濕氣管道是一類將氣井井口直接采出、未經脫水脫烴處理的天然氣輸送到處理站的管道,因其運行費用低、適應性強,常用于山地、海洋等惡劣環境下的天然氣開采和輸送。然而,濕氣管道內苛刻的介質環境導致其面臨嚴重的內腐蝕問題,據報道,某海底濕氣管道的腐蝕速率高達0.73~1.5 mm/a[1, 2]。常規天然氣采輸中的夾帶水、凝析液以及頁巖氣開采中的返排液都是管道中水的重要來源,當伴生的CO2等酸性氣體溶于水,其腐蝕性比同等pH條件下的鹽酸更強。在山地、海底等存在地形起伏的區域,液態水極易在低洼管段聚積[3],形成積液區,導致該管段的腐蝕較其它部分更為嚴重[4, 5]。
積液區管道腐蝕的復雜性表現在氣液兩相流動并不局限于典型的段塞流動,還包括分層波浪流等,積液在氣流擾動下,還可發生液膜向抬升段下游的流動和回流[11],發生局部管段被不同狀態的液膜周期性潤濕的情況。段塞流條件下的腐蝕研究表明,氣液交替流動或潤濕條件會對管壁腐蝕失效起到促進作用[19]。此外,則少有研究提及壁面液膜的動態分布所帶來的影響,且在氣液交替流動條件上缺少一定的量化分析。楊雨[20]在氣液兩相流的CO2腐蝕中涉及到管壁潤濕狀態對CO2腐蝕機制的影響,該研究區分了完全浸泡和間歇浸泡條件下的CO2腐蝕機制。但腐蝕條件的營造手段并不能完全真實地反應管內的真實流動和腐蝕狀況,也尚未說明動態液膜分布是否能夠影響管壁的腐蝕行為及機制。當前,積液區復雜氣液兩相流動狀態下的CO2局部腐蝕機制尚不明確,急切需要針對性研究的開展。
鑒于濕氣管道積液區氣液兩相流動的復雜性,液膜在管壁上分布時間和空間的不確定性,本研究自行設計并搭建了一套可以模擬開展管道積液區CO2局部腐蝕腐蝕測試的試驗裝置。本研究以管道傾斜角、氣體流速、腐蝕時間為主要研究變量,借助絲束電極測試、電化學阻抗譜測試等手段并結合氣液兩相流態觀察、理論分析等,研究了X70管線鋼在模擬積液區氣液流動條件下的CO2局部腐蝕電化學機制及影響因素。
1 實驗方法
實驗介質采用為1% (質量分數) NaCl水溶液,溶液由去離子水 (電阻率為0.78 MΩ·cm) 和分析級NaCl試劑配置而成。實驗前,采用99.99% CO2氣體對溶液除氧 (CO2分壓為0.1 MPa),除氧時間不低于4 h,然后密封待用。除氧后測得溶液pH為3.98。
設計并搭建了一套可模擬開展管道積液區CO2局部腐蝕測試裝置,如圖1所示。該裝置是由蠕動泵、CO2儲存箱、傾斜管路、循環風機、氣體流量計、電加熱臺、絲束電極測試部分等主要部件構成,可以對管內氣體流速、持液率、管路傾斜角度及管內溫度等變量進行控制。
