1.1渦輪葉片服役環境特點
發動機是航空裝備的“心臟”,發動機的性能決定了飛機的飛行速度、機動性、航程、有效載重等一系列性能[1]。圖1-1為Leap-1C航空發動機的基本構造圖,發動機主要包括風扇、壓縮系統、燃燒系統、渦輪系統和噴管系統等[7]。高溫燃氣經過燃燒室充分燃燒后,由燃燒室排出并流經渦輪系統。一部分燃氣的內能轉化為機械能,推動渦輪轉動,同時帶動壓氣機繼續吸入大量空氣;另一部分燃氣直接從尾噴管噴出,巨大反作用力推動飛機向前飛行。在燃氣渦輪發動機中,渦輪是極其關鍵的部件。渦輪的設計、制造與用材水平關乎到整個發動機的性能水平和使用可靠性[8]。
圖1-1 C919選用的Leap-1C發動機
渦輪轉子葉片是將發動機的熱能轉變為機械能的重要部件,其工作環境最為苛刻。在工作過程中,轉子葉片需要承受高溫高壓、離心載荷、振動載荷、熱應力、燃氣腐蝕及高溫氧化的綜合作用[34]。嚴苛的服役環境,導致轉子葉片失效的概率最高。統計表明發動機零部件失效事件中,轉子葉片占70%以上[1]。渦輪葉片的服役環境主要分為三類:工作溫度高、工作應力復雜和工作環境腐蝕性高[1, 3]。
(1)工作溫度高且分布不均勻。隨著渦輪發動機的發展,其推重比不斷增加,航空發動機的推重比每提高10%,渦輪進氣口溫度需提高100 °C左右。為了不斷提高發動機的推重比,渦輪前進氣口溫度也不斷增加,目前已知的第四代軍用發動機渦輪前溫度已達到1850-2000 K[9]。不僅如此,葉片不同部位的溫度分布還極不均勻,圖1-2為某渦輪葉片服役過程中溫度分布模擬結果圖[6, 10]。葉片縱向方向上榫頭和葉根的溫度最低,中間段至葉尖處于高溫區(圖1-2(a))。葉片橫截面方向上進氣邊和排氣邊均屬高溫區,但排氣邊溫度更高(圖1-2(b))。
(a) (b)
圖1-2 某渦輪葉片服役過程中溫度分布模擬結果[10, 36]
(a) 葉身縱向溫度分布;(b) 橫截面溫度分布
(2)轉速高,應力大。渦輪轉子葉片工作時的轉速通常在12000 r/ min左右。高速旋轉的情況下,渦輪葉片由于自身質量的作用,會產生很大的離心力。服役過程中葉身部分可能承受大約140 MPa的離心拉應力,而葉根部分承受的平均離心拉應力達到280~560 MPa[5]:同時,服役葉片應力分布不均勻。圖1-3為某渦輪葉片服役過程中應力分布模擬結果圖[6, 10]。葉片在服役過程中無論沿著葉尖到葉根的縱向方向還是葉片的橫截面方向,應力分布均存在較大梯度(圖1-3(a))。在葉片橫截面方向上,葉片的進氣邊、排氣邊及葉背處所受綜合應力最大(圖1-3(b))。
(3)工作環境腐蝕性強。渦輪葉片要經受高溫燃氣引起的氧化以及熱腐蝕[4, 1, 12]。航空發動機即使使用高品質航空煤油,燃油中依然含有微量硫。當飛機在沿?;蚝Q笊峡诊w行,發動機吸入含NaCl的空氣,會形成Na2SO4并沉積在渦輪葉片表面。熔化狀態的鹽膜導致渦輪葉片遭受熱腐蝕,其腐蝕程度要比純氧化嚴重得多,促使葉片過早失效。
除了環境因素外,渦輪葉片本身的復雜結構也增加了葉片失效的幾率。目前渦輪葉片普遍空心結構,內部存在很多細小的管道。高壓冷空氣通過這些管道流經葉片,起到強制冷卻的作用。為了提高冷卻效率,渦輪葉片的內腔結構越來越復雜,壁厚變得越來越薄。相較于實心葉片,空心葉片復雜的結構及較薄的壁厚,使得服役葉片中溫度和應力的分布更不均勻??招慕Y構也減少了有效承載面積,從而增加了葉片失效的風險。
(a) (b)
圖1-3 某渦輪葉片服役過程中應力分布模擬結果[10, 36]
(a) 葉身縱向溫度分布;(b) 橫截面溫度分布
1.2渦輪葉片對材料的要求
由于航空發動機渦輪葉片(包括渦輪工作葉片和導向葉片)服役環境極其惡劣,因而對所用材料的要求也極為苛刻。自20世紀四五十年代,國內外對航空發動機渦輪葉片用材料的研究都投入了大量的人力和物力[13, 14]。渦輪工作葉片的材料主要需要滿足以下要求[15-17]:
(1)渦輪葉片材料應具有良好的力學性能,包括高溫蠕變性能、機械疲勞性能、熱疲勞性能和抗沖擊性能,以及良好的高溫塑性。
(2)渦輪葉片材料應具有良好的抗熱腐蝕和抗氧化的性能,同時其表面適合涂覆各種防護涂層,如Al-Si涂層、MCrAlY涂層和熱障涂層等。
(3)渦輪葉片應具有良好的工藝性能,如鑄造性能、焊接性能、盡可能高的導熱系數和盡可能低的熱膨脹系數以及較小的密度等良好的物理性能。
(4)渦輪葉片材料應具有較高的初熔溫度,能夠承受短時超溫。
(5)渦輪葉片材料應具有較好的組織穩定性,在長期使用過程中,能夠保持組織相對穩定,避免析出TCP相等有害相。
