在過去的幾十年中,鋯合金包殼已經成功地應用于輕水堆(LWR),表現出了良好的抗輻照性和耐腐蝕性能。但是,鋯合金堆內應用一個主要問題是高溫時其與水蒸氣反應劇烈,當溫度大于1200 ℃時會放出大量的氫氣和熱量。日本福島核電事故后,核電的安全性再次擺在了所有核工作者的面前,如何進一步提高輕水堆核燃料元件在事故工況下的安全性和可靠性成了一個亟待解決的問題。
輕水堆核燃料元件面對的挑戰是耐事故燃料的發展,以滿足反應堆設計對燃料性能提出的更高安全裕量要求。科學家們已提出的耐事故燃料研發方向包括耐事故燃料芯體和耐事故包殼材料。耐事故包殼材料致力于改善鋯與水蒸氣的反應動力學,降低氫的釋放率,且包殼應具有良好的熱力學性能。耐事故包殼材料的發展主要體現在兩方面:一是提高鋯合金包殼的高溫抗氧化能力及強度;二是研發具有高強度和抗氧化能力的非鋯合金。本文討論的是針對前者而開展的鋯合金包殼表面涂層研究。
涂層鋯包殼應用的主要好處是經濟性,這是因為現有設備的生產能力可持續使用,易于實現鋯基涂層包殼的商業化應用。涂層鋯包殼面臨的技術挑戰是要滿足燃料包殼和組件的各種性能要求,而涂層包殼不改變燃料包殼的尺寸,這對堆內性能至關重要,特別是在正常運行的條件下。在長期運行過程中,涂層在腐蝕、蠕變和磨蝕條件下都應具有一定的穩定性。因此,需要不斷地探索、優化鋯合金表面涂層制備技術。
新技術應更易控制涂層質量,特別是涂層厚度,鋯包殼表面涂層在堆內環境下應能長期保持穩定性。
目前,國際上關于鋯合金包殼表面涂層研究還處于前期探索階段,已經開展了一系列涂層候選材料和涂層工藝的篩選工作,也進行了涂層性能表征,取得了一些成果。美國主要關注了MAX 相和陶瓷涂層材料,韓國和法國主要關注了金屬Cr 涂層材料,中國鋯合金包殼表面涂層研究還處于起步階段。
1 鋯合金包殼表面涂層研究現狀
鋯合金表面抗氧化涂層技術是一種主要的改善鋯包殼表面抗氧化能力的方法。通過在鋯合金外表面涂上一層材料以增強包殼耐磨、抗高溫氧化的能力,從而改善正常工況下以及事故工況下鋯包殼的耐事故性能。目前,國際上關于鋯合金包殼表面涂層研究已經取得了一些初步篩選結果,涂層材料主要涉及MAX 相和金屬Cr。
1.1 MAX 相涂層
美國能源部在2014 年輕水堆包殼結構材料研究建議書中重點提到了MAX 相材料的應用優勢和研究建議。美國Wisconsin 大學Benjamin 等選用了MAX相中Ti2AlC 材料作為鋯包殼表面涂層材料,涂層工藝采用了冷噴涂,涂層厚度約為90 μm。試驗結果表明,涂層與鋯基體間的結合力大于50 N,MAX 相涂層表面的耐磨性更好(如圖1)。700 ℃、60 min 高溫氧化實驗后,涂層與基體的界面間未觀察到氧化層,僅鋯合金涂層上表面有輕微的氧化,而同樣條件下Zr-4 合金的氧化膜厚度已達10 μm,這是因為涂層表面形成了致密而穩定的保護膜。模擬事故條件下的高溫氧化試驗結果表明,涂層對鋯基體具有保護作用。
Darin J. Tallman 等研究了溫度在1100~1300 ℃范圍時,MAX 相材料Ti3SiC2 和Ti2AlC 與Zr-4 合金的反應性。研究結果表明,Si 和Al 的擴散厚度均符合拋物線定律,且都形成了Zr-Si、Zr-Al 金屬間化合物,但Si 擴散至Zr-4 合金的速率比Al 擴散少一個數量級。
