質量濃度/(kg·m-3) | 料漿質量分數(shù)/% | |||
---|---|---|---|---|
尾砂 | 水泥 | 粉煤灰 | 水 | |
955 | 325 | 125 | 242 | 75/78 |
我國是鋁土礦的開采大國,在鋁土礦開采過程中產(chǎn)生了大量尾礦砂,如不加以合理利用,會對礦山的生態(tài)環(huán)境造成嚴重威脅[1]。目前,我國主要采用分層式充填回采工藝消納鋁土礦尾砂[2]。為了提高礦山的井下回采效率,采用尾砂和水泥組成的基體制備充填料漿,經(jīng)過水化形成的人工充填柱可以對井下地壓、圍巖應力和地層位移進行有效控制[3]。我國的膠東半島分布大量鋁土礦,礦山臨近黃海海域,該地區(qū)的地下水成分復雜,井下的水體通常高度礦化,富含大量腐蝕性鹽離子[4]。研究發(fā)現(xiàn),山東省部分鋁土礦的礦山水質腐蝕性較強,使材料的強度降低,加速充填體在上覆巖層壓力作用下的變形,進而降低開采的安全性和穩(wěn)定性[5]。目前,地下水的腐蝕效應對充填材料的破壞經(jīng)歷了復雜的化學反應,其腐蝕規(guī)律和機理尚不明確。
在富含鹽鹵離子的地下水中,大量腐蝕性物質的長期作用使得充填材料內的水化凝膠開裂,在腐蝕效應與外部荷載的共同作用下出現(xiàn)應力集中,這會降低材料的力學性能[6-8]。因此,掌握充填材料強度指標在腐蝕過程中的演變規(guī)律,對充填支護穩(wěn)定性具有重要意義。另外,溶液中腐蝕性離子的長期作用會對充填體的結構產(chǎn)生顯著影響,水化產(chǎn)物開裂,并逐漸發(fā)展形成裂隙通道,加速腐蝕性離子進入材料內部,導致力學性能進一步衰減[9-12]。尾砂-水泥充填材料實質上是一種水泥基砂漿材料,加強關于地下水腐蝕作用機理的研究,將有利于在實際工程中提出相應的防護措施,以保障充填采礦的安全施工。
筆者以膠東半島某鋁土礦的超細尾砂-水泥充填材料為研究對象,采用模擬地下水環(huán)境的腐蝕液對試件進行不同時間的浸泡處理,并分別對浸泡不同時間的試件開展單軸壓縮試驗、計算機斷層(CT)掃描與微觀形態(tài)分析,最后結合試驗結果探討地下水腐蝕的微觀機理,研究結果有利于加深對充填體性能長期穩(wěn)定性的認識。
1. 試驗
1.1 試驗材料
本研究參照山東淄博市某鋁土礦現(xiàn)場的充填材料配合比,如表1所示。原材料包括:超細尾砂,水泥和粉煤灰,充填料漿的質量分數(shù)分別為75%和78%。試驗用集料取自礦山現(xiàn)場的鋁土礦尾砂,通過礦山碎石機進行破碎,得到了顆粒粒徑分布如圖1所示的尾砂,可以看出尾砂粒徑范圍為0.1~10 μm,是一種超細尾砂。拌和料漿采用的膠凝劑為P. O 42.5型水泥熟料,摻合料采用II級粉煤灰。根據(jù)試驗需求,采用灌入的方式,制備了直徑50 mm,高度100 mm的圓柱體試件。
1.2 腐蝕試驗
基于表2所示的膠東半島地下水離子成分檢測結果配制腐蝕液,用以模擬地下水腐蝕效果。通過對礦區(qū)內12個測點水質進行調研,發(fā)現(xiàn)地下水的pH為5.62~9.55,陽離子主要為Na+、K+、Ca2+和Mg2+等,陰離子主要為、Cl-和
等。
離子名稱 | Na+ | K+ | Ca2+ | Mg2+ | ![]() |
Cl- | ![]() |
---|---|---|---|---|---|---|---|
質量濃度/(mg·L-1) | 9 865 | 299 | 1 235 | 1 279 | 1 905 | 18 052 | 195 |
采用浸泡法對試件進行腐蝕試驗,先將養(yǎng)護齡期為28 d的試件浸沒在溶液中,浸泡時間分別為0,30,60,90,180,360 d。在浸泡過程中,每隔3 d換一次新的腐蝕液,以保障溶液中各離子含量和pH的恒定。在達到預定的腐蝕時間后,將充填體試件從溶液中取出,拭干表面的水,晾干后再開展后續(xù)試驗。
1.3 檢測方法
1.3.1 力學試驗
