TC18 鈦合金是前蘇聯于20 世紀70 年代開發的一種綜合性能優良的航空結構材料,它具有高強度、高韌性、高淬透性以及良好的焊接性能。目前,國外已經廣泛地使用TC18 鈦合金制造大型飛機起落架、機身對接框等結構件。將該類鈦合金用于飛機起落架結構件來代替高強鋼,可使飛機整體減重15%~20%。由于TC18 鈦合金擁有一系列優異的性能,其使用將會更加廣泛,在起落架上也將會有越來越多的應用。然而起落架在沿海地區長時間服役時會承受嚴重的海洋性鹽霧腐蝕和摩擦磨損,因而需采用表面防護技術提高其表面耐蝕性能。目前已有研究報道各種表面防護技術替代電鍍硬鉻。經綜合評價,HVOF噴涂WC-Co涂層技術被認為最有可能替代電鍍硬鉻。此外,HVOF噴涂具有相對高的粉末粒子飛行速度和相對低的噴涂溫度的優勢,因而可以制備出綜合性能更優的WC-Co涂層。
本文以TC18 鈦合金為基體,采用HVOF 制備WC-12Co 涂層和WC-10Co4Cr 涂層。使用SEM,EDS和XRD分析試樣腐蝕前后的微觀結構,元素分布和物相組成,通過顯微硬度測試和納米壓痕測試分析涂層與基體的顯微硬度和塑韌性,采用電化學腐蝕測試和中性鹽霧腐蝕測試分析基體及噴涂試樣的耐蝕性能。
1 實驗方法
選用粒徑為15~45 μm 的WC- 12Co 和WC-10Co4Cr 噴涂粉末,基材為TC18 鈦合金,其合金元素含量(質量分數,%)為:Al 5.10,Mo 5.14,V 5.06,Cr 0.93,Fe 0.98,C 0.025,H 0.005,N 0.02,O 0.15,余量為Ti。采用國產XM-8000超音速火焰噴涂設備制備WC-12Co和WC-10Co4Cr涂層。噴涂燃料選用航空煤油,氧氣作為助燃氣,氮氣為送載氣。采用的工藝參數如下:距離為35 cm,送粉速率為1.5 g/min;燃油流速為25 L/h,壓強為12.55 MPa;氧氣流速為565 L/h,壓強為14.95 MPa;氬氣流速為7.5 L/h,壓強為0.8 MPa。在噴涂前使用丙酮和酒精對基體表面進行超聲震蕩清洗,采用60 目的剛玉對基體表面進行噴砂粗化處理,噴涂涂層厚度約為150 μm,噴涂后的試樣需使用不同型號金相砂紙依次打磨并使用金剛石研磨膏拋光。并使用表面粗糙度測試儀測量試樣表面粗糙度Ra均小于0.2 μm。
超顯微硬度計為正四棱錐金剛石壓頭,測試參數為:加載載荷為300 g,保持時間為15 s,每個試樣測量10 個點取算術平均數。為了分析涂層和基材的塑韌性,使用島津DUH-W201 型超顯微硬度計測量其彈性模量,該納米壓痕儀采用金剛石正三角錐壓頭,測試參數為:載荷500 mN,加載速度3.530394 mN/s,保持時間為10 s。為了分析與評價基體與噴涂試樣的耐腐蝕性能,本文采用電化學測試法和中性鹽霧腐蝕試驗。
使用CHI660D型電化學工作站測試涂層和基體在3.5%(質量分數)NaCl 溶液中的動電位極化曲線,并進行對比分析。使用AB膠封裝試樣并保留1 cm2的工作面積,封裝后使用丙酮、無水乙醇、去離子水進行清洗,再進行電化學腐蝕測試。電化學工作站采用標準三電極體系,工作電極為測試試樣,鉑電極為輔助電極,參比電極為飽和甘汞電極。極化曲線電位掃描范圍為-1~1 V,掃描速率5 mV/s。
