精密超精密加工技術的發展歷史
近年來,美國開始實施了“微米和納米級技術”國家關鍵技術計劃,國防部成立了特別委員會,統一協調研究工作。美國目前至少有30多家公司研制和生產各類超精密加工機床,如國家勞倫斯利佛摩爾實驗室(LLNL)、摩爾(Moore)公司等在國際超精密加工技術領域久負盛名。同時利用這些超精密加工設備進行了陶瓷、硬質合金、玻璃和塑料等材料不同形狀和種類零件的超精密加工,應用于航空、航天、半導體、能源、醫療器械等行業。日本現有20多家超精密加工機床研制公司,重點開發民用產品所需的超精密加工設備,并成批生產了多品種商品化的超精密加工機床,日本在相機、電視、復印機、投影儀等民用光學行業的快速發展與超精密加工技術有著直接的關系。英國從60年代起開始研究超精密加工技術,現已成立了國家納米技術戰略委員會,正在執行國家納米技術研究計劃,德國和瑞士也以生產精密加工設備聞名于世。1992年后,歐洲實施了一系列的聯合研究與發展計劃,加強和推動了精密超精密加工技術的發展。
國內真正系統地提出超精密加工技術的概念是從20世紀80年代~90年代初,由于航空、航天等軍工行業的發展對零部件的加工精度和表面質量都提出了更高的要求,這些軍工行業投入了資金支持行業內的研究所和高校開始進行超精密加工技術基礎研究。由于當時超精密加工技術屬于軍用技術,無論從設備還是工藝等方面,國外都實施了技術封鎖,所以國內超精密加工技術的開展基本都是從超精密加工設備的研究開始。由于組成超精密加工設備的基礎是超精密元部件,包括空氣靜壓主軸及導軌、液體靜壓主軸及導軌等,所以各家單位也正是以超精密基礎元部件及超精密切削加工用的天然金剛石刀具等為突破口,并很快就取得了一些進展。哈爾濱工業大學、北京航空精密機械研究所等單位陸續研制了超精密主軸及導軌等元部件,并進行了天然金剛石超精密切削刀具刃磨機理及工藝研究,同時陸續搭建了一些結構功能簡單的超精密車床、超精密鏜床等超精密加工設備,開始進行超精密切削工藝實驗。
非球面曲面超精密加工設備的研制成功是國內超精密加工技術發展的里程碑,非球面光學零件由于具有獨特的光學特性在航空、航天、兵器以及民用光學等行業開始得到應用,從而簡化了產品結構并提高了產品的性能。當時加工設備只有美國、日本及西歐等少數國家能夠生產,國內引進受到嚴格限制而且價格昂貴,國家從“九五”開始投入了人力物力支持研發超精密加工設備。到“九五”末期,北京航空精密機械研究所、哈爾濱工業大學、北京興華機械廠、國防科技大學等單位陸續研制成功代表當時超精密加工最高技術水平的非球面超精密切削加工設備,徹底打破了國外的技術封鎖。之后其他各類超精密加工設備,如超精密磨削設備、小計算機數控磨頭拋光設備、磁流變拋光設備、離子束拋光設備、大口徑非球面超精密加工設備(如圖1所示)、自由曲面多軸超精密加工設備、壓印模輥超精密加工設備等也陸續研制成功,縮小了超精密加工技術國內外的差距。同時由于有了超精密加工設備的支撐,在超精密加工工藝方面也有了很大進展,如ELID超精密鏡面磨削工藝、磁流變拋光工藝、大徑光學透鏡及反射鏡超精密研拋及測量工藝、自由曲面的超精密加工及測量工藝、光學薄膜模輥超精密加工工藝,超精密加工技術的應用領域也從軍工行業轉向了民用行業。
超精密加工技術的發展隨著時代的進步其加工精度也不斷提高,目前已經進入到納米制造階段。納米級制造技術是目前超精密加工技術的巔峰,其研究需要具有雄厚的技術基礎和物質基礎條件,美國、日本及歐洲一些國家以及我國都在進行一些研究項目,包括聚焦電子束曝光、原子力顯微鏡納米加工技術等,這些加工工藝可以實現分子或原子級的移動,從而可以在硅、砷化鎵等電子材料以及石英、陶瓷、金屬、非金屬材料上加工出納米級的線條和圖形,最終形成所需的納米級結構,為微電子和微機電系統的發展提供技術支持。
