-1- 新材料地位日益凸顯
2021是十四五的開局之年,作為整個軍工產業(yè)鏈核心位置的新材料板塊有望迎來較大的發(fā)展空間。20世紀是現(xiàn)代科學技術飛速發(fā)展的一個世紀,其中重要的標志之一就是人類在航空航天領域所取得的輝煌成就。進入21世紀,航空航天已展現(xiàn)出更加廣闊的發(fā)展前景,高水平或超高水平的航空航天活動更加頻繁。航空航天事業(yè)所取得的巨大成就,與航空航天材料技術的發(fā)展和突破是分不開的。材料是現(xiàn)代高新技術和產業(yè)的基礎與先導,很大程度上是高新技術取得突破的前提條件。航空航天材料的發(fā)展對航空航天技術起到強有力的支撐和保障作用;反過來,航空航天技術的發(fā)展需求又極大地引領和促進航空航天材料的發(fā)展。可以說,材料的進步對飛機的升級換代起到關鍵的支撐作用。
航空材料既是研制生產航空產品的物質保障,又是航空產品更新?lián)Q代的技術基礎。材料在航空工業(yè)及航空產品的發(fā)展中占有極其重要的地位和作用。進入21世紀,航空材料正朝著高性能化、高功能化、多功能化、結構功能一體化、復合化、智能化、低成本以及與環(huán)境相容化的方向發(fā)展。
1. 機身材料:輕質化、高強度
戰(zhàn)斗機的高空、高速和高機動能力要求飛機的結構選材必須保證足夠的使用強度、剛度要求。根據《先進戰(zhàn)斗機結構選材與制造工藝需求分析》(李航航等,2004年10月,高能束流加工技術國際研討會),90年代后期出現(xiàn)了以美國F-22戰(zhàn)斗機為代表的第四代戰(zhàn)斗機,飛機結構采用翼身融合體結構、菱形機翼、外傾式雙垂尾和大邊條翼等;飛機結構材料雖然仍以金屬材料為主,傳統(tǒng)的鋼材和鋁合金材料的用量比例已經降低,總和不到20%。鈦合金和復合材料用量均大大超過這一比例。F-22飛機這樣選材的主要原因,一是為了減輕結構重量;二是為了滿足高溫條件下的結構使用強度要求;三是實現(xiàn)飛機結構的隱身要求等,該飛機的結構重量系數(shù)降到了27.8%。
材料具有較高的比強度和比剛度,就意味著同樣質量的材料具有更大的承受有效載荷的能力,即可增加運載能力。結構重量的減少意味著可多帶燃油或其他有效載荷,不僅可以增加飛行距離,而且可以提高單位結構重量的效費比。
不僅在軍機領域,復合材料與鈦合金在民機的不斷迭代中也扮演重要角色。根據《從A350XWB看大型客機的選材方向》(陳亞莉,2009年2月,航空制造技術),在空客(AIRFP)與波音(BAUS)的客機中,復合材料與鈦合金機體質量分數(shù)占比約為50%與15%。以飛機制造商空客為例,在A350XWB大型民機中,復合材料的用量提升最快,在機身、機翼與尾翼上均有大量應用,全機結構質量分數(shù)為53%,相比上一代民機A380大幅提升31pct;同時,鈦合金結構質量分數(shù)為14%,相比A380提升4pct。
2. 發(fā)動機材料:耐高溫為主要發(fā)展方向
熱力學第二定律指出所有熱機的熱效率均有一個上限值。熱效率的上限和熱機輸入熱的溫度(熱源溫度)及熱機的環(huán)境溫度(冷源溫度)有關。我們可以用卡諾循環(huán)來表示理想的熱機循環(huán)熱效率。
在卡諾循環(huán)中,當吸熱量為Q1,放熱量為Q2時,循環(huán)所作凈功為W0=Q1-Q2,根據卡諾循環(huán)的熱熵曲線可得卡諾循環(huán)的熱效率為:η=1-T2/T1,由此可以看出,熱機的輸入熱源溫度T1越高,熱機工作效率越高。因此,動力領域對工作溫度要求的提升將帶動相關材料的升級換代。
航空發(fā)動機渦輪入口溫度需要不斷提高。噴口溫度從1300K提升到1610K時,渦輪輸出效率可從46.40%提升到51.60%。這要求發(fā)動機材料的升級換代,同時原來那些可以使用合金鋼的零件,如壓氣機盤和葉片等,也需要使用高溫合金。
