高溫合金具有優異的高溫強韌性、良好的抗氧化和抗熱腐蝕性能、顯著的抗蠕變與抗疲勞性能以及優良的組織結構高溫穩定性,被廣泛應用于航空航天、石油化工等領域關鍵熱端部件的制造[1~4]。其中渦輪動力系統關鍵熱端部件(渦輪盤、渦輪葉片等)被譽為渦輪發動機的心臟,需長時間在高溫、熱腐蝕環境服役。因此,提高渦輪轉子關鍵熱端部件用高溫合金的高溫性能,始終是渦輪動力系統能效躍升、服役安全的核心保障[5,6]。隨著高端航空發動機、重型燃氣輪機研制技術的飛速發展,高品質渦輪轉子用高溫合金,更需在長期高溫、疲勞環境下面臨“高溫強韌化”和“性能穩定性”的雙重考驗[7]。而強韌化設計與微結構熱力學往往相互制約[8~10],成為先進渦輪系統研發的瓶頸之一[11]。
近年來,高能噴丸(shot peening,SP)、表面高速機械擠壓(high-speed surface extrusion,HSE)、超聲表面滾壓(ultrasonic surface rolling process,USRP)和激光沖擊(laser shocking processing,LSP)等表面沖擊強化技術在兩機渦輪轉子抗疲勞制造領域的應用研究廣泛深入地展開,顯現出積極的效果和廣闊的前景[12~14]。表面沖擊強化通過在金屬表層引入可觀的塑性變形和殘余壓應力,誘導高密度位錯、孿晶等表面微結構的改變[15~17],從而獲得具有顯著綜合強化效果的梯度硬化層,有望成為高強金屬材料有效的表面抗疲勞制造技術[16~21]。
然而,表面沖擊強化在金屬表面獲得的高殘余壓應力硬化層[15],仍以垂直表面向內的沖擊形變強化為主[12,15,17]。硬化層在劇烈塑性變形(severe plastic deformation,SPD)時產生的高密度位錯、晶格畸變和亞穩界面,使表層獲得可觀殘余壓應力、顯著強化效果的同時,也在表面引入了缺陷密度梯度分布的微結構亞穩層[18]。而對高溫合金而言,600℃甚至以上的高溫條件下,硬化層中的亞穩微結構易發生回復和退化,導致殘余壓應力的松弛甚至消失。這直接影響高溫合金表面沖擊硬化層高溫強化作用的穩定性,也一直是制約表面強化技術在高溫合金渦輪轉子表面強韌化、抗疲勞制造中深入應用的瓶頸性問題[12,13],長期受到設計、制造和研究者的廣泛密切關注。
迄今為止,關于高溫合金表面沖擊強化的諸多實際應用和研究報道中,表面硬化層高密度亞結構的回復推遲、殘余壓應力可保留的機理尚不明確。本文歸納了鎳基高溫合金表面沖擊強化技術及應用的研究進展,在分析不同表面沖擊強化技術提升鎳基高溫合金表面強韌性及抗疲勞作用規律的基礎上,結合近年來本課題組的研究結果,探究了高溫合金表面硬化層在高溫下的顯微組織、微結構演化機理。分析高溫下維持表面強化作用的關鍵機制,展望鎳基高溫合金新型表面沖擊強化技術和抗疲勞調控機制的未來發展方向,以期為具有更高承溫能力的鎳基高溫合金關鍵渦輪轉子強韌化與抗疲勞制造提供思路和參考。
1 高溫合金的表面噴丸處理及噴丸強化
渦輪動力系統的高溫合金關鍵熱端部件,裝機前需經多道次復雜機械加工,構件表面完整性易被破壞,表面粗糙度增大。加之機械加工難以避免在表層引起殘余拉應力等,從而劣化了高溫合金的高溫疲勞性能[22]。尤其對于渦輪轉子,其在長期服役過程中的高溫抗疲勞性能,更是動力系統服役安全的關鍵[23,24]。因此,諸多金屬材料的表面強化技術在高溫合金轉子構件的抗疲勞制造領域倍受關注[23~25]。表面噴丸處理,作為便于實施、低成本和沖擊能量輸入可準確調控的表面處理技術,較早被用于高溫合金的表面強化[26,27]。噴丸處理采用硬質鋼丸、鑄鐵丸、陶瓷丸等轟擊工件表面,在表層引入殘余壓應力,可有效抵消機械加工的表面殘余拉應力,提高材料的抗疲勞能力[28~31]。噴丸處理對高溫合金構件的影響主要有:硬化層殘余應力分布狀態、表面形態和疲勞裂紋萌生阻力等[13,28]。
