0 引言
艦載機發動機熱端部件, 由于受海洋環境的影響, 長期處于空氣濕度大、 鹽堿重的惡劣環境中服役, 除了受到沖蝕、 磨損外還要經受腐蝕考驗。艦載機服役壽命的 90% 為停放狀態, 有研究表明:連續長時間停放的腐蝕比經常使用和維護的嚴重, 因此發動機高溫涂層耐常溫海洋大氣腐蝕的能力是不可忽略的。當發動機工作時, 熱腐蝕成為典型故障之一, 不僅降低了發動機的使用效能, 而且增加了維修的工作量和費用。熱腐蝕是在高溫環境下氧及其他腐蝕性氣體與材料表面的沉積鹽共同作用而發生加速腐蝕的現象, 其危害性要遠大于熱氧化;而且, 隨著“深藍戰略”實施的不斷深入, 超過 1000℃以上服役的高溫涂層抗熱腐蝕性能研究, 將是今后一個時期研究的重點。
1 海洋大氣特點
海洋大氣環境極其復雜, 隨著地球經緯度和海岸地理條件的差異, 溫度、 濕度、 輻照度、 氯離子濃度、 鹽度、 污染物等主要環境因子及其耦合作用對材料腐蝕行為的影響差異很大。海洋大氣中腐蝕顆粒主要為 SO2、 HNO3、N2O5 與 NaCl反 應 生 成 的 Na+、 [Cl-]、[SO42-]、 [NO3-]、 [HN4+]等離子顆粒 。我國典型海洋大氣表現為高溫、高濕和高鹽霧的特點。我國近海受大陸污染影響,離子、 SO2 含量都遠高于國外;遠海如西沙則離子含量高 。西太平沿岸 [NO3-] 濃度大于 [SO42-]濃度, 而我國 PM2.5、 PM10 離子顆粒濃度遠高于其他西太平洋其它國家。歐美國家近、 遠海主要是 [Cl-], SO2 含量很少, 近乎為零;東南亞[Cl-]、 SO2 相當。
海洋環境下服役艦載機發動機熱端零部件容易受高濕、 鹽霧以及微生物等形式的化學腐蝕,以及高溫氧化、 沖蝕等疊加效應而形成的復雜熱腐蝕,壽命大幅度縮短,維護費用和大修成本劇增,因此抗海洋大氣熱腐蝕的高溫涂層技術需求緊迫。
2 熱端涂層分類介紹
航空發動機不同部件由于工作環境的差別需要不同的涂層, 按功能可以分為:熱障涂層、 高溫抗氧化涂層、 耐磨/耐腐/抗沖蝕涂層、 封嚴涂層、抗微動磨損涂層、 阻燃涂層、 環境障涂層、 憎水涂層、 隱身涂層等。其中發動機熱端主要有熱障涂層、 耐磨/抗沖蝕涂層。
2.1熱障涂層
熱障涂層 (TBCs) 起源于 20 世紀 40 年代末50 年代初, 主要是用來提高鎳基高溫合金的高溫性能的 。世界航空推進計劃的三大隔熱防護技術中, 單晶 ( 每年 1~2℃的速度增長 ) 和冷卻氣膜技術 ( 不斷降低熱效率、 增加加工難度 ) 的發展潛力已非常有限, 但應用厚度約 100~ 400μm 的熱障涂層后, 基體溫度可以降低 100~200℃, 這相當于高溫合金過去三十年的發展總和 。因此,熱障涂層被認為是目前提高發動機服役溫度最切實可行的辦法。目前在有氣膜、 熱障涂層的情況下, 單晶葉片的使用溫度可以超過 1500℃, 未來需要承受 1800℃以上的溫度, 依賴于開發新的葉片、 熱障涂層材料(見圖 1)。
圖1 飛機發動機葉片耐溫發展趨勢
