鈦合金因其優異的比強度、高溫性能、耐腐蝕性和生物相容性,在航空航天、船舶制造、生物醫學及高端制造領域廣泛應用。鈦合金的顯微組織結構對其力學性能有著至關重要的影響,是研究和優化鈦合金性能的核心內容之一。顯微組織的類型、形態及其分布不僅決定了材料的強度、塑性和韌性,還對疲勞性能和斷裂韌性起到關鍵作用。本篇文案旨在系統梳理鈦合金顯微組織結構的常見檢測方法,包括光學顯微鏡(OM)、掃描電子顯微鏡(SEM)、透射電子顯微鏡(TEM)等技術,以及現代化手段如電子背散射衍射(EBSD)和原子力顯微鏡(AFM)的應用。同時,我們將探討顯微組織與力學性能之間的內在聯系,為鈦合金材料的研發與應用提供參考。
無論是鈦合金中的組織形態,還是相變,都需要相應的檢測方法進行判定。一般鈦合金中,只要檢測到某相,就可以認定合金中發生了某種相變,所以組織形態和相的檢測是認識鈦合金顯微組織結構的基礎。目前鈦合金中最常用的檢測儀器有光學顯微鏡(optical microscope,OM)、掃描電子顯微鏡(scanning electron microscope,SEM),X射線衍射(X ray diffraction,XRD)和透射電子顯微鏡(transmission electron microscope,TEM)。 光學顯微鏡(又稱金相顯微鏡)利用垂直或近似垂直的入射光照射試樣表面,通過反射光線成像。由于試樣表面對光反射能力的差異,需通過腐蝕處理展現晶粒、晶界及析出物的顯微形貌,不同區域的抗腐蝕能力導致反射效果不同,從而形成可觀察的組織結構。 在鈦合金研究中,光學顯微鏡主要用于以下幾個方面: 組織形態的判定 基體和析出相尺寸的測量 析出物數量的分析與對比 需要注意的是,光學顯微鏡通過腐蝕痕跡來判定組織結構,但其放大倍數限制了精細結構的觀察能力,同時對析出物的成分、類別和結構無法提供深入分析。此外,腐蝕痕跡可能受加工應力、內部缺陷和變形過程中產生的層錯帶等因素影響,這可能對組織形態和析出物的準確判定產生干擾。 掃描電子顯微鏡(掃描電鏡)通過電子束掃描樣品表面,利用激發出的信號成像,常用于觀察表面形貌(如斷口)及成分分布。在鈦合金研究中,普通掃描電鏡的應用較為有限,其主要功能是對金相組織的放大(分辨率可達1 nm,放大倍數達20萬倍)。鈦合金熱處理中的關鍵是識別細小的第二相析出,但在掃描電鏡下,這些析出物通常表現為腐蝕坑,僅能部分反映其位置和數量,與光學顯微鏡作用類似。相比普通成像,掃描電鏡的輔助成像和分析工具更具價值,常用方法包括: 背散射電子成像 二次電子成像 能譜分析 掃描電鏡的綜合功能可實現析出物的形貌和成分分析,及元素在熱處理過程中的偏聚分析。然而,由于鈦合金中析出物通常較細小(在SEM中表現為腐蝕坑),且多為同素異構相變(成分相同),其在鈦合金固態相變研究中的應用仍較為有限。 X射線衍射(XRD)通過晶體中的衍射現象分析材料的晶體結構、晶格參數、晶體缺陷、相含量及內應力等。由于制樣方便、測試簡單、能同時檢測所有衍射相,XRD在鈦合金相變研究中應用廣泛。 XRD檢測的核心在于比對PDF卡片,目前鈦合金主要相的卡片已納入分析軟件。通過觀察不同處理條件下XRD圖中衍射峰的變化,可判斷合金熱處理過程中發生的相變。例如:亞穩相的同素異構相變:難以判斷,通常需透射電鏡分析;若通過XRD解決,可大幅節省資源。