1.1 高溫合金噴丸處理后的表面應力狀態及分布
高溫合金表面噴丸強化的研究[29~31]表明,噴丸處理可明顯改變機械加工的殘留表面拉應力,在合金表面引入了較為理想的殘余壓應力層,這對高溫疲勞抗力要求很高的高溫合金渦輪轉子,無疑具有高的實用價值。鐘麗瓊等[28]的研究發現,對FGH97合金進行陶瓷彈丸90°噴射4 min處理后,次表層(距表面幾十微米)處獲得了較高的殘余壓應力,應力場深度可達280 μm左右。Wang等[30]對FGH96合金進行了車削、陶瓷噴丸和復合噴丸(高強鑄鐵彈丸和低強陶瓷彈丸)殘余壓應力場的對比研究,發現噴丸處理明顯增加了表層殘余壓應力,并且應力最高值、深度均隨噴丸強度的增加而增大(圖1[30])。在鑄造高溫合金、變形高溫合金的相關研究中也獲得了相似的效果。K4169鑄造高溫合金噴丸處理后表面殘余壓應力由258 MPa增加至1079 MPa,進而顯著提高了合金的疲勞壽命[32]。
圖1
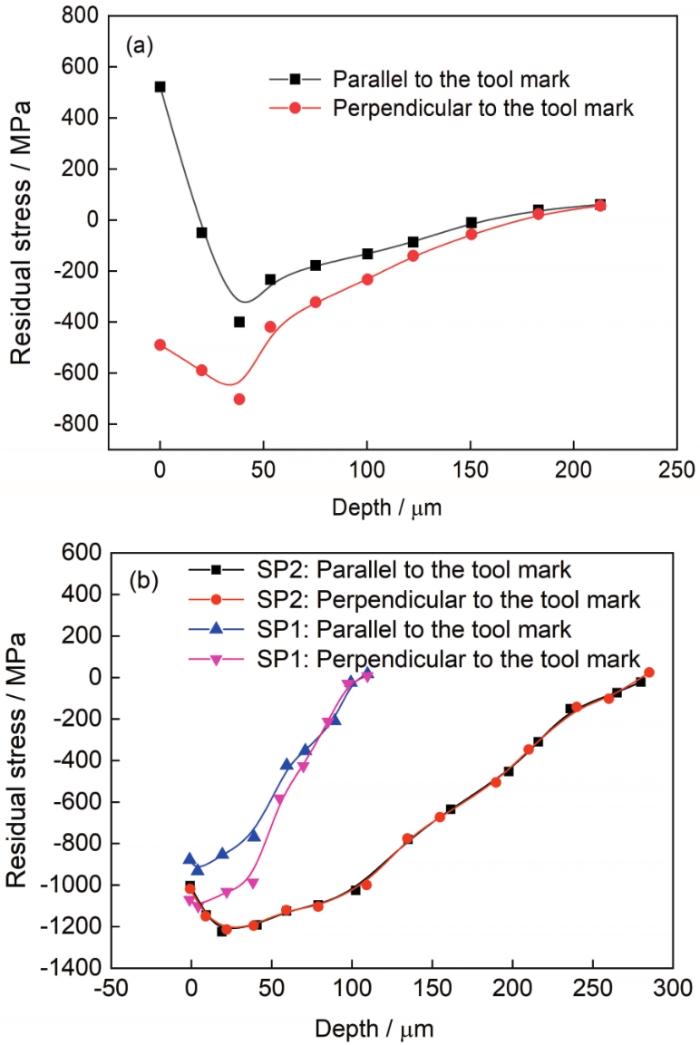
圖1 噴丸處理對FGH96合金表面硬化層殘余壓應力分布的影響[30]
Fig.1 Effects of shot peening on the residual compress-ive stress distribution of surface hardened layer of FGH96 alloy[30]
(a) before shot peening (turning)
(b) ceramic bead peening and compound shot peening (SP1—parallel to the tool mark, SP2—perpendicular to the tool mark)
1.2 高溫合金噴丸處理后的表面硬化層組織
噴丸處理過程中,高溫合金表面產生了理想殘余壓應力的同時,顯微組織亦發生了顯著變化。Zhao等[33]對GH4169合金噴丸強化的研究發現,經過噴丸強化后合金表面形成厚度約96 μm的硬化層,而且表面形成平均尺寸約為9 nm的等軸納米晶(圖2[33])。在一定深度范圍內還形成高密度形變孿晶,進一步細化了硬化層合金的顯微組織,提高了合金的高溫疲勞抗力。在IN718合金的研究[34]中發現,超聲噴丸處理也可獲得厚度約為90 μm、平均晶粒尺寸約為12 nm的表面納米晶層,有效地提高了合金的高溫疲勞抗力。噴丸處理中,高溫合金表面產生顯著塑性變形,必然引起位錯密度增加,并在晶界處形成大量的位錯塞積與纏結,這是噴丸處理獲得表面硬化層的根本原因。
圖2
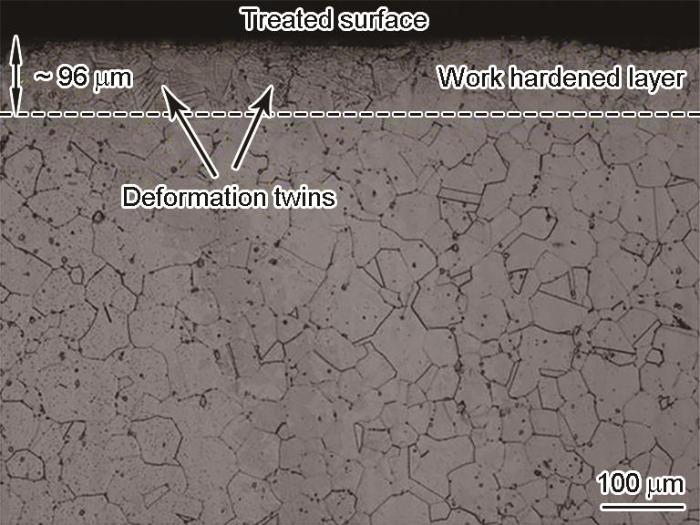
1.3 高溫合金噴丸處理后的表面粗糙度
圖3
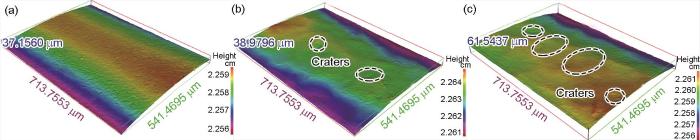
1.4 高溫合金表面噴丸強化的抗疲勞作用及影響因素
圖4
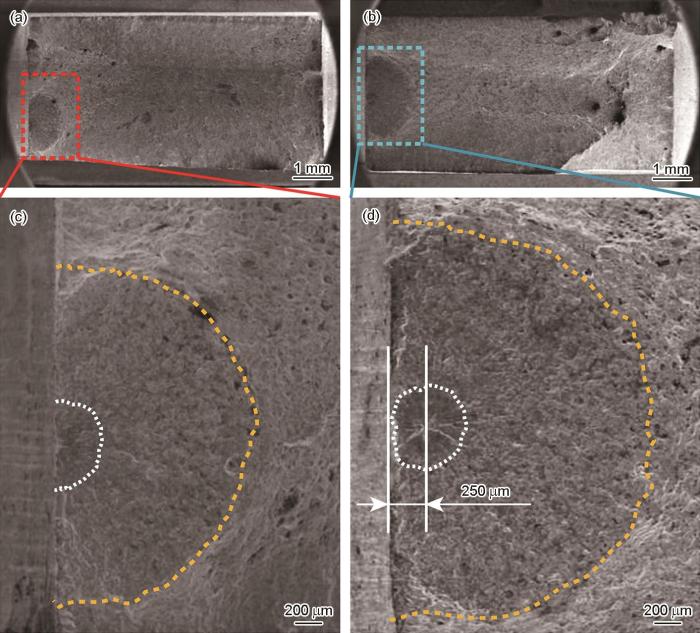
圖4 噴丸處理對Udimet 720Li合金相同載荷幅條件下疲勞裂紋萌生位置的影響[35]
Fig.4 Effects of shot peening on fatigue crack initiation location of Udimet 720Li alloy before (a, c) and after (b, d) shot peening under the same load amplitude[35] (Fig.4c enlarged for red frame in Fig.4a, Fig.4d enlarged for the lake blue frame in Fig.4b)