目 前 常 用 的 TBCs 材 料 有:7-8YSZ、 莫 來石、 Al2O3、YSZ+CeO2 、 La2Zr2O7、 硅酸鹽, 其中Y2O3 部分穩定的 ZrO2(YSZ, Y2O3 含量一般為7%~8%, 質量分數)是應用最廣泛的 TBCs 材料。近年來國內外在多元氧化物摻雜氧化鋯、 A2B2O7型燒綠石或螢石化合物、 磁鉛石型六鋁酸鹽化合物、 石榴石型化合物、 鈣鈦礦結構化合物和其他新型氧化物陶瓷等先進超高溫熱障涂層陶瓷材料方面進行了大量研究。2007 年哈佛大學 Clarke教授課題組和加州大學圣巴巴拉分校的 Lavi 教授等發現 ZrO2-YO 1.5-TaO2.5 的使用溫度可以達到1500℃, 而熱導率較 YSZ 下降 100%, 具有新型涂層發展潛質 。近幾年, 新型稀土鉭酸鹽高溫鐵彈相變陶瓷材料進入人們的視野, 預期最高使用溫度可以達到 1600℃ 。盡管稀土鉭酸鹽具有低熱導率和膨脹率, 但是作為涂層材料需要優異的斷裂韌性, 因此如何調控其鐵彈性增韌將是未來一段時間探索的熱點。
2.2耐磨涂層
高溫耐磨涂層主要應用于發動機燃燒室噴嘴外罩及軸承座等零部件。目前常采用等離子噴涂技術制備 Cr3C2-NiCr、 WC-Ni、 WC-Co、 Cr2O3 涂層 。研究表明, 水會惡化涂層性能, 涂層材料斷裂韌性越高, 孔隙率和微裂紋長度越小, 涂層的耐磨性越好 。有研究表明采用多層涂層可提高抗磨損性能。
2.3抗沖蝕涂層
飛機在低空飛行、 起飛和降落過程中, 空氣中的鹽粒、 火山灰、 雪和沙粒等, 燃油雜質以及發動機部件掉落的殘骸等, 在高速氣流作用下不可避免地被吸入渦輪發動機內 。風洞實驗表明,直徑大于 30μm 的砂粒能對葉片造成明顯的沖蝕磨損, 大顆粒甚至能使葉片變形, 影響發動機性能或導致其失效 。上世紀八十年末到九十年代初, 抗沖蝕涂層技術才真正應用于航空器抗砂粒環境。目前應用最廣泛的是合金化 TiAlN、ZrAlN 等涂層、 電弧鍍等技術制備的 ZrN/TiN 多層納米涂層以及復合的 Al/AlN、Ti/TiN、 Cr/CrN涂層等(如圖 2 所示)。廣泛應用于鎳基高溫合金、鈦合金部件的抗沖蝕性能提升。總體來說,我國能在航空發動機上得到應用的抗沖蝕涂層很少, 還不能滿足設計的技術要求。
抗沖蝕涂層脆性大, 增加了合金表面裂紋萌生的傾向, 從而降低合金的疲勞性能, 是亟待解決的技術難題。另外, 耐沖蝕涂層在干燥性空氣中對壓氣機葉片具有很好的抗沖蝕防護作用, 但在海洋環境卻可能受到嚴重的潮濕或鹽霧腐蝕破壞, 使葉片壽命縮短, 給發動機帶來安全隱患。目前這些工作還處在基礎和應用研究階段。
圖 2 TiN/Zr/ZrN 多層涂層
3 海洋大氣腐蝕研究現狀
3.1海洋大氣常溫腐蝕
航空發動機在停放時將受到廢氣和尾氣中的硫化物、 氮氧化物與海洋鹽霧組合成的 pH 值為2.4~4.0 的酸性潮濕層腐蝕, 再形成酸性液膜,加速了涂層的失效 。海洋大氣常溫腐蝕一般采用乙酸鹽霧試驗以及電化學腐蝕實驗。研究表明 TBCs 經過 400 小時的乙酸鹽霧試驗后, 表面變得粗糙不平, 產生了較大的裂紋 。通過改變TBCs 涂層化學結構, 比如摻雜YSZ/ (Ni,Al) 涂層較基體和純 YSZ 涂層有更低的自腐蝕電流密度, 表現出優異的耐腐蝕能力。像 WC-CoCr 耐磨涂層在 NaCl 溶液和 HCl 溶液中, 耐腐蝕性明顯優于鍍鉻涂層, 但在 NaOH 溶液中, 鍍鉻涂層發生劇烈鈍化形成保護膜, WC-CoCr 涂層的耐腐蝕性弱于鍍鉻涂層。又比如 Ni-C 封嚴涂層在NaCl 溶液中主要發生電偶腐蝕, 溶液中的氧濃度是影響涂層腐蝕的重要因素, 腐蝕速率隨氧濃度的提升而加快。
3.2海洋大氣熱腐蝕
