摘要:分析總結了進口含硫原油給我國石油運輸、貯存及煉化加工設備和裝置所帶來的新的腐蝕問題,并探討應對之策。
關健詞:含硫、原油、儲罐、管道、腐蝕、涂層防護
圖注:針對儲罐腐蝕的涂層防護
0 前言
隨著我國經濟的快速發展,對石油以及石化產品需求不斷增加,對進口原油的依賴越來越強。2011年我國原油消耗量4.9億噸,其中進口原油占54.8%。我國進口原油的主要產地有中東(沙特、阿曼、蘇丹等)、哈薩克斯坦、俄羅斯、南美(委內瑞拉)。不同產地的原油,其物性和腐蝕性不一樣,原油的腐蝕性可從五個指標來評價:即原油酸值、硫含量、鹽含量、氮含量和水含量。其中,硫含量<0.5%為低硫原油,硫含量0.5%~2.0%為中硫原油,硫含量>2.0%則為高硫原油。中東原油90%以上是含硫油,俄羅斯和哈薩克斯坦含硫原油占一半,委內瑞拉大多屬于高含硫原油。而國產原油除勝利原油屬于含硫原油外,其它多為腐蝕性較輕的低硫含蠟原油。含硫原油的大量進口和煉制給我國原油輸送管道和儲罐以及煉化廠的加工與貯運設施均會帶來嚴重的腐蝕問題,給安全運行帶來威協。因此,研究含硫油品的腐蝕與防護,選擇適用的防腐蝕涂料與涂層體系,就顯得尤為重要。
1 硫對鋼鐵的腐蝕
硫在原油中的存在形態主要有元素硫、硫化氫、硫醇、硫醚、二硫化物、噻吩類化合物以及分子量大、結構復雜的含硫化合物。一般將原油中存在的硫分為活性硫和非活性硫。元素硫、硫化氫和低分子硫醇等能直接與金屬作用而引起設備的腐蝕,統稱為“活性硫”,其余不能直接與金屬作用的硫化物統稱為“非活性硫”。但在高溫下,“非活性硫”能向“活性硫”轉化。不同產地的含硫原油,除了含硫量不同之外,由于所含硫化合物的種類及活性硫的含量也不同,也會影響到其腐蝕性能。含硫原油在煉制過程中,硫會不可避免地進人下游裝置的生產過程中并且和部分產品油共存。
而硫對金屬的腐蝕性,也與溫度及其它腐蝕性成分含量等有極大的關系。通常,在介質溫度≤120℃的情況下才會考慮采用涂層防護,因而,該溫度區間下的含硫油品的腐蝕與防護才是從事防腐蝕涂料技術工作需要關注的重點領域。
相關資料認為,當溫度≤120℃,硫對鋼材的腐蝕形式主要分為以下幾種:
①.H2S-H20型腐蝕
H2S氣體在沒有液態水時(氣相狀態)對鋼材的腐蝕很輕,甚至根本沒有腐蝕,但是當遇到水時,極易水解,在水中發生H2S-H20型腐蝕,其反應的電離方程式為:
H2S—H++HS-
H2S—H++S2-
在H2S-H20體系中的H+、HS-、S2-和H2S分子對金屬的腐蝕為去極化作用,其反應方程式為:
陽極反應:
Fe—Fe++2e
Fe2++S2-—FeS
或Fe2++HS-—FeS+H++e
陰極反應:
2H++2e—2H+H2
②.積水中SO2腐蝕
貯運裝置積水部位中的SO2對防腐層脫落的鋼材發生改性再生循環腐蝕,首先是S02在水中以亞硫酸形式存在,與Fe反應生成硫酸亞鐵FeSO3,之后硫酸亞鐵水解又形成游離的亞硫酸,而游離的酸又加速了鐵的腐蝕,生成新硫酸亞鐵,如此反復循環加速了對鋼材的酸性腐蝕。
③硫酸鹽還原菌腐蝕
