目前常用的腐蝕評定方法中,硫酸-硫酸銅腐蝕試驗方法應用廣泛,且自帶合格驗收指標,即可通過試樣自身彎曲后有無晶間裂紋產生而直觀地判定材料的耐晶間腐蝕性能是否合格。雖然有一些研究者們指出了其中存在的一些問題,但直至目前,硫酸-硫酸銅法依然是應用最多的晶間腐蝕試驗方法。
今天,本文將以GB/T 4334-2008標準為主線,總結對比分析了國內外各標準對該試驗方法要求的差異,以供相關人員在進行晶間腐蝕試驗時參考。
不同標準對硫酸-硫酸銅晶間腐蝕試驗的要求
1 試樣制備
國內外不同標準對試樣制備的要求如表1所示。
表1 不同標準對試樣制備的要求對比

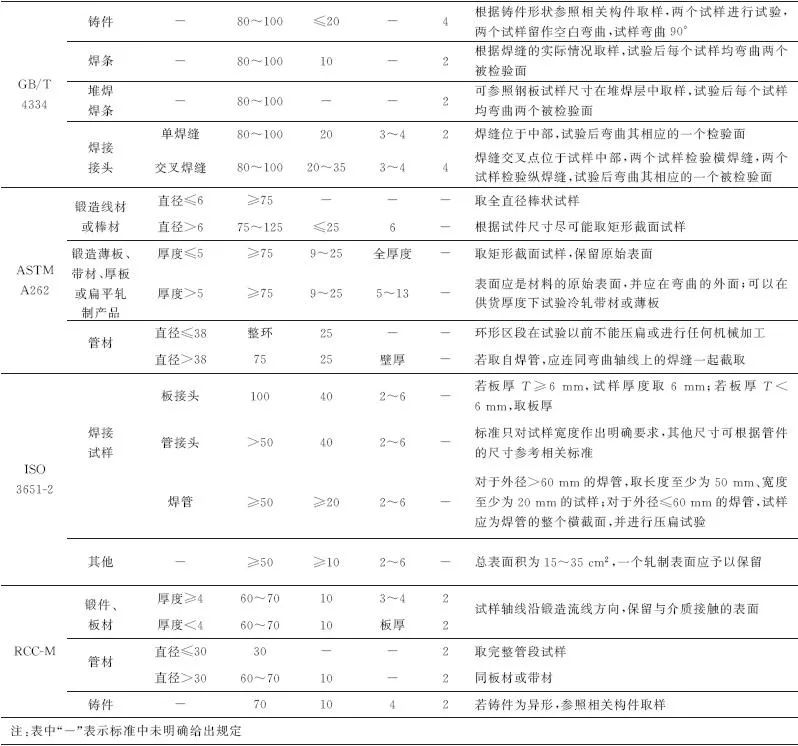
由表1可知,對于試樣的取樣及制備,國標和國外標準要求不盡相同,GB/T 4334規定最為詳細也最為復雜。
首先,關于試樣尺寸:由于試驗過程中溶液量與試樣的表面積是成比例要求的,試樣的長度和寬度在晶間腐蝕試驗過程中并不起主導作用,對試驗結果也未見顯著影響,而試樣的厚度則會影響后續彎曲過程中材料的延伸率,因此試樣厚度的選取對彎曲試驗結果的評定可能會有一定的影響,后文會對此進行詳細討論。
其次,關于試樣數量:國標要求試樣數量最多,厚度T≤3mm時,試樣數量一般為2個,厚度T>3mm時,試樣數量一般為4個,采用彎曲法進行評定,每個規格試樣還需增加一個空白對比試樣;RCC-M要求每一晶間腐蝕試驗至少要加工2個試樣,其中1個用作對比試樣;ASTM A262和ISO 3651-2對試驗的平行試樣個數沒有明確的規定,甚至未提及對比試樣,這就要求我們在必要時需要參照其他標準制備對比試樣。
另外,關于晶間腐蝕試樣的表面粗糙度,國標要求晶間腐蝕試樣的表面粗糙度Ra不大于0.8μm;而國外標準要求晶間腐蝕試樣表面采用120號砂紙打磨(根據實際測量,其表面粗糙度Ra約為15μm),要求彎曲試樣的凸面為試樣的原始表面。可見國標和國外標準對于試樣表面粗糙度的要求不盡相同,現有的試驗結果表明,試樣表面粗糙度對試驗結果的影響并不明顯。
2 敏化處理
各國標準對超低碳和穩定化不銹鋼晶間腐蝕試驗敏化處理制度的規定如表2所示。
表2 不同標準對晶間腐蝕試驗敏化處理制度的規定
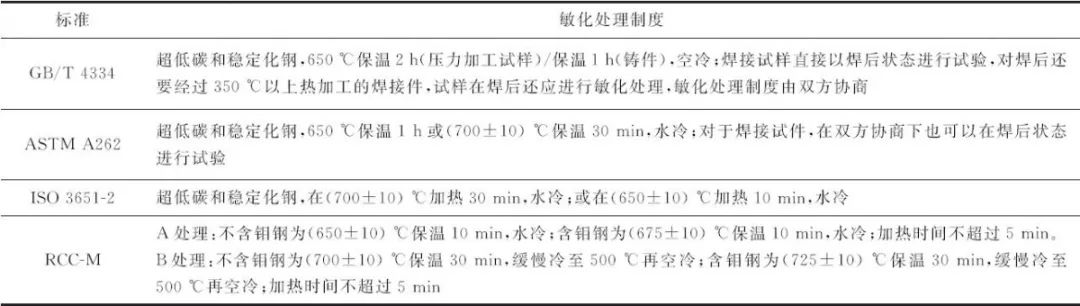
