1前言
資源消耗和環(huán)境污染已成為21世紀人類可持續(xù)發(fā)展面臨的首要問題。鎂合金以質(zhì)輕、結構性能優(yōu)異以及易于回收等眾多優(yōu)點成為裝備制造業(yè)輕量化發(fā)展的首選材料;而且,無論在儲量、特性、應用范圍、循環(huán)利用、以及節(jié)能環(huán)保等方面和鋼鐵產(chǎn)業(yè)相比,鎂合金均具有非常明顯的優(yōu)勢。據(jù)預測,隨著鎂合金應用技術和價格兩大瓶頸的突破,全球鎂合金用量將以每年20%的幅度快速增長,這在近代工程金屬材料的應用中是前所未有的[1].大規(guī)模開發(fā)和利用鎂合金的時代已經(jīng)到來,它必將成為未來產(chǎn)業(yè)革命可持續(xù)開發(fā)資源的核心。
然而,由于鎂的化學性質(zhì)十分活潑,標準電極電位很負(-2.36VSCE),導致鎂合金的耐腐蝕性很差,在腐蝕性介質(zhì)中很容易發(fā)生嚴重的腐蝕;并且,鎂合金的表面膜疏松多孔,MgO的PBR值為0.81,對基體保護能力差。不適用于大多數(shù)的腐蝕環(huán)境。因此,迄今為止,鎂的應用仍然非常有限,鎂合金的腐蝕與防護問題越來越受到人們的重視。鎂合金要大規(guī)模應用于工業(yè),必須選用或開發(fā)適當?shù)暮辖鸹驅(qū)︽V合金進行各種表面處理,采取一定的防護措施對鎂合金構件進行保護。
在近幾年的鎂合金腐蝕與防護研究熱潮中,具有不同功能特性的鎂合金表面防護技術被廣泛地研究,同時,針對新型鎂合金的成分、結構、組織形態(tài)等方面也展開了大量電化學腐蝕機理的研究。下面我們將簡要介紹當前鎂合金腐蝕與防護發(fā)展的現(xiàn)狀。
2鎂合金電化學腐蝕行為及影響因素
鎂合金腐蝕的直接原因是合金元素和雜質(zhì)元素的引入導致鎂合金中出現(xiàn)第二相,在腐蝕性介質(zhì)中,化學活性很高的鎂基體很容易與合金元素和雜質(zhì)元素形成腐蝕電池,誘發(fā)電偶腐蝕;此外,鎂合金的自然腐蝕產(chǎn)物疏松、多孔,保護能力差,導致鎂合金的腐蝕反應可以持續(xù)發(fā)展。
鎂合金在潮濕的大氣、土壤和海水中均會發(fā)生電化學腐蝕。鎂合金的腐蝕與純鎂的腐蝕相近,以析氫為主,氫離子的還原過程和陰極析氫過電位對鎂的腐蝕過程起重要作用。腐蝕過程的反應式為:Mg+2H2O→Mg(OH)2+H2↑。然而,鎂合金的腐蝕具有特殊的電化學現(xiàn)象,即負差數(shù)效應。Mordike認為陰極極化后,金屬表面狀況發(fā)生劇烈改變,與極化前相比差別很大,使鎂合金的自腐蝕速率增加,出現(xiàn)負差數(shù)效應。李瑛等利用掃描隧道顯微鏡,在微觀尺度下觀察腐蝕界面形貌特征,發(fā)現(xiàn)在pH=11的1mol/LNaCl水溶液中,金屬鎂表面形成塊狀氧化物,陽極極化后塊狀氧化物尺度變小,保護作用降低,導致鎂金屬溶解出現(xiàn)負差數(shù)效應。由于鎂的負差數(shù)效應是一個復雜的過程,對這一問題還有待深入研究和探索。當然,上述只是對鎂合金腐蝕機理的概述,下面將具體討論各種因素對鎂合金的腐蝕性能的影響。