精密超精密加工技術的作用
20世紀80年代以前,太赫茲(THz)波段(介于微波與紅外之間)的研究結果和數據非常少,主要是受到有效太赫茲產生源和靈敏探測器的限制。隨著80年代一系列新技術、新材料、新工藝的發展,使得太赫茲技術得以迅速發展。近年來由于太赫茲的獨特性能將給寬帶通信、雷達、電子對抗、電磁武器、天文學、醫學成像、無損檢測、安全檢查等領域帶來了深遠的影響,太赫茲基礎及應用基礎技術已經逐漸成為研究熱點。
太赫茲技術在航空領域的重要應用是太赫茲雷達可用于隱身飛行器探測,其中束控元件是太赫茲探測系統的重要功能部件,其透鏡主要采用硅基遠紅外透射材料,反射元件面形有拋物面、橢球面、離軸非球面以及賦形曲面等,采用鋁等金屬基材料。我國正研的主反射元件尺寸已有φ300mm、φ800mm、φ1000mm等,面形精度要求已要求達微米級,表面質量為鏡面,并且要求零件精度質量具有良好的穩定性。我國中期發展的太赫茲系統擬采用φ4~5m的主鏡,遠期主鏡直徑將達30m或更大,太赫茲系統束控主反射元件面形也將采用主動控制的拼接式平面、離軸非球面等形狀。基于上述要求,需要大型單點金剛石超精密車削設備、復雜曲面超精密加工工藝技術、大型復雜曲面的高精度三坐標測量技術等支撐。
2 精密超精密加工技術是現代高新技術產業發展的基礎
國家目前非常重視交通、能源、信息、生物醫藥等高新技術產業的發展,但是目前這些產業的核心技術國內還沒有掌握,關鍵設備或零部件仍然依賴進口。如高性能軸承是飛機發動機、高鐵、風電等產品的關鍵,但由于目前國內材料、工藝等方面的原因,其使用壽命遠遠不能滿足要求,其他一些承受高頻載荷的部件同樣面臨這些問題。近年國內開始研究的抗疲勞制造技術則是以被加工件的抗疲勞強度及疲勞壽命為判據,其中的核心技術之一是精密超精密加工工藝,可提高表面質量、改善表面應力狀態,從而提高零件的疲勞壽命,這不僅要求具有超精密加工設備及工藝,而且還需研制材料及零部件的疲勞壽命精密測試設備(如圖2所示)。
新能源產業(如太陽能)國內雖然發展很快,但核心技術還是掌握在國外,如硅片切割、研磨、拋光、刻劃設備,高倍聚光菲涅爾透鏡模具超精密加工設備等與國外還存在較大差距。信息產業的發展推動了芯片、存儲等發展,隨著存儲密度越來越大,對磁盤的表面粗糙度以及相應的讀寫設備的懸浮高度及磁頭的上下跳動量的要求大大提高,目前國外已經可以把磁頭、磁盤的相對間隙最高控制在1nm左右。在醫療器械行業,超精密加工技術也起著很大的作用,人造關節采用鈦合金或其他貴金屬材料,這些高精度零件的表面處理對清潔度、光整度和表面粗糙度具有極高要求,需要進行超精密研拋,形狀要根據個人的身體結構定制,國外價格昂貴,而國內無論從使用壽命和安全性等方面存在較大差距。其他如微型內窺鏡中的微小透鏡及器件、心臟搭橋及血管擴張器、醫用微注射頭陣列等國內現在還無法生產。
發動機噴嘴零件(如旋流槽、微小孔等特征)的精密加工與檢測技術、發動機葉片型面及進排氣邊的精密加工與檢測技術、整體葉盤的精密加工與檢測技術等發展為航空發動機零部件的加工與檢測提供了可靠保證,促進了航空發動機性能的提升。圖3為發動機零部件專用五軸非接觸掃描精密測量機。
超精密加工技術使導彈關鍵元器件的精度和質量產生了飛躍,進而大大提高了導彈的命中率。例如導彈頭罩形狀由球形向適應空氣動力學的復雜形狀發展,材料由紅外材料向藍寶石乃至金剛石發展,這也對超精密加工設備和超精密加工工藝提出了新的要求。
精密超精密加工技術發展趨勢
1 超精密加工技術基礎理論和實驗還需進一步不斷發展
