氫能作為清潔、高效、零碳的能源載體,被視為21世紀最具發展潛力的清潔能源。2022年,國家發改委發布的《氫能產業發展中長期規劃(2021-2035年)》明確指出,氫能將成為未來國家能源體系的重要組成部分,以及實現終端綠色低碳轉型的重要載體[1]。結合中國豐富的可再生能源資源和完善的天然氣基礎設施,利用天然氣摻氫技術,將可再生能源制取的綠氫摻入天然氣管網,可有效提升我國可再生能源利用比例,推進傳統能源的轉型。2023年9月,國家能源局綜合司發布《天然氣利用政策(征求意見稿)》,提出明確和優化天然氣利用順序,并在優先類中提到了在保障安全前提下的終端天然氣摻氫示范項目等天然氣利用新業態[2]。然而,氫氣與天然氣的結合對現役天然氣長輸管道帶來了新的安全技術挑戰。通常情況下,影響天然氣長輸管道壽命的主要因素是濕H2S、CO2等雜質氣體引起的管道內腐蝕[3],氫氣的摻入可能誘發氫脆,并影響天然氣長輸管道的腐蝕機理和破壞類型。為了解決摻氫天然氣管道的氫脆與腐蝕問題,國內外學者開展了一系列研究,提出了如無機涂層[4]、有機涂層[5]及其復合涂層等多種防護技術,為摻氫天然氣管道的安全運行做出了重要貢獻。
在氣體阻隔防護涂層領域,包括金屬及金屬氧化物涂層、聚合物涂層或以上涂層的復合涂層[6,7],其中最常見的為Al2O3[8]、ZrO2[9,10]涂層及其復合涂層,這些涂層具有良好的阻氫性和防腐蝕性,但大多數應用于熱核反應中,與摻氫天然氣管線鋼的實際工況不完全匹配,缺乏實用性。因此,本文通過文獻研究,對摻氫環境下天然氣管線鋼的氫脆及腐蝕防護技術的相關研究成果進行歸納與總結,當前,應用于管線鋼的防護涂層主要以含Ni類涂層為主的無機防護涂層和以含Mo類、氧化石墨烯類、金屬鋅、氧化鈰物質為填料的聚合物復合涂層為主。
1 含Ni類無機涂層
由于H在Ni等金屬中的擴散系數較低,Ni常被電鍍在管線鋼上以阻隔氣體與鋼材表面的接觸。Ni-P涂層具備優良的阻氫和防腐蝕特性,其阻隔能力與涂層結構密切相關。非晶態Ni-P涂層的氫滲透系數(~10-14 m2/s)小于晶態Ni涂層的氫滲透系數。Samanta等[11]采用含有NiSO4、Na2H2PO2和琥珀酸作為絡合劑的化學鍍液,在X70鋼基底上制備了非晶態Ni-P涂層,并利用Devanathan-Stachursky電化學滲透池對涂層的氫滲透性進行了詳細評價。圖1a顯示,非晶態Ni-P涂層有效減緩了氫的滲透,相比晶態Ni涂層顯示出更低的氫滲透電流,證實其作為氫阻隔層的潛力。圖1b顯示,動電位極化曲線揭示了非晶態Ni-P涂層相比晶態Ni涂層和基體鋼在3.5%NaCl溶液中展現出更低的腐蝕電流密度,表明了其更優異的防腐蝕性能。
