
常規涂層通過屏蔽水、氧氣、氯離子等腐蝕介質對金屬基體起到保護作用,而富鋅涂層不僅通過屏蔽作用,還通過具有陰極保護作用和自我修復功能的鋅粉實現對金屬基體的保護,因此其保護性能得到大幅提高[1-4]。為有效發揮鋅粉的陰極保護作用,鋅粉顆粒之間必須保持電連續,這就要求涂層中的鋅粉必須達到一定量[5],但高含量的鋅粉易導致涂層微觀多孔、與基體的附著力減弱[6-7]。為此,近年來國內外學者針對富鋅涂層的新型填料進行了研究。SCHAEFER等[8]發現用鋅納米顆粒替代一小部分鋅粉顆粒可使涂層的電化學作用增強;ARIANPOUYA等[9]揭示了納米鋅/納米黏土添加劑對富鋅涂層耐蝕性能的協同效應;解曉雷[10]研究發現添加0.2%(質量分數)單壁碳納米管和30%~40%(質量分數)鋅粉的環氧富鋅涂層滿足了體系耐鹽霧腐蝕性能的需求;ZHANG等[11]研究了含有改性硅基載體和層狀Zn(Al)顏料的富鋅涂層的保護性能,發現顏料使富鋅涂層的保護性能得到增強;GERGELY等[12]研究了負載有含聚吡咯氧化鋁納米顆粒的富鋅涂層的保護性能,發現該涂層具有陰極保護和阻隔作用。添加新型填料降低鋅粉的含量以改善陰極保護的電連續性、提高涂層的阻隔作用和耐蝕性能是富鋅涂料研究的主要方向。作者采用阻隔性能較好的片狀鋁粉替代部分鋅粉,通過馬丘試驗,快速選出最佳的鋁粉添加范圍,在此基礎上,采用電化學阻抗譜和紅外光譜研究了鋁粉添加前后涂層的耐蝕性,通過本文的研究,獲得一種能改善富鋅涂料耐蝕性能的環氧富鋅鋁涂層。
1. 試驗
1.1 涂層制備
試驗鋼板為Q235鋼,將試驗鋼板加工成尺寸為150 mm×75 mm×2 mm的試樣。對試樣進行噴砂除銹(Sa2.5級),使其表面粗糙度為50~100 μm,并用丙酮擦洗表面灰塵后干燥,備用。
涂料制備:依次將E44(6101)環氧樹脂、球狀鋅粉(粒徑15 μm,)、片狀鋁粉(尺寸30 μm)、稀釋劑二甲苯加入高速攪拌機中,以500 r/min轉速攪拌10 min;加入LD-1132分散劑,以1 300 r/min轉速攪拌10 min;加入LD-9108流平劑,以600 r/min轉速攪拌10 min;靜置10 min后待用。
在涂料中加入適量T-31固化劑,攪拌均勻。通過手工涂刷的方式將涂料涂刷到處理好的鋼板表面,共涂刷2遍。第一遍涂刷完成、表干后再涂第二遍。單次涂刷厚度為40~60μm,涂層總干膜厚度為90~100 μm。通過上述步驟,分別制備了Zn質量分數為75%、鋁質量分數分別為2%、4%、5%、6%的環氧富鋅鋁涂層,依次用75%Zn-2%Al涂層、75%Zn-4%Al涂層、75%Zn-5%Al涂層和75%Zn-6%Al涂層表示。另外,用相同方法制備了環氧清漆涂層、環氧富鋅涂層(Zn質量分數為80%)。
1.2 馬丘(Machu)試驗
參考QUALICOAT質量標準《建筑用鋁型材表面噴漆、粉末涂裝的質量控制規范》,對涂層試樣進行馬丘試驗。測試液為Machu溶液,含50 g/L氯化鈉、10 g/L冰醋酸,5 mL/L 30%(質量分數,下同)過氧化氫,pH為3.0~3.3。
用石蠟涂封涂層試樣的邊緣,用美工刀在涂層中央垂直刻畫兩條長度為3 cm的直線,刻痕達基體。試驗開始后,將涂層試樣浸沒在Machu溶液中,通過恒溫水浴鍋將溶液溫度控制在(37±1)℃,觀察試樣表面隨浸泡時間的變化,并通過拍照記錄。浸泡24 h后,向溶液中補加30%過氧化氫,加入量為5 mL/L。
1.3 電化學測試
采用CS350電化學工作站對涂層試樣進行電化學測試。電解液為3.5%(質量分數)NaCl溶液,測試溫度為室溫。測試過程采用了三電極體系:工作電極為表面涂覆不同鋅、鋁含量涂層的Q235鋼(1#、3#、4#、5#);參比電極為飽和甘汞電極(SCE)、輔助電極為鉑電極。交流正弦波振幅為20 mV,頻率范圍為10-2~105 Hz。測試后采用Origin軟件對數據進行處理。
1.4 紅外光譜測試
采用FTIR-650型傅里葉變換紅外光譜儀對浸泡前和浸泡20 d后的涂層試樣進行紅外光譜測試。將涂層用KBr壓片法制成透明的薄片,將制好的KBr薄片輕輕放在鎖氏樣品架內,插入樣品池并拉緊蓋子,在軟件設置好的模式和參數下測試紅外光譜圖。分辨率為4 cm-1,掃描次數為32次,掃描范圍為400~4 000 cm-1。
2. 結果與討論
2.1 馬丘試驗
從圖1(a)中可以看出:浸泡24 h后,環氧清漆涂層試樣劃痕處出現大量銹跡,且涂層表面還出現了大量的紅色銹點;浸泡48 h后,劃痕處的紅色銹跡顏色進一步加深至黑色,涂層表面紅銹蝕增多且銹蝕加重。以上結果表明,環氧清漆涂層中存在著大量的缺陷,腐蝕介質在劃痕處或者表面缺陷處透過涂層與碳鋼基體接觸,腐蝕了碳鋼基體。

