熱固性樹脂因其固化后不溶不融、硬度高、比剛性大、耐高溫且成品具有優異的尺寸穩定性,在防護涂料、軌道交通、航空航天等廣大應用領域獲得了認可。然而,隨著材料技術的高速發展,傳統熱固性樹脂的力學性能已難以滿足各行各業選用材料的性能要求。針對此類問題,目前的解決方案主要圍繞新型熱固性樹脂的研發和對傳統熱固性樹脂進行改性兩方面。改性后的熱固性樹脂綜合性能得到了顯著提升,且制備周期較短,在抗燒蝕、耐磨損和耐腐蝕等領域起著至關重要的作用。本文綜述了近年來熱固性樹脂基復合材料在抗燒蝕、耐磨損和耐腐蝕等表面防護領域的研究現狀,并對其材料種類、防護機理及環境對其性能的影響進行了梳理和總結,探討了熱固性樹脂基復合材料未來的發展方向,可為其在接下來的研究中提供理論和技術參考。 引 言 熱固性樹脂材料因固化后能夠形成穩定的、不可逆的高度交聯網狀結構而具有優異的尺寸穩定性,良好的耐腐蝕、耐高溫、耐磨性和優異的力學性能,被廣泛應用于涂料、膠粘劑、航空航天及汽車工業等領域 。目前應用范圍較廣的有環氧樹脂、酚醛樹脂、不飽和聚酯樹脂、有機硅樹脂等,其結構、制備方法、應用領域、力學和物理性能如表1所示,其中環氧樹脂因其原料和制備工藝不同,有五種常見結構。 然而,熱固性樹脂固化后較差的力學性能是拓寬其應用面必須解決的短板問題。此外,對不同類型的熱固性樹脂來說,其阻燃性、抗沖擊能力和固化收縮率等多方面特性各不相同,常見熱固性樹脂的性能見表1。如今,建筑、電子、航天等各個行業對材料性能有著越來越高的要求和標準,傳統的熱固性樹脂的性能很難直接滿足行業要求。對于上述問題,目前的解決方法可概括為以下兩種:一是在傳統熱固性樹脂的基礎上添加其他增強相,從而實現對熱固性樹脂的改性;二是研發新的熱固性樹脂。目前,針對熱固性樹脂的改性已有了大量較為成熟的研究成果,改性后的熱固性樹脂可統稱為熱固性樹脂基復合材料,其已成為抗燒蝕、耐磨損和耐腐蝕等功能防護材料首選材料之一。 本文針對熱固性樹脂樹脂基復合材料,分別以抗燒蝕、耐磨損和耐腐蝕三種功能防護材料為對象,綜述其防護性能和防護機理,對比了各增強填料對復合材料的影響,并指出了其在研究過程中的優缺點和未來發展方向。 抗燒蝕增強方法及機理 熱防護系統(TPS)是一種位于超音速飛行器機身外部的結構,它能使機身結構在高速飛行過程中免受氣動熱損傷,是航空航天設備突破“熱障”實現超音速飛行的必要條件。如今,抗燒蝕材料已成為航天器熱防護系統的核心材料,通常作為航天器發動機的內部熱絕緣層、火箭發動機的阻燃防護層使用。熱固性樹脂作為碳化型燒蝕材料,已成為應用極廣的抗燒蝕材料之一,其主要依賴于樹脂高分子材料在燒蝕過程中發生的碳化反應吸收部分熱量,同時利用其分解產生的氣體實現隔熱作用。因此,對樹脂材料而言,其抗燒蝕性能與碳化反應密切相關,典型熱固性樹脂的玻璃化轉變 溫度和開始降解溫度如表2所示。然而,由于高分子材料本身性能的限制,其燒蝕過程是不可逆的,其耐高溫性能和長期抗燒蝕能力已難以滿足飛行器結構部件和機身外部日益惡化的熱環境,因此提高樹脂基復合材料的燒蝕耐熱性能是十分必要的。 由于陶瓷材料優異的高溫穩定性,利用陶瓷粉體增強樹脂基體已成為提高復合材料抗燒蝕性能的常用手段,在高溫條件下,陶瓷填料會轉化為致密的陶瓷隔熱層,降低復合材料的燒蝕率。