圖1
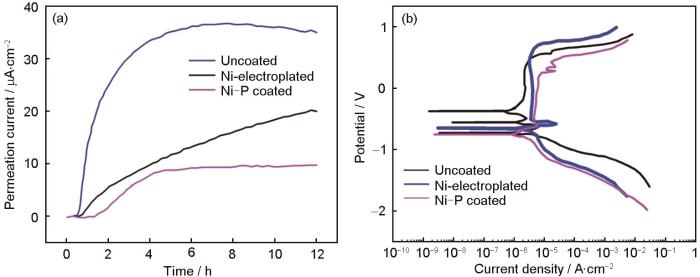
研究表明[12,13],在Ni-P-SiO2復合涂層中,SiO2的存在能夠細化鍍層晶粒,從而提高涂層的各項性能。Zhao等[14]通過預鍍制備了具有核殼結構的SiO2@Ni納米粒子,然后將這些納米粒子引入到Ni-P鍍層中,得到了Ni-P-SiO2@Ni復合鍍層。結果表明,SiO2@Ni納米粒子的存在可以顯著減少納米粒子在涂層中的團聚,提高納米粒子的分散程度,更好地填充鍍層孔隙,從而增強涂層性能。與Ni-P和Ni-P-SiO2納米復合涂層相比,Ni-P-SiO2@Ni復合涂層具有更好的阻氫和防腐蝕性能。其中,未鍍層基底具有較大的穩態氫滲透電流,而電鍍有Ni-P基涂層的基底則顯示出較低的氫滲透電流,特別是Ni-P-SiO2@Ni涂層,當SiO2@Ni納米粒子的含量為3.6 g/L時,Ni-P-SiO2@Ni涂層展現出最佳的氫氣阻隔性能,其有效氫擴散系數(Deff)達到最小值,SiO2@Ni納米粒子的引入可以顯著提高涂層的抗氫滲透能力。隨著Ni-P比例的變化,Ni-P由次共晶向近共晶轉化。圖2顯示了涂層在96 h鹽霧測試后的腐蝕形貌,Ni-P-SiO2@Ni涂層僅有輕微腐蝕,主要發生在晶界處,而Ni-P-SiO2涂層則遭受了更嚴重的腐蝕,不僅晶界受損,晶粒本身也受到了嚴重腐蝕,表明Ni-P-SiO2@Ni涂層在實際應用環境中具有優異的防腐蝕性能。
圖2
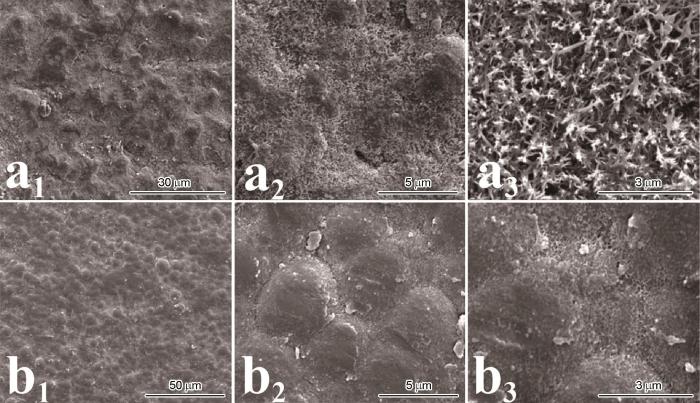
圖3
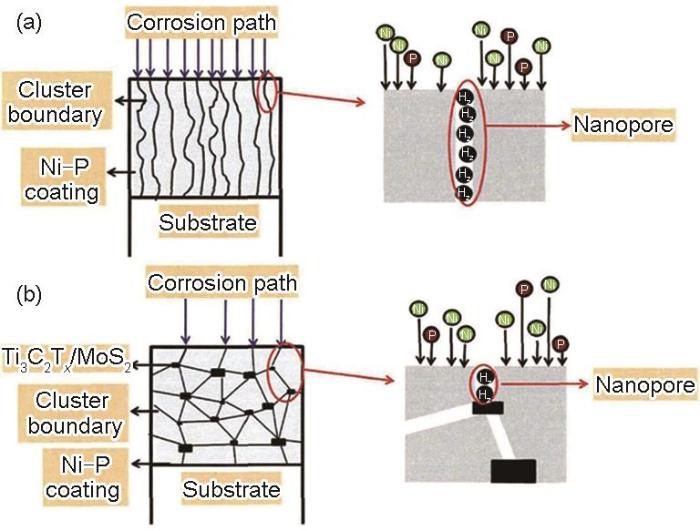
綜上所述,含Ni類無機涂層的研究已經取得顯著成果。與單層涂層相比,納米復合涂層具有更好的阻氫和防腐蝕性能,且其性能與納米容器在涂層中的均勻程度和分散性有關,并且與納米容器和涂層的熱膨脹系數的一致性有很大關系。然而,由于無機物涂層的制備工藝復雜且容易脫落,相關涂層在摻氫天然氣管道中的實用性較低。相比之下,有機涂層種類更多且適用性強,但其自由體積過大,很難阻隔小分子的進入[17]。將納米填料摻入有機涂層中可以降低涂層自由體積,是一種可靠策略。常見的納米填料包括含Mo類、氧化石墨烯類、石墨烯類、Zn等,這些納米填料具有出色的阻隔性[4,18,19]。聚合物基體與納米填料的適當組合對于提升涂層的性能具有重要影響。