采用MC-952C 型鹽霧試驗機對試樣進行中性鹽霧腐蝕測試,測試周期為30 d。根據GB6468-86中性鹽霧腐蝕標準,實驗采用5%(質量分數)的NaCl溶液,測量鹽霧箱內溶液pH值為6.9,鹽霧箱內溫度保持在35 ℃左右。鹽霧腐蝕實驗參數:噴霧速率為0.025 mL·cm-2·h-1,壓力為0.07~0.15 MPa,相對濕度為(94±4)%。試樣經鹽霧腐蝕不同時間段(3,6,12,18,24 和30 d)后使用去離子水清洗稱重,同時由于噴涂涂層經鹽霧腐蝕后并不能形成連續致密的保護膜而易于脫落,因此采用腐蝕失重法評定WC-12Co涂層和WC-10Co4Cr 涂層的耐腐蝕性能。鹽霧腐蝕后的試樣使用自帶能譜(EDS,XMS60S)的掃描電鏡(SEM,Quanta200)和X射線衍射儀(XRD,BurkerD8-ADVANCE)進行檢測與分析。
2 結果與討論
2.1 WC-Co涂層微觀形貌和物相組織
從圖1a 和c 可以看出,兩種WC-Co 涂層與TC18 鈦合金基體結合良好,WC-12Co 涂層厚度約為150 μm,WC-10Co4Cr 涂層厚度約為170 μm。能譜分析結果(圖1b 和d)顯示兩種涂層中各元素質量分數與其噴涂粉末中各元素質量分數基本一致,且不存在其他雜質元素,說明噴涂粉末純凈,在噴涂過程中實驗條件良好而未被其他雜質元素污染。從低倍橫截面顯微結構SEM圖可以看出,兩種涂層組織均勻致密,沒有明顯的分層現象。在高倍放大的顯微組織中,灰白色大小不一的多邊形顆粒為WC顆粒,四周包裹著顏色較深的粘結相金屬。硬質WC顆粒均勻地鑲嵌在粘結相中,從而確保涂層較高的硬度,Co和CoCr作為粘接相將WC顆粒粘結在一起,使得兩種涂層具有良好的韌性。
2.2 TC18基體和WC-Co涂層力學性能
圖2a 和b 分別為WC-12Co 和WC-10Co4Cr 涂層的XRD圖譜。從圖中可以看出,硬質相WC為兩種涂層的主要相,且其峰位基本一致,同時該硬質相的存在使得涂層擁有較高的硬度和耐磨性。在WC-10Co4Cr 涂層XRD圖譜中出現了較弱的CoCr 相衍射峰,表明在熱噴涂過程中Cr 和Co 形成了固溶體。兩種涂層均存在W2C相,在WC-12Co涂層中還出現脆性η相(Co6W6C),說明在HVOF 噴涂過程中WC存在一定的脫碳現象,在相同的熱噴涂工藝參數下,WC-10Co4Cr 粉末較WC-12Co 粉末熔化更充分、脫碳程度更低。
圖3a 為基體與涂層表面平均硬度值矩形圖,TC18 基體平均顯微硬度為HV0.3336.4,兩種涂層的平均顯微硬度都明顯高于基體,其中WC-12Co涂層為HV0.31177.2,WC- 10Co4Cr 涂層為HV0.31258.8。
WC-Co 涂層的高硬度主要是由于涂層中大量分布的硬質WC相,HVOF 具有相對低的噴涂速率和相對高的噴涂溫度的特點,可以有效地降低WC在噴涂過程中脫碳分解和氧化,因而涂層中WC顆粒的組織和形態基本得到保留而顯示出高的硬度,高的表面硬度意味著兩種WC-Co 涂層擁有良好的耐磨性。
