航空工業的發展對飛行器服役性能提出了更高的要求,期望航空發動機具有更好的動力性、安全性及經濟性。作為目前航空發動機渦輪葉片的首選材料,鎳基單晶高溫合金的最高工作溫度約為1 000 ℃,不能滿足航空發動機使用要求,需迫切提高其耐溫性。
熱障涂層(thermal barrier coatings, TBCs)是涂覆在渦輪葉片上的一種防護陶瓷材料,該材料具有低熱導率、高熔點、高溫相結構和穩定化學性等特點,是航空發動機制造的核心技術[1]。該技術最早由美國NASA-Lewis研究中心在20世紀50年代提出,經過30余年的研究后取得較大突破,CaO-ZrO2熱障涂層首次應用于X-15飛行器,成功使飛行速度提高到6.72馬赫及108 km升限[2]。在此基礎上,研究人員對穩定劑進行了進一步探索,Y2O3綜合性能優異,由其穩定后的ZrO2涂層在航空發動機中得到了大量應用,成為了現代熱障涂層技術開端的標志。Y2O3-ZrO2(YSZ)除了具有熔點高、熱導率低、性能穩定共同特點外,而且孔隙率高、強度高、韌性好,因而被譽為“陶瓷鋼”。w(Y2O3)為6%~8%部分穩定ZrO2(6-8YSZ)涂層是目前最廣泛的熱障涂層材料[3]。
雖然YSZ具有很多優勢,但YSZ在高溫(1 200 ℃以上)時易發生相變引發體積膨脹導致裂紋,同時因高溫燒結降低孔隙率,從而引起應變容限降低、隔熱效果變差、涂層失效加速。因此研究人員開展了 YSZ摻雜改性研究,并探討了燒綠石結構A2B2O7型化合物、鈣鈦礦結構及高熵陶瓷材料。此外通過選擇合適的制備方式及后處理技術,也可進一步提高熱障涂層的可靠性與耐久性。且隨著光譜測量技術、圖像處理技術及有限元模擬等先進技術的發展,基于多種熱力學實驗結論和斷裂力學、損傷力學等理論,TBCs的失效機制逐漸揭開了神秘面紗,通過模擬技術和實驗手段的有效結合,對界面間的相互作用實現了定量表征,為熱障涂層的失效分析及壽命預測指明了方向[4,5]。
本文主要從熱障涂層結構、材料分類、制備及后處理技術、失效機制四個方面對目前研究現狀進行了綜述,并展望了熱障涂層未來的研究趨勢,以期為熱障涂層的研究提供參考。
目前,TBCs常用的結構主要包括雙層、多層及梯度結構,具體見表1。
熱障涂層材料主要集中在陶瓷層材料和粘接層材料兩方面。
2.1 熱障涂層-陶瓷層材料
熱障涂層-陶瓷層材料的研究主要從 YSZ摻雜改性、A2B2O7型化合物、鈣鈦礦結構及高熵陶瓷材料四個方面展開。
(1)YSZ摻雜改性
根據摻雜元素種類分為單元素和多元素摻雜,見表2。單元素摻雜主要主要以稀土元素R(R 為 La→Lu,Sc,Gd)摻雜改性為主,當Sc3+到Y3+離子半徑的逐漸增大時,穩定性提高;而當Y3+到La3+離子半徑的繼續增大時,穩定性降低。此外也有非稀土元素如Al、Hf、Ta等元素作為摻雜穩定劑改性。
多元素共摻雜會使陶瓷材料性能更加優越,如相穩定性和抗燒結性提高、熱導率降低,因此多元素共摻雜是YSZ改性研究的重點。不過摻雜元素離子的半徑大小、價位高低及含量多少等均會對其產生影響,且受材料本身的限制,摻雜對提升其綜合性能已接近極限。
(2)A2B2O7型化合物
A2B2O7(A = La / Nd / Sm/ Gd / Dy / Er/ Yb 等稀土元素,B =Ce、Zr 等)型氧化物耐熱性強、高溫相穩定性好,且 A、B、O 種類多,為熱障涂層提供了多種選擇。表3為不同A2B2O7結構的熱導率和熱膨脹系數,與YSZ對比,因熱導率明顯下降而成為研究熱點,但熱膨脹系數變化不大且匹配性能較差限制了其應用。