2 含Mo類有機復合涂層
在管線鋼阻氫和防腐蝕研究過程中,有研究表明Mo類物質能夠改善涂層的阻氫和防腐蝕性能。Mo的摻入會提高C在奧氏體中的擴散激活能降低彌散系數,抑制先共析鐵素體的形成,Mo的摻入還會生成硫化鉬,降低H2S的活性,促進氧化膜的形成,從而提升管線鋼的性能[20]。Wallaert等[21]深入探究了在富含H2S的環境中,鋼材基體中Mo含量的變動對腐蝕產物的構成及其對氫吸收作用的影響,低Mo材料在670和700 ℃下回火1 h得到低Mo(A)和低Mo(B),高Mo材料在700 ℃情況下回火1 h得到高Mo材料。特別關注3種材料在H2S飽和溶液中形成的腐蝕產物的特性,研究結果如圖4所示,加入適量的Mo能夠改善腐蝕產物膜的致密程度,從而提高材料的阻氫和防腐蝕性能。
圖4
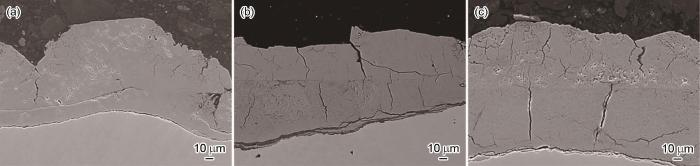
圖5
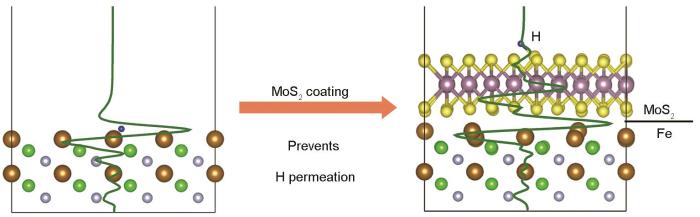
由于環氧樹脂(EP)具有高粘度、附著強度和優異的物理阻隔性,常被用作復合涂層的基體。在Mo類填料中,金屬有機框架材料(MoFs)能夠顯著改善高分子樹脂類涂層的性能。MoFs能夠進入涂層微陷處形成迷宮效應,延遲和切斷腐蝕離子與金屬表面的接觸。參與MoFs的有機配體中的官能團和金屬陽離子中心能夠作為路易斯(Lewis)酸/堿參與環氧基團的開環反應,預聚物和固化劑分子能夠進入多孔結構的MoFs中,為涂層分子固化提供條件。此外,MoFs作為異相核心能夠促進高分子樹脂聚合和凝固,提升涂層的固化反應,增加涂層的交聯密度,從而增強管線鋼的阻氫和防腐蝕能力[24,25]。Wang等[26]將多巴胺(DA)與MoF-5表面相結合,其中多巴胺中的氨基參與環氧樹脂中的開環反應,提升MOF-5與環氧樹脂的相容性,增加涂層的交聯密度。此外,MoF-5可作為氧化石墨烯(GO)、氮化硼(HBN)等的填料進一步改善涂層的孔隙率,提高涂層的性能。隨著MoFs材料的發展,其在有機涂層方面的應用逐漸走向成熟。MoFs在涂層阻氫和防腐蝕領域可與其他材料產生協同作用,提高涂層的被動阻隔性和主動防腐蝕性能。
圖6