亦有研究表明,高溫合金噴丸處理的抗疲勞強化作用與應力狀態、應力幅值均有關。Dong等[35]對Udimet 720Li合金的研究發現,與未噴丸合金相比,噴丸處理后合金的缺口低周疲勞壽命顯著提高,其在1390和1070 MPa應力幅下的增幅分別為2.05倍和6.07倍。由此可見,噴丸處理在低應力水平下對提高疲勞壽命的作用更加顯著。此外,應力狀態還影響噴丸硬化層的殘余應力松弛程度。高玉魁等[31]對FGH97合金噴丸前后的不同應力狀態疲勞壽命進行對比,發現在630 MPa的低應力狀態下,噴丸硬化層的殘余壓應力可有效延緩表面裂紋萌生,提高合金的疲勞壽命。而在740 MPa高應力狀態下硬化層的殘余壓應力作用減弱,抗疲勞作用并不明顯。Luo和Bowen[38]對Udimet 720Li合金的研究也證實了600℃高溫條件下,在較低的應力幅范圍內,噴丸處理可提高合金的疲勞壽命;而當處于高應力幅時,噴丸處理反而降低了合金的疲勞壽命。
圖5

2 高溫合金的表面機械擠壓強化
2.1 高溫合金機械擠壓表面粗糙度
2.2 高溫合金機械擠壓硬化層組織及硬度
2.3 高溫合金機械擠壓硬化層的殘余壓應力
圖6
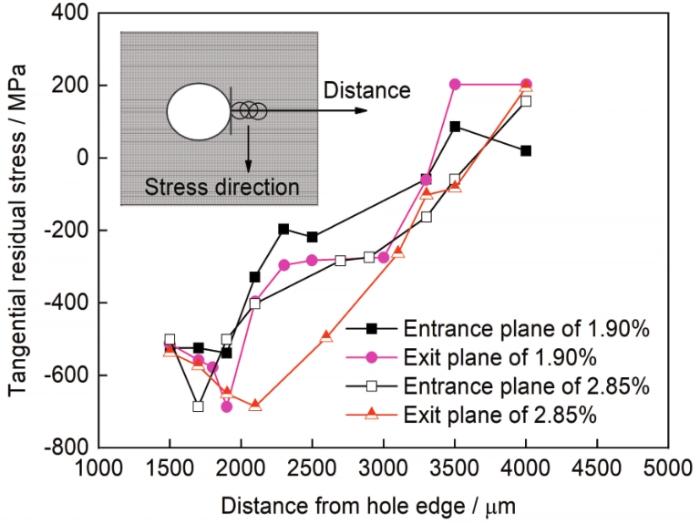
3 激光沖擊處理高溫合金表面強化
3.1 高溫合金LSP處理的表面粗糙度
圖7
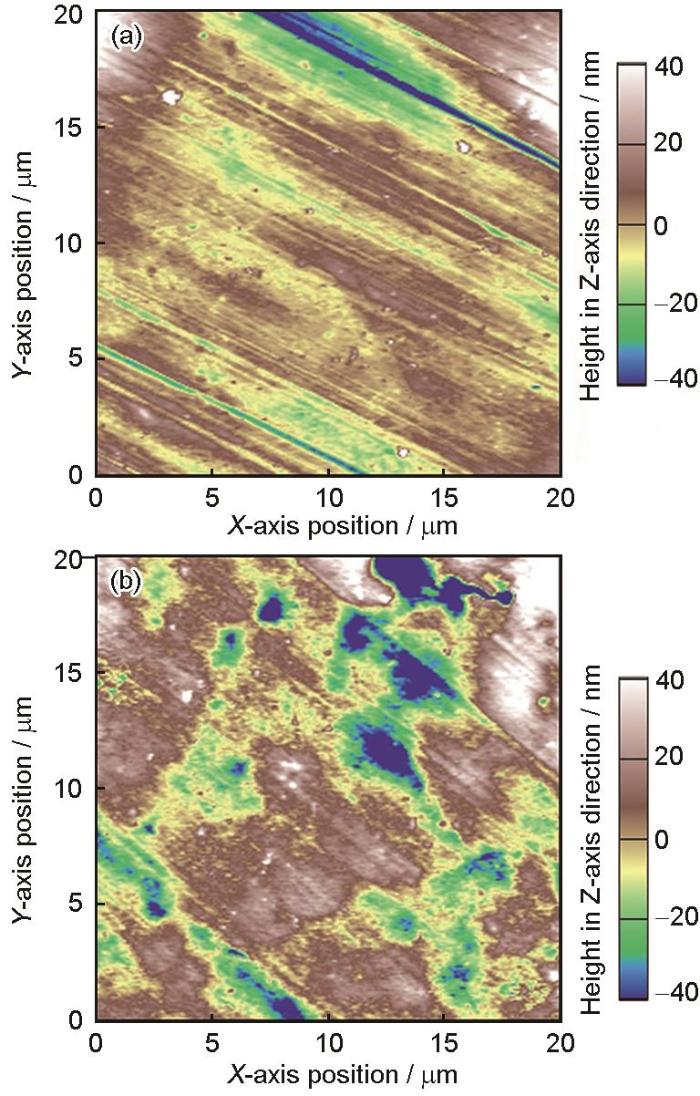
3.2 高溫合金LSP處理的硬化層組織及硬度
Rozmus-Górnikowska等[49]對Inconel 625合金LSP處理的研究發現,LSP處理后合金表面形成較大塑性變形,產生高密度位錯和密集分布的滑移帶,表面形成呈梯度分布的沖擊硬化層。Cao等[50]關于GH4586合金LSP處理的研究表明,LSP表面硬化層的位錯密度顯著增加,形成高密度纏結位錯、位錯壁和位錯胞結構,LSP處理后合金的疲勞壽命增加了近1倍。而且,LSP硬化層表面的平均晶粒尺寸降低約43.6%,同時發現基體中形變孿晶數量亦明顯增多,使GH4586合金LSP硬化層表面獲得了明顯的協同強化作用,硬度提高幅度達到27.4%。值得關注的是,經LSP處理的GH4586合金表層γ?相中也觀察到大量的層錯以及高密度位錯,這在傳統機械作用表面處理的高溫合金硬化層中未見報道。LSP處理后,GH4586合金硬化層中不同尺度、高密度微結構的形成與細化,有效抑制了疲勞裂紋的萌生和擴展,顯著提高了合金的疲勞抗力。Luo等[51]對K417合金進行LSP處理的研究發現,激光沖擊引入劇烈塑性變形,在合金表面產生更高密度的位錯纏結,硬化層表面形成納米晶,使表層硬度明顯增加。此外,LSP處理后進行900℃、10 h的保溫,K417合金硬化層中高密度位錯、晶粒細化等微結構特征并未見顯著變化,強化效果表現出了較好的高溫穩定性,這主要與LSP硬化層的高密度位錯與納米晶復合結構有關。
研究者們[12,13,19]對如何在高溫合金表面獲得高溫穩定的抗疲勞硬化層進行了大量的研究,發現引入溫度場的溫度輔助耦合激光沖擊強化技術(warm laser shocking processing,WLSP),可獲得高溫強化增幅更顯著的抗疲勞硬化層。本課題組[19,52]對比研究了LSP和WLSP處理IN718合金的表面硬化層微結構特征,發現WLSP作用下能夠在高溫合金表面獲得強化相/高密度位錯復合微結構(圖8[52])。而且,值得關注的是,IN718合金WLSP硬化層中的γ′′相內部觀察到高密度層錯及納米尺寸孿晶(圖8b[52]中藍色箭頭所示)。硬化層中有序強化相內部納米尺度微結構的形成和細化,顯著提高了硬化層的強化效果和高溫穩定性。
