晶格/點陣結構由于重量輕、高強度比,逐漸成為航空航天產品設計的寵兒。丹麥公司Adimant利用3D金屬打印技術制作了據說是迄今為止最大的金屬晶格結構,重1.7公斤,體積134×28×500毫米,用在歐洲最大的衛星制造商Thales Alenia Space的衛星上。
而近期,由中國空間技術研究院采用微單元包絡體(即點陣結構)結構進行輕量化設計的飛行器結構件,通過金屬3D打印技術研制成功,尺寸超過了Thales Alenia Space的衛星所采用的金屬晶格結構。這標志著國內金屬選區熔化3D打印在成形尺寸極限、薄壁結構、微單元包絡結構等關鍵技術方面取得重大突破。今天,我們不但為大家揭曉此飛行器結構件的真面目,還將揭秘其背后的技術難題。
圖1:飛行器框形狀
據悉,此飛行器結構件是采用鈦合金研發制造、包絡尺寸為長短軸在550至700mm的十字連接橢圓形結構件(外形如圖1所示)。如果采用傳統制造工藝制造,零件內部只能為實體結構,重量將高達3公斤,無法滿足減重設計要求。
為達到減重的目的,設計人員在零件設計優化過程中創造性地采用輕量化設計,用微單元包絡體結構代替原有的實體結構,這種結構的理論重量遠低于實體結構的重量,最終這樣一個大家伙成形零件的質量僅為600余克!讓人不得不驚嘆于點陣結構的神奇魅力(內部結構如圖2所示)。
圖2:飛行器框結構
由于傳統制造工藝無法實現這種微單元包絡體結構的制造,最終,通過采取金屬3D打印技術成功研制出該飛行器結構件。零件的質量僅為600余克,相比傳統制造工藝減重80%左右。該鈦合金零件體密度僅為1g/cm3,與水密度相當,減重效果極為明顯,是尺寸獲得重大突破的點陣輕量化飛行器結構件。眾所周知,飛行器通常由眾多復雜零部件構成,而這僅僅只是其中之一。如果能在更多的零部件尤其是大型結構件上實現晶格結構及金屬3D打印,發射中的燃料成本將可以大大節約!這對于金屬3D打印在航天航空領域的應用無疑具有里程碑式的重要意義。
據了解,此飛行器結構件成形采用的金屬3D打印技術為激光選區熔化成形技術。激光選區熔化成型技術成形的零件致密性好,能夠成形高精度復雜異型金屬零件。因其具有組織致密、綜合性能優良的特點,在國內外已得到了普遍重視,并具有一定程度商業化應用。
據項目相關專家介紹,采用激光選區熔化成形技術成形此結構件的背后,存在以下技術難題:
1、該飛行器結構件尺寸大,包絡體蒙皮壁厚較薄,厚度不足0.5mm,且內部為微單元結構,結構尺寸精度要求嚴格;
2、激光選區熔化成形過程中,溫度梯度產生的熱應力存在使零件變形的風險;
3、包絡體完全包絡微單元結構,無法通過添加支撐來確保懸空的包絡體蒙皮的成形。
4、零件整體尺寸較大,超出國際金屬3D打印廠家一般設備成形尺寸極限。
5、重量要求嚴格,實物重量不得超過模型理論重量的3%。
據悉,為了獲得性能優良、致密性高的輕量化飛行器結構件,中國空間技術研究院經過大量的工藝研究實驗,在大型薄壁微單元包絡體設計方面積累了豐富的經驗。而鑫精合團隊作為承制方,經過層層技術攻關,通過金屬3D打印技術成功研制出這一大尺寸3D打印輕量化飛行器結構件產品,一舉解決該結構件的減重制造難題。
更多關于材料方面、材料腐蝕控制、材料科普等方面的國內外最新動態,我們網站會不斷更新。希望大家一直關注中國腐蝕與防護網http://www.ecorr.org
責任編輯:劉洋
投稿聯系:編輯部
電話:010-62313558-806
郵箱:fsfhzy666@163.com
中國腐蝕與防護網官方 QQ群:140808414
免責聲明:本網站所轉載的文字、圖片與視頻資料版權歸原創作者所有,如果涉及侵權,請第一時間聯系本網刪除。
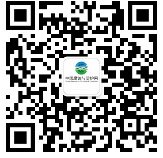
官方微信
《中國腐蝕與防護網電子期刊》征訂啟事
- 投稿聯系:編輯部
- 電話:010-62316606-806
- 郵箱:fsfhzy666@163.com
- 中國腐蝕與防護網官方QQ群:140808414