從圖7中可以明顯看出容抗弧半徑大小排序為:1% > 0.8% > 0.3% > 0% > 1.5%。在1%的鉬酸鹽水性環氧樹脂涂層中表現出最好的耐腐蝕性,適當的鉬酸鹽對抑制腐蝕的發生具有積極作用。鉬酸鹽能夠使金屬腐蝕電位正移,減緩腐蝕,形成鈍化膜增加涂層性能,但鉬酸鹽的特性在較高離子濃度下才能發揮,然而水性環氧樹脂涂層中鉬酸鹽的溶解能力有限,過高的濃度會破壞涂層連續性,降低涂層性能。因此,存在一個最佳濃度值,使得鉬酸鹽在水性環氧樹脂中表現出最佳性能。導致含Mo類涂層防護機理的研究仍然比較模糊,且難以實現長效防護,由此,以氧化石墨烯類復合涂層研究應運而生。
圖7
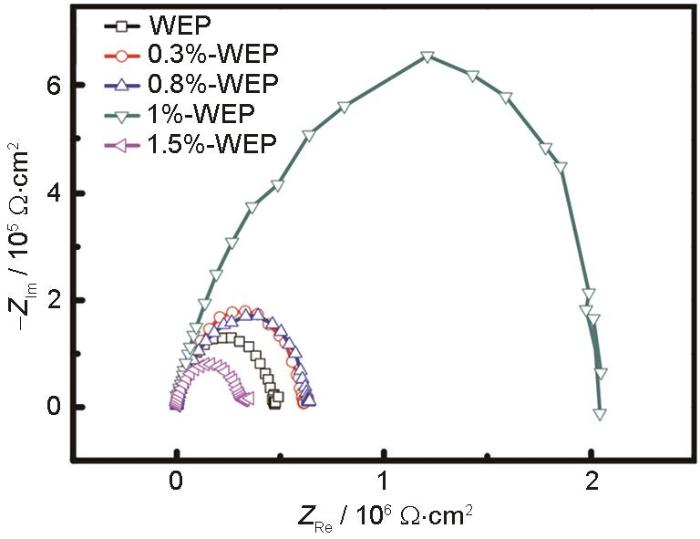
3 氧化石墨烯類聚合物復合涂層
在已知的納米填料中,氧化石墨烯的發展十分迅速。其緊密堆積結構、高表面能和局域電場能夠增強分子間作用力,從而提供較強的阻隔作用。大量研究表明環氧樹脂/氧化石墨烯(EP/GO)復合涂層具有耐腐蝕性、阻隔性和實用性[30,31]。Tran等[32]通過使用EP/GO復合涂層,發現基體的氫滲透系數下降了17.5%。Rajabi等[33]向水性環氧樹脂涂層中摻入0.25% (質量分數)的氧化石墨烯,提高了涂層的耐腐蝕性,腐蝕速率為2.3666 × 10-3 mm/a。盡管氧化石墨烯在阻氫和防腐蝕方面表現出良好的性能,但由于其在樹脂中的均勻度和分散度受到限制,阻隔性和耐腐蝕性未能完全展現,因此,改性GO的研究成為熱點。Yuan等[34]采用兩步高速自旋鍍膜法制備了熱塑性聚氨酯(TPU)和P-苯二胺非共價功能化取向石墨烯(Gr-PPD)雙層EP復合涂層,以協同提高其隔氣性能和耐腐蝕性。由于Gr-PPD良好的分散性和定向,提供了強大的納米屏障壁,減少了氫氣分子或腐蝕性介質與管道表面接觸的可能性,降低了管道失效可能性。
Li等[35]將十八烷胺(ODA)改性的氧化石墨烯(mGO-ODA)與接枝馬來酸酐的聚丙烯(MAPP)復合,制備成復合材料涂層。該涂層通過噴涂方法涂覆在尼龍片和鋼基底上,用于提高氣體阻隔性能和防腐性能。結果顯示,純尼龍薄膜具有較高的H2GTR和O2GTR值,分別為180和40 cm3/(m2·d·Pa)。相比之下,mGO-ODA/MAPP復合涂層顯著降低了這兩種氣體的傳輸率,60%mGO-ODA/MAPP涂層的H2GTR和O2GTR值分別降至10.6和2 cm3/(m2·d·Pa),表明該復合涂層對氫氣和氧氣具有極高的阻隔性能。此外,通過Henis和Tripodi電阻模型計算得到的滲透系數(P1)值進一步證實了60%mGO-ODA/MAPP涂層在阻隔氫氣和氧氣方面的效果,其P1(H2)和P1(O2)值分別為0.259和0.049 cm3/(m2·d·Pa)。