由表2可知,對于超低碳和穩定化奧氏體不銹鋼的敏化處理制度中,國標的敏化處理時間為2h,是各國標準中敏化處理時間最長?最嚴苛的。
再者,關于試樣敏化處理的冷卻方式,國標要求采用空冷,而國外標準要求采用水冷。
鑒于試樣體積一般較小,水冷、空冷的結果相差不大;現有的試驗結果也表明,對于小試樣水冷及空冷兩種不同冷卻方式對晶間腐蝕試驗最終結果的影響并不明顯。
綜上,針對超低碳和穩定化不銹鋼的敏化處理,各標準的規定尚不完全一致,試驗人員可在遵照特定標準時適當參照相關試驗標準,在和技術人員充分溝通后,明確具體的操作規程(如加熱時間、保溫溫度、保溫時間、冷卻方式等),并嚴格執行。
3 試驗過程
對于不銹鋼硫酸-硫酸銅晶間腐蝕試驗的過程,國標和國外標準的要求基本相同,區別主要表現在兩點:第一,試驗過程中是否需要加入銅屑;第二,試驗時間各不相同。銅屑的加入,主要是改變不銹鋼試樣在溶液中的腐蝕電位,酸性硫酸銅溶液中不銹鋼的電位(相對于標準氫電極)在+0.3~+0.58V,處于活化-鈍化的交界區域;當加入銅屑后,試驗過程中銅屑與不銹鋼接觸,不銹鋼試樣的電位與銅的電位相同,約為+0.3V,在此電位下,貧鉻區更容易被硫酸-硫酸銅腐蝕,晶間腐蝕的穿透速度增大,因此可以大大縮短試驗時間。目前只有RCC-M還保留采用不加銅屑的硫酸-硫酸銅晶間腐蝕試驗,試驗時間為72h,當然RCC-M并非不允許加入銅屑,加入銅屑后試驗時間縮短為24h;其他標準目前基本都采用添加銅屑的銅-硫酸-硫酸銅溶液。奧氏體不銹鋼?雙相不銹鋼的晶間腐蝕試驗采用銅-硫酸銅-16%(質量分數)硫酸溶液,試驗時間15~72h不等(國標要求為16h),委托方可以根據技術條件選擇確定具體的試驗時間。
4 結果評定
采用銅-硫酸-硫酸銅法進行晶間腐蝕試驗時,結果評定的方法有兩種:一為彎曲法;二為金相法。關于金相法一般采用允許的晶間腐蝕深度作為合格指標,目前國標和國外標準對此都沒有明確規定,需要供需雙方協商或者由技術條件確定。GB/T 4334.5-1990《不銹鋼硫酸-硫酸銅腐蝕試驗方法》中曾規定,晶間腐蝕深度不得超過5mm,但GB/T 4334.5-2000《不銹鋼硫酸-硫酸銅腐蝕試驗方法》中將此要求取消了,考慮到不同材料的不同工況,這種變動給供需雙方帶來了一個可以靈活掌握的空間。
