引言
隨著航天飛行器迫切的減重需求,對應用材料提出了更高的要求,具有優異力學性能的輕質結構材料,尤其是以鋁合金、鎂合金、鈦合金及復合材料等材料為代表的輕質結構材料成為航空航天研究的熱點。目前,國內航天箭體結構系統在輕質結構新材料應用方面完成了部分嘗試和探索。但就現在各材料行業內應用現狀和新材料預先研究結果看,各種材料性能、規格還有大幅提升的需求和潛力。從調研結果來看,技術成熟度還偏低,尚不能滿足全彈結構和未來型號發展的緊迫需求。本文從航天結構發展需求的角度出發,列舉了航天目前需要發展和研究的部分先進輕質結構材料,介紹了各材料發展的現狀,并進一步提出研究和發展的方向。
1 輕質合金結構材料
1.1 超高強鋁合金
不斷提高結構極限承載能力是航天運載器結構設計所追尋的目標,應用高強度材料是必然選擇。從第一代鋁合金到第四代高性能鋁合金在運載火箭上的應用不斷更新替換,鋁合金材料的發展趨勢也是對材料強度要求越來越高。國內以7A04 為代表的第一代,以7A09、7075 為代表的第二代變形鋁合金已得到廣泛應用。以7050 為代表的第三代,以7A60、7055、7056 等第四代高強變形鋁合金仍然處于實驗室或半工業試制階段,還未具備在運載器結構上大范圍工程化應用的條件。
超高強鋁合金主要以7XXX 系鋁合金為主,即Al-Zn-Mg-Cu 系合金。20世紀初至今,國外,主要以美歐等發達國家為主,已先后成功開發出了7X75、7X50/7010、7055/7449、7136/7056 等幾代典型的7XXX 系鋁合金,并在航空航天工業中得到了廣泛的應用[1-2]。20世紀90 年代,美國、英國、日本等工業發達國家,利用先進的噴射成形技術開發了含Zn 8wt% 以上的新一代超高強鋁合金,用于制造交通運輸領域強度高、抗腐蝕性能好的高應力結構件[3]。
國內超高強鋁合金的研究起步較晚,主要以中南大學、東北輕合金有限公司、北京航空航天大學等研究機構為主。部分普通7XXX 系鋁合金在我國已進入實際應用階段, 主要包括7075,7050,7175 等。由江蘇豪然公司開發的噴射擠壓成形7055 鋁合金T6 態抗拉強度最高可達到745 MPa[4],目前還成功研制出抗拉強度800 MPa 級噴射成形超高強鋁合金。
以7055 為代表的7XXX 系超高強鋁合金逐漸成為航天產品應用的翹楚。
7055 鋁合金于20 世紀90 年代研制成功,美國鋁業公司于1993 年申請專利,是Zn 含量超高的新一代鋁合金,據美國軍標記載,其抗拉強度高達648 MPa,是現在應用中使用的最高強度鋁合金。目前美國已將7055 鋁合金板材成功應用于波音777 飛機上翼結構,將型材和鍛件應用于龍骨架、行李軌道和座椅軌道結構。國內江蘇豪然公司將噴射成形材料制備工藝和7055 牌號成分相結合制備出更穩定、更均質的高性能鋁合金。
國內商飛在機翼長桁、某些航天運載器發動機燃燒室殼體、噴管、飛機輪轂等結構中也應用了7055 鋁合金材料,取代了部分30CrMnSiA 及鈦合金產品。
但是,超高強鋁合金因力學性能的大幅度提升造成相應的塑性降低、淬透性差、淬火殘余應力大、機加工難度大等一系列問題。從前期工程化應用的情況來看,后續還需要針對7XXX 系超高強鋁合金開展大量機理性及工藝性研究,系統評價材料成形工藝、熱處理工藝、綜合力學性能、切削加工工藝等,為航天運載器上材料的選用提供依據。
1.2 耐高溫高強鎂合金
鎂合金被譽為“21 世紀綠色金屬結構工程材料”。因其高比強度、高比模量、良好的高溫性能、阻尼減振性能及高性價比、優異的機加工性能越來越受到航空航天的青睞。可以預見,隨著鎂及鎂合金的深入研究,有望取代鋁合金,為航天飛行器的結構減重奠定重要的技術基礎。
