核能發電以其燃料能量密度高、基本零排放和土地占用少等優勢已經成為一些發達國家的首選和我國能源發展的重要趨勢之一。根據國際原子能機構(IAEA)統計,截至2023年10月,中國的在運核電機組規模居世界第三,居于世界領先地位;《中國核能發展報告2023》指出,未來我國核能發電占比將會逐步提高,保證核電產出的高效和安全是當前國家發展戰略之一。核電站的安全運行始終是擴大核電規模的重要前提,反應性控制、余熱排出和包容放射性物質是核電廠三項基本安全功能,其中“包容放射性物質”這一項對核電關鍵性結構材料在苛刻工況中服役的穩定性和可靠性提出了極高的要求。鋯合金具有力學性能優良、耐腐蝕強、中子吸收截面小和熱導率高等優點,廣泛應用于核反應堆的燃料包殼和堆芯結構部件的制造[1]。其中,重水堆中的重要結構部件壓力管就由Zr-2.5Nb合金制成。壓力管作為重水堆中燃料棒束和冷卻劑的容器,是重水堆一回路燃料通道的重要組成部分[2]。
19世紀70年代,研究人員首次在加拿大重水鈾反應堆(CANDU)中發現了壓力管內部氫化物引起壓力管內容物泄漏現象。研究表明,壓力管的破裂是由一種現在被稱為延遲氫化物開裂(DHC)的裂紋擴展造成的[3,4]。在反應堆運行過程中,壓力管與重水發生腐蝕會反應產生大量的氫原子,由于鋯金屬與氫結合力較強,氫原子極易進入壓力管內部。在應力場的作用下,氫原子易向高應力區(如微裂紋尖端)擴散,當高應力區的氫含量超出其極限固溶度時,難以繼續溶解的氫原子就會以氫化物脆性相的形式析出并穩定存在于鋯合金基體中。氫化物脆性相的存在會降低壓力管材料的斷裂韌性,當氫化物在應力作用發生斷裂時就會導致原有微裂紋的擴展或產生新的微裂紋,上述氫擴散、氫化物形核和生長、氫化物斷裂過程的反復發生,就會導致宏觀上DHC裂紋的擴展,最終致使重水冷卻劑的泄露,對重水堆的安全運行造成影響。目前,DHC被視為壓力管服役過程中最重要的潛在風險之一。來自加拿大、韓國、阿根廷和印度等國家的研究者均對重水堆壓力管用Zr-2.5Nb合金的DHC行為開展了大量研究,其中既包括DHC機理、模型構建及可靠性驗證,也較為系統的研究了溫度、氫含量、熱循環方式以及鋯合金本身微觀結構和力學性能等因素對DHC行為的影響。DHC擴展速率(DHCR)作為評估壓力管是否符合“破前漏”(LBB)準則的重要指標之一[5,6],是評價壓力管DHC行為的重點。此外,DHC作為一種受環境影響的亞臨界裂紋擴展[7],其萌生條件之一為應力強度因子達到DHC的門檻值KIH[8],為了預防和抑制DHC的產生,KIH測定是評價壓力管DHC失效的另一個重點。
當前我國僅有秦山三期建造的兩座重水堆核電站。秦山三期重水堆核電站自2003年7月建成投產以來,已服役超過20年(CANDU6型重水堆核電機組設計壽命為40年),根據加拿大標準協會相關標準CSA N285.4的要求,應定期對壓力管取樣并進行服役性能測試(其中包括DHCR測試和KIH測試),從而為壓力管的老化評估和壽命預測提供必要的數據支撐。此外,根據秦山三期重水堆設計文件手冊及最終安全分析報告,機組運行中期需更換壓力管。為提高核電站中國產零部件的比例,降低壓力管更換的經濟成本,減少進口依賴,近幾年我國陸續開展了國產壓力管的研制工作。在國產壓力管正式投入使用前,需對其抗DHC性能進行測試和驗證。目前國內對壓力管DHC行為的相關實驗研究較少,因此建立DHC行為相關測試方法,厘清各因素對DHC行為的影響,對壓力管的壽命評估與延壽以及國產壓力管制造和性能測試有重要意義。本文就常用DHC測試方法、DHC相關機理以及各種因素對DHC行為的影響等方面進行綜述,指出當前的研究不足,并對未來的研究趨勢進行了展望。
