-
0 前言
-
熱障涂層(Thermal barrier coatings,TBCs)是一種將陶瓷材料涂覆在合金基體表面,保障動力裝備的熱端部件可靠運行的功能隔熱涂層,具有耐高溫、低熱導(dǎo)率和耐腐蝕等優(yōu)點[1]。以航空發(fā)動機為例,推重比 10 級的航空發(fā)動機渦輪前端的溫度已經(jīng)超過 1 800 K,而渦輪葉片的鎳基高溫合金只能承受 1 373 K 的高溫。為了保障發(fā)動機能夠長期可靠的工作,過去通過在渦輪葉片內(nèi)部開設(shè)導(dǎo)氣通道的方法來降低葉片的基體溫度[2-3]。但是隨著航空發(fā)動機朝著高推重比方向發(fā)展,渦輪前進氣口的溫度不斷增加,即使采用先進的冷卻技術(shù)也無法解決鎳基高溫合金熔點遠低于環(huán)境溫度的問題[4]。為了降低葉片基體溫度,延長發(fā)動機的使用壽命,美國國家航空航天局于 20 世紀 50 年代提出了熱障涂層的概念。
-
傳統(tǒng)的熱障涂層體系如圖1 所示,其結(jié)構(gòu)主要包括 4 個部分:直接與高溫環(huán)境接觸的頂部涂層 (TC)、因氧化反應(yīng)生成的 TGO 層、金屬粘結(jié)層(BC) 和高溫合金基體。目前,應(yīng)用最成熟的 TC 材料是 YSZ,粘結(jié)層采用 MCrAlY 合金。在 1 200℃以上的高溫或超高溫環(huán)境,這類涂層在服役過程中長期受到熱循環(huán)作用,會導(dǎo)致涂層分層和剝落,降低涂層的使用壽命。因此,充分了解熱障涂層的失效機制,對延長 TBCs 壽命的研究至關(guān)重要。選擇低熱導(dǎo)率、良好高溫相穩(wěn)定和斷裂韌性的新型材料,可以顯著提高 TBCs 的隔熱性能和使用壽命。先進的 TBCs 結(jié)構(gòu)設(shè)計,可以有效緩解各層之間的熱膨脹系數(shù)差、減小涂層內(nèi)部應(yīng)力、增加涂層在熱循環(huán)下的使用壽命。本文主要綜述了熱障涂層幾種典型的失效機制、近年來新型頂部涂層材料和先進涂層結(jié)構(gòu)設(shè)計的研究進展。對熱障涂層超高溫環(huán)境應(yīng)用進行了展望。
-
圖1 TBCs 的多層功能示意圖[5]
-
Fig.1 Multilayer Functional Schematic of TBCs[5]
-
1 影響熱障涂層失效的原因
-
熱障涂層常用于極端工況下,涂層的熱物理性能和力學(xué)性能在高溫或超高溫環(huán)境中會顯著下降。此外,動力裝置在實際工作過程中會攝入各種環(huán)境污染物,這些污染物隨著溫度的升高而熔融沉淀在熱障涂層表面,從而造成侵蝕。殘余應(yīng)力、高溫?zé)Y(jié)、CMAS 腐蝕、氧化層(TGO)生長是造成熱障涂層剝落與開裂失效的重要因素[6],如圖2 所示。本章總結(jié)了殘余應(yīng)力、高溫?zé)Y(jié)、CMAS 腐蝕、氧化層(TGO)生長這四種影響熱障涂層壽命的主要因素。對涂層的層間界面失效、TGO 形成和生長、涂層氧化、裂紋萌生和擴展等失效機制進行了分析。
-
圖2 熱障涂層的主要失效模式及其影響因素[6]
-
Fig.2 Main failure modes and influencing factors of thermal barrier coatings[6]
-
1.1 殘余應(yīng)力
-
殘余應(yīng)力為多種原因引起的未能釋放的應(yīng)力的統(tǒng)稱,是導(dǎo)致涂層失效的主要因素。殘余應(yīng)力主要包括淬火應(yīng)力、熱失配應(yīng)力和相變應(yīng)力,其中涂層制備過程中產(chǎn)生的相變應(yīng)力較小,可忽略不計。本節(jié)主要總結(jié)了殘余應(yīng)力的產(chǎn)生原因、計算方法以及對涂層開裂分層失效的作用過程。
-
1.1.1 淬火應(yīng)力
-
熱障涂層的制備過程中,涂層材料被加熱到熔融或半熔融狀態(tài)。在沉積到粘結(jié)層與基體上時,由于基體溫度遠低于涂層材料的制備溫度,涂層材料沉積到基底會快速冷卻,導(dǎo)致熔融物心部和基體的底部體積脹縮不均勻,從而產(chǎn)生淬火應(yīng)力。淬火應(yīng)力的計算公式為[7]:
-
式中,Tm 是熱障涂層材料的熔點;Ts 是基體溫度; Ec 是涂層的彈性模量; ac 是涂層的熱膨脹系數(shù)。由于涂層中存在裂紋和孔隙,實際的淬火應(yīng)力往往會小于計算值。
-
KURODA 等[8]研究了等離子噴涂過程中涂層的材料屬性對殘余應(yīng)力的影響,最早發(fā)現(xiàn)了熔融或半熔融態(tài)的涂層粉末遇到低溫基體會產(chǎn)生淬火應(yīng)力。在涂層沉積過程中,淬火應(yīng)力對整個制備過程的殘余應(yīng)力影響較小;但在整體冷卻階段,對產(chǎn)生的殘余應(yīng)力占比影響較大[9]。PINA 等[10]通過 X 射線衍射(XRD)的方法來測試涂層的淬火應(yīng)力,發(fā)現(xiàn)淬火應(yīng)力的大小只與涂層和基體的溫度差有關(guān),與涂層厚度、基體和粘結(jié)層材料無關(guān)。為了對 TBCs 的淬火應(yīng)力和損傷狀況進行有效預(yù)測和評估,一些學(xué)者采用基于圖像處理的有限元方法[11-12]。但是,該方法未分析沉積應(yīng)力的影響[13-14]。此外,對多個微結(jié)構(gòu)圖像進行噪聲清除和網(wǎng)格重建十分繁瑣,使得該方案難以應(yīng)用[15-16]。近年來,針對上述問題,學(xué)者們提出了混合計算的方法,采用光滑粒子流體動力學(xué)(SPH)建立了噴霧模型,替代了先前難以處理的微結(jié)構(gòu)圖像。并且,通過鉆孔試驗證明了該方法能夠更有效預(yù)測涂層的微觀結(jié)構(gòu)缺陷(如孔隙,界面和裂紋)和淬火應(yīng)力[17]。
-
1.1.2 熱失配應(yīng)力
-
除淬火應(yīng)力外,熱失配應(yīng)力對熱障涂層的影響也不容忽視。熱障涂層中頂部涂層材料的熱膨脹系數(shù)最小,其次是粘結(jié)層材料,基體材料的熱膨脹系數(shù)最大。由于熱障涂層各層的熱膨脹系數(shù)存在差異,在熱循環(huán)過程中熱障涂層會產(chǎn)生熱失配應(yīng)力,該應(yīng)力會導(dǎo)致涂層內(nèi)部裂紋擴展,從而造成涂層分層。在涂層的制備過程中,淬火應(yīng)力是在從頂部涂層材料的熔點到沉積溫度(基體頂面溫度)的溫度范圍內(nèi)產(chǎn)生的,而熱失配應(yīng)力是在從沉積溫度到室溫的溫度范圍中產(chǎn)生的。熱失配應(yīng)力的數(shù)學(xué)式為[7]:
-
式中, Δα 是熱障涂層材料和基體材料的熱膨脹系數(shù)差;v 是涂層的泊松比。
-
