存貯有長壽命極毒組核素的 16MnR 廢物包裝容器存放在封閉洞室環境中,部分容器填埋在膨潤土和混凝土回填結構中。通過現場原位實驗和實驗室加速實驗,利用重量法,XRD,SEM/EDS,電化學阻抗技術和線性極化技術等方法開展了包裝容器腐蝕防護和評價研究。通過納米改性設計了納米重防腐有機涂層體系,探索了多種滿足包裝容器長效防腐要求的材料體系和涂裝工藝。
一定數量的 16MnR 鋼制密封容器存放在封閉洞室環境中,容器中封閉著 239Pu 等長壽命極毒組核素。在可見的將來,利用已有技術把放射性物質移出容器、轉移到其它存儲空間的技術難度大、成本高,因此把這些容器作為其中放射性廢物的包裝容器 。國內外大量的研究和工程實踐表明,放射性廢物處置和暫存均對存貯容器的耐腐蝕性能有較高要求 。前期研究結果表明,包裝容器選用的 16MnR 鋼材料在存放洞室中的腐蝕比較嚴重 。為了將地質條件用作防止放射性核素進入人類生存環境的屏障,借鑒高放廢物地質處置的多重屏障設計,部分容器被就地填埋處理,填埋過程中,在包裝容器與地質體之間填入混凝土和膨潤土回填材料 。因此,為了增強包裝容器的耐腐蝕性能,借鑒并優化商用重防腐有機涂層進行容器表面防腐,并研究探索將可用于多種介質環境常溫下重防腐的 Zn-Al 金屬涂層用于進一步提高包裝容器的耐腐蝕能力和耐磨性,對防腐涂層與包裝容器在填埋條件下的有效壽命進行預估。
實驗所用材料和儀器
試 樣 包 括 16MnR 裸 鋼 試 樣 和 6種 帶 涂 層 16MnR 鋼 試 樣, 涂 層 包 括Zn 涂 層、Al 涂 層、Zn/Al 復 合 涂 層(100/300μm 和 300/100μm 兩 種 設計)、Zn-Al 合金涂層和納米有機涂層。裸鋼試樣和涂層試樣基材的尺寸為100mm60mm6mm。納米有機涂層按照現場采用的涂層設計(如表 1 所示)和涂裝工藝進行加工,金屬涂層厚度設計為400μm,采用高速電弧噴涂技術加工。
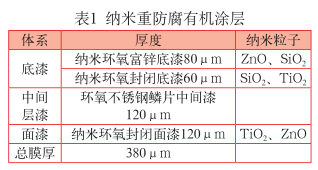
回填材料分別為輕集料混凝土和柯爾堿 200 目膨潤土。其中,膨潤土壓實干密度達到 1.5g/cm 3 ,含水率為26%~28%,輕集料混凝土的配方如表 2所示。
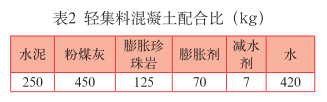
對于材料腐蝕研究,研究人員普遍采用室外現場埋設實驗和室內模擬實驗相結合的研究方法?,F場埋設實驗可以較客觀地反映實驗土壤腐蝕狀態,但其實驗周期一般較長,需要耗費大量的人力、物力。加速腐蝕實驗作為室內模擬實驗的重要組成部分,是在全面調查現場環境的基礎上,控制實驗參數,在較短時間內獲取材料腐蝕機理及腐蝕速率的有效方法。
