1.前言
現(xiàn)階段,在汽車工業(yè)領(lǐng)域中,緊固件(螺栓和螺母等)材料表面普遍使用電鍍鋅處理技術(shù),然而電鍍鋅存在著耐蝕性不理想、三廢排放污染等問題。而且,緊固件多與異金屬(熱軋鋼和鋁合金等)部連接使用,在腐蝕過程中,鍍鋅層電位較負,作為陽極性涂層,與其他部件構(gòu)成腐蝕電偶,導(dǎo)致鍍層腐蝕過程加速,破壞嚴(yán)重,未能對基體提供足夠的防護。因此,對于緊固件處理工藝,亟待尋求新興的表面處理技術(shù)替代傳統(tǒng)鍍鋅層的使用。
目前,新興的表面處理技術(shù)主要有無鉻鋅鋁涂層(以下稱鋅鋁涂層)和電鍍鋅鎳合金涂層(以下稱鋅鎳鍍層)等。鋅鋁涂層是由達克羅發(fā)展而來的一種新型涂層,是由金屬粉(鋅粉、鋁粉)、純化劑、粘結(jié)劑、去離子水及一些有機物組成的高分散混合溶液固化后形成的,具有耐蝕性、耐熱性、耐有機溶劑、無污染、無氫脆、對不規(guī)則或有孔隙零件涂覆均勻,適用于多種材料等優(yōu)點,是一種非常有發(fā)展?jié)摿Φ男滦头雷o涂層。鋅鎳鍍層同樣作為一種新型高耐蝕性合金鍍層也得到越來越廣泛的應(yīng)用。鋅鎳合金(其中含Ni為10%~20%,質(zhì)量分?jǐn)?shù))的防蝕性能比純Zn要優(yōu)越得多,據(jù)國內(nèi)外資料報道,相同厚度的鋅鎳和純Zn鍍層,前者抗蝕性比后者要高幾倍乃至十多倍,同時該合金具有優(yōu)良的抗鹽霧腐蝕性及低氫脆性,可代替劇毒Cr鍍層,有利于環(huán)境保護。鋅鎳鍍層與基體結(jié)合力強,可焊性、成型性及拉伸性良好,熔點及硬度也比純Zn高。總的來說,對于汽車緊固件,鋅鋁涂層與鋅鎳鍍層是兩種非常有潛力替代純Zn鍍層的表面處理技術(shù),有望大范圍推廣應(yīng)用。
雖然,國內(nèi)外學(xué)者針對兩種涂層的制備技術(shù)以及耐腐蝕性能進行了大量研宄,但是鮮有以汽車緊固件與異金屬連接的腐蝕問題為背景,研宄經(jīng)鋅鋁涂層和鋅鎳涂層處理后的鋼板與熱軋鋼材料偶接后的電偶腐蝕行為研宄。因此,本文基于中國一汽公司已有工藝,在ST12鋼板上分別制備了鋅鋁涂層和鋅鎳鍍層,利用電化學(xué)手段研宄了經(jīng)兩種涂層處理后的鋼材與熱軋鋼材的電偶腐蝕行為。
2.實驗方法
2.1試樣制備
為滿足實際應(yīng)用過程的顏色需求,分別制備了銀白色和黑色的兩種涂層。實驗用基體材料為ST12冷軋鋼,其化學(xué)成分(質(zhì)量分?jǐn)?shù),%)為:C≤0.10,Mn≤0.50,P≤0.035,S≤0.035,Fe余量。對電偶材料為S≤400熱軋鋼,其化學(xué)成分(質(zhì)量分?jǐn)?shù),%)為:P≤0.05,S≤0.05,Fe余量。
鋅鋁涂層處理所用處理液的主要成分為:片狀Zn粉(片徑10~30urn)占25%(質(zhì)量分?jǐn)?shù),以下相同),片狀A(yù)1粉(片徑5~10nm)占8%,硅烷偶聯(lián)劑KH-560占10%,丙烯酸樹脂占15%,增稠劑纖維素占10%,分散劑OP-10占6%,色漿占4%,其余為水。按照上述配比配制鋅鋁涂層處理液,用磁力攪拌器連續(xù)攪拌使鋅鋁粉充分分散。
