0 引言
鐵路客車車體壽命直接決定客車壽命,車體防腐質量直接影響車體壽命,車體防腐所用防腐底漆質量及其施工工藝與防腐效果有直接關系。為避免車體內部噴丸后發生車體鋼結構變形,通常采用以機械或手工打磨為主的除銹方式對車內進行除銹檢修,但車體內部除銹又存在難以清除干凈的難題,需要采用新的方式來應對車內鋼結構及鐵質零部件銹蝕,減緩其銹蝕速度,以保證車體運行壽命。
磷化底漆是一種高效金屬表面預處理劑,其所形成的10 ~ 15 μm薄膜牢固附著在金屬表面,起到磷化和鈍化的作用,可增加有機涂層和金屬表面的附著力,防止銹蝕,延長有機涂層的使用壽命。它一般不用于代替底漆,而是與其他底漆或防銹漆配合以獲得較好的效果,廣泛應用于鋼板及鋼結構增強防銹,尤其適宜濕熱環境地區的鋼板和鋼結構的保護。
1 研究內容
本文主要探討除銹磷化底漆的選擇及應用以及與環氧磷酸鋅、環氧重防腐復合涂層間的配套性能,并進行初步現車試用,選擇合適的防腐涂裝工藝。
1.1 磷化底漆的選用
結合運輛客車函[2015]73號《中國鐵路總公司運輸局關于印發〈25型客車防腐涂料工藝規范(試行)〉和〈25型客車用涂料技術條件(試行)〉通知》內容要求,選擇的磷化底漆既要與金屬表面具有良好的化學結合,又要確保與后涂雙組分環氧底漆具有良好的配套性,故確定選用雙組分環氧磷化底漆(主要基料為環氧樹脂)。
磷化底漆又稱洗滌底漆,主要作為有色及黑色金屬底材的表面處理劑,能起磷化作用,可增加有機涂層和金屬表面的附著力。磷化底漆為雙組分涂料,由主劑與磷化液組成,使用時按質量比4 ∶ 1配制,其性能應符合HG/T 3347—2013《乙烯磷化底漆(雙組分)》的規定,具體技術參數見表1。
1.2 不同除銹程度與磷化底漆的相適應情況
根據樣板銹蝕程度,采用手工打磨方式除銹,除銹后表面清潔度不同,然后噴涂磷化底漆,觀察不同除銹效果的樣板噴涂磷化底漆的情況。
1.3 磷化底漆、環氧磷酸鋅底漆、重防腐涂層間的配套性
根據防腐涂層設計結構,觀察不同底漆之間的配套性能。
底漆結構一:磷化底漆+環氧底漆;
底漆結構二:磷化底漆+環氧底漆+重防腐。
1.4 磷化底漆的車內現車應用
根據廠修車車體內部銹蝕情況,選擇銹蝕嚴重、阻尼涂料脫落嚴重的車輛進行磷化底漆應用研究,重點部位為車內側墻板(含側墻骨架)、車內頂板(含車頂骨架)等。
2 探討方法
2.1 試驗驗證
利用樣板驗證方式探討不同除銹程度的表面狀態與磷化底漆相適應的情況,以及復合防腐涂層間的配套性,為現車應用做好準備。
2.2 現車應用
現車選用南方路局運行線路環境比較潮濕車輛,初步驗證磷化底漆的使用效果。
2.3 處理工藝流程
根據車體防腐的整體要求,制定如下車內防腐工藝路線。
1)含磷化底漆車內防腐工藝流程
防腐結構一:車內手工除銹→磷化底漆→環氧磷酸鋅底漆→阻尼涂料;
防腐結構二:車內手工除銹→磷化底漆→環氧磷酸鋅底漆→重防腐涂料→阻尼涂料。
2)原車內防腐工藝流程
防腐結構一:車內手工除銹→環氧磷酸鋅底漆→阻尼涂料;
防腐結構二:車內手工除銹→環氧磷酸鋅底漆→重防腐涂料→阻尼涂料。
3 樣板試驗
3.1 樣板前處理
使用傳統手工打磨除銹的方式初步清除碳鋼樣板表面銹蝕,根據工藝要求,手工除銹表面為St2級,局部不易除銹部位為St3級。
采用樣板手工除銹,除銹效果如圖1所示(因銹蝕嚴重,考慮驗證的實用性,不以傳統除銹等級衡量,僅以實物表面狀態為參考)。
3.2 油漆施工及要求
1)表面處理要求:保持表面干燥,無油污、灰塵等異物。
2)配比:m甲 ∶ m乙=4 ∶ 1。
3)將磷化底漆攪拌均勻,如由于顏料沉淀不易攪拌時,可先將上層漆液倒出,把沉淀顏料和剩余漆液攪拌均勻,再逐漸加入漆液攪拌均勻。