圖8
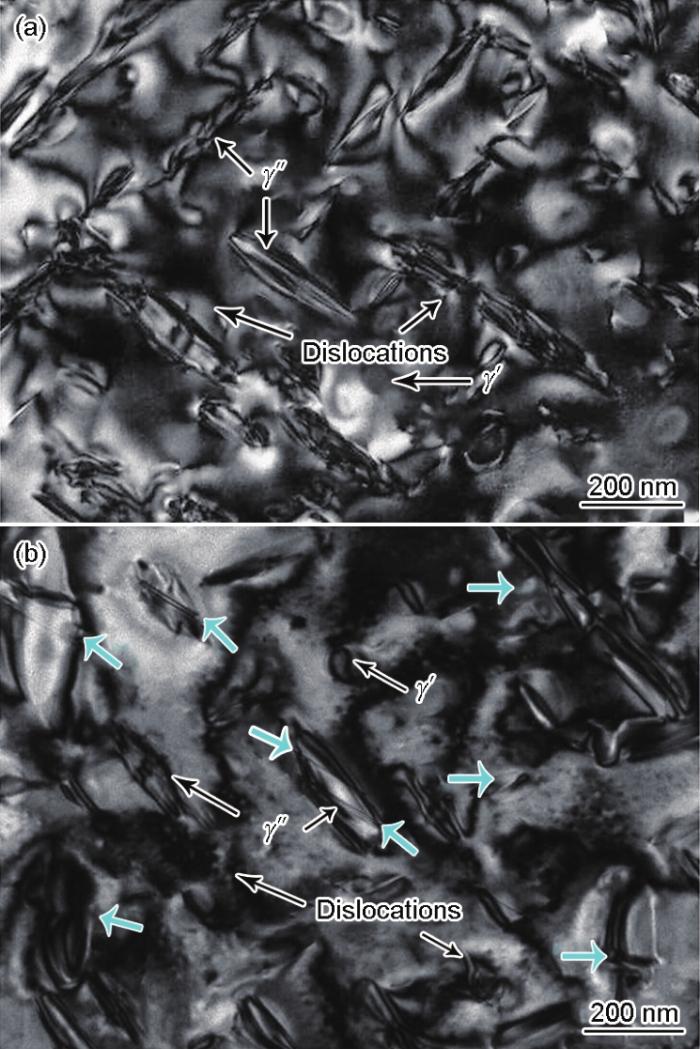
圖8 IN718合金LSP、溫度輔助耦合激光沖擊強化技術(WLSP)硬化層中的γ″相及位錯形態[52]
Fig.8 Morphologies of γ″ phase and dislocation patterns in the hardened layers of IN718 alloy treated with LSP (a) and warm laser shocking processing (WLSP) (Blue arrows show the γ″ phase/high-density dislocation complex structure containing stacking faults and nanosized twins) (b)[52]
3.3 高溫合金LSP處理的硬化層殘余應力狀態
圖9
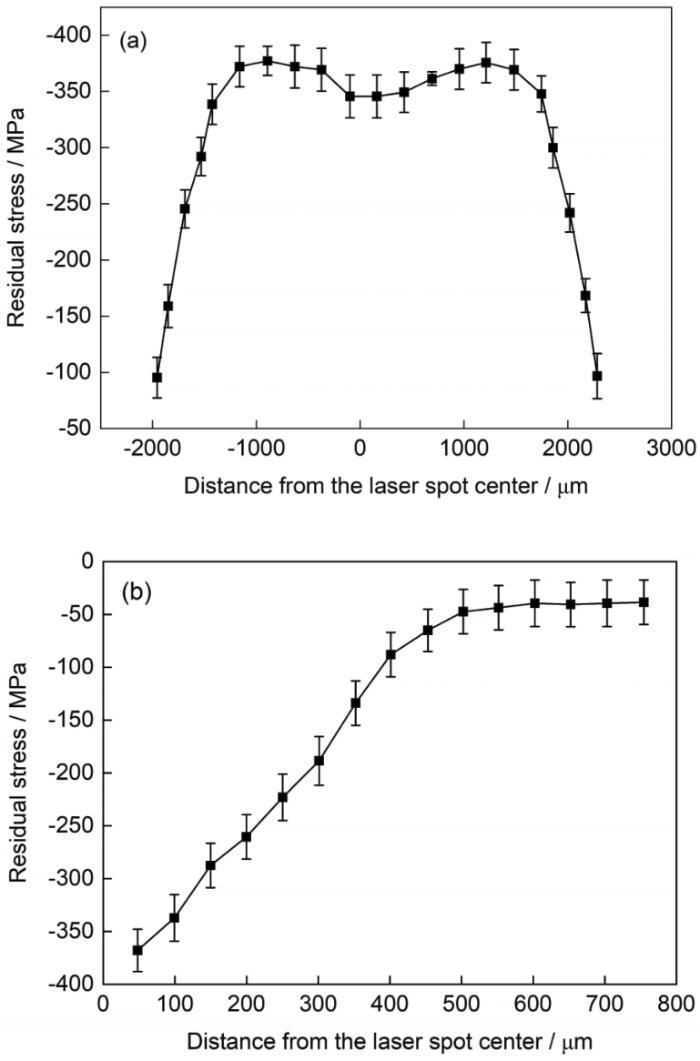
4 高溫合金的表面沖擊強化微觀機制
4.1 噴丸及機械沖擊表面硬化機理
高溫合金表面噴丸、機械擠壓處理硬化層的形成,主要是表面機械沖擊過程中基體劇烈塑性變形的結果[32~34,54~59],塑性變形程度及影響層深度與彈丸、機械沖擊的能量輸入直接相關。孔擠壓強化IN718合金孔內壁表面160 μm深度范圍內可觀察到明顯的旋轉塑性變形,越靠近內壁表面,變形程度越大[60]。RR1000合金經過噴丸處理后,表面硬化層劇烈塑性變形的晶粒比例明顯增加,形成大量亞結構[61]。FGH96合金[30]、FGH97合金[28]經噴丸處理后,硬化層小角晶界比例顯著增加。隨表面噴丸或機械沖擊能量輸入的增加,高溫合金硬化層表面發生了明顯的晶粒細化。對K417合金的噴丸硬化層進行后處理,亦可形成較大深度范圍的細晶硬化層,有效抑制表面疲勞裂紋的萌生[62]。
4.2 LSP和WLSP處理表面強化機理
圖10
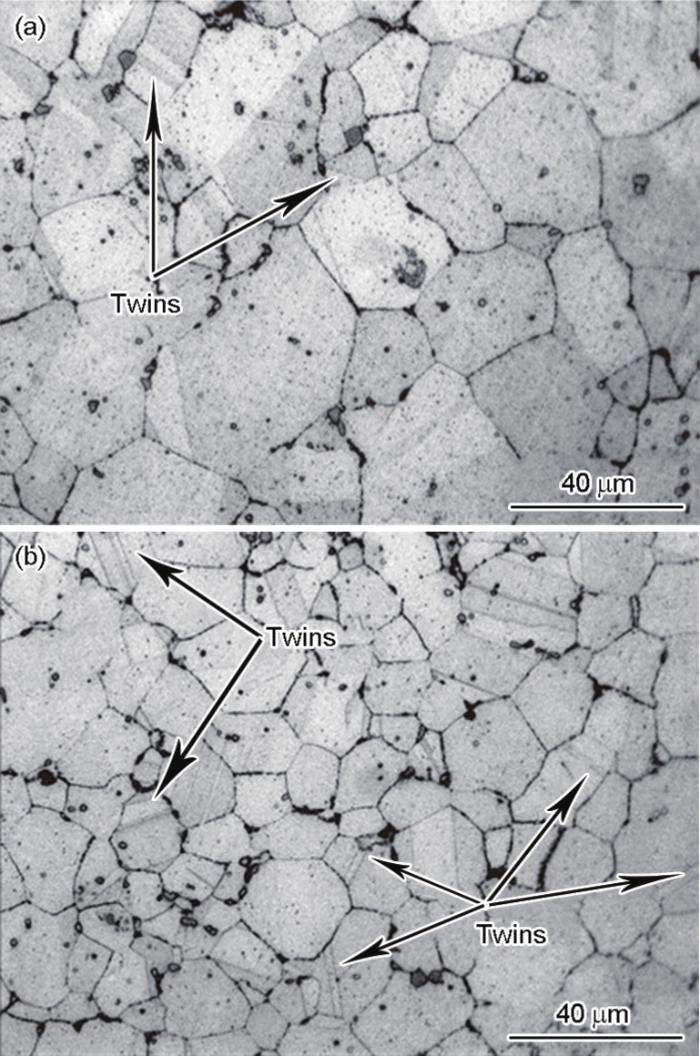
調整LSP處理參數可在高溫合金表面硬化層形成不同的組織結構。Yu等[64]對GH4169合金利用高能LSP、低能LSP和飛秒LSP處理調控硬化層微結構,發現飛秒LSP硬化層深度基本小于100 μm,而低能LSP處理后,合金硬化層深度增加,表面可誘導形成高密度亞結構。但由于能量輸入較低,低能LSP處理僅在距表面約100 μm范圍內形成了致密的亞結構,在100 μm以下的區域,主要以位錯的增殖或纏結為主,而未發現致密亞結構層。當提高輸入能量時,高能LSP處理的劇烈變形影響層深可達幾百微米甚至幾毫米,層深1400~1600 μm時,仍可觀察到致密亞結構。
圖11
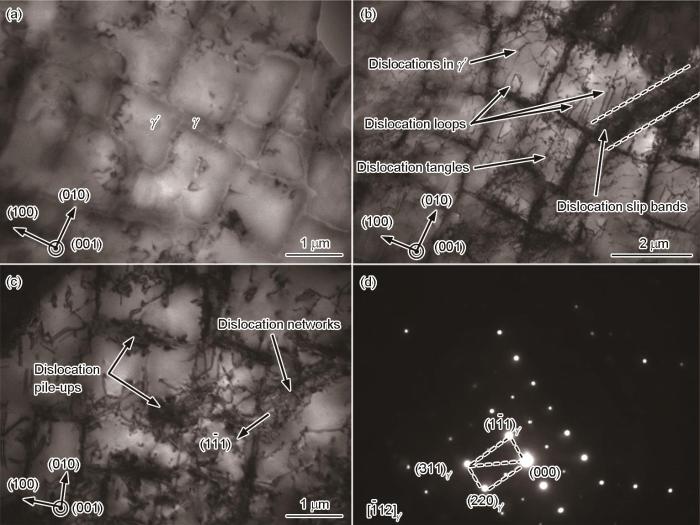
圖11 LSP處理對某鎳基單晶高溫合金表面硬化層基體位錯密度及γ′相內部微結構的影響[65]
Fig.11 Effect of LSP on the dislocation density of matrix and microstructure of γ′ phase in the surface hardened layer in nickel-based single crystal superalloy[65]