A2B2O7結構示意圖如圖1,根據A、B離子半徑之比和
分為螢石和燒綠石結構[17,18],均是面心立方,螢石結構中B4+、A3+隨機分布在格點位置,與8個O2-配位,其中O2-位于(1/8,1/8,1/8)格點,易產生空位缺陷,可通過單元素、多元素摻雜產生晶格缺陷,聲子散射加強,平均自由程降低、晶格振動減弱從而降低熱導率。
KHAN等[19]對La2Zr2O7進行Gd摻雜,圖2為La2Zr2O7體系熱導率曲線。可以看出,隨Gd濃度的增大,熱導率下降。與此同時摻雜導致原子振動不調和及鍵長的改變導致晶體的結合能變小,熱膨脹系數變大,KEYVANI等[20]在1 000 ℃測得的熱膨脹系數,如圖3所示。得(La0.8Gd0.2)2Zr2O7高溫時熱膨脹系數明顯較大,因此可通過單元素、多元素摻雜A2B2O7結構可更好地滿足航空發動機的需求。
(3)鈣鈦礦結構
鈣鈦礦結構材料為ABO3(A= La / Ba / Ca等,B=Sc、Cr等)型結構,因高溫時性能穩定、熱導率低等優良性能,可作為潛在的新型熱障涂層候選材料。在ABO3化合物中,A-O鍵比B-O鍵弱,且A、B兩種原子吸引電子的能力越接近,理論上熱導率越低,抗損傷能力越好[21,22]。EJAZ等[23]表明1 273 K時,CaZrO3的熱膨脹系數為12.4×10-6 K-1,而YSZ的熱膨脹系數為10.2×10-6 K-1,CaZrO3熱膨脹系數較高、導熱系數較低、高溫相穩定性能好。馬伯樂等[24]在1 600 ℃時測得SrZrO3 在100 h~360 h之間的熱導率逐漸下降、熱穩定性能好,如圖4所示。此外,通過摻雜稀土元素Yb、Y等,可獲得具有柱狀、多孔的復合鈣鈦礦涂層,可承受高熱應力及二次相形成引起的應力,顯著提高了涂層的熱循環壽命。MA等[25]在SrZrO3中摻雜Yb2O3和 Y2O3后得到Sr(Zr0.9Y0.05Yb0.05)O2.95,在室溫到1 400 ℃及1450℃以上均表現出良好的相穩定性,且熱導率在全溫范圍內比SrZrO3下降了30%。整體而言,ABO3的導熱系數較低,通過摻雜引起結構變化還可使導熱系數降低。
(4)高熵陶瓷材料
高熵陶瓷材料是單相陶瓷體系,由多主元高熵合金化設計。通常按相同物質量將五種以上的金屬離子合成多組元固溶體。因其成分特點,具有熱力學高熵、晶格畸變、遲滯擴散及性能“雞尾酒”四種核心效應,使該材料硬度高、韌性強、熱導率低,應用前景廣泛。高熵陶瓷材料體系以稀土元素為主,因性質相近,易形成穩定的單相固溶體,便于性能優化。高熵陶瓷材料的研究主要集中在以下6類:稀土鉭酸鹽、硅酸鹽、鋁酸鹽、鋯/鉿酸鹽、磷酸鹽、氧化物,其性能參數對比見圖5[26]。比較發現,鋯酸鹽的熱導率最好而鋁酸鹽最差;斷裂韌性方面,高熵稀土氧化物有明顯優勢[27]。大多數高熵陶瓷材料熱導率低、高溫相穩定性好、抗燒結性強,但針對各自劣勢,仍需進行改進。
2.2 熱障涂層-粘接層材料
熱障涂層中粘結層的效果包括兩種,一是在其表面形成Al2O3阻氧層,提升高溫環境下基體葉片的抗氧化、抗腐蝕性;二是作為中間層有隔熱作用,避免上層陶瓷材料和基體高溫合金材料因熱膨脹系數匹配不高而導致熱失配。
(1)MCrAlY合金材料
MCrAlY合金(M為Fe、Co、Ni或Ni+Co)廣泛應用于抗氧化防護涂層及TBCs粘接層,與鎳基體高溫合金界面結合能力良好。其中,鋁的質量分數通常為8%~12%,在工作過程中與空氣中的O2反應生成具有抗氧化能力的Al2O3層;Cr質量分數一般為20%以上,主要作用是促進Al2O3的快速形成并提升抗熱腐蝕能力;Co則能夠改善界面結合性;少量稀土元素Y可具有氧化物釘扎和細化晶粒的作用,防止黏結層中氧化層生成過多,間接提高其抗氧化性[28]。