β相分離反應(β→β+β'):XRD可通過衍射峰寬化反映晶格常數變化,顯示分離反應的存在。馬氏體α''相識別:由于α''相與α相晶格參數的不同,XRD圖中衍射峰會出現分裂,可通過對比標定α相和α''相。 表1 α''相晶面間距、譜線強度和衍射角 表2 w相的晶面間距、譜線強度和衍射角 相較于同素異構相變,XRD更容易判斷共析和有序化反應生成的相,但其應用仍受到局限。主要問題包括:析出物定量分析難度大:衍射峰強度雖與析出物的量相關,但受到吸收因子、組織織構及未知相衍射峰疊加等多種因素影響,難以準確判定析出物的數量。檢測靈敏度限制:析出物需達到一定量(通常超過1%-5%)才能產生衍射峰,而鈦合金中共析元素含量較低,生成的共析產物往往不足以被XRD檢測。這些限制使XRD在鈦合金析出物和相變分析中的應用受到一定制約。 透射電子顯微鏡(TEM)利用電子束透過薄膜樣品成像,可以同時觀察樣品微觀組織形態和鑒定晶體結構,其分辨率高達0.1 nm,放大倍數達10^6倍。在鈦合金研究中,TEM彌補了光學顯微鏡、掃描電鏡和X射線衍射的局限性,尤其在檢測微量析出物和重要相變時具有關鍵作用。以下是TEM在鈦合金相變分析中的應用: 馬氏體相變 高溫淬火生成的六方結構α′相和斜方結構α″相可通過選區電子衍射(SAED)判斷,其針狀組織在明場像中的表現與生成條件相關。 ω相變 ω相的晶體結構和與β相的位相關系使得在β相衍射花樣上出現附加衍射點(位于1/3和2/3處)。等溫ω相呈分散細小的橢球狀,無熱ω相呈立方形,均可通過TEM觀察到形貌和結構特點。 β相分離反應(β → β富 + β') β相分離反應類似于調幅分解,但其組織周期性源于形核和長大過程。TEM可通過形貌觀察和電子衍射斑點的位移或扭曲分析這一反應。 有序化反應 電子衍射能有效檢測有序化反應,如α相向α2長程有序相的轉變。此過程中會在電子衍射花樣上出現超點陣衍射斑點,反映了晶體結構的有序化。 盡管TEM在鈦合金相變分析中的作用顯著,但仍存在一些局限: 制樣復雜且成本較高,例如需粒子減薄處理。 檢測目標相的觀察難度大,需大量實驗驗證。 對操作技術要求高。 這些因素限制了TEM的普及應用,但在鈦合金研究中,TEM仍是不可替代的工具。 在鈦合金相分析檢測過程中,首先應根據合金成分和熱處理特點對可能析出的相進行預判,明確可能出現的相的結構和形貌特征。接著,根據不同檢測方法的適用范圍,有針對性地進行選擇和應用,這是進行鈦合金相變研究的基本思路。在實際檢測過程中,應逐步推進、循序漸進,避免毫無目的地同時使用多種檢測手段,這樣不僅會浪費大量實驗資源,還可能導致得到一些無意義的實驗結果。 鈦合金的組織結構不僅包括不同相的分布、晶粒的大小、形貌等微觀特征,還與合金的成分、熱處理工藝等因素密切相關。鈦合金的顯微組織結構決定了其力學性能,在生產實踐中,通常根據所需的力學性能反推最優組織狀態,并通過優化熱加工和熱處理工藝來實現。這一過程中,組織與性能的關系至關重要。通過深入分析鈦合金顯微組織的演變規律和力學性能之間的相互關系,可以為鈦合金的設計和應用提供理論依據,為開發更高性能的鈦合金材料提供技術支持。
光學顯微鏡是判定鈦合金組織形態的主要工具,可清晰區分雙態組織、網籃組織、等軸β晶組織和片層組織等結構,這些組織形態對材料性能具有重要影響。
借助光學顯微鏡的比例尺,可以準確測量基體晶粒的大小,以及析出相如β晶粒、初生α相和片層α相的尺寸。這些尺寸是評價鈦合金微觀結構的重要參數。