圖1
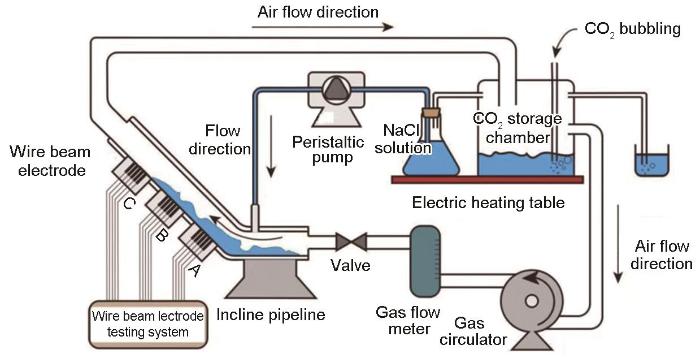
圖1 模擬積液區CO2局部腐蝕試驗裝置示意圖
Fig.1 Schematic diagram of CO2 local corrosion test device in the simulated water accumulation area
該裝置通過綜合調節風機檔位及閥門開度實現對管內氣體流速的控制。通過蠕動泵持續向管路中注入腐蝕溶液,以模擬濕氣管道內液體持續穩定析出過程。參考低持液率輸氣管線內液體體積含量[7],結合測試管段的結構尺寸,通過預實驗摸索確定了實現可控可重現波狀流動的注液量 (氣體流速為2、4和6 m/s時,注液量分別設為0.5、1和2 mL/min)。實驗過程中持續向裝置內通入CO2,以維持系統內部的微正壓,杜絕外界空氣的干擾。
實驗測試部分包含3個測試用絲束電極,分別為絲束電極A、B和C,沿氣液流動方向依次排布 (圖1)。
每個絲束電極由5排×4列的工作電極絲和5排×1列的參比電極絲組成,具體布置見圖2。工作電極絲直徑1 mm,高度30 mm,由X70鋼加工而成,其化學成分為 (質量分數,%):C 0.058、Si 0.425、Mn 1.418、Nb 0.049、Ti 0.009、Mo 0.146、Cr 0.146、Ni 0.038、P 0.011、S 0.002,剩余為Fe。參比電極絲為直徑為1 mm的高純鋅絲99.998%。每根電極絲等間距排列,間距為2 mm。每個絲束電極之間間距為30 mm。
圖2
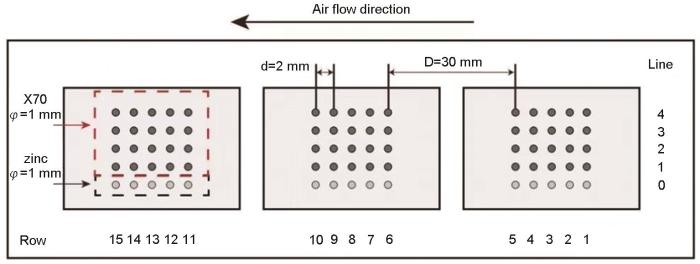
圖2 實驗絲束電極示意圖
Fig.2 Schematic diagram of experimental wire beam electrode
制備絲束電極時,將X70鋼電極絲及純鋅絲的一端與銅導線焊接,相互之間絕緣處理,按圖2所示方式排布好后用環氧樹脂封裝成塊。將絲束電極工作面由200#水磨砂紙逐級打磨至1000#,再用丙酮和蒸餾水清洗,經冷風吹干后放入干燥皿中備用。
實驗所用絲束電極測試裝置為實驗室自行研制的微電極陣列電偶腐蝕測試系統,該系統采用LabVIEW 8.5編寫測控軟件,系統由PXI-2535、PXI-1033、PXI-4022以及PXI-4071等模塊化儀器組成[21]。在測試時,將絲束電極的接線端與該系統連接,系統可依次測量每根電極絲的耦合電流。測試結束后通過Surfer軟件對原始數據進行圖像處理和分析。