參考 GB 1763 和 GB 1690,利用強化介質法對 16MnR 鋼及其防腐涂層在存放洞室中的大氣腐蝕行為進行了鹽霧加速腐蝕實驗研究。為提高腐蝕實驗相關性,鹽霧腐蝕實驗溶液以 5%wtNaCl 溶液為基礎,其它離子的濃度按照洞室冷凝水水中離子含量 1:1 配制。
為開展 16MnR 鋼材料及其防腐涂層在洞室環境與膨潤土和輕集料混凝土的相容性研究,開展了 180d 的填埋環境加速腐蝕實驗研究。兼顧相關性和加速比,利用現場回填所用的輕集料混凝土和膨潤土,并采用類似的回填工藝制備了埋有試片的混凝土結構件和膨潤土結構件,以此實現現場回填環境的模擬,并依據上述腐蝕機理周期性采用“強化介質法 + 干濕交替法”兩種方法實現加速腐蝕。包裹塊的包裹厚度為 25 ~ 30mm;強化介質溶液以 3.5%wtNaCl 溶液為基礎,其它離子的濃度按照洞室現場裂隙水中離子含量 1:1 配制;包裹塊浸泡 -干燥周期時間為 168h,其中浸泡時間為72h,干燥時間為 96h。
利用 PARSTAT2273 電化學工作站測試回填材料中涂層試片的線性極化曲線和電化學阻抗譜,并計算極化電阻 Rp和斯特恩 - 蓋里常數 B 值。利用 B 值和極化電阻 Rp 計算得到腐蝕電流密度,進而利用法拉第定律計算出腐蝕速率。試樣為工作電極,采用石墨電極為輔助電極,飽和甘汞電極為參比電極。
涂層體系設計
與中國科學院金屬研究所合作,將經過包覆改性、微膠囊化表面改性的納米 SiO 2 、TiO 2 和 ZnO 顆粒作為填料分散在在環氧樹脂的聚合物結構中,研制出了如表 1 所示的環氧系納米重防腐有機涂料。一方面,納米粒子的比表面積大、表面活性大,因此可以提高納米粒子與環氧基料、涂層與金屬基體之間的結合力;另一方面,致密的納米粒子網絡結構能夠有效抵抗腐蝕介質的滲透 。為實現納米有機涂層在 16MnR 鋼容器表面的良好涂裝,根據涂層的表面質量、硬度及其與 16MnR 基體的結合強度等指標開展工藝優化實驗,確定了高壓無氣噴涂工藝參數:噴涂速率為 40 ~ 50cm/s,噴涂距離為 40 ~ 60cm;空壓機輸出壓力為 0.3 ~ 0.5MPa(壓力比為 65:1)和0.4 ~ 0.6MPa(壓力比為 32:1)。利用上述工藝得到的涂層硬度≥ 0.5(別爾科維其硬度),其與 16MnR 基體的附著力為 1 級(劃圈法)。