Re、Hf、Ce 和 Zr 等元素的摻雜會進一步提高MCrAlY合金黏接層的熱腐蝕和抗氧化性能。Re通過抑制NiAl2O4和 NiCr2O4等的生成,提高涂層的抗氧化能力;Hf通過加快α-Al2O3的生成速度及形成結構穩定的HfO2,延長熱循環使用時間;CeO2和 Al2O3通過加快α-Al2O3的生成速度,降低涂層氧化的增重[29]。
綜上所述,MCrAlY 及其摻雜材料具有良好的抗熱腐蝕和抗氧化能力,但后者隨著溫度的升高而下降。
(2)NiAl 合金材料
NiAl 合金粘結材料具有高熔點(1 638 ℃)、低密度(5.9 g/cm3)、強抗氧化能力,溫度高于1200℃時能形成氧化膜,且與陶瓷層的結合強度良好,應用前景廣泛,也可通過其他元素摻雜以提高其性能。NiAl涂層中加入 Pt 形成 NiPtAl 涂層,有助于使其組織穩定性提高,與基體的擴散減少,一定程度上減少涂層與部分元素(如S和C)的反應,延長粘接層的壽命,其最佳Pt含量與合金基體種類有關;Hf的摻雜有助于改善抗熱循環性利用Hf的“阻擋效應”抑制Al的擴散,降低了TGO的增長速率;Zr改性后可顯著降低涂層界面上孔洞的形成率同時提高涂層的多項力學性能[30,31]。
NiAl合金性能提升主要通過摻雜Pt、Hf等元素實現。后續可通過第一性原理來尋找新的材料進行摻雜改性提高涂層室溫下斷裂韌性和延性[32],并通過工藝及結構體系的優化提升粘接層的綜合性能,如選擇合適的后處理方式,采用功能梯度粘接層等。
3.1熱障涂層制備方式
TBCs的制備方式很多,各有優缺點,主要包括等離子噴涂(APS)、電子束-物理氣相沉積(EB-PVD)和在二者基礎上發展的新技術等離子噴涂-物理氣相沉積(PS-PVD)。
APS的工作原理是等離子噴槍在噴嘴處產生高頻電弧,引燃高溫高速的大氣等離子火焰,粉末被加熱到熔融狀態,以片狀結構高速沉積在基底表面,沉積效率高,與基底的兼容性好,成本低。EB-PVD的工作原理是高能電子束將涂層粉末塊體加熱至表面熔化,在真空條件下,氣化的粉末通過直線路徑運動到工件表面沉積為涂層[33,34],沉積效率低。CALIEZ等[35]制備的TBC截面的微觀結構如圖6a、b所示。結果顯示,APS得到的涂層為典型的層狀結構,存在孔隙和裂紋,抗震性較差,熱導率約為1~1.2W/(m·K),通常用于制備性能要求較低的靜子件(如噴管涂層)。EB-PVD得到的涂層結構為柱狀晶,柱狀晶的間隙增加了涂層的應變空間,降低了頂層的內部應力[36],熱導率約為1.5~2.0 W/(m·K),提高了熱導率及高溫壽命,通常用來制備服役環境要求高的動部件(如渦輪葉片涂層)。
因APS抗震性差和EB-PVD熱導率高,在兩者的基礎上發展了的新技術PS-PVD,該技術具有更低的工作壓力、更高的噴槍功率及沉積效率,VON等[37]給出如圖4c顯示的PS-PVD微觀截面圖,該涂層結構是羽-柱狀,因存在缺陷及孔隙,可通過聲子散射使熱導率更低,壽命更長,隔熱效果介于APS和EB-PVD之間,這種性能綜合的涂層是后續研究重點。
3.2 熱障涂層后處理技術
為了提高熱障涂層的綜合性能,使航空發動機服役時安全可靠,國內外進行了熱障涂層后處理技術研究。該技術可改變涂層的結構或組成成分,節約成本,滿足高端領域對涂層性能的各種要求。熱障涂層后處理技術主要有真空熱處理(VHT)、熱等靜壓處理(HIP)、激光重熔、激光上釉和激光熔覆[38]。