其中碳化鋯(ZrC)是目前常用的陶瓷填料之一。Wang等指出增加ZrC含量能夠有效提高碳/酚醛(C/Ph)樹脂復合材料的耐燒蝕性能,如圖1所示,隨著ZrC質量分數的增加,復合材料表面耐溫性得到了顯著提高,且燒蝕后背面溫度逐漸降低。這是由于ZrC具有較高的熔點,其在燒蝕過程中氧化形成的氧化鋯(ZrO2)能夠充當隔熱層并阻止熱量進一步傳遞到樣品中,且隨著ZrC含量的增加,該層變厚,為樣品提供了更多保護。 碳化硅(SiC)和硼化鋯(ZrB2) 也具有類似的性質,Liu等利用雙酚環氧樹脂(BER)改性硅橡膠,并額外引入了二氧化硅(SiO2)和碳纖維作為增強填料,相較純基體材料,改性后的復合材料線燒蝕率降低了54.7%。在燒蝕過程中復合材料發生了陶瓷化反應,生成了陶瓷質SiC,且BER的加入使熱解過程中石墨結構更加有序,進而提高了陶瓷層的強度。Zhang等 指出加入 ZrB2-SiC復合填料能夠使復合材料長時間處于燒蝕環境下而不損壞,同時詳細分析了復合材料的燒蝕狀態和燒蝕機理,如圖2所示。對于Tmax=2480℃燒蝕100s的復合材料,由于氧化鋯(ZrO2)相的粗化和玻璃態氧化硅(SiO2) 相的轉變,試樣表面形成了致密的ZrO2+SiO2層,中間則因SiO2的不完全融化形成了多孔ZrO2+SiO2層,最下方則由于SiC的活性氧化只留下了ZrO2層;當燒蝕時間持續到200s(Tmax=2465℃)時,表面SiO2揮發剝落,形成多孔ZrO2層,中間則由于玻璃態SiO2增加了ZrO2顆粒層的粘度而形成了致密的SiO2+ZrO2層,最下方為多孔ZrO2層;最后隨著燒蝕時間延長至500s(2440℃),ZrO2顆粒在表面堆積燒結形成致密的ZrO2層,中間層由于玻璃態 SiO2擴散受到限制而形成了致密的SiO2+ZrO2層,最下方為多孔ZrO2層。這說明復合材料的燒蝕行為受微觀結構、組分分布、燒蝕溫度、燒蝕時間和形成的氧化層等多種因素的影響。 除了使用高溫陶瓷之外,碳納米管和炭黑等碳基納米粒子也被證明是增強復合材料力學和燒蝕性能的有價值的候選材料,即使只添加很少量的碳納米管,對復合材料的抗燒蝕性能的提升也十分顯著。一方面,碳納米管能夠提高復合后材料的熱導率。Park等對比了酚醛樹脂(PR)、隨機切碎的碳纖維增強酚醛復合材料(RCFPC)、編織碳纖維氈增強酚醛復合材料(MCFPC)和編織碳纖維氈/CNT增強酚醛復合材料(MCF/CNTPC)四種材料在1300℃下的燒蝕性能,碳納米管的加入使復合材料的燒蝕性能提高了25%,相較純酚醛樹脂,其燒蝕率下降了78.6%。對比四種材料的熱導率發現,碳納米管的引入使復合材料的熱導率顯著提高,如圖3所示。Ahmad等采用氧乙炔火焰測試進行燒蝕試驗,結果表明復合材料的線燒蝕速率隨碳納米管含量的增加而降低,當樣品中碳納米管含量為0.4%時,燒蝕效果最好,且與不含多壁碳納米管的原始復合材料相比,含有多壁碳納米管的復合材料具有更好的導熱性。另一方面,碳納米管能夠促進復合材料的石墨化過程,在燒蝕過程中形成具有優異性能的石墨結構,相較純酚醛樹脂,加入碳納米管能夠使復合材料抗燒蝕性提高30%以上,在燒蝕過程中,碳納米管充當了成核劑的作用,作為碳化酚醛樹脂石墨化的晶體生長核,其周圍形成緊密的石墨結構進而提高了復合材料的耐高溫燒蝕性能 。