相比較海洋大氣常溫腐蝕, 海洋大氣熱腐蝕要復雜得多。燃氣熱腐蝕試驗 (gas hot-corrosiontest) 在指定的溫度、 燃油流量、 油氣比及海鹽含量的條件下所形成的燃氣中, 對試樣進行冷熱交變循環試驗。葉片表面溫度、 燃氣中的鹽含量以及燃油中的硫與釩是導致熱腐蝕的重要因素。目前, 熱腐蝕實驗主要是采用有涂鹽法和浸鹽法兩種。常用的熔鹽有:NaCl/Na2SO4/K2SO4/V2O5等單一或兩兩組合。熱腐蝕溫度主要集中在 800-1000℃。熱腐蝕時間以 2~10h 居多。從目前查閱的文獻來看, 實驗特點可以分為以下三種:
(a) 不帶基體的純熔鹽熱腐蝕
常用于新型陶瓷涂層材料的熱腐蝕產物分析、熱腐蝕動力學研究。采用涂鹽法或者浸鹽法, 將試樣靜置在高溫爐內。比如多元氧化物摻雜的氧化鋯/氧化鋁/磷酸涂層材料與熔鹽反應, 會生成摻雜金屬的氧化物或者鹽類而使得涂層失效。
(b) 帶基體的純熔鹽熱腐蝕
基體不一定是單晶或定向組織。采用涂鹽法或者浸鹽法, 將試樣靜置在高溫爐內。此類研究最多, 也是應用最成熟的 YSZ 及其復合涂層。研究表明采用電子束物理氣相沉積 (EB-PVD) 工藝制備 YSZ 涂層的熱腐蝕壽命可以達到等離子噴涂 (APS) 工藝制備的兩倍, 但是制備成本高、熱導率高 。YSZ 的抗熱腐蝕效應主要來自致密的 Al2O3, 其中 Cr、 Ta、 Y 能穩定 Al2O3 的生成提高涂層的抗熱腐蝕性。而外來的 Na、 V 和 S都會引起 Y 元素生成 YVO4, 使得 YSZ 涂層退化。海洋環境下, 氯化物則是 YSZ 涂層熱腐蝕的主要因素, 會造成涂層頂部以及涂層/粘結層之間產生大量的無保護性氧化物。近幾年, 人們嘗試著通過制備復合涂層來提高抗熱腐蝕性能,在實驗室獲得比較好的效果, 比如 LaPO4/YSZ/NiCoCrAlY,Sm2Sr Al2O7(SSA)/NiCrAlY 復合涂層 MgO 和 NiO 起到提高抗熱腐蝕的能力的作用。還有改進涂層制備技術, 如采用大電流脈沖電子束 (HCPEB) 工藝可以改善抗熱腐蝕性能 。
(c) 模擬海洋大氣熱腐蝕
包括高溫熔鹽電化學測試,高溫燃氣熱腐蝕,先涂鹽, 再高溫燃氣燒蝕。這類對模擬裝置要求高, 國內主要參照中華人民共和國航空工業標準HB7740-2004 進行 , 采取燃氣 + 高溫爐的方式保證高溫, 試樣保持靜置。絕大多數文獻都是以考核不同涂層工藝、 不同種類鹽、 不同溫度、 時間等對涂層材料熱腐蝕產物的影響為主, 而結合力學失效分析的研究相對較少。發動機實際工作時, 涂層是處于動態的高溫、 沖蝕、 腐蝕、 離心力環境, 因此實現模擬實際工況考察涂層的熱腐蝕顯得尤為重要, 遺憾的是, 國內外大部分實驗室還無法模擬發動機實際工況, 在這一塊發表的數據非常少, 因此模擬設備的標準化建設值得進一步探索和研究。
4 海洋大氣環境涂層腐蝕失效機制
4.1海洋大氣環境涂層常溫腐蝕失效機制
發動機各種高溫涂層一般具有多孔、 多相、多層的特性, 因而在海洋大氣環境下的失效機理可主要分為閉塞電池腐蝕和電偶腐蝕。
閉塞電池腐蝕
閉塞電池腐蝕存在特有的微縫的金屬構件中縫內外組成的電池。由于高溫涂層往往具有連續的多孔結構, 在腐蝕性環境中, 腐蝕介質能夠通過孔隙向涂層內部滲透, 在縫隙、 蝕孔內部存在“閉塞電池” 。在閉塞區域內發生貧氧、 酸化、[Cl-] 富集等變化, 在閉塞區內外電化學條件的差異產生自催化加速腐蝕效應。
電偶腐蝕
