金屬材料 ( 如鋁、鈦、鎂等有色金屬及其合金 ) 因具有不吸濕、尺寸穩定性好、導熱及導電性能優異、耐老化、比強度高、易成型等一系列優異的性能 , 成為了航空航天領域應用最廣泛的材料 , 大量應用于各類航天器的殼體、蒙皮、精細結構件及航天器平臺、骨架結構、工裝等。
航天器及相關裝備投入運行及服役過程中 , 其所處環境惡劣 , 環境過程變化劇烈。據統計 , 航天器發射飛行過程中 , 其外表面往往處于 1000℃以上的高溫 , 而在軌運行中從照射區 (120℃ )到陰影區 (-160℃ ) 的溫度交變過程非???(90min 繞地球一圈為例 ), 除不斷承受宇宙射線的輻照外 , 其返回地面時還需經歷大于 2000℃的高溫灼燒。有資料顯示“挑戰者號”發射入軌時的速率超過 27000km·h -1 , 頭錐前沿溫度達到 1370℃ ; 美國 NASP 空天飛機 X-30高速飛行時其表面任何區域溫度都不低于 650℃ , 頭錐至尾部溫度由 1793℃至871℃迅速降低 , 發動機整流罩溫度始終保持在 982℃以上。目前這些溫度均已超過了大部分現有航天材料的耐溫極限。還有一些裝備 ( 如導彈等飛行器 )常會從腐蝕環境惡劣的海上航母或水下潛艇中發射 , 這類嚴酷的服役環境也會對航天器的安全使用壽命造成影響。以上這些不利因素都對航天產品所用的各類金屬材料提出了嚴苛要求。將這類材料進行一定的表面處理 , 提高材料的安全性和適應性、降低腐蝕速率、延長使用壽命 , 或賦予材料其他特殊功能是相關金屬材料研究領域的一個重要方向。
筆者主要對航天材料表面處理技術的研究進展和發展趨勢進行了綜述。
1 航天材料表面處理技術的研究進展航天用材料表面處理技術的根本任務是通過表面處理使材料形成新的表面 , 以增強材料的使用性能或賦予材料新的功能。通常的表面處理方法主要有:
陽極氧化、微弧氧化、電鍍、熱噴涂、氣相沉積以及高能束處理。
1.1 陽極氧化陽極氧化 (AnodicOxidation) 是指以被處理金屬材料為陽極 , 在電解質溶液和外施陽極電流的共同作用下 , 利用電解作用在金屬材料表面生成一層金屬氧化膜保護層的表面處理技術。材料的表面狀態因金屬氧化膜的形成而改變 , 金屬氧化膜的存在使得材料表面著色性增強、耐腐蝕性提高、耐磨性增強、硬度增加 , 并對材料表面起到保護作用。鋁及其合金材料通常采用陽極氧化處理生成氧化鋁保護膜進行表面防護。氧化鋁保護膜使得鋁或鋁合金的表面狀態和性能被改變 , 起著增強表面著色和耐腐蝕性能、提高耐磨性能和硬度、保護零部件表面等作用。
在鋁合金陽極氧化處理應用方面 ,趙啟龍等人采用陽極氧化處理結合鍍金處理的方法 , 研究了航天器鋁合金部件分離面的物理嵌合機理。研究結果表明:
在光亮陽極氧化的鋁合金與光亮鍍金的鋁合金配對時 , 由于光亮陽極氧化增加了鋁合金的表面硬度 , 降低了表面粗糙度 , 從而可以有效防止航天器鋁合金部件分離面的物理嵌合 , 保證了分離部件的有效分離過程。
其他有色金屬或合金 ( 如鎂合金、鈦合金等 ) 為了增強其表面性能 , 均可進行陽極氧化處理。章玨等人在對GWK(Mg-7Gd-4Y-0.5Zr) 鎂合金進行陽極氧化處理的過程中 , 對電解液的配方及陽極氧化工藝進行陽極氧化處理的過程中 , 對電解液的配方及陽極氧化工藝進行了優化研究 , 得到了厚度為16μm 左右的氧化膜 , 其主要由鎂、氧、硅3種元素組成,并且氧化膜表面平整,致密性好 , 與基體結合力強 , 耐腐蝕性優異。