KARABAS 等[18]研究了由非晶態(tài) La2Zr2O7 (LZA)和晶態(tài) La2Zr2O7(LZC)原料制備的 La2Zr2O7 (LZ)單層熱障涂層和 YSZ / LZ 雙層熱障涂層。三種涂層橫截面的顯微照片如圖3 所示。LZC 的孔隙率高于 LZA,由于較高的孔隙率可以緩解涂層的熱失配應(yīng)力,LZA,LZC 和 YSZ / LZC 雙層 TBC 分別在 67、86 和 400 次熱循環(huán)后發(fā)生剝落,剝落后的涂層樣品如圖4 所示。此外,YSZ / LZC 雙層 TBC 的耐燒結(jié)性較高,且陶瓷層和金屬層之間的熱膨脹系數(shù)差較小,因此 YSZ / LZC 雙層 TBC 的熱循環(huán)壽命高于 LZA,LZC 單層涂層。LIU 等[19]對高溫環(huán)境下 LaZrCeO / YSZ 涂層在熔融 NaCl 中的腐蝕反應(yīng)進行了研究,發(fā)現(xiàn)頂部涂層與粘結(jié)層由于較大的熱膨脹系數(shù)差而產(chǎn)生熱失配應(yīng)力,這是造成涂層損傷的主要原因。考慮熱失配應(yīng)力對裂紋萌生和擴展的影響, RANJBAR-FAR 等[20]和 KRISHNASAMY 等[21]分別建立了堆疊扁平顆粒模型和宏觀-微觀積分模型來研究涂層界面裂紋和裂紋擴展行為。結(jié)果表明,基體的熱失配應(yīng)力是導(dǎo)致冷卻過程中涂層邊緣裂紋萌生和擴展的關(guān)鍵因素。
-
圖3 涂層的橫截面顯微照片[18]
-
Fig.3 Cross-sectional photomicrographs of coatings[18]
-
圖4 熱循環(huán)試驗后的 TBCs 樣品照片[18]
-
Fig.4 Photos of TBCs samples after thermal cycling test [18]
-
基于上述研究可知,層間熱膨脹系數(shù)差會導(dǎo)致涂層內(nèi)部產(chǎn)生熱失配應(yīng)力,從而嚴重影響涂層的使用壽命。主要有兩種方法來提高涂層的抗剝落性和抗裂性,一種方法是通過釋放應(yīng)力的方法來緩解涂層內(nèi)部應(yīng)力,例如增大涂層內(nèi)部的孔隙率、用以裂止裂的方法在涂層內(nèi)部制備的垂直裂紋來釋放熱失配應(yīng)力;另一種方法是選取熱膨脹系數(shù)接近基底的新型陶瓷材料,從而緩解涂層與基體的熱膨脹系數(shù)差。這兩個方面在未來還需要更多研究。
-
1.2 燒結(jié)效應(yīng)
-
熱障涂層內(nèi)部往往具有孔隙,在高溫工況下陶瓷頂部涂層不可避免的會產(chǎn)生燒結(jié)現(xiàn)象。隨著燒結(jié)的進行,多孔的頂部涂層會逐漸致密化。一方面會引起涂層的熱膨脹系數(shù)降低,進一步增加熱失配應(yīng)力;另一方面會降低涂層的應(yīng)變?nèi)菹蓿鸾缑鎽?yīng)力的增加。較差的應(yīng)變?nèi)菹迺?dǎo)致燒結(jié)應(yīng)力的產(chǎn)生,從而造成頂部涂層的開裂和剝落。此外,燒結(jié)效應(yīng)會導(dǎo)致涂層彈性模量增加,引起涂層內(nèi)部應(yīng)力增加。
-
LIU 等[22]研究了 La2Ce2O7 / 8YSZ 雙陶瓷層熱障涂層在極端溫度梯度下的抗熱震性和失效機理。結(jié)果表明,高溫?zé)釕?yīng)力對涂層有很大影響,La2Ce2O7 陶瓷層的燒結(jié)會產(chǎn)生很大的燒結(jié)應(yīng)力,這是 La2Ce2O7 / 8YSZ 熱障涂層失效的主要原因,并且溫度越高,La2Ce2O7 層的燒結(jié)過程越快。李太江等[23] 采用等離子噴涂法制備氧化釔穩(wěn)定氧化鋯(YSZ)涂層,并對其進行 1 000、1 100、1 200 和 1 300℃高溫?zé)Y(jié)試驗,研究其高溫?zé)Y(jié)過程中的微觀結(jié)構(gòu)及熱導(dǎo)率演變規(guī)律。結(jié)果如圖5 所示,同一溫度的條件下,孔隙率隨熱接觸時間的增加而減小;同一時間的條件下,孔隙率隨溫度的增加而減小。 LAVASANI等[24]采用大氣等離子噴涂法制備了噴涂參數(shù)不同的 8YSZ 涂層,研究了燒結(jié)對涂層微觀結(jié)構(gòu)、孔隙率和抗熱震性的影響。結(jié)果表明,噴涂參數(shù)會改變涂層的基本特性、孔隙率和裂紋的數(shù)量和大小,并且較大的孔隙率和裂紋百分比、較小的孔隙尺寸和裂紋尺寸會導(dǎo)致更高的燒結(jié)率。在陶瓷基體內(nèi)摻雜金屬氧化物可以有效解決涂層的燒結(jié)問題。例如,采用固相反應(yīng)燒結(jié)法在 YSZ 涂層內(nèi)摻雜質(zhì)量分數(shù)為 7.5%的 TiO2 可以調(diào)整內(nèi)部孔隙結(jié)構(gòu),但存在嚴重的氣孔愈合現(xiàn)象,減小了應(yīng)變?nèi)菹轠25]。而按一定比例摻雜 CeO2和 Sc2O3 在燒結(jié)過程中,涂層內(nèi)部其他位置處的晶界消失之后,孔隙仍然保留并且存在于晶粒內(nèi)部,有效降低了涂層的燒結(jié)致密化程度[26]。
-
圖5 YSZ涂層在不同溫度熱處理不同時間的表觀孔隙率[23]
-
Fig.5 Apparent porosity of YSZ coating at different temperatures and heat treatment times[23]
-
燒結(jié)應(yīng)力是導(dǎo)致熱障涂層失效的驅(qū)動力之一,環(huán)境溫度越高,燒結(jié)過程越快。高溫環(huán)境中,涂層材料的燒結(jié)會導(dǎo)致涂層內(nèi)部的孔隙和裂紋愈合,涂層表層發(fā)生明顯硬化[27]。涂層內(nèi)部的孔隙決定了其應(yīng)變?nèi)菹蓿紫逗土鸭y的愈合將減小涂層的應(yīng)變?nèi)菹蓿瑢?dǎo)致涂層產(chǎn)生較大的燒結(jié)應(yīng)力。為了延長涂層的壽命,一方面可通過在涂層基體中摻雜金屬氧化物來調(diào)整內(nèi)部孔隙結(jié)構(gòu),改善涂層的抗燒結(jié)性;另一方面,可以設(shè)計具有孔隙率梯度的先進涂層來提高涂層的應(yīng)變?nèi)菹蓿缇哂屑{米分區(qū)結(jié)構(gòu)的涂層。
-
1.3 鈣-鎂-鋁-硅酸鹽(CMAS)滲透腐蝕
-
除了應(yīng)力導(dǎo)致的熱障涂層失效,熔融沉淀物腐蝕也是使熱障涂層失效的一個重要原因。在實際工況下,航空發(fā)動機會攝入大量沙塵、火山灰、跑道碎屑以及各種環(huán)境污染物,這些污染物在高溫下附著于發(fā)動機熱端部件(如渦輪葉片、燃燒室壁等) 形成沉積物。沉積物的成分主要為 CaO、MgO、 Al2O3 和 SiO2,簡稱 CMAS[28]。CMAS 對熱障涂層的滲透過程如圖6 所示,其中圖6a 為沒有沉積 CMAS 的熱障涂層;隨著飛機發(fā)動機在高溫環(huán)境中運行,熱障涂層開始發(fā)生變化,CMAS 逐漸沉積在熱障涂層表面上如圖6b 所示;當(dāng)環(huán)境溫度升高到 CMAS 的熔點溫度(高于 1 200℃)時,固體 CMAS 沉積物轉(zhuǎn)變?yōu)橐簯B(tài),從而滲透到頂部涂層的孔隙與裂縫中,如圖6c 所示[29]。在航空發(fā)動機的熱-冷循環(huán)過程中,CMAS 的熔融和固化會導(dǎo)致涂層的應(yīng)變?nèi)菹藿档停瑥亩a(chǎn)生較大的應(yīng)力而導(dǎo)致涂層的開裂與剝落,降低涂層壽命。
