熱噴涂可磨耗封嚴涂層(簡稱封嚴涂層)被廣泛應用在航空發動機的風扇、壓氣機和渦輪等部位。在發動機運行過程中,葉片尖端對封嚴涂層產生刮削作用,從而減小發動機徑向氣流間隙,減少發動機內部氣體泄漏,獲得最大壓差,顯著提高航空發動機效率并降低油耗。數據顯示,航空發動機的渦輪葉尖間隙與葉片長度比每增加 1%,發動機整體效率下降 1.5%,油耗上升 3% ;壓氣機徑向間隙每增加 0.076mm,發動機的單位油耗量增加 1% 。
航空發動機用可磨耗封嚴涂層在實際工作中與葉片、篦齒等零件刮磨,通過犧牲自身達到氣路封嚴,保護葉片。可磨耗封嚴涂層由起支撐作用的金屬相、潤滑作用的非金屬相和降低涂層硬度的孔隙組成;通常采用等離子噴涂或火焰噴涂工藝方法制備,為底層 / 面層雙層結構,保證涂層結合力的同時又起到封嚴作用。可磨耗封嚴涂層的工作環境及服役特點決定了其具有質軟、多孔、多相、多層等組織結構特點。
隨著海上和沿海地帶空軍防務力量的增加,越來越多的可磨耗封嚴涂層需在空氣濕度大、鹽堿重的惡劣環境中服役,然而到目前為止,航空發動機可磨耗封嚴涂層的研究仍主要集中在耐沖蝕性、可磨耗性等服役性能的提高,在涂層設計方面缺乏耐蝕性的考慮,導致現役的封嚴涂層存在較大的海洋環境腐蝕隱患。雖然對發動機結構件腐蝕性能的研究已經有所報道,但目前針對可磨耗封嚴涂層腐蝕問題的研究報道還很少,尚未檢索到國外相關資料。
國內科研院所也是近些年才開展相關研究,尚未形成系統。中科院金屬所雷兵以 Al-BN,CuAl-NiC 和NiCrAl-NiC 3 種涂層為代表,針對封嚴涂層模擬實際工況開展腐蝕行為研究,得出 Al-BN 主要發生電偶腐蝕,各層之間的電化學性質不匹配是導致嚴重電偶腐蝕的原因;CuAl-NiC 和 NiCrAl-NiC 在中溫鹽和水蒸汽綜合作用環境下則發生嚴重的整體腐蝕破壞 。中科院過程工程研究所針對 Ni-C、TiAl-BN 的耐腐蝕性能開展研究,得出 Ni-C 涂層在腐蝕環境中,在表面和內部形成宏觀腐蝕電池,加速了涂層內部金屬相的腐蝕 ;TiAl-BN 復合涂層在中性鹽霧腐蝕環境中發生鈍化現象,比 Al-BN涂層更耐腐蝕 。
封嚴涂層腐蝕研究現狀
由于國外對航空發動機涂層腐蝕問題的研究保密,對于不同狀態下封嚴涂層的腐蝕行為研究尚無文獻報道。目前可查到資料僅為CFM56-7 型發動機封嚴涂層腐蝕失效破壞實例(圖 1)。這臺裝配于波音 737 的 CFM56-7 發動機一級壓氣機的 Al 基封嚴涂層內部結構因腐蝕而完全破壞,涂層分層,并發生整體開裂、剝離,失去封嚴效果。
封嚴涂層的腐蝕失效形式對發動機的安全服役存在著嚴重的安全隱患。首先是難以發現,腐蝕通常發生在涂層內部,常規檢測、觀察不易發現。其次危害嚴重,腐蝕破壞涂層在發動機運行過程中一旦脫落,將被高速氣流吸入發動機內部,嚴重時可能毀壞發動機內部零件,造成安全事故。
中科院金屬研究所盧旭陽等人研究(NiCoCrAlYSiB+AlSiY)涂層在高溫及低溫熱腐蝕條件下的腐蝕行為,發現(NiCoCrAlYSiB+AlSiY)復合涂層相對于單一的 NiCoCrAlYSiB涂層具有更好的抗高溫熱腐蝕能力,腐蝕環境中 NaCl 的存在會加劇腐蝕進程。
