帶涂層試樣 | 21.0 20.2 32.2 | 24.5 |
2.5 濕摩擦磨損試驗結(jié)果
帶砂粒的濕摩擦磨損試驗更加貼近隨鉆儀器零件在井下的工作狀況,攜帶巖屑的鉆井液連續(xù)沖刷儀器零件表面的耐磨涂層,使涂層發(fā)生沖刷磨損。當巖屑進入到隨鉆儀器零件之間的間隙,還可以引發(fā)磨粒磨損。經(jīng)過濕砂膠輪磨粒磨損試驗,無涂層試樣被磨出深溝,而帶涂層試樣只有輕微的磨損痕跡,涂層表面的磨痕寬度和磨痕深度均遠低于無涂層試樣,見圖6(a)。用卡尺測量無涂層試樣表面最深的磨痕深度為1.34 mm,通過電子天平計算磨損量V,無涂層試樣的磨損量為0.866 6 g,帶涂層試樣的磨損量為0.013 5 g。而材料耐磨性ε被定義為磨損量V的倒數(shù),即ε=1/V,涂層顯著改善了鈦合金基體的耐磨性。
由圖6可見,在摩擦試驗部位,無涂層試樣有大量的劃痕和犁溝,呈現(xiàn)出磨粒磨損的典型特征,磨損表面還伴隨材料的轉(zhuǎn)移、黏著、塑性變形及流動,這是黏著磨損的典型特征。由此可見,鈦合金的磨損機制包含磨粒磨損及黏著磨損兩種形式。而帶涂層試樣則表現(xiàn)出優(yōu)良的耐磨性,摩擦表面形貌比較平滑,只有細微的犁溝,未見到材料轉(zhuǎn)移、黏著及塑性變形等黏著磨損特征。這是因為高硬度的WC顆粒均勻分布在柔韌的CrCo合金基體上,這樣的涂層結(jié)構(gòu)具有良好的耐磨性[20-21]。較硬的石英砂粒遇到更硬的WC顆粒會產(chǎn)生阻力,只會在涂層表面留下輕微的劃痕犁溝及少許的磨屑而發(fā)生磨粒磨損。帶涂層試樣的磨損機制是磨粒磨損。
材料的磨粒磨損與磨粒的特征(硬度、粒度和尖角程度等),磨損工況條件(載荷、速度、溫濕度等環(huán)境因素)和材料成分及組織性能有關(guān)。大量的現(xiàn)場觀察分析和實驗室試驗發(fā)現(xiàn),材料的磨粒磨損在很大程度上取決于磨粒的硬度Ha和金屬材料的硬度Hm之比。石英的硬度為1 000~1 300 HV,WC涂層的硬度約1 400 HV,鈦合金基體硬度為343~363 HV。根據(jù)硬度比值,鈦合金的磨粒磨損處在高磨損區(qū),即Hm<0.8Ha,磨粒的顯微切削是材料磨損的主要機制;而涂層的磨粒磨損處在過渡磨損區(qū),即Hm≈Ha。由于涂層中含有大量的高硬度碳化物,能夠有效阻止磨料的顯微切削和塑性變形犁鏵作用,使涂層材料具有較高的耐磨性。
2.6 電化學性能
由圖7可見:帶涂層試樣和無涂層試樣的自腐蝕電位(Ecorr)分別為-432 mV和-548 mV,與無涂層試樣相比,帶涂層試樣在陽極極化區(qū)和陰極極化區(qū)腐蝕速率均較小,帶涂層試樣和無涂層試樣的自腐蝕電流密度分別為2.2 μA/cm2和12.2 μA/cm2。極化曲線測試結(jié)果說明,帶涂層試樣的耐腐蝕性能優(yōu)于無涂層試樣。
鄧春明等[22]研究了Cr元素對WC涂層耐腐蝕性能的影響。結(jié)果表明:Cr元素在腐蝕性介質(zhì)中浸泡后形成耐蝕性很好的Cr2O3鈍化膜,可以有效提高涂層的耐腐蝕性能;同時,涂層致密的結(jié)構(gòu)對腐蝕介質(zhì)的擴散起到一定的阻礙作用。
3. 結(jié)論
(1)HVOF工藝對TC11鈦合金的組織和性能影響較小,相較于無涂層試樣,帶涂層試樣界面處基體的顯微組織和顯微硬度沒有明顯變化,沖擊韌性稍有提高。
(2)HVOF工藝穩(wěn)定可靠,涂層呈片層結(jié)構(gòu),致密度高,涂層的孔隙率為2.55%,硬度達到1 400 HV,涂層主要由WC和W2C相組成,其與基體結(jié)合良好,為機械結(jié)合。
(3)金屬陶瓷涂層能夠顯著改善鈦合金的耐磨性和耐蝕性,帶涂層試樣的磨損量只有無涂層試樣的1.56%,帶涂層試樣的磨損機制是磨粒磨損,無涂層試樣的磨損機制是磨粒磨損+黏著磨損。
免責聲明:本網(wǎng)站所轉(zhuǎn)載的文字、圖片與視頻資料版權(quán)歸原創(chuàng)作者所有,如果涉及侵權(quán),請第一時間聯(lián)系本網(wǎng)刪除。
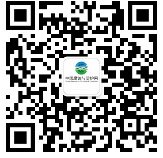
官方微信
《腐蝕與防護網(wǎng)電子期刊》征訂啟事
- 投稿聯(lián)系:編輯部
- 電話:010-62316606
- 郵箱:fsfhzy666@163.com
- 腐蝕與防護網(wǎng)官方QQ群:140808414