納米壓入測試結果如圖3b 所示,可以看出,WC-12Co 和WC-10Co4Cr 涂層的加載-卸載曲線與橫坐標軸所圍成的面積均小于TC18 鈦合金基體的,說明兩種涂層的形變功均小于基體的形變功,即WC-Co涂層較TC18 基體更難發生塑性變形。彈性模量通??梢杂脕肀碚魍繉拥膹椥宰冃涡袨椋瑴y得WC-12Co 涂層的彈性模量值為355 GPa,WC-10Co4Cr 涂層的彈性模量值為391 GPa,基體的彈性模量值則為102 GPa,這表明WC-Co 涂層抵抗彈性變形的能力遠大于TC18鈦合金,即剛度更大。
2.3 電化學腐蝕性能
圖4 所示為WC-Co涂層和TC18 基體在3.5%的NaCl 溶液中的電化學極化曲線。兩種涂層的電化學極化曲線變化相類似,但與基體存在明顯不同,WC-Co 涂層極化曲線隨著測試電位的增加呈現指數增長趨勢,然后趨于平緩并基本保持不變。這個過程中涂層首先受到腐蝕溶液的腐蝕,然后在其表面形成鈍化膜,因而腐蝕電流密度基本保持不變[13]。電化學測試結果表明,TC18 鈦合金基體、WC-12Co 涂層和WC-10Co4Cr 涂層的自腐蝕電位及腐蝕電流密度分別為-0.167 V,7.136×10-9 A/cm2;-0.621 V,5.257×10- 7 A/cm2;-0.495 V,1.573×10- 7 A/cm2。WC-12Co涂層和WC-10Co4Cr 涂層與TC18 基體相比,自腐蝕電位分別降低了0.454 和0.328 V。自腐蝕電位是電化學腐蝕熱力學參數,表征材料在溶液中失電子難易程度,由此表明兩種涂層熱力學穩定性低于基體,而且兩種WC-Co 涂層的腐蝕電流密度高于基體腐蝕電流密度兩個數量級。這都說明涂層相對于基體更容易被腐蝕,然而由于兩種WC-Co涂層均勻致密并緊密的覆蓋在TC18 鈦合金基體表面,因而對基體具有一定的物理保護作用。同時在電化學腐蝕過程中WC-Co涂層最先受到腐蝕,并且在涂層表面形成致密的氧化膜,因此能有效地阻止進一步的腐蝕而保護TC18 鈦合金基體。與WC-12Co 涂層相比,WC-10Co4Cr 涂層具有相對高的自腐蝕電位和低的腐蝕電流密度,因而擁有更好的耐蝕性能而能夠更好地保護基體。
2.4 鹽霧腐蝕性能
圖5 所示為兩種WC-Co 涂層在NaCl 中性鹽霧中腐蝕失重隨時間變化的情況。從腐蝕失重曲線分析可以看出WC-12Co 涂層的失重量明顯大于WC-10Co4Cr 涂層,同時兩種涂層在5%NaCl鹽霧中腐蝕速度較為平均,失重變化曲線大致呈線性變化。
根據失重試驗數據計算得出,WC-12Co 和WC-10Co4Cr 涂層的單位面積平均腐蝕速率分別為0.2 mg·cm-2·h-1和0.033 mg·cm-2·h-1。這表明在NaCl腐蝕介質中,WC-10Co4Cr 涂層的耐蝕性高于WC-12Co涂層。
2.5 WC-Co涂層鹽霧腐蝕物相組織及形貌
