元素 | C | Mn | Si | S | P | Fe |
---|---|---|---|---|---|---|
質量分數/% | 0.15~0.20 | 0.32~0.65 | ≤0.30 | ≤0.05 | ≤0.042 | 余量 |
傳統的涂料體系中含有一定量的揮發性有機化合物(VOCs),會造成嚴重的環境污染。與傳統涂料相比,水性環氧涂料更加環保,已成為有機涂料的主要研究對象。但是,在固化成膜的過程中,由于水和溶劑的蒸發,會形成細小的孔隙,為腐蝕介質提供通道,加速腐蝕。納米顆粒由于體積小,常被用于解決水性涂料的微孔問題[1]。Fe3O4納米顆粒由于成本低、耐腐蝕、導電性好等優點,在防腐蝕涂料領域得到了廣泛應用。但單一納米Fe3O4容易團聚,體系分散性差。因此,合成分散性良好的Fe3O4納米復合材料成為研究熱點。當金屬基體暴露在水、氧等腐蝕性介質中時,由于聚苯胺(PANI)在酸性溶液中具有可逆的氧化還原活性,可以激發聚苯胺的電化學活性,并在腐蝕反應中進行電荷轉移,促進氧化膜的形成,從而有效提高涂層的耐蝕性[2-4]。氧化石墨烯(GO)由于其片狀結構,與Fe3O4結合時具有較大的表面積和良好的分散性,可有效防止腐蝕介質在涂層中的滲透,發揮良好的屏蔽作用[5-8]。聚苯胺和石墨烯的導電性在一定程度上有利于提高涂層的耐蝕性,但當導電性較高時,電化學腐蝕過程中的電子轉移會加速,從而加速金屬基體的腐蝕[9]。ZHOU等[10]研究了石墨烯/銅復合材料防腐蝕后期情況。結果表明:石墨烯的高導電性使陰極反應從銅表面擴散到石墨烯導電網絡,傳質阻力的降低進一步加速了陰極反應,導致銅的腐蝕更加嚴重。因此,Fe3O4的加入可以有效降低材料的電導率。同時,Fe3O4能減弱聚苯胺由中性向堿性的轉變,增強聚苯胺在溶液中的電化學腐蝕性能[11]。EL-MAHDY等[12]將Fe3O4納米顆粒加入交聯丙烯酰胺-丙烯酸鈉基體中制備復合材料。結果表明,Fe3O4納米顆粒與聚合物在分子水平上發生了相互作用,提高了Fe3O4納米顆粒的分散性和基體的耐蝕性[13]。BAGHERZADEH等[14]通過苯胺原位氧化聚合在Fe3O4納米顆粒表面制得Fe3O4/PANI納米復合材料,填充環氧樹脂后納米復合涂層的耐蝕性明顯增強。以Fe3O4/PANI納米復合材料為基礎,通過添加還原氧化石墨烯(rGO)納米片,將球形核殼結構轉變為三維層狀結構。結果表明,rGO表面的疏水性和大比表面效應在一定程度上增強了涂層的納米阻隔效果。此外,PANI優異的導電性也促進了金屬表面的鈍化[15]。ZHU等[16]采用苯胺原位氧化聚合法制備了rGO/Fe3O4/PANI三元納米復合材料,并將其添加到氨基丙烯酸樹脂中制備納米復合涂層,分析了復合涂層的防腐蝕機理。結果表明,納米復合涂層的耐蝕性得到了很大的提高,復合涂層具有獨特的物理屏障作用和陽極鈍化機制[13]。
Fe3O4納米顆粒由于具有小尺寸納米阻隔效應和耐蝕性,已被廣泛應用于金屬防腐蝕涂料領域。為了進一步提高其金屬防腐蝕活性和分散性,筆者采用具有電化學防腐蝕活性的PANI對其復合改性,構建了具有核殼形態的二元納米復合材料。在此基礎上,引入氧化石墨烯負載Fe3O4納米顆粒,并以水性環氧樹脂(EP)為填料,采用苯胺原位氧化聚合法制備了水基rGO/Fe3O4/PANI三元納米復合材料。采用Tafel極化曲線、電化學阻抗譜和中性鹽霧試驗研究了該腐蝕涂層的防腐蝕性能和機理,以期為替代有毒重金屬防腐蝕材料提供理論依據。