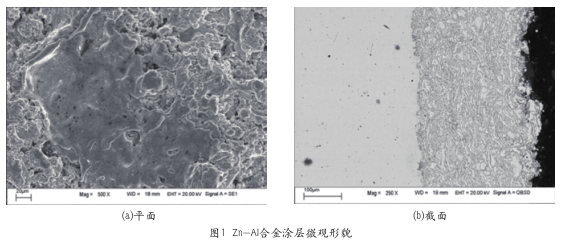
與有機涂層相比,合金涂層具有與金屬基體更大的結合力、可涂裝厚度大(mm 級 ) 等優點,而且其成本較低、工藝周期較短(不需要涂層干燥和固化時間),因此選擇以高速電弧噴涂工藝為主要技術特征的 Zn、Al 合金涂層開展研究,以豐富 16MnR 包裝容器的表面防腐涂層體系。綜合考慮涂層孔隙率、硬度及其與基體的結合強度,采用正交實驗方法優化得到了 Zn-Al 合金涂層高速電弧噴涂工藝參數為:噴涂電壓 30V、噴涂電流 180A、噴涂距離150mm、噴涂氣壓 0.7MPa。按照此組參數制備的 Zn-Al 合金涂層,其表面和截面顯微組織形貌如圖 1 所示,涂層由淺色區富 Zn 相和深色區富 Al 相二相組成,其中富 Al 相呈連續的框架網絡,富 Zn相以塊狀形式存在于富 Al 相的網絡包圍之中。經性能檢測,涂層結合強度為32.5MPa,孔隙率為 2.1%,顯微硬度為HV49.45。
納米有機涂層耐腐蝕性能原位考核研究
在 16MnR 包裝容器暫存洞室內經歷5a 掛片實驗,16MnR 鋼裸片表面發生全面腐蝕,部分鐵銹脫落,在焊縫兩側熱影響區腐蝕嚴重;采用納米有機涂層保護的 16MnR 鋼試片表面的涂層無可檢測到的破壞,沒有起泡、剝離、脫層和生銹現象,如圖 2 所示。
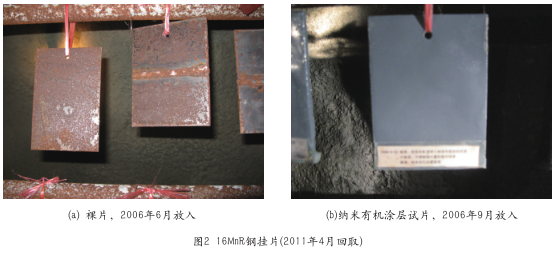
從經歷 4 年掛片實驗的試片邊緣處剝去部分涂層發現,邊緣部分的涂層發生腐蝕,基體沒有發現可見腐蝕現象,如圖 3 所示。邊緣處發生銹蝕是試片制備過程中封邊質量不佳造成的。對納米環氧富鋅底漆中的 Zn 粉進行 X 射線衍射分析發現,Zn 粉的相組成為 Zn 和 ZnO,兩者的質量比例為Zn:ZnO=89:11,如圖 4(a) 所示;收集圖 3 中白色粉末進行 X 射線衍射分析發現,其相組成為 Zn、ZnO 和 Zn(OH)2,三者的質量比為:Zn:ZnO:Zn(OH)2=2:46:31,如圖 4(b) 所示;對圖 3 中的黑灰色部分進行 X 射線衍射分析發現,該部分的相組成為 Zn 和 ZnO,兩者的質量比例 Zn:ZnO=92:8,與涂料中原始 Zn 粉的質量組成相當,如圖 4(c) 所示。這表明,一方面,經過洞室環境 4年考核,腐蝕性介質并未穿過涂層而造成基體腐蝕,這說明采用的納米重防腐有機涂層對腐蝕性介質具有較好的機械屏蔽作用;另一方面,盡管因涂層工藝缺陷原因(如封邊質量不佳等)會使得腐蝕性介質沿平行于涂層方向傳輸到達涂層與基體界面,但由于 Zn 粉可通過消耗自身來保護基體,起到了很好的陰極保護作用。