原油中硫化物含量的增加,加大了硫酸鹽還原菌腐蝕的風險。硫酸鹽還原菌在缺氧的條件下,可以在金屬表面的水膜中,利用溶液中的硫酸鹽進行繁殖,硫酸鹽在細菌作用下被還原為腐蝕性硫化物和有機酸。在缺氧的條件下,硫酸鹽還原菌的代謝引起硫化物在金屬表面附近的積累,當金屬表面被生物膜覆蓋時,硫化物在金屬表面附近的濃度最高。如果鐵離子和硫化物離子都存在,硫化鐵很快在碳鋼上形成并覆蓋其表面。硫化鐵的生成促進了陰極反應,電通道一旦形成,一個以低碳鋼表面為陽極的電偶就生成了,電子通過硫化鐵來傳遞。在鐵離子濃度低時,暫時附著的保護性硫化鐵膜在鋼鐵表面形成,從而降低了腐蝕速率,因此在完全無氧條件下的硫酸鹽還原菌具有較低的腐蝕速率。然而一旦有氧存在時,硫酸鹽還原菌代謝過程中產生的硫化亞鐵開始氧化,最常見的有兩種氧化過程:一種是直接吸收氧,生成硫酸亞鐵,硫酸亞鐵在水中水解并氧化成鐵的氧化物和硫酸,加大了腐蝕速度。另一種是硫化亞鐵氧化成鐵的氧化物和硫磺,反應生成的硫磺將溶于油品中,在腐蝕鋼材的同時造成油品污染。
當然,硫介質只是貯運設施中存在的各種復雜腐蝕性介質中的一種,水的存在是產生硫腐蝕的必要條件,而且在不同的運行環境下,硫對底材的腐蝕形式和程度也不同。但硫在油品中的存在會大大加速腐蝕,從而減短設備使用壽命,甚至導致安全和環境污染事故的發生,這是我們必須引起重視的。
2 含硫原油輸送管道內腐蝕與防護
由于國產原油大多為低硫含蠟原油,通常情況下,原油中的蠟會在長輸管道內壁沉積,因此早期我國長輸管道內腐蝕問題相對較輕,長輸管道內腐蝕問題也并沒有受到人們的重視,也并沒有采取防護措施。但近年來長輸管道內腐蝕檢測發現,輸送進口含硫原油長輸管道內腐蝕問題日益突出,如今年針對甬寧線的內腐蝕檢測發現,內壁已出現多處腐蝕減薄現象。國外關于管線內腐蝕引起原油泄漏事故的報導也時有發生。
目前,各石油公司多采用原油脫水、除鹽、加緩蝕劑和滅菌劑等方式來進行長輸管道的內腐蝕防護,尚未采取涂層防護。由于腐蝕過程難于監測,內腐蝕檢測費用相當困難和昂貴,現行防護手段是否足夠保證管線的設計使用壽命尚未可知。
在含硫原油輸送管道內表面采用涂層防護以延長管線使用壽命,技術上完全具有可行性。采用高固體份或無溶劑等液體環氧涂料,通過無空氣噴涂或離心噴涂方式在流水線上完成工廠化涂裝和現場管道補口,這已經在大量輸水、輸鹵管道等工程上得到了成熟應用。在含硫原油輸送管道上推行內涂層防護只是需要進一步的經濟性和必要性評估與論證。
3 含硫原油儲罐的內腐蝕與防護
國家石油戰略儲備計劃的實施需要建設大量原油儲罐,這些儲罐多為大型外浮頂罐,大多貯存進口含硫原油。由于油田采油時脫水不完全以及在管輸、船運及泵送過程中難已避免地混入水蒸汽及海水,水易在罐底沉積,導致罐底板上表面成為腐蝕最嚴重的部位。相關資料介紹,罐底板上表面以坑蝕為主,均勻腐蝕減薄也很嚴重,有些原油罐投用后未到檢修年限,底板便腐蝕穿孔。硫在罐底板腐蝕過程中無疑扮演了最為重要的角色。
《GB50393-2008鋼質石油儲罐防腐蝕工程技術規范》、中石化《加工高含硫原油儲罐防腐蝕技術管理規定》及中國涂料工業協會行業規范CNCIA-HG/T0001-2006《石油貯罐導靜電防腐蝕涂料涂裝與驗收規范》中均指出:原油儲罐底板內表面和油水分界線以下的壁板內表面應采用犧牲陽極和絕緣型防腐蝕涂層保護相結合的保護形式,但在絕緣涂層的表面電阻率和最小干膜厚度要求上存在差異。高固體厚漿型環氧玻璃鱗片涂料、無溶劑環氧防腐涂料等,以其優異的耐油性、耐酸堿性、耐硫化物、絕緣性和易厚涂性,已成為該部位常用的涂料類型。
4 含硫中間產品及部分成品油儲罐的腐蝕與防護
含硫原油在煉制過程中,各種型態的硫化物及其遇高溫時分解產生大量的H2S氣體均會不可避免地進入下游產品中。而硫在下游產品中存在的型態及含量與原油及煉制工藝相關。一般認為,硫醇和硫化氫主要分布在沸點50~250℃的餾分中,元素硫和二硫化物主要分布在100~250℃的餾分中,二硫醚類和噻吩類硫化物則主要分布在沸點高于200℃的餾分中。沸點越低,活性硫特別是硫化氫的比例越高,因硫而造成的腐蝕就越嚴重。通常存在硫腐蝕的中間產品和成品油儲罐包括中間汽柴油罐、石腦油罐、蠟油罐、污油罐、重油罐及含硫污水罐等。