-
圖6 CMAS 對熱障涂層的滲透過程[29]
-
Fig.6 Penetration process of CMAS on thermal barrier coatings[29]
-
LI 等[30]采用放電等離子燒結(jié)法(SPS)制備了釔穩(wěn)定氧化鋯涂層,對涂層在 CMAS 攻擊下的演變過程進行了研究。發(fā)現(xiàn) CMAS 腐蝕對應(yīng)力場(如峰值應(yīng)力)具有顯著影響。應(yīng)力峰值隨著保溫時間的增加而增加,最后導(dǎo)致熱障涂層的脆性斷裂。此外,體積應(yīng)變是導(dǎo)致CMAS腐蝕在過程中應(yīng)力增加和集中的主要原因。SHAN 等[31]研究了 YSZ 涂層在 CMAS 滲透腐蝕下的屈曲現(xiàn)象,指出液態(tài)的 CMAS 由于毛細力的作用滲透到頂部涂層,導(dǎo)致頂部涂層體積膨脹。在高溫環(huán)境中,涂層發(fā)生大規(guī)模屈曲變形,使涂層由于較大應(yīng)力剝落。GUO 等[32]對未拋光和拋光狀態(tài)下的塊狀 YSZ、GdPO4 和 LaPO4 涂層試樣進行了研究。與未拋光的樣品相比,拋光樣品上的熔融 CMAS 具有較低的潤濕性和較小的鋪展面積,由此認為降低表面粗糙度有利于提高 TBCs 的 CMAS 耐腐蝕性。KUMAR 等[33]研究了 CMAS 黏度和涂層微觀結(jié)構(gòu)對 CMAS 滲透深度的影響。結(jié)果表明,低黏度的 CMAS 容易滲透 TBCs,并且具有垂直裂紋和水平帶狀孔隙的涂層結(jié)構(gòu)的樣品,與其他樣品相比,滲透深度更低。MORELLI 等[34]研究了四種不同熱噴涂工藝制備出的等離子噴涂涂層在 CMAS 侵蝕下的腐蝕降解過程,測試的 YSZ 涂層樣品包括:標(biāo)準(zhǔn)化學(xué)純度的 YSZ 原料粉末大氣等離子噴涂(APS)涂層;高化學(xué)純度的 YSZ 原料粉末 APS 涂層;致密垂直裂紋結(jié)構(gòu)(DVC)的大氣等離子噴涂涂層;懸浮等離子噴涂(SPS)涂層。結(jié)果表明,當(dāng)比較兩個具有相似微觀結(jié)構(gòu)的傳統(tǒng) APS 涂層樣品時,化學(xué)純度較低的樣品發(fā)生了更嚴重的腐蝕降解;DVC 涂層的主要問題是大量的 CMAS 滲透到裂縫中,在冷卻過程中對涂層造成了冷沖擊。此外,SPS 涂層發(fā)生了最嚴重的腐蝕降解。當(dāng) TC\BC 界面被 CMAS 侵蝕時會出現(xiàn)界面高溫分層現(xiàn)象。目前,通過制備致密覆蓋層或采用原位自生的制備方法,可以抵抗 CMAS 滲透。使用稀土鋯酸鹽材料制備涂層,可在陶瓷層頂部形成致密層,該致密層由結(jié)晶磷灰石結(jié)晶組成[35]。采用原位自生方法制備 LCO(La2Ce2O7)的雙層 TBC,由于 CMAS 和 LCO 在高溫狀態(tài)下發(fā)生反應(yīng),可以形成由鈣長石、尖晶石和 La2Si2O7 組成的致密保護層,能夠有效抑制 CMAS 的滲透[36]。
-
上述研究表明,CMAS 腐蝕會使涂層發(fā)生體積應(yīng)變,從而導(dǎo)致涂層內(nèi)部應(yīng)力集中,這是涂層失效的主要原因。此外,CMAS 侵蝕會導(dǎo)致涂層屈曲變形,從而引起界面應(yīng)力增加,導(dǎo)致涂層剝落。并且涂層的表面粗糙度、環(huán)境中的 CMAS 黏度、涂層原料的化學(xué)純度和熱噴涂工藝會影響熱障涂層的壽命。通過制備致密覆蓋層或采用原位自生的制備方法可以提高涂層的抗侵蝕性,但該方法還須要進一步研究。
-
1.4 TGO 失效
-
1.4.1 TGO 形成與生長
-
TBCs 中的 BC 層通常由 MCrAlY 合金(M 主要有 Fe、Ni、Co 以及 Ni 和 Co 共摻等幾種選擇) 制成。在高溫環(huán)境下,氧氣從 TC 層擴散到 BC 層時會形成 TGO 層,并沿著 TC 和 BC 的界面生長[37]。初始的氧化物可以保護基體不被進一步氧化,但當(dāng) TGO 生長到臨界厚度(通常為 5~10 μm),TGO 中逐漸積累的最大應(yīng)變能會使 TGO 或 TGO 層附近產(chǎn)生裂紋導(dǎo)致 TBCs 失效,因此延緩高溫環(huán)境中 TGO 的生長速率對延長 TBCs 的壽命非常重要。根據(jù)傳統(tǒng)的 Wagner 氧化理論(拋物線定律),TGO 的增長率可以表示為:
-
式中,δ 是 TGO 厚度, k 是速率常數(shù),t 是氧化時間。TGO 厚度的增長率在較短的氧化時間滿足拋物線定律,但是隨著氧化時間的增加,增長率會逐漸偏離拋物線定律。因此,ZHANG 等[38]研究了低壓等離子噴涂 MCrAlY 粘結(jié)涂層的非拋物線等溫氧化動力學(xué),并修正了傳統(tǒng)的拋物線定律,如式(4)。
-
修正后的模型與試驗結(jié)果相一致,如圖7 所示。 TGO 層主要是由 a-Al2O3 和其他混合氧化物所組成,其中氧化初期會形成的 Al2O3層。但隨著環(huán)境溫度升高和涂層氧化時間增加,其他混合氧化物會快速生長,使 TGO 層體積膨脹從而產(chǎn)生較大的應(yīng)力。有學(xué)者提出,由于 Al2O3層具有優(yōu)異的高溫穩(wěn)定性,并且氧和金屬離子的擴散系數(shù)較低,在沉積頂部涂層之前,在低氧分壓下對粘結(jié)涂層進行適當(dāng)?shù)念A(yù)處理是降低 TGO 生長速率和抑制混合氧化物生長的有效方法[39]。根據(jù)上述觀點,MENG 等[40]利用空氣等離子噴涂法和可控氣氛熱處理制備了有 a-Al2O3 的 TGO 的涂層,分析了粘結(jié)涂層界面微觀結(jié)構(gòu)的變化對 TGO 生長的影響。指出非熱處理粘結(jié)涂層的氧化速率常數(shù)為 0.26μm/h1/2,而熱處理粘結(jié)層的氧化速率常量為 0.14μm/h1/2。由于晶界擴散會影響 TGO 的生長,因此可以通過增大晶粒尺寸來降低其生長速率[40-42]。在制備涂層時使用可控氣氛處理,預(yù)先在粘結(jié)層表面制備一層具有大尺寸晶粒的 TGO 層[43]。通過調(diào)節(jié)熱處理過程的氧壓,控制 MCrAlY 粘結(jié)層表面保持氧化膜形態(tài),可以制備平均晶粒尺寸高達 1 μm 的 TGO 層。如圖8 所示,在熱循環(huán)過程中,TGO 層的較大晶粒尺寸顯著抑制了 TGO 的生長率[44]。
-
圖7 改進模型理論值與試驗值的比較[38]
-
Fig.7 Comparison between theoretical and experimental values of the improved model[38]
-