Natali等也得到了類似的結果。碳纖維/樹脂基復合材料的燒蝕機理如圖4所示,復合材料在燒蝕過程中可劃分為碳化層和熱解層。在氧?乙炔燒蝕的過程中,樹脂最先發生降解,吸收一定熱量并依附在纖維骨架上形成石墨結構,且在此過程中,樹脂降解產生的氣體向外逸出,在到達材料表面后形成氣膜并作為反應屏障,阻止熱量傳輸。 近年來,其他新型抗燒蝕復合材料也越來越多。郭慧等利用長度分別為6mm和3mm的纖維增強酚醛氣凝膠,并對比了二者的抗燒蝕性能,研究發現以6mm 纖維為增強相的復合材料具有更低的室溫熱導率和更強的抗燒蝕能力。張鵬飛等利用陶瓷先驅體對纖維進行抗氧化防護,并在纖維骨架中填充酚醛樹脂,制得了一種抗氧化三維纖維增強酚醛氣凝膠材料,該材料在燒蝕過程中,熔融的先驅體陶瓷氧化物包覆在纖維表面,并填封纖維間隙,使復合材料能夠在高溫環境下長期存在。Cheng等制備的碳纖維氈?酚醛燒蝕材料(NCF-PR) 在電弧燒蝕過程中線燒蝕率低至0.029mm/s,在樣品表面溫度超過2000℃的情況下,樣件內18mm處溫度僅為150℃,其原因在于燒蝕過程中樹脂降解吸收熱量,且復合材料內部纖維能夠很好地維持網狀結構,防止降解后殘余的碳被高速氣流吹走,進而防止復合材料被進一步燒蝕。碳纖維/環氧樹脂復合材料在接枝有機硅后其抗燒蝕性得到了顯著提升,且有機硅含量越高其效果越明顯 。燒蝕后燒蝕中心形成了多孔碳層,其主要由二氧化硅和碳組成,這是由于在燒蝕過程中有機硅會熱解為類SiO2物質,并在表面形成保護層,且高溫下樹脂降解形成的熔融碎片會在熱解氣體的推動下不斷向表面遷移,最終在表面聚結后形成致密的多孔炭層。 綜上所述,抗燒蝕型復合材料的防護機理可歸結為兩點: (1)燒蝕過程中樹脂基體降解產生的氣體向外溢出,在材料表面形成氣膜以阻止外部熱量向內傳遞,且降解產物依附在內部增強纖維上形成高強度碳層,進一步保護復合材料; (2)類陶瓷或陶瓷填料在燒蝕過程中被嚴重氧化形成隔熱陶瓷層,對復合材料起到良好的保護作用,如圖4所示。但是,部分材料在受到高溫或受到高溫后冷卻的過程中,其體積會發生變化,對復合材料造成進一步的損傷,因此在制備復合材料時應考慮避免此類現象 。此外,對納米級別的填料來說,如納米陶瓷顆粒與碳納米管,其在高濃度下會出現聚集現象 。因此必須優化這類填料在復合材料中的含量,并且必須均勻分散,以便其與基體材料建立強相互作用,否則,隨著添加量的增加,復合材料的性能將會惡化。對于有絕緣性、導電性等特殊服役要求的復合材料,大部分增強填料無法得到應用,因此開發新型抗燒蝕材料也是一種前景可觀的研究方向。 耐磨損增強方法及機理 樹脂基摩擦材料優異的耐磨性、低廉的成本且制備簡單等優點使其得到越來越廣泛的應用。然而,如今人們對飛機、汽車安全性能的要求不斷提高,現有的傳動、制動等摩擦材料勢必要不斷進行革新,且復合材料在摩擦過程中受到多種因素影響,發生的變化也非常復雜,因此開展樹脂基復合材料的耐磨性研究是十分必要的。 目前,樹脂基摩擦材料已被大量用作汽車、飛機、賽車及其他車輛的剎車片的組成材料。高質量的摩擦復合材料必須具備優異的性能,如高熱穩定性、低磨損率、低噪音、穩定且足夠的摩擦系數、可靠的抗衰退性以及生態友好性。