被稱為核電站“主動脈”的一回路主管道,是核島內七大關鍵設備之一。它連接著反應堆壓力容器、蒸汽發生器和反應堆冷卻劑泵,從而組成一條封閉式的循環回路。主管道總共包含兩個環路,共計存在12個焊接接頭。在核電站運行環境下,這些不銹鋼焊接接頭不可避免的會受到核電一回路高溫高壓含硼水的腐蝕,焊接接頭的穩定性關系到整個一回路的安全。核電站管道破裂事故分析表明,帶有焊縫的管道更容易發生事故,其原因大多與焊接接頭的抗腐蝕性能有關。
根據文獻報道,不銹鋼在高溫高壓溶液環境中容易形成富Cr的致密內層氧化膜和富Fe的疏松外層氧化物顆粒,這種雙層結構氧化膜的形成與腐蝕時間存在較大的聯系。較多研究者認為,隨著腐蝕時間的增加,氧化膜均由單一的富鐵層逐漸變為表層富鐵、內層富鉻鎳的雙層結構。目前,大量文獻對不銹鋼材料在高溫高壓腐蝕介質中的氧化膜生長進行了觀察和研究,而對于不銹鋼焊接接頭整體在高溫高壓環境中的腐蝕行為研究較少。除此之外,對于焊縫區 (WM) 和母材區 (BM) 腐蝕行為的差別也尚未見相關報道。為了保證核電站一回路主管道的運行安全,有必要對不銹鋼焊接接頭在高溫高壓溶液環境的腐蝕行為進行研究。
本文主要針對316LN不銹鋼焊接接頭在高溫高壓含硼水中的腐蝕行為展開研究,圍繞其腐蝕變化規律及相應的氧化行為,對不同區域下的氧化膜成分和結構進行了觀察和分析,為不銹鋼焊接接頭的安全服役評價提供一定的參考和數據支持。
1 實驗方法
1.1 實驗材料
本文實驗材料為AP1000核電站鍛造主管道316LN不銹鋼,焊接材料是ER316L。母材和焊接材料的成分如表1所示。焊接工藝采用25~26 V的焊接電壓,焊接電流控制在80~100 A,熱輸入量為24 kJ/cm,焊接速率為70~80 mm/min,焊接過程在氬氣的保護下完成。焊接完成之后,對試樣進行615 ℃下16 h的焊后熱處理。
1.2 組織形貌觀察
在管道的橫截面上進行取樣,分別在WM和BM截取尺寸為15 mm×15 mm×2 mm的試樣。將所有試樣用砂紙從60#、120#逐級磨到2000#,用2.5 μm的金剛石研磨膏進行拋光,然后電解侵蝕、蒸餾水洗滌干凈后干燥備用。電解液為10% (質量分數) 的草酸溶液,電解電壓為5 V,電解時間為30 s。采用Olympus金相顯微鏡 (OM) 和Zeiss Auriga掃描電鏡 (SEM) 對試樣組織、氧化膜形貌進行觀察和分析。采用Rigaku DMAX-RB 12 kW旋轉陽極X射線衍射儀 (XRD) 和AXIS ULTRADLD X射線光電子能譜儀 (XPS) 分別對WM和BM表面氧化膜成分和結構進行分析。
1.3 均勻腐蝕實驗
均勻腐蝕實驗參考JB/T 7901-2001《金屬材料實驗室均勻腐蝕試驗方法》標準。腐蝕試樣尺寸為25 mm×20 mm×2 mm,試樣從焊接接頭截面處切取,具體取樣方向如圖1所示。所有切取后的試樣都經過SiC砂紙打磨后用去離子水和丙酮清洗干凈并干燥備用。在腐蝕實驗開始之前,采用精度為0.01 mg的分析天平對均勻腐蝕試樣進行稱重。高溫高壓腐蝕實驗所用裝置為5L靜態高溫高壓釜,溫度設定為320 ℃,相應的飽和蒸汽壓力為11 MPa,實驗介質為模擬壓水堆核電站一回路工作介質 (2.2 μg/mL Li+ (LiOH)+800 μg/mL B3+ (H3BO3) 水溶液),溶液體積為2.6 L。實驗開始前,用純度99.9999%的氮氣對高溫高壓釜進行除氧處理1 h。均勻腐蝕實驗周期分別為50,200,360,760,1080和1440 h,每周期平行試樣為3個。每周期實驗完成之后,將試樣從高溫高壓釜中取出,并用丙酮、酒精和去離子水清洗干凈后干燥稱重,記錄不同腐蝕周期下試樣的重量,從而得到試樣的腐蝕增重和腐蝕增重速率。腐蝕增重速率計算公式如下:
2 結果與討論
2.1 組織形貌分析
圖2a和b分別為316LN焊接接頭BM和WM金相組織形貌圖。從圖2a中可以看出,BM組織為等軸的奧氏體晶粒,有明顯的孿晶存在。而從圖2b中可以看出,WM組織為奧氏體和蠕蟲狀或板條狀的鐵素體。圖2c和d分別是316LN焊接接頭BM和WM的局部取向差圖。可以看出,與BM相比,WM具有更大的局部取向差 (殘余應變)。
2.2 腐蝕增重和腐蝕增重速率
圖3a和b分別為316LN焊接接頭均勻腐蝕增重和腐蝕增重速率。可以看出,在實驗的前期 (360 h之內),試樣先失重并且腐蝕增重速率較大,說明在腐蝕前期階段,焊接接頭區域金屬的溶解速率大于氧化膜的形成速率,從而導致試樣發生腐蝕失重;然后隨時間延長,腐蝕失重逐漸減小,一直到發生腐蝕增重;1080 h以后,腐蝕增重趨于穩定,腐蝕增重速率略有降低。說明隨著腐蝕時間的增加,焊接接頭試樣表面形成了致密穩定的氧化膜,使金屬溶解受到抑制,基體材料得到了有效的保護。
2.3 氧化膜形貌和成分
圖4為不同腐蝕時間下試樣表面典型的氧化膜形貌。可以看出,在腐蝕時間較短時,焊接接頭試樣表面形成了較少的氧化物顆粒,其平均尺寸約為200 nm;隨著腐蝕時間的延長,一方面,氧化物顆粒數量逐漸增加,氧化膜變得更為致密;另一方面,氧化物顆粒尺寸逐漸增加,其中試樣表面出現少許較大尺寸的氧化物顆粒 (平均尺寸為500 nm),這些氧化物顆粒都具有規則外形和較直的棱邊。
為了分析316LN焊接接頭中WM和BM腐蝕情況的差別,分別對腐蝕360和1440 h后試樣WM和BM的表面氧化膜進行了觀察和分析,其結果如圖5所示。隨著腐蝕時間的延長,WM和BM表面氧化物顆粒分布較為均勻和緊湊,這種致密分布的氧化物顆粒能夠有效地減緩材料的溶解速率[9],從而保證焊接接頭具有較好的耐均勻腐蝕性能。
對不同腐蝕時間下的外層氧化物顆粒 (圖5中1~4點) 進行了EDS分析,結果如表2所示。可以看出,試樣表面氧化物顆粒主要由Fe和Cr的氧化物組成;隨著實驗周期的增加,試樣表面氧化物顆粒中的Cr含量和Ni含量相對減少較多。結合本文圖5和表2結果可以得出,隨著腐蝕時間的增加,WM和BM表面氧化膜表層逐漸形成較多的富Fe氧化物顆粒,同時二者表面氧化膜成分和結構沒有明顯的差別。
圖6為腐蝕360和1440 h后,316LN焊接接頭BM和WM表面氧化膜的XRD譜。可以看出,所有試樣表面氧化膜成分差別不大。由于氧化膜較薄易被X射線穿透,圖譜中也出現了基體衍射峰。在不同周期下的試樣表面氧化膜均主要由FeOOH,FeCr2O4和Fe3O4組成。同時,還可以看出,在腐蝕360 h后WM和BM均出現了較為明顯的FeOOH峰,說明此時,離子溶解會形成較多的水化物,因此在短期腐蝕時間下焊接接頭的腐蝕敏感性較高。隨著腐蝕時間延長到1440 h,WM和BM表面氧化膜相組成沒有明顯的差別,主要由FeCr2O4和Fe3O4組成。
2.4 氧化膜結構和相組成
圖7和8分別為腐蝕360和1440 h后試樣WM和BM表面氧化膜的XPS譜。