國內中科院寧波材料所也進行了MAX 相材料涂層研究,開展了不同涂層材料、不同涂層工藝的前期探索試驗。該所更側重于涂層機理方面的探討,指出MAX 相涂層的實質是穿衣作用,問題的關鍵在于解決氧原子向鋯基體擴散。中科院寧波材料所ZongjianFeng 等用直流磁控濺射工藝制備了Ti2AlC 涂層,并對涂層成分控制進行了研究。基體材料選擇了316L 奧氏體不銹鋼,涂層厚度約為10 μm,后分別進行了750 ℃、空氣或純水蒸汽環境中Ti2AlC 涂層樣品的高溫氧化試驗,并對氧化分層現象和氧化機制進行了討論。Ti2AlC 涂層在空氣中的氧化試驗結果顯示,樣品共形成四層:最外層是厚的Al2O3 和TiO2混合氧化物,隨后是薄的α-(Al,Cr)2O3 底層,中間是厚的Fe2O3 和TiO2 混合氧化物,內層是薄的Al2O3 富集層。而在純蒸汽水中的氧化結果顯示,樣品內部發生了氧化,Ti2AlC 涂層沒有形成清晰的氧化物層,這可能與涂層質量控制有關。因此,采用磁控濺射法制備合金表面涂層還有待進一步研究。
E.N. Hoffman 等[6]對MAX 碳化物材料用于未來核電廠的堆心應用和中子嬗變性能進行了分析。將商業純度的MAX 相材料分別置于快中子反應堆和熱中子反應堆10 年、30 年和60 年,模擬計算它們的中子活度。模擬分析結果表明,不論是在快中子堆還是在熱中子堆中,三種活化時間條件下,MAX 相材料的活度與SiC 相似,而比617 合金低三個數量級。
Ti3SiC2、Ti3AlC2 和Ti2AlC 三種MAX 相材料的中子輻照試驗結果也驗證了中子輻照模擬分析結果的合理性。Ian Younker 等對用于耐事故燃料的涂層候選材料中子性進行了評估,結果表明MAX 相涂層厚度應控制在10~30 μm,以限制中子的損耗。 Darin J.Tallman 等對Ti3SiC2 和Ti2AlC 材料在中子輻照過程中的缺陷演化行為進行了研究,表明作為高溫核能應用的MAX 相涂層候選材料,Ti3SiC2 比Ti2AlC 表現出更好的前景。Qing Huang 等[9]也對MAX 相材料Ti3SiC2 和Ti3AlC2 的抗輻照性能進行了研究,結果表明,室溫時,Ti3AlC2 的抗輻照性能比Ti3SiC2 好,且兩種MAX 相材料在600 ℃的輻照穩定性均比室溫好。
已有報道結果表明,作為耐事故包殼涂層材料,MAX 相是一種有發展前景的候選材料,但其涂層制備工藝還需進一步篩選、優化。關于MAX 相涂層包殼的堆內應用性能研究工作也有待進一步開展。
1.2 金屬Cr 涂層
為了降低高溫水蒸汽環境中鋯基合金的氧化速率,韓國原子能研究院(KAERI)Hyun-Gil Kim 等對相關涂層材料和涂層技術進行了探索。采用3D 激光涂層技術制備了鋯合金表面Cr 涂層,涂層厚度為90 μm。檢測了鋯合金表面涂層的附著力,開展了高溫氧化試驗。研究結果表明,由于中間擴散層的形成,Zr-4 合金與Cr 涂層間具有優異的粘附性。Cr涂層包殼直到4%應變前(如圖2),都未出現裂紋,滿足燃料包殼1%的應變要求。氧化試驗數據顯示,涂層鋯合金的高溫抗氧化性能明顯優于Zr-4 基體。
Jung-Hwan Park 等采用了電弧離子鍍技術制備了Zr-4 合金表面Cr 涂層,金屬Cr 靶純度為99.9%,制備過程中沉積溫度控制在473 K。1200 ℃、2000 s 水蒸氣環境中的氧化試驗結果表明,涂層鋯合金的高溫抗氧化性能明顯強于鋯合金基體(如圖3),且Cr 涂層鋯包殼具有更優異的延展性。