光學顯微鏡能夠反映熱處理過程中析出物的數量及分布情況。通過對析出物數量的比較,可以評估合金加工和熱處理工藝的合理性,盡管難以精確定量分析,但仍具有重要參考價值。
背散射電子源自樣品表層幾百納米深度,信號強度與原子序數有關,可用于形貌分析和定性成分分析。該技術在斷口分析中應用廣泛,可通過間隙元素分布(原子序數較低)判斷合金斷裂失效機制。
二次電子從樣品表面5-10 nm深度發射,能敏銳捕捉表面形貌,適用于斷口分析。通過觀察斷口形貌,有時可推斷熱處理過程中的相變情況。
基于元素特征X射線進行點、線、面成分分析,為判斷析出物提供證據,但無法解析結構。
通過大量測試和實踐,鈦合金的組織與力學性能之間的關系已達成共識。四種典型組織形態與力學性能的關系表明,每種組織都有其優勢和劣勢。然而,現代航空材料的復雜服役條件要求材料具備更好的綜合力學性能,而這一要求與現有材料性能的局限性之間存在矛盾。為了解決這一問題,工藝創新不斷推進,如近β、準β和多重熱處理技術,通過優化組織形態以獲得更好的綜合力學性能,盡管這些方法可能會犧牲一些工藝的便利性。
表3 鈦合金四種典型組織形態與合金力學性能的一般關系
顯微組織對室溫強度和塑性的影響
一般認為,隨著初生α相含量的增加,合金的強度會下降,而塑性則會提高。因此,從等軸組織到雙態組織再到片層組織,合金的塑性逐漸降低,強度逐漸升高。在不同組織狀態下,TC4合金的室溫力學性能表現有所不同,具體見表4。
表4 不同組織狀態下TC4合金的室溫力學性能
顯微組織對斷裂韌性和裂紋擴展速率的影響
通過大量研究,已得出一些關于組織對鈦合金斷裂韌性和裂紋擴展速率影響的規律。通常,在β區變形或β區熱處理獲得的片層狀組織結構,能夠提供更高的斷裂韌性和抗裂紋擴展速率。這是因為原始β晶界和α集束的影響,使裂紋容易分叉并形成次生裂紋,因此裂紋在片狀組織中的擴展路徑更為曲折,從而增加了裂紋的總長度,消耗更多的能量。兩種典型組織狀態下,TC4合金的性能見表4,而不同組織狀態下,TC11合金的性能見表5。
表4 兩種典型組織狀態下TC4合金的性能
機械性能 |
魏氏組織 |
等軸組織 |
拉伸強度/MPa |
1020 |
961.1 |
延伸率/% |
9.5 |
16.5 |
斷面收縮率/% |
19.5 |
45 |
斷裂韌性/(MPa·m1/2) |
102 |
58.9 |
表5 不同組織狀態下TC11合金的性能
組織類型 |
熱處理制度 |
Rp0.2/MPa |
A/% |
斷裂韌性/(MPa·m1/2) |
等軸組織 |
雙重退火 |
1018 |
14.8 |
73.1 |
網籃組織 |
雙重退火 |
1083 |
12.8 |
91.9 |
雙態組織 |
強韌化 |
1098 |
16.8 |
88.6 |
顯微組織對合金熱強性的影響
鈦合金的熱強性是指材料在高溫下抵抗變形的能力,通常關注的性能包括高溫下的瞬時強度、持久強度和蠕變強度。研究表明,片狀組織的熱強性優于球狀組織。當晶粒尺寸增大并且晶粒結構從球狀轉變為片狀時,持久強度首先增加然后降低,而合金的抗蠕變能力隨著β晶粒尺寸的增大而提高。在鈦合金的四種典型組織形態中,網籃組織的熱強性最強,具備最佳的高溫拉伸強度、持久強度和蠕變強度綜合性能,其次是魏氏組織,而等軸組織的熱強性最差。TC11合金的熱強性與組織類型的關系見表6。