4.1中間汽柴油罐及石腦油罐
芳烴(溶劑)、酸、堿、烴類、硫、水等,罐體結構為內浮頂或固定拱頂,在所有被腐蝕的儲罐中,中間汽油罐和石腦油罐的腐蝕最嚴重。
1)腐蝕狀況
主要表現為涂層鼓泡、脫落、鋼板表面產生大量鐵銹(包括硫化鐵),掉鐵銹后鋼板表面發現密密麻麻的坑點,有些坑點在打砂后出現穿孔。內浮頂罐的腐蝕部位一般出現在罐體中間壁板部分,罐頂及頂第一圈板、罐底及底第一圈板往往涂層完好。傳統的油罐腐蝕理論認為,汽油罐頂板腐蝕最嚴重,底板次之,圈板最輕,與目前的實際情況相反。上述油罐涂層使用時間均在4年以下。硫化氫或堿含量高的中間汽油罐鋁浮盤腐蝕較嚴重。拱頂罐的腐蝕部位主要在氣相,罐底存水部位也較嚴重。
2)腐蝕機理分析
油罐任何部位的腐蝕都是由氧和水(液態)的參與而發生的,其它腐蝕介質如酸、硫化氫、二氧化碳等,特別是硫化氫的存在加劇了罐體的腐蝕,加工高含硫原油以來罐體腐蝕速度增加數倍,甚至數十倍于加工國產原油時的情況,原因正在于此。空氣中的相對濕度越大,腐蝕速度越快;介質溫度越高,腐蝕速度越快。這也是南方地區油罐腐蝕遠較北方嚴重的原因之一。總的來看,汽油中的含氧量在油品中最高,含硫化氫濃度最高,故腐蝕最劇烈。
內浮頂罐的結構是造成上述腐蝕狀況的另一重要因素。內浮頂密封膠帶對罐壁長期的反復摩擦使涂層造成破壞,如果涂層不光滑,這種破壞將更加廣泛和容易。罐內油氣絕大部分集中于密封膠帶附近的罐壁處,這里的油氣含硫化氫濃度高,油氣相交替最頻繁,腐蝕也較嚴重。
外浮頂石腦油罐罐內壁自浮船起浮高度(約210m)到安全高度間涂層出現局部鼓泡,后續則出現大面積鼓泡脫層現象。外浮盤密封形式造成油氣濃度(含硫化氫)在密封膠帶附近的罐壁處最高,同內浮頂罐一樣,采用非浸液式密封的石腦油罐也出現同樣的腐蝕情況。故浮盤起浮高以下的罐壁板未發現明顯腐蝕。
4.2蠟油、重油及污油罐
芳烴(溶劑)、酸、堿、烴類、硫、鹽、水等,罐體結構多為固定拱頂,大型重油罐也常采用外浮頂。
4.3含硫污水罐
芳烴(溶劑)、酚、酸、堿、烴類、硫、鹽、水、等,固定拱頂罐中間產品儲罐的內壁均應采用耐溫、耐油性導靜電防腐蝕涂層;底漆宜采用無機富鋅類防腐蝕涂料,面漆可采用環氧類和聚氨酯類導靜電防腐蝕涂料;涂層干膜厚度不得低于250μm,其中,罐底涂層干膜厚度不宜低于350μm。
5 結語
以上是針對含硫油品對管道、儲罐腐蝕與防護的具體介紹,總體而言,我國儲油罐腐蝕防護控制水平的提高,還需要相關各方及各界人士共同的努力。
參考文獻
1.王紹青.高含硫石腦油對常壓儲罐的影響及對策[J].石油和化工設備,2005(1):46-47
2.卜文平,王劍梅.高含硫原油儲運問題研究[J].油氣儲運,2003(7):48-49
3.GB50393-2008,鋼質石油儲罐防腐蝕工程技術規范[S]
責任編輯:田雙
《中國腐蝕與防護網電子期刊》征訂啟事
投稿聯系:編輯部
電話:010-62313558-801
郵箱:ecorr_org@163.com
中國腐蝕與防護網官方 QQ群:140808414
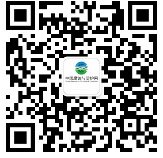
官方微信
《中國腐蝕與防護網電子期刊》征訂啟事
- 投稿聯系:編輯部
- 電話:010-62313558-806
- 郵箱:fsfhzy666@163.com
- 中國腐蝕與防護網官方QQ群:140808414