然而,對純樹脂基摩擦材料而言,其在摩損過程中產生的摩擦熱的作用下會發生嚴重的衰退現象,且在載荷的作用下磨屑不斷剝落并在摩擦面留下大量凹坑和犁溝,導致摩擦材料表面的粗糙度和磨損率急劇升高。因此,向樹脂基摩擦材料中引入增強填料以增強其承載能力和抗衰退能力是當下的主要研究方向。摩擦復合材料通常由熱固性樹脂基體和摩擦改性填料組成,其中樹脂材料主要起粘合劑的作用,并通過纖維或顆粒增強復合材料的力學性能和摩擦性能。 纖維在摩擦復合材料界面制動過程中發揮著重要作用,并能夠有效改善樹脂基體耐熱性差等缺點 。王亞楠等向硼酸酯改性后的酚醛樹脂中引入玻璃纖維增強填料,較純樹脂而言,復合材料的摩擦系數降低了22%。王春紅等將竹纖維(BF)引入環氧樹脂(EP)中,制得了BF/EP 復合材料。相同測試環境下,復合材料的體積磨損量較純環氧樹脂而言最多可降低65%。其原因在于,當包覆在纖維表層的基體磨損脫落后,質地較硬的BF能很好地承受和傳遞接觸面的大部分載荷,且纖維不易被拔出和拉斷,有效提高了復合材料的耐磨性。此外,向樹脂基體引入碳纖維能夠有效提高復合材料的物理性能和耐磨性,且隨著碳纖維含量的增加,其對復合材料的增強效果越來越顯著。Ahmadijokani等指出,碳纖維加入樹脂材料中后,復合材料的儲能模量增加,因而復合材料的剛度有所提高。在磨損實驗中,碳纖維的多層微結構及其固有的潤滑作用有助于在磨損表面形成牢固且粘附的潤滑膜,從而有效降低磨損率。然而,加入碳纖維加劇了復合材料的熱衰退行為,且隨著滑動速度和載荷的提高,摩擦熱升高,衰退行為更加強烈。Rahmani 等對比了芳綸纖維(KFR)、玻璃纖維(GFR)和碳纖維(CFR)三種增強材料對復合材料耐磨性的影響,如圖5所示。從圖5可以明顯看出碳纖維/樹脂復合材料的耐磨性最好,玻璃纖維/樹脂復合材料次之,對比它們的顯微硬度可知,復合材料的硬度越高,磨損率越低。這是由于耐磨性是硬度和韌性這兩種力學性能的函數,即實驗時塑性變形越小的材料耐磨性越好。 除纖維填料外,陶瓷顆粒因其優異的力學性能和較低的溫度敏感性而被廣泛用于樹脂基摩擦材料,其在磨損過程中能夠在摩擦界面形成摩擦膜,極大地提高復合材料的耐磨性。Vlastimil等 研究了不同SiC顆粒尺寸條件下摩擦膜的形成,結果表明,摩擦膜的穩定性隨著顆粒尺寸的增加而增加。Sun等在探究樹脂基摩擦材料的摩擦膜力學性能與摩擦性能的關系時發現,摩擦材料表面粗糙度越高,其在低溫下磨損率越低。這是由于摩擦過程中產生的磨屑更容易在粗糙顆粒周圍聚集,加速摩擦膜的形成;然而,因摩擦面磨屑的主要成分是樹脂基體碎屑,隨著溫度升高,摩擦材料的熱衰退更加顯著。由此可得,摩擦材料顆粒表面越粗糙,越有利于摩擦膜的形成,但會降低摩擦材料的抗衰退性。其他顆粒填料對樹脂基摩擦材料的防護機理與陶瓷顆粒類似,如銅顆粒同樣能以在摩擦面形成摩擦膜的形式降低摩擦材料的磨損率,但隨著磨損的不斷進行,銅顆粒會從摩擦材料表面脫落,導致其耐磨性有所下降 。 考慮到摩擦材料復雜的服役工況,學者對其摩擦過程中的磨損機理展開了研究,如表3所示。不同摩擦環境下復合材料的磨損機理不同。玻璃纖維/樹脂復合材料在干滑動(Dry)、油潤滑滑動(Oil)和惰性氣體滑動(Argon)三種不同滑動環境下的磨損率如圖6所示 。