所謂超精密加工技術基礎理論,是指在了解并掌握超精密加工過程的基本規律和現象的描述后才能駕馭這一過程,取得預期結果。例如上世紀90年代初,日本學者用金剛石車刀在LLNL的DTM3上加工出最薄的連續切屑的照片,當時認為達到了1nm的切削厚度,已成為世界最高水平,并至今無人突破(如圖4)。那么超精密切削極限尺度是多少、材料此時是如何去除的,此外超精密加工工藝系統在力、熱、電、磁、氣等多物理量/場復雜耦合下的作用機理是什么、此時系統的動態特性、動態精度及穩定性如何保證等都需要得到新理論的支持。
隨著計算機技術的發展,分子動力學仿真技術從20世紀90年代開始在物理、化學、材料學、摩擦學等領域得到了很好的應用,美國、日本等國首先應用該技術研究納米級機械加工過程,國內從21世紀初在一些高校開始應用分子動力學仿真技術對納米切削及磨削過程進行研究,可描述原子尺寸、瞬態的切削過程,在一定程度上反映了材料的微觀去除機理,但這一切還有待于實驗驗證。
2 被加工材料和工藝方法也在不斷擴展
鈦合金是航空最常用的材料之一,氫作為有害雜質元素對鈦合金的使用性能有極其不利的影響,如會引起鈦合金氫脆、應力腐蝕及延遲斷裂等,但是近年來研究表明通過合理有效地控制滲氫、相變及除氫等過程,獲得鈦合金組織結構的變化,從而可以改善其加工性能,提高加工表面質量和效率。同樣通常認為黑色金屬是無法利用天然金剛石進行超精密切削加工的,多年來也一直在進行各種工藝研究,如利用低溫流體(液氮或二氧化碳)冷卻切削區進行低溫冷卻車削、采用超聲振動切削黑色金屬、采用金剛石涂層刀具等,采用離子滲氮和氣體滲氮工藝對模具鋼進行處理,但上述方法到目前為止還無法工程化應用。近年來通過離子注入輔助方式改變被加工材料表層的可加工性能,實現硅等硬脆材料復雜形狀的高效超精密切削。
抗疲勞制造技術的發展為超精密加工技術提出了新的發展方向,超硬材料的精密加工工藝要求控制表層及亞表層的損傷及組織結構、應力狀態等參數,如航空發動機軸承材料M50NiL表面處理后硬度超過了HRC70。隨著單晶渦輪葉盤和單晶渦輪葉片在航空發動機上的應用,要求被加工材料沒有重融層和變質層,從而對精密加工工藝提出了新要求。隨著導彈馬赫數的增加,要求頭罩材料的抗耐磨性提高,已從紅外材料向藍寶石材料頭罩乃至金剛石材料發展,形狀也從球形向非球面乃至自由曲面發展,對超精密加工設備、工藝及檢測技術提出了新的要求。
在未來零部件設計與制造將會增加一項功能表面結構的設計與制造,通過在零件表面設計和加工不同形狀的微結構,從而提高零部件力學、光學、電磁學、升學等功能,這將是微納制造的重要應用領域,2006年成立的國際納米制造學會經專家討論并認同,納米制造中的核心技術將從目前以MEMS技術逐步轉向超精密加工技術。
4 超精密加工開始追求高效
超精密加工技術從發展之初是為了保證一些關鍵零部件的最終精度,所以當初并不是以加工效率為目標,更多關注的是精度和表面質量,例如一些光學元件最初的加工周期是以“年”為加工周期。但是隨著零件尺寸的進一步加工增大和數量的增多,目前對超精密加工的效率也提出了要求。例如為了不斷提高觀察天體范圍和清晰度,需不斷加大天文望遠鏡的口徑,這就同樣存在天文版的摩爾定律,即每隔若干年,光學望遠鏡的口徑增大一倍,如建于1917年位于美國威爾遜山天文臺的Hooker望遠鏡的口徑為2.5m,是當年全世界最大的天文望遠鏡;到1948年被Hale望遠鏡取代,其口徑達到了5m;1992年新建成的Keck望遠鏡的口徑達到了10m,目前仍在發揮著巨大的作用。目前正在計劃制造的巨大天文望遠鏡OWL主鏡口徑達到100m,由3048塊六邊形球面反射鏡組成,次鏡由216塊六邊形平面反射鏡組成,總重約1~1.5萬t,按照目前現有的加工工藝,可能需要上百年的時間才能完成。此外,激光核聚變點火裝置(NIF)需要7000多塊400mm見方的KDP晶體,如果沒有高效超精密加工工藝,加工時間也無法想象。為此需要不斷開發新的超精密加工設備和超精密加工工藝來滿足高效超精密加工的需求。