軍用航空發(fā)動機歷經五代,推重比不斷提升,高溫合金、陶瓷基復材是核心材料。第一代渦扇發(fā)動機出現(xiàn)在20世紀50年代,以英國的康維發(fā)動機、美國的JT3D發(fā)動機為代表,推重比在2左右;第二代渦扇發(fā)動機出現(xiàn)在20世紀60年代,以英國的斯貝MK202和美國的TF30發(fā)動機為代表,推重比在5左右;第三代渦扇發(fā)動機出現(xiàn)在20世紀70-80年代,以美國的F100、歐洲的RB199和蘇聯(lián)的AL-31F發(fā)動機為代表,推重比在8左右;第四代渦扇發(fā)動機出現(xiàn)在20世紀90年代,以美國的F119和歐洲的EJ200發(fā)動機為代表,推重比在10以上;第五代渦扇發(fā)動機出現(xiàn)在21世紀初,以美國的F135和英、美聯(lián)合研制的F136發(fā)動機為代表,推重比為12-13。未來航空發(fā)動機推重比將不斷提高,美國已經開啟第6代航空發(fā)動機的研發(fā),預計推重比將達到16-18。
-2- 鈦合金:性質優(yōu)良的“萬能金屬”
1. 高性能航空耗材,形成“一超多強”格局
鈦金屬具有低比重和高比強度的特性,其合金在航空航天領域對于提升飛行器推重比有重要意義,近年來受到廣泛使用。除軍工、航空航天領域之外,鈦合金還較多應用于化工、冶金、醫(yī)療、體育休閑等領域。
鈦產業(yè)鏈主要分為有色金屬和化工涂料兩條,有色金屬鏈為:鈦精礦→四氯化鈦→海綿鈦→鈦錠/鈦合金→鈦材,化工涂料鏈為:鈦精礦→四氯化鈦→鈦白粉。兩個領域上游共用鈦鐵礦、金紅石等資源。
全球鈦材消費量與航空航天業(yè)的發(fā)展息息相關。自2000年以來,我國鈦材需求主要集中在中低端的石油化工領域,隨著2016年中國“十三五”規(guī)劃的制定以及國防軍隊現(xiàn)代化的“三步走”戰(zhàn)略的更新,航空航天領域用鈦量不斷提升。對于軍用鈦材而言,由于軍工行業(yè)的特殊性,需接受國防科工局監(jiān)管,采用嚴格的行政許可制度,對產品質量的要求更苛刻,在鈦材“高均勻性、高純凈性、高穩(wěn)定性”方面提出更高的要求。2019年中國鈦材總消費量達6.9萬噸,其中航空航天用鈦量約為1.2萬噸,占總消費量的17%。我們認為,雖然近年來中國航空航天、船舶制造、海洋工程等高端用鈦占比持續(xù)優(yōu)化,但是與全球鈦材需求結構相比,高端用鈦占比依舊偏低,未來增量空間廣闊。
2021年起中國“十四五”規(guī)劃和軍隊現(xiàn)代化建設正式進入加速期,航空航天、軍工裝備等高端領域用鈦大幅提升,2019年中國鈦材總產量為7.5萬噸,同比增長18%。從產品組成上來看,板材為主要產品,產量達3.9萬噸,同比增加9%,占據鈦材產量的52%。從供給結構來看,中國鈦材制造企業(yè)呈現(xiàn)一超多強的局面。“一超”為中國鈦企龍頭寶鈦股份(600456CH),“多強”包括西部超導(688122CH)、西部材料(002149CH)等公司。雖然中國高端鈦材制造能力近年來高速發(fā)展,但仍無法完全滿足下游軍品鈦材的旺盛需求,部分鈦材仍需從烏克蘭、哈薩克斯坦等國進口。2019年中國鈦材總進口量達8116噸,小幅下滑7%。其中,技術要求較高的薄鈦板、片、帶常年處于凈進口狀態(tài),2019年凈進口1823噸,較2018年增長3%。
2. 軍用市場:新機置換進行時,高端鈦材市場廣闊
目前中國軍品鈦材主要應用在軍事戰(zhàn)機,軍用戰(zhàn)機中鈦合金主要應用于兩個部位:
(1)航空發(fā)動機:作為飛機的心臟,發(fā)動機不僅要承受極大的應力和高溫,同時還要保證高推重比(推力/質量)。發(fā)動機壓氣機盤、葉片、高壓壓氣機轉子、壓氣機機匣等部件均采用鈦合金材料。
(2)飛機機體及緊固件:鈦在中等溫度下高強度、耐腐蝕、質量輕等特性完美滿足機身用料的要求,起落架部件、大型鍛造機翼結構件、機身蒙皮、隔熱罩等均采用鈦合金制造。同時飛機上采用許多碳纖維復合材料,鈦合金與碳纖維增強的復合材料彈性模量匹配、熱膨脹系數(shù)相近;并具有很好的化學相容性,不易發(fā)生電位腐蝕。
我國軍機在數(shù)量上與美國存在較大差距,具有顯著的總量提升需求。軍用飛機是直接參加戰(zhàn)斗、保障戰(zhàn)斗行動和軍事訓練的飛機的總稱,是航空兵的主要技術裝備。據《WorldAirForces2021》統(tǒng)計,截至2020年美國現(xiàn)役軍機總數(shù)為13232架,在全球現(xiàn)役軍機中占比為25%,而我國現(xiàn)役軍機總數(shù)為3260架,在全球現(xiàn)役軍機中占比僅為6%。按各個細分機型來看,戰(zhàn)斗機是我國軍機中的主力軍,總數(shù)為1571架,但數(shù)量不到美國同期的60%,且其他機型的數(shù)量都遠落后于美國,具有顯著的總量提升需求。