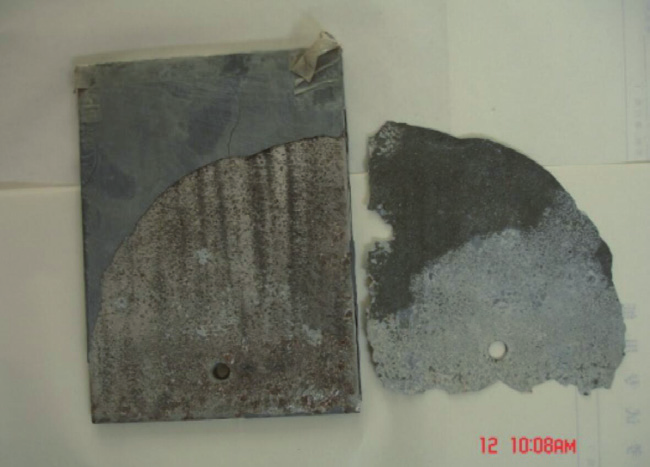
圖3 剝離部分涂層的掛片的表觀形貌
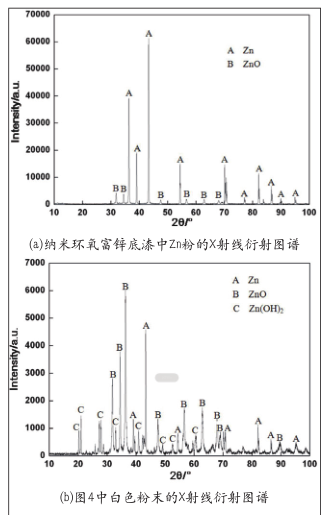
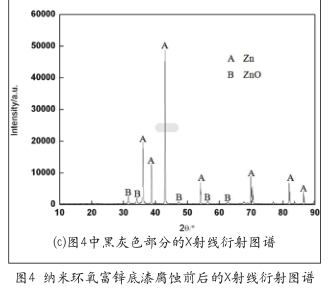
在 16MnR 包裝容器暫存洞室內膨潤土和水泥粉中經歷 4a 埋片實驗,16MnR鋼裸片發生顯著腐蝕,采用納米重防腐有機涂層保護的 16MnR 鋼試片表面的涂層基本無破壞,沒有起泡、剝離、脫層和生銹現象,如圖 5 所示。
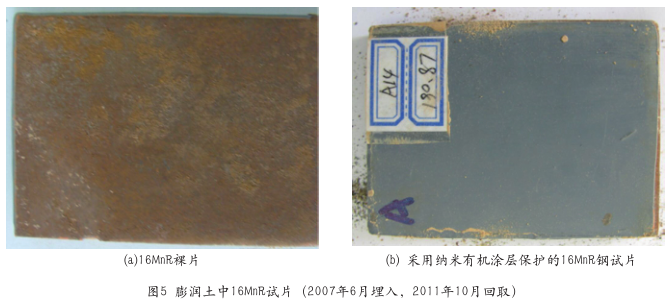
涂層耐洞室大氣腐蝕性能的鹽霧腐蝕考核研究
鹽霧腐蝕實驗過程中,未經防腐處理的 16MnR 鋼試片經歷 120h 加速腐蝕實驗即發生大面積腐蝕,如圖 6 所示;采用納米改性前的商用重防腐環氧有機涂層試片在 3600h 加速實驗后表面出現起泡和少量銹斑現象;而采用納米有機涂層保護的 16MnR 鋼試片表面經歷4500h基本無破壞,沒有可檢測的變化,如圖 7 所示。根據腐蝕與防護領域的工程經驗,以 1000h 加速腐蝕實驗相當于海洋大氣環境或濕熱大氣環境現場腐蝕10a 為參考,預估納米有機涂層可在 45a內保護 16MnR 鋼容器在洞室大氣環境中不發生腐蝕,超過 30a 的防腐壽命需求。
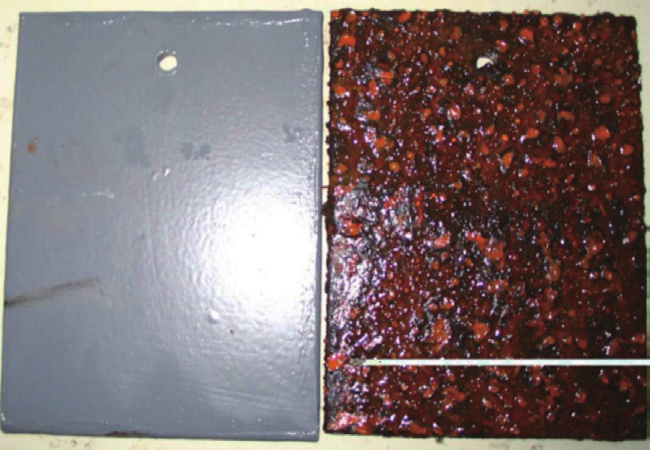
(左試片涂有納米復合涂層,右為裸片)
圖6 120h加速實驗后試片照片
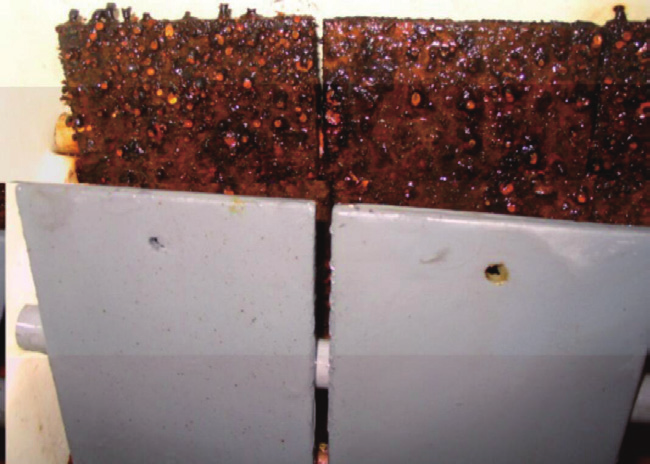
(前試片涂有納米復合涂層,后為裸片)
圖7 4500h加速實驗后試片照片
圖 8 和圖 9 分別給出了 5 種合金涂層的腐蝕累計增重和增重速率隨鹽霧時間的變化,Zn 涂層和 Zn-Al 合金涂層的增重數據接近,腐蝕速率較高;Al 涂層與兩種Zn/Al復合涂層的腐蝕速率較??;Zn-Al 合金涂層 30d 腐蝕增重是 Al 涂層的 1.88 倍,Zn 涂層 30d 的腐蝕增重是Al 涂層的 1.69 倍;Al 合金涂層的累計增重速率隨鹽霧實驗時間顯著下降,這是 Al 涂層孔隙率低、結合強度大,其腐蝕產物因充填涂層空隙而形成“鈍化膜”,因此其耐腐蝕性能較優。
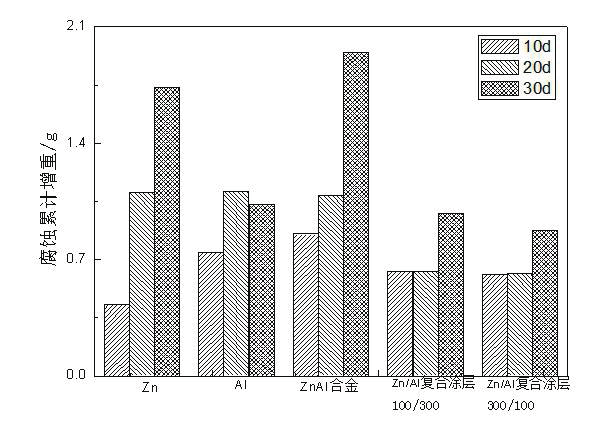
圖8 合金涂層的累計增重