關于彎曲法,如果試驗后,試樣沒有產生明顯的晶間腐蝕,材料仍保持較高的塑性,彎曲后不會發生開裂;如腐蝕試驗后產生了晶間腐蝕,晶粒之間的連接被破壞,材料基本上喪失了塑性,試樣在彎曲時外表面承受拉應力,已發生晶間腐蝕的試樣會在拉應力的作用下發生開裂。彎曲直徑與試樣厚度對彎曲結果存在著一定的影響,試樣彎曲時外側的變形如圖1所示,假設試樣彎曲時的變形是均勻變形,且中性層位于板厚中間,塑性變形后,試樣受拉面延伸率的計算公式為
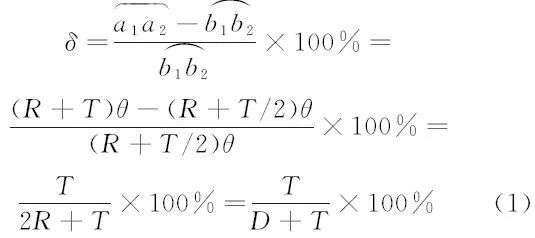

圖1 試樣彎曲過程中各部位的變形情況
式中:δ為延伸率;
和


分別為試樣彎曲部分外側弧長和中性層弧長;θ為彎曲角度;T為試樣厚度;R為壓頭半徑;D為壓頭直徑。
表3 不同標準對彎曲參數的規定
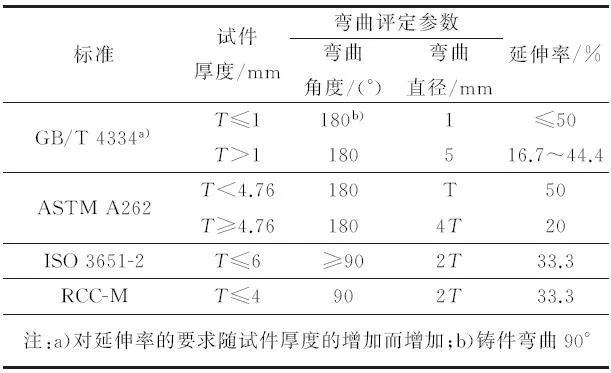
由表3可知:ASTM A262對于薄板的延伸率要求較高(板厚T<4.76mm時,延伸率A=50%),而對于厚板的要求則較低(板厚T≥4.76mm時,延伸率A=20%);ISO 3651-2和RCC-M因為試樣彎曲直徑較大(Φ=2T),對材料的延伸率要求相對較低(A=33.3%),原材料容易滿足,且對材料延伸率要求不隨試件厚度的變化而變化。
按照GB/T 4334的要求,化工常用不銹鋼材料的延伸率至少要在37.5%(T≥3mm)以上,根據GB/T 24511-2009《承壓設備用不銹鋼和耐熱鋼鋼板和鋼帶》規定,不銹鋼板的延伸率不小于40%,所以不銹鋼板容易通過檢驗;而焊材的延伸率相對較低,根據GB/T 983-2012《不銹鋼焊條》的規定,大部分焊材熔敷金屬的延伸率為25%~30%;因此就原材料和焊接接頭而言,原材料通過率較高,而焊接接頭試樣容易造成晶間腐蝕的誤判,試驗檢測結果也證明了這一點,焊接接頭試樣在彎曲過程中經常會發生開裂。然而,晶間腐蝕試驗后的彎曲不是為了考核材料本身的塑性,而是為了確定材料是否發生了晶間腐蝕,如果材料沒有發生晶間腐蝕或晶間腐蝕深度很淺,那么從試驗本身來看,該材料應該通過晶間腐蝕試驗。因此,對彎曲參數的選擇,還要考慮材料本身的因素,彎曲直徑為4倍試樣厚度(Φ=4T)時,彎曲過程中要求材料的延伸率達到20%,既兼顧了焊縫金屬延伸率相對較低的特性,也考慮到發生了晶間腐蝕的材料在彎曲過程中應被撕裂的要求。
綜上而言,對于硫酸-硫酸銅晶間腐蝕試樣,彎曲角度為180°?彎曲直徑為4倍試樣厚度是較為合適的彎曲參數。
