內徑/mm | 壁厚/mm | 材質 | 入口溫度/℃ | 出口壓力/MPa | 輸量/(kg·s-1) | 上下坡段傾角/(°) | CO2摩爾分數/% | 氣油比/(m3·t-1) | 含水率/% |
---|---|---|---|---|---|---|---|---|---|
300 | 16 | L360N | 52 | 14 | 30 | 45 | 3 | 8 523 | 3.5 |
內腐蝕是導致油氣田集輸管道失效的重要原因,具有隱蔽性、突發性等特點。隨著國內非常規油氣田開發的不斷深入,采出介質的組成和運行工況更為復雜苛刻,集輸管道面臨的內腐蝕問題也更為突出。其中高壓氣田集氣管道運行壓力高,一旦發生腐蝕失效,就會造成極為嚴重的后果。
CO2是集輸管道內腐蝕的主要影響因素,其腐蝕作用機理復雜,國內外研究人員對此進行了大量研究[1-3]。鐘功祥等[4]采用失重法研究了溫度和CO2分壓對X52管線鋼腐蝕速率的影響,結果表明管道沿線的溫度、壓力、持液率、流型及pH對CO2腐蝕的影響都很大。張喜慶等[5]對CO2和Cl-共同作用下的腐蝕規律進行了研究,結果表明流速、CO2分壓等的升高會增加L245M管線鋼的腐蝕速率。謝飛等[6]總結了現行CO2腐蝕研究的缺陷和不足,認為目前的腐蝕速率預測模型只考慮了電化學腐蝕因素,沒有考慮管道內介質流動的影響,應建立更符合管道實際工況的預測模型。SADEGHI等[7]研究了溫度和NaCl濃度對X65管線鋼在CO2腐蝕介質中應力腐蝕開裂(SCC)的影響,發現腐蝕敏感性隨溫度升高和NaCl濃度降低而增加。ELGADDAFI等[8]研究了介質流動對高強度API碳鋼CO2腐蝕的影響,發現無論溫度高低,介質流速都會影響API鋼的CO2腐蝕速率。目前,現有CO2腐蝕規律的研究主要側重于常規運行工況或單一變量的影響,對于處在介質溫度最高達90 ℃、運行壓力超過15 MPa、輸量最高達50 kg/s的高溫、高壓、大輸量苛刻服役工況的管道沿線CO2腐蝕速率變化規律研究較少。此外,腐蝕試驗無法體現長距離輸送條件下的多相流變化特點及其對腐蝕速率的影響,而多相流仿真軟件結合CO2腐蝕計算模型可以彌補上述問題。因此,筆者采用模擬計算的方式,以某高壓氣田集氣管道為例,研究了溫度70~90 ℃、壓力15~18 MPa、輸量35~50 kg/s的苛刻工況及15°~60°傾角變化對管道CO2腐蝕速率分布的影響規律,以期明確主要影響因素,為該高壓氣田集氣管道腐蝕控制提供指導。
1. 試驗
1.1 仿真模擬方法
已有文獻研究表明[9-10]碳鋼的CO2腐蝕受到多種因素影響,包括物理因素、環境因素和管道材料參數以及腐蝕產物膜等。
為提高腐蝕預測的準確度,將多相流瞬態模擬和De Waard95 CO2腐蝕模型相結合,進行苛刻服役工況下CO2腐蝕規律模擬研究,這克服了傳統CO2腐蝕模擬對管內流型流態考慮不足的問題。De Waard95 CO2腐蝕模型是應用廣泛的典型半經驗模型[11],其包含了與流速相關的物質過程及與流速無關的腐蝕反應動力學過程,考慮了影響腐蝕的多個因素。多相流瞬態模擬采用OLGA多相流瞬態仿真模型,它能模擬管道中流體與時間相關的瞬態流動過程,精確預測生產系統中的諸多關鍵參數[12-13]。
1.2 模擬試驗條件
以國內某條集氣管道的正常運行工況數據建立對照模型,其正常運行工況如表1所示。此外,受地層波動影響,該集氣管道面臨異常高溫、高壓和大輸量,采出介質最高運行溫度為90 ℃,最高運行壓力為18 MPa,最高輸量為50 kg/s。此外,管道沿山脈鋪設,高程變化較大,爬坡角度最高達60 ℃。為避免與CO2腐蝕有關的多因素混雜對本研究產生影響,將集氣管道模型進行簡化,如圖1所示。管道模型水平段長3 200 m,上下坡段均長1 000 m,相對高差70 m。