電化學阻抗譜 (EIS) 測試采用Autolab系列PGSTAT302N型電化學工作站,測試過程激勵信號幅值為10 mV,測試頻率為10-2~105 Hz。測試結果采用Zview軟件進行擬合。鑒于EIS測試中對電極放置位置有明確的要求,而在本研究中難以實現在對氣液分層波浪流動無干擾的情況下開展原位EIS測試,故采用了與實驗條件相近的靜態溶液條件下的非原位測試。EIS測試中,工作電極絲為工作電極,高純鋅絲為參比電極,鉑片作對電極,鉑片與工作電極平行布置。
采用KUY NICE體視顯微鏡觀察腐蝕后的電極表面形貌。
采用Sony-FDR-AX700 4K高清攝像機拍攝并記錄傾斜管路內不同工況條件下的積液分布和流動狀態。人工計數獲得單位時間內流經不同電極位置處的波浪次數
2 實驗結果
2.1 X70鋼在不同管道傾角下的測試結果
測試獲得氣體流速為2 m/s,不同傾角下的耦合電流結果 (圖3)。由圖可知,在不同傾角下,電極表面耦合電流呈現非均勻分布。傾角為15°時,最大陽極電流為0.896 μA,在第10排;最大陰極電流為-1.43 μA,在第3排。傾角為30°時,最大陽極電流為2.43 μA,在第10排;最大陰極電流為-4.15 μA,在第6排。傾角為45°時,最大陽極電流為1.95 μA,在第8排;最大陰極電流為-1.29 μA,在第12排。電流的符號與陰陽極反應有關,其中負號表示發生陰極反應,電偶腐蝕過程中受到保護;正號表示陽極反應,即發生腐蝕。綜合可知,在傾角為15°時,陽極反應主要發生在第7~第11排;在傾角30°時,陽極反應主要發生在第8~第10排和第12~第14排;在傾角為45°時,陽極反應主要發生在第6~第9排。
圖3
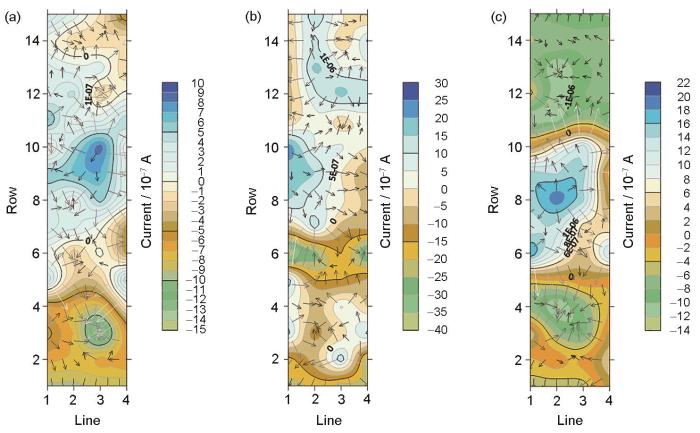
圖3 不同傾角下的耦合電流測試結果
Fig.3 Test results of coupling current at different inclination angles: (a) 15°, (b) 30°, (c) 45°
拍照得到不同傾角下電極表面的液膜分布情況 (圖4)。可知各傾角下管道內的流型都屬于波狀流。當傾角為15°時,電極表面的液膜厚度整體較薄,不同電極表面液膜厚度相差不大。傾角增大到30°時,整體液膜厚度則顯著增厚,不同電極表面液膜厚度差別開始增大。傾角為45°時,電極表面液膜厚度有顯著的差異,表現為上游電極表面液膜厚度較厚,而下游表面液膜厚度較薄。
圖4