需要注意的是,彎曲試樣的開裂,并不一定代表試樣耐晶間腐蝕性能不合格。此時可采用空白試樣進行對比彎曲,或者用金相法進行分析,通過觀察裂紋擴展路徑來判定試樣開裂是由于塑性變形過大造成的穿晶斷裂還是由于晶間腐蝕造成的沿晶斷裂。對于焊接接頭的彎曲試樣,普通的光學金相因為難以區分晶界,掃描電鏡金相是較為合適的選擇,晶間腐蝕裂紋為沿晶的脆性斷口裂紋,塑性不足產生的裂紋斷口呈典型的韌窩形貌。
關于試樣的彎曲方式,國標和國外標準也略有區別:國外標準只要求將被檢驗面(與腐蝕介質接觸的表面)彎曲90°~180°即可。對于非焊接接頭的薄板試樣,國標要求每個試樣均彎曲兩個檢驗面,即試樣需要被彎成“Z”字形,如圖2所示。而實際操作過程中“Z”字形并不易彎曲成形,尤其還需要保證彎曲半徑。其實,若需要檢驗試樣的兩個被檢驗面只需增加一倍試樣數量即可,每個試樣只彎曲一個檢驗面,這將極大地降低后續彎曲的復雜程度。
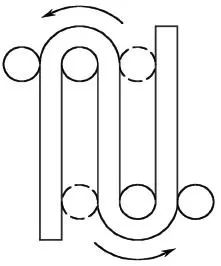
圖2 國標中的彎曲方法示意圖
結束語
不銹鋼硫酸-硫酸銅晶間腐蝕試驗作為一種最為常用的晶間腐蝕試驗方法,各國各行業針對不銹鋼的晶間腐蝕試驗制定了不同的標準,其主要異同點總結如下。
(1)國標和國外標準的規定不盡相同,實際操作過程中可適當相互借鑒。
(2)國標中對于試樣制備的要求最為詳細?復雜,且試樣數量最多,試樣表面粗糙度對試驗結果影響并不明顯。
(3)國標中要求的敏化處理時間最長也最為嚴格。
(4)銅屑可以降低不銹鋼在硫酸-硫酸銅溶液中的腐蝕電位,增大腐蝕速率,縮短試驗時間,因此添加銅屑的晶間腐蝕試驗方法更為合適。
(5)彎曲參數的選擇對試驗結果存在一定的影響,過小的彎曲半徑容易導致誤判。
免責聲明:本網站所轉載的文字、圖片與視頻資料版權歸原創作者所有,如果涉及侵權,請第一時間聯系本網刪除。
-
標簽: 硫酸-硫酸銅腐蝕試驗方法, 晶間腐蝕試驗, 國內外標準
相關文章
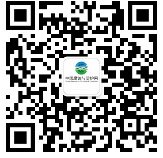
官方微信
《中國腐蝕與防護網電子期刊》征訂啟事
- 投稿聯系:編輯部
- 電話:010-62313558-806
- 郵箱:fsfhzy666@163.com
- 中國腐蝕與防護網官方QQ群:140808414
點擊排行
PPT新聞
“海洋金屬”——鈦合金在艦船的
點擊數:5768
腐蝕與“海上絲綢之路”
點擊數:4763