蠕者,慢也。蠕變時效成形技術,是一種慢心態的技術。
1.什么是蠕變時效成形
在講時效成形之前,先來科普一下什么是蠕變。蠕變是指固體材料在一定的溫度和較小的恒定外力作用下,其形變隨時間增加而逐漸增大的現象。舉個生活中常見的栗子,家里用的晾衣繩,剛掛上去的時候繃得很緊,但晾曬衣服用得久了繩子就變得松弛了。
松弛的晾衣繩
最為關鍵的一點是,材料的變形不是像塑性變形那樣在短時間較大的力作用下完成,而是遠小于其屈服強度的力長時間持續緩慢作用的結果。
有了蠕變的概念,我們再來看看什么是蠕變時效成形。蠕變時效成形(creep-age forming)主要是將材料的人工時效與零件成形相結合,同時利用材料在彈性應力作用下于一定溫度時發生的蠕變變形,從而得到帶有一定形狀的結構件。
鋁合金蠕變時效成形
2.蠕變時效成形的過程
蠕變時效成形工藝過程可分為3個階段:
蠕變時效成形工藝過程
1)加載。在室溫下,將零件通過一定的加載方式使之產生彈性變形,并固定在具有一定外形型面的模具上。
2)人工時效。將零件和模具一起放入加熱爐或熱壓罐內,在零件材料的人工時效溫度內保溫一段時間,材料在此過程中受到蠕變、應力松弛和時效機制的作用,內部組織和性能均發生較大變化。
3)卸載。在保溫結束并去掉模具的約束后,所施加到零件上的部分彈性變形在蠕變和應力松弛的作用下,轉變為永久塑性變形,從而使零件在完成時效強化的同時,獲得所需外形。
3.蠕變時效成形的力學特性
下圖是蠕變時效成形過程中應力與應變的關系曲線。
時效成形過程的應力應變路徑
在初期彈性加載的過程中,彈性應變逐漸增加;當進入時效保溫過程時,隨著加載時間的增加,蠕變變形逐漸增加,而彈性形變因總變形不變而逐漸減少,由于彈性變形降低引起應力相應地減少產生應力松弛;最后,去除外加約束,零件自由回彈,由于蠕變應變的存在,零件將無法回彈到初始狀態,從而保留了一定的外形。
4.蠕變時效成形的優勢
與傳統的冷加工塑性變形相比,蠕變時效成形的優點主要有:
1)蠕變時效成形時,成形應力通常低于其屈服應力,因此相對于常規塑性變形而言,時效成形減小了零件因進入屈服狀態后而引發失穩甚至破裂的危險,大大降低了零件發生加工裂紋的幾率;
塑性變形中的裂紋擴展
2)利用材料時效強化和應力松弛特性,在成形的同時,還完成了對零件材料的人工時效強化,從而改善了材料的微觀組織,提高了材料強度;
蠕變時效成形中長條狀碳化物逐漸變成顆粒狀
3)蠕變時效成形的零件具有很高的成形精度、可重復性和成形效率。在成形復雜外形和結構的零件時,時效成形技術僅需要一次熱循環就可使零件的外形達到所需精度,外形精度誤差小于1mm;
蠕變時效成形加工的高精度飛機薄板結構
4)蠕變時效成形的零件內部殘余應力幾乎完全被釋放,尺寸穩定,不會出現像噴丸成形的零件在放置一段時間后因內部殘余應力釋放而造成外形變化等問題。此外,對于焊接整體壁板,還可有效降低焊接殘余應力,增強耐應力腐蝕能力,延長零件的使用壽命。
低殘余應力的飛機薄壁結構
5.蠕變時效成形的關鍵技術
01工裝外型面優化技術
由于受到材料本身時效周期的限制,無法將試件內已有的彈性變形全部轉變為塑性變形,因此成形后均存在一定的回彈量。通常,回彈量可達到總應變量的70%以上。因此,應用蠕變時效成形工藝需要精確預測回彈量,并將回彈量補償到模具型面上,只有解決這一關鍵問題,才能得到所需的零件外形。
蠕變時效成形中的回彈現象
最初,對于零件成形后回彈量的確定主要是采用試錯法,通過大量的基礎工藝試驗以及經驗公式的外推來完成對模具型面的設計。由于這種方法效率不高,而且適應性較差,數值模擬被引入到了蠕變時效成形技術的研究中。
一種方法是通過有限元模擬的方法從宏觀角度進行應力應變分析,利用有限元建立能夠描述蠕變成形的材料本構模型。然而由于該方法忽略了成形過程中時效強化和塑性應變之間的相互作用,因此還無法對蠕變時效成形過程進行全面準確的描述。
當前,隨著材料微觀組織演化模擬理論的不斷完善以及各種測試手段的出現,研究材料微觀組織演變和蠕變時效成形過程工藝參數之間的關系,建立它們之間的本構方程,已成為當前該領域研究人員的主要研究方向。
02蠕變時效成形工裝
蠕變時效成形發展之初,主要是通過機械壓板或卡板使零件產生彈性變形,使用普通熱處理爐即可進行。該種工裝比較容易實現,但由于機械加載所產生的壓緊力不夠大且分布不均勻,因此該種方法一般僅限于成形不太厚的、厚度均勻的和加強筋與成形軸線平行的零件。
20世紀80年代中期,美國Textron公司開發了熱壓罐蠕變時效成形工藝。其基本的成形過程是先用真空袋和密封裝置將零件和工裝的型面密封起來,通過抽真空,使零件在上下表面空氣壓差的作用下固定到工裝的型面上,然后一同放入熱壓罐內,通過熱壓罐的壓力系統對零件施加足夠的均勻壓力,使零件完全貼合到工裝型面上,與此同時加熱到一定溫度并保溫一定時間,完成對零件的精確時效成形。因此,該工裝工藝能夠很好地控制零件的外形,特別適合具有復雜外形和結構的大型整體壁板構件的成形。
熱壓罐式蠕變時效成形原理圖
6.蠕變時效成形與航空制造
由于蠕變時效成形具有諸多優點,因此歐美等國很早就開展了對時效成形技術的相關研究,并已將該技術廣泛應用于飛機蒙皮和壁板制造中。
軍用飛機方面,以美國B-1B超音速戰略轟炸機的上下機翼壁板為典型案例。
在當時,這被認為是飛機工業使上所成形的最大、最復雜的機翼壁板。該零件材料采用可熱處理強化的鋁合金2124和2419,厚度突變從2.54mm增加到63.5mm,展向有整體加強桁條。該壁板的生產采用熱壓罐時效成形技術,壁板表面十分光滑,形狀準確度高,裝配貼合度可控制在0.25mm以下。
在民用飛機的應用方面,空客、波音和麥道的早期機型已經部分采用該項技術,如MD82、A330/340和A380等大型民用飛機的整體壁板制造中。
A380飛機
其中采用蠕變時效成形技術制造的A380飛機,機翼上壁板材料為鋁合金7055,零件長33m,寬2.8m,變厚度3mm~28mm,成形后外形貼合度小于1mm。
2000年美國NASA的IAS(Integral airframe structures)研究計劃將該技術列為整體機身結構的制造技術之一。
免責聲明:本網站所轉載的文字、圖片與視頻資料版權歸原創作者所有,如果涉及侵權,請第一時間聯系本網刪除。
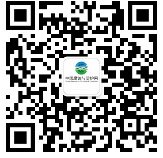
官方微信
《腐蝕與防護網電子期刊》征訂啟事
- 投稿聯系:編輯部
- 電話:010-62316606-806
- 郵箱:fsfhzy666@163.com
- 腐蝕與防護網官方QQ群:140808414