1 DHC行為研究方法
為模擬壓力管服在富氫環境下大量吸氫的現象,需在DHC實驗前對壓力管材料進行預充氫實驗,通常用的充氫方法有氣體充氫、高壓釜滲氫、電解充氫等[9~11]。其中,電解充氫所需設備簡單易得、操作便捷且可重復性高,應用最為廣泛。由于壓力管材料的各向異性,研究者結合壓力管的形狀和實際服役工況,通常采用兩種不同的試樣分別用于研究壓力管軸向和徑向DHC行為。其中,測試徑向DHC行為采用的是懸臂梁(CB)試樣;測試軸向DHC行為采用的是彎曲緊湊拉伸(CCT)試樣,其取樣方式如圖1所示。為促進DHC裂紋的萌生,縮短加載與裂紋萌生之間的孕育期,通常需要在CCT試樣上預制疲勞裂紋;受限于CB試樣的形狀,在CB試樣上引入疲勞裂紋較為困難,因此在加工試樣時盡量降低缺口底部幾何形狀的直徑。圖2為測試過程中兩種試樣的受載示意圖,除圖2中所示的基本受載條件外,DHC實驗還需要高溫爐等能精確控制溫度變化的設備加以輔助,常采用聲發射法(AE)或直流電位降法(DCPD)監測裂紋的萌生與擴展[12~14]。由于DHCR和KIH是評估壓力管服役性能的重要指標,目前中國科學院金屬研究所已經建成了壓力管軸向DHCR和KIH的測試方法,并聯合上海核工程研究設計院股份有限公司、中核核電運行管理有限公司、廣東腐蝕科學與技術創新研究院和核工業標準化研究所編制了針對壓力管軸向KIH和DHCR測試的中國核學會團體標準3項,預計將于近期發布實施。
圖1
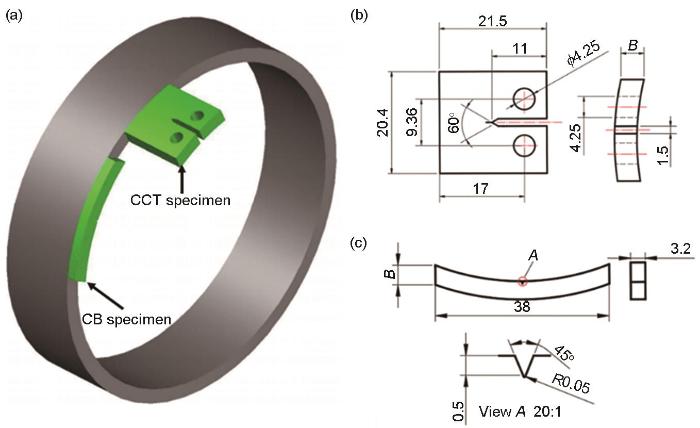
圖1 試樣取樣及尺寸示意圖
Fig.1 Schematic diagrams of sampling (a) and dimensions of CCT specimen (b) and CB specimen (c). B is thickness of pressure tube in Fig.1b and 1c, the unit is mm
圖2
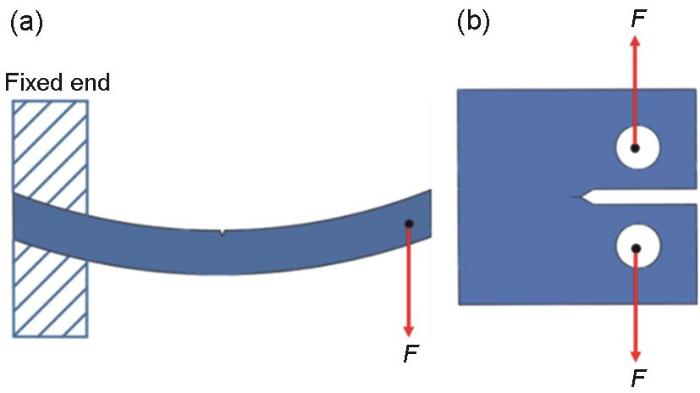
圖2 試樣加載示意圖
Fig.2 Schematic diagrams of loading for CB specimen (a) and CCT specimen (b). F is the external load
1.1 KIH 測試
由于升K法測KIH時,先施加的較小載荷雖不會引起裂紋擴展,但可能會導致裂紋尖端發生鈍化[16],從而降低了裂紋尖端的應力集中程度,因此一定程度上會造成所測的KIH值偏大;而降K法實驗過程中,施加初始載荷初期就使裂紋尖端產生DHC擴展,可避免裂紋尖端的鈍化,保證了KIH測試值的準確性。因此,通常采用降K法測試KIH。當采用降K法測試KIH時,判定所測的KIH是否有效,除需滿足DHC裂紋保持24 h以上不發生擴展外,還需滿足兩個條件:(1) 試樣斷口表面,靠近試樣兩側自由表面的韌性斷裂區域的面積小于試樣表面總的斷裂區域面積的10%;(2) DHC擴展過程中,在試樣的厚度方向,裂紋擴展的前沿近似均勻、平直,厚度方向大多數位置的裂紋擴展長度與利用九點法測得的平均裂紋長度之間的偏差小于10%。