由圖6可知,摩擦材料在惰性氣體環境中的磨損率最大,這是由于氣體會將玻璃纖維碎片分離并帶離摩擦區域,使其無法在復合材料表面形成保護膜,加速材料的磨損。反之,油潤滑劑則能夠吸附摩擦時剝落的玻璃纖維碎片并在材料表面形成保護膜從而降低材料的磨損率。此外,隨著摩擦速率的增加,油潤滑環境下摩擦材料的磨損率反而有所降低,其原因是摩擦面溫度的升高產生熱擴散,軟化樹脂基體使玻璃纖維更容易破裂,加速表面保護膜的形成,摩擦系數減小。 不同溫度下,復合材料的磨損機理同樣不同。以熱解碳改性碳纖維立體織物增強聚酰亞胺復合材料(PI-C/CF)為例,三種溫度下該復合材料的磨損過程如圖7所示。室溫下,復合材料在磨損過程中增強相和基體產生磨屑并不斷剝落,形成潤滑膜,并在磨損過程中不斷擴大。因此,室溫下的磨損機理主要包括連鎖效應、黏著和磨粒磨損;在380℃時,基體和增強相因摩擦和剪切而斷裂,跑合磨損完成后,磨屑產生形變并粘附在復合材料表面,形成自潤滑膜;同時,樹脂基體在高溫下會發生熱解并被不斷氧化,使復合材料表面出現微孔和微裂紋。因此,此時的磨損機理可斷定為黏著磨損、磨粒磨損和氧化磨損;在RT~380℃~RT環境下,復合材料的磨損機理與380℃時類似,但由于周期性環境變化的影響,摩擦表面的潤滑膜會不斷被撕裂并從復合材料表面剝落,故可認為交變溫度下的磨損機理為黏著磨損和氧化磨損。 在不同載荷下,試樣與載荷的實際接觸面積不同,材料的磨損率在實質上是由其承載面積控制的。低載荷下,復合材料表面出現大量微裂紋,如圖8a所示 。在摩擦磨損過程中,試樣表面的微凸點在周期性循環載荷作用下發生微形變和微熔化。由于復合材料中存在的孔隙、雜質等缺陷,在這種周期性形變的作用下,復合材料表面應力集中處分子鏈或分子間鍵斷裂并形成裂紋,此時,磨損形式主要為疲勞磨損;隨著載荷增加,磨損表面出現大量劃痕,其主要磨損形式是磨粒磨損。這是由于樹脂基體較軟,此時,參與磨損的是復合材料表面的微凸塊,其在載荷的作用下發生變形并產生微裂紋,并隨著磨損的進行從復合材料表面脫離,在摩擦面堆積并造成磨粒磨損。 綜上所述,樹脂基摩擦材料在引入填料后的耐磨損機理如圖9所示,在纖維和顆粒類填料的共同作用下,復合材料的承載能力和耐磨性得到了明顯提高。各類填料對樹脂基摩擦材料的影響如表4所示,可見,僅由單一類型填料增強的樹脂基摩擦材料難以滿足復雜工況對摩擦材料的性能要求,因此,使用混合填料已成為樹脂基摩擦材料的普遍趨勢。而摩擦材料的性能是一個多準則決策問題,在探究各類與性能相關的問題時,需要綜合考量摩擦材料的耐磨性、力學性能等方面,且同一材料在不同環境下的磨損形式、磨損機理不盡相同。因此,對復合材料磨損機理的探究任重而道遠,在不斷的研究過程中形成系統、完整的理論體系對復合材料的發展具有重要指導作用。 耐腐蝕增強方法及機理 腐蝕是日常生活中最常見的材料失效形式。與地震、海嘯等“驚天動地”的自然災害不同,腐蝕會在無聲無息中對材料造成極大的破壞。根據世界腐蝕組織的一項調查,每年全球的經濟損失有超過4萬億美元是腐蝕造成的。此外,材料的腐蝕還會產生嚴重的環境污染與資源浪費 。由于涂覆有機防腐涂料具有施工簡便、適用性廣、成本低廉且性能優越等優點,樹脂基復合材料在防腐領域主要以防腐涂層的形式存在,其防腐機理主要可分為屏蔽和抑制作用,在涂層內部,樹脂材料主要起屏蔽作用以防止腐蝕介質向金屬內部方向擴散;在金屬基體表面,樹脂基材料通過與金屬基體的強粘結作用和化學作用防止金屬基體發生腐蝕,從而實現防腐 。 