2. 結果與討論
2.1 溫度的影響
以對照模型為基礎,僅改變管道入口溫度為70、80、85、90 ℃,研究溫度對集氣管道CO2腐蝕速率的影響。不同入口溫度條件下管道沿線腐蝕速率分布如圖2所示,最大腐蝕速率如表2所示。

入口溫度/℃ | 52 | 70 | 80 | 85 | 90 |
最大腐蝕速率/(mm·a-1) | 4.88 | 5.77 | 6.23 | 6.45 | 6.67 |
由模擬結果可以發現,管道沿線腐蝕速率分布與高程變化直接相關,腐蝕速率的變化拐點與高程變化拐點重合。下坡管段腐蝕速率最高,水平管段次之,上坡管段腐蝕速率最小。各溫度下,最大腐蝕速率均出現在下坡段的坡腳位置,最小腐蝕速率均位于上坡段。下坡管段和水平管段的腐蝕速率隨入口溫度變化均較為明顯,即隨溫度的升高而增大。上坡管段腐蝕速率則隨入口溫度的升高有所降低。
上述規律表明,管道沿線腐蝕速率分布主要受高程引起的腐蝕介質傳質速率變化控制。上坡段流速降低、傳質速率降低,腐蝕速率降低;下坡段流速增加,傳質速率增加,腐蝕速率升高。而溫度的升高會影響多相流介質的氣液比、黏度等,上坡段主要受氣液比升高、液相減少的影響,流速降低,導致腐蝕速率降低;下坡段和水平段主要受液相黏度隨溫度升高而降低的影響,流速增加,腐蝕性離子傳質速率增加,且壁面剪切力上升,影響腐蝕產物膜的穩定性,腐蝕速率升高[14-15]。
2.2 運行壓力的影響
以對照模型為基礎,僅改變出口壓力,分別研究15、16、17、18 MPa高壓輸送工況下集氣管道CO2腐蝕速率變化規律。不同出口壓力下的腐蝕速率分布和最大腐蝕速率分別如圖3和表3所示。

出口壓力/MPa | 14 | 15 | 16 | 17 | 18 |
最大腐蝕速率/(mm·a-1) | 4.88 | 5.04 | 5.18 | 5.28 | 5.37 |
由圖3可見,單一工況下,管道沿線的腐蝕速率仍與高程變化直接相關,最大腐蝕速率均位于管線下坡段的坡腳位置。對比不同出口壓力下的模擬結果可知,管道腐蝕速率隨著出口壓力的升高而上升,且最大腐蝕速率隨出口壓力的變化尤為明顯。
隨著壓力的增加,CO2氣體分壓增加,CO2在液相中的溶解量增大,陰極去極化過程加快,因此壓力增加腐蝕速率增大[16]。下坡段腐蝕速率顯著增大主要還是因為管內液相介質流速在重力作用下迅速增大,腐蝕離子傳質速率快速提高,且使壁面剪切力銳增,腐蝕產物保護膜的穩定性顯著降低。
2.3 輸量的影響
以對照模型為基礎,僅改變入口流量為35、40、45、50 kg/s,研究輸量對集氣管道CO2腐蝕速率的影響。不同輸量下管道的腐蝕速率分布和最大腐蝕速率分別如圖4和表4所示。

進口流量/(kg·s-1) | 30 | 35 | 40 | 45 | 50 |
腐蝕速率/(mm·a-1) | 4.88 | 4.96 | 5.02 | 5.06 | 5.08 |
由圖4可見,管道沿線腐蝕速率的分布規律不受管道輸量變化影響,僅隨管線高程變化,最大腐蝕速率仍位于下坡段的坡腳位置,且相對其他位置,該處的腐蝕速率增幅較小。橫向對比各工況發現,隨著輸量的增大,管道腐蝕速率明顯增大。這是因為隨著輸量增大,介質流速增大,腐蝕性離子傳質速率增加,壁面剪切力提高,H+等去極化劑能更快地擴散到電極表面,增強陰極去極化作用,腐蝕產生的Fe2+能夠迅速離開金屬表面,阻止金屬表面保護膜的形成,并對已形成的保護膜起到破壞作用,形成活化鈍化微電池,使腐蝕速率升高[17]。此外,在出口壓力不變的情況下,隨著輸量增大,管線壓力會升高,CO2氣體分壓也會相應增加,導致CO2在液相中的溶解量增大。下坡段坡腳處的腐蝕速率增幅相對較小是因為該位置液相流速和壓力的增幅均較小。
2.4 管道傾角的影響
以對照模型為基礎,僅改變上下坡管道傾角為15°、30°、45°和60°,研究上下坡管道傾角對集氣管道CO2腐蝕速率的影響。不同傾角下的腐蝕速率分布和最大腐蝕速率分別如圖5和表5所示。