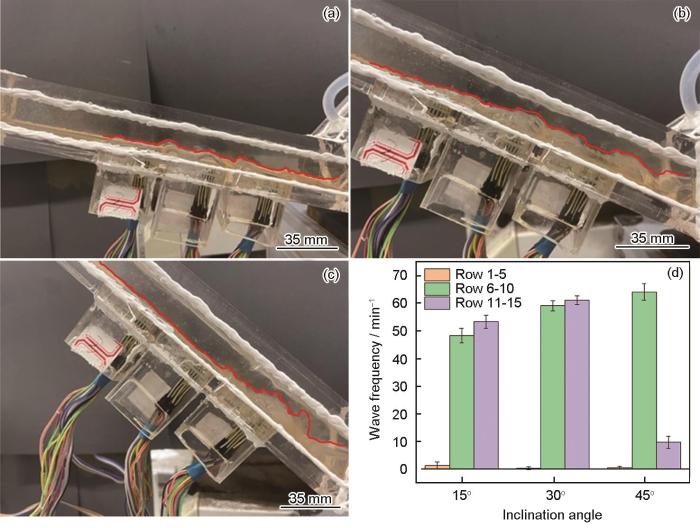
圖4 不同傾角管內積液流動狀態
Fig.4 Flow state of liquid accumulation in tubes with different inclination angles: distribution of water film in the pipe at 15° (a), 30° (b), 45° (c) and frequency of waves flowing through the electrodes at different inclination angles (d)
值得注意的是,液膜并非是靜止的,而是在氣流和重力的共同作用下,交替出現以波浪的形式出現向下游的流動和回流。分別記錄了3個電極表面波浪的流經頻次,如圖4d所示。可知,電極A表面流經的波浪頻次遠小于電極B和C。隨著傾角的增大,電極A表面波浪數量基本無區別,而電極B壁面經歷的波浪數不斷增加。對于電極C,其表面流經的波浪數量隨著傾角的增大則表現為先增多后大幅減少。
2.2 X70鋼在不同氣體流速下的測試結果
測試獲得傾角為30°,氣體流速分別為4和6 m/s時的耦合電流結果 (圖5)。由圖可知,氣體流速4 m/s時,最大陽極電流在第9排,為0.775 μA;最大陰極電流在第10排,為-1.2 μA。氣體流速為6 m/s時,最大陽極電流在第14排,為0.43 μA;最大陰極電流在第6排,為-0.5 μA。隨氣體流速的增大,最大陰、陽極電流都呈減小趨勢。
圖5
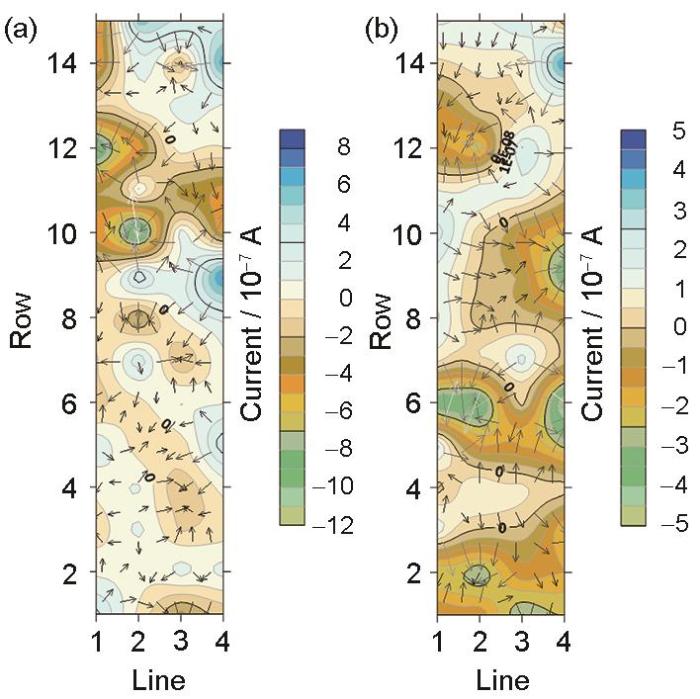
圖5 不同氣體流速下的耦合電流測試結果
Fig.5 Test results of coupling current at different gas flow rates: (a) 4 m/s, (b) 6 m/s
結合流動狀態圖和不同電極處氣液交替頻率分布圖 (圖6) 來看,隨著流速的增大,相同位置不同流速下電極表面的液膜厚度整體呈減薄趨勢,電極表面不同位置處液膜厚度差異逐漸增大。電極A所處的上游位置處液膜厚度整體較大,電極B和C表面液膜厚度較小,有波浪經過時將發生厚度的變大。圖6c所示電極表面波浪的頻次,可知電極A表面頻次較低,電極B和C表面頻次則較高。隨著氣體流速的增大,電極A壁面處的波浪頻次增多,而電極B和C壁面處的波浪頻次則逐漸減小。這是由于氣體對液體有裹挾作用,氣體流速越大,對液體的裹挾作用越大,導致更多的液相被帶到下游,積液區整體積液量減少,因而電極表面整體液膜厚度較小。隨著液體量的減小,氣體裹挾作用下波浪的頻次也相應地降低。