1. 試驗
1.1 試驗材料及表面預處理
試驗基體材料為馬口鐵工件,其化學成分如表1所示。將其加工成尺寸為120 mm×50 mm×0.5 mm的試樣,采用高溫(200~300 ℃)除油,用砂紙拋光,然后在丙酮和乙醇溶液中超聲處理以脫脂,干燥后備用。
主要試驗試劑有四氧化三鐵(山東國化化學有限公司),乙酸(濟南廣宇化工有限公司),氧化石墨烯(常州第六元素材料科技股份有限公司),苯胺(濟南銀潤化工有限公司),過硫酸銨(APS)(濟南金昊化工有限公司),正丁醇(南京卓誠石油化工有限公司),環氧樹脂(E-44)(廣州共富化工有限公司),吡啶(C5H5N)(南京華曦化工有限公司),固化劑(T-31)(山東優索化工科技有限公司),分散劑D-346(廣州共富化工有限公司)。
1.2 納米復合涂層的制備
1.2.1 納米復合材料的制備
將0.25 g氧化石墨烯和0.25 g Fe3O4加入200 mL蒸餾水中,倒入容量為300 mL的三頸燒瓶中。加入0.5 g苯胺,100 ℃下反應3 h冷卻至20 ℃。加入乙酸使溶液pH為1,加入0.5 g苯胺,冰浴使溫度穩定在0~5 ℃。用電子天平稱量2.72 g過硫酸銨溶于50 mL蒸餾水中,通過滴液漏斗勻速加入三頸燒瓶中,氧化聚合10 h。經過濾后,用乙醇和水各洗滌3次,80 ℃真空干燥24 h,得到rGO/Fe3O4/PANI復合材料。圖1為rGO/Fe3O4/PANI復合材料制備工藝示意,可以看出氧化石墨烯薄片首先被超聲波分散,而Fe3O4則在鐵氧配位的驅動力下被加載到氧化石墨烯薄片上。其次,以苯胺為還原劑制備rGO,形成rGO/Fe3O4復合材料。然后苯胺在Fe3O4和rGO表面進行原位氧化聚合,最后用聚苯胺涂覆rGO/Fe3O4復合材料,制備出了具有多層結構的rGO/Fe3O4/PANI三元復合材料。
1.2.2 納米復合涂層的制備
將0.6 g rGO/Fe3O4復合材料(rGO、Fe3O4質量比為1∶1)與0.225 g分散劑D-346摻入10 g蒸餾水中,超聲分散均勻。稱取環氧樹脂15 g,加入15 mL稀釋劑,機械攪拌至均勻分散。1 h后,加入促進劑吡啶(2.5 mL),攪拌20 min。加入固化劑T-31(3.0 mL),攪拌30 min。將分散好的rGO/Fe3O4復合材料加入環氧樹脂中,室溫超聲2.5~3 h。將rGO/Fe3O4/EP涂料均勻涂覆在拋光干凈的馬口鐵試樣上,在180 ℃下固化1 h,制備得到填充量為2.5%的rGO/Fe3O4/EP涂層。同樣的,采用上述方法制備填充量為2.5%的rGO/Fe3O4/PANI/EP涂層(rGO、Fe3O4和PANI的質量比為1∶1∶4)。
1.3 rGO/Fe3O4/PANI復合材料的分散性
分別取10 mL rGO/Fe3O4/EP和rGO/Fe3O4/PANI/EP涂料倒入離心管中靜置48 d,結果如圖2所示。從圖2中可以看出,rGO/Fe3O4/EP涂料靜置48 d后發生分層,上層為環氧樹脂,下層為rGO/Fe3O4二元納米顆粒。這是因為氧化石墨烯還原后,表面活性基團消失,其表面與樹脂基團相互作用的活性點大大減少,疏水性增加,因此rGO/Fe3O4復合材料不易分散在環氧樹脂中。對于rGO/Fe3O4/PANI/EP涂料,表面PANI可與環氧樹脂中的環氧基團發生開環反應生成羥基,極大地促進了其在樹脂中的分散。因此,與二元納米材料相比,三元納米材料具有更好的分散穩定性。
1.4 表征與測試