2.1介質(zhì)對鎂合金的電化學腐蝕的影響
各種介質(zhì)對鎂合金耐蝕性的影響是不同的,了解介質(zhì)對鎂合金耐蝕性的影響規(guī)律,可以指導人們正確選擇鎂合金的工作、貯存和運輸?shù)慕橘|(zhì)環(huán)境。介質(zhì)的pH值對鎂的電位及耐蝕性影響很大。當pH為3~11.5時,鎂的電位很低,基本保持在-1.4V的水平上;當pH<3時,鎂的電位進一步降低,腐蝕速率急劇加快;當pH>11.5時,鎂的電位升高,腐蝕速率顯著減慢。而且,溶液中不同離子對鎂及鎂合金的腐蝕作用不同。
Cl-,SO24-,NO3-,Br-和含有氯的氧化性的陰離子都會加速鎂的腐蝕,原因是這些離子能夠改變鎂合金表面層的保護性能。空氣中的CO2溶于水中形成的HCO3也會對鎂在溶液中的腐蝕行為產(chǎn)生影響。
此外,針對海洋環(huán)境,賈瑞靈等探討了氯離子含量、附著鹽粒2種特征環(huán)境因素對鎂合金腐蝕行為的影響規(guī)律。研究結果表明:可溶鹽下鎂合金的腐蝕行為受可溶鹽的潮解能力、水解能力和侵蝕能力的共同影響。其中NaCl和NH4Cl2種氯化物對鎂合金的腐蝕較嚴重,(NH4)2SO4和Na2SO42種硫酸鹽對鎂合金的腐蝕較輕,且銨鹽大于鈉鹽。張濤等建立了薄液膜下鎂合金電化學腐蝕的噪聲測量方法,用這種方法能夠長期、準確地控制鎂合金表面薄液膜的厚度以及研究薄液膜厚度對鎂合金腐蝕行為的影響。
2.2合金元素(成分與結構)對鎂合金電化學腐蝕行為的影響
合金元素和雜質(zhì)元素對鎂合金的耐蝕性有顯著的影響。Hanawalt等研究了14種元素對二元鎂合金在鹽水中腐蝕速率的影響。發(fā)現(xiàn)Fe,Ni,Cu在濃度低于0.2%時就明顯加速腐蝕。而Al,Sn,Cd,Mn,Si,Na,Pb等,濃度達到5%左右時,對腐蝕速率幾乎沒有什么影響。Fe不能固溶于鎂中,以金屬Fe形式分布于晶界,成為有效陰極,降低了鎂的耐蝕性。Ni,Cu等在鎂中溶解度極小,常和鎂形成Mg2Ni/Mg2Cu等金屬間化合物,以網(wǎng)狀形式分布于晶界,使鎂的腐蝕性能變差。此外,不同工藝條件下鎂合金的組織結構不同,與金屬模鑄造相比,壓鑄AZ91鎂合金的組織更為細小,并且鑄件表面的組織與內(nèi)部組織相比,β相的組分更為連續(xù),比例也最大。張濤等以鑄態(tài)AZ91D合金(α+β相)與T4固溶處理合金(α相)在1mol/LNaCl中的腐蝕為背景,通過測量動電位極化曲線、MottSchottky曲線和不同電位下氫氣析出速度,研究了β相(結構)對AZ91D鎂合金腐蝕行為的影響。結果表明,β相對AZ91D鎂合金腐蝕行為起到2方面的影響:①H原子擴散進入β相,使AZ91D合金的析氫速度減緩,負差數(shù)效應減弱;②β相中的H原子在鎂合金的腐蝕過程中會進入腐蝕產(chǎn)物膜(P型半導體),發(fā)生離子化并放出自由電子,造成價帶空穴密度降低,產(chǎn)物膜的耐蝕能力增強。