1.2 DHCR測試
如前文所述,DHCR是評價材料抗DHC性能和是否符合“破前漏”要求的重要指標之一。如圖3所示,DHCR隨KI的變化可分為3個階段,當位于Stage II時,DHCR幾乎不隨KI的變化而改變[17,18]。因此,在DHCR測試實驗中,對試樣施加適當恒載荷,使KI處于Stage II階段。KIH一般小于10 MPa·m-2,KIC大于30 MPa·m-2,因此初始KI通常設置在15~20 MPa·m-2的范圍內。在此條件下,雖然KI隨著DHC擴展而增加,但DHCR基本不受KI改變的影響。實驗結束后,通過九點法或面積法測量斷口的DHC裂紋長度,裂紋擴展時間則通過DCPD或AE信號的變化獲得。由于在Stage II階段,DHCR對KI無明顯依賴性,因此通常將實驗過程中的裂紋擴展視為勻速擴展,將裂紋長度與裂紋擴展時間的比值作為DHCR的測試值。
圖3

2 鋯合金中氫化物析出行為和氫固溶度
2.1 氫化物在鋯合金中的析出行為
氫在鋯合金中的擴散和聚集是發生DHC現象的首要原因,因此對氫化物在鋯合金中析出行為的研究是明確DHC機理的基礎。如上文所提到的,壓力管在高溫高壓的服役過程中與重水發生腐蝕反應而產生大量的氫原子:
(1)
當進入材料內部的氫原子數量超出氫固溶度時,氫原子會以氫化物的形式析出,造成鋯合金部件局部或整體力學性能的下降。Zr為密排六方結構,目前在Zr及其合金中觀察到的氫化鋯有δ-ZrH1.66、γ-ZrH、ε-ZrH2和ζ-Zr2H[20,21],最為常見的是前兩種。其中δ-ZrH1.66結構最為穩定[22],為面心立方結構,在鋯合金中沿特定的慣習面析出[23~25];近期,西安交通大學在Zr-Zn-Nb-Fe合金中觀察到應力誘發δ-ZrH1.5在Zr晶體的柱面析出,取向關系為<10
在工程使用前,壓力管經歷了高溫擠壓、冷加工和去應力退火等過程,壓力管用Zr-2.5Nb合金由α-Zr相和β-Zr相兩相組成。α-Zr相被沿壓力管軸向方向拉長,β-Zr相呈薄片狀分布在兩個相鄰的α-Zr相晶粒之間[14]。δ-ZrH1.66多在α-Zr和β-Zr相界處形核,并由相界處向α-Zr相內部生長形成穿晶氫化物片[29]。Zr-2.5Nb合金中觀察到的δ-ZrH1.66析出慣習面多近似平行于(0001) α-Zr[30]。Perovic等[29]研究表明無外加應力條件下,氫化物片沿壓力管切向堆疊,在宏觀上呈現出氫化物長度方向與壓力管切向平行的現象;有外加應力條件下,氫化物片沿壓力管徑向堆疊,在宏觀上呈現出氫化物長度方向與壓力管徑向平行的現象。切向氫化物通常對壓力管影響較小,而外加應力作用下產生的徑向氫化物會顯著降低鋯合金管材的力學性能,其破裂直接導致DHC的萌生和擴展[31,32]。
2.2 鋯合金中的氫固溶度
