1 引言
貫穿碳纖維增強復合材料研究最引人注目的是其沖擊損傷問題,無論是相關的材料(包括纖維和樹脂)研究,結構設計的重點還是工藝制造和維護問題,碳纖維復合材料一進入解決輕量化需求的高端應用,遇到的技術關鍵就是沖擊損傷,本文試圖還原復合材料沖擊損傷問題的來龍去脈。
回顧碳纖維應用的發展史,大家都知道英國羅羅公司是第一個試圖把碳纖維用于高端應用——在1967年開始研制飛機發動機進氣風扇葉片的吃螃蟹者,當然失敗的原因很多,但很重要的一個原因是復合材料葉片沒有通過外來物沖擊的考驗,致使英國在碳纖維復合材料發展中失去了先機,退出了領先的地位。1970年代初國際石油危機爆發,民用飛機的機體結構輕量化被提上了日程,碳纖維作為首選再一次受到了關注。為解決新材料應用中首先遇到的信心(安全性)問題,波音公司研制了100多付擾流板在波音707上試用,1975年經試用考核后,對這些擾流板進行了檢查,發現碳纖維復合材料部件出現了金屬結構沒有遇到的新問題——濕熱引起的材料性能下降和沖擊損傷(擾流板是薄蒙皮夾層結構)。自此復合材料沖擊損傷就成了復合材料技術中的核心問題之一。
2 復合材料沖擊損傷研究歷程
2.1 壓縮下沖擊強度研究和應用
由于最初沖擊損傷問題是由擾流板這類薄蒙皮夾層結構引起的,當時關注的外來物主要是地面和空中飛行時的冰雹和跑道碎石,都是在結構受載時受到的外來物沖擊,因此美國NASA在1970年代和1980年代初期主要研究壓縮下沖擊強度,采用的設備是由壓縮空氣槍裝置對受壓縮載荷的復合材料試樣射出鋁丸(模擬密度相近的跑道碎石和冰雹),變量是鋁丸的速度(有壓縮空氣壓力控制)和復合材料試樣的壓縮應變(由壓縮載荷控制),試驗結果是沖擊能量~壓縮破壞應變曲線。在發表的文獻中給出了當時波音民用飛機使用的復合材料體系T300/5208的沖擊能量~壓縮破壞應變曲線(見圖1),其門檻值大約為2800με。
圖1 翼面結構典型鋪層試樣壓縮下沖擊破壞曲線
國內從1985年開始沖擊損傷的研究,在中國飛機強度所建立了壓縮下沖擊的試驗設備及開展了相關的理論和試驗研究。這項研究在航空用復合材料體系的研發和復合材料飛機結構的損傷容限設計和試驗驗證中得到應用。1980年代國內開始軍機復合材料結構的設計和研制,當時首先遇到的問題是沒有復合材料結構設計知識,特別是當時作為設計入門的國外某公司《復合材料設計手冊》中給出一組設計用材料數據(見圖2),從文獻可知,其所用材料體系是T300/5208。通常金屬結構極限載荷與限制載荷相差1.5倍,結構在極限載荷下的設計許用值一般采用材料的極限強度,因此限制載荷下使用的材料性能應是極限強度除以1.5,這組數據背離了人們的常識。當時國內軍機采用T300碳纖維,但使用國內研制的樹脂,其設計值該如何確定成了航空復合材料界的難題,航空界進行了研究和向國外專家咨詢,但始終沒有解決(關于許用值與設計值將在另文討論),但在該文件中指出了壓縮限制應變的確定與沖擊損傷有關。在此背景下,當年作者提出了確定設計值的一種工程方法:鑒于設計值與沖擊損傷有關,且國外該公司所用的材料體系是T300/5208,而文獻中提供了該材料體系典型結構鋪層試樣的沖擊能量~壓縮破壞應變曲線的門檻值為2800με,只要將國內軍機所用材料同樣結構典型鋪層試樣的沖擊能量~壓縮破壞應變曲線門檻值與其進行比較,即可確定國內軍機所用材料體系的壓縮設計值。在設計經驗比較缺乏的1990年代,根據作者提出的這種確定壓縮設計值的簡便方法,解決了軍機復合材料結構研制中遇到的一系列問題。例如成功確認了國內研制的T300/改性雙馬可用于某軍機帶整體油箱復合材料機翼;發現了國內研制的另一款T300/改性雙馬材料體系的沖擊能量~壓縮破壞應變曲線門檻值偏低的原因是未進行適當的后處理,同時證實了將其固化溫度降低到200°C仍可滿足設計要求,解決了該材料體系在工程應用中遇到的難題。
