航空發動機被譽為現在工業皇冠上的明珠,是一個極端復雜的系統,是一個在極端苛刻的惡劣條件下(高溫高壓高應力)追求長期、穩定、安全的極端性能的尤物,難做自然是一定的。因為航空發動機涉及到一系列高性能渦輪葉片、單晶高溫合金制備和冷卻、熱障涂層防護等先進材料制造、加工技術。路上隨便找一個老大爺,聊到航空,或許都會對我國造不出高性能的航發痛心疾首。
1 航空發動機的結構
火箭
小時候,我們都玩過氣球。將氣球吹大后,一旦松開手指,氣球就會飛起來四處亂竄。這是因為氣球中的氣體在向外泄的同時,給氣球一個向前的反作用力。
火箭就是用這個原理,攜帶大量的燃料來制造氣體,再迅速向后排出從而獲得推力。
而航空發動機,也是在用這個原理讓飛機飛行的。所不同的是,飛機在大氣層下飛行,不需要自帶燃料制造空氣。
要說航發的原理也很簡單、巧妙,發動機首先通過風扇吸入空氣,然后壓氣機將空氣壓縮提高壓力,然后壓縮空氣進入燃燒室與燃料混合點燃,最后將高速氣體噴出推動渦輪旋轉;渦輪和壓氣機以及風扇是連在一或者兩根軸上的,渦輪旋轉又會帶動風扇與壓氣機轉動,不斷壓縮空氣產生部分推力,燃氣推動渦輪旋轉后經尾噴管噴出,又會產生部分推力。這兩部分推力共同為飛機提供動力。
更高性能的航發,需要更高性能的渦輪葉片
要想獲得在尺寸小、重量輕的前提下獲得高性能,也就是通常所說的提高推重比(發動機的推力和自重的比值),主要的措施是提高燃氣溫度。因為發動機的推力主要是靠燃燒產生的熱氣體與冷空氣混合產生的氣壓差來產生的。氣壓差越大,推力越大。要想提高氣壓差,燃燒溫度就要更高。
數據顯示渦輪前進口溫度每提高100度,在發動機尺寸不變的條件下,推重比可以增加10%.
早在1928年,英國工程師就提出了航空發動機的構想。但是,直到1939年,第一臺發動機才問世。因為按照當時的設想,根本沒有材料扛得住它的高溫。
現在,主流航空設備上采用的是推重比是7-8的第三代航空發動機,如美國的F-15、F-16、F-18,中國的殲10、殲11等戰機,民航的各個系列如空客A320、波音737等。渦輪前進口溫度大約在1680-1750K.美國普拉特·惠特尼公司研發的F119發動機(準備于美軍F-22戰機,世界上第一款五代機),推重比10.8,渦輪前進口溫度達到了1900K.這個溫度,已經超過碳鋼的熔點上百度了。
除了高溫,渦輪葉片同時還在以極高速旋轉。高速旋轉導致渦輪葉片必須承擔極高的離心力。而在高溫下、高加載下,金屬材料會發生蠕變。簡單來說,蠕變是在一定溫度下,材料長期在較小的外力作用下發生形變。蠕變對于葉片來說不是好事,它能使葉片徑向伸長 、扭轉和彎曲,影響葉片的使用壽命。
另外,材料在使用時會發生疲勞,可能導致疲勞斷裂,危及安全。
因此,渦輪葉片材料既要耐高溫,又要低蠕變,耐疲勞、力學性能還要好。要說它好造,那恐怕現在也沒有其他難造的東西了。
2 渦輪葉片選材
越來越高的標準,渦輪葉片自然不能使用等閑材料。從第三代航發,一般采用單晶或者定向合金制造渦輪葉片。
通常鑄造的金屬材料都是多晶的,為什么要用單晶或者定向合金?
對于多晶材料,晶粒與晶粒之間有晶界。在某些場合下,晶界對于材料性能提高有好處。但在上個世紀60年代,美國惠普公司發現對于渦輪葉片來說,晶界是個"壞孩子".普通鑄造多晶高溫合金中與應力軸垂直的晶界是高溫應力下產生裂紋的"源頭",所以必須減少晶界,由此發展了高溫合金定向凝固技術。
3 單晶高溫合金
定向凝固高溫合金通過控制結晶生長速度、使晶粒按主承力方向擇優生長,可以改善合金的強度、塑性、熱疲勞性,使渦輪葉片的使用溫度達到了 1273K .