高溫環(huán)境中 TGO 的生長會導(dǎo)致 TGO 層的厚度增加,TGO 層附近會產(chǎn)生較大的應(yīng)力,從而導(dǎo)致涂層產(chǎn)生裂紋和剝落,縮短 TBCs 的使用壽命。為了延長 TBCs 的使用壽命,可以對粘結(jié)層進行特殊的預(yù)處理,預(yù)先制備具有大尺寸晶粒的 TGO 層來減緩 TGO 的生長速率。目前對高溫環(huán)境下 TGO 生長速率模型還須不斷改進,對粘結(jié)層預(yù)處理的方法還缺少深入研究。
-
圖8 熱處理后粘結(jié)層和普通粘結(jié)涂層的增長率比較[40]
-
Fig.8 Comparison between the growth rate of the heattreated bond coat and the as-sprayed bond coat[40]
-
1.4.2 TGO 生長誘發(fā)的應(yīng)力
-
熱氧化物的生長會導(dǎo)致 TGO 層的厚度增加。在高溫環(huán)境中,超過臨界值的 TGO 厚度是衡量導(dǎo)致 TBC 剝落的失效機制之一。除此之外,BC 系統(tǒng)中的 TGO 生長會導(dǎo)致 TGO / BC 或 TC / TGO 界面之間的熱膨脹失配,進而導(dǎo)致熱障涂層的失效。
-
ABDELGAWAD 等[45]建立了一個有限元模型研究 TGO 厚度對 TBCs 損傷的影響,結(jié)果如圖9 所示,TBC 的裂紋長度隨著 TGO 整體厚度的增加而增加。DONG 等[46]通過控制冷噴涂 MCrAlY 粘結(jié)涂層的等溫氧化時間,制備了不同 TGO 的 TBCs,并對具有不同 TGO 厚度的 TBCs 進行了梯度熱循環(huán)試驗。結(jié)果表明,存在臨界 TGO 厚度 6.01 μm,在小于該臨界厚度的范圍內(nèi),熱循環(huán)壽命隨著 TGO 厚度的增加而顯著降低,結(jié)果圖10 所示。WEI 等[47]建立了含有非均勻 TGO 的 TBCs 有限元模型,探討了 TGO 的非均勻特征對局部應(yīng)力狀態(tài)和開裂分層行為的影響。結(jié)果表明,氧化物的不均勻生長會導(dǎo)致 TGO 層局部厚度增加,與均勻的 TGO 相比,8 μm 非均勻 TGO 模型的裂紋驅(qū)動力增加了 30%,并且隨著不均勻度的增加,裂紋長度也會逐漸增加。
-
上述研究表明,TGO 厚度的增加會導(dǎo)致涂層的開裂分層,并且均勻度低的 TGO 層會導(dǎo)致局部氧化層厚度增加,因此減緩 TGO 層厚度的增長速率及通過工藝優(yōu)化來提高 TGO 層的均勻度,是延長 TBCs 使用壽命的關(guān)鍵措施。
-
圖9 不同冷卻時間下 TBC 的裂紋長度[45]
-
Fig.9 Crack length of TBC under different cooling times[45]
-
圖10 具有不同厚度 TGO 的 TBC 在失效后的宏觀形貌[46]
-
Fig.10 Macromorphology of TBC with different thicknesses of TGO after failure[46]
-
2 熱障涂層陶瓷層材料
-
2.1 傳統(tǒng)釔穩(wěn)定氧化鋯(YSZ)
-
氧化鋯通常處于三種不同的狀態(tài),分別為單斜晶、四方晶和立方晶。在加熱過程中,純氧化鋯會在 1 170℃左右發(fā)生從單斜晶相到四方晶相的轉(zhuǎn)變,陶瓷晶體內(nèi)部結(jié)構(gòu)變化會導(dǎo)致陶瓷的體積變化,這種變化會引起陶瓷內(nèi)應(yīng)力的升高,從而生成裂紋。為了防止上述情況的發(fā)生,可以添加具有穩(wěn)定性的氧化物(如 MgO、CaO、Y2O3)。其中 Y2O3 為常用的穩(wěn)定劑,質(zhì)量分數(shù)為 6%~8%的氧化釔穩(wěn)定氧化鋯的柱狀微觀結(jié)構(gòu)提供了優(yōu)異的應(yīng)變?nèi)菹藓蛯ν繉拥母街Γ⑶宜€具有良好的耐 Na2SO4 和 V2O5 的腐蝕性,因此成為目前應(yīng)用廣泛的熱障涂層材料。然而 YSZ 在高溫下也易發(fā)生相變,當(dāng)溫度高于 1 200℃時,非穩(wěn)態(tài)四方相(t')會轉(zhuǎn)變?yōu)樗姆较啵╰) 和立方相(c)的混合物,冷卻過程中四方相又轉(zhuǎn)變?yōu)閱涡毕啵╩),此過程會發(fā)生體積膨脹,產(chǎn)生裂紋,導(dǎo)致熱障涂層系統(tǒng)的失效[48]。除了相變,嚴重的燒結(jié)收縮也對 TBCs 的性能造成不利影響,會使 TBCs 產(chǎn)生較大的應(yīng)力,熱循環(huán)載荷下的壽命降低。
-
由于 YSZ 在高溫下的力學(xué)性能較差,尋找替代 YSZ 的新型 TBC 材料就顯得格外重要。新型 TBC 材料與 YSZ 相比應(yīng)該具有更低的熱導(dǎo)率,更高的熱膨脹系數(shù),以及具有良好的高溫相穩(wěn)定性。針對超高溫和極端工況,稀土摻雜氧化鋯、A2B2O7 型化合物、稀土鉭酸鹽和自愈合材料受到了廣泛關(guān)注。
-
2.2 幾種新型涂層材料
-
2.2.1 多元稀土氧化物穩(wěn)定氧化鋯
-
盡管 YSZ 具有優(yōu)異的物理性能,但在高溫環(huán)境中依然會有不穩(wěn)定性。以 Ta2O5、Yb2O3、Gd2O3和 Sc2O3 等多元稀土氧化物共摻雜的 YSZ 涂層可以提高相穩(wěn)定性,成為 YSZ 材料的替補材料。CHEN 等[49]的研究表明,試驗測得的摻雜 Ta2O5-Y2O3的 ZrO2 (TYSZ)涂層的導(dǎo)熱系數(shù)為 1.8~2.0 W·m−1 ·K−1,比 YSZ 涂層的導(dǎo)熱系數(shù)(2.0~2.3 W·m−1 ·K−1) 低約 20%,試驗結(jié)果如圖11 所示,其原因是 Ta2O5 的摻雜會誘導(dǎo)晶格畸變,晶格畸變的存在增加了聲子散射,從而導(dǎo)致低熱導(dǎo)率。 SONG 等 [50]對 Yb2O3-Gd2O3-Y2O3 共摻雜 ZrO2(YGYZ)涂層在 Na2SO4和V2O5熔鹽環(huán)境的熱腐蝕行為進行了研究,結(jié)果表明 YGYZ 涂層具有很好的耐腐蝕性與相穩(wěn)定性,在腐蝕 20 h 后涂層仍保留較高的四方相,并且降解的涂層比 YSZ 涂層少 40%。LIU 等[51]研究了 8 mol.%Sc2O3,0.6 mol.%Y2O3穩(wěn)定的 ZrO2 (ScYSZ)涂層的相穩(wěn)定性和燒結(jié)行為。在 1 500℃ 下熱處理 10 h 后,ScYSZ 涂層仍為單一的不可轉(zhuǎn)變四方相,但 YSZ 涂層中單斜相的含量達到 49.4 mol.%,ScYSZ 涂層表現(xiàn)出更加優(yōu)異的高溫穩(wěn)定性。溫度從 1 000℃升高到 1 500℃,ScYSZ 涂層比 YSZ 涂層具有更優(yōu)異的抗燒結(jié)性,因此涂層表面更光滑,如圖12 所示,且提高抗燒結(jié)性能降低材料的熱導(dǎo)率,從室溫到 700℃,ScYSZ 涂層的熱導(dǎo)率為 2.22~2.1 W·m−1 ·K−1,YSZ 涂層的熱導(dǎo)率為 1.21~1.04 W·m−1 ·K−1。