試樣尺寸為35mm×150mm×1mm,經(jīng)打磨、除銹、去脂、干燥后,噴覆涂層。鋅鋁涂層采用F75型噴槍在試樣上勻速噴涂處理液(工作壓力0.8MPa,噴涂距離20cm,噴槍移動速率30cm/s)后,將試樣放入101-1S型烘箱內(nèi)于80℃下烘干10min,再將其放入燒結(jié)爐中于300℃下燒結(jié)20min,空冷后得到鋅鋁涂層。鋅鋁涂層的本色為銀白色,在汽車工業(yè)中銀白色和黑色是最為常用的兩種顏色,本實驗通過添加黑色漿得到黑色鋅鋁涂層。
鋅鎳鍍層鍍液的主要成分為:NiS04?6H2012~18g/L,NaOH100-140g/L,ZnO8-12g/L,絡(luò)合劑A30-60g/L,添加劑B1-2mL/L,光亮劑C4-6mL/L。鋅鎳鍍層采用掛鍍的方法制備,陰極移動進行攪拌,使用直流電源保持恒定的電流,陰極電流密度為3~4A/dm2,施鍍溫度30~40℃,電鍍時間為30min,得到銀白色的鋅鎳鍍層。涂層制備完畢后分別進行本色鈍化、黑色鈍化,得到銀白色與黑色的鋅鎳鍍層。清洗、干燥后放置于干燥器中預(yù)留測試使用。
2.2實驗過程
采用PhilipsFEGXL30掃描電子顯微鏡(SEM)觀察鋅鋁涂層以及鋅鎳鍍層表面微觀形貌,并且使用自帶能譜儀(EDX)部件分析涂層的元素成分。
采用AMETEKP4000型電化學(xué)工作站進行電化學(xué)測試:腐蝕介質(zhì)為3.5%NaClC質(zhì)量分?jǐn)?shù))水溶液,測試溫度25℃。極化曲線采用標(biāo)準(zhǔn)三電極系統(tǒng),參比電極為飽和甘汞電極,輔助電極為Pt電極。實驗在3.5%NaCl溶液中進行,溫度控制在25℃,掃描頻率為0.166mV/s。極化曲線采用CView軟件進行擬合。電偶實驗按照HB5374-1987標(biāo)準(zhǔn)進行,涂層試樣和SS400試樣棱角等非測試區(qū)域均采用石蠟封閉,實驗部位表面積約為56cm2,試樣間距5mm,測試時間為20h,參比電極為飽和甘汞電極。
3.結(jié)果與討論
3.1微觀形貌及元素成分
圖1為鋅鋁涂層和鋅鎳鍍層試樣的表面形貌以及元素成分。由圖la可見,鋅鋁涂層中鱗片狀鋅、鋁粉堆疊粘接在一起,鋅粉、鋁粉分布較均勻,無明顯的團聚現(xiàn)象。涂層表面沒有明顯的裂紋,均勻致密,能夠有效地阻止Cl-等腐蝕介質(zhì)滲入基體,具有較好的遮蔽作用。圖lc中,鋅鋁涂層的主要組成成分為Zn和A1,兩種金屬粉末在腐蝕過程中將作為犧牲陽極,對基體具有陰極保護的作用。圖lb中鋅鎳合金鍍層晶粒均勻、細密,沒有明顯的裂紋,可以起到較好的阻擋作用。圖1d顯示鍍層中含有Zn和Ni,其中Zn在腐蝕過程中同樣對基體具有陰極保護的作用。
3.2極化曲線分析