進一步,航空業發展了單晶合金渦輪葉片,其耐溫能力、蠕變強度、熱疲勞強度、抗氧化性能和抗腐蝕特性較定向凝固柱晶合金有了顯著提高。
但是,單晶合金渦輪葉片的制造工藝難度可就高了許多。目前,最常使用的用于制造單晶葉片的工藝方法是螺旋選晶法,其基本原理就是利用選晶器的這種狹窄界面,只允許一個晶粒長出它的頂部,然后這個晶粒長滿整個型腔,從而得到單晶體。其晶體競爭生長機制是螺旋結構總的攀升走向正好與散熱方向相反,致使螺旋體內散熱均勻,因此在整個螺旋形生長過程中,位向最適合生長的那個晶粒將其他眾多的初生晶粒一一淘汰,不斷長出枝晶并最終進入試樣本體成為單晶鑄件。單向散熱看似簡單,其實這個過程是極其難控制的,這涉及到材料本身及鑄模的熱物理特性,并且考慮制造過程中的散熱條件等因素的影響,以及晶體的生長速度等,這些都需要經過嚴格的實驗設計以及大量的實驗數據,經計算后才能夠得出準確的結果,難度非常之大。
此外,高溫合金中還添加微量元素提高使用溫度。第二代單晶合金與第一代單晶合金相比,通過加入3%的錸、適當增大了鈷和鉬的含量,使其工作溫度提高了30 K.第三代單晶合金Rene N6和CMSX-10加入高達5wt%以上的錸,顯著提高高溫蠕變強度。第四代單晶合金,通過添加釕,進一步提高了合金微觀結構的穩定性,使用溫度已達到了1473K.
4 冷卻技術
不過采用單晶高溫合金材料并不能解決問題。實際上,單靠尋找更耐高溫的材料來滿足更高渦輪前溫度是不切實際的。目前,渦輪前進口溫度已達到了 2000K 左右,比高壓渦輪葉片金屬材料的熔點高400K.而近年來,渦輪前溫度以每年平均提高 20K的速度增加,而金屬耐溫程度僅以每年約 8K的速度增加。
兩者之間的缺口就必須依靠航發先進的冷卻系統來實現,例如氣膜冷卻技術。通過噴入冷氣,借助高溫燃氣的壓力和摩擦力讓其粘附在壁面附近,形成一個較低的冷氣膜,將壁面同高溫燃氣隔離,并帶走部分高溫燃氣或明亮火焰對壁面的輻射熱量,從而對壁面起到良好的保護作用。
據數據記載,目前的冷卻技術可以實現溫降已達400 K-600 K.
隨著航空發動機渦輪前溫度的不斷提升,原有的單通道空心冷卻葉片的冷卻效果已經不能滿足現實需求,發展更為先進更復雜的多通道多路冷卻方案成為下一代航發的關鍵技術。而每一次冷卻方案的優化都對渦輪葉片的設計和制造提出了極大的考驗!
冷卻技術的發展,依然不能完全解決、或者滿足材料承載溫度與渦輪前進口溫度之間的差距。因此,還需要對在渦輪葉片燃氣流道表面噴涂熱障涂層。
5 熱障涂層
熱障涂層(簡稱 TBC)是在零件表面沉積黏接 一層低導熱系數的材料,利用其低熱傳導特性,在其內、 外表面形成溫降,用以降低零件表面工作溫度(或提高零件的承溫能力)的方法。據資料介紹,熱障涂層可取得 50K-150 K 的隔熱效果。
目前在渦輪發動機上獲得實際應用的熱障涂層均為雙層結構: 表層為陶瓷層,主要起隔熱作用, 此外還起抗腐蝕、 沖刷和侵蝕的作用 ; 內層為金屬粘接層, 主要起改善金屬基體與陶瓷層之間的物理相容性, 增強涂層抗高溫氧化性能的作用。
由于是把涂層涂覆在金屬基體上,需要考慮涂層的附著力,對金屬基體顯微組織穩定性的影響以及涂層與金屬因熱膨脹系數差異而可能導致的剝落問題等,這就需要空心葉片金屬材料學科領域聯合諸多其他領域的相關專家合力公關、共同研發。
至此,一片單晶空心葉片真正的造價堪比同重量的黃金或許并不為過。甚至高性能的葉片也是有價無市。
同時,我們也能看到。為了能讓渦輪葉片正常工作,材料科技工作者們真是無所不用其極。
免責聲明:本網站所轉載的文字、圖片與視頻資料版權歸原創作者所有,如果涉及侵權,請第一時間聯系本網刪除。
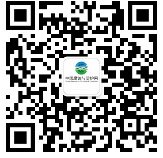
官方微信
《腐蝕與防護網電子期刊》征訂啟事
- 投稿聯系:編輯部
- 電話:010-62316606-806
- 郵箱:fsfhzy666@163.com
- 腐蝕與防護網官方QQ群:140808414