目前,鎂合金在航天飛行器上的應用正由簡單的構件向復雜承力耐熱構件跨越,主要應用于火箭、飛機( 包括軍用和民用)、衛星和飛船上比較重要的零部件,這對鎂合金的耐熱高強性能提出了更高的要求。早在20 世紀60 年代,國外在大力神、丘辟特、雷神和北極星等戰略導彈上都曾選用變形鎂合金做結構材料,其中“大力神”Titan 號洲際彈道導彈上用變形鎂合金達900 kg,其蒙皮選用了Mg-Th 系(HK31A、HM21A) 板材、AZ31B 板材。另外,小型導彈上用鎂量更大,如以色列“獵鳥”Falcon 空對空導彈結構件上用鎂量達到90%,其中,導彈殼體由ZK60A 管材和AZ31 板材制備而成,而舵選用了ZK60A 鍛件。在常規武器上,鎂合金也廣泛應用。如:英國大口徑120mm BATL6Wombat 無后座力反坦克炮采用了鎂合金,大大減輕了質量,加上所配的M80.5in 步槍,總重才308kg[5]。美國M274 A1 型軍用吉普車采用了鎂合金車身及橋殼,大大減輕了結構質量,具有良好的機動性及越野性能,4 個士兵可以抬起來[6]。
近年來,隨著新技術的應用,鑄造鎂合金性能也有很大提升,如上海交通大學應用坩堝液態金屬密封技術與精密低壓鑄造技術開發的高溫高強鑄造鎂合金JDM1 和JDM2 取得了成功,但規模較小。國內鎂合金結構件的應用以鑄件為主,軍用方面,如在直徑1 m 以下的戰術艙段、支架及局部結構等;民用方面- 如汽車、3C 產品等。同時變形鎂合金的研究也越來越多,因為變形鎂合金相對鑄造有力學性能好、延伸率大、缺陷少、用途廣等優勢。對于小尺寸結構件,變形鎂合金抗拉強度能達到400MPa 以上,且耐高溫。在航天運載器上的局部結構及支架上正在推廣應用。對于占航天運載器結構主要質量的整體艙段,特別是直徑1 m 以上的大尺寸艙段,變形鎂合金潛力巨大。
但目前耐熱鎂合金在工程化應用方面還面臨一些問題,主要表現在國內的工業化變形鎂合金總體強度水平不高,抗拉強度基本在200~300 MPa,且塑性較差,還不能很好滿足航天發展的需求;小尺寸結構件,變形鎂合金抗拉強度可達到400 MPa 以上,但對于大尺寸結構件,其抗拉強度和延伸率有待進一步提高;高強耐熱變形鎂合金大尺寸鑄錠的熔鑄技術有待進一步提升和發展,成熟的大尺寸鑄錠的缺失影響了變形鎂合金在航空航天中的大規模應用;高強耐熱變形鎂合金的加工成型,特別是大直徑與大變形量結構的成形,雖然有一定的基礎,但是還沒有成熟的技術;鎂合金的表面防護技術已開展較多研究,但對于結構件的全生命周期的防護,特別是有較長貯存期要求的結構件,還有待進一步研究。
1.3 耐高溫高強鈦合金
耐高溫高強鈦合金的研制與應用在世界范圍內都受到了高度重視。早期,高溫鈦合金是指在航空發動機上使用溫度超過350℃以上的無序固溶強化鈦合金。
1954 年,美國成功研制出世界上第一個高溫鈦合金Ti-6Al-4V,奠定了高溫鈦合金研究的基礎。后來美國的艾伯星火箭、阿波羅飛船和發現者衛星均采用了Ti-6Al-4V 合金[7]。之后各國學者研制高溫鈦合金也多是以此為基礎進行的。
從20 世紀50 年代起到80 年代的近40 年,是國外高溫鈦合金的快速發展時期,使用溫度從最初的350℃提高到600 ℃。20 世紀90 年代以后,高溫鈦合金的研究熱點轉向Ti-Al 系金屬間化合物。在此期間,以美、英、俄等為主的航空發達國家均建立了各自相對獨立的高溫鈦合金材料體系,如表1所示[8]。
美國的麥道公司采用快速凝固或粉末冶金技術研制出一種高純度、高致密性的鈦合金,在760℃下的強度相當于目前常溫下使用的鈦合金強度。