然而,受熱固性樹脂材料高交聯密度的影響,樹脂基材料中會產生微裂紋和孔洞,在樹脂基材料中形成針孔狀孔隙,在實際應用中,腐蝕性介質分子(如水、氧和離子)會滲透到復合涂層中 。在濕熱環境下,復合材料會吸水導致樹脂基體脹大,使界面層結構遭到破壞,從而導致復合材料受力狀態發生變化,如圖10所示 。水分子在吸濕過程中影響了分子鏈間的折疊距離和破壞了分子間的范德華力。另外,水分子擴散到樹脂基體中會引起基體中某些極性基團產生化學反應,使基體水解或破壞其中的鏈結構,削弱分子間化學鍵的結合力,從而降低其防腐性能。此外,樹脂材料對紫外線的低穩定性也在一定程度上限制了它的應用。 此外,復合材料在濕熱環境下的服役時間越長,其力學性能的損傷越顯著 。在諸如海水等堿性環境中,復合材料除了受吸濕性影響外,還會受到水中堿性離子的影響。對比濕熱和堿性環境下玻璃纖維/環氧乙烯基酯復合材料的吸濕速率可知,相同時間內,堿性環境中復合材料吸水率較濕熱環境更大,如圖11所示,即堿性介質促進了復合材料的吸濕速度。對比兩種環境腐蝕后的復合材料表面形貌可發現,相同時間內,堿性環境對試樣的破壞程度遠大于濕熱環境。可以判斷堿溶液除了會對樹脂基體造成嚴重腐蝕外,還會透過基體并進一步腐蝕其中的纖維,削弱纖維與基體界面的結合力,加劇纖維與樹脂基體間界面的破壞。 為解決上述問題,目前主要從以下兩方面提高樹脂基復合材料的防腐性能:(1)減少樹脂基復合材料中的孔隙,提高腐蝕介質向材料內擴散的難度;(2)降低腐蝕介質與復合材料間的親和力。如Fihri等制備的纖維狀二氧化硅改性環氧樹脂材料表現出了優異的疏水性能,且在腐蝕環境中具有優異的耐久性,實驗所用碳鋼基體在涂覆該復合材料后,腐蝕電流密度降低了兩個數量級,其疏水性能是由烴鏈的低表面能和Si-O-Si網狀結構的協同作用決定的。Xia等將改性二硫化鉬(MoS2)引入環氧樹脂體系,與純環氧樹脂材料相比,改性后的復合材料在3.5%(質量分數)NaCl溶液中腐蝕35d后,其耐腐蝕性能提高了近三個數量級。Dagdag等以亞甲基二苯胺為固化劑制備了環氧樹脂復合涂層,并以3% (質量分數)NaCl為腐蝕介質,測試復合涂層的耐腐蝕性。復合涂層的防腐蝕效率最高可達93%左右,這是因為完整的高分子環氧涂層可以抑制腐蝕環境中腐蝕性物質的進入。Situ等向環氧樹脂中加入聚苯胺?氮化鈦納米填料,制得了具有高耐腐蝕性的復合材料,相較純環氧樹脂材料,復合材料的阻抗數量級提高了1~3倍。Yao等制備了聚乙烯醇/酚醛(PVB/PF) 復合材料,在3.5%(質量分數)的NaCl中浸泡30d后,復合材料的低頻阻抗模量(|Z|0.01Hz)為2.41×107Ω·cm2,這是因為PVB和PF形成了均勻致密的結構,使復合材料具有良好的柔韌性、較高的機械強度和優良的阻隔性能。Li等在聚氨酯(PU)制備中合成了銅配合物(Cu(HD)2),加入Cu2+后形成的配位鍵改善了聚氨酯的力學性能,使其結構更加緊密,復合材料的|Z|0.01Hz值從6.033×106Ω·cm2提高到了7.943×107Ω·cm2,且復合材料具有釋放Cu2+的抑菌作用,其在防腐防污領域具有很好的潛力。 