這些結果表明,mGO-ODA/MAPP復合材料通過在聚合物基質中形成高縱橫比的二維層狀結構,有效地增加了氣體分子的擴散路徑和曲折度,從而實現了優異的氣體阻隔性能,有效減少了氫氣分子和腐蝕介質與管道表面接觸的機率。Wan等[36]將羧甲基殼聚糖(CMCS)修飾在GO上,顯著改善了GO在水性環氧樹脂中的分散性和均勻性。研究表明,當羧甲基殼聚糖改性氧化石墨烯(CGO)濃度為0~0.25% (質量分數)時,隨著CGO濃度的增加,涂層的阻氫能力隨之上升,當CGO為0.25%時,兩種組分相容性最高,環氧樹脂/CGO涂層在氫滲透測試中展現出最低的氫滲透電流密度、最小的有效氫滲透系數,以及最低的固溶氫和擴散氫含量。隨著CGO濃度繼續增加,涂層的附著強度降低,導致涂層的阻氫能力下降。不同涂層的SEM形貌如圖8所示,CGO的摻入使涂層產生了迷宮效應,提高納米填料的分散度可以有效的增加迷宮效應的效果,從而達到阻氫和防腐蝕的目的,產生的迷宮效應路徑如圖9所示。
圖8
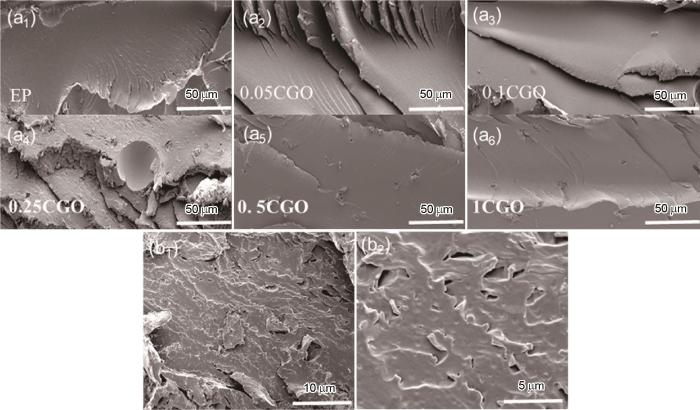
圖9
黃科智[5]制備了一種APTES-GO改性環氧樹脂/PVDF有機涂層,研究表明當APTES-GO在PVDF中的含量在0.1%~1% (質量分數)時,隨著含量的增加,涂層性能不斷提高。然而,當APTES-GO含量超過1%時,由于超出涂料溶解度發生團聚,導致涂層性能開始下降。APTES-GO能夠改善PVDF有機涂層的結晶度和鏈段完整度,從而提高涂層的阻氫和防腐蝕性能。
不透氣的疏水APTES-GO分散在PVDF有機涂層降低了PVDF有機涂層的自由體積,并且改變了腐蝕物質的傳播路徑,延遲和切斷了氫氣分子和腐蝕物質與金屬表面的結合,如圖10所示。
圖10
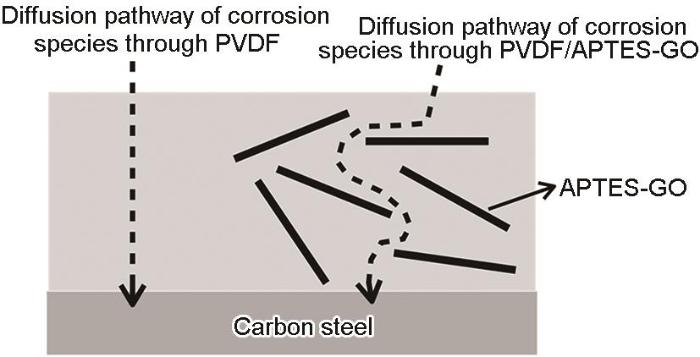
此外,二維材料被證明具有良好的阻氫和防腐蝕性能,氧化物、碳化硅等傳統的材料顯示出更高的氫滲透減少因子[37]。近些年,類石墨烯MXenes材料在各個領域得到廣泛關注[38]。MXenes分子篩和儲氫特性增加了其對H的有效阻隔[39,40]。Shi等[41]采用旋涂法將MXene (Ti3C2T x 納米片)涂層沉積在X70管線鋼上,并對其阻隔性能進行了電化學氫滲透實驗評估,研究表明,MXene (4 mg/mL-1L)涂層的阻氫性能最優,氫滲透電流為9.1 × 10-6 A/cm2,低于X70鋼的27.5 × 10-6 A/cm2。