圖2 國外設計手冊給出的設計值
2.2 沖擊后壓縮強度的研究和應用
從1980年代開始,工程應用部門逐漸發現,對復合材料蒙皮結構威脅最大的是制造和使用期間遇到的工具掉落等低能量外來物沖擊,因為這種沖擊往往從外表面無法發現,但內部可能已出現大量的內部缺陷,包括分層和基體裂紋,其壓縮剩余強度有可能只有完好材料的40%或更低,此后國外對沖擊損傷的研究轉為采用落錘方法引入損傷,然后測試其含沖擊損傷試樣的壓縮強度。隨著對復合材料結構設計的經驗積累,國外已認識到結構壓縮設計值的確定應基于開孔壓縮強度和沖擊后壓縮強度(見圖3),特別是后者。
圖3 用于確定結構設計值的條件
前面提到1970年代初國際石油危機爆發,碳纖維在民用飛機的機體結構上的應用提到議事日程,美國NASA和FAA贊助了ACEE(飛機能效)計劃,當時的目標是把復合材料最終用于機翼機身等主承力結構。由于對沖擊損傷的考慮復合材料結構壓縮設計值只能取為3000~4000με,美國和歐洲在關于論證復合材料機翼方案時均指出,為使減重得到的效益超過使用復合材料帶來成本的增加,其必要條件是把壓縮設計值提高到6000με。復合材料界的共同認識復合材料沖擊后壓縮性能低的原因是樹脂的脆性,實現這一目標的關鍵是樹脂增韌,自此以后,樹脂增韌成了航空復合材料的研究重點。同時波音公司向東麗提出了研制第二代碳纖維T800的要求,具體指標是:1) 模量提高30%;2) 強度提高50%;3) 與增韌樹脂復合后其壓縮設計值由3000~4000με提高到6000~8000με;4) 用于Boeing777的垂尾。當然波音公司對T800提出的壓縮設計值研制目標最后沒有達到,目前在Boeing787的結構設計中采用的壓縮設計值僅為4000~4500με,復合材料結構降成本的途徑是通過其他設計與制造工藝技術實現的。
在ACEE計劃的贊助下為評定樹脂增韌的成果,NASA先后制訂了一系列評定樹脂增韌效果的試驗方法,這就是NASA RP1142(1985年)“NASA/Aircraft Industry Standard Specification for Graphite Fiber/Toughened Thermoset Resin Composite Materials”中給出的7項試驗標準(最初以NASA RP1092形式出現,1982年),其中最關鍵是首次提出了CAI(沖擊后壓縮強度)試驗方法,并指出,按此方法得到的CAI值大于207MPA(30ksi)即可認為是韌性樹脂。這一試驗標準的建立是基于大量的試驗研究,其中標準使用27J的能量進行沖擊,是認為這一能量代表了使用中經常可能出現的工具掉落的能量;使用12.7mm直徑沖擊頭的試驗基礎是對于固定能量的沖擊,研究表明直徑在12.7~25.4mm之間時產生的沖擊損傷最為嚴重,小于12.7mm時,易于產生目視可見的凹坑,但損傷面積比較小,而大于25.4mm時,雖然不易產生目視可見的凹坑,但也不易產生內部分層;采用6mm的試樣厚度代表了翼面結構的典型厚度,研究還表明,同樣能量下產生的沖擊損傷嚴重程度與厚度有關,試樣厚度超過~7mm時,產生內部損傷所需的能量可能超出了實際使用中可能出現的情況。NASA提出的這一CAI試驗標準奠定了目前所用確定CAI性能試驗方法的基礎。