3. 民用市場:亞太地區(qū)需求強勁,C919放量在即
全球客機市場空間廣闊,中國及亞太地區(qū)交付預計快速增長。
根據中國商飛公司市場預測年報(2020-2039),2019年全球噴氣式機隊共有客機共23856架。從全球歷史交付量而言,以空客為主的歐洲市場和以波音為主的北美市場占總市場的份額較大,分別占比全球總份額的20.27%和27.99%。中國和亞太地區(qū)(除中國)分別占比16.62%和16.02%,中國已成為亞太地區(qū)接近半數(shù)以上的客機交付國家。預計2020-2039年中國及亞太地區(qū)將在民航領域快速發(fā)展,占據全球約41.6%的客機交付量。
據中國商飛預測,2020-2039年全球將有40664架新機交付,價值約5.96萬億美元,用于替代和支持機隊的發(fā)展。其中,渦扇支線客機交付量為4318架,價值約為0.23萬億美元;單通道噴氣客機交付量為29127架,其占交付總量三分之二以上,價值約為3.44萬億美元;雙通道噴氣客機交付量將達7219架,總價值約為2.30萬億美元。到2039年,預計全球客機機隊規(guī)模將達44400架,是現(xiàn)有機隊的1.86倍。
面對波音、空客公司高度占據市場的既有格局,受益于本土較大的需求空間,預計未來C919、ARJ21等機型將保持一定的追趕態(tài)勢。根據中國商飛公司市場預測年報(2020-2039),預計2020-2039年中國將累計交付8725架新機,其中雙通道客機占21.41%,共計1868架;單通道客機占比高達68.05%,共計5937架;余下10.54%為920架支線客機。2020-2039年,C919和ARJ21機型市場總規(guī)模達到7320億美元,約合人民幣超4萬億。
與軍用戰(zhàn)機類似,民用客機中鈦材同樣應用于機體以及航空發(fā)動機兩大部位。雖然鈦合金結構占比整體低于軍用戰(zhàn)機,但由于空機質量大,單架客機鈦材用量顯著高于軍用戰(zhàn)機。根據《THE TRADE AND EMPLOYMENTIMPLICATIONS OF ANEWAIRCRAFT LAUNCH: THE CASE OF THE BOEING 7E7》(David Pritchard and Alan MacPherson,2003年12月,Canada-United States Trade Center),波音787夢幻客機鈦合金結構占比達15%,機身鈦合金用量約為8.5噸—10噸。中國首款具有自主知識產權的單通道渦扇噴氣客機C919,機翼機體上共有二十多個鈦合金零部件包括鍛件、厚板、薄板、管材等,鈦合金結構占比為9.3%,用量約為1.9噸。結合中國商飛《民用飛機市場預測年報(2020-2039)》,2020-2039年C919大飛機(單通道客機)民用市場帶來鈦合金需求量約11280噸。根據中國航空新聞網,2021年第一架國產大飛機C919取得適航證后或將交付給東方航空公司,隨著國產大飛機的正式交付,民用航空鈦材市場將實現(xiàn)從“零”到“一”的飛躍。
-3- 高溫合金:重點關注軍用發(fā)動機需求
1. 高溫合金,為高溫而生
傳統(tǒng)鋼鐵在300攝氏度以上會軟化,無法適應高溫環(huán)境。為了追求更高的能量轉化效率,熱機動力領域需要的工作溫度越來越高。高溫合金因此孕育而生,在600攝氏度以上的高溫環(huán)境中還可以穩(wěn)定工作,并且技術不斷進步。
高溫合金按合金的主要元素分為鐵基高溫合金、鎳基。根據智研咨詢,2018年以產品工藝區(qū)分,鎳基高溫合金產量占比為80%,鐵基高溫合金產量占比14.3%,鈷基高溫合金產量占比5.7%。
高溫合金是航空發(fā)動機的關鍵材料。根據鋼研高納(300034CH)招股說明書,高溫合金從誕生起就用于航空發(fā)動機,是制造航空航天發(fā)動機的重要材料。發(fā)動機的性能水平在很大程度上取決于高溫合金材料的性能水平。在現(xiàn)代航空發(fā)動機中,高溫合金材料的用量占發(fā)動機總重量的40%~60%,主要用于四大熱端部件:燃燒室、導向器、渦輪葉片和渦輪盤,此外,還用于機匣、環(huán)件、加力燃燒室和尾噴口等部件。
我國高溫合金產業(yè)目前處于成長期,產業(yè)鏈企業(yè)未來發(fā)展空間廣闊。我國高溫合金生產企業(yè)數(shù)量有限,生產水平與美國、俄羅斯等國有較大差距,但近些年在產能與產值上皆有明顯提升,煉石航空、西部超導等多家公司高溫合金產能項目在建設投產中。