在耐磨涂層的腐蝕行為研究中,有學者對 WC-CoCr、FeCrSiB 涂層進行研究,發現在 NaCl 溶液和 HCl 溶液中,WC-CoCr 涂層的耐腐蝕性明顯優于鍍鉻涂層,但在 NaOH 溶液中,鍍鉻涂層發生劇烈鈍化形成保護膜,WC-CoCr 涂層的耐腐蝕性弱于鍍鉻涂層。FeCrSiB 涂層與 WC-CoCr 涂層類似 ,在中性和酸性的環境中耐蝕性能優于鍍鉻涂層,但耐堿性溶液腐蝕能力不如鍍鉻涂層。在中性和酸性腐蝕環境中,FeCrSiB 腐蝕過程可分為活性溶解、鈍化、過鈍化 3 個步驟,鈍化保護作用能有效提升 FeCrSiB 耐蝕性。
針對航空發動機用可磨耗封嚴涂層的腐蝕機理報道不多,目前北京科技大學許存官及中科院過程工程研究所杜令忠等人采用掃描電鏡觀察結合能譜分析等方式對火焰噴涂的 Ni-C 涂層進行了鹽霧腐蝕行為及電化學過程研究 。結果表明,在NaCl 溶液中 Ni-C 封嚴涂層主要發生電偶腐蝕,溶液中的氧濃度是影響涂層腐蝕的重要因素,腐蝕速率隨氧濃度的提升而加快。同時,由于電偶腐蝕的作用,480h 后涂層結合強度下降。分析認為,由于孔洞結構封閉使涂層內外物質交換受阻,涂層自身形成宏觀電化學腐蝕電池,加劇了涂層內部鎳金屬相的腐蝕過程。中國科學院過程工程研究所的研究中比較了 TiAl-BN 與 Al-BN 涂層,TiAl-BN 粉末材料為類球形,BN 作為核心外部包覆 TiAl 合金粉末,通過試驗得出在封嚴涂層中加入 Ti 元素可以有效提升涂層的腐蝕電位,增強涂層的耐蝕性。
熱噴涂涂層腐蝕機理
1 涂層在海洋環境中的腐蝕規律
航空發動機在飛行和停放過程中會遇到各種不同的環境,根據結構腐蝕調查,發動機在不同環境中的腐蝕特點不盡相同,但主要發生在海洋大氣區內,可以得到如下規律 :
(1)沿海地區的腐蝕比內地嚴重,離海岸越近越嚴重;(2)大氣污染嚴重地區的腐蝕比其他地區嚴重;(3)南方沿海的腐蝕比其他沿海地區嚴重;(4)在多雨水、多鹽霧或空氣濕度大、溫度高的地區腐蝕比較嚴重;(5)服役日歷年限長的腐蝕比服役時間短的嚴重;(6)連續長時間停放的腐蝕比經常使用和維護的嚴重。
在實驗室研究階段得出 ,常溫水溶液環境下,部分封嚴涂層的腐蝕速率隨環境氯離子濃度增加而增加,隨溫度的升高而加快,如 Al-BN涂層;在中高溫且潮濕環境下,涂層中金屬相抗氧化能力弱是引發涂層腐蝕的主要因素,石墨相的存在是加速封嚴涂層金屬基腐蝕速率的又一因素,如 CuAl-NiC、NiCrAl-NiC涂層。
2 涂層在海洋環境中的腐蝕分類及腐蝕機理
按腐蝕發生的發動機服役狀態分類,可分為飛行環境和停放環境。
據統計,航空發動機服役壽命的 90%為停放狀態,發動機在加工、裝配、運輸、運行、存放和修理過程中的任何一個環節都可能發生腐蝕,尤其是在靠近沿海地區的存儲及服役環境下,腐蝕問題將更為嚴重。
2.1 停放期間涂層腐蝕
發動機在停放時 , 從封嚴涂層失效機理可主要分為閉塞區腐蝕和電偶腐蝕。
(1)閉塞區腐蝕。