2.3鎂合金的組織形態(tài)(微晶和非晶)對鎂合金腐蝕行為的影響
近年來,鎂基非晶態(tài)合金由于具有非常高的抗拉強度、良好的韌性和耐蝕性,越來越受到重視。對純鎂、多相異質(zhì)結晶的Mg65Y10Cu25合金及非晶態(tài)鎂合金耐蝕性的對比研究表明,這幾種材料的電化學特性有很大不同,非晶態(tài)鎂合金的耐蝕性最好,Mg65Y10Cu25合金次之,純鎂最差。非晶態(tài)鎂合金的耐蝕性優(yōu)于Mg65Y10Cu25合金的主要原因是:Mg65Y10Cu25合金的組織不是非晶態(tài)組織,具有不均勻性,故非晶態(tài)鎂合金比Mg65Y10Cu25合金有更強的鈍化作用和耐蝕性。而且,發(fā)現(xiàn)非晶化改善了Mg58.5-Cu31.5-Y10合金表面氧化膜的化學穩(wěn)定性,膜溶解速度成倍數(shù)降低,同時非晶化顯著提高了鎂合金的耐點蝕能力,在6mol/LNaCl的堿性介質(zhì)(pH=14)中非晶合金無點蝕發(fā)生。而相應的鑄態(tài)合金在1.5mol/LNaCl的介質(zhì)中發(fā)生嚴重的點蝕。
李瑛等通過濺射方法能夠制備出微晶/納米晶AZ91D和純鎂涂層,發(fā)現(xiàn)納米化顯著影響鎂合金的腐蝕行為,提高了鎂合金腐蝕產(chǎn)物膜的保護能力(圖1)。機理分析表明,對于鑄態(tài)純鎂,鈍化膜生長過程為:最初為溶解-沉積生長,然后鈍化膜發(fā)生破裂,最后以離子遷移方式生長。對于微晶化的純鎂來說,鈍化膜生長過程為:先為溶解-沉積生長,然后以離子遷移方式生長,沒有出現(xiàn)鈍化膜的破裂過程。微晶化使純鎂鈍膜中的載流子密度減小。同時,微晶化造成純鎂鈍化膜內(nèi)缺陷擴散系數(shù)發(fā)生數(shù)量級地減小,從而使得微晶化后純鎂的耐點蝕能力提高。
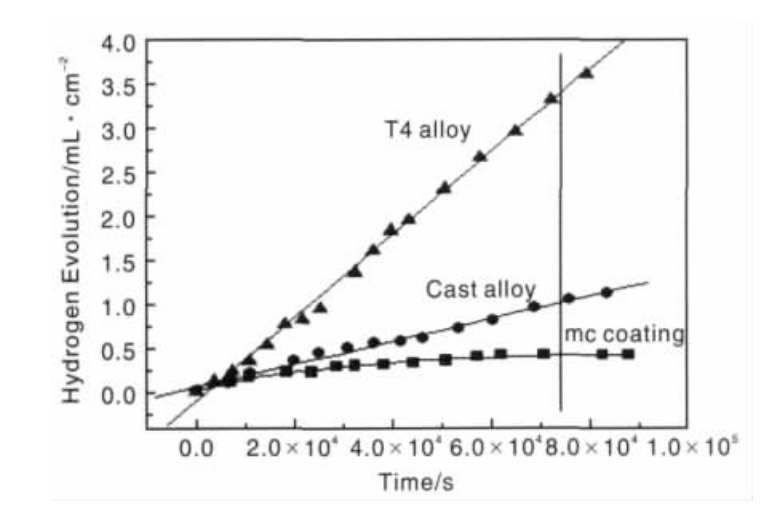
圖1鎂合金在1mol/LNaCl溶液中析氫速度測量結果
2.4新型Mg-Gd-Y-Zr稀土鎂合金腐蝕行為
上海交通大學等研制的新型Mg-xGd-Y-Zr稀土鎂合金具有較高的抗拉強度、伸長率及抗腐蝕疲勞性能,成為未來武器裝備領域最有前途的鎂合金材料,所以,研究新型Mg-xGd-Y-Zr稀土鎂合金的電化學腐蝕行為對支撐高性能鎂合金在重大領域中的應用具有重要的意義。目前,郭興伍等研究了稀土元素對鎂合金在常溫和高溫條件下形成的氧化膜的穩(wěn)定性和保護作用的影響;揭示了影響氧化膜保護性能的關鍵因素以及闡明了合金元素對腐蝕性能的影響規(guī)律。
其中,研究了不同Gd含量對Mg-xGd-Y-Zr稀土鎂合金腐蝕行為的影響,發(fā)現(xiàn)合金的耐蝕性隨著Gd含量從6%升高至10%時,合金的耐蝕性能逐漸下降,而當Gd含量從10%升高至12%時,合金的耐蝕性能又有所升高。
