相信很多關心航空發動機發展的金粉們都聽過這樣一個斷言:航空發動機不好是因為材料不行。材料是問題之一,但難題是多方面的。一臺民用發動機需要無故障地、穩定地工作3萬小時,在工作過程中,一方面轉速極高(每分鐘約15000轉),需要承擔葉片本身重量1萬倍的離心力;另一方面,燃燒室溫度達到1800K以上,與之對照,目前熔點最高的鎳基高溫合金初熔點不到1600K。
今天,我們來盤點一下民用航空發動機制造的四個難點。
↓↓航空發動機爆炸圖↓↓
1 對安全性和可靠性要求極高
在極端的工作條件下,民用航空發動機需要穩定地工作3萬小時,預計未來要求能達到穩定工作10萬小時以上。為了確保航發的安全和可靠,兩個實驗必不可少——拋鳥實驗、吞冰實驗。
↓↓拋鳥實驗↓↓
美國2009年哈德遜河迫降是航空史上有名的事件,當時飛機出故障的原因,正是在紐約機場起飛一分鐘后兩個引擎均受鳥撞擊而失去動力,最后不得不迫降在哈德遜河。
↓↓吞冰實驗↓↓
2 每分鐘15000轉,承受巨大離心力
發動機葉片每分鐘轉速大約在15000~16000rpm之間,此時,轉動葉片的離心力相當于葉片重量的10000倍。更為直觀地說,航空發動機1個葉片榫頭(工作葉片和渦輪盤相連的部分)所承受的離心力高達約150kN,大約15噸。
3 燃燒室溫度1800K以上,超過高溫合金熔點
↓↓航發各部分金屬材料分布↓↓
民機發動機燃燒室的溫度達到1800~1900K,鎳基高溫合金的初熔點大概也就在1300℃左右,也不到1600K。
↓↓鎳基高溫合金在高溫下比強度較其他金屬更高↓↓
發動機葉片的工作溫度已經遠遠超出了合金的熔點,為解決這個問題,可以采取幾大技術。
1、冷卻
早期葉片多為實心,隨著鑄造技術的進步,葉片發展為定向(單晶)空心無余量葉片。空心氣冷葉片的出現,在降低葉片重量的同時,可讓冷空氣可進入腔內冷卻。
上文提到單晶葉片,在此不妨稍微離題,介紹下國內單晶葉片的生產水平。單晶葉片是航發零件中生產工序多(40~60道工序)、周期長、合格率低的一種零件,其生產的關鍵設備包括熱處理爐和單晶爐。一級航空熱處理爐在生產葉片時爐內溫度在1330℃,爐內任意兩點溫度差處于正負3℃范圍內,這種熱處理爐國內尚無法生產,單晶爐的供應面臨著類似狀況。根據《經濟半小時》報道,2015年,成都航宇成功突破技術難關,成為國內首家單晶錸合金葉片達到量產標準的企業。
↓↓單晶鑄造渦輪葉片的微觀結構↓↓
2、繼續提高合金承溫能力
↓↓渦輪葉片的成形工藝和晶相結構↓↓
3、熱障涂層(Thermal Barrier Coating)
熱障涂層本質是一層陶瓷涂層,此概念于上世紀50年代提出,80年代技術取得重大突破。
熱障涂沉積在耐高溫金屬或超合金的表面,對于基底材料起到隔熱作用,降低基底溫度,使得用其制成的器件(如發動機渦輪葉片) 能在高溫下運行,并且可以提高器件(發動機等)熱效率達到60%以上。
4 17級風速下,火焰還需穩定燃燒
↓↓渦扇發動機發動機氣流控制↓↓
免責聲明:本網站所轉載的文字、圖片與視頻資料版權歸原創作者所有,如果涉及侵權,請第一時間聯系本網刪除。
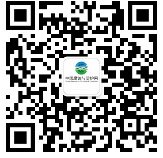
官方微信
《腐蝕與防護網電子期刊》征訂啟事
- 投稿聯系:編輯部
- 電話:010-62316606
- 郵箱:fsfhzy666@163.com
- 腐蝕與防護網官方QQ群:140808414