鋯合金中氫的極限固溶度(TSS)直接影響氫化物能否析出和溶解氫的含量,后者還是氫原子擴散速率的重要影響參數。獲得準確的TSS有助于預測壓力管的DHC行為,因此許多研究者用差示掃描量熱法和紅外熱導法等測量了不同鋯合金在不同溫度下的TSS[33,34]。鋯合金的TSS通常有兩種表示方法:一種是在升溫過程中鋯合金中所能溶解的最高氫含量,稱為溶解極限固溶度(TSSD);另一種是在降溫過程中氫化物恰好不析出的最大溶解度,稱為析出極限固溶度(TSSP)。Motta等[35]總結了以上兩種條件下測得的極限固溶度數據。如圖4所示,TSSD固溶曲線和TSSP固溶曲線并不重合,相同溫度下,TSSP固溶度高于TSSD固溶度。造成TSSD和TSSP差異的原因主要是析出的氫化物與鋯基體的晶格失配度較大。降溫過程中,氫原子從基體中脫溶導致晶格應變能的降低并不足以抵消氫化物析出造成晶格應變能的增加,因此氫化物析出受到抑制,氫在鋯中過飽和溶解,導致TSSP高于平衡條件下的TSS;在升溫過程中,氫化物發生溶解,由于已經析出的氫化物在其周圍造成了塑性變形,消耗了由于氫化物析出造成的多余晶格應變能,降低了氫化鋯溶解進鋯基體的傾向,使TSSD低于TSSP[36]。
圖4
3 DHC行為機理及模型
圖5為DHC裂紋擴展的基本過程示意圖。如5a所示,氫原子在應力誘導作用下向高應力區(裂紋尖端或缺口前端)擴散并富集;當裂紋尖端氫濃度高于氫的固溶度時,氫化物形核析出并長大(圖5b);位于裂尖的氫化物在應力集中的作用下斷裂,且裂紋與原有的裂紋尖端相連,引起原有裂紋擴展一小段距離后止裂(圖5c);隨后氫原子向新的裂紋尖端擴散,并形成新的氫化物(圖5d)。以上過程不斷重復進行就導致了DHC裂紋的擴展[40]。目前,不同研究者對上述的DHC裂紋擴展過程基本認同,但對氫原子向高應力區擴散的根本驅動力還存有爭議。國內外研究者針對DHC裂紋擴展機理建立了多種模型,其中比較具有代表性的是Dutton-Puls模型[41,42]和Kim's模型[36],下面就兩個模型進行討論。
圖5
3.1 Dutton-Plus模型
Dutton-Puls模型(D-P模型)認為發生DHC的第一步是氫原子向裂紋尖端等應力集中區域的擴散[43]。拉應力使鋯的晶格常數增加,更易容納氫原子,即拉應力的存在使氫原子在鋯基體中的化學勢降低[44]。在應力集中的作用下,裂紋尖端受拉應力最大,因而氫原子在裂紋尖端的化學勢最低,相當于在裂紋尖端形成“氫阱”[43,45]。位于低應力區的氫原子在化學勢梯度的作用下向裂紋尖端擴散,造成氫原子不斷在裂紋尖端富集,直至達到平衡狀態。由上述分析可知,氫原子擴散的直接原因是化學勢梯度,而化學勢梯度是由應力梯度造成的,因而D-P模型中認為氫原子擴散的根本驅動力是應力梯度。如果達到平衡時裂紋尖端的氫含量高于TSSP,則在氫擴散至平衡狀態前,裂紋尖端處會因氫含量達到TSSP而析出氫化物,從而導致裂紋尖端的溶解氫濃度降低;由于未達到平衡狀態,氫原子持續向裂紋尖端擴散,從而導致裂尖區氫化物的生長,生長至臨界尺寸后發生斷裂。反之,若達到平衡所需的氫含量低于TSSP,則裂紋尖端無氫化物析出,DHC現象也就不會發生[46]。
(2)
(3)
(4)
(5)
(6)
其中,DH = α-Zr中氫擴散常數(m2/s);C
從表達
3.2 Kim's模型
