由于CO2具有良好的驅油效果和廣泛的適應性,并且CO2驅能夠實現溫室氣體的地下封存,具有環保效益,國內各油田相繼開展了規模不同的先導試驗,探索了不同類型油藏CO2驅的可行性,現場試驗表明,國內適合CO2驅的儲量豐富,應用前景廣闊。腐蝕控制是油田CO2驅的關鍵技術,國內外都開展了有針對性的腐蝕機理與腐蝕控制技術研究。國外自上世紀八十年代就進入了規模應用,腐蝕控制技術成熟。國內目前還處于探索階段,現場實驗取得了良好效果。從國內外CO2驅的腐蝕控制技術來看是基本一致的,但對于腐蝕速率的控制,國內外做法具有明顯的不同。開展腐蝕控制研究,確定合理的腐蝕速率控制值對于降低油田開發成本,保證CO2驅油田生產順利進行具有重要意義。
圖注:CO2驅油田注采井油套管腐蝕速率控制值的探討
1 CO2驅油田腐蝕速率控制值現狀
國內外CO2驅油田普遍采用普通碳鋼(J-55、N-80等)油套管通過添加緩蝕劑的措施來控制腐蝕。中石油的吉林油田在黑59、黑79試驗區在油層部位還使用了不銹鋼套管。
通過公開發表的文獻檢索分析以及與國外資深專家交流情況來看,在使用緩蝕劑控制碳鋼腐蝕速率方面,國外并無統一或明確的腐蝕速率控制標準值,他們的做法是通過實驗選擇最優的緩蝕劑。
與國外不同的是,我國在腐蝕速率控制方面普遍采用了0.076mm/a作為開發方案設計控制值、緩蝕劑篩選評價值或腐蝕控制效果評價值。這一數值從工程安全和成本上是否是最優的,仍需要進一步探討。
2 關于腐蝕速率0.076mm/a的探討
平均腐蝕速率0.076mm/a來自于《碎屑巖油藏注水水質推薦指標及分析方法》(SY/T5329-2012)中的推薦注水水質的控制指標。這一指標的確定方法是,當水質滿足了其它指標后,檢測試樣水對現場用鋼(一般選碳素鋼如Q235)的腐蝕速率,測試時間為30±2天,得出最大腐蝕速率小于0.076mm/a。該數值是基于水質的其它控制指標達到標準后的一個必然數值。
上述標準中主要考慮的腐蝕源不同于CO2驅油田的實際。標準中CO2是輔助性控制指標,是腐蝕的次要因素。一方面,水中的細菌作為主要腐蝕因素在標準中是主要控制指標,而CO2濃度是作為輔助性控制指標。另一方面,標準中規定CO2濃度為-1.0≤ρCO2≤1.0㎎/L,且在早期的標準版本中規定PH值為7±0.5,研究表明,CO2腐蝕依賴于PH值,在注入水為中性的條件下,CO2引起的腐蝕基本是可以忽略的。
上述標準中的腐蝕環境與CO2驅油田的腐蝕環境也是大不相同的。CO2驅油田的注入井在氣水交替初期,或采油井產出液中含水和CO2較高的井,其水中溶解的CO2濃度往往達到飽和狀態。研究表明,在常壓下,油田水中CO2的飽和濃度約為270㎎/L,注采井隨井深的增加,溫度和壓力上升,雖然溫度升高會降低CO2的溶解度,但壓力升高又提高了CO2的溶解度,因此,井下環境中CO2濃度遠遠超過1.0㎎/L。另外,標準中的腐蝕速率0.076mm/a是未加緩蝕劑條件下產生的,而油田井下一般通過添加緩蝕劑來控制CO2的腐蝕。
從測試環境、主要考慮的腐蝕源和腐蝕環境來看,將《碎屑巖油藏注水水質推薦指標及分析方法》中規定的0.076mm/a這個數值直接作為CO2驅油田腐蝕環境下的選材與腐蝕控制衡量指標是不合理的。