表面陽極氧化處理的另外一個應用就是降低電偶腐蝕。電偶腐蝕是鈦合金在與其他金屬配對使用時所遇到的難題。研究表明 : 陽極氧化處理的鈦合金和鋁合金 , 其電偶腐蝕敏感性明顯降低 ; 將鈦合金陽極氧化 , 而將鋼進行電鍍鎘 - 鈦處理可將電偶腐蝕敏感性降低到極低的程度。
1.2 微弧氧化微弧氧化 (Micro-ArcOxidation), 又稱等離子氧化 , 它是在鋁、鎂、鈦、鈮、鋯等有色金屬及其合金的表面利用微弧區瞬間高溫燒結作用 , 原位生長出陶瓷質氧化膜保護層的表面處理技術。微弧氧化克服了陽極氧化的一些不足 , 其生成的陶瓷氧化膜具有與基體結合力強、硬度及強度高、絕緣性好、耐磨、耐腐蝕、耐高溫等特點 , 而且工藝簡單、易操作、處理效率高 , 是近幾年材料表面處理的研究熱點之一 , 并在航天航空領域得到越來越多的應用與發展。
鋁合金經過微弧氧化處理之后,其表面原位生長的陶瓷膜厚度可達到200~300μm( 是傳統陽極氧化膜的數十倍 ), 顯 微 硬 可 達 到 1500~2500HV( 遠高于傳統陽極氧化膜的 ), 該陶瓷氧化膜由 γ-Al 2 O 3 和 α-Al 2 O 3 共同構成。
與硬質合金相比 , 所得的陶瓷氧化膜具有較高的耐磨性和較小的摩擦因數 ; 而且 , 對鋁合金進行微弧氧化處理后 , 可明顯提高其耐蝕性 , 其腐蝕速率比不銹鋼的要小得多。
微弧氧化處理技術當前的研究熱點主要集中于膜層性能、復合處理等方面。
在電解液中添加不同的陶瓷微?;蛱砑觿?, 可使所得到的富含硬質顆粒的陶瓷氧化膜的性能進一步提高。LEE 等人在對鎂合金進行表面微弧氧化處理時 , 將ZrO 2 納米粒子加入到電解液中 , 得到的復合陶瓷膜耐腐蝕性能優異。SARBISHEI等人對鈦合金進行表面微弧氧化處理時 , 在電解液中加入氧化鋁顆粒得到懸浮液 , 經過微弧氧化后 , 所得到的鈦合金表面復合陶瓷膜的孔隙率大幅降低 ,因此使得耐腐蝕性能提高。李玉海等人對 TC4 鈦合金進行表面微弧氧化處理過程中 , 在電解液中加入了兩種陶瓷顆粒(SiC 和 SiO 2 ), 經過微弧氧化處理后 , 在其表面得到復合陶瓷膜。研究結果表明:
在電解液中添加陶瓷顆粒能使膜層表面變得致密平整且膜層的厚度增加 ; 陶瓷顆粒能夠進入到氧化層中 , 但并不發生相變反應 ; 陶瓷顆粒的加入使得復合陶瓷膜的耐磨性能顯著提高。
微弧氧化處理過程中稀土的作用也是研究的一個熱點。加入稀土元素 , 可使陶瓷質氧化膜的致密性、韌性、燒結性能等得到提高和改善。馬躍宇等人深入研究了稀土對鎂合金微弧氧化的作用 , 結果表明 , 稀土對鎂合金微弧氧化具有明顯的促進作用。這是因為:其一,稀土氧化物的存在鈍化了金屬陽極 , 使得起弧電壓和電流密度等參數降低 ; 其二 , 稀土元素的引入 , 使得 Mg 2+ 從鎂合金內部向膜層表面的轉移速度得到提高 , 增加了微弧氧化層外層的鎂元素含量 , 明顯提高了膜層厚度和氧化層的均勻性 , 降低了微弧氧化陶瓷層的孔隙率 , 提高了致密性 , 增加了處理表面的平整度 , 而且基體金屬與微弧氧化層之間緊密結合 , 從而提高了材料表面的耐腐蝕性能和耐磨性能。