Kim's模型認為DHC現象發生的第一步是氫化物的析出[43],DHC裂紋擴展的驅動力是裂紋尖端處氫化物析出后導致裂紋尖端與其他位置的氫濃度差ΔC[36]。Kim等用TSSD和TSSP曲線對該模型進行了解釋,如圖6所示,當溫度升高至300 ℃時,試樣中的溶解氫含量處于A點,此時裂紋尖端和基體沒有濃度差。當再降溫至250 ℃時,由于TSS的“滯后效應”,基體的溶解氫含量會降至B點,但此時基體中的溶解氫含量未達到析出值。裂紋尖端處應力較大,誘發了氫化物的析出(Kim's模型認為[36],應力集中使裂紋尖端產生塑性變形,能降低氫化物析出產生的晶格應變能,使氫化物更易析出),溶解氫含量降至C點。至此,裂紋尖端和基體產生了氫的濃度差ΔC。為證明DHC裂紋擴展的驅動力是ΔC而非D-P模型中的應力梯度,研究中通過將試樣加熱到不同溫度后再降溫的方法獲得具有不同ΔC的試樣,并對這些試樣施以相同的應力強度因子。結果表明,在應力強度因子相同的情況下,ΔC越大,試樣的DHCR越大,ΔC可達到的最大值為測試溫度下的TSSP減去TSSD[36]。
圖6
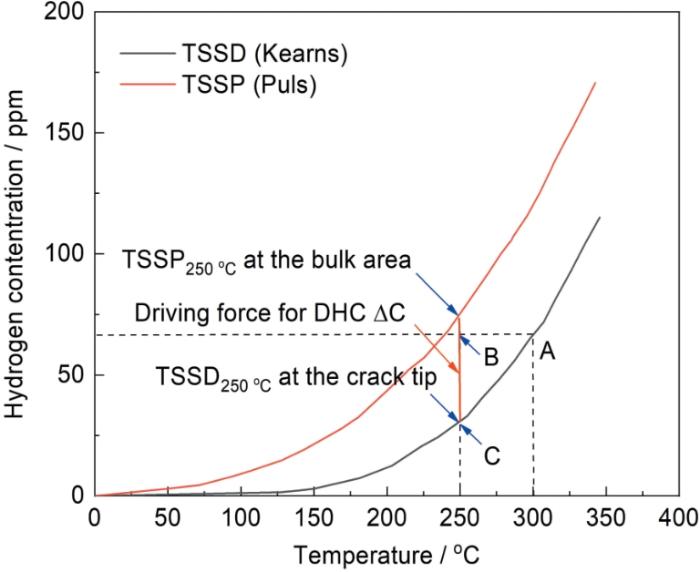
基于以上分析,Kim還提出了DHCR計算公式:
(7)
其中,k =與材料有關的系數;JH =氫擴散通量(kg/(m2/s));ΔC =基體和裂紋尖端的氫濃度差(mg/kg);DH =氫擴散系數(m2/s);ΔX =裂紋尖端塑性區尺寸(m);KIH =裂紋擴展臨界應力強度因子(MPa·m-2);σYS =屈服強度(MPa)。
3.3 其它模型
不同于以上兩種模型對DHC過程進行大量簡化和假設,Varias 模型將含有氫化物的鋯合金視為彈性復合材料,引入連續的擴散-熱力學-機械耦合場,模擬DHC過程中真實的應力和溫度[50,51]。Jernkvist等在Varias模型中引入氫化物相轉變動力學,以更精確的描述氫化物的析出和溶解行為[52,53]。Shmakov模型采用了與D-P模型相似的物理原理,不同的是該模型認為氫原子擴散是非穩態的,并用分步數值計算的方法獲得氫原子擴散通量[54]。Shmakov模型能較好的預測DHCR隨KI變化的3個階段和接近臨界溫度時DHCR降低的現象。上述模型各具特色,但仍難以統一共識。隨著模擬計算能力和微觀分析檢測能力的不斷提升,相信未來的模型會越來越準確。
4 不同因素對DHC行為的影響
4.1 材料微觀結構和力學性能的影響
壓力管在服役過程中受到高溫和輻照的雙重影響,其微觀結構和力學性能會發生變化,進而對DHC行為產生影響。
前文已經提到,Zr-2.5Nb合金中含有α-Zr相和β-Zr相兩相,α-Zr相晶粒沿壓力管軸向被拉長,β-Zr相呈連續或半連續狀態沿軸向分布在α-Zr相晶粒之間[14]。由于微觀結構的各向異性,DHC行為也表現出各向異性。Kim等[14]研究表明氫在β-Zr相中的擴散速率較快,當裂紋擴展方向與β相分布方向一致時,會形成氫擴散的快速通道,裂紋起裂要求較低,因此軸向DHCR是徑向DHCR的1.8~2倍,軸向KIH也高于徑向KIH。研究結果表明,400 ℃熱處理會使原本在軸向上連續分布的β-Zr相發生分解,熱處理時間越長,β-Zr相分解程度越高[55]。隨著熱處理時間延長,軸向和徑向的DHCR均降低。Jovanovic等[12]認為β-Zr相的分解降低了氫原子在壓力管軸向的擴散速率,這是熱處理導致軸向DHCR降低的主要原因;此外,材料的屈服強度隨著熱處理時長的增加而降低,有效緩解了裂紋尖端的應力集中程度,降低了裂紋尖端氫化物的斷裂傾向,一定程度上抑制了DHC裂紋的萌生和擴展,這是導致軸向DHCR隨熱處理時長的延長而降低的另一個原因。對于徑向DHCR,軸向氫擴散速率的下降對其基本沒有影響,導致徑向DHCR降低的主要原因是屈服強度的降低,因此徑向DHCR下降幅度也小于軸向DHCR,且隨著熱處理時間的延長,軸向DHCR與徑向DHCR的比值減小[55],壓力管DHC行為的各向異性程度降低。除熱處理外,輻照也能顯著提高材料的屈服強度,從而導致較高的DHCR,使代表氫化物斷裂尺寸的斷口條紋寬度降低[56]。