-
圖11 TYSZ 和 YSZ 的熱導(dǎo)率與溫度變化曲線[49]
-
Fig.11 Thermal conductivities versus temperature curves of TYSZ and YSZ bulks[49]
-
圖12 試樣在 1 500℃燒結(jié) 10 h 后的 SEM 顯微照片[51]
-
Fig.12 SEM micrographs of the specimen after sintering at 1 500℃ for 10 h[51]
-
近年來學(xué)者們研制了不同的氧化物穩(wěn)定氧化鋯涂層來解決 YSZ 涂層遇到的問題。從抗燒結(jié)性、低熱導(dǎo)率、高溫穩(wěn)定性這三個角度來分析,該涂層材料具有卓越的物理性能,但從氧化物摻雜含量、涂層的制備、氧化物摻雜機理對涂層性能影響的方面來考慮,還需要更加深入的研究。
-
2.2.2 A2B2O7 型化合物
-
在新型 TBC 材料研究中,除了一些對氧化物穩(wěn)定氧化鋯涂層的研究,還探索了一些新的涂層材料。 A2B2O7(A 為稀土元素,B 為四價元素,如 Zr,Ce 等)化合物根據(jù)氧空位的順序分為燒綠石結(jié)構(gòu)(被視為有序缺陷螢石結(jié)構(gòu))和螢石結(jié)構(gòu)[52]。A2B2O7 型氧化物具有高熔點,并且熔點以下無相變,因此具有良好的高溫穩(wěn)定性。A2B2O7 型氧化物具有復(fù)雜的晶體結(jié)構(gòu),晶體內(nèi)部具有高濃度的氧空位和質(zhì)量更大的稀土原子,會降低平均聲子的自由程,從而降低熱導(dǎo)率。目前對 A2B2O7 化合物的研究主要集中在 A2Zr2O7和 A2Ce2O7類型的材料上。BOBZIN 等[53] 分析了La2Zr2O7和YSZ在1 000~1 300℃的高溫環(huán)境下的熱導(dǎo)率,結(jié)果表明,隨著溫度的升高,兩種材料的熱導(dǎo)率均升高,但在某一溫度下 La2Zr2O7 的熱導(dǎo)率(0.87~1.24 W·m−1 ·K−1)顯著低于 YSZ 的熱導(dǎo)率(1.83~1.59 W·m−1 ·K−1)。王衍飛等[54] 研究了 La2Zr2O7 涂層在高溫長時間條件下的物相組成與微觀結(jié)構(gòu),結(jié)果表明,隨著熱處理時間的增加,La2Zr2O7 涂層始終為單一綠燒石結(jié)構(gòu),表明高溫暴露對 La2Zr2O7 的晶體結(jié)構(gòu)影響不大,因此不會導(dǎo)致膨脹失效,具有良好的高溫相穩(wěn)定性。雖然 La2Zr2O7 涂層具有優(yōu)異的高溫性能,但相對較低的熱膨脹系數(shù)以及較差的斷裂韌性,使其無法作為頂部陶瓷層直接制備在粘結(jié)層上[55]。因此,如何通過采用材料摻雜、結(jié)構(gòu)設(shè)計的方法來改善涂層和粘結(jié)層之間膨脹系數(shù)的匹配、提高斷裂韌性、延長涂層的使用壽命還需要進一步研究。
-
除了 A2Zr2O7 化合物,很多學(xué)者發(fā)現(xiàn) A2Ce2O7 化合物也具有的較低的熱導(dǎo)率、較高的熱膨脹系數(shù)以及優(yōu)異的高溫相穩(wěn)定性,由此成為制備熱障涂層的候選材料之一。與 A2Zr2O7 化合物不同,A2Ce2O7 化合物一般以螢石結(jié)構(gòu)為主。俞顯芳等[56]研究了 Dy2Ce2O7 和 Y2Ce2O7陶瓷材料的相組成、微觀組織和熱導(dǎo)率。試驗結(jié)果表明,在 800℃的工作環(huán)境下, Dy2Ce2O7 的熱導(dǎo)率為 1.78 W·m−1 ·K−1,Y2Ce2O7 的熱導(dǎo)率為 1.82 W·m−1 ·K−1,均低于 YSZ 的熱導(dǎo)率(2.15 W·m−1 ·K−1)。XU 等[57]通過固態(tài)反應(yīng)的方法合成了一類高熵螢石型氧化物,并研究了它們的熱膨脹系數(shù)、熱導(dǎo)率、抗燒結(jié)性和相穩(wěn)定性。如表1 所示,室溫下氧化物具有很低的熱導(dǎo)率,遠遠低于 La2Ce2O7 的熱導(dǎo)率和 YSZ 的熱導(dǎo)率,并且這類氧化物同樣具有優(yōu)異的抗燒結(jié)性和高溫相穩(wěn)定性,由于這些優(yōu)異的物理性質(zhì),可以作為熱障涂層材料的候選。盡管 A2Ce2O7 化合物有很多優(yōu)異的性能,但如何制備具有額定化學(xué)計量比的 A2Ce2O7 化合物仍是一大難題。
-
表1 室溫下高熵氧化物的熱導(dǎo)率[57]
-
Table1 Thermal conductivity of high entropy oxides at room temperature [57]
-
2.2.3 稀土鉭酸鹽
-
由于鉭酸鹽具備高熔點、鐵彈增韌等特性,近年來,高熵稀土鉭酸鹽作為熱障涂層候選材料備受關(guān)注[58]。根據(jù)氧化釔和氧化鉭比例的變化,稀土鉭酸鹽主要包括 3 種化學(xué)結(jié)構(gòu):ReTaO4、Re3TaO7 和 ReTa3O9 [59]。CHEN 等[60]研究了 ReTaO4 的熱力學(xué)性能,并探討了其作為高溫環(huán)境下 TBC 的應(yīng)用,研究結(jié)果如圖13 所示,在 900℃的高溫條件下 ReTaO4 的熱導(dǎo)率為 1.40~2.1 W·m−1 ·K−1,遠遠低于 YSZ 的熱導(dǎo)率。 WANG 等 [61] 成功制備了(Y0.2Ce0.2Sm0.2Gd0.2Dy0.2)TaO4,并對其相的結(jié)構(gòu)、鐵彈增韌機理、熱力學(xué)性能進行了研究,結(jié)果表明 ReTaO4 的斷裂韌性(3.05 MPa⋅m 1/2)高于 YSZ 的斷裂韌性(2.5 MPa·m 1/2),ReTaO4 的脆性指數(shù) (1.34 μm−1/2)低于 YSZ(7 μm−1/2),因此 ReTaO4 具有更好的力學(xué)性能,與此同時,與其他高熵陶瓷相比,它的熱導(dǎo)率也較低(1.2~2.6 W·m−1 ·K−1),在 1 200℃的高溫條件下,它的熱膨脹系數(shù)高達 10.03×10−6 / K,但彈性模量低至 66~189 MPa,這導(dǎo)致了材料具有更高的應(yīng)變?nèi)菹蕖U 等[62]通過固相反應(yīng)合成了(AlxGd1-x)3TaO7(x=0,0.01,0.03,0.05) 固溶體陶瓷,研究了它們的熱導(dǎo)率和熱膨脹系數(shù),結(jié)果表明,在 900℃以內(nèi)的環(huán)境中,(AlxGd1-x)3TaO7 的熱導(dǎo)率為 1.37~1.47 W·m−1 ·K−1,低于 YSZ 的熱導(dǎo)率,與此同時,在 100~1 200℃的環(huán)境下,(AlxGd1-x)3TaO7 的熱膨脹系數(shù)為 6×10−6 / K~10× 10−6 / K,與 YSZ 接近。CHEN 等[63]通過固態(tài)反應(yīng)制備了 RETa3O9 塊狀陶瓷,研究了該材料的熱物理性能,結(jié)果表明,RETa3O9 的熱導(dǎo)率低至 1.33~3.37 W·m−1 ·K−1,遠低于 YSZ 和 La2Zr2O7;熱膨脹系數(shù)范圍為 4.0×10−6~10.2×10−6 / K,接近 La2Zr2O7和 YSZ。