(a) untreated
(b-d) low (b) and high (c) magnified images of samples treated by LSP, and SAED pattern of Fig.11c (d)
圖12
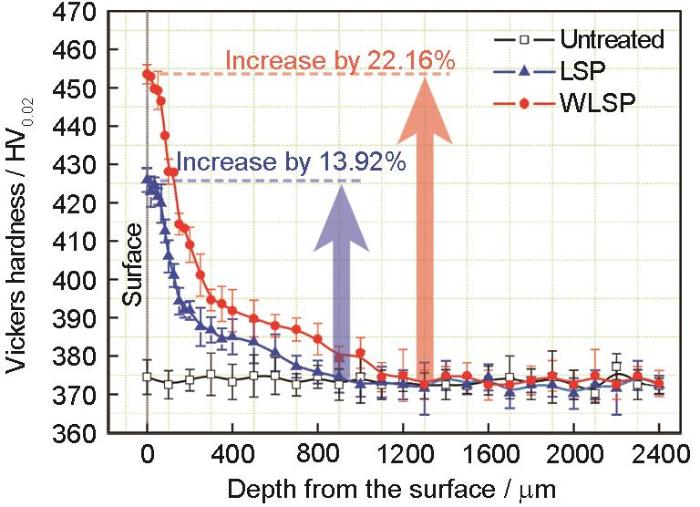
圖13
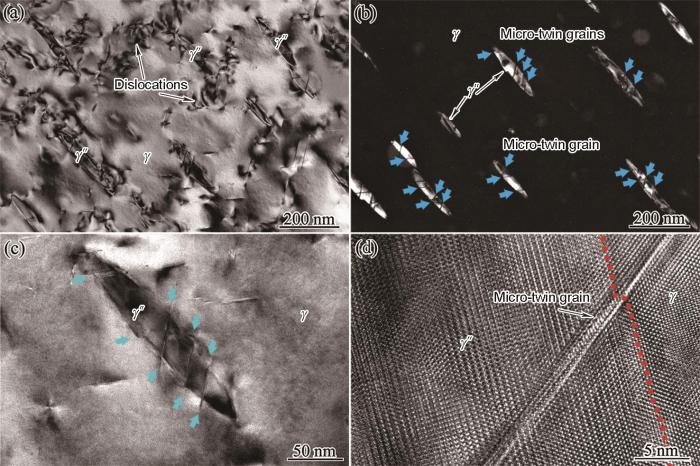
圖13 WLSP處理后IN718合金表面硬化層γ″相/高密度位錯復合體形態及強沖擊作用下γ″相中出現的微孿晶[19]
Fig.13 Morphologies of complex structure of γ″ phase/high-density dislocation and micro-twins in γ″ phase induced by strong impact in the surface hardened layer of WLSP-treated IN718 superalloy[19]
(a) morphology of complex structure of γ″ phase/high-density dislocation
(b) dark field morphology of γ″ phase in Fig.13a (Blue arrows show micro-twins)
(c) micro-twins in γ″ phase induced by strong impact (Blue arrows show micro-twins)
(d) HRTEM image of micro-twins at the γ/γ″ interface
圖14

圖14 經WLSP處理后IN718合金表面硬化層中γ″/γ界面細節的HRTEM像[52]
Fig.14 HRTEM images of the details of γ″/γ interface in the surface hardened layer of WLSP-treated IN718 superalloy[52] (a, d) HRTEM images of γ″/γ interface (a) and γ″ phase (d) in the surface hardened layer (Insets show fast Fourier transform (FFT) diffraction patterns) (b, e) magnified parts in the red boxes in Fig.14a (b) and Fig.14d (e), showing HRTEM images and corresponding maps of the geometric phase images (GPA) strain component εxx (εxx —x-direction in-plane strain) (c, f) line profiles of strain maps scanned along lines 1, 2, and 3 in Fig.14b (c) and lines 4, 5, and 6 in Fig.14e (f)
WLSP處理IN718合金硬化層中這種特殊結構貫穿γ″/γ相界面,其改變了γ″/γ相界面形態,使得γ″相內部及其周圍應變分布的復雜程度提高。這種特殊結構勢必阻礙高溫服役下位錯反應和位錯回復。同時,高溫下這些高密度位錯包裹、內含微孿晶的γ″相,其長大以及γ″→δ相轉變的復雜程度均將加劇。