從圖1(b)中可以看出:浸泡24 h后,環氧富鋅涂層試樣劃痕處并未出現銹點,但涂層表面出現了細小的紅色銹點,這說明透過涂層的腐蝕介質與涂層中的鋅粉發生了反應,生成的腐蝕產物填充在涂層縫隙中防止介質進一步侵蝕[13];浸泡48 h后,劃痕處出現大量細小紅色銹點及一處較大銹點,且涂層表面原有銹點擴大。隨著浸泡時間的延長,腐蝕產物不能完全覆蓋鋼基體暴露部分,暴露部分發生腐蝕,因此劃痕處銹蝕點增多并出現較大銹蝕點。隨著浸泡時間的延長,涂層表面原有銹點擴大說明鋅陽極的陰極保護不能完全覆蓋到整個涂層表面。
從圖1(c)中可以看出:浸泡24 h后,75%Zn-2%Al涂層試樣劃痕處出現大量銹跡,但涂層表面并未出現了大量的紅色銹點;浸泡48 h后,劃痕處的紅色銹跡顏色進一步加深,同時涂層表面也出現了較多銹點。以上結果表明,在75%Zn-2%Al涂層中,少量的片狀鋁粉對改善涂層中鋅粉的電連續性和涂層的屏蔽作用均有限。
從圖1(d)中可以看出:浸泡24 h和48 h后,75%Zn-4%Al涂層試樣表面和劃痕處的銹跡較75%Zn-2%Al涂層試樣均大幅降低,這表明添加4%片狀鋁粉進一步改善了涂層中鋅粉的電連續性和涂層的屏蔽作用。
從圖1(e)中可以看出:浸泡24 h后,75%Zn-5%Al涂層試樣劃痕處并未出現大量銹跡,涂層表面也未出現大量紅色銹點;浸泡48 h后,劃痕處的紅色銹跡變化不明顯,但涂層表面出現了一定量的銹點。以上結果表明,在75%Zn-5%Al涂層保護下碳鋼基體只出現了輕微腐蝕,涂層中片狀鋁粉可較好改善涂層中鋅粉的電連續性和涂層的屏蔽作用。
從圖1(f)中可以看出:75%Zn-6%Al涂層試樣中鋁粉質量分數增加到了6%,此時其表面和劃痕處銹蝕又開始加重。這說明當添加的鋁粉超過一定量后,涂層對基體的保護效果反而變差,基體的腐蝕程度加重。
環氧清漆涂層由于不含鋅粉,不具有陰極保護作用,涂層耐蝕性能差;環氧富鋅涂層由于含有較大量(80%)的鋅粉,具有陰極保護的作用,耐蝕性好;當環氧富鋅鋁涂層中添加了2%、4%和6%片狀鋁粉時,鋁粉對屏蔽作用和電連續性的綜合改善效果小于鋁粉對鋅粉的擠占效果,而鋁粉不具有陰極保護作用,所以涂層的耐蝕性能下降,但添加5%片狀鋁粉時,鋁粉對屏蔽作用和電連續性的改善效果與鋁粉對鋅粉的擠占效果相當,涂層的耐蝕性能達到最佳[14]。因此,環氧富鋅鋁涂層中鋁粉的最佳添加量為5%。
2.2 電化學阻抗測試
從圖2中可知,當浸泡時間為0~8 h時,環氧富鋅涂層的容抗弧半徑較大且隨浸泡時間延長緩慢減小,低頻(0.017 Hz)阻抗和相位角隨浸泡時間的延長均變化較小,這說明涂層在該階段擁有較好的物理阻隔功能,碳鋼基體無法與浸泡溶液接觸從而產生腐蝕;浸泡2 d后,涂層的低頻阻抗下降了約1個數量級,從109 Ω·cm2下降至108 Ω·cm2,并且容抗弧半徑急劇縮小;浸泡16 d后,涂層的低頻阻抗下降了3個數量級,降至106 Ω·cm2,在此階段,浸泡溶液逐漸滲透涂層到達基體,與基體發生電化學反應,使基體腐蝕;浸泡20 d后,涂層的容抗弧半徑和低頻阻抗都出現小幅增大,這說明隨著腐蝕反應的持續進行,腐蝕產物慢慢累積,形成了新的物理阻隔層,從而延緩了腐蝕進程。