-
圖13 RETaO4(RE=Nd,Sm,Eu,Gd,Dy, Ho,Y,Er)的熱導(dǎo)率[60]
-
Fig.13 Thermal conductivity of RETaO4 (RE=Nd, Sm, Eu, Gd, Dy, Ho, Y, Er) [60]
-
三種化學(xué)結(jié)構(gòu)的稀土鉭酸鹽(ReTaO4、Re3TaO7 和 ReTa3O9)都具有很好的熱物理性質(zhì)和熱力學(xué)性能,可以作為熱障涂層材料的候選。但是,由于高熵稀土鉭酸鹽的研究正在起步,各項綜合性能有待提高,所以高熵稀土鉭酸鹽成為更好的 TBC 材料還缺少更多的理論和試驗來論證。
-
2.2.4 自愈合材料
-
熱障涂層一般應(yīng)用于惡劣的工況下,所以可靠性和耐久性往往是涂層材料選擇的重要考慮因素。熱障涂層在工作條件下的壽命與裂紋的產(chǎn)生和擴展密切相關(guān),有效抑制裂紋的產(chǎn)生和擴展是熱障涂層提高壽命的關(guān)鍵。自愈合熱障涂層通常具有抑制裂紋擴展的功能,因此自愈合材料成為 TBC 材料的候選。自愈合材料(又稱自修復(fù)材料)是一類從結(jié)構(gòu)上具有自修復(fù)能力的智能材料。具有這種能力的材料在受到長期的熱載荷和機械載荷或其他外部載荷時,能夠自行修復(fù)內(nèi)部損傷。然而,這些材料實際上不能實現(xiàn)完全自愈合,所以,凡是能夠一定程度實現(xiàn)自愈合的材料稱為自愈合材料[64]。SONAYA 等[65]通過低壓等離子噴涂法制備了頂部為 YSZ、中間引入 MoSi2、底部為 NiCrAlY 合金的涂層,結(jié)果表明,MoSi2氧化產(chǎn)生的 SiO2 可以密封裂縫和孔隙,防止了粘結(jié)涂層的氧化,從而改善涂層的熱循環(huán)性能,將熱循環(huán)壽命提高為傳統(tǒng) YSZ 涂層的 3 倍,與此同時,通過引入中間層來消除頂部涂層和粘結(jié)涂層之間的熱膨脹和收縮差異的梯度來改善熱循環(huán)性能。HUANG 等[66]通過火花等離子燒結(jié)制備了具有增韌和裂紋愈合性能的 NiAl 顆粒改性 Al2O3復(fù)合材料,研究了不同顆粒尺寸和含量的 NiAl 的增韌效應(yīng),結(jié)果表明,與純 Al2O3 相比,加入質(zhì)量分數(shù)為 15 wt.%的 1 μm NiAl 顆粒后,涂層的斷裂韌性提高了 80%,且裂紋自愈合過程后,復(fù)合材料的斷裂韌性進一步提高 40%。
-
盡管自愈合材料可以抑制涂層裂紋的產(chǎn)生與擴展,但自愈合材料的制備過程比較復(fù)雜,對制備環(huán)境依賴極強。此外,自愈合材料在高溫環(huán)境中生成的氧化物可能和涂層材料的熱膨脹系數(shù)較大,可能導(dǎo)致涂層產(chǎn)生較大的應(yīng)力而剝落。自愈合材料在熱障涂層方面的應(yīng)用還較少,并且此類涂層的制備方法還需要進一步探究。
-
3 長壽命熱障涂層的結(jié)構(gòu)設(shè)計
-
新型頂部材料的熱力學(xué)能更優(yōu)異,抗腐蝕性更好,可以有效延長 TBC 的使用壽命。此外,從結(jié)構(gòu)設(shè)計的角度考慮,單層涂層具有較低的制備成本和較小的層間熱膨脹系數(shù)差,但單層涂層在極端高溫下容易相變和燒結(jié)。因此,在極端高溫環(huán)境中,TBC 結(jié)構(gòu)優(yōu)化對降低內(nèi)部熱應(yīng)力、提高涂層可靠性和延長壽命起著至關(guān)重要的作用。
-
3.1 層狀結(jié)構(gòu)
-
層狀結(jié)構(gòu)的熱障涂層主要有兩種結(jié)構(gòu),單層熱障涂層和雙層熱障涂層。層狀結(jié)構(gòu)的涂層一般由等離子噴涂法來制備,制備原理如圖14 所示。在噴涂過程中,位于等離子射流內(nèi)部的涂層材料被加熱到熔融或半熔融狀態(tài),并高速噴向工件表面。由于液滴與工件表面之間具有較大溫差,使得液滴迅速凝固,最終形成層狀結(jié)構(gòu)。傳統(tǒng)的單層熱障涂層具有制備方法簡單,制備成本較低的優(yōu)點,因此被廣泛使用。新型涂層材料可以解決單層 YSZ 涂層在超高溫環(huán)境中發(fā)生相變和燒結(jié)的問題,但新型材料的熱膨脹系數(shù)與粘結(jié)層材料往往具有較大差異,容易導(dǎo)致熱障涂層層間產(chǎn)生較大的熱失配應(yīng)力。因此,單層的新型材料涂層效果遠不及 YSZ 涂層[67-68]。為了克服上述缺點,學(xué)者們綜合結(jié)構(gòu)和材料兩方面因素,開發(fā)了雙層熱障涂層結(jié)構(gòu)。
-
圖14 等離子噴涂示意圖[67]
-
Fig.14 Schematic diagram of plasma spraying [67]
-
雙層熱障涂層結(jié)構(gòu)由新的頂層材料、YSZ 涂層和粘結(jié)層組成。新的頂層材料直接暴露在工作條件中,往往具有高溫穩(wěn)定性,YSZ 涂層用來降低頂部涂層材料和粘結(jié)層材料的熱膨脹系數(shù)差,減小內(nèi)部熱應(yīng)力。WANG 等[69]通過等離子噴涂在鎳基高溫合金基底上以 NiCrAlY 為粘結(jié)層,制備了單層 YSZ 涂層(常規(guī)和納米結(jié)構(gòu))和雙層 La2Zr2O7 / 8YSZ 熱障涂層,并且研究了三種涂層在高溫下的熱沖擊行為。結(jié)果表明,La2Zr2O7 / 8YSZ 涂層在 1 000、 1 200℃的高溫環(huán)境下與納米結(jié)構(gòu)和傳統(tǒng)結(jié)構(gòu)的 YSZ 涂層相比具有更好的抗熱震能力和更長的熱循環(huán)壽命。WEI 等[70]設(shè)計了三組具有不同彈性模量組合的 La2Zr2O7/ YSZ 雙層熱障涂層,進行了梯度熱循環(huán)試驗。結(jié)果表明,三組不同彈性模量組合的 La2Zr2O7/ YSZ 雙層熱障涂層均具有較長的熱循環(huán)壽命,其中兩組低彈性模量的 La2Zr2O7/ YSZ 雙層涂層的熱循環(huán)壽命比純 YSZ 涂層高 50%。CHEN 等[71] 采用等離子噴涂法制備了基于Mg2SiO4 / 8YSZ雙層熱障涂層,并且在高溫環(huán)境下進行了熱循環(huán)試驗。結(jié)果表明,與單層 Mg2SiO4 涂層相比,Mg2SiO4 / 8YSZ 雙層熱障涂層具有更長的熱循環(huán)壽命。雙層熱障涂層結(jié)構(gòu)可以滿足熱障涂層的隔熱和壽命要求,也可以減小高溫工作環(huán)境下單層熱障涂層內(nèi)部的熱應(yīng)力。但是,熱障涂層只有在固定的厚度范圍才可以具有優(yōu)異的性能,而不是涂層越厚越好,因此在制備雙層熱障涂層時要考慮厚度比例對性能的影響。此外,雙層熱障涂層較單層熱障涂層增加了一個層間界面,如果該界面粗造度較低,那么涂層的粘合度下降易導(dǎo)致剝落;如果界面粗造度較高,那么涂層會產(chǎn)生較大的應(yīng)力而產(chǎn)生裂紋,所以雙層涂層的制備要充分考慮層間界面的設(shè)計。