軍用高溫合金處于持續(xù)升級中,研發(fā)能力是高溫合金企業(yè)的立足之本。以撫順特鋼,鋼研高納為首的國內老牌高溫合金企業(yè)科研根基扎實。其中,撫順特鋼的變形高溫合金市場和技術優(yōu)勢明顯,而鋼研高納鑄造高溫合金國內頂尖、研發(fā)能力卓越。以萬澤股份為代表的新興高溫合金企業(yè),業(yè)務覆蓋面廣,同時也注重新型高溫合金的研發(fā)。
2. 航空發(fā)動機用高溫合金性能不斷發(fā)展
鐵基高溫合金:我國高溫合金體系的一大特色
由于我國資源缺鎳少鈷,鐵基高溫合金的研制、生產和應用成為六七十年代的一道絢麗的風景線。根據《GH1040鐵基高溫合金》(劉哲等,2019年4月,熱處理技術與裝備)以及《高溫合金-特殊鋼叢書》(黃乾堯,2000年4月,冶金工業(yè)出版社),大量應用至今的有GH1140、GH2135、GH1040等鐵基合金。
鐵基高溫合金使用溫度較低(600~850℃),一般用于發(fā)動機中工作溫度較低的部位,如渦輪盤、機匣和軸等零件。但鐵基高溫合金中溫力學性能良好,與同類鎳基合金相當或更優(yōu),加之價格便宜,熱加工變形容易,所以鐵基合金至今仍作為渦輪盤和渦輪葉片等材料在中溫領域廣泛使用。
鎳基高溫合金:變形/鑄造/新型合金逐代升級
鎳基高溫合金一般在600℃以上承受一定應力的條件下工作,它不但有良好的高溫抗氧化和抗腐蝕能力,而且有較高的高溫強度、蠕變強度和持久強度,以及良好的抗疲勞性能。主要用于航天航空領域高溫條件下工作的結構部件,如航空發(fā)動機的工作葉片、渦輪盤、燃燒室等。
鎳基高溫合金按制造工藝,可分為變合金、鑄造高溫合金、新型高溫合金。鎳基鑄造高溫合金在發(fā)動機中主要用于渦輪導向葉片,工作溫度可達1100°C以上,也可用于渦輪葉片,其所承溫度低于相應導向葉片50-100°C。
隨著耐熱合金工作溫度越來越高,合金中的強化元素也越來越多,成分也越復雜,導致一些合金只能在鑄態(tài)上使用,不能夠熱加工變形。并且合金元素的增多使鎳基合金凝固后成分偏析也嚴重,造成組織和性能的不均勻。采用粉末冶金工藝生產高溫合金,就能解決上述問題。因為粉末顆粒小,制粉時冷卻速度快,消除了偏析,改善了熱加工性,把本來只能鑄造的合金變成可熱加工的形變高溫合金,屈服強度和疲勞性能都有提高,粉末高溫合金為生產更高強度的合金產生了新的途徑。粉末高溫合金主要用于制造高推比先進航空發(fā)動機的渦輪盤,也用于生產先進航空發(fā)動機的壓氣機盤,渦輪軸和渦輪擋板等高溫熱端零部件。
鈷基高溫合金:抗腐蝕等特殊領域前景廣闊
鈷基高溫合金的抗氧化性能較差,但其抗熱腐蝕能力比鎳好;鈷基高溫合金的高溫強度、抗熱腐蝕性能、熱疲勞性能和抗蠕變性能也比鎳基高溫合金更強,適用于制造燃氣輪機導向葉片、噴嘴等。
我國由于資源限制,目前研制了K40、GH188和L605等鈷基合金,使用范圍有限。2001年以后,通用電氣在鈷基高溫合金方面的研究主要集中在將鈷基合金作為制備燃氣渦輪機的基材材料,并在合金表面制備涂層如熱障涂層以提高耐侵蝕性能。
由于材料方面的限制,鈷元素在地球上儲量較少,價格較為昂貴。目前鈷基研究的熱度有所下降,很多科研研究也停留在數(shù)字建模試驗等理論階段。
3. 一代軍機一代合金,發(fā)動機用高溫合金或進入快速放量期
發(fā)動機對溫度的要求不斷提升。高推重比需要更高的噴口溫度,需要工作溫度更高的材料支撐。在世界高溫合金的發(fā)展歷程中,發(fā)動機葉片和盤件材料分別經歷了變形、鑄造、定向、單晶四個階段。適應溫度從600°C逐步提升至1100°以上。
最新發(fā)動機的兩片一盤的制備,取用的都是最先進的高溫合金材料。渦輪葉片和導向葉片的結構性材料以單晶高溫合金和定向金高溫合金為主。由于葉片橫截面都很薄,而橫截面尺寸越小,蠕變斷裂強度就越低,但是定向晶消除了易于形成裂紋的橫向晶界,因此持久性能、冷熱疲勞性能能及薄壁性能大幅提升,而單晶由于消除了一切晶界,性能改善更加明顯,蠕變斷裂強度降低幅度最小,因此是目前最能滿足葉片工作要求的材料。