從圖7a中Fe 2p3/2譜中可以看出,不同實驗周期下試樣表面氧化膜Fe 2p3/2的結合能都位于約711 eV。通過分峰擬合可以看出,試樣表面氧化膜中Fe主要以FeCr2O4或Fe3O4 (結合能為710.5 eV)、FeOOH (結合能為711.8 eV) 和FeO (結合能為709.5 eV) 形式存在[8]。從圖7b的Cr 2p3/2譜圖中可以看出,試樣表面氧化膜Cr 2p3/2的結合能約在577 eV,不同周期下試樣表面氧化膜中Cr主要以Cr2O3 (結合能為576 eV)、Cr(OH)3 (結合能為577.4 eV) 和CrO3 (結合能為579 eV) 形式存在。從圖7c的Ni 2p3/2譜圖中可以看出,試樣表面氧化膜Ni 2p3/2的結合能約在856 eV,不同周期下試樣表面氧化膜中Ni主要以Ni(OH)2 (結合能為 856 eV) 形式存在。從圖7d的Mo 3d5/2譜圖中可以看出,試樣表面氧化膜中Mo 3d5/2的結合能約在233 eV,不同周期下試樣表面氧化膜中Mo主要以MoO3 (結合能為232.85 eV) 形式存在。除此之外,還可以看出,WM和BM表面氧化膜成分沒有明顯的差別,說明在高溫高壓環境中WM和BM腐蝕機理是一致的。
圖9為不同腐蝕時間下WM和BM表面氧化膜中O的XPS譜。可以看出,不同實驗周期下試樣表面氧化膜O 1s的結合能都位于約531 eV。通過分峰擬合可以看出,所有試樣表面氧化膜中O主要以O2- (結合能為531 eV) 和OH- (結合能為532.5 eV) 形式存在[8]。腐蝕360 h后,WM區表面氧化膜中O主要以OH-為主,說明在較短的腐蝕時間下,WM中有較多的金屬離子溶解從而形成了大量的水化物。以上結果表明,WM存在更多金屬離子的溶解和沉積,在較短的腐蝕時間下,WM會表現出更高的腐蝕敏感性,這與焊接過程中WM形成較大的殘余應變 (圖2)、析出物[2,3,4]等有著密不可分的關系。同時,由于WM中鐵素體相的存在 (圖2),致使WM和BM發生電偶腐蝕以及WM內部出現鐵素體/奧氏體相電偶腐蝕,進一步增大了WM的腐蝕敏感性。但隨著腐蝕時間延長到1440 h,WM和BM中O均以O2-為主。結合XRD譜 (圖6) 和EDS結果 (表2) 說明,腐蝕1440 h后WM和BM表面氧化膜無明顯差別,兩者都形成了穩定的氧化膜,從而使316LN焊接接頭區域在高溫高壓水環境下具有較好的耐均勻腐蝕性能。
3 結論
(1) 316LN不銹鋼焊接接頭中,焊縫區具有與母材區相當的耐均勻腐蝕性能。
(2) 焊接接頭隨著腐蝕時間的延長,先發生腐蝕失重,隨后失重減小直至發生較小增重,并保持穩定。焊縫區在腐蝕初期大量離子溶解形成水化物,較母材區表現出更高的腐蝕敏感性。
(3) 焊接接頭表面隨著腐蝕時間的增加,氧化物顆粒數量和尺寸逐漸增加。表面氧化膜主要由FeOOH,FeCr2O4和Fe3O4組成。
免責聲明:本網站所轉載的文字、圖片與視頻資料版權歸原創作者所有,如果涉及侵權,請第一時間聯系本網刪除。
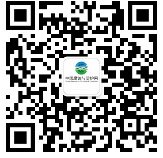
官方微信
《中國腐蝕與防護網電子期刊》征訂啟事
- 投稿聯系:編輯部
- 電話:010-62313558-806
- 郵箱:fsfhzy666@163.com
- 中國腐蝕與防護網官方QQ群:140808414