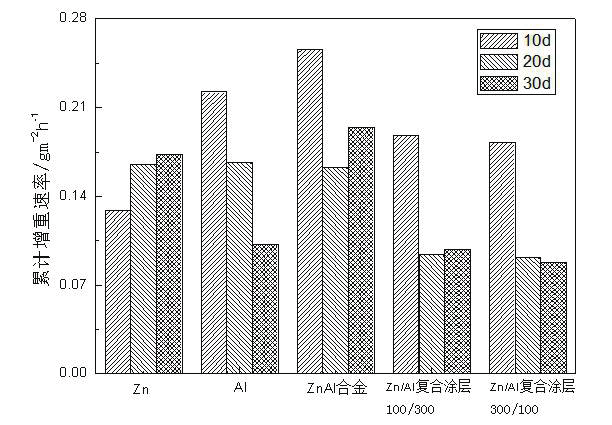
圖9 合金涂層的累計增重速率
實驗時間為 10d、20d、30d 時,納米有機涂層腐蝕速率分別是 6.40×10-3μm/a、4.22×10-2μm/a 2.62×10-1μm/a。納米有機涂層在鹽霧腐蝕過程中的腐蝕速率較低,而且涂層宏觀微觀未發生明顯變化,仍有較好的屏蔽保護性。Al 涂層靠涂層自身屏蔽作用及陰極保護作用達到保護基體的效果,加速30d 后涂層仍較為致密,且 Al 涂層有一定的鈍化自修復作用,因此認為其防護作用優于納米有機涂層。由于 Zn/Al 復合涂層出現鼓泡,Zn-Al 合金涂層發生明顯腐蝕,可認為其對基體的防護效果差于納米有機涂層。因此,對各涂層在鹽霧腐蝕實驗過程中的耐蝕性進行排序,由高至低依次為:Al 涂層 > 納米有機涂層 >Zn/Al-100/300 復合涂層 >Zn/Al-300/100 復合涂層 >Zn-Al 合金涂層 >Zn 涂層。
涂層耐土壤腐蝕性能的加速腐蝕考核研究
經過 180d 模擬膨潤土和輕集料混凝土填埋環境的加速腐蝕實驗,通過與耐洞室大氣腐蝕性能的鹽霧腐蝕考核研究類似的評價內容,根據重量法、厚度法、宏觀微觀觀察法和電化學阻抗法的綜合分析發現,6 種涂層在膨潤土和輕集料混凝土環境中的耐蝕性排序相同,均為 Al 涂層 > 納米有機涂層 >Zn/Al-300/100 復合涂層>Zn/Al-100/300 復合涂層 >Zn-Al 合金涂層 >Zn 涂層。
對比研究發現,納米有機涂層顯著提高了 16MnR 鋼容器在膨潤土和輕集料混凝土環境中的耐腐蝕能力,其腐蝕速率在研究范圍內降低了 1888 倍和 52倍以上。鑒于納米有機涂層具有優良的耐腐蝕性能,而且可以利用無氣噴涂、空氣噴涂和手工刷涂等多種工藝進行涂裝,對狹窄空間和深地坑等施工環境也具有較好的適應性,納米有機涂層已經用于部分 16MnR 放射性廢物包裝容器的表面防腐。
涂層耐腐蝕壽命預估
研究發現,Al 涂層試樣在容器存貯洞室經歷 10 個月和 16 個月的掛片實驗的大氣腐蝕速率分別為 9.32m/a 和3.59m/a,而且 Al 涂層由于生成鈍化膜導致其腐蝕速率隨腐蝕時間而降低,因此預估 400m 厚的 Al 涂層在存貯洞室有不少于 111a 的耐大氣腐蝕壽命,同樣超過 30a 的防腐壽命需求。