1.3渦輪葉片用高溫合金的發展
航空發動機的發展和高溫合金的發展是齊頭并進、密不可分的,前者是后者的主要動力,后者是前者的重要保證[18]。圖1-4為航空發動機渦輪葉片材料及工藝發展歷程圖[2]。自上世紀40年代以來,渦輪葉片材料經歷了變形(鍛造)高溫合金、普通鑄造等軸晶高溫合金、定向凝固高溫合金和單晶高溫合金四個階段,合金的承溫承載能力不斷提升[2]。
圖1-4 航空發動機渦輪葉片材料及工藝發展歷程[2]
(1)變形高溫合金
為滿足渦輪噴氣式發動機熱端部件的要求,上世紀三十年代末鎳基高溫合金開始發展。1939年英國Mond鎳公司首先在20%Cr-80% Ni電熱合金中添加了少量C和Ti研制出了鎳基合金Nimonic75,隨后又研究出一種含有Al和Ti合金元素的Nimonic80合金[19],并于1942年將Nimonic80合金成功地用作渦輪發動機葉片材料,是最早應用γ‘-Ni3(Al,Ti)相強化的渦輪葉片材料。該合金與Nimonic75合金相比,蠕變性能在應力和持續時間相同的條件下,蠕變溫度至少可以提高50℃。后來,人們在合金中加入B、Zr合金元素,開發出了Nimonic80A合金。隨后加入Co元素提高γ’相固溶溫度得到Nimonic90合金[46]。在此基礎上添加Mo,以及添加更多的Al和Ti元素來提高固溶體強度,從而發展成Nimonic95、Nimonic100、Nimonic115等合金,形成了Nimonic系列合金[20]。美國和前蘇聯高溫合金發展與英國相似。美國Halliwell于40年代中期開發出K42B合金用于制造活塞式航空發動機的增壓渦輪。隨后,美國的PW公司、CE公司和特殊金屬公司于50年代分別開發出了Waspalloy、M252和Udimet500等合金,并在這些合金的基礎上形成Inconel、Mar-M和Udimet等一系列牌號的合金。這些合金都是通過鍛造、軋制等加工成渦輪噴氣式發動機所需的渦輪葉片等部件[21, 22]。因此,這一階段的合金稱為變形高溫合金。然而,隨著航空工業的發展,葉片需要滿足具有更高的工作溫度和強度,以及葉片結構復雜程度的增加,致使通過鍛造成型的變形高溫合金已無法滿足要求,鑄造高溫合金孕育而生。
(2)等軸晶鑄造高溫合金
20世紀50年代,真空熔煉和熔模精密鑄造技術的先后出現,使合金的性能和鑄件的質量大幅度提高,從而使高溫合金進入了“鑄造時代”。鑄造高溫合金得到迅速發展,并逐漸成為高溫合金的主流,許多高性能鎳基鑄造合金如:IN100、B1900、ЖC6К、MAR-M200、IN713、MAR-M002和René125等相繼出現[50]。鑄造鎳基高溫合金發展可以分為三個階段,在鎳基高溫合金發展的初期,通過適當調整和添加合金成分完全能夠滿足渦輪葉片材料的設計要求,而鑄造過程對改善葉片性能貢獻不大,因此,第一階段被認為是合金成分占主導地位的發展階段。隨著鎳基高溫合金發展,僅僅靠合金成分的發展不能適應葉片材料性能的進一步要求,于是合金的鑄造過程控制也成為材料技術的一個關鍵,所以第二階段被認為是合金成分和鑄造過程共同決定葉片材料性能階段。隨著鎳基高溫合金繼續發展,高溫合金的使用溫度已經接近極限,通過調整合金成分的發展來調高合金的使用性能的空間已變得已非常小,因此,必須通過采用新工藝,以提高合金的使用性能,所以第三階段即鑄造技術占主導地位的發展階段,如定向凝固和單晶技術。
(3)定向凝固和單晶高溫合金
普通鑄造高溫合金在提高強度的同時,由于其自身是由多個晶粒組成的特點,存在多個晶界,而晶界處雜質較多、原子擴散較快、原子排列不規則,成為合金高溫服役過程中的薄弱環節[23]。在較高服役溫度下,裂紋往往首先在垂直于應力方向上的橫向晶界上萌生并擴展。在針對Mar-M200等軸晶合金的研究過程中發現,該合金中溫性能尤其是中溫塑性很低,出現所謂“塑性低谷”問題。為了克服橫向晶界的有害作用,進一步提高葉片的高溫力學性能,通過開發定向凝固技術避免了橫向晶界的產生。在定向凝固技術的基礎上,人們相繼開發出了消除橫向晶界的定向凝固高溫合金和消除所有晶界的單晶高溫合金。目前,定向凝固高溫合金發展至今已有四代,且每代定向合金的承溫能力均比上一代提高近30℃[24];而單晶高溫合金已發展至第六代。一代又一代單晶高溫合金的相繼出現和應用,為航空發動機和燃氣輪機的性能大幅度提升作出了重大貢獻,成為最具潛力的先進燃氣渦輪用材料。
參考文獻
[1] 陶春虎, 鐘培道, 王仁智。 航空發動機轉動部件的失效與預防[M]. 北京: 國防工業出版社, 2000.