另外,該研究組采用場發(fā)射掃描電鏡觀察不同浸泡時間下GW63K合金表面腐蝕產(chǎn)物的產(chǎn)生及發(fā)展變化過程。研究結果表明,腐蝕產(chǎn)物的形貌隨浸泡時間的變化而不同,在5%NaCl溶液中浸泡60min之前為蜂窩狀結構,過了60min后又變?yōu)槎嗫谞罱Y構。在腐蝕過程中,第二相從T6狀態(tài)合金中脫落的現(xiàn)象可以作為鎂合金腐蝕中負差效應機理的有效證據(jù)。
3鎂合金的防護技術研究現(xiàn)狀針對鎂合金自身的特點,不同的研究者提出了不同的方法來提高鎂合金的抗腐蝕性能,這對實現(xiàn)鎂合金大規(guī)模應用具有重要的意義。目前,鎂合金表面處理技術的研究和應用主要有以下幾種。
3.1化學轉(zhuǎn)化涂層
鎂合金的化學轉(zhuǎn)化膜就是通過化學處理在合金表面形成由氧化物或金屬化合物構成的鈍化膜的處理工藝。
目前,化學轉(zhuǎn)化膜以鉻酸鹽轉(zhuǎn)化膜的防蝕效果最好,這種方法主要采用鉻酐或重鉻酸鹽。美國化學品Dow公司開發(fā)了一系列鉻化處理液。著名的Dow7工藝采用鉻酸鈉和氟化鎂,在鎂合金表面生成鉻鹽及金屬膠狀物,這層膜起屏障作用,減緩了腐蝕,并有自修復功能力。但是由于鉻酸鹽處理工藝中含Cr+離子,具有毒性,污染環(huán)境,且廢液的處理成本高,而且,化學轉(zhuǎn)化膜的耐磨性、耐蝕性不太好,它只能減緩腐蝕速度,并不能有效防止腐蝕。
3.2有機涂層
有機物涂層是鎂合金保護的一種常見方法。應用于鎂合金表面的有機物涂層通常采用環(huán)氧樹脂、乙烯樹脂、聚氨酷以及橡膠等材料。也可以在鎂合金上涂油脂、油漆、臘和瀝青等。但是單獨的有機物涂層耐蝕性能有限,結合力也較低,只能用來作為短時間的防護處理,或者在其它轉(zhuǎn)化膜表面涂敷作為復合涂層。
3.3化學鍍鎳涂層
在鎂合金的表面可以通過電鍍、化學鍍、熱噴涂等方法獲得金屬涂層。其中應用最廣的是化學鍍Ni-P,工藝簡單,鍍液中不含氰化物,逐漸受到重視。Sharma等討論了熱傳導性高的ZM21鎂合金用堿式碳酸鎳、次磷酸鈉為還原劑的直接化學鍍鎳工藝。得到的鍍層具有良好的力學性能、耐蝕性、可焊性和對環(huán)境的穩(wěn)定性。霍宏偉等在傳統(tǒng)直接化學鍍鎳方法的基礎上,對鍍液成分和操作進行改進,在AZ91D鎂合金表面得到了均勻、致密,無明顯表面缺陷的Ni-P涂層。國內(nèi)有人在鎂合金表面化學鍍Ni/電鍍Au,這種涂層能經(jīng)得起-196~150℃的極端溫度循環(huán),而且不會降低鍍層的物理光學性能,使鎂合金具有了能滿足航天要求的優(yōu)良性能。但是,由于鍍層金屬的電極電位遠遠大于鎂,如果鍍層有通孔,反而會加速基體的腐蝕。而且,這樣的工藝復雜、成本較高,而且僅適合于形狀簡單零件的處理。
3.4鎂合金表面鋁涂層