5 超精密加工技術將向極致方向發展
隨著科技的進步,對超精密加工技術已經提出了新的要求,如要求極大零件的極高精度、極小零件及特征的極高精度、極復雜環境下的極高精度、極復雜結構的極高精度等。
歐洲南方天文臺正在研制的超大天文望遠鏡VLT反射鏡為一塊直徑8.2m、厚200mm的零膨脹玻璃,經過減重后重量仍然達到了21t。法國REOSC公司負責加工,采用了銑磨、小磨頭拋光等加工工藝,加工周期為8~9個月,最終滿足了設計要求,目前許多新的超精密加工工藝如應力盤拋光、磁流變拋光、離子束拋光等出現為大鏡加工提供了技術支撐。前面提到的微納結構功能表面結構尺寸小到幾個微米,如微慣性傳感器中的敏感元件撓性臂特征尺寸為9μm,而其尺寸精度卻要求±1μm。
美國國家標準計量局研制的納米三坐標測量機(分子測量機)是實現如何在極復雜環境下的極高精度測量的典型例子,該儀器測量范圍50mm×50mm×100μm,精度達到了1nm,對環境要求及其嚴格,最內層殼溫度控制17±0.01℃,次層殼采用主動隔振,高真空層工作環境保持1.0×10-5Pa,最外層殼用于噪聲隔離,最后將整體結構安裝在空氣彈簧上進行被動隔振。自由曲面光學曲面精度要求高、形狀復雜,有的甚至無法用方程表示(如賦值曲面),但由于其具有卓越的光學性能近年來應用范圍不斷擴大,但自由曲面光學零件的設計、制造及檢測等技術還有待于進一步發展。
6 超精密加工技術將向超精密制造技術發展
超精密加工技術以前往往是用在零件的最終工序或者某幾個工序中,但目前一些領域中某些零部件整個制造過程或整個產品的研制過程都要用到超精密技術,包括超精密加工加工、超精密裝配調試以及超精密檢測等,最典型的例子就是美國的美國國家點火裝置(NIF)。
為了解決人類的能源危機,各國都在研究新的能源技術,其中利用氘、氚的聚變反應產生巨大能源可供利用,而且不產生任何放射性污染,這就是美國國家點火工程。我國也開始了這方面的研究,被稱為神光工程。NIF整個系統約有2個足球場大小,共有192束強激光進入直徑10m的靶室,最終將能量集中在直徑為2mm的靶丸上。這就要求激光反射鏡的數量極多(7000多片),精度和表面粗糙度極高(否則強激光會燒毀鏡片),傳輸路徑調試安裝精度要求極高,工作環境控制要求極高。對于直徑為2mm的靶丸,壁厚僅為160μm,其中充氣小孔的直徑為5μm,帶有一直徑為12μm、深4μm的沉孔。微孔的加工困難在于其深徑比大、變截面,可采用放電加工、飛秒激光加工、聚焦離子束等工藝,或采用原子力顯微鏡進行超精密加工。系統各路激光的空間幾何位置對稱性誤差要求小于1%、激光到達表面時間一致性誤差小于30fs、激光能量強度一致性誤差小于1%等。如此復雜高精度的系統無論從組成的零部件加工及裝配調試過程時刻都體現了超精密制造技術。
更多關于材料、材料腐蝕控制、材料科普等方面的國內外最新動態,我們網站會不斷更新。希望大家一直關注中國腐蝕與防護網http://www.ecorr.org
責任編輯:楊揚
投稿聯系:編輯部
電話:010-62313558-806
中國腐蝕與防護網官方 QQ群:140808414
免責聲明:本網站所轉載的文字、圖片與視頻資料版權歸原創作者所有,如果涉及侵權,請第一時間聯系本網刪除。
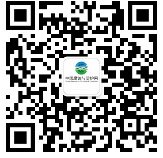
官方微信
《中國腐蝕與防護網電子期刊》征訂啟事
- 投稿聯系:編輯部
- 電話:010-62316606-806
- 郵箱:fsfhzy666@163.com
- 中國腐蝕與防護網官方QQ群:140808414