向環氧樹脂中添加導電聚合物也是提高復合材料耐腐蝕能力的可行方式之一。缺陷少、石墨化程度高的石墨烯納米片(GO)也是有效提高樹脂基復合材料耐腐蝕性的增強填料之一,適量 GO的加入不僅能有效提高樹脂基復合涂料的耐腐蝕性,還能提高其韌性和結合強度,在10%(質量分數)NaCl腐蝕液中的對比實驗表明,當GO質量分數為1.0%時,復合材料的防腐性能最好 。Dermani等向GO改性環氧樹脂體系加入了活性輔助劑,增強了GO與環氧樹脂間的相容性,并促進其在樹脂體系中的分散。加入活性輔助劑后的復合材料中GO無明顯團聚,且復合材料在3.5%(質量分數)NaCl溶液中腐蝕14d后,相較未加入活性輔助劑的材料,其質量損失減少了40%。此外,無機納米功能填料能夠均勻分散在基體中,堵塞樹脂固化過程中產生的微孔道,提高復合材料的耐腐蝕性。Chang等利用納米鑄造技術制備了具有仿生疏水表面的環氧/石墨烯復合涂層 (HEGC),表面水接觸角約為127°,與純環氧涂層相比,HEGC涂層腐蝕電流密度降低,阻抗模值得到極大提高。Mo等研究利用功能化石墨烯(FG)和FGO提高PU涂層的抗腐蝕性能。研究表明,FG和FGO的引入均降低了涂層的腐蝕電流密度,提高其防腐保護效率,石墨烯復合防腐涂層的防腐蝕性能與純PU涂層相比明顯提高,這是因為具有潤滑和阻隔性的FG和FGO片狀填料分散在聚氨酯基體后,增加腐蝕介質的擴散路徑的曲折程度,復合涂層的抗腐蝕性能大大提高。 近年來,隨著對長期防腐能力要求的不斷提高,研究人員開發出了受到機械損傷后能夠自我修復的自愈合防腐材料。目前,材料的自愈合性能主要來自于向材料內部添加具有緩蝕效果的微粒,這些材料能夠促進材料內部分子間的作用力并在材料受到損傷后為材料提供后續防腐能力。Kim等將碳納米管(CNTs)嵌入溴丁基橡膠(BIIR)制備了CNT/BIIR自愈合復合材料,并將其涂覆在鋼板上,在模擬葉輪工作環境下測試復合材料的耐腐蝕性能,經過40h的腐蝕后,鋼板邊緣出現銹跡,但幾乎覆蓋整個前表面的雙層涂層并沒有剝落,而是一直粘附在基底上,防止其生銹。另外,在150~170℃下測試復合材料的自愈合特性,結果表明材料表面的裂紋只需1h便能完全愈合。Liu等以聚丙二醇(D400)為交聯劑,通過接枝嘧啶酮(UPy)將氫鍵引入環氧網絡,所制得的自愈合環氧復合材料在沒有任何干預的情況下,即使在水浸條件下,也能在5min內發揮自愈功能,且電化學阻抗譜測試結果表明,該自愈合涂層在NaCl溶液中浸泡60d后具有較高的|Z|0.01Hz值,為4.8×1010Ω·cm2 。其自愈合過程如圖12所示,UPy?D400的引入能夠確保分子鏈的高流動性,在室溫下使損壞的涂層界面快速閉合。Wang等向純環氧樹脂中加入緩蝕劑苯并三唑(BTA),對比發現加入6%BTA的復合材料的耐腐蝕性能最好,其在3.5%(質量分數)的NaCl溶液中的耐腐蝕性提高了1.4倍,這是由于BTA具有優異的超疏水性能,可以在不破壞材料微觀結構完整性的情況下延長腐蝕介質在材料中的擴散路徑,且材料表面損傷后,BTA可以從其損傷區域釋放出來,提高復合材料的自愈合性能。 綜上所述,復合材料的腐蝕和老化是不可避免的,目前針對樹脂基防腐材料的研究主要集中在添加增強相,阻止腐蝕介質向復合材料內部滲透,即主動防腐領域。