在鎂合金表面制備結合力好、均勻致密的鋁錳合金鍍層不僅可以單獨作為防護層使用,而且可通過后續(xù)加工處理進一步轉(zhuǎn)化為更加耐蝕耐磨及高硬度的膜層,以提高鎂合金表面的綜合性能。張吉阜等在熔鹽中對鎂合金直接進行電鍍鋁實驗。首先對鎂合金進行預鍍鋅處理,以鍍鋅層作為鍍鋁前的過渡層。然后再進行熔鹽電鍍實驗,結果表明,鋅層代替了夾雜層成為了熔鹽鍍層與鎂合金基體之間的中間層,涂層表現(xiàn)了良好的結合性能。而且,電鍍鋁錳合金后鎂合金的腐蝕電位得到了很大的提高,說明材料的腐蝕熱力學穩(wěn)定性得到了提高。
3.5微弧氧化及其復合涂層技術的發(fā)展
微弧氧化是最近發(fā)展起來的,被認為是最有前途的輕合金表面處理方法。同其它表面處理方法相比,具有工藝簡單、處理效率高、工藝成本低、無污染等特點,符合當前清潔工業(yè)的發(fā)展要求。它結合電化學,熱化學及等離子體化學等方法,在鎂合金表面可原位形成陶瓷質(zhì)的氧化膜,該陶瓷膜能極大地提高輕合金表面的硬度、耐磨性、耐腐蝕性和電絕緣性能等指標[33-34].目前,金屬研究所等單位[35-39]正在開發(fā)系列微弧氧化及其復合涂層技術。
3.5.1微弧氧化膜致密化研究
針對鎂合金微弧氧化過程中金屬界面等離子及電化學作用的特點,王福會研究組通過認識關鍵工藝因素對氧化膜自身致密性及微結構的影響機制,實現(xiàn)了氧化膜微結構與性能的設計和制備。張偉等以KF作為主鹽的新型電解液,通過控制不同工藝條件(使用添加劑和不同的電源控制模式),在AZ91D鎂合金表面制備新型氟化物PEO陶瓷膜,其主要相組成為MgF2和KMgF3,而傳統(tǒng)PEO陶瓷膜中主要相組成為MgO,由于VMgF2/VMg=1.41>1,VKMgF3/VMg=1.98>1,VMgo/VMg=0.81<1,因此,氟化鎂或其復合物能夠被成功地合成到PEO膜層當中,并且取代傳統(tǒng)的氧化鎂成為PEO膜層的主要相,大大降低了傳統(tǒng)PEO膜層的孔隙率,進而提高了抗腐蝕能力,該氧化膜的自腐蝕電流達到10-8A/cm2,鹽霧實驗接近1000h.
3.5.2微弧氧化陶瓷基復合涂層技術
微弧氧化膜(PlasmaElectrolyticOxidation,PEO)雖有良好的結合力、機械性能,但由于自身的微孔結構或不致密性,不能滿足腐蝕防護的實際要求。如果采用傳統(tǒng)的適用于較小孔徑氧化膜的"封閉"方法,微弧氧化膜不能產(chǎn)生有效的"封閉"效果。針對微弧氧化膜結構特點,段紅平系統(tǒng)研究了微弧氧化界面能量作用機制,在基本實現(xiàn)氧化膜孔隙結構設計控制的前提下,通過物理或化學方法引入有機聚合物形成的復合膜層。
研究了微弧氧化工藝參數(shù)對微孔結構以及有機聚合物樹脂基質(zhì)的影響,提出微弧氧化層與有機聚合物層具有最佳協(xié)和作用(防護性能、耐磨性能等)的涂層體系,開發(fā)了基于微弧氧化及其微孔結構的復合防護涂層技術。
動電位極化曲線及電化學阻抗結果表明微弧氧化膜基復合涂層具有最好的耐蝕性能,其自腐蝕電流達到10-9A/cm2,鹽霧實驗達到2000h.