可磨耗封嚴涂層具有連續的多孔結構,在腐蝕性環境中,腐蝕介質能夠通過孔隙向涂層內部滲透,其腐蝕機理與縫隙腐蝕以及點蝕相似。它們的共同特點是在縫隙、蝕孔內部存在“閉塞電池”。由于閉塞的幾何條件,縫隙、孔內外存在對流和擴散障礙,隨著腐蝕的進行閉塞區內溶液會發生貧氧、酸化、Cl - 富集等變化,腐蝕條件惡化。閉塞區內外電化學條件的差異產生自催化加速腐蝕效應。
(2)電偶腐蝕。
封嚴涂層體系一般由可磨耗表層、連接層、基體 3 部分構成,由于不同層的材料不同、結構不同、開路電位不同,因此在不同層之間、同層的不同材料之間形成電位差,滿足電偶腐蝕產生的熱力學因素;封嚴涂層因其服役性能要求具有多孔,在不同層之間由于孔隙存在可以形成導通的回路,在高電位區域與低電位區域之間形成暢通的電子通道和離子通道,滿足電偶腐蝕產生的動力學因素;當熱力學和動力學條件同時滿足時,即可發生電偶腐蝕。
以航空發動機壓氣機用 Al-BN封嚴涂層為例,在含氯介質中,涂層會發生 Al-BN 表層、NiAl 連接層和不銹鋼基體 3 部分的電偶腐蝕。在3部分的腐蝕電偶中,Al-BN為陽極,優先腐蝕。通常發生電偶腐蝕的涂層,會引起表層或連接層甚至基體的破壞,從而導致整個系統涂層的破壞以及結合強度的降低。
在停放期間,海洋環境中的真菌和霉菌沉積在金屬表面,加速了金屬的腐蝕。另外,航空發動機在停放時將受到廢氣和尾氣中的硫化物、氮氧化物與海洋鹽霧組合成的pH 值為 2.4~4.0 的酸性潮濕層腐蝕,再形成酸性液膜,加速了涂層的失效。
2.2 發動機運行時腐蝕機理
航空發動機在服役狀態下,通常面臨中溫鹽和水蒸汽綜合作用腐蝕,即在航空發動機運行時,外部氣體被壓入發動機中,隨著壓氣機級數的升高,氣壓和氣體溫度隨之升高,在壓氣機區域溫度可達 300~700℃。當發動機在海洋環境下服役運轉時,大氣中的鹽分將隨氣體被吸入發動機中,沉積在壓氣機葉片和機匣內表面,形成沉積鹽膜。在壓氣機區域溫度下,沉積鹽以固態形式存在,一旦氣氛中含有水蒸汽,涂覆于壓氣機部位的封嚴涂層將遭受中溫固態鹽膜和水蒸汽協同作用下的腐蝕,造成封嚴涂層嚴重的腐蝕失效。
未來發展展望
1 設計新型抗腐蝕涂層材料體系
熱噴涂封嚴涂層中使用的復合粉體材料根據使用部位的不同而多種多樣,表 1 列出航空發動機上常見的可磨耗封嚴涂層。
隨著我國航空發動機服役環境和區域范圍的增加,對熱噴涂可磨耗封嚴涂層的抗海洋腐蝕能力提出了明確要求,現有涂層材料體系已經不能滿足實際使用,發展新型的抗海洋腐蝕涂層材料迫在眉睫。基于電化學腐蝕的特點,選擇電極電位比部件基體材料低的的元素形成涂層,充當電化學腐蝕電池中的陽極,先失去電子不斷被腐蝕,而電位較高的基體材料成為陰極,不斷得到電子而受到保護。由于石墨具有較高的自腐蝕電位,會引起封嚴涂層內部金屬相與非金屬相間的電偶腐蝕,導致涂層的結合強度急劇下降;六方氮化硼具有極小的導電性,可以有效抑制涂層內不同相組成間發生的電偶腐蝕,因此中科院過程工程研究所采用六方 BN替代石墨作為潤滑相材料,開發新型耐腐蝕涂層粉末。
2 優化涂層結構