近年來,盡管有學者展開了被動防腐(即自愈合復合材料)的研究,但目前針對這方面的研究尚淺,所研制的復合材料的自愈合作用不可逆,且承載能力受到空間的限制,其愈合性能和力學性能相互制約。此外,因為自愈合復合材料的分子間相互作用非常敏感,并且對水、酸、堿分子具有滲透性,所以其對酸堿腐蝕的抵抗力較低。同時,由于具有自愈性能的材料通常力學性能較差,自愈性能與材料力學性能之間存在相互限制。因此,有必要根據其物理和化學性質設計出合適的聚合物,合理利用填料優良的理化性能改善自愈合復合材料的綜合性能,降低其成本,這將會是未來很長一段時間的研究方向。理想情況下,防腐材料應該具有高阻隔能力、良好的力學和自愈性能,能夠適用于重型防腐應用。 結語與展望 改性后的樹脂基復合材料在抗燒蝕、耐磨損和耐腐蝕等表面防護領域表現出了優異的性能,但綜述國內外研究成果后發現,其在制備和使用中仍存在一系列問題,如填料與樹脂體系無法緊密相容、某些填料在樹脂體系中均勻分散難度大、改善某種性能的同時降低了其他方面的性能等。面對材料技術高速發展的趨勢,未來應結合材料基因組計算技術對樹脂基復合材料進行進一步組分和結構優化,結合有機與無機材料的工藝性能特點,筆者認為,在后續的研究工作中,應注意以下三個方面內容: 1 高性能、多功能、輕量化是基本性能要求復合材料的服役環境十分復雜,部分材料在滿足功能材料要求的基礎上,還需要充當承重結構件,有些部件在服役過程中還會受到嚴重的沖蝕作用,這意味著材料還應該具有高抗沖蝕性和一定的斷裂韌性。此外,復合材料輕量化已成為近年來的熱點問題,材料的質量越輕,設備運行速度就越快,續航時間就越長。因此,在提高復合材料性能的過程中,還應同時注意復合材料的輕量化問題。 2 規范、系統的理論指導是重要保障目前,針對增強改性后的樹脂基復合材料的研究主要是為了提高復合材料的實用性,其機理方面的研究較少,尤其是對于服役環境復雜的樹脂基摩擦材料,其磨損形式受多種因素影響,掌握其摩擦磨損機理至關重要。因此,研究樹脂基復合材料的增強機理及復合材料在服役過程中的損傷機理,形成一套完善的理論體系,對樹脂基復合材料的結構設計和改良有重要指導意義。 3 綠色、環保的材料特性是大勢所趨熱固性樹脂固化后不溶不融的特性使其應用領域廣闊,卻也使其在循環回收方面給人們帶來了極大的困擾。目前主要的處理方式有填埋、研磨、燃燒和熱解等,這些方法不僅會消耗大量能源,造成嚴重的資源浪費,還會對環境產生一定污染。樹脂基復合材料的回收利用已成為實現環境保護和社會可持續發展的重要挑戰。因此,無論是開發新型復合材料還是改進現有材料時都應把其可回收性作為設計依據之一,此舉不僅能夠賦予樹脂基復合材料可持續發展能力,還是降低其成本、擴大其應用范圍的長久之計。
免責聲明:本網站所轉載的文字、圖片與視頻資料版權歸原創作者所有,如果涉及侵權,請第一時間聯系本網刪除。
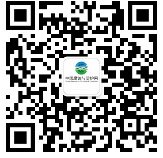
官方微信
《腐蝕與防護網電子期刊》征訂啟事
- 投稿聯系:編輯部
- 電話:010-62316606
- 郵箱:fsfhzy666@163.com
- 腐蝕與防護網官方QQ群:140808414