由圖2a可以看出,銀白色和黑色鋅鋁涂層的自腐蝕電位五。分別為-1.04和-0.94V,SS400熱乳鋼的自腐蝕電位為-0.66V,加入色漿使得黑色鋅鋁涂層的自腐蝕電位提高。圖2b中,銀白和黑色鈍化鋅鏡合金鍍層的自腐蝕電位分別-0.82和-0.80V。經(jīng)兩種涂層處理后ST12的腐蝕電位均低于熱軋鋼的,兩種涂層都作為陽極性涂層,偶接后,將首先發(fā)生ST12表面涂層的腐蝕,并且電偶對加速涂層的腐蝕過程。由于接觸電位差越大,電偶腐蝕的推動力越大,金屬腐蝕越嚴(yán)重,因此,在腐蝕過程中,電偶對對鋅鋁涂層的腐蝕反應(yīng)推動力要大于對鋅鎳鍍層的推動力。動電位極化曲線的擬合結(jié)果如表1所示,可以看出鋅鎳鍍層的自腐蝕電流要小于鋅鋁涂層的,表明鋅鎳涂層自身耐腐蝕性要優(yōu)于鋅鋁涂層。
3.3不同涂層對電偶腐蝕電位的影響
圖3為4個電偶對在20h標(biāo)準(zhǔn)電偶腐蝕處理過程中電偶電位隨時間的變化曲線。可以看出,銀白色鋅鋁涂層ST12/SS400電偶對的電位最負,穩(wěn)定在-0.98V附近;其次是黑色鋅鋁涂層ST12/SS400電偶對的電位,穩(wěn)定在約-0.82V。銀白色和黑色鋅鋁涂層ST12偶接后與偶接前的電位差分別為0.06和0.12V。銀白色鋅鎳鍍層ST12/SS400電偶對的電位約為-0.73V;黑色鋅鎳鍍層ST12/SS400電偶對的電位約為-0.72V。銀白色和黑色鋅鎳鍍層偶接后與偶接前的電位差分別為0.09和0.08V雖然,銀白色鋅鋁涂層偶接前后電位差較小,由于與SS400偶接相當(dāng)于把ST12試樣陽極化到電偶電位,結(jié)合極化曲線(圖2)可以看出,銀白色鋅鋁涂層在陽極化0.06V后腐蝕電流卻大于黑色鋅鋁涂層的,銀白色和黑色鋅鎳鍍層陽極化0.09和0.08V后腐蝕電流大小相似,均小于鋅鋁涂層的。因此,可以推斷在電偶腐蝕過程中,鋅鋁涂層的腐蝕速率要大于鋅鎳鍍層的。
3.4不同涂層對電偶腐蝕電流的影響
為了進一步分析4個電偶對對于不同涂層處理后ST12鋼板的電偶腐蝕加速作用,測量了20h標(biāo)準(zhǔn)電偶腐蝕處理過程中電偶電流隨時間的變化曲線C如圖4所示)。將圖中20h的腐蝕電流取平均,并精確測量實驗面積,計算得到各電偶對的平均腐蝕電流密度。經(jīng)銀白色鋅鋁涂層處理的ST12/SS400電偶對的電偶腐蝕電流最大(10.66nA/cm:),黑色鋅鋁涂層次之(9.50nA/cm2),銀白色鋅鎳鍍層再次之(8.15(iA/cm2),黑色鋅鎳鍍層最小(6.56jxA/cm2)。表明在電偶腐蝕過程中,電偶對對鋅鋁涂層的腐蝕加速作用要大于對鋅鎳鍍層的加速作用。
3.5涂覆不同涂層的ST12/SS400熱軋鋼的電偶腐蝕行為分析