目前,常見封嚴涂層體系為基體→粘接層(底層)→功能層(面層),現階段航空發動機粘接層通常采用鎳鋁或鎳鋁鎢,面層根據涂層服役工況進行選擇。當前航空發動機用封嚴涂層在選材時通常僅考慮涂層的使役性能,對涂層的耐腐蝕性能并未納入其中。基體與粘接層、粘接層與功能層之間的電勢對涂層的腐蝕速率有很大影響,優化涂層基體 / 粘接層/ 功能層 3 者之間的電化學性能匹配,對熱噴涂封嚴涂層的耐腐蝕性能具有重要的意義。有研究表明,將Ni5Al 粘接層替換為 Ni20Al 粘結層,可以降低涂層體系電偶腐蝕過程中的電偶電位,從而抑制鋁基封嚴涂層的自發點蝕行為,降低涂層體系腐蝕速率。
3 加強發動機存放期間管理
航空發動機服役壽命的 90% 為停放狀態,發動機存放期間的防腐蝕管理就變得尤為重要。當發動機在濕熱的海洋性氣候下停放時,盡量使發動機處于陰涼通風的環境中,降低環境的濕度,降低涂層腐蝕速率。在發動機停放期間,對封嚴涂層表面進行適當的清洗維護,并將發動機置于通風陰涼處,可以在一定程度上減緩已經服役封嚴涂層的腐蝕速率。
在航空發動機停放場所,存放封嚴涂層模擬試驗件,跟蹤發動機內涂層腐蝕情況。在預測發動機內涂層腐蝕情況的同時,又可以積累發動機存放期間涂層腐蝕數據,避免因未發現涂層腐蝕而引發飛行事故。
4 建立熱噴涂涂層腐蝕性能測試方法
豐富封嚴涂層性能檢測手段,完善封嚴涂層性能評價體系和選材體系,建立封嚴涂層模擬實際工況試驗裝置,是滿足熱噴涂工藝以及穩定批量供應和高質量批量生產的必要條件。目前,金屬材料耐腐蝕性測試可依據 ASTM G76 標準進行,而涂層的腐蝕性能測試標準及主要性能指標尚未頒布。因涂層的多孔、多相、多層結構,在腐蝕過程中呈現出多元性、復雜性等特點,不能與金屬材料測試標準混用,需編制涂層專用腐蝕測試標準。目前,航空行業部分研究院所及制造單位正在累積相應數據,為編制涂層腐蝕性能測試標準進行技術儲備。
結束語
隨著我國航空事業的飛速發展,尤其對艦載飛機、沿海飛機等需求激增,航空發動機零部件的海洋環境腐蝕損傷及其防護研究已成為熱點。需要涂層體系設計、涂層材料開發和工藝研制等領域的技術人員攜手攻關,通過大量嚴苛的試驗測試,完成耐海洋腐蝕熱噴涂可磨耗封嚴涂層的開發。同時,對航空發動機封嚴涂層在海洋環境中腐蝕失效機理研究、服役壽命預測等方面均需加大科研力度,以便為設計部門提供可靠的數據支持及解決方案。另外,相關科研單位應著手準備建立涂層在海洋環境中腐蝕測試方法,完善封嚴涂層的海洋腐蝕性能測試技術,確保航空發動機封嚴涂層在海洋環境中服役壽命的設計要求。
更多關于材料方面、材料腐蝕控制、材料科普等方面的國內外最新動態,我們網站會不斷更新。希望大家一直關注中國腐蝕與防護網http://www.ecorr.org
責任編輯:王元
《中國腐蝕與防護網電子期刊》征訂啟事
投稿聯系:編輯部
電話:010-62313558-806
郵箱:fsfhzy666@163.com
中國腐蝕與防護網官方 QQ群:140808414
免責聲明:本網站所轉載的文字、圖片與視頻資料版權歸原創作者所有,如果涉及侵權,請第一時間聯系本網刪除。
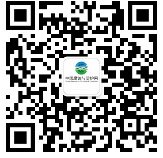
官方微信
《中國腐蝕與防護網電子期刊》征訂啟事
- 投稿聯系:編輯部
- 電話:010-62313558-806
- 郵箱:fsfhzy666@163.com
- 中國腐蝕與防護網官方QQ群:140808414