圖6
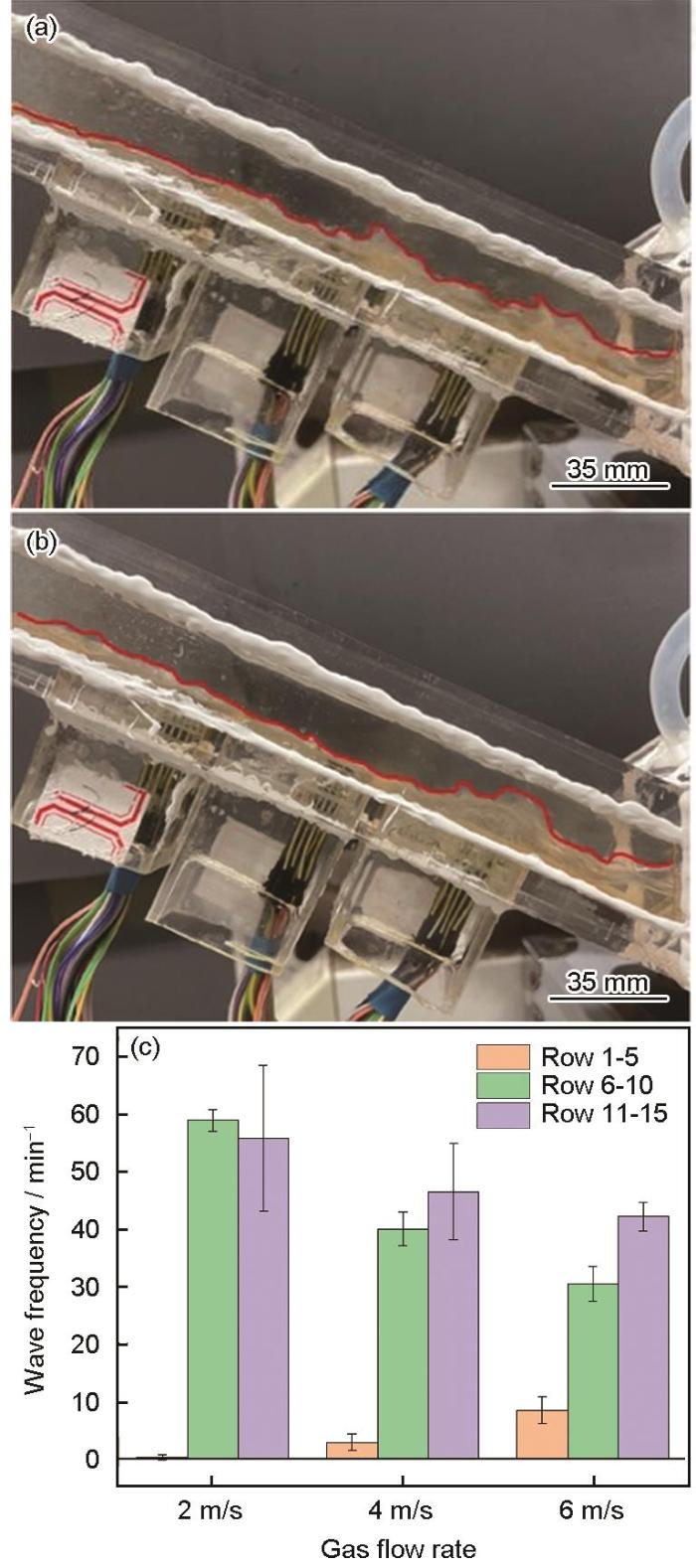
圖6 不同氣體流速管內積液流動狀態
Fig.6 Flow state of liquid accumulation in pipes with different gas velocities: distribution of water film in the pipe at 4 m/s (a), 6 m/s (b) and frequency of waves flowing through the electrodes at different gas velocities (c)
2.3 X70鋼在不同時長下的測試結果
測試獲得氣體流速2 m/s,傾角30°,不同時長下的耦合電流結果 (圖7)。由圖可知,實驗24 h之后,最大陽極電流在第13排,為1.59 μA;最大陰極電流在第11排,為-2.3 μA。168 h之后,最大陽極電流在第13排,為1.504 μA;最大陰極電流在第11排,為-1.96 μA。
圖7
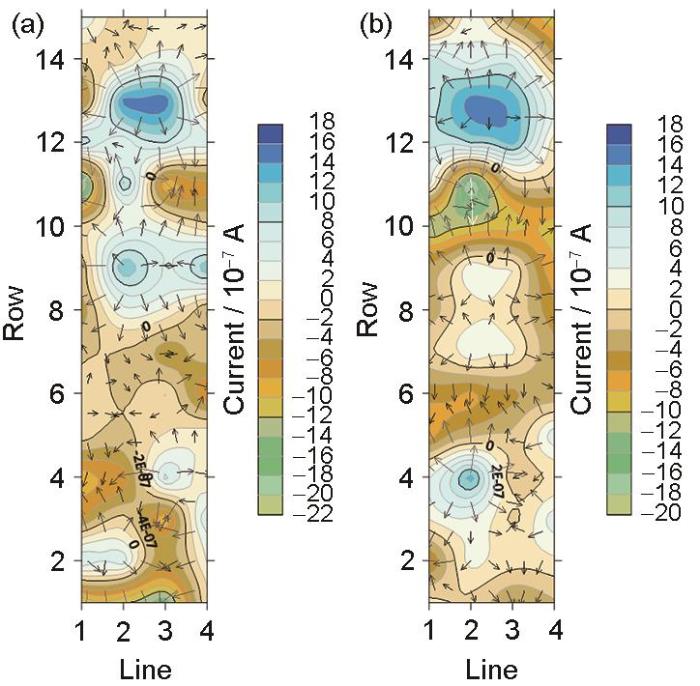
圖7 不同腐蝕時間條件下耦合電流分布結果
Fig.7 Coupling current distribution under different corrosion time: (a) 24 h, (b) 168 h
對比可知,隨著時間的延長,陰極電流微弱減小。與此同時,除12~14排陽極點的位置無顯著變化外,其它位置的陰、陽極極性分布則發生了一定程度地轉變,尤其是第8~第10排由陽極區轉變為陰極區。陽極區隨實驗時間的延長而變得更為集中地分布于局部位置。
統計得到了電極表面的陰陽極面積比 (即陰陽極電極的數量比) 隨時間的變化,得到12、24和168 h后的陰陽極面積比分別為32∶28、32∶28和31∶29。可見,陰極面積整體略大于陽極,且隨著腐蝕時間的延長,陽極面積緩慢增加,陰陽極面積比呈小幅減小的趨勢。
董澤華等[22]依據局部腐蝕指數 (LI)提出了可更好地表征絲束電極表面腐蝕非均勻性程度的局部腐蝕因子 (LF),即:
式中分別為絲束電極表面陽極區和陰極區的任一單電極的耦合電流值,Nc/Na代表絲束電極表面陰極區和陽極區單電極數量之比。根據
圖8
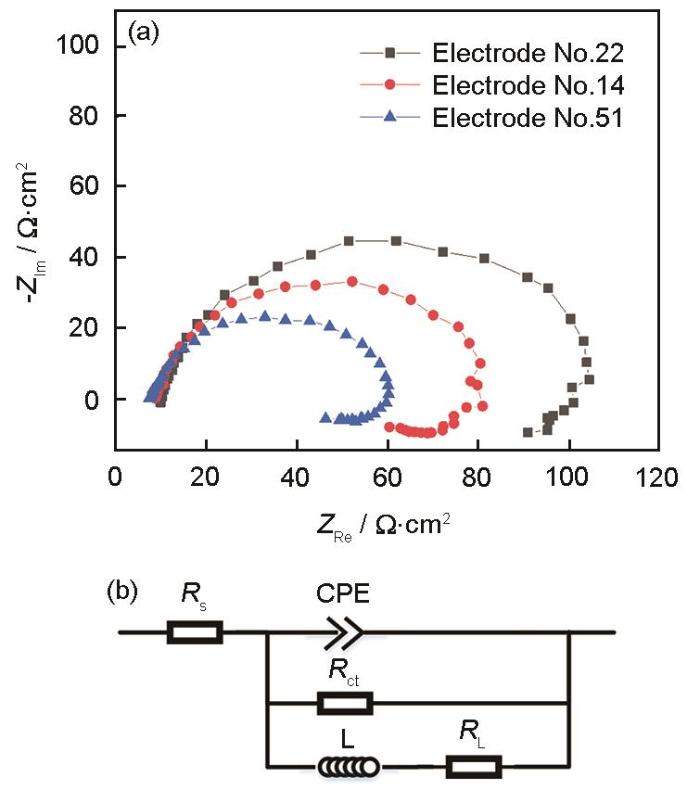