我國渦輪葉片用高溫合金從變形合金逐漸升級到單晶合金。20世紀50年代,第一代發(fā)動機的推重比為3-4,燃氣溫度為800-1050°C,渦輪葉片材料選用使用溫度較低的變形鎳基高溫合金,其承溫能力在700-900°C;20世紀70年代前后,第二代推重比5-6的發(fā)動機選用使用溫度較同一成分變形高溫合金高30°C左右的鎳基鑄造高溫合金,其使用溫度達950°C左右;到20世紀80年代,消除了橫向晶界的定向凝固高溫合金得到了廣泛應用,其使用溫度較同一成分等軸晶鑄造合金高20-30°C,第四代發(fā)動機的葉片承溫能力達980°C左右;20世紀90年代至21世紀初,第五代發(fā)動機采用了消除了一切晶界的鎳基單晶高溫合金,由于其使用溫度又比定向凝固柱晶合金有進一步大幅度提高,最高溫度可達1050-1100°C,因而得到了廣泛應用。
軍機的換代伴隨著高溫合金的升級。第一代渦噴發(fā)動機的核心材料是變形高溫合金,核心材料工作溫度650°C,到第四代的渦扇發(fā)動機,核心材料工作溫度已經達到了1200°C,采用了單晶高溫合金。歷代軍機的換代一直伴隨著發(fā)動機核心材料——高溫合金的升級。高溫合金的升級需要研發(fā)的支持。在航空工業(yè)的發(fā)展需求牽引下,中國高溫合金先后研制出了變形、鑄造、等軸晶、定向凝固柱晶和單晶合金體系。上述高溫合金的相繼問世,不斷地推動航空工業(yè)向前發(fā)展。
據前瞻產業(yè)研究院發(fā)布的研究數(shù)據,發(fā)動機占軍用飛機成本的25%,材料成本占發(fā)動機成本的50%,而高溫合金占材料成本約35%。
根據華泰軍工《航天軍工:大國復蘇,軍工崛起》(2021年3月5日)報告,我國2021年-2030年新增軍機合計約4940架,其中以殲10、殲11、殲15為代表的三代機新增1440架,以殲16為代表的三代半戰(zhàn)斗機新增600架,以殲20為代表的四代機新增800架。根據以上假設,2021-2030年單發(fā)三代機共新增2040架,雙發(fā)四代機共新增800架。
根據美國安全研究中心發(fā)布的報告,美軍三代戰(zhàn)機F-15、F-16的制造成本分別為6500萬和4000萬美金。美軍第四代戰(zhàn)機F-22、F-35A、F-35C的制造成本分別為2.5億、1億、1.3億美金。
我們以雙發(fā)戰(zhàn)斗機對標美軍F35A、F15戰(zhàn)斗機平均8000萬美金造價;單發(fā)戰(zhàn)斗機對標美軍F16戰(zhàn)斗機4000萬美金造價;按美金:人民幣=1:6.5,發(fā)動機成本占整機25%,原材料占發(fā)動機成本占比50%,高溫合金占原材料成本35%計算,采購比1:1.2計算。2021-2030年軍機擴編將帶來高溫合金規(guī)模約497億人民幣。
高溫合金另一主要市場為發(fā)動機的維修換新。結合《World Airforces 2021》,截至2020年我國殲10保有量260架,殲11保有量315架,殲15保有量45架,殲20保有量19架。考慮到軍隊的保密措施,我國戰(zhàn)斗機實際數(shù)量或略高于《World Airforces 2021》保有量數(shù)據,我們預計到2030年,三代機與四代機的保有量預計在3000架左右,其中單發(fā)三代半機約2000架,雙發(fā)四代機約1000架。根據中國產業(yè)信息網預測,2019年軍用飛機整機采購成本和生命周期內維修成本的比例接近1:1,我們假設發(fā)動機使用壽命為10年。戰(zhàn)斗機售后維修成本中,發(fā)動機維修占比最高達到45%。其中雙發(fā)戰(zhàn)斗機對標美軍F35A、F15戰(zhàn)斗機8000萬美金造價,單發(fā)戰(zhàn)斗機對標美軍F16戰(zhàn)斗機4000萬美金造價,按美金:人民幣=1:6.5,發(fā)動機成本占整機45%,發(fā)動機1:1.2采購比計算,2021-2030年軍用發(fā)動機維修市場規(guī)模達到7020億元。根據前瞻產業(yè)研究院,原材料占發(fā)動機成本50%,高溫合金占原材料比重70%,故2030年飛機保有量達到穩(wěn)態(tài)后,我國高溫合金年均維修市場規(guī)模約295億人民幣。
根據以上測算,2021-2030年軍機列裝擴編是軍用高溫合金市場的主要增量點,總規(guī)模約為497億元,2030年軍機換代基本完成后,維修需求是高溫合金市場的主要貢獻點,年均市場規(guī)模達到295億元。我們假設2021-2030軍機列裝數(shù)量平均分布,年均49.7億元,那么2030年高溫合金總市場規(guī)模約為345億元。結合智研咨詢,2020年我國高溫合金市場規(guī)模達到231億元,其中航空航天部分占比55%,約為127億元。2021-2030年我國軍用高溫合金市場規(guī)模CAGR約為10.5%。