-
3.2 柱狀結(jié)構(gòu)
-
柱狀結(jié)構(gòu)的熱障涂層一般由電子束物理氣相沉積法 EB-PVD 和等離子物理氣相沉積法 PS-PVD 制備。EB-PVD 的設(shè)備組成如圖15 所示,其工作原理是利用電子束的能量加熱并汽化蒸發(fā)涂層材料,在真空的低氣壓環(huán)境中,蒸發(fā)的涂層材料在熔池上方汽化形成云狀物,氣相原子通常是以直線從熔池表面運動到工件表面并沉積在工件表面形成涂層。袁柯等[72]通過 EB-PVD 技術(shù)在 DZ406 合金和 DZ125 合金表面制備了 1.0Gd2O3-2.0Yb2O3 稀土摻雜改性 YSZ 陶瓷層(GYb-YSZ),由圖16a 和 16c 所示,該涂層均呈典型的柱狀晶結(jié)構(gòu),圖16b 和 16d 可以發(fā)現(xiàn)陶瓷層和粘結(jié)層結(jié)合良好,研究了該涂層在 1 250℃下的高溫燃氣熱沖擊性能。結(jié)果表明, DZ406 / GYb-YSZ 熱障涂層的熱沖擊壽命為 10 000 次,DZ125 / GYb-YSZ 熱障涂層的熱沖擊壽命為 7 800 次。SHEN 等[73]通過 EB-PVD 技術(shù)制備了一系列稀土氧化物穩(wěn)定 La2Zr2O7涂層,研究結(jié)果表明,所獲得的涂層具有相對較高的熱循環(huán)壽命 (395 次循環(huán))和熱沖擊壽命(2 201 次循環(huán)),并且涂層具有極低的熱導(dǎo)率和氧化物生長速率。
-
圖15 EB-PVD 設(shè)備示意圖[74]
-
Fig.15 Schematic diagram of EB-PVD equipment[74]
-
圖16 熱障涂層試樣的截面微觀形貌[72]
-
Fig.16 Cross section micromorphology of thermal barrier coating specimen[72]
-
PS-PVD 的設(shè)備組成如圖17 所示,由真空泵、噴槍、除塵系統(tǒng)、冷卻系統(tǒng)、電力系統(tǒng)和中控系統(tǒng)構(gòu)成。與 EB-PVD 技術(shù)相比,PS-PVD 技術(shù)可實現(xiàn)大面積、均勻化物理氣相沉積,并且可以實現(xiàn)多相復(fù)合涂層的沉積。付朗等[75]以納米團聚的 8YSZ、Gd2Zr2O7(GZO)及(Gd0.9Yb0.1)2Zr2O7(GYbZ)粉末為原料,采用 PS-PVD 工藝制備出柱狀結(jié)構(gòu)完整、力學(xué)性能優(yōu)異的鋯酸釓熱障涂層。結(jié)果表明,只噴涂 GZO 的涂層出現(xiàn)了剝落,噴涂 GZO 和 8YSZ 的涂層未剝落但內(nèi)部存在大量微裂紋,而 Yb 摻雜的 GZO 涂層((Gd0.9Yb0.1)2Zr2O7,GYbZ)內(nèi)無裂紋存在,并且和 GZO 涂層相比,GYbZ 涂層具有更高的硬度(5.4 GPa)、彈性模量(111.6 GPa)和結(jié)合強度(41.3 MPa)。REZANKA 等[76]使用 PS-PVD 制備出了具有柱狀結(jié)構(gòu)的 YSZ 熱障涂層,結(jié)果表明, PS-PVD 技術(shù)制備的柱狀熱障涂層比APS制備的層狀熱障涂層具有更好的的抗 CMAS 腐蝕能力。
-
圖17 PS-PVD 設(shè)備示意圖
-
Fig.17 Schematic diagram of PS-PVD equipment
-
上述兩種方法制備的柱狀結(jié)構(gòu)熱障涂層的優(yōu)勢在于,從結(jié)構(gòu)設(shè)計方面有效提高了涂層的熱力學(xué)性能,增加了熱障涂層的使用壽命。但由于柱狀結(jié)構(gòu)間存在很多間隙,會使得涂層的熱導(dǎo)率普遍較高。因此,如何縮小柱間間隙、降低涂層熱導(dǎo)率是設(shè)計柱狀結(jié)構(gòu)時需要考慮的問題。此外,柱間間隙較大容易導(dǎo)致 CMAS 侵蝕涂層,該結(jié)構(gòu)的耐腐蝕性也會降低。因此如何提高該結(jié)構(gòu)的硬度和抗顆粒侵蝕性是未來發(fā)展的關(guān)鍵。
-
3.3 新型結(jié)構(gòu)設(shè)計
-
3.3.1 納米結(jié)構(gòu)
-
納米結(jié)構(gòu)涂層一般由懸浮液和固體粉末等離子共噴涂技術(shù)制備,該方法的設(shè)備組成和噴涂過程如圖18 所示。ZHANG 等[77]通過懸浮液和固體粉末等離子共噴涂技術(shù)將具有大長徑比的均勻納米顆粒堆引入到傳統(tǒng)的層狀涂層中,制備了具有納米結(jié)構(gòu)的 YSZ 涂層,并且發(fā)現(xiàn)復(fù)合納米結(jié)構(gòu)涂層的熱導(dǎo)率比傳統(tǒng)等離子噴涂法制備的層狀涂層低 1 / 5。JOSHI 等[78]通過懸浮液和固體粉末等離子共噴涂技術(shù)制備了 YSZ 納米結(jié)構(gòu)涂層,并與傳統(tǒng)的大氣等離子噴涂法和液相等離子噴涂法制備的涂層進行對比,結(jié)果表明,納米結(jié)構(gòu)涂層在熱導(dǎo)率、熱循環(huán)耐久性和熱腐蝕性方面優(yōu)于傳統(tǒng)方法制備的涂層。
-
圖18 懸浮液和固體粉末等離子共噴涂示意圖[79]
-
Fig.18 Schematic diagram of plasma co spraying of suspension and solid powder [79]
-
盡管納米結(jié)構(gòu)涂層有優(yōu)異的熱力學(xué)性能,可以應(yīng)用于各種惡劣的工況。但是,學(xué)者們在懸浮液和固體粉末等離子共噴涂技術(shù)方面的研究還不夠豐富,并且納米結(jié)構(gòu)的涂層在實際應(yīng)用中出現(xiàn)的問題還沒有相關(guān)報道,所以這些原因制約了納米結(jié)構(gòu)涂層的發(fā)展。
-
3.3.2 功能梯度涂層結(jié)構(gòu)
-