4.2 KI 的影響
KI對DHC行為的影響可根據KI與KIH和KIC相對關系大致分為3個階段(圖3):在Stage I,KI略大于KIH,DHCR隨KI的增加而急劇上升;Stage I的KI范圍較小,隨后進入DHCR對KI不敏感的Stage II;當KI繼續增加至KIC附近時,DHCR再次隨著KI的增加而急劇增長,即進入Stage III。在Stage III發生裂紋失穩擴展的現象較易理解,但對Stage I和Stage II所呈現的規律的機理以及這兩個階段的具體的分界點仍不清晰。
Yan等[57,58]重點關注了KI在KIH附近時氫化物的生長及斷裂情況。結果表明,當KI < KIH時,裂紋尖端的氫化物尺寸隨KI的增加而增加且不發生斷裂;當KI > KIH時,氫化物斷裂,其斷裂尺寸隨KI的增加呈先降低后趨于穩定的趨勢。氫化物的生長是一個自限性過程,隨著氫化物尺寸的增加,氫化物生長的驅動力逐漸減弱,因此在達到臨界斷裂尺寸前,氫化物就已經停止生長,即DHC不發生。隨著KI的增加,裂紋尖端氫化物所受的應力增加,這會導致氫化物更易斷裂,即臨界斷裂尺寸減小;裂紋尖端塑性區尺寸隨KI增加,這為氫化物提供了更大的生長空間和驅動力。因此,在KI增加的過程中,必然存在一個臨界點,使氫化物的實際尺寸等于臨界斷裂尺寸,該臨界點對應的KI即KIH[41]。在KI略大于KIH的小范圍內,KI的增加使氫化物臨界斷裂尺寸繼續減小,氫化物更易斷裂;并且KI的增加促進了氫原子向裂紋尖端擴散和氫化物的生長速率,因此在該范圍內DHCR隨KI的增加而急劇升高(Stage I)。
圖7
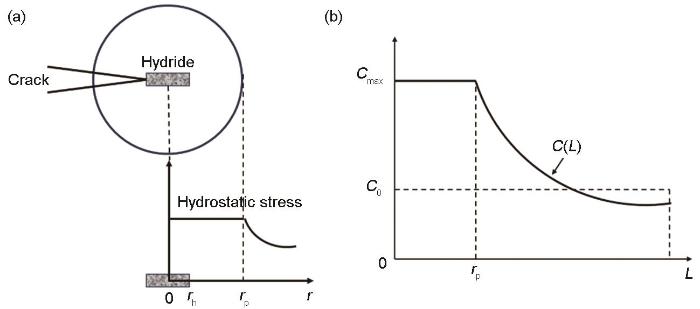
圖中,C0為無應力區原始氫濃度,rp為靜水應力開始降低的轉折點(在裂紋尖端附近),L ? rp,C(L)為r=L處的氫濃度,Cmax為應力作用下裂紋尖端所能達到的最高氫濃度(并非裂紋尖端實際的氫濃度,若Cmax > TSSP,則在實際氫濃度到達Cmax前就有氫化物析出,導致氫含量降低)。從圖中可知,當r < rp時,即在裂紋尖端及其附近的范圍內,靜水應力保持恒定,氫濃度也保持恒定。C0與C(L)以及Cmax的關系,如
(8)
(9)
(10)
(11)
其中,Φ(r)為應力勢能;
裂紋足夠尖銳的條件下,塑性區內P(r)的表達式如下:
(12)
(13)
其中,σy為屈服強度(MPa);KI為應力強度因子。
將
(14)
將
(15)
由
4.3 溫度的影響
DHC裂紋擴展是一個熱激活過程[41],其中,氫原子擴散、氫化物析出和氫化物斷裂等均受到溫度的影響。雖然壓力管的實際服役溫度較為穩定,但停堆檢修期間涉及到溫度的變化,因此明確溫度對DHC行為的影響有助于尋找降低壓力管泄漏風險的措施。
對于固定的氫濃度,溫度過高會使氫濃度低于或略高于TSSP,從而導致氫化物不析出或析出困難,因此DHC現象的發生存在臨界溫度。Sagat等發現當溫度升高至350 ℃時,壓力管不產生DHC現象[61]。