圖8 典型位置處電極絲的EIS及其等效電路圖
Fig.8 EIS of electrode wire at typical location (a) and equivalent circuit diagram (b)
由擬合結果可以看出,不同位置處電極絲的電荷轉移電阻有明顯差異,Rct(22)>Rct(14)>Rct(51)。由于電荷轉移電阻跟腐蝕速率呈反比關系,對應第51根電極腐蝕速率最大,第14根次之,第22根最小。這與絲束電極測得耦合電流結果所反映的規律一致,即i(51)>i(14)>i(22),表明耦合電流測試結果具有代表性。
圖9
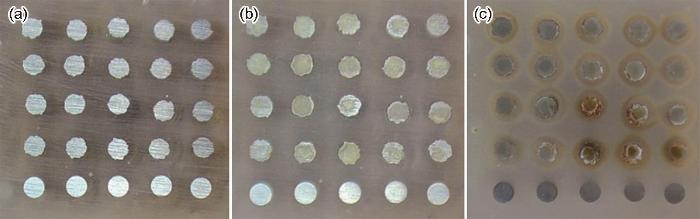
圖9 絲束電極C在不同腐蝕時間后的腐蝕形貌
Fig.9 Corrosion morphology of wire beam electrode C after different corrosion time: (a) fresh surface, (b) 24 h, (c) 168 h
由腐蝕168 h后不同位置處的腐蝕形貌圖 (圖10) 可知,電極B表面不同位置處的腐蝕銹層形態較均勻,而電極A和C的不同位置處銹層形態差異則較明顯。電極A銹層差異較大區域主要分布于左上角,而電極C則主要分布于右下角。電極絲周圍環氧材料的顏色也一定程度地反映出腐蝕的嚴重程度,可知盡管電極B表面的腐蝕產物膜層比較均勻,但同樣發生了較嚴重的腐蝕,膜層的分布可歸因于氣液流動對膜層的沖刷破壞。
圖10
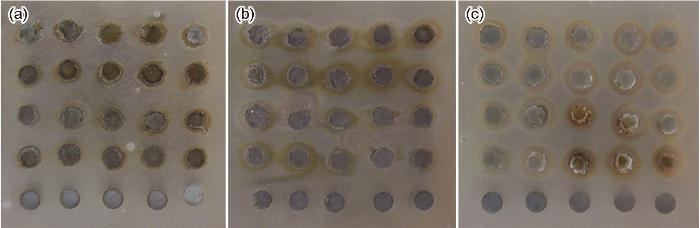
圖10 腐蝕168 h后不同位置處電極絲腐蝕形貌
Fig.10 Corrosion morphology of electrode wires at different positions after 168 h corrosion: (a) electrode A, (b) electrode B, (c) electrode C
3 討論
3.1 腐蝕電化學過程分析
CO2腐蝕體系下,陽極過程主要為Fe的氧化反應:
(2)
該反應又可細分為以下反應步驟[23],包括:
(3)
(4)
(5)
陰極過程跟溶液pH有關。當前100% CO2環境下的pH為3.98,陰極過程主要為H+和碳酸的還原反應[24]為:
(6)
(7)
式中,δ是邊界層厚度,Re是雷諾數,d是水力直徑。Re與流速成正比,因此流速越大,Re越大,δ數值則越小。相應地,傳質也就越快。