VHT在真空中操作,實現了制作過程無氧化、無滲碳,優化工件缺陷、脫脂除氣,研究表明溫度為主要影響因素,決定了涂層的相對密度。圖7為在780、870、960、1 050 ℃不同溫度下經過VHT的NiCrAlYSi微觀結構圖[39]。可見隨著溫度的升高,孔隙變多變大,因此應選取最佳溫度進行真空熱處理。一方面,涂層界面的氧化膜抑制了熱生長,減少了裂紋,延長了壽命;另一方面,涂層內部的氧化物降低了熱膨脹系數,減少了因熱膨脹引起的應力開裂,涂層的綜合性能提高。
HIP在高溫、高壓、密閉容器操作,將制品加熱到高溫且各向施加相同的壓力燒結和致密,溫度通常為1 000~2 000 ℃,壓力可達200 MPa。HIP涂層質量主要受壓力和溫度影響,高溫高壓下,內部的疏松和空隙基本被消除,明顯提升致密性、力學性能及循環次數,Abdel等[40]對Mg2Zr5O12的循環次數進行測試,未處理的涂層在240次循環后失效,而HIP處理后的涂層在一千次循環后仍然完好。但隔熱性能明顯不足,因此如何控制涂層和基體孔隙率是未來研究方向[41]。
激光重熔、激光上釉和激光熔覆均利用激光使材料表面快速熔化和凝固,形成具有改性層的表面改性技術,具有高效、無污染、局部處理等優點,其耐腐蝕性、抗磨性和抗熱震性能均得到改善,是目前綠色高效的方法。
航空發動機葉片工作環境復雜,存在高溫、高壓、環境微粒侵蝕、高速粒子沖擊等多因素復合作用,且熱障涂層為多界面構成,故在熱-力-化學耦合條件下因內部結構性能發生變化而引起失效。國內外學者對熱障涂層界面微觀及宏觀結構變化進行了分析,基于多種熱力學實驗結論和斷裂力學、損傷力學等理論,通過數值分析及建模等方式,研究了TBCs的失效機制,為TBCs可靠性和耐久性研究奠定了基礎[42]。其失效模式主要包括TGO失效、CMAS及熔鹽腐蝕。
4.1 TGO失效
熱障涂層失效的主要原因是各層材料間因熱膨脹系數不同導致的熱應力及內部氧化層的過量生長。服役過程中粘接層發生氧化反應,生成的TGO(熱生長氧化物)是導致失效的主要因素。圖8為在YSZ/NiCrAlY涂層失效后的EDS分析[43]。圖8a顯示反應起初主要是Al2O3保護涂層,圖8b顯示當服役時間延長時,Al逐漸消耗,Ni/Cr/Co等開始被氧化,此時TGO附件壓應力逐漸增大,受到相鄰界面束縛時,沿與界面垂直的方向變形,對相鄰涂層造成較大的拉應力,導致涂層內部產生裂紋,且涂層與TGO界面因產生大量尖晶石等脆性相而導致涂層脫落失效。
此外,TGO厚度有臨界值(8~12μm),當厚度增加到臨界值時,其應力分布發生變化,涂層將脫落失效。圖9為薛文利等在YSZ/NiCrAlY界面上測得不同溫度下循環次數和TGO厚度和最大裂紋的變換關系[43]。可見溫度為1 150 ℃時,其厚度增加最快,裂紋長度增加也最快。在1 100 ℃時,其厚度增加最慢,裂紋長度增加也最慢,可見TGO厚度直接影響了裂紋的產生,增加了失效速度。
(a)TGO厚度(b)最大裂紋長度
因此,改善TBCs壽命的有效方式是抑制混合氧化物的生成或降低混合氧化物的含量、延緩循環過程中TGO厚度的增長。通過粘接層成分改性、預氧化熱處理、擴散強化熱處理等方式可有效降低TGO的生長動力學,提高涂層和基體間的結合強度。
4.2 CMAS侵蝕失效