在DHC現象能發生的溫度范圍內,DHCR通常是隨著溫度的升高而增大。許多研究者[61~63]在100~300 ℃的范圍內測量了Zr-2.5Nb壓力管軸向的DHCR,結果表明,該溫度范圍內DHCR和溫度呈現出正相關,并符合Arrhenius規律[63]。隨著溫度的升高,斷口的條紋特征也變得更加明顯[13],條紋寬度也增大[56]。根據Kim's模型,DHCR主要由氫擴散速率和氫濃度梯度決定,其中氫擴散速率占主導地位;當溫度增大到300 ℃以上時,氫擴散速率不再是DHCR的決定性因素,DHCR會隨著溫度的升高而降低[61],DHCR和溫度之間不符合Arrhenius規律。Sunil等[64]認為,DHCR的降低和存在DHC裂紋擴展臨界溫度的原因是溫度升高使材料發生蠕變,導致裂紋尖端的應力松弛,使氫化物的斷裂變得困難;也有研究認為[65],在加載的過程中只有鋯合金基體的屈服強度大于氫化物的斷裂應力,氫化物才會發生斷裂,而隨著溫度的升高,基體的屈服強度降幅超過了氫化物斷裂應力的降幅,使氫化物的斷裂變得困難。
Holston和Stjärnsäter[66]采用降載荷法測量了不同溫度下Zr-4包殼管DHC的KIH,研究表明隨著溫度的升高,KIH值緩慢升高,但當溫度超過300 ℃時KIH會急劇增加,Kim等[67]也觀察到了類似的現象。這與上述關于300 ℃以上DHCR降低的現象相符合,即KIH越高,DHC裂紋擴展越困難。但同樣采用降載荷法測量KIH值,Sagat等[68]研究表明,KIH值與溫度的關聯性并不大。Kim等[67]認為,裂紋尖端塑性變形區中產生的變形孿晶與氫化物的相互作用使氫化物斷裂。同時,Kim還分別采用降載荷法和升載荷法獲得了300 ℃以下不同溫度的KIH值,發現使用降載荷法時,裂紋前端的塑性變形區較大,變形孿晶數量多[16]。雖然在300 ℃以下時,變形孿晶數量隨溫度的升高而增加,但在較低溫度時變形孿晶數量并不是氫化物斷裂的限制條件,所以KIH值與溫度關聯性不大;使用升載荷法時,裂紋前端塑性變形區小,變形孿晶數量較少,因此成為氫化物斷裂的限制條件,溫度越高,變形孿晶數量越多,氫化物越容易斷裂,KIH值隨溫度的升高而降低[16]。當溫度在300 ℃以上時,變形孿晶數量隨溫度的升高而減少,導致氫化物不容易發生斷裂,使KIH急劇上升,也導致了DHCR的下降。
4.4 熱循環過程的影響
在重水堆檢修期間,壓力管道不可避免的會經歷升溫或降溫過程。因此,明確熱循環過程對DHC行為的影響有助于改進檢修方案,最大限度的降低DHC裂紋擴展對壓力管的損傷。
升溫、降溫過程的重復會使氫化物反復溶解和析出。當氫化物第一次析出后會使析出周圍的基體發生塑性變形,因而造成氫化物析出的“記憶效應”,再次降溫時氫化物會更易析出,導致DHC發生的臨界溫度上升[69,70]。DHCR受裂紋尖端(高應力區)和低應力區的氫濃度梯度影響,但由于溶解氫含量受溫度變化過程影響較大,材料經歷的熱循環過程會導致其中的氫含量產生差異,進而造成DHCR的不同。實驗結果表明,升溫至實驗溫度時所測的DHCR明顯低于降溫至實驗溫度時所測的DHCR[47]。對于具有相同氫含量的試樣,如果升溫到實驗溫度,則DHCR發生轉折的溫度比降溫至實驗溫度時所測的轉折溫度低[18,71]。Shi等[46]利用D-P模型預測了不同熱循環條件下所得的臨界溫度,結果表明,降溫至實驗溫度條件下計算得到臨界溫度取決于氫含量,而升溫至實驗溫度條件下計算得到的臨界溫度不受氫含量影響[46],該預測結果得到了實驗數據的驗證。