1.4.1 電化學測試
在CHI660A電化學工作站上進行電化學試驗。試樣用HY914膠水密封。工作電極為涂覆純環氧樹脂涂層、rGO/Fe3O4/EP和rGO/Fe3O4/PANI/EP復合涂層的馬口鐵試樣(以下分別簡稱純環氧涂層試樣,rGO/Fe3O4試樣,rGO/Fe3O4/PANI試樣),工作面積為10 mm×10 mm,參比電極為飽和甘汞電極(SCE),輔助電極為1.0 cm2鉑網,腐蝕介質為室溫3.5%(質量分數)NaCl溶液,試驗時間為1,7,14,21,28,35,42,49,56,70 d,溶液pH為7。在N2下穩定10 min開始測試,試驗在室溫下進行。在開路電位穩定后,測試電化學阻抗譜(EIS)和Tafel極化曲線。在3.5%(質量分數)NaCl溶液中,pH為1和9條件下,試驗時間為1,7,14,21,28,35,42,49,56,70 d,對rGO/Fe3O4/PANI試樣進行EIS測試。
Tafel極化曲線測試參數如下:掃描范圍為開路電位±500 mV,掃描速率為5 mV/s。EIS測試參數如下:頻率范圍為0.01~ 105 Hz,交流電壓幅值為0.01~1 V。為了避免雜散電流和外部干擾,系統被放置在一個自制的法拉第屏蔽籠中。利用電化學分析儀軟件對試驗數據進行外推。用Zsimp Win軟件進行數據擬合。
1.4.2 中性鹽霧試驗
根據GB/T 10125-2012《人造氣氛腐蝕試驗鹽霧試驗》,采用HDYW-120鹽霧箱進行中性鹽霧試驗,試驗介質為5%(質量分數)NaCl溶液,試驗材料為純環氧涂層試樣、rGO/Fe3O4/EP試樣和rGO/Fe3O4/PANI/EP試樣。具體方法為將涂層以傾斜角度15°放置在鹽霧腐蝕試驗箱中,連續噴5%NaCl溶液,試驗時間為168 h和360 h。
1.4.3 透射電子顯微鏡(TEM)
將樣品分散在乙醇中,用移液槍取少量樣品滴在銅網上烘干,通過TecLiiG20型透射電子顯微鏡(TEM)觀察樣品的微觀形貌。
2. 結果與討論
2.1 微觀形貌
如圖3所示:Fe3O4納米顆粒負載在rGO薄片上;rGO/Fe3O4/PANI三元共聚物中,Fe3O4與PANI形成了核殼結構,且PANI覆蓋在rGO薄片上。
2.2 涂層耐鹽霧腐蝕性能
由圖4可見:連續鹽霧168 h后,純環氧涂層試樣表面整個區域都發生了鼓泡和腐蝕,腐蝕程度比較嚴重,說明純環氧涂層的耐鹽霧腐蝕性能較差;rGO/Fe3O4/EP試樣表面起泡面積達到1/3以上,少數部位生銹,說明rGO/Fe3O4復合材料的加入提高了涂層的耐鹽霧腐蝕性能;相比之下,rGO/Fe3O4/PANI/EP試樣表面幾乎不起泡,說明rGO/Fe3O4/PANI/EP涂層的耐鹽霧腐蝕性能最好,涂層阻隔腐蝕介質效果明顯;rGO/Fe3O4/PANI/EP試樣在連續鹽霧360 h后開始起泡,這是由于涂層中rGO/Fe3O4/PANI三元共聚物多層結構的物理阻隔效應。
2.3 涂層電化學性能
2.3.1 Tafel極化曲線
由圖5可見:在3.5%NaCl溶液中浸泡21 d后,純環氧涂層試樣的自腐蝕電位為-513 mV,而rGO/Fe3O4/EP和rGO/Fe3O4/PANI/EP試樣的自腐蝕電位分別為-368 mV和-257 mV。這是由于rGO/Fe3O4/EP和rGO/Fe3O4/PANI/EP涂層的阻擋作用避免了陽極反應,陽極電位升高,說明兩者在3.5%NaCl溶液中都具有良好的阻擋作用。rGO/Fe3O4/PANI/EP試樣的自腐蝕電位最高,自腐蝕電流密度最低;rGO/Fe3O4/PANI/EP試樣的自腐蝕電流密度比rGO/Fe3O4/EP試樣低一個數量級,因此rGO/Fe3O4/PANI/EP涂層具有最好的耐蝕性[17]。