綜上,高溫合金表面LSP和WLSP硬化層的強化本質,除劇烈塑性變形在基體中引入的高密度缺陷及亞結構和大量形變孿晶外,還包括在γ'、γ″主要相內部誘導形成大量層錯、微孿晶等特殊微結構。與傳統噴丸處理和表面機械沖擊/擠壓強化相比,LSP和WLSP處理合金表面硬化增量更顯著、硬化層更深,并且形成了穩定強化相/高密度位錯復合結構和劇烈塑性變形亞結構,有利于提高高溫合金的表面強化和抗疲勞能力。那么,如能利用耦合場在硬化層引入更多微納尺度“異質結構(heterostructure)”[66~68]、“化學界面工程(chemical boundary engineering)”[69,70]等強化因素,有望在高溫合金表面處理過程中收獲更顯著的強韌化效果。
5 高溫合金表面強化的高溫穩定性
5.1 硬化層高密度亞結構的演化與位錯反應
王欣等[42]對比研究了孔擠壓GH4169合金在400和600℃條件下抗疲勞強化的高溫穩定性。發現,即使孔擠壓合金獲得了明顯的強化;但高溫下,位錯運動激活能降低、位錯運動能力增加,殘余壓應力易發生應力松弛,硬化層的疲勞抗力降低;當溫度提高到600℃時,基體高密度位錯的強化作用下降更加明顯。
圖15
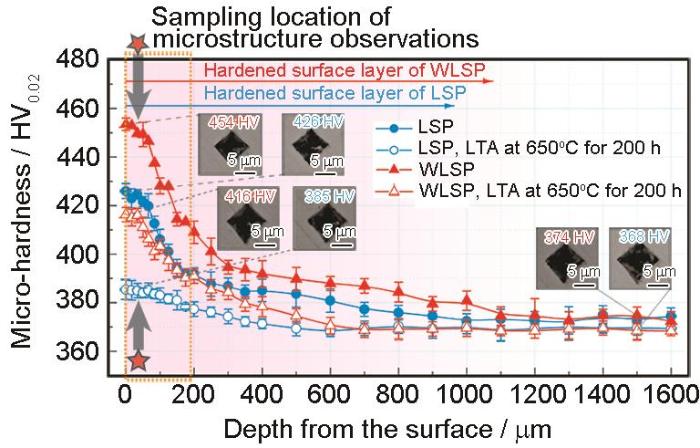
基體中高密度位錯缺陷在高溫下的快速演化,在經表面機械沖擊/擠壓、LSP和WLSP硬化層中普遍發生。機械沖擊/擠壓處理的高溫合金硬化層,由于表面強化的主要微結構為高密度缺陷,高溫下這些缺陷的減少,導致硬化層穩定性降低、強化作用退減。
5.2 高溫下硬化層細晶組織及形變孿晶的演化
超細晶(納米晶)層并非高溫合金表面硬化層的普遍性微結構特征,多出現在高能機械沖擊/擠壓疊加硬化層和LSP硬化層表面,其分布深度也僅約100 μm。高溫時效中,表面晶粒長大迅速,硬化層穩定性降低。而高溫合金表面硬化層的形變孿晶比納米晶更為常見,且生成深度達200~500 μm,是高能機械沖擊/擠壓處理高溫合金硬化層的典型微結構特征。Zhao等[33]研究GH4169合金超聲噴丸硬化層形變孿晶高溫穩定性發現,350℃保溫后硬化層形變孿晶無明顯改變;當溫度升高至650℃時,孿晶間距明顯加寬,導致硬化層的硬度降低。
5.3 沖擊誘導強化相內部微結構的高溫穩定性
研究[65,81~93]發現,與機械沖擊/擠壓硬化層相比,LSP和WLSP處理硬化層在高溫長期時效后的抵抗疲勞裂紋萌生、擴展方面更具優勢。Buchanan等[82]對比研究了IN100合金的噴丸處理、LSP處理硬化層的高溫應力松弛,發現650℃、100 h時效后,噴丸硬化層最大殘余壓應力下降約800 MPa,而LSP處理的僅下降200 MPa (圖16[82])。可見,LSP處理除使表面強化幅度和硬化層深度明顯增加外,硬化層高溫服役的穩定性也更佳。Lu等[83]研究GH4169合金WLSP硬化層的高溫長期時效組織、性能穩定性發現,WLSP硬化層的殘余應力降低幅度明顯小于LSP硬化層。而且,600℃的時效未觀察到表面殘余壓應力的顯著改變。但當時效溫度升高至650℃時,LSP硬化層的殘余壓應力幾乎完全釋放,而WLSP處理的殘余壓應力僅降低約8%。當時效溫度增加到700℃時,WLSP硬化層的殘余應力在時效100 h后仍可保持在原來的50%左右,表現出極高的高溫穩定性。
圖16