CO2腐蝕體系下,腐蝕產物膜的生成是影響腐蝕速率和分布的重要因素。當金屬壁面上Fe2+與
(9)
FeCO3在金屬壁面的沉積成膜可抑制電化學反應物質向金屬壁面的傳質、減少金屬壁面的活性區域,進而降低金屬的腐蝕速率[28]。但FeCO3產物膜對腐蝕速率的有效抑制作用的前提是膜層較為致密,這就要求FeCO3的生成速率足夠快,或者其過飽和度大于2[29]。其中,FeCO3的過飽和度 可表示為:
式中,分別為Fe2+、
為FeCO3的溶解度。盡管此前研究多指出,生成保護性腐蝕產物膜的通常要求溫度大于60 ℃[30],這是本研究條件所不具備的。但薄層液膜下腐蝕產物膜也有希望生成[31],液膜越薄,溶液更新速率越低,產物膜生成速率越大。相反,液膜厚度大,流速快,波浪的頻次高,溶液水化學更新速度快,腐蝕產物膜則越不容易生成。與此同時,在較快的流速沖刷和高頻次的波浪沖擊作用下,腐蝕產物膜在金屬壁面的沉積速率及分布的完整性也將受到影響[32]。
3.2 積液區局部腐蝕的發生與演變行為機制分析
不難理解,腐蝕的不均勻分布與傾斜管道結構影響下的氣液兩相流動狀態有關。模擬析出液體在重力的作用下主要積聚在管道低洼處。當高速氣體流過,氣流與液體之間的剪切作用導致液體被夾帶著向下游流動。根據持液量、管道傾角、氣體流速的不同,液體將以不同的流態向下游流動。本研究的流速條件下,液體主要表現為波浪流流型。液膜在管道壁面上的分布狀態受到流型的影響,表現為液膜厚度從上游到下游主要表現為逐漸降低的趨勢,同時有波浪不斷從上游運動到下游。波浪初始流速高,攜液量大,但在向下游運動過程中不斷減小,甚至有一部分液體在重力作用下發生回流。
鑒于CO2腐蝕速率受陰極過程控制,陰極過程受到液膜厚度、液膜流速的影響,因而液膜厚度越薄、流速越快,腐蝕速率則越快。結合各流動條件下的液膜厚度分布可知,越往下游液膜厚度越薄,但流速也越低,上游厚度較大,而流速也較大。在液膜厚度超過邊界層厚度時,往往流速的影響更為重要,因而上游的腐蝕速率理應更大。當波浪存在時,腐蝕速率還受到波浪的擾動影響。結合不同傾角、不同流速下的測試結果可知,波浪頻次越高,測得耦合電流越大,這反映出了波浪對腐蝕速率的影響占據更主導的作用。因而,不穩定流動下的腐蝕,較于穩定流動,腐蝕問題突出。段塞流等流型下更為嚴重的腐蝕問題也說明了這一點。