由表2可見,rGO/Fe3O4/PANI/EP涂層的防護效率為99.85%,這主要是由于涂層中rGO/Fe3O4/PANI復合材料的阻隔作用。具有層狀自組裝結構的rGO/Fe3O4/PANI納米復合材料增加了腐蝕性介質在涂層中的擴散和彎曲程度,對金屬基體起到良好的防腐蝕效果。
|
(1) |
式中:Jcorr,0為純環氧涂層試樣的腐蝕電流密度;Jcorr,i為其他涂層試樣的腐蝕電流密度;QEPE為涂層的防護效率。
試樣 | Ecorr/V | Jcorr/(A·cm-2) | QEPE/% |
---|---|---|---|
純環氧涂層 | -513 | 3.19×10-7 | — |
rGO/Fe3O4/EP | -368 | 3.37×10-9 | 93.20 |
rGO/Fe3O4/PANI/EP | -257 | 1.85×10-10 | 99.85 |
2.3.2 電化學阻抗譜
由圖6(a)和(b)可見:純環氧涂層試樣的|Z|0.01 Hz值從浸泡1 d時的3.67×108 Ω·cm2快速下降到浸泡21 d時的3.46×105 Ω·cm2,此后涂層基本失去防護性能;而浸泡21 d時rGO/Fe3O4/EP試樣和rGO/Fe3O4/PANI/EP試樣的|Z|0.01 Hz值分別為2.76×107 Ω·cm2和3.45×108 Ω·cm2,說明rGO/Fe3O4和rGO/Fe3O4/PANI納米復合材料提高了涂層的防腐蝕性能;其次,rGO/Fe3O4/EP試樣的|Z|0.01 Hz值在浸泡49 d時下降到5.32×105 Ω·cm2,此時涂層已失去防腐蝕效果[18];而rGO/Fe3O4/PANI/EP試樣在浸泡70 d時的|Z|0.01 Hz值仍有2.31×107 Ω·cm2,說明rGO/Fe3O4/PANI/EP涂層的阻隔性能優于rGO/Fe3O4/EP涂層。這是由于自組裝的rGO/Fe3O4/PANI復合材料使腐蝕性介質在涂層中的擴散路徑更長,所以腐蝕性介質到達金屬基體的時間也更長[19-20]。由圖6(d)~(f)可見:浸泡初期,涂層的單容抗弧半徑明顯減小,甚至低頻處出現尾弧,這表明腐蝕性介質開始穿透涂層,涂層阻抗逐漸減小,涂層電容逐漸增大,耐蝕性逐漸降低;隨著腐蝕介質的繼續滲透,浸泡21 d后純環氧涂層試樣的Nyquist圖出現了明顯的雙容抗弧,這表明腐蝕介質已穿透涂層到達金屬基體,基體表面發生了電化學腐蝕反應;rGO/Fe3O4/EP涂層的保護時間比純環氧涂層延長了28 d,即rGO/Fe3O4/EP涂層的耐蝕性優于純環氧涂層;而rGO/Fe3O4/PANI/EP涂層處于單容抗弧狀態,在浸泡70 d后,rGO/Fe3O4/PANI/EP涂層仍起到了良好的保護作用。這是因為,除了rGO/Fe3O4/PANI復合材料具有良好的阻隔效果外,PANI在中性溶液中具有氧化還原活性和良好的耐電化學腐蝕性能,可在金屬基體上形成致密的氧化膜。在浸泡初始階段,采用圖7(a)所示的等效電路擬合,隨著浸泡時間的延長,腐蝕性介質在涂層中不斷擴散,直至與金屬基體接觸,此時采用圖7(b)所示的等效電路擬合。其中:Rs為工作電極和參比電極間溶液電阻;Rc為涂層電阻;Cc為涂層的常相位角元件;Cd為雙電層的常相位角元件;Rcorr為電化學電荷轉移電阻。