3.5.3微弧氧化/化學鍍復合涂層技術
對鎂合金進行化學鍍處理,可獲得較好的表面機械性能(硬度、耐磨性、抗機械損傷性等)。但鎂合金直接化學鍍存在較明顯的技術問題:①化學鍍層是陰極性的,一旦存在缺陷或損傷將引發(fā)嚴重的局部加速腐蝕破壞;②結合力較難保證。為解決鎂合金的實際防護(如輪轂的防護及表面性能)要求,曾立云等在完善氧化膜孔隙結構設計控制的前提下,開發(fā)了一種新型PEO陶瓷膜表面自催化化學鍍工藝,研究了自催化顆粒在氧化膜表面的分散性以及與微孔結構物理化學配合特性,使化學鍍鎳涂層在膜層表面具有較快的生長速率,而且氧化膜完全將基體與鎳磷層隔離防止陰極效應的發(fā)生。該復合涂層表現(xiàn)出優(yōu)良的防護性能,耐鹽霧時間達到1200h以上,實現(xiàn)了耐磨性和抗刮傷性能的統(tǒng)一。
孫碩等用廉價的TiB2催化涂層取代鈀活化工藝,制備了均勻、致密的陽極氧化膜/化學鍍鎳復合涂鍍層,TiB2粉體和部分暴露的粉體是化學鍍鎳最初成核的催化活性點。化學鍍鎳層直接在催化層上生長,鋸齒狀的界面表明化學鍍鎳層與催化層和鎳磷層之間具有良好的結合力。用拉開法測試的結合強度為40MPa.表面顯微硬度Hv為9000~10000MPa;鹽霧實驗(ASTMB117)大于1000h,具備實際應用的潛力。
4總結與展望
我國是一個鎂資源大國,可是我國的鎂主要用于出口,附加值低。要改變我國鎂業(yè)的現(xiàn)狀,必須打破鎂合金應用中的瓶頸,即解決鎂合金耐腐蝕性差的問題,因此,我們必須加強鎂合金腐蝕和防護的研究。當前在鎂合金腐蝕研究方面應開展以下幾方面的研究。①新型鎂合金腐蝕機理與腐蝕規(guī)律研究。包括腐蝕動力學,陰極、陽極過程,鈍化等方面的研究。②稀土第二相細晶化、熔體純凈化以及準晶均勻化過程對材料的耐蝕性的影響規(guī)律,揭示耐蝕性提高的機理,為稀土鎂合金研制、提升材料綜合性能提供理論指導。③各種鎂合金在自然環(huán)境(大氣、海水、土壤)中腐蝕行為的研究,為鎂合金結構件設計提供依據(jù)。在腐蝕防護技術方面,各種高效、經(jīng)濟、無污染的表面處理技術將是鎂合金腐蝕與防護研究的重點發(fā)展方向。因為電鍍和化學鍍一般都需要復合疊加才能達到所需的耐腐蝕性能,因此開發(fā)無鉻、無磷、無氟的綠色環(huán)保型化學氧化技術、微弧陽極氧化技術以及能抵抗惡劣環(huán)境的單層防護層技術是目前鎂合金防護技術研究的主要發(fā)展方向。
更多關于材料方面、材料腐蝕控制、材料科普等方面的國內(nèi)外最新動態(tài),我們網(wǎng)站會不斷更新。希望大家一直關注中國腐蝕與防護網(wǎng)http://www.ecorr.org
責任編輯:汪玉玲
免責聲明:本網(wǎng)站所轉(zhuǎn)載的文字、圖片與視頻資料版權歸原創(chuàng)作者所有,如果涉及侵權,請第一時間聯(lián)系本網(wǎng)刪除。
相關文章
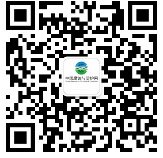
官方微信
《中國腐蝕與防護網(wǎng)電子期刊》征訂啟事
- 投稿聯(lián)系:編輯部
- 電話:010-62316606-806
- 郵箱:fsfhzy666@163.com
- 中國腐蝕與防護網(wǎng)官方QQ群:140808414
文章推薦
點擊排行
PPT新聞
“海洋金屬”——鈦合金在艦船的
點擊數(shù):8125
腐蝕與“海上絲綢之路”
點擊數(shù):6461