適合濃度的MXene涂層具有優異的阻氫和防腐蝕性能。氧化石墨烯類復合涂層憑借其優異的防腐蝕性和氣體阻隔性,以及良好的機械性能和化學穩定性,已經成為各個領域廣泛關注的對象。隨著科技的不斷進步和應用領域的不斷拓展,氧化石墨烯類復合涂層的發展潛力將會得到進一步挖掘和利用,同時,由于金屬及金屬氧化物作為納米填料,能夠極大的改善涂層在高溫、高壓環境下阻氫和防腐蝕性能,此類涂層也成為學者的研究熱點。
4 其他金屬及金屬氧化物有機復合涂層
氧化鈰和鋅等金屬及金屬氧化物也可作為納米填料。由于這些無機物需要改性以增加與涂層的相容性,其填料的加入能改善有機涂層的耐腐蝕性和阻氫性能。
納米氧化鈰毒性小,作為金屬化緩蝕劑已被廣泛使用[42]。CeO2摻入有機涂層中,不僅發揮物理屏障作用,且Ce3+向Ce4+(CeO2)轉化過程中會形成許多氧空位,對H產生吸附阻隔作用[43]。CeO2在陰極的沉淀反應會形成腐蝕產物膜,增加涂層的耐腐性能[44]。但由于氧化鈰容易團聚,難以協助涂層形成致密保護膜,因此需要改性以制備成與有機涂層基體高相容性和分散性的物質。Yuan等[45]在玻璃薄片(GFs)上采用水熱原位法生成疏水性CeO2,制備一種獨特的復合填料,并將其加入到環氧樹脂(EP)中。EP和填料之間通過共價鍵Ce-O-Si和最佳樣品中的氫鍵形成的強界面力減少了EP中的自由體積,有效地提高了CeO2分散性,增強了阻氫和防腐性能,CeO2薄膜的抑制作用和復合填料的疏水性可以防止進一步的腐蝕。從圖11中不同填料含量涂層的微觀形貌可以看出,30%FAS-CeO2@GFs/EP中出現空腔,50%FAS-CeO2@GFs/EP和60%FAS-CeO2@GFs/EP由于納米填料發生團聚,涂層內部出現裂紋;而40%FAS-CeO2@GFs/EP的結構比較完整,阻隔性能最佳。在3.5% (質量分數) NaCl溶液中浸泡60 d后,|Z|0.01 Hz保持最高值2 × 1010 Ω·cm2,其H2GTR值比純PET薄膜降低約42%,其氫氣滲透系數比純EP涂層降低約65.64%,如圖12所示這是由于高填充量下的GFs的擇優取向和高縱橫比,以及CeO2納米粒子的錨定,這些因素共同產生了“迷宮效應”,為氫氣分子提供了更長、更曲折的擴散路徑,材料表現出優異的阻氫和防腐蝕性特性。
圖11
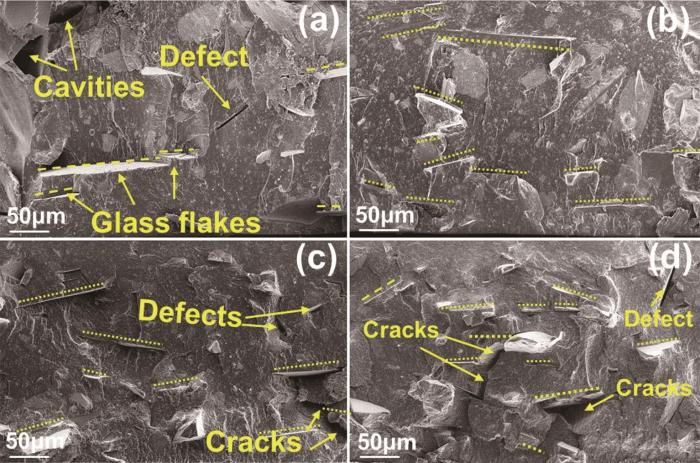
圖12
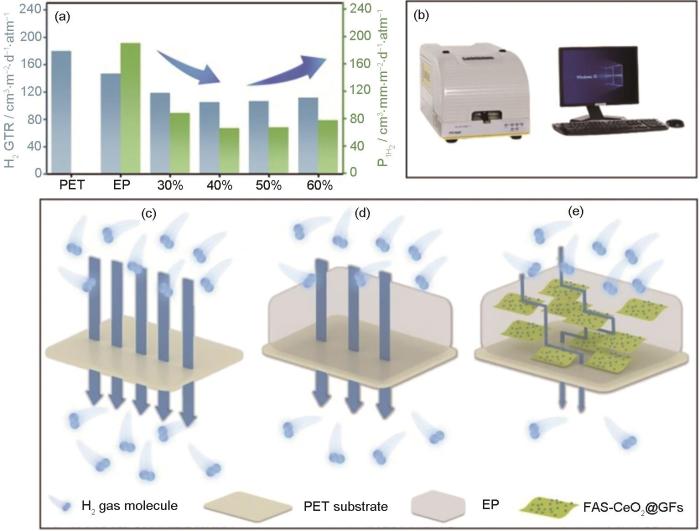