微弧氧化與其他許多材料表面改性或涂覆技術相比具有很多優越性 ,勢必將成為今后材料表面處理重要的發展趨勢。
1.3 電鍍電鍍 (Electroplating) 是指借助外界電流的作用 , 在溶液中進行電化學反應使得導電體的表面沉積一層金屬或合金。電鍍能夠處理結構復雜的器件表面 , 因此廣泛應用于航天航空相關材料的表面防護。通過電鍍可以在航天用金屬材料的表面形成鎢合金層 ,其可承受 2000℃以上的高溫。其他特殊功能的鍍層也可以通過電鍍技術實現。隨著航空工業的發展 , 電鍍技術也得到了新的發展。
為了適應航空航天的快速發展 , 擴展鈦合金在航空航天工業中的應用范圍 , 劉洪濤等人研究了 Ti6A14V 鈦合金鍍鎳在航空航天材料應用中的可行性。研究結果表明 , 在 Ti6A14V 鈦合金表面施鍍鎳層不但鍍鎳層與基體之間具有良好的結合力 ( 結合強度達到了232MPa), 而且能極大提高鈦合金的表面性能 ( 表面硬度達 527HV0.1)。這不僅使鈦合金表面抗咬合、抗劃傷、抗磨損等性能提高 , 而且因為鈦合金具有比強度高、耐蝕性好等特點 , 因此電鍍鎳處理將使鈦合金在航空航天工業中發揮更重要的作用。
氰化電鍍鎘工藝制備的鍍層性能優異 , 航空航天等領域的零部件常采用氰化電鍍鎘來制備鍍層進行防護。氰化物是環境污染物之一 , 電鍍技術發展到現在 , 無氰鍍鋅、無氰鍍銅、無氰鍍金及無氰鍍銀等工藝已經很成熟 , 無氰鍍鎘工藝研究成為電鍍行業內的又一研究熱點。陳建銳等人針對含乙二胺四乙酸(EDTA) 的無氰鍍鎘工藝存在的缺點 ,開發出了適用于航空航天設備零部件的無氰酸性鍍鎘工藝。應用結果表明 , 該工藝所得到的無氰鍍鎘層 , 按照航空航天工業部標準的要求 , 其各項性能均能達到要求 , 而且在鍍層的耐腐蝕性方面也有了較大的進步 , 使得航空航天零部件的使用壽命明顯延長。
脈沖電鍍是近幾十年發展起來的一種新型表面處理技術 , 其可使電鍍層的結合力提高、孔隙率降低。在鍍鉻方面 ,近年來脈沖電鍍鉻技術已成為國際上研究的熱點。脈沖電鍍鉻可使鍍層裂紋尺寸減小、數量減少 , 鍍層的結晶更加致密 ; 雙向脈沖電鍍鉻則可得到特殊的多層納米晶鉻鍍層結構 , 使裂紋尺寸及數量進一步降低、耐腐蝕性能明顯增加 ,鍍層應力減小。就鍍銅而言 , 致密銅鍍層是阻止碳、氮等元素滲入的有效保障,在航空發動機中通常采用局部鍍銅工藝在器件表面得到銅鍍層以防止碳或氮元素的滲入。李晗曄等人為了解決航空發動機部件在直流鍍銅過程中存在鍍層過厚、結合力差等問題 , 通過研究確定了具有良好零件防滲作用的脈沖鍍銅工藝。所得的脈沖鍍銅層厚度由 50~70μm下降到了 20μm, 鍍銅的成本降低了 ,而鍍覆的效率則提高了。就性能方面 ,與直流鍍銅層相比 , 脈沖鍍銅層在表面形貌、孔隙率以及結合力等方面都有明顯改善。
電鍍硬鉻工藝已廣泛應用于航天產品結構件中 , 能顯著提高器件表面硬度、耐腐蝕性。在電鍍硬鉻過程中 ,會反應產生氫化鉻 (CrH 或 CrH 2 ), 氫化鉻的存在會使得鉻鍍層內部產生裂紋而導致耐腐蝕性能降低。這個缺點在飛機起落架緩沖器上會導致起落架出現滲、漏氣 ( 油 ) 的現象 , 為了解決該問題 , 通常利用硬質粒子摩擦作用 ,在電鍍過程中形成組織致密鉻層 , 使得鉻鍍層氣密性提高。鄧云等人提出了柔性摩擦輔助電鍍鉻技術 , 即引入柔性摩擦介質 , 在電鍍鉻過程中降低陰極析氫的影響 , 提高鉻鍍層的致密性 , 使硬鉻鍍層的氣密性問題得到解決。熊俊等人對某航空器用活塞桿內筒尺寸修復的鍍鉻工藝進行了研究 ,通過充分的分析 , 設計了專門的修復工裝 , 確定了匹配的鍍鉻工藝參數。