力學試驗所用的充填體圓柱試樣的直徑與高度分別為50 mm與100 mm。試驗前,將試件靜置在加載平臺上,壓縮速率設定為0.02 MPa/s。通過數(shù)據(jù)采集系統(tǒng)收集壓力和位移數(shù)據(jù),進而轉換成應力和應變數(shù)據(jù)。根據(jù)這些數(shù)據(jù)得到單軸抗壓強度fc,充填體變形模量Em按照式(1)計算。
|
(1) |
式中:σm和εm分別為峰值應力和應變;σi和εi分別為線彈性階段初始點的軸向應力和應變。
1.3.2 CT掃描
采用西門子公司生產(chǎn)的Sensation 40型X-ray CT掃描儀對充填材料進行掃描分析,通過高精度的圖像采集器捕捉試件的橫面切片,單次得到約280張的掃描切片。將CT圖像導入Image J軟件中,經(jīng)過像素點的統(tǒng)計與計算,得到充填體試件的面孔隙率ρ,計算公式如式(2)所示。
|
(2) |
式中:n為CT切片總數(shù)量;i為圖像序號;si為第i張圖像中的固體物質面積;ci為第i張圖像中孔隙面積。
1.3.3 SEM觀察
在大塊充填體試件中隨機選取具有代表性的小塊樣品,經(jīng)過切割、打磨、干燥、噴金處理后,采用場發(fā)射掃描電鏡(SEM)對樣品進行微觀形貌觀察。
2. 結果與討論
2.1 力學性能
由圖2可見:在初始加載階段,隨軸向應變的增加,軸向應力上升速率緩慢;隨后材料隨應變增加發(fā)生線彈性變形,應力在接近直線末端達到峰值,該值為抗壓強度fc;應力在達到峰值后迅速跌落,試件發(fā)生斷裂破壞;軸向應變超過1%后,應力下降趨勢趨于平穩(wěn),結構損傷達到最大。初始壓密階段和彈性變形分界點約在軸向應變?yōu)?.1%處,說明0.1%的應變是結構損傷發(fā)育的起始點[13]。
如圖3所示,隨著腐蝕時間不斷延長,充填體試件壓縮破壞類型逐步從壓裂型轉變?yōu)榧羟行?破壞過程中的剪切滑移面愈發(fā)明顯。綜合單軸壓縮試驗結果可以發(fā)現(xiàn),盡管不同時間下試件的應力-應變關系曲線的變化趨勢相近,但是試件的脆性破壞特征會隨著腐蝕損傷程度的累積而不斷提升。此外,根據(jù)充填體試件的表面狀態(tài),還可以看出隨著地下水的腐蝕時間增加,試件表面的腐蝕面積逐漸增大,說明地下水對試件的腐蝕程度不斷加重,這是出現(xiàn)材料力學性能衰減的直接原因[14]。
如圖4所示,隨著地下水腐蝕時間的增加,fc逐漸降低,且fc和Em在30~90 d范圍內變化較快,超過180 d后fc逐漸趨于穩(wěn)定。如圖4(a)所示,料漿質量分數(shù)為78%和75%的充填體試件的抗壓強度fc分別為10.92 MPa和9.79 MPa,在浸泡360 d后,fc的下降幅度分別為38.8%和33.6%。如圖4(b)所示,兩組試件的變形模量Em分別為155.8 MPa和122.9 MPa,浸泡360 d后Em的下降幅度分別為46.6%和36.3%。綜上可見,充填料漿質量分數(shù)對試件的力學性能也有顯著影響,適當提高料漿的質量分數(shù)有利于提高充填體的力學性能。然而,腐蝕180 d后,兩種充填體試件的強度參數(shù)逐漸趨于一致。
2.2 微觀結構
如圖5所示:CT圖像中的灰色區(qū)域為水化產(chǎn)物和尾砂組成的膠結體,黑色區(qū)域為裂隙;通過對比圖5(a)和(b)的CT圖像可見,漿體質量分數(shù)為78%的樣品密實度顯著高于漿體質量分數(shù)為75%的樣品。在腐蝕性地下水環(huán)境中,兩組充填體試樣在腐蝕0~60 d時的裂縫數(shù)量、寬度和長度均處于較小的狀態(tài),裂隙的開裂程度較低,在腐蝕60~360 d時,充填體內部的裂縫迅速延展、相互連接,裂隙數(shù)量快速增多。
2.3 面孔隙率