圖12 PET基材、EP涂層PET和復合涂層涂層涂層PET的H2氣體透過率(GTR),不同填料含量的EP和復合涂層的H2滲透系數值,氣體滲透機示意圖PET、EP涂層PET和復合涂層覆蓋PET的H2氣體分子滲透過程和還原機理示意圖[45]
Fig.12 H2 gas transmission rate (GTR) of PET substrate, EP coated PET and composite coatings coated PET, H2 permeability coefficient values of EP and composite coatings with different filler content (a), schematic diagram of gas permeability machine (b), schematic illustrations of H2 gas molecule permeation process and reduction mechanism of PET, EP coated PET and composite coatings covered PET (c-e)[45]
此外,金屬有機復合涂層的研究也在進行。Yang等[46]采用堿性鋅酸鹽電沉積技術成功制備了鋅-環氧粉末(Zn-EP)復合涂層,結果表明,環氧粉末的添加使得涂層結構更加致密。通過電化學氫滲透實驗,探討了涂層對鋼基底氫擴散行為的影響,環氧粉末的添加有效阻礙了氫氣向鋼基底的滲透,這可能有助于減輕鍍鋅鋼的氫脆化問題。隨后,通過電化學方法來評估EP對復合涂層耐腐蝕性能的影響,結果表明,EP的加入顯著提升了涂層的耐腐蝕性,且Zn-6 g/L EP涂層的耐腐蝕性最佳。
總之,無機涂層與有機涂層都能夠顯著提高管線鋼的阻氫和防腐蝕性能,上述研究中,涂層阻氫性能實驗多以電化學氫滲透方法為主,難以模擬在高壓氣相氫對防護涂層的實際影響規律,摻氫天然氣管道中產生氫脆的氫原子來源主要有兩種,一是來源于濕H2S等腐蝕介質在發生腐蝕時析出的氫,二是管道輸送介質中的高壓氣態氫。兩種來源的氫對管線鋼的破壞機制相同,但氫原子進入鋼材內部的機理不同,電化學液相氫滲透的擴散動力來源于自由電子,摻氫天然氣管道中的高壓氣相氫滲透的擴散動力來源于氫原子濃度梯度。有關摻氫天然氣氫脆行為研究中,學者們將充氫方法劃分為液相充氫法和氣相充氫法兩種方式,并且在研究過程中學者們觀察到,氣相充氫法更接近摻氫天然氣運行的實際工況[47~49]。