本課題組[81]對長期時效后LSP和WLSP處理IN718合金的硬化層硬度進行了系統對比,發現600和650℃時效200 h后,LSP和WLSP硬化層硬度、深度均有所降低。但經過650℃及以下溫度長期時效后,WLSP處理的IN718合金表面硬化層硬度、深度的降低幅度均小于LSP處理(圖17[81])。尤其是,WLSP處理合金經650℃、200 h長期時效后表面硬度增量的下降幅度僅為40.79%,而相同時效條件下LSP處理合金表面硬度增量的下降幅度達71.69%。680℃、200 h時效后,LSP處理合金的表面硬化現象幾乎完全消失,而此時WLSP處理合金表面硬度仍保持一定的增量。研究[81]還發現,表面硬化層的強化增量主要來源于LSP和WLSP處理后合金中的高密度位錯增殖和塞積(圖18[81])。尤其對于WLSP硬化層而言,更顯著的強化作用主要來源于硬化層γ″相/高密度位錯復合微結構。同樣,WLSP硬化層的強化現象在600℃以上長期時效后仍得以保持,也主要取決于WLSP處理誘發的高密度位錯和特殊亞結構。
圖17
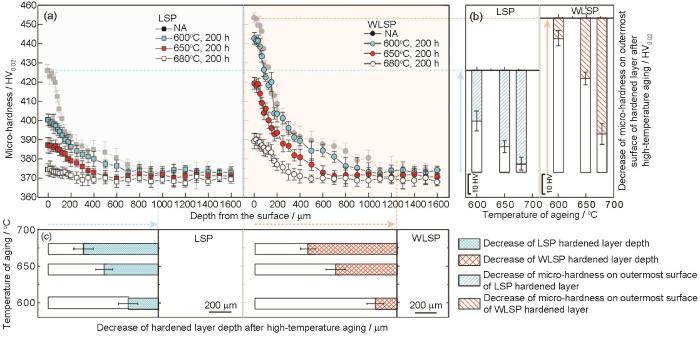
圖17 不同溫度長期時效后IN718合金LSP和WLSP硬化層硬度分布及硬化層深度變化[81]
Fig.17 Micro-hardness distributions and depth changes of the surface hardened layer of LSP and WLSP IN718 alloys after aging at high temperatures (NA—non-aging)[81]
(a) micro-hardness of surface hardened layer after aging at different temperatures treated by LSP and WLSP
(b) comparison of micro-hardness of hardened layer
(c) comparison of hardened layer depth
圖18
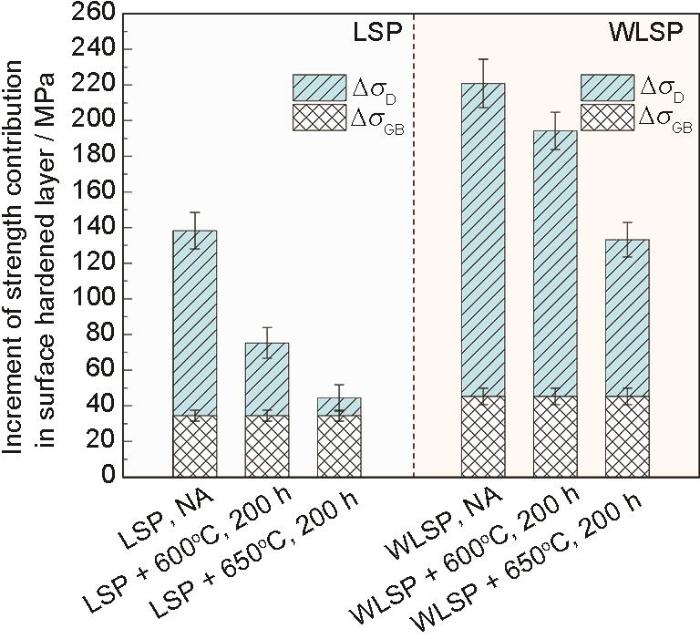
圖18 長期時效對LSP和WLSP處理的IN718合金表面硬化層強化機制貢獻增量的影響[81]
Fig.18 Effects of long-term aging on the contribution increment of strengthening mechanism of the surface hardened layer of LSP and WLSP IN718 alloys[81] (ΔσD—strength contribution from dislocation strengthening, ΔσGB—strength contribution from grain boundary strengthening)
本課題組[54]在研究長期時效后LSP和WLSP處理IN718合金表面硬化層的幾何必需位錯(geometrically necessary dislocation,GND)演化行為發現,WLSP硬化層的GND密度明顯高于LSP處理,升高幅度約為248.71% (圖19[52])。硬化層中GND密度的增加,除形成各向同性強化外,更重要的是可產生更加顯著、穩定的背應力強化。經長期時效處理后,LSP硬化層中的GND密度明顯降低,而WLSP硬化層的GND密度雖有降低,但降幅很小。而且長期時效后,LSP處理合金GND密度統計分布的相對頻率峰位,向低位錯密度方向發生了明顯的移動,同時相對頻率峰值也呈現出明顯的上升趨勢。但WLSP硬化層在長期時效后GND密度統計分布相對頻率的峰值、峰位、峰寬無明顯變化。這進一步說明,WLSP處理不僅僅使IN718合金獲得了更高的GND密度,而且GND密度的集中程度和分布位置變化并不明顯,WLSP處理合金均表現出了比LSP處理合金更顯著的高溫長期服役穩定性。