我國鈦合金研究起步于20 世紀60年代, 從前期仿制TC4、TC6、TA7、TA11 等低溫鈦合金,到90 年代末,研制出TA12、Ti633G、Ti53311S 等550℃高溫鈦合金,近10 年,又研制具有自主知識產權的600℃至650℃高溫鈦合金Ti60、Ti600、TG6、Ti65 等[9]。就研究成果而言,我國當前已經研究出了一些性能較為優越的合金,但大多耐高溫合金工程化應用水平尚不成熟,未能得到大批量應用。尤其隨著我國航天運載器的發展,耐高溫高強鈦合金的需求日益明顯,為了支撐與促進我國航天的發展,應加快對高溫鈦合金的研究工作。
一方面,盡快完成對已研發高性能鈦合金的材料評價;另一方面,要積極借鑒外國研究者的研究方法,研發更高級別的耐高溫高強鈦合金。
2 輕質復合材料
2.1 高強/高模碳纖維樹脂基復合材料
樹脂基復合材料常用的增強纖維包括碳纖維和其他高性能有機纖維,而目前用得最多和最重要的是碳纖維[10]。以碳纖維為增強體的樹脂基復合材料因其高比強度、高比模量、高溫尺寸穩定性和可設計性等一系列突出的優點,廣泛應用于戰略導彈艙段等彈體結構上,已成為先進導彈結構輕質化不可缺少的關鍵材料。
航天用碳纖維的應用以高強、中模為主,高模也有少量應用。碳纖維復合材料在國外航天領域主要應用在運載火箭、戰略導彈、衛星結構、承力構件等方面。如美國的戰略導彈“侏儒”、“三叉戟”、民兵系列[11],戰術導彈THAAD、ERINT 等在發動機殼體、發動機噴管等部位都有成熟應用[12];同時,日本“M-5”、法國“ 阿里安-2”、“阿里安-5”等火箭發動機殼體上也大量采用碳纖維復合材料[13]。由美國赫克里斯公司生產的IM-7 碳纖維是目前使用量最大的碳纖維[14]。我國各類航天運載器上也大量采用碳纖維復合材料作為殼段結構、主承力構件。目前,已形成T300 級、T700 級、T800 級等約20多個品種[15],廣泛應用于航空航天。
2014 年,據東麗工業公司報道,已開發出一種新型高強高模碳纖維,稱為TORAYCA T1100G;同時開發出了T1100G 高性能預浸料( 樹脂浸漬碳纖維薄板)。東麗利用碳化技術,在納米尺度上精確控制纖維結構。與東麗現有的應用于航空航天中的碳纖維產品如T1000G 和T800S 相比(T-800纖維,拉伸強度5.65 GPa、彈性模量300 GPa),新型的T1100G 性能得到了顯著提高。隨著航天運載火箭對減重增程等戰標的要求不斷提高,對碳纖維,尤其是高強/ 高模碳纖維復合材料提出更高的要求,因此,高性能的碳纖維材料是一個必然的趨勢和發展方向。面對國外的技術封鎖,我國應該從制造工藝、生產成本等方面分步推進,在研發的同時逐步提高碳纖維工程化應用的成熟度。
2.2 耐中高溫樹脂基碳纖維復合材料
樹脂基復合材料的耐溫性主要取決于基體。耐高溫樹脂基復合材料通常指在250~300℃ ( 目前可以提至更高) 內可以長期使用[16-17]。
近年來,先進材料耐溫等級不斷提升,從工程中廣泛應用的耐溫材料來看,從輕質鋁合金、雙馬樹脂基復合材料、鈦合金到聚酰亞胺樹脂基復合材料,耐溫等級依次升高。采用力學性能好、密度小、耐溫等級高、生產工藝相對成熟的耐高溫樹脂基復合材料進行承力結構設計,不僅可以實現承力結構質量的降低,而且可以有效減少熱防護材料的使用,是實現高速飛行器輕質化的有效途徑。
20 世紀50 年代末,美國“北極星A-2”導彈發動機圓柱殼開始采用玻璃/ 環氧纏繞成型,與相應的高強度鋼發動機相比較,在減輕質量與減小脆性方面都有明顯的改進,質量約可減輕50%,射程增大27%[18]。直到20 世紀60 年代末,玻璃纖維/ 環氧復合材料一直是彈道導彈與運載火箭固體火箭發動機圓柱殼的標準材料,應用于“民兵”、“海神”等固體導彈的發動機圓柱殼。