-4- 碳纖維:制造全環(huán)節(jié)技術壁壘高
1. 航空航天核心材料,技術壁壘較高
碳纖維是由有機纖維(主要是聚丙烯腈纖維)經碳化及石墨化處理而得到的微晶石墨材料纖維。碳纖維的含碳量在90%以上,具有強度高、比模量高(強度為鋼鐵的10倍,質量僅有鋁材的一半)、質量輕、耐腐蝕、耐疲勞、熱膨脹系數(shù)小、耐高低溫等優(yōu)越性能,是軍民用重要基礎材料,應用于航空航天、體育、汽車、建筑及其結構補強等領域。相比傳統(tǒng)金屬材料,樹脂基碳纖維模量高于鈦合金等傳統(tǒng)工業(yè)材料,強度通過設計可達到高強鋼水平、明顯高于鈦合金,在性能和輕量化兩方面優(yōu)勢都非常明顯。然而碳纖維成本也相對較高,雖然目前在航空航天等高精尖領域已部分取代傳統(tǒng)材料,但對力學性能要求相對不高的傳統(tǒng)行業(yè)則更看重經濟效益,傳統(tǒng)材料依然為主力軍。
碳纖維按不同的原材料分類,可以分為PAN基碳纖維、瀝青基碳纖維或粘膠基碳纖維。PAN基碳纖維的原料來源豐富,且其抗拉強度其他二者優(yōu)越,因此PAN基碳纖維應用領域最廣。根據智研咨詢,2018年我國PAN基纖維產量份額占90%以上。瀝青基碳纖維和粘膠基碳纖維的用途較為窄、產量小。通用級瀝青碳纖維強度和模量較低,主要應用于保溫材料領域;高性能瀝青基碳纖維多用于航空航天的工程材料。粘膠基碳纖維主要用于制作耐燒蝕和隔熱材料。
現(xiàn)代碳纖維材料始于軍用,目前航空航天為重要應用領域。現(xiàn)代的碳纖維是一種含碳量在90%以上的無機高分子纖維,具有良好的柔軟性,且縱軸方向的強度很高,具有超強的抗拉力,屬于新一代增強纖維,且碳纖維化學性質穩(wěn)定,對高溫耐受能力強,不易被腐蝕,是大型整體化結構的理想材料。與常規(guī)材料相比,碳纖維復合材料可使飛機減重,并有能力克服金屬材料容易出現(xiàn)疲勞和被腐蝕的缺點。我國軍用碳纖維產業(yè)鏈企業(yè)主要有中航高科、光威復材、中簡科技等,其中中航高科偏下游,主要為航空復材產品;光威復材實現(xiàn)全產業(yè)鏈布局,為碳纖維產業(yè)龍頭;中簡科技布局偏上游,產品技術含量相對更高。
完整的碳纖維產業(yè)鏈包含從一次能源到終端應用的完整制造過程。從石油、煤炭、天然氣均可以得到丙烯,目前低油價形勢下,原油制丙烯的成本最優(yōu);丙烯經氨氧化后得到丙烯腈,丙烯腈聚合和紡絲之后得到聚丙烯腈(PAN)原絲,再經過預氧化、低溫和高溫碳化后得到碳纖維,并可制成碳纖維織物和碳纖維預浸料,作為生產碳纖維復合材料的原材料;碳纖維經與樹脂、陶瓷等材料結合,形成碳纖維復合材料,最后由各種成型工藝得到下游應用需要的最終產品。
碳纖維制備過程中,質量過關的原絲是產業(yè)化的前提。碳纖維的強度顯著地依賴于原絲的致密性和微觀形態(tài)結構,質量過關的原絲是實現(xiàn)產業(yè)化的前提,是穩(wěn)定生產的基礎。目前,比較常用的紡絲工藝是濕法紡絲、干濕法(干噴濕紡)紡絲。在致密性方面,干噴濕紡紡絲工藝是高性能碳纖維原絲的主流制備方法,且成本相比于濕法較低。據《PAN基碳纖維生產成本分析及控制措施》(馬祥林等,2015年7月,紡織導報),在同樣的紡絲裝備及能源消耗條件下,干濕法紡絲的綜合產量是濕法紡絲的2-8倍,PAN基碳纖維絲束的生產成本可降低75%。干噴濕紡中,紡絲液從噴絲孔噴出形成細流后,先經過一段空氣層(1-20厘米),再進入凝固浴,在凝固浴中完成固化,可實現(xiàn)高速紡絲,用于生產高性能的纖維,同時具有干法和濕法的優(yōu)點。干噴濕紡也是當前國際碳纖維巨頭的主要紡絲方法,日本東麗(3402JP)的主流型號T700、T800、T1000碳纖維都是采用干噴濕紡制備而成。截止2019年,國內企業(yè)的碳纖維大部分仍采用濕法紡絲制備,頂尖龍頭已成功掌握干噴濕紡工藝。