從圖3中可知,當浸泡時間為0~8 h時,75%Zn-5%Al涂層的容抗弧半徑較大且隨浸泡時間延長緩慢減小,低頻(0.017 Hz)阻抗和相位角隨浸泡時間的延長均變化較小,說明涂層在這個階段擁有較好的物理阻隔功能,使碳鋼基體無法與浸泡溶液接觸而產生腐蝕;浸泡1 d后,涂層的低頻阻抗下降了約1個數量級,從107 Ω·cm2下降至106 Ω·cm2;浸泡16 d后,低頻阻抗下降了2個數量級,下降至105 Ω·cm2,容抗弧半徑和低頻相位角也出現明顯降低;但是在隨后的浸泡過程中(至42 d),涂層的阻抗呈緩慢下降趨勢,容抗弧和相位角與阻抗一樣,也呈緩慢下降的趨勢。這說明浸泡溶液在涂層內滲透是非常緩慢的,當其與碳鋼基體接觸后,未能使基體形成較大面積的腐蝕,加之腐蝕產物的出現,基體腐蝕速率大幅降低。

比較圖2和圖3中電化學阻抗譜可知,在浸泡初期(2~8 h),環氧富鋅涂層與75%Zn-5%Al涂層的低頻阻抗數量級分別為109 Ω·cm2和107 Ω·cm2,這說明鋁通過架橋作用改善了涂層中鋅粉的電連續性,從而改善了涂層的陰極保護效果[15];浸泡2、16 d后,這兩種涂層的低頻阻抗數量級從109 Ω·cm2和107 Ω·cm2分別下降到106 Ω·cm2和105 Ω·cm2,說明介質浸透涂層后與鋅、鋁反應生成的腐蝕產物比單獨與鋅反應生成的腐蝕產物具有更好的保護性能。
從圖4可見,浸泡前(0 h),75%Zn-4%Al涂層的低頻阻抗數量級為107 Ω·cm2,浸泡2、4 h時,其又增加到108 Ω·cm2。從圖5可見,浸泡0~8 h時,75%Zn-6%Al涂層的低頻阻抗數量級為108 Ω·cm2,高于相同浸泡時間其他幾種環氧富鋅鋁涂層的。比較圖2~5可知,加入5%片狀鋁粉對鋅粉電連續性的改善效果最優。


2.3 紅外光譜測試
由圖6(a)可知,浸泡20 d后,環氧清漆涂層中-CH2-的彎曲振動峰位出現較高增長,C-O伸縮振動峰位略有上升,而羥基伸縮振動峰位出現較大幅的增加。這說明涂層中含有了氫氧化物,腐蝕介質中的氧氣、水等透過涂層直接和碳鋼基體發生反應,生成不具有保護性的堿性氧化物。由6(b)圖可知,浸泡20 d后,環氧富鋅涂層中C-O伸縮振動峰位和羥基伸縮振動峰位出現了大幅增加,而-CH2-的彎曲振動峰位和C=O伸縮振動峰位則基本不變,-CH2-對稱伸縮振動峰位降低。這說明腐蝕介質進入涂層后與涂層中的鋅反應生成了保護性能較好的鋅的堿性化合物。由圖6(c)圖可知,75%Zn-5%Al涂層中-CH2-對稱伸縮振動峰位基本無變化,羥基伸縮振動峰位出現小幅增加,其余峰位也基本不變。這說明進入涂層的腐蝕介質與涂層中的鋅、鋁反應生成的腐蝕產物除鋅的堿性化合物外,還包括鋁的堿性化合物,且后者比前者更穩定。因此,環氧富鋅鋁涂層比環氧富鋅涂層對基體的保護性能更好。

3. 結論
(1)馬丘試驗結果表明,環氧清漆涂層存在大量的缺陷,在浸泡過程中,腐蝕介質會通過涂層缺陷直接和碳鋼基體接觸使基體發生腐蝕;環氧富鋅涂層中的鋅具有陰極保護作用,透過涂層的腐蝕介質先和鋅反應生成具有保護性能的腐蝕產物,使基體金屬免遭腐蝕;在富鋅涂層中加入5%的片狀鋁粉,能有效改善鋅粉的電連續性和涂層的阻隔作用,提高了涂層的耐蝕性。
(2)電化學阻抗測試結果表明,添加的片狀鋁可通過架橋作用改善涂層中鋅粉的電連續性,從而改善鋅粉的陰極保護效果。
(3)在3%NaCl溶液中浸泡20 d后,環氧清漆涂層中的腐蝕產物不具有保護性,而富鋅涂層和含5%鋁的富鋅鋁涂層中的腐蝕產物具有較好的保護性。
免責聲明:本網站所轉載的文字、圖片與視頻資料版權歸原創作者所有,如果涉及侵權,請第一時間聯系本網刪除。
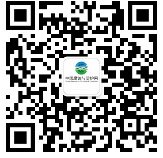
官方微信
《腐蝕與防護網電子期刊》征訂啟事
- 投稿聯系:編輯部
- 電話:010-62316606
- 郵箱:fsfhzy666@163.com
- 腐蝕與防護網官方QQ群:140808414