結果表明 : 該工裝和鍍鉻工藝參數匹配良好 , 不僅修復后的活塞桿內筒尺寸滿足技術要求 , 而且鍍層表面均勻、光滑 , 可重新用于航空器。
除了電鍍技術本身的進展外 , 有關電鍍產生的廢水、重金屬污染等環保問題 , 相關研究也有了很大的進步。相信在所有相關技術人員的不懈努力下 , 電鍍相關技術在航空航天領域具有更加廣闊的應用空間。
1.4 熱噴涂熱噴涂 (ThermalSpraying) 是表面工程領域中的一項重要技術 , 其過程是首先將噴涂材料加熱 , 使其達到熔化或半熔化狀態 , 然后通過特定設備以一定速率噴射沉積到預處理的表面上從而生成一定厚度的涂層。利用熱噴涂的方法可以得到具有特定功能的表面涂層 , 如 :
熱障、耐磨密封、抗高溫氧化、導電絕緣、抗遠紅外輻射等。熱噴涂技術具有所用材料種類多 , 如金屬、金屬合金、陶瓷、金屬陶瓷、塑料以及復合材料等 , 工作效率高和成本低等優點 , 隨著航天工業的空前發展 , 熱噴涂技術在航天產品的各類零部件中得到了廣泛的應用。我國的載人航天器中就有一部分部件采用熱噴涂技術形成的熱障涂層 , 像在飛船逃逸系統中 , 其中的柵格翼就采用等離子噴涂的 Al 2 O 3 熱障涂層 ; 長征 3 號火箭氫氧發動機渦輪泵動密封結構采用等離子噴涂 Cr 2 O 3 涂層達到其使用要求。
碳纖維增強型 C/C 復合材料廣泛應用于航空航天產品中的零部件 , 如火箭發動機、機翼邊沿、螺旋槳葉片導邊、葉輪葉片等部位。但是 C/C 復合材料在超過 450℃的高速含氧氣流下 , 會產生嚴重的氧化燒蝕剝離。LI 等人為使 C/C 復合材料在高溫下不被氧化而破壞 ,將 C/C 復合材料置于氬氣氛中 , 使用兩步包埋法在其表面噴涂得到了 Mo-Si-Al-C 復合涂層 , 并進行了一系列表征 :X 射線衍射結果表明 , 復合涂層是 由 SiC,Mo(Si,Al) 2 ,MoSi 2 ,Al4Mo 3 Si 2等共同組成 ; 恒溫絕熱試驗結果表明 , 所得的 Mo-Si-Al-C 復合涂層在1773K 條件下絕熱氧化 510h, 其質量損失率僅為 0.409%; 循環氧化結果表明 , 從常溫加熱至 1773K 往復循環25 次后 , 復合涂層的質量損失率僅為1.217%, 這表明復合涂層具有良好的抗高溫氧化作用……雷達吸波涂層制備也是熱噴涂技術近年來的研究重點和熱點。技術人員對于各類吸波材料 , 如鐵氧體、碳系材料、碳化硅、金屬微粉、導電陶瓷等 , 通過熱噴涂技術制備相關雷達吸波涂層均有了較詳盡的研究 , 不僅在涂層吸波性能調控方面取得了一定的突破 , 而且對熱噴涂技術工藝的進步與改進也有一定的推動作用。WEI 等人對 ZnO/Al 2 O 3 涂層在熱噴涂過程中的退火工藝 ( 退火溫度和退火氣氛 ) 對介電性能的影響進行了研究 , 發現當在空氣中進行退火時 , 所得涂層復介電常數的實部和虛部都明顯下降 ; 而當在真空中進行退火時 , 所得涂層的復介電常數表現出增加的趨勢。對于工藝調控而言 , 韋萍等人研究了 ZnO/Al 2 O 3 涂層制備時喂料工藝對涂層介電性能的影響 , 結果表明在等離子噴涂制備 ZnO/Al 2 O 3涂層的過程中 , 控制喂料也可有效調節所得涂層的復介電常數。