[2] Reed R C. The superalloys: fundamentals and applications[M].New York: Cambridge university press, 2008.
[3] Carter T J. Common failures in gas turbine blades[J].Engineering Failure Analysis, 2005, 12: 237-247.
[4] Ali L, Ghauri K M, Hasan F. Cracking failure in gas-turbineblades[J]. Pakistani Journal of Engineering & Applied Sciences, 2011, 9:98-102.
[5] Kargarnejad S, Djavanroodi F. Failure assessment of Nimonic80A gas turbine blade[J]. Engineering Failure Analysis, 2012, 26: 211-219.
[6] Wen Z, Hou N, Wang B, et al. Crystallographic life model forsingle crystal turbine blade and validation by the miniature specimens cut fromthe turbine blades[J]. Multidiscipline Modeling in Materials and Structures,2010, 6(4): 508-520.
[7] https://web.stanford.edu/group/fpc/Durbin/wu/pictures/engine.html.
[8] 馮強, 童錦艷, 鄭運榮, 等。 燃氣渦輪葉片的服役損傷與修復[J]. 中國材料進展, 2012, 31(12): 21-34.
[9] 劉大響, 程榮輝。 世界航空動力技術的現狀及發展動向[J]. 北京航空航天大學學報, 2002, 28(5): 490-496.
[10] Reed R C, Green K A, Caron P, et al. Numerical modelling ofcreep deformation in a CMSX-4 single crystal superalloy turbine blade[J].Superalloys 2008: Proceedings of the 11th Intenational Symposium ofSuperalloys. 2008: 911-919.
[11] Chen Y, Feng Q, Zheng Y, et al. Formation of hole-edge cracksin a combustor liner of an aero engine[J]. Engineering Failure Analysis, 2015,55: 148-156.
[12] Xie Y J, Wang M C, Zhang G, et al. Analysis of superalloyturbine blade tip cracking during service[J]. Engineering Failure Analysis,2006, 13(8): 1429-1436.
[13] Matysiak H, Zagorska M, Andersson J, et al. Microstructure ofhaynes? 282? superalloy after vacuum induction melting and investment castingof thin-walled components[J]. Materials, 2013, 6(11): 5016-5037.
[14] 何玉懷, 蘇彬。 中國航空發動機渦輪葉片用材料力學性能狀況分析[J]. 航空發動機, 2005, 31(2): 51-54.
[15] 郭建亭。 高溫合金材料學 (上冊)[M]. 北京: 科學出版社, 2008.
[16] Amano. R S, Malloy R J. Study of the flow over wind turbineblade[J]. Proceedings of ASME Turbo Expo 2011, 2011: 1-10.
[17] 劉慶瑔。 航空發動機葉片制造技術及失效分析[M]. 北京: 航空工業出版社, 2011.
[18] 陳榮章, 王羅寶, 李建華。 鑄造高溫合金發展的回顧與展望[J]. 航空材料學報, 2000, 20(3): 55-61.
[19] Goswami T. Conjoint bending torsion fatigue-fractography[J].Materials & Design, 2002, 23(4): 385-390.
[20]Bruni C, Forcellese A,Gabrielli F. Hot workability and models for flow stress of Nimonic 115 Ni-basesuperalloy[J]. Journal of Materials Processing Technology, 2002, 125(1):242-247.
[21] 郭建亭。 變形高溫合金和等軸晶鑄造高溫合金材料與應用基礎理論研究[J]. 金屬學報, 2010,(11): 1303-1321.
[22] 冶軍。 美國鎳基高溫合金[M]. 北京: 科學出版社, 1978.
[23] 陳國良。 高溫合金學[M]. 北京: 冶金工業出版社, 1988.
[24] 黃頌惠。 定向凝固高溫合金的發展[J].材料導報, 1988,(8): 11-13.
免責聲明:本網站所轉載的文字、圖片與視頻資料版權歸原創作者所有,如果涉及侵權,請第一時間聯系本網刪除。
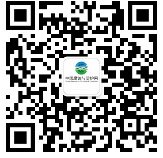
官方微信
《中國腐蝕與防護網電子期刊》征訂啟事
- 投稿聯系:編輯部
- 電話:010-62316606-806
- 郵箱:fsfhzy666@163.com
- 中國腐蝕與防護網官方QQ群:140808414