法國J.C.Brachet 等采用PVD 法制備了鋯合金表面金屬Cr 涂層。最新試驗結果顯示,制備的Cr 涂層十分密實,沒有缺陷(如圖4)。工藝優化后制備的Cr 涂層提高了鋯包殼的耐高溫氧化性能,在事故條件下氧化淬火后仍保留了一些殘余延展性(如圖5),為采取補救措施提供了重要的事故反應時間。
研究表明,金屬Cr 涂層耐高溫氧化性能良好,可作為耐事故鋯合金包殼的涂層候選材料。
目前,美國鋯合金表面涂層研究主要集中在MAX 相材料上,包括涂層工藝、涂層鋯合金的高溫氧化性能以及涂層材料的輻照性能等。韓國和法國主要關注了金屬Cr 涂層的制備工藝以及高溫氧化性能研究。國內對MAX 相材料的制備工藝和一些性能也進行了前期探索。由于鋯合金包殼表面涂層研究處于可行性探索階段,關于涂層應用性能研究的報道主要集中在高溫氧化和腐蝕性能上,其他應用性能的研究還有待進一步開展。
2 鋯合金表面涂層研究的幾個關鍵問題
2.1 涂層材料選擇
考慮特殊的應用環境,包殼涂層材料的選擇主要基于其物理性能。首先,涂層材料要改善鋯包殼的抗高溫氧化性能。事故條件下,涂層鋯包殼應表現出明顯低的氧化速率,能在其表面形成一層致密而穩定的保護膜,阻止或延緩氧化的進一步加劇,從而阻止鋯包殼因氧化疏松而破損。在選擇鋯包殼涂層材料時,除了考慮必備的高溫抗氧化性,還需要考察候選材料的熔點、導熱性和溫度梯度下的力學性能,以及它的中子經濟性等。
綜合考慮上述因素,Cr2O3 和Al2O3 兩種陶瓷材料表現突出,在高溫時生長速率低,非常穩定。由于其脆性,如果直接在鋯合金表面形成陶瓷層,在核燃料機械制備過程中將會很容易開裂。考慮與鋯合金的相容性,若涂層材料在高溫氧化反應時能在包殼表面形成陶瓷氧化膜則更穩定。金屬Cr 和MAX 相材料在高溫氧化后能形成致密的保護膜,是有應用前景的鋯包殼涂層候選材料。
2.1.1 MAX 相
2000 年以來,新起的MAX 相材料兼具了金屬和陶瓷的一些優良性能。MAX 相材料具有很好的塑性變形能力,這種微觀塑性及良好的導熱性能使該材料具有很好的抗熱震性能,微觀塑性也使其具有較好的抗破壞性能。表1 和表2 分別給出了一些常用MAX 相材料的典型物理性能和力學性能。
可知,Ti2AlC、Ti3AlC2、Ti3SiC2 和Cr2AlC 四種合金兼備了金屬和陶瓷材料的一些優良性能,綜合性能好。
已有研究表明,MAX 相材料是一種優異的耐高溫結構材料,表3 給出了一些常用的MAX 相材料在空氣中1000~1300 ℃氧化時的拋物線速率常數,可知這些MAX 相材料的耐高溫氧化性能均較好。一般來說,Ti3AlC2 的抗氧化性比Ti3SiC2 好,大概高2~3 個數量級,其抗氧化性好的原因在于表面氧化后形成了一層致密的Al2O3 保護膜。Ti2AlC也具有很好的抗氧化性,其氧化機制與Ti3AlC2 相同。Cr2AlC的高溫抗氧化性很好,與Ti3AlC2 相當,但其熱膨脹系數(13.3×10-6 K)與鋯基體的熱膨脹系數(7.2×10-6K)差異太大,不利于涂層質量控制。Ti3SiC2 材料的抗高溫氧化性能相對而言較差,隨著溫度的升高,氧化速率上升明顯,且生成氧化膜為熱導率很低的陶瓷材料SiO2,不利于包殼內部熱量導出。Ti3AlC2和Ti2AlC 氧化后均生成致密的Al2O3 保護膜,膜的熱膨脹系數(8.4×10-6 K)與鋯合金(7.2×10-6 K)的差異較小。Ti3AlC2 雖然比Ti2AlC 的高溫抗氧化性更好,但考慮中子經濟性,Ti2AlC 是更理想的鋯合金包殼涂層候選材料。