3 合理的CO2驅油田腐蝕控制速率探討
3.1 通過強度計算反推平均腐蝕速率控制值
通過加注緩蝕劑減緩CO2對碳鋼的腐蝕或選擇耐腐蝕材料,其目的是保護井下油套管,保證采油設施和各種采油作業的正常、安全運行,只要井下油套管的剩余強度達到需求,其壽命期間的控制腐蝕速率就應該是合理的。
下面分析找出注采井的危險工況,然后計算其所需強度,進而計算出合理的控制腐蝕速度。由于CO2驅大多應用于低滲透油藏,下面的分析以低滲透油藏為例。
油井完井后的套管強度,對于采油井來說,低滲透油藏的壓裂改造作業是最危險的工況。實際上,低滲透油藏開發井一般在投產時或投產初期即進行壓裂,進行重復壓裂的井是很少的,且壓裂也不會安排在20年末進行,況且,為了防止低滲透油藏CO2驅開發井發生氣竄,油井可能不進行壓裂,對于腐蝕后的剩余強度來說,壓裂作業并不是最危險工況。采油生產過程中,套管最危險處是水泥返高處,當動液面低于這個深度時,套管就受到了管外地層靜壓力的擠壓,此為工況Ⅰ;對于注氣井來說,最危險的工況莫過于出現井口失控,注入氣氣化噴出后井筒掏空,此時套管的危險井段是油層部位,套管需要承受地層的靜壓力的外擠,此為工況Ⅱ。
根據以上的分析進行計算條件假設:油層中深H=3000m,水泥返高h=2000m,套管外徑D=139.7㎜,套管壁厚δ=9.17㎜,油層部位套管鋼級P110(758MPa),其它部位套管鋼級N80(552MPa)。油層靜壓Pr=40MPa,沿井筒平均地層壓力系數1.2,油井壽命20年。
套管抗外擠強度經驗計算公式為:
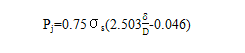
式中:
Pj—套管的抗外擠強度,MPa
σs—屈服應力,MPa。
假定腐蝕僅從內部發生,抗擠毀強度安全系數取1.125 。首先計算以上二種危險工況下套管的允許極限剩余壁厚,然后求出20年平均腐蝕速率,計算結果見表1。
表1 二種工況下套管允許腐蝕速率計算結果
工況 | 原始壁厚 mm |
剩余壁厚 mm |
被腐蝕厚度 mm |
20年平均腐蝕速率 mm/a |
工況Ⅰ | 9.17 | 6.22 | 2.95 | 0.1475 |
工況Ⅱ | 6.99 | 2.18 | 0.109 |
3.2 現場使用緩蝕劑取得的控制腐蝕速率值
為了控制CO2腐蝕,科學工作者針對不同油田的腐蝕環境,開發出了多種類型緩蝕劑,包括通常采用的油溶性、水分散劑型緩蝕劑(常用長鏈脂肪酸),如胺類、酰胺類、亞胺類、咪唑啉等有機長鏈化合物,還有有機磷酸鹽。緩蝕劑全面地減緩了CO2對碳鋼的腐蝕,緩蝕率一般達到80%以上,優選的緩蝕劑的緩蝕率可達90%以上。
緩蝕劑在現場應用中也表現了較好的效果。
草舍油田泰州組油藏于2005年7月開始CO2驅試驗,注入方式為水氣交替注入,綜合含水率51%。通過室內實驗,評價出HS-20型CO2高效緩蝕劑并在現場應用,濃度為50~200μL/L。監測結果表明,井下油管腐蝕速率為0.01~0.001mm/a。