碳纖維技術發(fā)展至今已經歷三代變遷,同時實現(xiàn)高的拉伸強度和彈性模量是目前碳纖維研制過程中的技術難點。近年來日美從兩條不同技術路徑在第三代碳纖維上取得技術突破,并有望在未來5-10年內實現(xiàn)工業(yè)化生產,對于提高戰(zhàn)機、武器的作戰(zhàn)能力意義重大。東麗利用傳統(tǒng)的PAN溶液紡絲技術使得碳纖維強度和彈性模量都得到大幅提升,通過精細控制碳化過程,在納米尺度上改善碳纖維的微結構,對碳化后纖維中石墨微晶取向、微晶尺寸、缺陷等進行控制。以當前東麗較為先進的碳纖維制品T1100G為例,T1100G的拉伸強度和彈性模量分別為6.6GPa和324GPa,比T800提高12%以及10%,正進入產業(yè)化階段。美國佐治亞理工學院從原絲制備工藝入手,利用創(chuàng)新的PAN基碳纖維凝膠紡絲技術,通過凝膠把聚合物聯(lián)結在一起,產生強勁的鏈內力和微晶取向的定向性,保證在高彈性模量所需的較大微晶尺寸情況下,仍具備高強度,從而將碳纖維拉伸強度提升至5.5~5.8GPa,拉伸彈性模量達354~375GPa。
2. 軍用需求空間廣闊,下游市場以CFRP為主
碳纖維復合材料是指至少有一種增強材料是碳纖維的復合材料,其中最常見的是樹脂基碳纖維復合材料(CFRP)。由于CFRP比強度、比彈性模量等機械性能,以及耐疲勞性、穩(wěn)定性等相比傳統(tǒng)材料有明顯優(yōu)勢,因此在很多領域內對金屬材料,尤其是輕質金屬材料形成競爭取代的局面。CFRP應用場景廣泛,在航空航天和體育休閑領域率先形成大規(guī)模市場,而隨著21世紀以來碳纖維及其復合材料制造成本不斷下降,在汽車制造、風力發(fā)電等領域應用比例在不斷提高。
根據《2019年全球碳纖維復合材料市場報告》公布的數(shù)據顯示,2019年中國碳纖維的總需求為37840噸,對比2018年的31000噸,同比增長了22%,其中,進口量為25840噸(占總需求的68%,比2018增長了17.5%),國產纖維供應量為12000噸(占總需求的31.7%,比2018年增長了33%),2019年的中國市場的總體情況供不應求,無論是進口還是國產纖維。
同時,在航空航天領域中,商用飛機需求貢獻最大,2019年商用飛機所需碳纖維達到1.62萬噸,占比約70%。商用飛機碳纖維應用市場的影響因素主要有三個:一是波音737系列停飛停產,國際航空器市場形成巨大的不確定性;二是新的單通道飛機平臺,是否會同雙通道飛機B787、A350一樣,廣泛地使用碳纖維;三是數(shù)量是雙通道飛機10倍的單通道飛機,會采用何種復合材料工藝。
此外,根據《航空航天復合材料發(fā)展現(xiàn)狀及前景》(唐見茂,2013年8月,航天器環(huán)境工程),軍用旋翼機的螺旋槳及機體結構也大量使用復合材料,如V-22“魚鷹”傾轉旋翼機所用復合材料占結構質量的40%以上,包括機身、機翼、尾翼、旋轉機構等,共用復合材料超過3000kg。歐洲最新批次的“虎”式武裝直升機結構部件的復合材料用量高達80%,接近全復材結構。相對而言,軍用運輸機上復合材料用量不多,如C-17占8%、C-130J僅占2%,但空客A400M軍用運輸機上采用全復合材料機翼,復合材料用量占飛機空載時結構質量的35%。
我們根據美國三代機及以上機型數(shù)量測算,結合智研咨詢預測,2021-2030年中國新增軍機4940架左右,其中殲20空機重量18噸,生產800架,需求將達到1944噸,殲11空機重量10噸。此外,考慮軍用直升機約600架,空機重量5噸;大型運輸機及加油機等200架,空機重量60噸,碳纖維比例10%。按照結構重量占50%計算,同時參照智研咨詢及《航空航天復合材料發(fā)展現(xiàn)狀及前景》(唐見茂,2013年8月,航天器環(huán)境工程)對各型號軍機碳纖維比例的統(tǒng)計,我們預計2021-2030年我國新增軍機的碳纖維需求量約為6524噸。
3. 碳碳復合材料:新型剎車材料,軍用市場前景明朗
碳/碳復合材料是以碳纖維為增強體,以化學氣相沉積炭或樹脂炭為基體的復合材料,主要用作剎車盤。剎車盤是以摩擦材料設計技術和制備技術為核心的剎車制動類產品,用于飛機、坦克裝甲車輛和高速列車的剎車制動。
在“最嚴酷著陸停止”實驗中,即考慮其他剎車系統(tǒng)都損壞的情況下,飛機機輪剎車可吸收超300兆焦耳能量,溫度短時間內快速上市至千度以上,因此飛機對剎車盤材料耐高溫性及穩(wěn)定性、減少變形等方面都有嚴格的要求。
與鋼剎車盤相比,碳剎車盤的突出優(yōu)點是:
(1)減輕了剎車裝置的重量:根據《C/C復合材料在制動系統(tǒng)的應用及發(fā)展》(程皓等,2020年3月,炭素),炭剎車盤的密度為1.75g/cm3~1.80g/cm3左右,與金屬剎車相比,可節(jié)省40%左右的結構重量。剎車力矩平穩(wěn),剎車時噪聲小,飛機性能明顯改進。