2.1.2 金屬Cr
金屬Cr 具有良好的金屬光澤和抗腐蝕性,常用來鍍在其他合金表面。高純金屬Cr 具有耐高溫、抗氧化、抗振動和抗蠕變等優點,可用作各種等離子和電子束濺噴的靶材,具有廣泛的應用。
韓國原子能研究院Hyun-Gil Kim對涂層候選材料的高溫氧化性能進行了研究,試驗結果見表4。
1200 ℃水蒸汽環境中氧化后,在四種候選材料中,SiO2 的耐高溫氧化性能表現最好,且Si 比Cr 的耐氧化性能更有效。他同時開展了360 ℃、18.9 MPa 模擬運行條件下的腐蝕試驗,結果表明金屬Cr 比Zr-4 合金表現出更好的耐腐蝕性能,而Si 晶片和SiO2 樣品在腐蝕條件下很快溶解,即在高溫水蒸汽環境中抗氧化性能好的材料,并不能保證其在堆內正常運行條件下的腐蝕穩定性。因此,KAERI 選擇了金屬Cr 合金作為鋯合金包殼的涂層材料。法國CAE 也致力于金屬Cr 涂層研究,調研了20 多種以Zr-4 為基體的涂層材料,包括陶瓷和金屬,發現金屬Cr 涂層最有發展潛力。已有研究表明,金屬Cr 也是一種有發展前景的鋯合金涂層候選材料。
2.2 涂層工藝選擇
為了使涂層鋯包殼在事故工況下能提供有效的保護,表面涂層必須均勻、密實,具有良好的耐高溫氧化。因此,表面涂層質量的控制非常重要,特別是膜基結合力和膜致密度,而這依賴于所采用的沉積技術和工藝參數。制備涂層的過程最好在真空保護的條件下進行,其制備效率高,最重要的是適用于燃料組件涂層制備。一般而言,涂層沉積溫度應低于鋯包殼的最終退火溫度,約500 ℃,以避免鋯合金基體微觀組織的變化。綜合比較不同表面制備技術的優缺點,電弧離子鍍技術是一種有發展前景的鋯包殼表面涂層制備工藝。
2.2.1 熱噴涂
熱噴涂包括火焰噴涂、電弧噴涂、等離子噴涂以及超音速火焰噴涂等。涂層與基體之間主要靠機械結合,界面的結合強度相對較低,因而耐沖擊性能不好。在熱噴涂過程中,會存在粉末氧化、相變、脫碳或改變原始粉末的物理和化學性質等問題,同時也會對基體產生不良的熱影響。小面積熱噴涂經濟性差,涂層厚度一般為0.5~5 mm,應盡量選擇與基體熱膨脹系數相近的涂層材料。
相對而言,等離子噴涂的涂層孔隙率更低,涂層與基體間的結合強度較高。但等離子噴涂更適宜鍍厚膜,對鋯合金表面幾十微米薄的涂層制備的質量控制較難。韓國早期采用了等離子噴涂PS(PlasmaSpraying)技術,但存在一些技術問題,如Si 涂層中形成了氣孔,由于結合力低而在界面層發生了氧化。后改進工藝將等離子噴涂制備的涂層再經激光束掃描LBS(Laser Beam Scanning)處理后,去掉了Si涂層中的氣孔,因界面形成擴散層而抑制了其氧化。但涂層制造成本急劇增加,產品質量控制困難,且PS+LBS 制備工藝復雜,該工藝未被采用。
2.2.2 冷噴涂
冷噴涂是在低溫狀態下通過高速粉末顆粒撞擊基體時發生強塑性變形而形成涂層。冷噴涂工藝具有沉積溫度低,對基體熱影響小,分布均勻,以及涂層基本無氧化現象等優點。因此,冷噴涂主要用于對溫度敏感材料、氧化敏感材料或相變敏感材料等的噴涂。冷噴涂沉積速率很高,涂層可獲得比較大的厚度。相對而言,冷噴涂涂層與基體間的結合強度不高,但可在犧牲一定的沉積速率的條件下達到較低的孔隙率和比較高的結合強度。