4)將攪拌均勻的底漆放入非金屬容器內邊攪拌邊緩慢加入比例量的磷化液,加畢,加入適量稀釋劑調配黏度(涂-4杯)為15 s左右為宜,放置15 ~ 30 min后使用,并在12 h內用完,放置時間過長易于凝膠,不能使用。
5)采用噴涂施工,漆膜厚度以10 ~ 15 μm為宜,施工時要尤其注意磷化膜厚度,不宜過厚。
6)施工環境要比較干燥,如濕度太高,會使漆膜發白,影響漆膜的附著力和使用效果,環境溫度應不低于18 ℃。
7)漆膜涂布后2 h即可涂其他防銹漆、底漆和面漆,于不低于18 ℃自干或(60±5) ℃下烘干均可。
3.3 過程記錄
3.3.1 磷化底漆樣板
磷化底漆在4種不同程度除銹后的樣板上結合良好,未出現縮孔、咬底、鼓泡等涂層缺陷等。根據GB/T 9286—1998進行劃格試驗,4種不同除銹程度的樣板表面噴涂磷化底漆后,磷化底漆樣板1#、2#、3#、4#的附著力均達到0級的要求,磷化底漆與金屬樣板間附著力良好。
3.3.2 “磷化底漆+環氧磷酸鋅底漆”樣板
4種不同除銹程度的樣板表面噴涂“磷化底漆+環氧磷酸鋅底漆”后,兩種底漆層之間均未出現縮孔、咬底、鼓泡等涂層缺陷。根據GB/T 9286—1998劃格試驗,“磷化底漆+環氧磷酸鋅底漆”涂覆后樣板1#、2#、3#、4#兩涂層層間附著力劃格試驗均可達到0級的要求,說明兩種底漆間配套性良好。
3.3.3 “磷化底漆+環氧磷酸鋅底漆+重防腐涂料”樣板
4種不同除銹程度的樣板表面噴涂“磷化底漆+環氧磷酸鋅底漆+重防腐涂料”后,3種底漆層之間均未出現縮孔、咬底、鼓泡等涂層缺陷。根據GB/T 9286—1998進行劃格試驗,“磷化底漆+環氧磷酸鋅底漆+重防腐涂料”涂覆后樣板1#、2#、3#、4#的涂層層間附著力均達到0級的要求,說明3種底漆間配套性良好。
4 車輛應用
樣板驗證結果說明復合防腐涂層性能符合工藝要求。為保證驗證的全面性,對現車進行工藝配套性試驗,在此僅就復合防腐涂層進行裝車應用。根據廠修車車體內部銹蝕情況,選擇銹蝕嚴重、阻尼涂料脫落嚴重的部分車輛,對磷化底漆進行現車驗證。
4.1 施工過程記錄
1)除銹
對車體內部銹蝕嚴重、阻尼涂料脫落嚴重的部位,采取手工打磨除銹(盡量接近于St2級)。
2)防銹涂層
采用“磷化底漆+環氧磷酸鋅底漆+重防腐涂料”的復合體系,分步驗證,結果如圖2 ~ 6所示。
4.2 試驗評定
試驗評定結果:磷化底漆現車噴涂施工未出現縮孔、咬底、鼓泡等涂層缺陷,表面覆涂環氧底漆后,兩種底漆未出現縮孔、咬底、鼓泡等涂層缺陷,說明復合防腐涂層施工性良好。
對于最終質量效果,應在車輛出廠運用過程中認真進行質量跟蹤,并在下次廠修時對其進行質量評價。
5 結語
通過樣板和現車試驗驗證,磷化底漆施工性良好,與不同除銹程度的金屬基材基本都能實現良好的配套結合,不同防腐涂層間的配套性能也表現良好。
在實際檢修過程中,車輛腐蝕情況各異,對于車輛不同程度腐蝕情況,根據其結構局限性及表面處理情況采用不同的涂層結構,選用不同的防腐處理工藝。
1)車內腐蝕較輕,除銹效果符合St2級標準,表面處理良好的車輛使用“環氧磷酸鋅底漆+其他”的復合涂層,不建議使用磷化底漆。
2)車內腐蝕嚴重,且除銹后達不到St2級標準,表面存在牢固腐蝕層或浮銹的車輛使用“磷化底漆+環氧磷酸鋅底漆+其他”的復合涂層,客車檢修時建議磷化底漆配合環氧磷酸鋅底漆作為防腐底漆。
免責聲明:本網站所轉載的文字、圖片與視頻資料版權歸原創作者所有,如果涉及侵權,請第一時間聯系本網刪除。
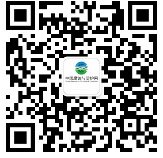
官方微信
《中國腐蝕與防護網電子期刊》征訂啟事
- 投稿聯系:編輯部
- 電話:010-62313558-806
- 郵箱:fsfhzy666@163.com
- 中國腐蝕與防護網官方QQ群:140808414