美國潛基戰略導彈“三叉戟”、MX、法國的M-4 和前蘇聯的SS-24、SS-25的發動機圓柱殼設計均采用了芳綸纖維/ 環氧樹脂基復合材料[19],通用動力(General Dynamics) 公司在F-111 水平安定面上首次使用了環氧復合材料,減重達25%,并且通過了靜力、疲勞和地面振動試驗,安全飛行250 h。后來此項設計還應用在了F-14、F-15 上。在航天飛機有效載荷艙門上也采用了石墨/ 環氧復合材料面板夾芯結構,相比于鋁蜂窩結構,質量減輕了410 kg。同時環氧樹脂基復合材料在空間結構如衛星天線、光學結構和桁架結構設計中也占有很大的比例[20]。
隨著航空航天器飛行馬赫數的不斷提高,氣動加熱日趨嚴重。耐中高溫樹脂基復合材料的需求愈顯迫切,并受到越來越多國內外研發機構的重視,樹脂基復合材料的發展趨勢是繼續提高其耐熱性、對高性能樹脂基體改性、研發新型高性能樹脂基體,以滿足運載、導彈武器等飛行器的使用需求。
3 結語
總的來說,目前普通高性能金屬材料仍是航天結構材料的重要組成部分,但其應用已基本接近技術的極限,而高強、耐高溫的輕質金屬結構材料將是未來航天應用和發展的必然趨勢。同時,先進的復合材料在航天中的應用前景廣闊,逐步取代了部分金屬材料,在導彈和航天器結構中所占比例日益增加,提高結構復合材料的耐高溫性能、力學性能,掌握耐高溫樹脂基結構成型技術,降低制造成本,形成具有自主知識產權的結構復合材料體系成為當今航天新材料研究和發展的重點。
航空航天是引領帶動新材料、新工藝發展的主要領域,隨著新材料的出現也給航天飛行器的設計提供了更多的可能和選擇空間。除了上述文中提到的輕質結構材料外,還有許多防熱材料、密封材料、智能材料等功能材料也是航天領域需要擴展的方向。深入開展先進輕質新材料的研究,在新材料研發的同時對新研材料做深入的機理性研究,系統評價新材料的綜合性能,進一步提升新材料的可靠性和成熟度,對于促進新材料的工程化應用和航天的發展具有重要的意義。
參考文獻
[1]WARNER T. R e c e n t l y-de v e l o p e d a l u m i n i umsolutions for aerospace applications[J]. Mater. Sci.Forum., 2006, 519-521 : 1271–1278.Click to displaythe text
[ 2 ] JOHN L . Ad v a n c e d a l u m i n u m a n d h y b r i daerostructures for future aircraft[J]. Mater. Sci.Forum., 2006, 519-521 : 1233–1238.Click to displaythe text
[3] 張永安, 韋強。 噴射成形制備高性能鋁合金材料[J]. 機械工程材料, 2001(4) : 22. Cited By in Cnki (96)
[4] 李先聚, 楊杰, 張豪, 等。 噴射成形7055 鋁合金的顯微組織和力學性能[J]. 中國有色金屬學報, 2007, 17(12): 1987–1992. Cited By in Cnki (25)
[5] 張文毓。 鎂合金及其加工技術研究進展[J]. 稀有金屬快報, 2007(8) : 15–19. Cited By in Cnki (37)
[6] 肖冰, 康鳳, 胡傳凱, 等。 國外輕質結構材料在國防工業中的應用[J]. 兵器材料科學與工程, 2011, 4(11) :94–976. Cited By in Cnki (32)