上下坡傾角/(°) | 15 | 30 | 45 | 60 |
腐蝕速率/(mm·a-1) | 3.88 | 4.56 | 4.88 | 5.09 |
由圖5可見,水平段的腐蝕速率基本不受管道傾角的影響。當傾角為15°、30°、45°時,上坡段腐蝕速率較水平段低,但當傾角為60°時,上坡段腐蝕速率較水平段高。上坡段腐蝕速率隨著傾角的增大而增大;下坡段腐蝕速率顯著高于水平段,亦隨著管道傾角的增大而增大,最大腐蝕速率仍位于下坡段坡腳處。
管道傾斜會導致上坡段管道內液相爬升困難,流速降低,因此腐蝕速率較水平段低,但當傾角增大到一定程度后(60°),管內液體持續集聚,持液率上升,出現段塞流現象,增大流速和壁面剪切力,腐蝕速率會高于水平段。對于下坡段,傾角增大使管內介質流速增大,腐蝕性離子擴散速率增大,且壓力逐漸上升導致CO2分壓增大,促使其更多溶解于液相水中,增大了管道的腐蝕速率。
2.5 討論
為了分析苛刻服役工況下管線最大腐蝕速率對介質溫度、運行壓力、輸量和管道傾角變化的敏感性,以表1所示工況為基礎模擬條件,將各影響因素的變化程度和對應最大腐蝕速率的變化程度按照百分數進行計算,曲線斜率可以直觀顯示最大腐蝕速率對各因素變化的敏感性。
由圖6可見:在給定的苛刻服役工況下,管道的最大腐蝕速率對介質溫度變化最為敏感,其次為運行壓力,對輸量的變化則相對最不敏感。這主要是因為介質溫度的變化對管道腐蝕具有綜合性作用,雖然溫度升高會降低CO2在水中的溶解度,但同時會使CO2的擴散過程和電極反應速率加快,且溫度升高還會降低液相黏度和流動阻力,提高液相流速,促進陽極和陰極反應的去極化作用;溫度升高還會增加溶液的電導率,使腐蝕電流增大。運行壓力則直接決定了介質中CO2分壓的大小,顯著影響CO2在液相中的溶解度和溶液pH,這些是影響CO2腐蝕的重要因素。此外,由于所選取的基礎工況輸量較大,輸量繼續增大則主要使運行壓力升高、介質被壓縮,而對流速提高有限,即傳質速率變化不大,因此,最大腐蝕速率對輸量變化相對不敏感。而管道傾角是影響腐蝕的外部因素,其對最大腐蝕速率的影響亦有限。

3. 結論
(1)隨著介質溫度從52 ℃提高到90 ℃,管道的腐蝕速率在上坡段降低,在水平段和下坡段明顯提高,特別是下坡段增幅最大,約為37%;隨著運行壓力從14 MPa提高到18 MPa,管道的腐蝕速率稍有增加,但下坡段的增幅較明顯,約為10%;隨著輸量從30 kg/s提高到50 kg/s,管道的腐蝕速率在水平段和上坡段大幅提高,最大增幅約為93%,而在下坡段的最大增幅僅4%;隨著管道傾角從15°增加到60°,管道的腐蝕速率在水平段未見明顯變化,而上下坡段明顯增大,尤其下坡段增幅最大,約為31%。
(2)在苛刻服役工況下,管道沿線腐蝕速率分布主要受高程引起的腐蝕介質傳質速率變化控制,其變化拐點與高程變化拐點重合,下坡段腐蝕速率最高,最大腐蝕速率位于下坡段的坡腳處,溫度、壓力、輸量及管道傾角變化不影響腐蝕速率分布走向。
(3)在給定的苛刻服役工況下,管線最大腐蝕速率對介質溫度變化最為敏感,其次為運行壓力,對輸量和管道傾角的變化最不敏感,腐蝕控制應重點關注介質溫度、運行壓力和下坡段等。
免責聲明:本網站所轉載的文字、圖片與視頻資料版權歸原創作者所有,如果涉及侵權,請第一時間聯系本網刪除。
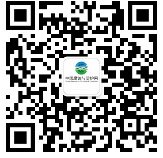
官方微信
《腐蝕與防護網電子期刊》征訂啟事
- 投稿聯系:編輯部
- 電話:010-62316606
- 郵箱:fsfhzy666@163.com
- 腐蝕與防護網官方QQ群:140808414