根據對 Zn 涂層的腐蝕機理分析及腐蝕形貌觀察認為,Zn 涂層的腐蝕屬于均勻腐蝕,而且其腐蝕產物覆蓋于涂層表面產生一定的屏蔽作用,因此認為其腐蝕規律與低合金鋼類似。利用電化學線性極化曲線法原位測量得到 Zn 涂層在輕集料混凝土環境模擬腐蝕實驗中的腐蝕速率 R,進而計算得到 Zn 涂層的腐蝕深度 C 與時間 t 的關系為:

將 Zn 涂層的腐蝕深度 C=400μm代入 (1) 式計算可得 400μm 厚的 Zn 涂層在輕集料混凝土模擬腐蝕實驗過程中的防腐壽命約為 252a。在研究過程中,模擬腐蝕實驗混凝土塊的包裹厚度(2.5 ~ 3cm)比包裝容器的輕集料混凝土層厚度(20cm)大約低 1 個數量級,因此 400μm 厚的 Zn 涂層在真實回填場景中的防腐壽命不低于 252a。而且在研究的 6 種涂層中,Zn 涂層對 16MnR 的防護效果最差,因此可以預估 400μm 厚的6 種涂層在真實回填場景中的防腐壽命均不低于 252a,超過 100a 的防腐壽命要求。
結論和后續考慮
通過 16MnR 放射性廢物包裝容器的表面腐蝕防護研究,分析了包裝容器在封閉洞室環境中大氣腐蝕機理和在膨潤土、輕集料混凝土填埋環境中的土壤腐蝕機理,針對性設計了納米有機涂層和 5種合金涂層,開展了模擬封閉洞室環境大氣腐蝕的鹽霧加速考核實驗和模擬膨潤土與輕集料混凝土填埋環境的土壤腐蝕加速考核實驗。6 種涂層在洞室大氣環境、膨潤土以及輕集料混凝土填埋環境中耐蝕性排序類似,均為 Al 涂層 > 納米有機涂層 > 其它 4 種涂層。納米有機涂層和 Al 涂層在存貯洞室分別有不少于 45a和 111a 的耐大氣腐蝕壽命,在填埋環境中的防腐壽命不低于 252a,均顯著超過防腐需求。納米有機涂層已經用于小型16MnR 放射性廢物包裝容器的表面防腐。
后續將開展 Zn-Al 合金涂層的失效機理研究,明確其在洞室大氣和膨潤土以及輕集料混凝土填埋環境耐腐蝕性能不佳的原因;針對洞室大氣環境和膨潤土以及輕集料混凝土填埋環境開展 Al 涂層的封閉涂層體系研究,為最終用于大型16MnR 放射性廢物包裝容器表面防腐提供支持。
免責聲明:本網站所轉載的文字、圖片與視頻資料版權歸原創作者所有,如果涉及侵權,請第一時間聯系本網刪除。
相關文章
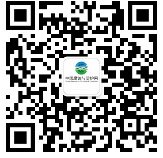
官方微信
《腐蝕與防護網電子期刊》征訂啟事
- 投稿聯系:編輯部
- 電話:010-62316606-806
- 郵箱:fsfhzy666@163.com
- 腐蝕與防護網官方QQ群:140808414
點擊排行
PPT新聞
“海洋金屬”——鈦合金在艦船的
點擊數:8135
腐蝕與“海上絲綢之路”
點擊數:6475