吉林油田黑59塊CO2驅試驗區,注CO2前產出水對碳鋼的腐蝕速率就達到0.5~0.7mm/a,通過緩蝕劑優選和加注工藝優化,現場應用的FRD-10型緩蝕劑將CO2腐蝕速率控制在了0.0067~0.0125mm/a 之間。
四川氣田是典型的含硫氣田,其幾個主力氣田均存在較為嚴重的腐蝕,其天然氣中含CO2 0.1%~ 4. 69%,通過井下加注緩蝕劑防腐,監測腐蝕速率為0.0066~0.0081 mm/a。
現場應用表明,通過優選、復配適用的緩蝕劑,配套優化緩蝕劑加注工藝,CO2對碳鋼的腐蝕速率一般可控制在0.01 mm/a左右。
3.3 腐蝕速率控制值的討論
對于發生均勻腐蝕的材料來講,通過選取最危險工況條件下油套管的強度計算,所獲得的20年壽命周期內允許的平均腐蝕速率,完全可以滿足安全生產需要,可以作為選材依據。
對于發生非均勻腐蝕的普通碳鋼來講,不能把獲得的20年壽命周期內允許的平均腐蝕速率來作為選擇緩蝕劑的依據。實驗研究表明,CO2對碳鋼的腐蝕形態主要是點蝕、臺地腐蝕和全面腐蝕,在腐蝕較嚴重的環境,點蝕的平均腐蝕坑深是平均腐蝕速度的10倍以上,臺地腐蝕的平均腐蝕坑深是平均腐蝕速度的2倍以上。即使使用緩蝕劑,也不能阻止點蝕或臺地腐蝕的發生。按照上述實驗成果并結合表1中的計算結果,點蝕的數學累積深度分別會達到29.5mm(采油井)/21.8mm(注氣井),這顯然會造成油套管的早期腐蝕穿孔。
如前所述,現場科學地使用緩蝕劑能夠使CO2對碳鋼的腐蝕速率控制在0.01 mm/a左右。這一數據僅是強度計算所獲得的20年壽命周期內允許的平均腐蝕速率的10%左右,顯然滿足生產過程對油套管的強度需求。按照點蝕坑深是平均腐蝕速度的10倍來計算,20年的最大坑深的數學累積深度為2mm,也不會造成管材腐蝕穿孔。實驗室篩選緩蝕劑,模擬現場腐蝕最嚴重的工況,由于實驗時間短,所獲得的腐蝕速率會較現場實際應用的真實腐蝕速率高。因此,就CO2緩蝕劑優選來講,沒有一個合適的、可以作為標準的控制腐蝕速率值,從經濟性、技術性和安全性三個方面綜合考慮,優選出最優的緩蝕劑更為恰當。
4 結論
0.076mm/a 來自于標準SY/T5329-2012《碎屑巖油藏注水水質推薦指標及分析方法》,它是基于水質的其它控制指標達到標準后的一個必然數值,直接把它作為CO2驅油田腐蝕環境下的選材與腐蝕控制衡量指標是不合理的。
對于發生均勻腐蝕的材料,通過最危險工況條件下油套管的強度計算所獲得的壽命周期內允許的平均腐蝕速率可以作為選材依據。
沒有必要設定一個平均腐蝕速率標準值來作為CO2驅油田腐蝕環境下優選、評價緩蝕劑的衡量指標。從經濟性、技術性和安全性三個方面綜合考慮科學選用緩蝕劑,更具有實際意義。
責任編輯:田雙
《中國腐蝕與防護網電子期刊》征訂啟事
投稿聯系:編輯部
電話:010-62313558-801
郵箱:ecorr_org@163.com
中國腐蝕與防護網官方 QQ群:140808414
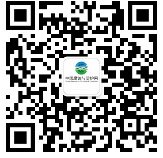
官方微信
《中國腐蝕與防護網電子期刊》征訂啟事
- 投稿聯系:編輯部
- 電話:010-62313558-806
- 郵箱:fsfhzy666@163.com
- 中國腐蝕與防護網官方QQ群:140808414