1.5 氣相沉積氣 相 沉 積 (VaporDeposition) 是最近 20 多年來發展起來的一表面處理技術 , 可以劃分為化學氣相沉積(ChemicalVaporDeposition,CVD) 和 物 理氣相沉積 (PhysicalVaporDeposition,PVD)兩類。化學氣相沉積方法又包括常規化學氣相沉積、等離子體強化化學氣相沉積、等離子體輔助化學氣相沉積、激光化學氣相沉積、金屬有機化合物化學氣相沉積等方法 ; 物理氣相沉積方法則包括真空蒸鍍、濺射、離子鍍和離子注入等方法。
氣相沉積技術因具有涂層材料種類多、沉積速度快、在材料表面附著性好、所得涂層致密性好、不污染環境等優點而備受關注 , 采用該技術可改善材料及零部件表面的耐磨性、耐腐蝕性以及抗氧化性等。
近年來 , 對物理氣相沉積在航空航天零部件中的應用研究有了較大的進展。孫德恩等人對物理氣相沉積在航空發動機的壓氣機葉片表面抗固體粒子沖蝕涂層的應用研究進展進行了比較詳盡的綜述 , 認為在大功角的情況下 , 提高葉片沉積涂層的韌性是提高抗沖蝕能力的關鍵 , 而采用物理沉積的方法在壓氣機葉片表面沉積得到多元納米復合涂層和多層膜結構是提高涂層韌性進而提高涂層抗固體粒子沖蝕能力的有效手段。
彭徽等人對近幾年等離子體輔助電子束物理氣相沉積技術在制備航空發動機熱防護涂層上的應用研究進展進行了綜述 , 在此基礎上 , 采用相應的電子束物理氣相沉積技術成功制備得到了氧化釔穩定的氧化鋯 (YSZ) 熱障涂層 , 并采用等離子體輔助沉積技術對 YSZ 涂層進行了結構改性 , 使得 YSZ 涂層增強了抵抗外來物沖蝕及硅鎂鋁酸鹽 (CMAS) 侵蝕的能力。王喜忠等人以電子束物理氣相沉積 (EBPVD) 為手段 , 制備得到一種由La 2 Ce 2 O 7 /8YSZ(YSZ 中氧化釔的物質的量分數為 8%) 構成的熱障涂層 , 該熱障涂層的壽命比 8YSZ 熱障涂層的延長了 30%, 而且比 La 2 Ce 2 O 7 熱障涂層的壽命增加了 5 倍。La 2 Ce 2 O 7 陶瓷涂層在海水和航空煤油的熱腐蝕環境下于 950℃曝露 100h 后 , 涂層未發生分解和相變 ,顯示了良好的抗燃氣熱腐蝕性能。
化學氣相沉積技術在航天設備 ( 特別是微電子芯片和微波元器件等 ) 中也經常被應用 , 其所采用的原材料通常為氮化硅、二氧化硅、碳纖維以及碳納米纖維等。王少龍采用低壓化學氣相沉積技術 (LPCVD) 在 C/C 復合材料和碳纖維表面分別制備了 SiC 和 ZrC 涂層 , 探討了影響涂層微觀結構的主要因素 ; 同時還利用氧乙炔焰 , 研究了該涂層的抗燒蝕性能和燒蝕機理 ; 在 C/C 復合材料表面分別制備得到了 SiC/ZrC 復合涂層以及 SiC/ZrC/SiC 復合涂層 , 利用各種涂層的不同特點 , 增強了 C/C 復合材料的抗燒蝕性能 , 擴展了 C/C 復合材料在航空航天領域的應用范圍。