表6 TC11合金的熱強性與組織類型的關系
組織對疲勞性能的影響
在對稱循環高頻應力作用下,光滑試樣的疲勞強度與組織類型密切相關。研究表明,等軸組織的疲勞強度優于片狀組織,同時,組織越細小,疲勞性能越好。在四種典型組織狀態中,等軸組織的疲勞性能最好,其次是雙態組織,再次是網籃組織,魏氏組織的疲勞性能最差。表7展示了不同組織對TC6合金疲勞性能的影響。
表7 不同組織對TC6合金疲勞性能的影響
表8 材料選材判據與組織性能的關系
選材要素 |
主要力學性能表征 |
最優的組織狀態 |
“未損傷”材料的靜強度及剛度 |
室溫強度 |
片層組織 |
室溫塑性 |
等軸組織 |
|
“未損傷”材料的疲勞性能 |
高周疲勞 |
等軸組織 |
低周疲勞 |
片層組織 |
|
高溫使用時的蠕變、持久和熱穩定性 |
高溫蠕變 |
片層組織 |
高溫持久 |
片層組織 |
|
熱穩定 |
等軸組織 |
|
有損傷材料的靜強度 |
斷裂韌性 |
片層組織 |
有損傷材料的疲勞性能 |
裂紋擴展速率 |
片層組織 |
高溫鈦合金的顯微組織設計
實際應用中高溫鈦合金需要在室溫性能、高溫強度、蠕變性能、熱穩定性、疲勞性能和斷裂韌性等方面達到良好的匹配,特別是熱穩定性、高溫蠕變性能和疲勞性能的平衡。IMI834合金通過采用15%初生α相的雙態組織,在兩相區上限溫度進行固溶處理,以兼顧蠕變和疲勞性能。大于15mm的坯料采用油冷,小于15mm的坯料采用空冷,并在700℃時效處理。此外,合金中加入0.06%C以擴大兩相區熱處理溫度范圍,更好地控制初生α相含量。圖1顯示了IMI834合金的最佳熱處理區及對應的組織形態。
圖1 IMI834合金最佳熱處理區及其對應的組織形態
為了提高蠕變性能,Til100合金鍛件的生產推薦采用β鍛造和直接時效的熱加工工藝,獲得片層組織。具體工藝是在相變點以上25~55℃范圍內進行鍛造,鍛造后直接進行600℃/8小時的時效處理。該工藝減少了一次高溫熱處理,簡化了生產流程,降低了成本。圖2顯示了Ti1100合金使用狀態的組織形態。
圖2 Ti1100合金使用狀態的組織形態
高強韌鈦合金的組織設計
高強韌鈦合金在兼顧多種性能時需要協調組織特性,通常選擇介于等軸組織和片層組織之間的“中間”組織狀態,并采用復雜的鍛造與熱處理工藝。例如,Ti62222合金通過三重熱處理實現拉伸性能、斷裂韌性和抗疲勞裂紋擴展性能的優化;Ti17合金通過雙固溶+時效工藝獲得綜合性能良好的組織;Ti5553合金通過雙重時效調整析出相的位置和形態,獲得優異的綜合力學性能。
典型的設計思路包括近β鍛造、準β鍛造和鍛后水冷技術。近β鍛造在細化初生等軸α相含量的同時,增加次生條狀α和時效α相,提升韌性和抗疲勞裂紋擴展能力;準β鍛造基于網籃組織的綜合性能優勢,進一步優化工藝;鍛后水冷通過細化片層和條狀α相,提高合金的斷裂韌性和抗裂紋擴展能力。這些方法有效平衡了高強韌鈦合金的多項性能需求。
免責聲明:本網站所轉載的文字、圖片與視頻資料版權歸原創作者所有,如果涉及侵權,請第一時間聯系本網刪除。
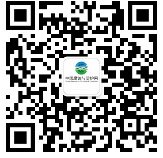
官方微信
《腐蝕與防護網電子期刊》征訂啟事
- 投稿聯系:編輯部
- 電話:010-62316606
- 郵箱:fsfhzy666@163.com
- 腐蝕與防護網官方QQ群:140808414