(2)提高了剎車盤的使用壽命:根據《C/C復合材料在制動系統(tǒng)的應用及發(fā)展》(程皓等,2020年3月,炭素),在同等使用條件下的磨損量約為金屬剎車的1/3~l/7,使用壽命是金屬剎車的5~7倍。一般軍機上的使用壽命約1000次起落,客機的使用壽命2000~3000次起落。磨損到極限后,炭剎車盤還可以通過整體粘接、“二合一”鉚接等修復方式進行維修,繼續(xù)延長使用壽命,降低成本,提高經濟性。
(3)工作溫度高:根據《某民用飛機碳剎車動力實驗》(張強等,2007年3月,江蘇省航空航天學會飛行器專業(yè)委員會2007年學術年會),當使用溫度上升到775°C時,碳/碳復合材料的比強度仍保持不變,鋼材料則有顯著降低,鋼剎車盤的最高使用溫度不超過900°C,溫度高于900°C時,鋼剎車盤會發(fā)生粘結現(xiàn)象。碳/碳復合剎車材料在2000°C的高溫下也不會熔化,不會發(fā)生粘結現(xiàn)象,也沒有明顯的翹曲變形。
(4)剎車平穩(wěn):碳剎車系統(tǒng)中的碳剎車機輪和防滑控制系統(tǒng)配合使用,可以保證恒定的打滑量并及時釋放剎車能量,并且在高溫下剎車盤也不易損壞,從而保證了剎車過程的平穩(wěn)。
由于碳/碳復合材料具有密度低、耐高溫、抗腐蝕、摩擦磨損性能優(yōu)異、抗熱振性好及不易發(fā)生突發(fā)災難性破壞等一系列優(yōu)點,現(xiàn)已成為航空制動裝置的首選剎車材料。現(xiàn)代的高性能民用客機,如波音747、波音757、波音767、空客系列、麥道系列等都采用碳/碳復合制動材料剎車裝置。隨著我國經濟的不斷發(fā)展和經濟全球化的深入,整個航空業(yè)呈現(xiàn)出快速發(fā)展的趨勢,國內營運機隊數(shù)量及規(guī)模的不斷擴大,給民航產品業(yè)務發(fā)展帶來了巨大的機遇。而飛機剎車盤作為耗材,每次在磨損到標后都需要進行更換,市場需求量很大,目前主要依賴于進口。國外主要的碳剎車盤制造商有法國賽峰公司(SAFFP)、美國聯(lián)合航空運輸公司(UALUS)、霍尼韋爾(HONUS)與英國的美捷特(MGGTLN)公司。國外公司(OEM件)采用短纖維模壓工藝生產碳剎車盤,具有良好的摩擦磨損性能,但是其力學性能相對偏低。
為了進一步提高碳剎車盤的力學性能,以提升剎車材料及飛機的安全性,以北摩高科、西安制動為代表的國內公司采用整體針刺氈聯(lián)合化學氣相沉積工藝制備碳剎車盤,最終實現(xiàn)碳剎車盤國產化。
根據北摩高科招股說明書,軍用飛機主機輪裝配數(shù)量約為戰(zhàn)斗機4個/架,加油機3個/架,運輸機12個/架,武裝直升機4個/架,教練機3個/架,結合智研咨詢對我國軍機2021-2030增量的預測,2030年新裝機主機輪市場總容量有望達到48332余個。單價方面,由于國內該產品單價涉及國家機密暫無公開披露,我們參考國外航空設備采購網站skygee的碳/碳剎車系統(tǒng)(Aircraft Braking Systems 5011809-3 Carbon Brake)標價為15萬美元,約合90萬人民幣。考慮到國產產品的成本優(yōu)勢以及國外剎車系統(tǒng)按組裝完成后售賣,有一定的溢價,我們按照剎車盤+主機輪60萬人民幣/套的單價估算,2030年增量市場穩(wěn)定后,預計軍用飛機每年更換一次主機輪,2030年剎車系統(tǒng)市場規(guī)模有望達到290億元。根據《WorldAir Forces 2021》,我國目前有維修價值的二代、三代戰(zhàn)機和各類通用機型保有量約為3365架,按照北摩高科招股說明書的主機輪裝配數(shù)量測算,2020年軍機剎車主機輪需求約為21272套。2021-2030剎車系統(tǒng)市場規(guī)模CAGR約為8.6%。
免責聲明:本網站所轉載的文字、圖片與視頻資料版權歸原創(chuàng)作者所有,如果涉及侵權,請第一時間聯(lián)系本網刪除。
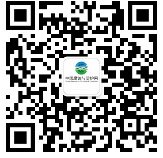
官方微信
《中國腐蝕與防護網電子期刊》征訂啟事
- 投稿聯(lián)系:編輯部
- 電話:010-62316606-806
- 郵箱:fsfhzy666@163.com
- 中國腐蝕與防護網官方QQ群:140808414