西安交通大學、中科院寧波材料所均具有開展冷噴涂工藝研究和涂層性能表征方法研究的基礎,前者的噴涂過程可在真空或氣氛保護下進行。冷噴涂實現幾十微米的薄涂層有一定難度,且冷噴涂過程中,涂層顆粒高速沉積對約0.6 mm 薄壁鋯管變形的影響還有待探究。冷噴涂膜層與基體間為機械結合,結合強度相對較低,可通過熱處理來提高膜基結合力。為了獲得高質量涂層,冷噴涂對粉末顆粒尺寸和雜質含量有一定要求,這也帶來粉末制備工藝研究的問題。目前,國內外MAX 相材料粉末制備工藝較成熟,可嘗試采用冷噴涂工藝進行鋯合金表面涂層工藝探索。
2.2.3 氣相沉積法
材料表面工程制備技術中。氣相沉積法分為物理氣相沉積(Physical Vapor Deposition-PVD)和化學氣相沉積(Chemical Vapor Deposition-CVD)。化學氣相沉積過程大多在相對較高的壓力和較高的沉積溫度(900~1200 ℃)下進行。考慮到涂層制備過程應盡量避免對鋯基體組織的影響,沉積溫度應盡可能的低。因此,鋯合金表面涂層制備工藝可采用沉積溫度相對較低的物理氣相沉積法。
目前,常用物理氣相沉積法主要為磁控濺射和離子鍍。磁控濺射的成膜效果好,基體溫度低,膜的粘附性強,尤其適用于大面積鍍膜。磁控濺射過程中的基體溫度是涂層微觀結構和性能的一個最重要影響因素,合適的基體溫度能提高薄膜的附著力和沉積速度。采用磁控濺射技術制備的膜層質量好,但沉積速率低,膜層相對薄。一般膜層厚度可達幾微米,但沉積幾微米的涂層耗時長,且膜層殘余應力大。采用磁控濺射法進行鋯包殼表面涂層制備的可行性還有待進一步探究。
離子鍍技術的沉積溫度明顯下降,這有利于降低或消除涂層與基體間的熱應力,改善涂層結合力。電弧離子鍍具有沉積涂層質量好、沉積速率高、繞射性強、可以大面積沉積等優點。該工藝的不足是沉積過程易產生噴射顆粒,影響膜層質量,可采用磁場過濾等技術來改善。作為陰極靶材,涂層材料必須具備一定的導電性。MAX 相和金屬Cr 材料均具有導電性,將其制成合適的靶材,即可進行鋯包殼表面涂層制備。針對鋯合金表面涂層研究,電弧離子鍍技術是一種有發展前景的涂層制備工藝。
2.3 涂層質量表征
抗高溫氧化涂層候選材料,如MAX 相和金屬Cr,均具有相對較高的熱中子吸收截面。考慮中子經濟性,鋯包殼表面涂層厚度應設計的盡量薄。在涂層制備工藝研究中,涂層質量表征非常重要。涂層結構和性能表征主要包括化學成分和相結構、微觀形貌、顯微硬度、涂層厚度和涂層附著力等。
通過比較涂層質量表征結果,優化涂層制備工藝。 一般采用X 射線衍射(XRD)分析涂層的晶體結構、涂層與基體的表面相結構變化等。采用能譜儀(EDS)分析涂層、基體、涂層與基體界面處各元素成分分布,以確定制備工藝對涂層成分、相結構的控制是否滿足技術要求。
采用掃描電鏡(SEM)觀察涂層表面以及界面形貌,包括氣孔、表面形貌、組織結構和涂層厚度等,分析涂層分布的均勻性。從涂層斷面測量其厚度時,必須防止金相拋光時造成斷面試樣的倒角。孔隙率是表征涂層密實度的度量,它是影響涂層耐腐蝕性的重要指標。采用硬度儀檢測能反映涂層性能的顯微硬度。
涂層附著力是評價涂層質量最關鍵的性能指標,常規檢測方法包括壓痕法、劃痕法和拉伸法等。不論是在反應堆正常運行還是事故條件下,鋯包殼管發生環向變形時涂層都應保持其完整性。室溫時,針對涂層鋯包殼管可采用環向張力及壓縮試驗來評估涂層與基體間的結合強度。
2.4 涂層鋯包殼關鍵應用性能研究