4.5 H含量的影響
研究認為,在一定溫度下,裂紋尖端DHC行為發生的臨界氫含量與TSSD接近,因此TSSD是裂紋尖端發生DHC現象的氫含量閾值[74]。Kim等[75]用升K法和降K法分別測量了280 ℃時不同氫含量試樣的KIH值,結果表明,當實際氫含量高于該溫度下的TSSD,且差值ΔC (ΔC =實際氫含量-TSSD)在25 mg/kg以下時,兩種方式測得的KIH值均隨氫含量的增加而降低;當ΔC超過25 mg/kg時,KIH值保持穩定[75]。Kim等[67]在隨后的研究中還觀察到氫化物尺寸越大,越容易與變形孿晶相互作用導致氫化物斷裂,即ΔC越大,形成的氫化物尺寸越大,DHC越容易發生,這解釋了KIH對氫含量的依賴性。同樣,DHCR也是先隨著氫含量的增加而增大,但是當氫含量增加至35 mg/kg后,DHCR趨于穩定[67]。Kim's模型[36]中DHC裂紋擴展的驅動力是裂紋尖端處與其他位置的溶解氫的濃度差,而裂尖處溶解氫含量為TSSD,因此在一定溫度下,不同位置的溶解氫的差值最大為TSSP減去TSSD,所以當氫濃度差超過TSSP-TSSD的值時,氫含量的變化不會對DHCR和KIH產生影響。然而,也有研究發現當溫度為250 ℃,氫含量在40~60 mg/kg的范圍內,DHCR隨氫含量的升高而增加[76]。
5 總結與展望
針對鋯合金在高溫環境中的延遲氫化物開裂行為已開展了大量的研究,為壓力管等核電關鍵結構的鋯合金部件的安全運行和老化管理提供了大量理論和數據支撐。但是,在研究中仍存在以下不足:(1) 由于鋯合金的延遲氫化物開裂行為受溫度、氫含量、受力和材料微觀結構等因素的影響,其發生機理存在爭議,氫化物的形核、生長和斷裂過程以及影響氫化物斷裂尺寸的因素仍不明確,對于不同因素間的耦合作用的影響有待進一步探索。(2) 氫含量對DHCR的影響趨勢尚存在爭議。(3) 普遍的鋯合金DHC行為測試方法較為單一,且測試過程耗時長,效率較低。(4) 缺乏能實時監測DHC裂紋擴展長度的方法。(5) 缺乏模擬核用鋯合金實際服役工況的實驗設備,尤其是中子輻照的影響,使實驗測試結果可能與材料實際服役結果有較大的出入。
針對上述的不足之處,未來要繼續深入研究不同因素對DHC行為的影響。結合壓力管的實際服役工況,不斷改進實驗方法,開發更接近實際服役狀態的實驗設備,尤其是針對中子輻照樣品的自動化操作設備及熱室。隨著研究的深入和計算機技術的發展,模擬計算 被越來越廣泛的應用到DHC行為的研究中。將模擬計算的結果與實驗結果相結合,會極大的提高實驗效率,有助于進一步探索DHC機理;還可以模擬壓力管實際服役環境,為降低壓力管的失效風險和延長使用壽命提供數據支撐。
免責聲明:本網站所轉載的文字、圖片與視頻資料版權歸原創作者所有,如果涉及侵權,請第一時間聯系本網刪除。
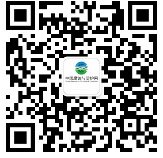
官方微信
《腐蝕與防護網電子期刊》征訂啟事
- 投稿聯系:編輯部
- 電話:010-62316606
- 郵箱:fsfhzy666@163.com
- 腐蝕與防護網官方QQ群:140808414