1.6 其他表面處理技術近年來隨著科學技術的發展 , 也形成了一些材料表面處理新技術 , 例如電子束、等離子束、激光束等高能束表面處理技術就是其中的一類。高能束表面處理技術具有表面加熱及冷卻速度快、元素直接注入材料表面等特點 , 其改變了材料表面的物理結構或化學組分 , 從而可明顯提高材料的性能。當前 , 因等離子表面處理技術所具有的獨特優勢而使其受到材料表面科學領域的廣泛關注 , 成為了該領域的研究熱點。圖 1a)是按照文獻顯示的電極電壓 / 電流特征曲線 , 結合筆者試驗繪制的等離子電解處理時電流 - 電壓曲線及各個階段的現象圖。利用等離子電解滲碳技術對 Q235 鋼進行表面處理后 , 得到的滲層組織主要由馬氏體和奧氏體組成 , 材料表面硬度和強度都有大幅度提高。表面處理后 Q235鋼表面硬度可達到 779HV( 基體僅 170HV 左右 ), 因此可使得航天產品組件的表面具有高的硬度和良好的耐磨性 , 而心部則具有優良的塑性、韌性 , 滲碳器件剖面顯微組織形貌見圖 1b)。此外 , 等離子電解處理后材料表面粗糙度明顯變大 ( 由 0.05μm變為 0.3μm 左右 ), 這是因為等離子電解處理后滲層致密結構外部表層會呈現一層較薄的疏松多孔結構。這種結構可吸收、存貯潤滑油 , 應用在航天器件的一些動結構中能使其獲得較好的耐磨性。
隨著科學技術的發展,航天航空部件的材料表面處理技術也在不斷進步和完善。
采用兩種及兩種以上的表面處理技術對材料表面進行防護處理 , 已經逐漸被采用。
例如 , 王棟開發了一種 SiO 2 溶膠封孔劑 , 對等離子噴涂 NiCr-Cr 3 C 2 涂層采用溶膠 -凝膠技術進行封孔處理 , 提高了該涂層的致密性 , 并增加了涂層與基體的結合強。
2 航天材料表面處理技術的發展趨勢隨著科學技術的飛速發展 , 航空航天設備用材料表面處理技術正朝向高效化、低能耗、高性能化方向發展、具體而言 , 航空航天用材料表面處理技術將朝以下幾個方向發展。
(1) 表面處理所用涂層材料的研究與開發 , 包括新材料的開發和原有材料的性能改進。
(2) 適用于航空航天工業的新的表面處理技術的研究與開發。科學技術不斷進步 , 新的表面處理技術也層出不窮 , 努力開發適用于航空航天工業的表面處理新技術是促進航空工業發展的必要手段。
(3) 改善和提高現有航空航天用材料的表面處理技術。在研究成膜技術、涂層技術、熱表處理等表面處理工藝技術的同時 , 利用各種在線監測技術確定表面處理時材料表面的動力學特征、溫度場、速度場等因素 , 深入分析處理層的形成過程 ,從而提高處理的表面層的性能。
(4) 表面處理效果的評定。對于航天用材料表面處理的各種現行工藝方法 , 目前還沒有出現較為科學、量化的效果評定方法及相關研究。對航天器材料膜層力學性能 ( 包括顯微硬度、屈服強度、殘余應力、韌性等 ) 建立科學量化的工藝優化評定指標體系 , 將對材料表面處理工藝技術的發展起到有效的指導作用。
免責聲明:本網站所轉載的文字、圖片與視頻資料版權歸原創作者所有,如果涉及侵權,請第一時間聯系本網刪除。
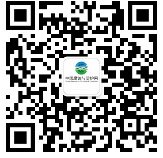
官方微信
《腐蝕與防護網電子期刊》征訂啟事
- 投稿聯系:編輯部
- 電話:010-62316606-806
- 郵箱:fsfhzy666@163.com
- 腐蝕與防護網官方QQ群:140808414