波浪的存在不僅影響到腐蝕電化學陰極過程,對腐蝕產物膜的生成也會產生影響[33]。腐蝕產物膜的生成需要適宜的條件,同時需要較長時間的積累,所以往往腐蝕初始腐蝕產物膜的影響比較有限,隨時間的延長才會比較突出。一方面,波浪會導致溶液化學環境的更新,通過不斷注入新鮮低濃度的溶液,降低腐蝕產物膜的飽和度,降低腐蝕產物膜的生成速率和致密程度。另一方面,對于已生成的腐蝕產物膜,波浪的沖擊導致金屬壁面更大的剪切力,破壞腐蝕產物膜的完整性,降低腐蝕產物膜對腐蝕速率的抑制作用。由于不同位置波浪的頻次、波浪的影響程度不同,腐蝕產物膜受到的影響也有不同,因而對不同位置的保護性就有所不同。波浪沖擊和腐蝕產物膜共同作用下,導致不同位置處的腐蝕速率差異顯著增大,并向局部位置集中,如傾角30°、流速2 m/s下的第13排。隨時間的延長,該位置處的耦合陽極電流 (亦為電極表面最大陽極電流) 有所降低,但降幅很小并始終保持較大的電流數值,這與常規體系下均勻腐蝕速率隨時間延長大幅降低的趨勢有顯著區別。對于這種電流數值的降低,陰極區面積減小而陽極區面積增大也會產生一定程度的影響。需要指出,CO2體系下碳鋼的腐蝕形貌常表現為凸臺狀,并不會形成顯著的大陰極小陽極。盡管如此,電極表面局部位置相較于其它區域維持著較高的腐蝕速率,腐蝕非均勻性程度隨著腐蝕時間的延長不斷增大。
由圖10可知,短時間內并不能形成致密并具備良好保護性的產物膜,因而金屬壁面的液膜狀態成為影響腐蝕均勻性的重要因素,這包含液膜厚度分布的均勻性及液膜的運動狀態。液膜厚度的不均勻性可導致腐蝕陰極反應速率及近壁面處液膜pH的差異。局部位置液膜不規律的運動,可加快反應物質的傳質,稀釋現有的飽和溶液,促進相應位置的腐蝕。
4 結論
(1) 對濕天然氣管道,低洼段積液位置處將發生局部腐蝕,表現為局部位置處的腐蝕電位、耦合電流存在顯著差異。在本文研究條件下,氣體流速為2 m/s,管道傾角為30°時,局部腐蝕最為嚴重。
(2) 隨著腐蝕時間的延長,陽極區將向局部位置集中,表現為更嚴重的局部腐蝕現象。
(3) 在管道結構、流動參數等的影響下,積液區局部位置處液膜厚度的不均勻分布、波浪流經的頻次大小、腐蝕產物膜的生成情況等共同影響液膜下的局部腐蝕行為,其中波浪頻次、腐蝕產物膜的影響更為顯著。
免責聲明:本網站所轉載的文字、圖片與視頻資料版權歸原創作者所有,如果涉及侵權,請第一時間聯系本網刪除。
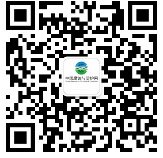
官方微信
《腐蝕與防護網電子期刊》征訂啟事
- 投稿聯系:編輯部
- 電話:010-62316606
- 郵箱:fsfhzy666@163.com
- 腐蝕與防護網官方QQ群:140808414