由圖8可見:當pH為1時,rGO/Fe3O4/PANI試樣在浸泡1 d后的|Z|0.01 Hz為2.49×109 Ω·cm2,浸泡21 d后為5.99×107 Ω·cm2;浸泡56 d后,|Z|0.01 Hz還穩定在2.5×106 Ω·cm2,Nyqusit圖仍然顯示單容抗弧;當pH為9時,浸泡49 d后,rGO/Fe3O4/PANI試樣的|Z|0.01 Hz降至106 Ω·cm2以下,浸泡56 d后,Nyqusit曲線出現雙容抗弧,說明涂層在堿性介質中已基本失去防護功能。結合圖6和圖8可知,rGO/Fe3O4/PANI/EP涂層在中性和酸性溶液中具有良好的防腐蝕性能。
2.4 防腐蝕機理討論
由圖9可見:在浸泡初期,兩種涂層由于疏水性好,都能起到很好的阻隔作用,O2和H2O等腐蝕性介質被阻隔在涂層的外表面;隨著浸泡時間的延長,腐蝕性介質逐漸滲透到涂層中,與圖9中的純環氧涂層相比,加入rGO/Fe3O4和rGO/Fe3O4/PANI復合材料可以填充環氧樹脂的孔隙。這可在涂層中引起“迷宮效應”,即腐蝕性介質在涂層中滲透路徑的彎曲程度增大,涂層的耐蝕性得到進一步提高[21]。
在浸泡過程中,涂層電阻降低,對應的涂層電容(Cc)增大。當腐蝕性介質穿透涂層并到達金屬基體表面時會與其發生腐蝕反應,此時界面處會出現雙電層電容(Cd)和電荷轉移電阻(Rcorr),rGO/Fe3O4/EP涂層在界面處的電荷轉移電阻較低,金屬基體在腐蝕介質H2O和O2等的作用下容易生銹,造成表面腐蝕。對于rGO/Fe3O4/PANI/EP涂層,聚苯胺和石墨烯都具有一定的導電性,可以將電子轉移到涂層表面,發生陰極反應O2+2H2O+4e-→4OH-。當基體接觸到腐蝕性介質時,發生電化學腐蝕產生Fe3+,聚苯胺本身被還原為還原態聚苯胺(LS),而Fe3+與O2-反應生成穩定氧化物Fe2O3[22]。LS在O2和H2O共存環境中被氧化成本征態聚苯胺(EB)。由于PANI的還原氧化活性具有可逆性,在腐蝕介質不斷滲透的過程中,反應可以循環進行,從而逐漸形成致密的氧化膜。致密氧化膜的存在大大增加了界面Rct,延緩了金屬表面的腐蝕速率。因此,與rGO/Fe3O4/EP涂層相比,rGO/Fe3O4/PANI/EP涂層不僅具有更好的阻隔效果,而且在腐蝕性介質滲透過程中可以激發聚苯胺的電化學防腐蝕性能,從而形成涂層的智能防腐蝕機制。
3. 結論
(1)與純環氧涂層和rGO/Fe3O4/EP涂層相比,rGO/Fe3O4/PANI/EP涂層的耐鹽霧腐蝕性能最佳,分散性好,穩定性好。腐蝕介質通過涂層發生電化學腐蝕時可激發聚苯胺的還原氧化活性,形成致密的氧化膜。rGO/Fe3O4/PANI/EP涂層在中性和酸性溶液中具有良好的耐蝕性,優于rGO/Fe3O4/EP涂層。
(2)rGO/Fe3O4/PANI納米復合材料的防腐蝕機理是層狀的微觀結構產生的有效物理屏障作用和聚苯胺在腐蝕性介質滲透過程中激發的電化學防腐蝕性能,二者協同作用形成智能防腐蝕機制。
免責聲明:本網站所轉載的文字、圖片與視頻資料版權歸原創作者所有,如果涉及侵權,請第一時間聯系本網刪除。
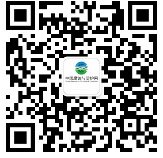
官方微信
《腐蝕與防護網電子期刊》征訂啟事
- 投稿聯系:編輯部
- 電話:010-62316606
- 郵箱:fsfhzy666@163.com
- 腐蝕與防護網官方QQ群:140808414