涂層質量對鋯包殼抗腐蝕性能有明顯影響。對同一種涂層材料,涂層致密度越好,孔隙率越低,涂層鋯包殼的抗腐蝕性能就越好。鋯包殼材料在反應堆中會發生蠕變、疲勞和受熱沖擊等行為,因此,涂層與基體間的結合強度的好壞將直接影響涂層技術是否能夠用于鋯合金包殼材料研究。
好的涂層質量是為了更好地滿足鋯合金包殼的應用性能要求。將涂層鋯包殼應用性能研究結果及時反饋給涂層制備工藝,以不斷優化制備工藝參數,獲得高質量表面涂層。考慮涂層質量的影響,有必要對鋯合金涂層堆外關鍵應用性能進行研究,主要關注涂層鋯包殼在反應堆運行過程中是否能實現涂層與鋯基體間的協調一致性。
2.4.1 高溫氧化性能
提高鋯包殼抗高溫氧化性能是耐事故燃料包殼發展的關鍵。因此,首先需要研究涂層鋯合金的高溫氧化性能。采用綜合熱分析儀進行涂層鋯合金的高溫氧化性能研究,試驗過程通入水蒸氣流,溫度范圍為700~1300 ℃。根據實驗結果分析涂層鋯合金的氧化動力學曲線,采用顯微鏡和掃描電鏡觀察樣品表面氧化膜的組織形貌,采用能譜分儀分析氧化膜成分。
2.4.2 腐蝕性能
在反應堆中長期服役的鋯包殼材料需要具有良好的耐腐蝕性能。在靜態高壓釜中進行涂層鋯合金的腐蝕試驗,其試驗結果分析方法同高溫氧化性能中所述,主要包括氧化動力學曲線研究和氧化膜表面形貌和成分分析。
2.4.3 熱沖擊性能
耐事故包殼材料應具有良好的抗熱沖擊能力,在事故條件下不發生破裂,以避免放射性裂變產物的釋放。試驗是將樣品在高溫、高壓水蒸氣環境中保持一段時間后使其迅速冷卻。采用微觀顯微鏡和掃描電鏡觀察樣品表面組織形貌及涂層與基體間的結合情況,分析涂層鋯合金的抗熱沖擊性能。
2.4.4 蠕變性能
與鋯基體比較,進行涂層鋯合金的蠕變性能研究,分析溫度、應力對涂層鋯合金耐蠕變性能的影響。試驗過程中,觀察涂層是否會出現起皮、脫落的現象。采用掃描電鏡觀察端口組織形貌,分析涂層與基體間的變形協調性。
3 結語
鋯合金包殼表面涂層研究作為耐事故燃料發展的一個主要方面,具有制造經濟性好,易于實現商業化等優點。目前,國際上鋯合金表面涂層技術研究還不成熟,處于不斷論證的探索階段。對已有涂層材料和涂層工藝研究的系統調研,為我國鋯合金表面涂層研究工作奠定良好的基礎。作為涂層候選材料,Ti-Al-C 系MAX 相材料和金屬Cr 應用前景很好。鋯合金包殼涂層材料和涂層工藝的選擇是一個復雜的過程,需要根據后續涂層關鍵應用性能研究結果進行反復驗證。總而言之,國際上關于鋯合金表面涂層技術研究還沒有完全成熟,處于多方探索和不斷論證階段,這也為我國鋯合金表面涂層技術研究帶來了機遇和挑戰。
更多關于材料方面、材料腐蝕控制、材料科普等方面的國內外最新動態,我們網站會不斷更新。希望大家一直關注中國腐蝕與防護網http://www.ecorr.org
責任編輯:王元
《中國腐蝕與防護網電子期刊》征訂啟事
投稿聯系:編輯部
電話:010-62313558-806
郵箱:fsfhzy666@163.com
中國腐蝕與防護網官方 QQ群:140808414
免責聲明:本網站所轉載的文字、圖片與視頻資料版權歸原創作者所有,如果涉及侵權,請第一時間聯系本網刪除。
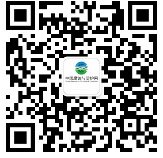
官方微信
《中國腐蝕與防護網電子期刊》征訂啟事
- 投稿聯系:編輯部
- 電話:010-62313558-806
- 郵箱:fsfhzy666@163.com
- 中國腐蝕與防護網官方QQ群:140808414