如圖6所示:在腐蝕初期,隨著腐蝕時間的延長,面孔隙率上升速率較快;在腐蝕時間大于120 d時逐漸減緩并逐漸趨于穩(wěn)定,漿體質量分數(shù)為78%和75%的充填體的平均面孔隙率分別達到了7.29%和7.01%。另外,面孔隙率隨著時間的增加呈指數(shù)型上升趨勢,兩者的相關系數(shù)為0.965。根據(jù)圖7呈現(xiàn)的擬合結果可見,在腐蝕過程中,充填體試件面孔隙率與抗壓強度呈現(xiàn)出相反的變化規(guī)律,但總體變化速率是相似的。對兩者進行數(shù)據(jù)擬合分析發(fā)現(xiàn),面孔隙率間存在負相關的線性關系,相關系數(shù)大于0.95。這說明在鹽鹵的腐蝕作用下,超細尾砂-水泥充填材料的微觀損傷程度與宏觀強度折減幅度具有一定的相關性,該現(xiàn)象與前人研究結果一致[15]。力學試驗和CT掃描結果共同表明,鹽鹵的腐蝕作用使得材料受到持續(xù)性的宏觀和微觀損傷,且損傷程度隨著腐蝕時間的增加不斷加重。試驗得到的抗壓強度與孔隙率的相關性較高,這說明采用CT掃描圖像預測充填體抗壓強度在地下水腐蝕過程中的折減程度較為合理且可行。
2.4 討論
為了進一步認識充填礦柱在地下水腐蝕作用下的損傷機理,以料漿質量分數(shù)為78%的充填體試件為觀察對象,對材料內部形成的水化產(chǎn)物進行觀察,得到了如圖8所示的未腐蝕與腐蝕90 d、180 d的微觀形貌。由圖8可見:未腐蝕的充填體水泥水化產(chǎn)物主要由絮凝狀水化硅酸鈣和針棒狀的鈣礬石組成,水泥凝膠物質呈現(xiàn)出均勻、平整和致密的狀態(tài),水泥膠結尾砂緊密接觸,孔隙尺寸較小;在腐蝕90 d后,充填體中的水化硅酸鈣排列較為松散,結石體中出現(xiàn)孔隙連通現(xiàn)象;充填材料的水化硅酸鈣在腐蝕180 d后明顯減少,孔隙在腐蝕過程中擴張,形成可供離子侵入和流動的連通裂隙,加速了水化產(chǎn)物的腐蝕進程[16]。由于在鹽鹵腐蝕環(huán)境中,超細尾砂-水泥充填材料中的孔隙液中富含大量的腐蝕性離子,誘發(fā)水化凝膠的解體和流失,且腐蝕液中大量Cl-侵入充填體內部后,促進了Na+和K+等陽離子的交換反應,進而加速化學腐蝕速率[17]。
因此,水化膠凝物質在地下水中的化學水解作用是充填體出現(xiàn)結構損傷的重要因素。在采礦工程中應重視對腐蝕環(huán)境中的人工礦柱進行有效的表面防護,以防止地下水中腐蝕性離子的滲入,從而減少充填體發(fā)生腐蝕的概率。
3. 結論
(1)超細尾砂-水泥充填體試件的抗壓強度衰減程度在鹽鹵腐蝕過程中逐漸提高,抗壓強度和變形模量隨腐蝕時間的增加均呈下降趨勢,料漿質量分數(shù)為78%和75%的充填體試件的抗壓強度分別降低了38.8%和33.6%,變形模量分別降低了46.6%和36.3%。料漿質量分數(shù)為78%的充填體試件的抗壓強度明顯高于料漿質量分數(shù)為75%的試件。然而,當腐蝕時間超過180 d時,料漿質量分數(shù)對試件抗壓強度的影響程度更加明顯。
(2)腐蝕作用對超細尾砂-水泥充填體試件的微觀結構產(chǎn)生顯著影響,面孔隙率的提高速率隨腐蝕時間的增加呈先快后慢的趨勢,兩者呈典型的指數(shù)關系,當腐蝕時間達到360 d時,料漿質量分數(shù)為78%和75%的充填體試件的面孔隙率分別達到7.32%和6.99%。
(3)充填體試件的抗壓強度和面孔隙率之間存在明顯的負線性關系,相關系數(shù)高達0.964,說明試件的宏觀力學性能與微觀裂隙指標的相關性較高。
(4)在地下水腐蝕環(huán)境中,離子與水泥水化物發(fā)生相互作用,孔隙持續(xù)擴張,顆粒間黏結程度不斷降低,最終導致充填體抗壓強度弱化。在實際工程中,應對鋁土礦礦井中的人工充填礦柱實施表面防護措施,以減輕鹽鹵腐蝕造成的微觀缺陷。
免責聲明:本網(wǎng)站所轉載的文字、圖片與視頻資料版權歸原創(chuàng)作者所有,如果涉及侵權,請第一時間聯(lián)系本網(wǎng)刪除。
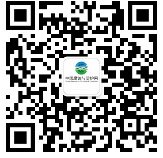
官方微信
《腐蝕與防護網(wǎng)電子期刊》征訂啟事
- 投稿聯(lián)系:編輯部
- 電話:010-62316606
- 郵箱:fsfhzy666@163.com
- 腐蝕與防護網(wǎng)官方QQ群:140808414