圖6a 和b 是WC-12Co 涂層和WC-10Co4Cr 涂層鹽霧腐蝕30 d 后的XRD圖譜。從圖6a 可以看出,WC-12Co涂層腐蝕層主要含WC相和Co相,而在腐蝕過程中生成的CoO、WO3氧化膜已不存在,這是由于這兩種生成的氧化膜耐蝕性能不強,在鹽霧腐蝕過程中易出現點蝕而逐漸破壞脫落。WC-10Co4Cr涂層經鹽霧腐蝕后的物相組織如圖6b 所示,涂層主要含有WC相、CoCr2O4和Cr2O3相,但在腐蝕過程中形成的穩定Cr2O3氧化物并不能完整的覆蓋于涂層表面,裸露的Co 粘結相和WC會發生腐蝕,生成的CoO和WO3并不穩定而會很快破裂脫落。
WC-Co 涂層經30 d 中性鹽霧腐蝕后的截面微觀形貌如圖7a 和c 所示,可以看出,兩種涂層中腐蝕介質并沒有進一步向內擴散,涂層的內部保持均勻致密而并未受到腐蝕,同時WC-12Co涂層的腐蝕層厚度明顯大于WC-10Co4Cr 涂層腐蝕層厚度。從圖7a 可以看出WC-12Co涂層腐蝕層形貌非常粗糙,存在著大量的裂紋、孔洞等缺陷。結合腐蝕區域EDS分析(圖7b)和物相組成分析(圖6a),這是由于當腐蝕介質接觸到涂層時,優先腐蝕自腐蝕電位更高的Co 粘結相,而且涂層中的Co6W6C 相也易于腐蝕而形成CoO 和WO3 腐蝕產物,伴隨著粘結相不斷腐蝕,最終導致WC顆粒和CoO、WO3腐蝕產物大量的脫落,形成裂紋、孔洞等缺陷。圖7c 所示為WC-10Co4Cr 涂層截面腐蝕形貌,與WC-12Co 涂層相比,腐蝕層厚度更小、孔洞裂紋等缺陷較少、形貌更為平整。結合腐蝕區域EDS分析(圖7d) 和XRD物相分析(圖6b),這是由于在腐蝕過程中形成了穩定的Cr2O3陶瓷鈍化相,從而提高了WC-10Co4Cr 涂層中粘結相的自腐蝕電位,延緩了腐蝕介質向內部擴散。因此,兩種WC-Co 涂層都能有效地提高TC18 鈦合金在NaCl 鹽霧中的耐蝕性能,其中WC-10Co4Cr涂層顯示出更好的耐鹽霧性能。
3 結論
(1) 使用HVOF技術在TC18 鈦合金上制備了組織致密、缺陷較少的WC-12Co 涂層和WC-10Co4Cr涂層,涂層與基體結合良好。兩種涂層的顯微硬度和彈性模量均明顯高于基體,其中WC-10Co4Cr 涂層擁有更高的顯微硬度和彈性模量。
(2) 兩種WC-Co涂層在電化學腐蝕測試過程中表面均能形成氧化膜而阻止腐蝕溶液向內部腐蝕,有效地提高了基體耐蝕性,且WC-10Co4Cr 涂層顯示出更優的耐蝕性能。
(3) WC-12Co 涂層的腐蝕失重、平均腐蝕速率和截面腐蝕層深度均明顯大于WC-10Co4Cr 涂層,WC-Co涂層的腐蝕機理是腐蝕介質不斷腐蝕涂層中的粘結相并向其內部擴散,其耐蝕性能主要取決于粘結相,添加少量的Cr能有效提高WC-Co涂層的耐蝕性,因而WC-10Co4Cr涂層抗鹽霧腐蝕性能更好。
免責聲明:本網站所轉載的文字、圖片與視頻資料版權歸原創作者所有,如果涉及侵權,請第一時間聯系本網刪除。
-
標簽: TC18鈦合金, 超音速火焰, 噴涂WC-Co-Cr涂層, 微觀結構, 耐蝕性能
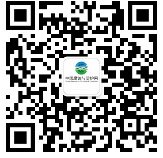
官方微信
《中國腐蝕與防護網電子期刊》征訂啟事
- 投稿聯系:編輯部
- 電話:010-62313558-806
- 郵箱:fsfhzy666@163.com
- 中國腐蝕與防護網官方QQ群:140808414