值得指出的是,對通常的桿板殼結構,沖擊損傷不一定都是對結構安全最嚴重的威脅,當厚度小于3mm時,造成結構失效的通常是屈曲失穩破壞,沖擊損傷雖有影響,但不是致命的,外來物沖擊產生的問題多半是表面產生凹坑而引起的維修問題;當蒙皮厚度大于7mm時,使用中可能出現的沖擊能量往往不足以產生使壓縮強度急劇降低的損傷,這種區域重點要考慮的是與其他骨架結構進行機械連接,或由于意外的離散源損傷用補片進行臨時修補需要開孔而產生的開孔壓縮強度指標。對沖擊損傷格外關注的是厚度在3~7mm之間的蒙皮結構,這也是翼面結構出現面積最大的厚度范圍。
由于CAI值不僅用作評定材料性能的指標,同時也是用于結構設計確定設計值的基礎,因此碳纖維復合材料的CAI值測試越來越重要,測試的量越來越大,對CAI值的測試標準的建立和修訂一直受到了工業界特別關注。自從1985年NASA首次提出CAI的測試標準以來,已經歷了長期的試用,隨著對CAI值的理解和認識不斷深入,由初始僅作為評定樹脂增韌的標準,到目前已用于從材料研制擴展到為結構設計提供有關損傷容限能力的知識更大范圍內的數據需求,所以直至2007年才分為2個標準以D7136和D7137形式上升為ASTM D30復合材料委員會標準(即美國國家標準)。
幾十年來,沖擊損傷的研究一直是復合材料界關注的焦點,其中包括理論和工程應用研究兩部分,本文只涉及工程應用的研究。
3 CAI試驗標準的演變
沖擊后壓縮(CAI)強度實際上有兩種含義:1) 評定含損傷時的材料性能指標;2) 一般而言的復合材料層壓板受沖擊產生損傷后的壓縮強度。前者一定是對特定的層壓板,在特定條件下得到的含沖擊損傷層壓板的壓縮強度;而后者可以是任意的層壓板(包括結構)在壓縮載荷下的壓縮剩余強度。在提到CAI時通常人們的反應是一個材料性能指標。
1080年代初期人們普遍采用NASA RP1142建立的CAI測試方法,該方法的要點是:采用鋪層形式為[45/0/-45/90]6s(約6mm厚),178 mm?254 mm的矩形層壓板,用12.7mm直徑鋼沖擊頭在試樣中心以27J能量進行沖擊引入損傷,然后切割到127 mm?254 mm,用帶防失穩立柱的壓縮夾具承受壓縮載荷直至破壞,得到其壓縮強度。國內在1993年基于該標準制訂了航標HB6739沿用至今,只是考慮到國內在制造試樣時厚度控制比較差,將27J能量改為4.5J/mm。
CAI性能的研究在美國各飛機公司也大量進行,考慮到NASA的方法成本太高,因此波音公司在此方法的基礎上進行了改進,提出了更方便和節約成本的試驗標準,該方法的要點是:采用鋪層形式為[45/0/-45/90]4s(約4mm厚),150 mm?100 mm的矩形層壓板,用16mm直徑鋼沖擊頭在試樣中心以4.5和6.7J/mm能量進行沖擊引入損傷,然后直接裝在試驗夾具上承受壓縮載荷直至破壞。能量的選擇基于原來采用的27J,最初選擇27/6=4.5J/mm是與原NASA標準一致,但考慮到27J是通常遇到的外來物沖擊能量,與試樣厚度無關,因此增加了27/4=6.7J/mm的能量級別。在此基礎上美國先進復合材料供應商協會(SACMA)于1988年制定了SACMA SRM-2R-88,1994年對此又進行了修訂。SACMA的標準基本上與波音標準一致,但只保留了一個能量即6.67J/mm。由于SACMA標準比較節約,被國內廣泛采用。這一標準主要用于評定復合材料用樹脂的增韌效果,材料研制單位為證明自主研發的材料具有高CAI值,喜歡采用較低的能量,即4.5J/mm進行沖擊,但在給出數據時又不標注采用的沖擊能量,除了少數幾個專業人員外一般用戶并不清楚這里的奧妙,無人關注,從而在相當一段時間里造成了國內CAI數據的混亂。