由于腐蝕電位不同, 異種金屬彼此接觸或通過其他導體連通, 處于同一介質中, 造成異種金屬接觸部位的局部腐蝕, 就是電偶腐蝕, 亦稱接觸腐蝕。高溫涂層一般由幾部分構成, 由于不同層的材料不同、 結構不同、開路電位不同, 因此在不同層之間、同層的不同材料之間形成電位差,滿足電偶腐蝕產生的熱力學因素;加之具有多孔,在不同層之間由于孔隙存在可以形成導通的回路,在高電位區域與低電位區域之間形成暢通的電子通道和離子通道, 滿足電偶腐蝕產生的動力學因素;當熱力學和動力學條件同時滿足時, 即可發生電偶腐蝕 。
4.2海洋大氣環境涂層熱腐蝕失效機制
發動機在海洋環境中服役, 必然受到高溫、高濕、 高鹽度以及大量腐蝕顆粒的考驗。因此,其熱腐蝕失效是高溫腐蝕、 熱應力、 高溫沖蝕的共同結果。
從單一因素考慮, 包括氧化相變機制、熱應力作用機制 和外來物沖蝕 三種失效機制。在熱腐蝕過程中, 氧化相變來自熔鹽與涂層的腐蝕產物、 涂層自身高溫相變以及涂層多結構之間的化學作用;熱應力作用則更為復雜, 因溫度梯度引起的熱應力、 相變導致的熱應力、 熱不匹配引發的形變熱應力、 氧化膜生長引起的應力等在界面處的聚集, 使得界面區域是破壞發生最多的區域。周益春等人 研究了涂層在熱錯配應力作用下的開裂機理, 建立了一種具有真實 TGO形貌的 TBCs 裂紋擴展有限元方法。通過對界面裂紋擴展的分析, 發現 TC/TGO 界面存在兩種失效機理:(1) 由于沒有微水平裂紋, 界面裂紋的發展導致 TC 層發生開裂;(2) 當存在微水平裂紋時,TC 層的開裂是水平裂紋和界面裂紋發展相互作用的結果。
海洋大氣環境中的鹽顆粒對涂層的沖蝕作用不可忽略。這種高溫、 高速沖蝕會在涂層粘結層內部造成裂紋源, 從而引起涂層的失效。周益春團隊構建了 APS TBCs 沖蝕模型:
其中 α 是沖擊角度, Ke 每顆粒子吸收動能的比率, v 粒子速度, δ 層厚, ρc 陶瓷層密度, Γ 陶瓷層斷裂韌性。
圖 3 熱障涂層沖蝕速率模擬
事實上, 航空發動機的高溫涂層在海洋大氣環境中服役剝落的本質是受到溫度場、 應力場、化學場等“熱力化” 耦合作用的結果。三者關系如下:
(1) 溫度場:界面氧化、 沖蝕、 CMAS 都在高溫下進行, 與溫度場有直接的關系;
(2) 應力場:TBCs 各層熱膨脹系數的不匹配、服役過程中的機械載荷決定了界面氧化、 沖蝕、CMAS 均在有應力場的作用下發生;
(3) 化學場:氧、 CMAS 和 TBCs 體系的各種元素反應生成新的化合物, 如 TGO, 硅酸鋯, 尖晶石, 而它們取決于體系的化學勢、 濃度等化學場的參量;
(4) 化學場、 溫度場、 應力場的相互促進:化學反應時新的化學產物形成時會影響體系的溫度場, 同時約束體系以及新材料加劇的熱失配將改變體系的應力場;溫度場極大的影響化學反應,如元素擴散、滲透深度、反應速度以及熱失配應力;應力場則極大的影響氧或化學反應元素的擴散。
(5) 裂紋也是熱力化耦合多場作用下的擴展過程:當有微缺陷存在時, 氧的擴散、 化學反應、應力場會在缺陷處產生明顯的聚集、 集中 , 然后進一步促進裂紋的擴展。
Loeffel 和 Anand針對熱障涂層的氧化 - 粘塑性變形問題建立了傳熱、 彈性 - 粘彈性變形、氧氣擴散和氧化反應之間的耦合, 但該理論僅考慮氧化膨脹應變而不涉及擴散介質引起的體積變化, 同時采用冪函數形式的演化率方程來抽象地描述反應速率也是有欠缺的。
湘潭大學周益春課題組對 CMAS 滲透與腐蝕的熱力化耦合理論進入了深入研究, 推導了不帶基體 TBCs 高溫腐蝕過程廣義本構關系:熵與溫度, 應力與彈性應變, 化學勢與濃度三個廣義本構關系:
其中, s 代表 CMAS 腐蝕涂層過程單位體積材料系統的熵;εe 代表高溫腐蝕過程熱量流動導致涂層的熱應變, 考慮到腐蝕條件為恒溫,則此應變等于零;Hemholtz 自由能 Ψ;溫度 θ;CMAS 濃度 c;彈性應變 εe。從目前人們對 TBCs 破壞機制的研究來看,熱力化耦合的本質機制依然存在一系列的科學問題需要解決:包括模型的建立和實驗表征等。
5 涂層性能常用的測試分析方法
研究表明熱端涂層失效的原因是受到溫度場、應力場、 化學場耦合的結果, 因此選擇時間、 空間分辨率高的分析技術來研究熱端涂層服役過程中的溫度場、 應力場、 化學場顯得極為關鍵。目前常用的測試分析方法如下。
5.1溫度場測量
隨著航空航天事業的發展, 航空發動機正向著高效率、 高性能、 高推重比(發動機推力與發動機或飛機重量的比值) 發展, 為滿足更高的要求, 需提高燃燒室的溫度, 使燃料充分燃燒, 渦輪前進口溫度也相應提高, 由于受到渦輪葉片材料的限制,熱端部件的溫度不能超過其承受范圍,否則渦輪葉片將會融化變形,造成毀滅性的事故。現在服役的第四代發動機前進口溫度已經接近2000K, 未來第五代發動機甚至可達到 2250K,在如此高的溫度下, 發動機熱端部件的溫度測量已變得極為困難。
目前航空發動機渦輪葉片溫度測量技術分為接觸式和非接觸式兩類。接觸式測量有壁溫熱電偶、 薄膜熱電偶 、 液晶測溫和示溫漆等。
壁溫熱電偶測溫是基于溫差電效應, 兩種不同材料連接成閉合回路, 當兩種金屬連接點存在溫差時會產生相應的熱電勢, 以此判定材料此時的溫度, 但是需要在測量目標上面開槽埋入熱電偶,如此會對材料的強度造成影響。為避免這個缺點,隨著沉積技術的日趨成熟, 可以將熱電偶沉積在具有絕緣層的材料表面, 這就是薄膜熱電偶。液晶測溫和示溫漆只能顯示被測材料所經歷的溫度范圍, 精確度不足, 不能實時顯示溫度, 且當渦輪葉片高速旋轉時還會發生脫落, 造成溫度測量的不準確, 因而科研工作者探索了非接觸式測溫方法。非接觸式測溫主要有紅外輻射溫度計、熱輻射高溫計, 這兩種測溫方法都是基于普朗克輻射定律, 通過搜集被測材料表面所發出的熱輻射量而確定溫度, 這種測溫方法提供了既不干擾表面也不影響周圍介質的測溫方法, 對于高速旋轉的渦輪葉片溫度的實時檢測是非常合適的。除此之外, 還有熒光溫度計、 超聲波等方法, 但是由于熒光材料、 測量精度等問題尚未在渦輪葉片上實現溫度測量。
5.2應力場測量
目前, 測量應力的方法主要分為兩大類。
(1) 機械法, 如鉆孔法、 取條法等。機械法測量殘余應力一般將具有殘余應力的部分從構件中分離或切割出來, 使應力釋放。然后測量其應變的變化求出殘余應力, 是一種間接測量手段。機械法會對工件造成一定的損傷和破壞, 但由于其具有理論完善、 技術成熟、 測量精度較高等優點,目前在現場測試中應用廣泛。
(2) 物理檢測法, 如 X 射線衍射法、 中子衍射法、 超聲波法、 納米壓痕法、 濺射深度剖析法、光激發熒光譜技術、 顯微拉曼光譜技術、 聲發射法等。這些方法均屬于無損檢測, 對工件不會造成破壞, 但成本較高, 其中 X 射線衍射法發展最為成熟。周益春團隊開展了十多年的聲發射無損檢測技術研究, 已經掌握了該方法的集成、 檢測與信號分析, 實現了服役環境模擬下失效過程的實時檢測。
5.3化學場測量