從腐蝕學(xué)原理來說,兩金屬偶合后的電偶電流密度與開路電位、偶合電位、極化率有關(guān),接觸電位差越大,陽極金屬極化率越低,電偶腐蝕的推動力越大。同時,陽極金屬的自腐蝕性越差,陽極金屬的腐蝕越嚴(yán)重。實驗發(fā)現(xiàn),不論是與哪種涂層處理過的ST12試樣偶接,SS400熱軋鋼試樣在實驗周期內(nèi)都沒有發(fā)生明顯的腐蝕現(xiàn)象,試樣表面基本沒有變化。SS400熱軋鋼電極電位較正,都處于腐蝕電偶的陰極,受到保護,而涂層處理的ST12試樣則處于陽極,腐蝕過程加速,ST12表面的涂層都是陽極性涂層,涂層首先發(fā)生腐蝕。銀白色鋅鋁涂層偶接前后電位差最小,但其自腐蝕電流最大,且陽極極化率較小,整體表現(xiàn)出電偶腐蝕速率最大。黑色鋅招涂層雖偶接前后電位差大,但自腐蝕電流小,且極化率最大,電偶腐蝕速率小于銀白色鋅鋁涂層。鋅鎳鍍層的自腐蝕電流和偶接前后電位差小于黑色鋅鋁涂層,雖極化率小于黑色鋅鋁涂層,但整體電偶腐蝕速率要小于黑色鋅鋁涂層。
鋅鋁涂層中,Zn粉和A1粉都是作為腐蝕電偶的陽極,腐蝕被加速,而且,Zn粉和A1粉依靠樹脂粘接在一起,不可避免具有較多縫隙,使腐蝕介質(zhì)可以滲透到涂層內(nèi)部,導(dǎo)致Zn粉和A1粉腐蝕。雖然鋅鋁涂層在陽極極化率較大,但涂層自腐蝕電位較負,且自身腐蝕速率大,在與熱軋鋼偶接后,整體腐蝕速率較大。鋅鎳鍍層中,Ni的存在使合金鍍層的自腐蝕電位高于純Zn鍍層,與鋼鐵之間的電位差小。雖然仍是腐蝕電偶的陽極,相比于鋅鋁涂層,鋅鎳鍍層自腐蝕電位較正,且自身腐蝕速率小,在與熱軋鋼偶接后,整體腐蝕速率較小,因此,在汽車工業(yè)中,鋅鎳鍍層有潛力替代純Zn鍍層,成為汽車工業(yè)中緊固件表面處理的優(yōu)選工藝。
4.結(jié)論
(1)經(jīng)鋅鋁涂層處理后ST12的腐蝕電位均低于鋅鎳合金鍍層,在腐蝕過程中,電偶對對鋅鋁涂層的腐蝕反應(yīng)推動力要大于對鋅鎳鍍層的推動力。
(2)經(jīng)銀白色和黑色鋅鋁涂層處理的ST12/SS400電偶對的電偶腐蝕電流分別為10.66和9.50nA/cm2,經(jīng)銀白色和黑色鋅鎳鍍層處理的ST12/SS400電偶對的電偶腐蝕電流分別為8.15和6.56nA/cm2,可見電偶對對鋅鋁涂層的腐蝕加速作用要大于對鋅鎳鍍層的。
(3)鋅鋁涂層和鋅鎳鍍層均為陽極性涂層,雖然鋅鋁涂層在陽極極化率較大,但涂層自腐蝕電位較負,且自身腐蝕速率大,在與熱軋鋼偶接后,整體腐蝕速率較大。相比于鋅鋁涂層,Ni的存在使鋅鎳鍍層自腐蝕電位較正,且自身腐蝕速率小,在與熱軋鋼偶接后,整體腐蝕速率較小。
免責(zé)聲明:本網(wǎng)站所轉(zhuǎn)載的文字、圖片與視頻資料版權(quán)歸原創(chuàng)作者所有,如果涉及侵權(quán),請第一時間聯(lián)系本網(wǎng)刪除。
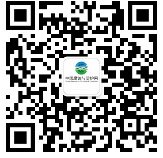
官方微信
《腐蝕與防護網(wǎng)電子期刊》征訂啟事
- 投稿聯(lián)系:編輯部
- 電話:010-62316606-806
- 郵箱:fsfhzy666@163.com
- 腐蝕與防護網(wǎng)官方QQ群:140808414