與傳統(tǒng)層狀結(jié)構(gòu)涂層和柱狀結(jié)構(gòu)涂層相比,功能梯度涂層的特征是涂層材料的成分或材料的微觀結(jié)構(gòu)(晶粒尺寸、密度、孔隙率等)至少沿一個方向逐漸發(fā)生變化,從而導(dǎo)致該涂層物理性質(zhì)發(fā)生轉(zhuǎn)變[80]。功能梯度涂層可分為連續(xù)和不連續(xù)兩種,如圖19 所示,左圖為連續(xù)功能梯度涂層,右圖為不連續(xù)功能梯度涂層。連續(xù)功能梯度涂層一般沒有明顯的界面分層,如圖20a~20c 所示,可分為尺寸/ 結(jié)構(gòu)梯度涂層、取向梯度涂層和體積分數(shù)連續(xù)變化梯度涂層;不連續(xù)功能梯度涂層一般有明顯的界面分層,如圖20d~20f 所示,可分為成分梯度涂層、晶粒排列梯度涂層和體積分數(shù)不連續(xù)變化梯度涂層。 FAN 等[81]通過改變噴涂參數(shù)制備了一種新型的 Sc2O3-Y2O3共穩(wěn)定 ZrO2功能梯度結(jié)構(gòu)涂層,該梯度涂層根據(jù)納米顆粒含量的不同分為三層。結(jié)果表明,該梯度涂層平均隔熱溫度為 132.6℃熱循環(huán)壽命達到 641 次,這兩個指標(biāo)較傳統(tǒng)納米涂層分別高約10 %和 70.5%。SOLTANI 等[82]通過等離子噴涂法制備了三種熱障涂層,分別為 NiCrAlY / YSZ 雙層結(jié)構(gòu)涂層、NiCrAlY / YSZ / 莫來石三層結(jié)構(gòu)涂層和 NiCrAlY / YSZ / 莫來石梯度結(jié)構(gòu)涂層,然后在 1 050℃下,在 45 wt.%Na2SO4 和 55wt.%V2O5 熔鹽中對上述三種熱障涂層進行了熱腐蝕研究,結(jié)果發(fā)現(xiàn),NiCrAlY / YSZ / 莫來石的抗熱腐蝕性能優(yōu)于常規(guī)層狀 YSZ 試樣,并且梯度熱障涂層上致密莫來石層的存在減少了熔鹽滲透到這些涂層中,并增加了涂層的抗熱腐蝕性。
-
圖19 功能梯度涂層的分類[80]
-
Fig.19 Classification of functional gradient coatings[80]
-
圖20 功能梯度涂層的種類[80]
-
Fig.20 Types of functionally gradient coatings[80]
-
層狀結(jié)構(gòu)陶瓷直接將頂部涂層制備到粘結(jié)層上,由于材料較大的熱膨脹系數(shù)差,在高溫條件下會出現(xiàn)裂紋或陶瓷層的剝落。但是功能梯度涂層的材料成分或微觀結(jié)構(gòu)是沿一個方向逐漸變化,可以有效的控制熱膨脹系數(shù)差,此外與層狀結(jié)構(gòu)厚熱障涂層相比,帶有垂直裂紋的梯度結(jié)構(gòu)涂層具有更好的耐久性,其內(nèi)部裂紋提供了大量的應(yīng)變?nèi)菹蓿尫帕撕駸嵴贤繉觾?nèi)部積累的熱膨脹應(yīng)力。盡管功能梯度涂層有很多優(yōu)點,但是在涂層的制備工藝和技術(shù)方面還存在很多問題。如何將不同材料應(yīng)用于功能梯度熱障涂層制備,怎樣實現(xiàn)涂層材料成分和微觀結(jié)構(gòu)呈現(xiàn)線性變化是目前學(xué)者應(yīng)該聚焦的問題。
-
4 結(jié)論與展望
-
TBCs 能夠在先進航空發(fā)動機、燃汽輪機和其他動力裝置的高溫段部件中提供必要的熱保護,是降低基體溫度的關(guān)鍵技術(shù)之一。目前,TBCs 在高溫環(huán)境下長時間服役的失效機制已較為明晰,主要分為殘余應(yīng)力失效、高溫?zé)Y(jié)、CMAS 腐蝕、TGO 生長導(dǎo)致失效這四個部分。針對此,以高隔熱、長壽命為目標(biāo),從頂部涂層材料選擇和先進結(jié)構(gòu)設(shè)計的角度,總結(jié)了近年來 TBCs 的研究進展:
-
(1)殘余應(yīng)力、高溫?zé)Y(jié)、CMAS 腐蝕、TGO 生長是造成 TBCs 失效的主要原因。為了減小殘余應(yīng)力,一方面須要逐步完善不同制備工藝、不同材料 TBCs 的失效預(yù)測模型,提高預(yù)測模型結(jié)果的可靠性和準(zhǔn)確性;另一方面,可以增大涂層應(yīng)變?nèi)菹迊磲尫艢堄鄳?yīng)力,從而緩解涂層應(yīng)力集中現(xiàn)象,例如增加涂層內(nèi)部孔隙率、在涂層內(nèi)部預(yù)制裂紋。針對高溫?zé)Y(jié)問題,如何通過在基體摻雜金屬氧化物來調(diào)整涂層內(nèi)部孔隙結(jié)構(gòu)的方法還有待進一步研究。為了延緩 CMAS 侵蝕,可以考慮熱-力-化學(xué)耦合效應(yīng),采用原位自生的方法制備致密層,但這一方面的研究偏少。此外,在粘結(jié)層表面預(yù)先制備一層具有大尺寸晶粒的 TGO 層,能夠通過增大晶粒尺寸減緩晶界擴散,限制 TGO 的生長。
-
(2)氧化鋯基陶瓷韌性高,熱導(dǎo)率低,且與基體熱匹配較好,因此被廣泛使用。關(guān)于多元稀土元素摻雜氧化鋯材料的研究,大多數(shù)集中在摻雜后如何提高涂層的熱力學(xué)性能和隔熱性能,而關(guān)于稀土元素的摻雜含量和摻雜方式對材料性能的影響以及相關(guān)機理研究較少。目前常用的新型 TBC 材料有 A2B2O7 型氧化物、稀土鉭酸鹽、自愈合材料等,這些材料都具有低熱導(dǎo)率、高溫穩(wěn)定性、優(yōu)異的抗燒結(jié)性和耐腐蝕性,能夠滿足 TBC 材料的需求。
-
(3)為進一步提高 TBCs 的高溫穩(wěn)定性并延長其壽命,先進的結(jié)構(gòu)設(shè)計也至關(guān)重要。針對傳統(tǒng)單層涂層結(jié)構(gòu)由于熱失配應(yīng)力剝落的問題,提出了雙層結(jié)構(gòu)、柱狀結(jié)構(gòu)、納米結(jié)構(gòu)和功能梯度結(jié)構(gòu)這四種先進結(jié)構(gòu)設(shè)計,詳細的介紹了 APS、EB-PVD、 PS-PVD 等涂層制備方法。
-
基于以上總結(jié),為進一步提高 TBCs 的隔熱性能、延長 TBCs 的使用壽命,針對現(xiàn)有涂層材料和結(jié)構(gòu)的研究做出如下展望:
-
(1)通過傳統(tǒng)的制備工藝(APS、EB-PVD 等) 沉積新材料,易導(dǎo)致涂層成分偏析和內(nèi)部相結(jié)構(gòu)差異較大等問題,目前涉及新型陶瓷材料可沉積特性的研究報道較少,因此 TBC 材料的可沉積性是未來重點關(guān)注的方向。
-
(2)在實際生產(chǎn)中,先進結(jié)構(gòu)涂層的制備難度較大、成本較高,因此將計算機數(shù)值模擬技術(shù)與傳統(tǒng)的 TBCs 制備相結(jié)合,能夠直觀反應(yīng)不同結(jié)構(gòu)涂層的可靠性,協(xié)助選擇最合適的制備工藝參數(shù),從而降低研發(fā)成本。
免責(zé)聲明:本網(wǎng)站所轉(zhuǎn)載的文字、圖片與視頻資料版權(quán)歸原創(chuàng)作者所有,如果涉及侵權(quán),請第一時間聯(lián)系本網(wǎng)刪除。
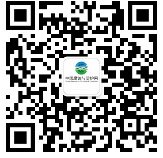
官方微信
《腐蝕與防護網(wǎng)電子期刊》征訂啟事
- 投稿聯(lián)系:編輯部
- 電話:010-62316606
- 郵箱:fsfhzy666@163.com
- 腐蝕與防護網(wǎng)官方QQ群:140808414