目前化學元素、 相成分、 相結構方面的測定主要有:X 射線衍射相分析、 電化學原位拉曼光譜法、 交流阻抗譜 、 原位紅外反射吸收光譜法(IRRAS)等。宮聲凱等人發現交流阻抗譜中低頻段阻抗值的變化可以有效地反映熱障涂層熱氧化層內橫向裂紋的萌生及擴展 。周益春等人從實驗和理論上解釋了熱障涂層復阻抗譜測量時電場發散的本質, 表征了氧化層厚度、 陶瓷層孔隙與氧化環境的演化關系。
但總的來說, 高溫服役環境下損傷的實時檢測,尤其是損傷的定量評價還不成熟。更重要的是,在現有的試驗模擬裝置中, 除了靜態裝置中有少量圖像、 重量、 溫度等參數的檢測手段外, 很少有成熟的無損檢測技術, 動態裝置中的檢測方法尤為匱乏, 是這一研究領域的巨大挑戰。
6 結論
航空發動機高溫涂層在海洋大氣環境下服役,除了常溫-高溫熱循環沖擊外, 還要受到高濕、 高鹽分的大氣腐蝕, 因此其失效是一個非常復雜的熱、 力、 化耦合的過程。
海洋大氣具有復雜的腐蝕性,且具有動態性、地域性等特點。同一地點的海洋大氣成分、 溫度、濕度時刻發生著變化, 不同經緯度的海洋大氣也存在差異, 因此在研究航空發動機高溫涂層耐海洋大氣腐蝕時, 需要考慮不同鹽分、 濃度、 溫度、濕度的情況;甚至需要仿真動態氣氛環境下高溫涂層的耐腐蝕性能。航空發動機高溫涂層種類多, 每一種都具有其特定的性能, 但在海洋環境中卻可能受到嚴重的潮濕或鹽霧腐蝕破壞, 使葉片壽命縮短, 給發動機帶來安全隱患。目前這些工作還處在基礎和應用研究階段。航空發動機實際服役情況是常溫-高溫熱循環狀態, 且 90% 以上時間處于常溫狀態。常溫腐蝕機制為閉塞電池腐蝕和電偶腐蝕, 常采用鹽霧腐蝕實驗和電化學腐蝕實驗進行考核。高溫熱腐蝕失效是高溫腐蝕、 熱應力、 高溫沖蝕的共同結果,本質是受到溫度場、 應力場、 化學場等“熱力化”耦合作用的結果。
測試分析的方法由事后靜態分析法向原位動態分析法發展,由接觸破壞法向無損檢測法發展。新的測試分析方法為更好地研究海洋大氣環境涂層的腐蝕失效機制提供更加精確的數據。但也要看到:針對航空發動機高溫涂層耐海洋大氣腐蝕的研究, 依然存在很多問題, 可以預期的是:
(1) 理論方面, 需要綜合考慮常溫腐蝕與高溫腐蝕交替進行過程中的氧化、 腐蝕、 蠕變、 塑性變形、 溫度梯度及基底曲率等因素的影響, 分析不同結構涂層熱循環、 腐蝕、 氧化、 沖蝕等作用下應力場與應力強度因子的演變規律。
(2) 結合非線性連續介質力學與相場理論, 建立涂層高溫氧化、CMAS 腐蝕的力化本構模型,揭示出其熱力化耦合的失效機制。
(3) 實驗方面, 探索了原子尺度下涂層界面氧化、 涂層 CMAS 的高溫原位透射電鏡觀察方法,結合第一性原理揭示了熱障涂層原子尺度下氧化、腐蝕的機理。基于所發展的各種熱力與服役環境模擬方法, 結合實時檢測技術, 系統研究了熱力載荷、 高溫氧化、 沖蝕、 CMAS 腐蝕等載荷下的失效模式與失效準則。
本文發表在《熱噴涂技術》第11卷第四期(總第42期)2019年12月:P1-P9。
免責聲明:本網站所轉載的文字、圖片與視頻資料版權歸原創作者所有,如果涉及侵權,請第一時間聯系本網刪除。
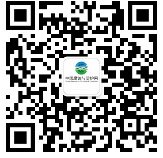
官方微信
《中國腐蝕與防護網電子期刊》征訂啟事
- 投稿聯系:編輯部
- 電話:010-62316606-806
- 郵箱:fsfhzy666@163.com
- 中國腐蝕與防護網官方QQ群:140808414