CMAS指航空發動機服役期間來自外部自然環境,主要成分包括CaO、Al2O3、MgO和SiO2為主的沉積物。CMAS的腐蝕機理主要體現在兩方面:一是CMAS小顆粒吸附在涂層表面,高溫熔化消耗YSZ涂層的Y2O3,加速ZrO2發生相轉變,產生相變應力并誘發裂紋產生,CMAS沿裂紋穿透涂層,導致涂層失效;二是CMAS到達TGO層時與其反應,增加層間壓力導致裂紋產生與擴展[44,45]。
CMAS侵蝕主要與溫度有關,郭磊等[46]在1 200 ℃和1 250 ℃時CMAS腐蝕4h時的YSZ涂層截面圖,如圖10所示。CMAS的熔點約為1 230 ℃,因此在1 200 ℃保溫4 h時(圖10a),CMAS在YSZ 表面鋪展,厚度為 143.35 μm,沒有熔化不會引起實質性腐蝕。但在1 250 ℃(圖10b)保溫4h時,涂層厚度明顯減小到19.35 μm,CMAS熔化而滲入涂層內部導致微觀結構變化,涂層失效。因此當發動機工作溫度超過1 200 ℃時,CMAS腐蝕是TBCs失效的主要原因。
CMAS侵蝕還與致密性有關。涂層致密度越高,抵抗腐蝕越強。謝詩駿等[47]通過調整送粉速率,得到不同致密的熱障涂層,圖11為PS-PVD涂層耐熔鹽腐蝕圖。觀察可知,由下往上按5g-10g-15g/min梯度遞增方式送粉得到的涂層防失效能力更強,在20h后涂層才開始脫落。
由此可見,針對CMAS侵蝕失效,主要防護技術有四種:(1)在TC層上制備Al2O3、Pd、Pt、Ti2AlC等非滲透性的防護層阻擋CMAS的滲入;(2)利用激光對頂層進行釉化處理或制備過程中調整送粉速率,提高微觀結構的致密性;(3)熱噴涂納米結構涂層以減少孔隙和裂紋;(4)采用稀土共摻雜的熱障涂層,通過層間快速形成新物質阻礙CMAS的進一步滲入,且可保留更多的Y2O3[48]。
航空工業的高速發展需要航空發動機在輕量化、推重比及服役時間等不斷迭代升級。在服役過程中,熱障涂層系統的組成、結構等將動態變化,導致其物理、機械性能在不同壽命時期均有不同的表現。作為渦輪葉片保護的核心技術,熱障涂層的材料選擇、制備方式、后處理方式及失效分析等將是未來研究的重點。
(1)材料方面。新型陶瓷層,尤其是高熵陶瓷相對于傳統熱障涂層材料具有優異的熱穩定性及力學性能,后續需持續開展高熵化合物(如硼、硅、氮、氧、碳等)的研究;粘接層的研究將關注 MCrAlY和NiAl 合金的摻雜改性以及新型粘結層材料(如Pt-Al )的研發。
(2)制備及后處理技術。APS常用于制備性能要求較低的靜子件,EB-PVD常用來制備服役環境要求高的動部件,兩者結合的PS-PVD可制備性能綜合的涂層是后續研究重點。后處理技術可有效提高涂層綜合性能,選取最佳溫度進行真空熱處理、控制涂層與基體孔隙率、激光表面改性技術是未來研究方向。
(3)失效機制。TGO失效是決定涂層壽命的主要因素,CMAS侵蝕失效限制了涂層工作溫度。通過粘接層成分改性、預氧化熱處理、擴散強化熱處理抑制混合氧化物的生成和延緩循環過程中TGO厚度的增長,通過增加防護層、提高微觀致密性及稀土共摻雜阻擋CMAS的滲入,后續需持續通過數值分析及建模等方式開展失效機制研究,為TBCs可靠性和耐久性研究提供指導。
免責聲明:本網站所轉載的文字、圖片與視頻資料版權歸原創作者所有,如果涉及侵權,請第一時間聯系本網刪除。
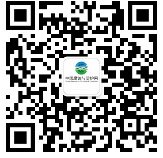
官方微信
《腐蝕與防護網電子期刊》征訂啟事
- 投稿聯系:編輯部
- 電話:010-62316606
- 郵箱:fsfhzy666@163.com
- 腐蝕與防護網官方QQ群:140808414