從1990年代起CAI的試驗方法就已列入ASTM D30委員會制定新標準的計劃,但由于對CAI的認識在業內人士中并不統一,因此將SACMA標準升級為ASTM標準的工作遲遲沒有進展。直至2007年沖擊后壓縮的試驗標準才正式以D7136,“測量纖維增強聚合物基復合材料對落錘沖擊事件損傷阻抗的標準試驗方法”和D7137“含損傷聚合物基復合材料板壓縮剩余強度性能的標準試驗方法”升級進入ASTM標準行列。在D7136的范圍中指出:“當受到沖擊的試樣按試驗方法D7137/D7137M進行試驗時,通常將整個試驗順序稱為沖擊后壓縮(CAI)方法。”與原來標準相比,除保留原來的試驗用途外,增加了下述用途:“某些試驗機構可能希望將本試驗方法與D7137/D7137M一起使用,來評定含規定損傷狀態(如規定的凹坑深度、損傷尺寸等)試樣的壓縮剩余強度。”得到的性能“能為得到用類似材料、厚度、鋪層順序等制造的復合材料結構預期的損傷容限能力提供指南。”之所以在標準中增加這部分內容,是因為6.7J/mm的沖擊能量產生的損傷程度(凹坑深度)與飛機結構損傷容限設計要求中對初始損傷尺寸的定義(目視勉強可見——BVID)不一定一致(有關內容將在另文中說明)。把標準一分為二的原因還有一個考慮,即一旦得到更充分的研究后有可能使用更方便的靜壓痕方式引入損傷。CAI試驗標準的演變見表1。
表1 CAI試驗標準的演變
4 含缺陷/損傷層壓板剩余強度估算方法概述
從1970年代起就已開展了大量有關缺陷/損傷層壓板剩余強度估算方法的研究,類似于金屬,最初研究人員集中于對含裂紋和開孔層壓板在受拉伸載荷下剩余強度估算方法的研究,提出了各種各樣的估算方法,其中工程上應用最多的是Whitney, J. M和 R. J. Nuismer提出的點應力(PS)判據和平均應力(AS)判據,由于判據中增加的材料特征常數除與材料體系有關外,還與鋪層、孔徑等有關,因此工程上應用時還需輔以由試驗數據給出的大量曲線。但復合材料強度對缺陷/損傷影響最大的是在壓縮載荷下的強度降,40年來對此發表了大量的論文,但實際上進展不大,迄今尚未發現被工程應用普遍認可的方法。中國飛機強度研究所(ASRI)在2000年以前的15年間對此進行了大量的理論和試驗研究,得到了一些可喜的研究成果,由于當時國內復合材料飛機結構應用不多,損傷容限設計主要依靠試驗結果,這些成果只是以論文發表的形式存在,無緣在實踐中應用改進。目前飛機復合材料飛機結構已得到大量應用,因此本文在此給出概述,供感興趣的研究人員參考。
4.1 缺口敏感性和適用的失效判據
層壓板的鋪層形式不同時其缺口敏感性不同,所用的失效判據也不同。表2列出了不同層壓板的缺口敏感性和適用的失效判據。另外失效判據還同層壓板的破壞模式有關,表中列出的判據主要適用于纖維控制破壞模式的層壓板。
表2 層壓板缺陷敏感性和適用的失效判據
注:壓縮載荷下的失效判據僅適用于失效前不出現失穩的情況
研究表明,隨載荷增加,缺口附近會形成由分層和基體裂紋構成的損傷區,損傷區內的應力分布呈均勻化的趨勢,同時降低了缺口引起的應力集中,因此所有含缺口層壓板剩余強度的失效判據均含有反映這一現象的附加參數。
4.2 損傷影響(Damage Influence —— DI)判據
損傷影響失效判據可表述為:當缺口(或損傷)附近特征點處的加權法向應力達到層壓板的破壞強度時,含損傷層壓板出現破壞(見圖4),其數學表達式為
圖4 DI判據示意
4.3 損傷區纖維斷裂(Fiber breakage in Damage zone——FD)失效判據
損傷區纖維斷裂(FD)失效判據可表述為:當缺口(或損傷)附近特征長度l0范圍內0°層的平均法向應力(見圖5)達到單向板的極限強度時,含損傷層壓板出現破壞,其數學表達式為:
圖5 含孔層壓中缺口附近0o層的應力分布
4.4 含沖擊損傷層壓板壓縮剩余強度估算方法
本節給出兩種可供設計使用的含沖擊損傷層壓板剩余強度估算方法。
(1) 基于FD判據的估算方法這種方法的主要步驟為:
a) 實測或估算沖擊損傷;
b) 按圖6所示的原則將沖擊損傷簡化為橢圓孔,其長軸等于分層區投影圖的寬度,分層區投影圖可由無損檢測給出或用上節所述的方法計算得到;其短軸等于表面凹坑的寬度,表面凹坑的寬度可以直接測出或簡單假設為長軸的0.3;
c) 用復應力函數法或有限元方法計算得到含橢圓孔層壓板缺口附近0°層的法向應力分布;
d) 利用FD判據和含孔層壓板受壓試驗給出的特征長度l0值估算壓縮剩余強度。
圖6 沖擊損傷的分析模型
(2) 基于DI判據的估算方法基于DI判據的估算方法進行沖擊后壓縮剩余強度估算的主要步驟為:
a) 用上節所述方法確定沖擊損傷的特征損傷狀態(通常包括分層、基體裂紋和纖維斷裂)或直接用適當的無損檢測方法確定,然后用損傷數據結構(DDS)存儲損傷信息;
b) 把沖擊分層處理為具有一定厚度的子層,進行多子層的屈曲分析;
c) 利用多子層屈曲的分析結果對分層區域進行剛度折減。如果DDS內包括纖維斷裂或基體裂紋等信息,則還需要對相應損傷單元進行剛度退化處理,把損傷區處理為軟化夾雜。分層及分層區域的規定如圖7所示;
d) 利用有限元計算含軟化夾雜層壓板的應力分布;
e) 利用DI失效判據估算壓縮強度。損傷影響距離Di的含義見圖4。對含沖擊損傷的層壓板,a為計及分層沿層壓板厚度方向分布的影響系數,定義為
圖7 沖擊損傷區剖面示意圖
圖8 tdmax的計算方法
表3 ASRI和其他的剩余強度估算方法
表4 ASRI和其他方法剩余強度估算與試驗結果的比較
4.5 CDTAC軟件介紹
CDTAC(Composite Damage Tolerance Analysis Code)是一個針對復合材料結構損傷容限方面的分析軟件它是中國飛機強度研究所在含損傷層壓板剩余強度估算方法研究方面部分研究成果的幾種體現。CDTAC1.0版本的功能包括:
復合材料層壓板剛度計算機強度計算;靜力有限元(應力/應變)計算;沖擊作用下層壓板的瞬態響應分析;沖擊分層損傷的估算;含(沖擊)損傷復合材料層壓板剩余強度分析。
CDTAC是由主窗體、功能模塊及數據管理器組成的,其組織結構如圖9所示。
圖9 CDATC的組織結構
圖10是采用CDTAC軟件分析得到的沖擊損傷的層間分布及估算結果與試驗結果的比較。
圖10 CDTAC的一個算例
該軟件是德國宇航院(DLR)相關軟件的基礎,曾用于空客飛機的研制。詳可參見下列的參考文獻。
更多關于材料方面、材料腐蝕控制、材料科普等方面的國內外最新動態,我們網站會不斷更新。希望大家一直關注中國腐蝕與防護網http://www.ecorr.org
責任編輯:王元
《中國腐蝕與防護網電子期刊》征訂啟事
投稿聯系:編輯部
電話:010-62313558-806
郵箱:fsfhzy666@163.com
中國腐蝕與防護網官方 QQ群:140808414
免責聲明:本網站所轉載的文字、圖片與視頻資料版權歸原創作者所有,如果涉及侵權,請第一時間聯系本網刪除。
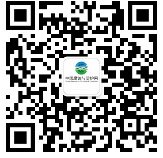
官方微信
《中國腐蝕與防護網電子期刊》征訂啟事
- 投稿聯系:編輯部
- 電話:010-62313558-806
- 郵箱:fsfhzy666@163.com
- 中國腐蝕與防護網官方QQ群:140808414