[7] 任朋立。 高溫鈦合金的應用及其發展前景[J]. 新材料產業, 2014(3) : 56–58. Cited By in Cnki (2)
[8] 王清江, 劉建榮, 楊銳。 高溫鈦合金的現狀與前景[J].航空材料學報, 2014, 34(4) : 1–26. Cited By in Cnki(24)
[9] 侯金健, 高強強, 安曉婷。 國內外高溫鈦合金研究及應用的最新發展[J]. 熱加工工藝, 2014, 43(1) : 11–15.Cited By in Cnki (7)
[10]MAZUMDAR S K.Composites manufacturing:materials,product,and process engineering[M].USA:CRCpress Ltd,2002.
[11] 唐見茂。 碳纖維樹脂基復合材料發展現狀及前景展望[J]. 航天器環境工程, 2010(3) : 269–280. Cited By inCnki (65)
[12] 張曉虎, 孟宇, 張煒。 碳纖維增強復合材料技術發展現狀及趨勢[J]. 纖維復合材料, 2004(1) : 50–53. CitedBy in Cnki (163)
[13] 葛明龍, 田昌義, 孫紀國。 碳纖維增強復合材料在國外液體火箭發動機上的應用[J]. 導彈與航天運載技術,2003(4) : 22–26. Cited By in Cnki (30)
[14] 林德春, 潘鼎, 高健, 等。 碳纖維復合材料在航空航天領域的應用[J]. 玻璃鋼, 2007(1) : 18–28. Cited Byin Cnki (2)
[15] 李國麗, 彭公秋, 王迎芬, 等。 T700 級碳纖維/QY9611 雙馬樹脂復合材料界面性能研究[J]. 航空制造技術, 2014(15) : 93–97. Cited By in Cnki (1)
[16] 黃曉艷, 劉波。 先進樹脂基復合材料在巡航導彈與戰機上的應用[J]. 飛航導彈, 2011(8) : 87–92. Cited Byin Cnki (3)
[17] 劉蘿威, 曹運紅。 高溫樹脂基復合材料在超聲速導彈彈體上的應用[J]. 宇航材料工藝, 2002, 32(5) : 15–19.Cited By in Cnki (17)
[18]LOVELACE, A. M., Advance composites[C].AIAA 10th Annual Meeting and Technical Display,Washington, D. C., January 28-30, 1974.
[19] 宋健朗。 先進聚合物基結構復合材料在導彈和航天中的應用[J]. 工程塑料應用, 2008(7) : 50–54. Cited Byin Cnki (9)
[20]PURDY, D. M., Evolution of new materials forspace applications[C]. Structure, Structural Dynamics& Materials Conference, May 2-4, 1983
免責聲明:本網站所轉載的文字、圖片與視頻資料版權歸原創作者所有,如果涉及侵權,請第一時間聯系本網刪除。
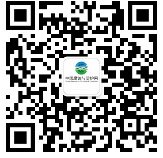
官方微信
《腐蝕與防護網電子期刊》征訂啟事
- 投稿聯系:編輯部
- 電話:010-62316606-806
- 郵箱:fsfhzy666@163.com
- 腐蝕與防護網官方QQ群:140808414