圖19
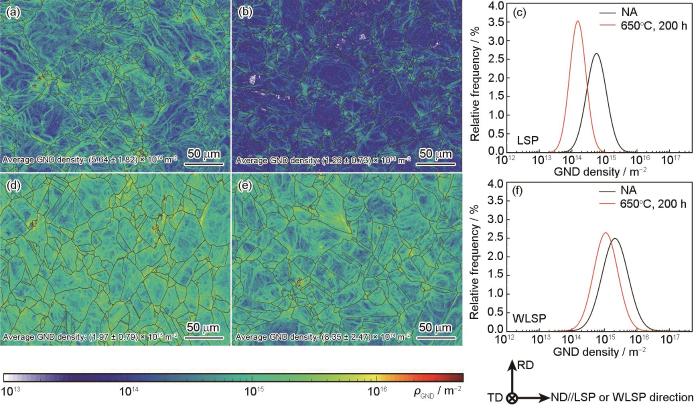
圖19 650℃長期時效后LSP和WLSP處理IN718合金表面硬化層的幾何必需位錯(GND)密度分布圖及正態分布統計圖[52]
Fig.19 Geometrically necessary dislocation (GND) density (ρGND) maps (a, b, d, e) and corresponding normal distribution statistical diagrams of GND density (c, f) of the surface hardened layer of LSP (a-c) and WLSP (d-f) IN718 alloys before (a, d) and after (b, e) long-term aging at 650oC[52] (RD—rolling direction, TD—transverse direction, ND—normal direction)
6 總結與展望
本文基于先進渦輪動力系統用鎳基高溫合金的典型表面強化技術,以及強化作用高溫穩定性的研究和應用分析,就鎳基高溫合金表面沖擊強化總結與展望如下。
(1) 高溫合金的表面機械噴丸、擠壓/滾壓強化處理,均可產生明顯殘余壓應力和硬化層,有效阻礙裂紋在表面萌生,從而提高高溫合金的疲勞抗力。但應用中需注意控制噴丸處理造成的表面粗糙度增大、擠壓/滾壓處理的殘余壓應力梯度調控以及表面機械強化超過500℃后的強化作用衰減。
(2) LSP和WLSP處理等表面高能沖擊強化技術具有不受構件規格、形狀限制的獨特優勢,同時其強化增幅及層深均優于機械表面強化處理,由此經其處理的高溫合金顯示出更高的疲勞抗力。WLSP處理在高溫合金表面硬化層中形成的“有序強化相/高密度位錯復合特殊微結構”,進一步提升了表面強化的作用效果。
(3) 硬化層微結構的高溫、長時穩定性,是高溫合金表面強化技術飛躍發展與深入應用的關鍵。高溫合金表面劇烈塑性變形產生的基體微結構中,高密度缺陷的高溫演化與回復顯著,不具備高溫穩定能力。表面細晶(納米晶)層較淺,高溫下長大傾向明顯,穩定性亦不足。而形變孿生可在600℃以下保持一定的高溫穩定性。耦合場高能強沖擊(LSP和WLSP等)處理在獲得上述基體微結構的同時,誘導γ′、γ″相內部形成內含大量層錯、微孿晶的“強化相/高密度位錯復合特殊微結構”,是使硬化層兼具強化作用、高溫穩定性與長時穩定性的關鍵特殊微結構。
(4) WLSP處理在高溫合金表面沖擊強化作用高溫穩定性方面所凸顯的優勢,啟發人們應關注硬化層不同尺度關鍵微結構的綜合調控。如能利用高能沖擊耦合場將諸如“異質結構”、“化學界面工程”等微納尺度強韌化理念引入高溫合金的表面微結構精準設計,在硬化層精準誘導“有序強化相/高密度位錯特殊微結構”的梯度分布,構筑具有更高高溫強度與高溫穩定性的表面硬化層,將有望開辟高溫合金表面強化相關研究的新方向。
免責聲明:本網站所轉載的文字、圖片與視頻資料版權歸原創作者所有,如果涉及侵權,請第一時間聯系本網刪除。
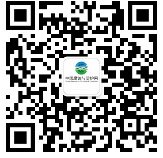
官方微信
《腐蝕與防護網電子期刊》征訂啟事
- 投稿聯系:編輯部
- 電話:010-62316606
- 郵箱:fsfhzy666@163.com
- 腐蝕與防護網官方QQ群:140808414