對于管線鋼涂層防腐蝕性能研究中采用的實驗方法多以室內環境下的電化學腐蝕實驗為主,并未模擬出摻氫天然氣管道內由H2S和CO2等雜質為主組成的腐蝕環境,涂層在摻氫天然氣管道環境中的防護效果仍然模糊,需要改進實驗裝置,開展原位測試進行涂層性能測試。因此,在進行摻氫天然氣管道防護涂層阻氫和防腐蝕性能研究時,應綜合考慮管道的高壓氣相氫環境,采用氣相充氫法進行實驗,也要考慮濕H2S和CO2等雜質氣體引起的液相氫滲透,同時還需要考慮雜質引發的析氫腐蝕問題,是氣相液相充氫的協同,同時也是氫脆和腐蝕的耦合,因此,開展氣液相充氫共存并耦合腐蝕的涂層防護性能評價研究將更符合工程實際。
5 總結
目前,隨著全球清潔能源的需求的增加以及“雙碳”目標的提出,摻氫天然氣項目的發展進入關鍵時期,摻氫天然氣管道阻氫和防腐蝕復合技術成為管道安全運行的必要保障,但氣液相充氫共存并耦合腐蝕的研究處于起步階段,未來將成為研究熱點。通過上述研究可知:
(1) 腐蝕介質通過接觸管道表面擴散入管道內部破壞管道結構。涂層作為一種有效的防護技術機制主要分為兩種,首先是作為物理屏障,通過迷宮效應延遲和切斷腐蝕分子與金屬表面的接觸;其次,通過與氫原子競爭或捕獲氫原子,減少氫原子在金屬表面的吸附和解離,從而達到阻氫和防腐蝕效果。
(2) 無機涂層、有機涂層及其復合涂層都具有更優異的阻氫和防腐蝕性能,相比之下有機復合涂層的種類更加豐富,性能更加優異。它們由納米填料和涂層基體組成,納米填料通過減小有機涂層的自由體積提高涂層的阻氫和防腐蝕能力。選擇納米填料時需考慮其與有機涂層的相容性,通常通過改性增加其在有機涂層中的分散性和均勻性,從而增強涂層性能。隨著納米填料含量增加,涂層性能也隨之提升至最佳值,繼續增加則因填料團聚而使涂層性能降低。
(3) 目前的涂層防護技術研究未考慮摻氫天然氣管道實際運行過程中高壓氣相氫對涂層的作用效果,與工程偏差較大,需要進一步開展針對摻氫天然氣管道涂層防護性能的氣液相充氫共存并耦合腐蝕的研究,為摻氫天然氣管道的安全運輸提供參考。
免責聲明:本網站所轉載的文字、圖片與視頻資料版權歸原創作者所有,如果涉及侵權,請第一時間聯系本網刪除。
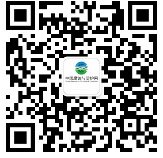
官方微信
《腐蝕與防護網電子期刊》征訂啟事
- 投稿聯系:編輯部
- 電話:010-62316606
- 郵箱:fsfhzy666@163.com
- 腐蝕與防護網官方QQ群:140808414