1、前言
保溫層下腐蝕 (corrosion under insulation,CUI) 是指外部被保溫層覆蓋的管道或設備,由于水分和腐蝕性物質的進入而發(fā)生的腐蝕現(xiàn)象。在管道或容器的外表面包裹保溫層材料,一方面可以減少熱量損失、維持操作系統(tǒng)的溫度、節(jié)約能源,另一方面也可以阻止外界有害介質接觸到管道或設備金屬表面,提高其運行能力。
管道或設備的保溫層下腐蝕,往往是在保溫材料及外防護層 (通常為鋁箔或不銹鋼) 安裝后的使用過程中,由于安裝、操作、性能或外界因素造成外防護層的破損,在保溫材料和基體金屬間局部區(qū)域形成腐蝕環(huán)境,導致CUI的發(fā)生。對于沒有施加涂層或處于腐蝕性工業(yè)氣氛情況下的管道或設備表面,保溫層下腐蝕會更加嚴重。研究表明,施加了保溫結構的設備或管道,運行5年后發(fā)生保溫層下腐蝕的概率將大幅上升,使用10年后的保溫層60%都含有腐蝕性冷凝水,極大地提高了CUI發(fā)生的概率。
由于外層不銹鋼或鋁箔以及保溫材料的存在,使得CUI具有較強的隱蔽性且難以檢測,往往很難在第一時間察覺,容易引起突發(fā)的嚴重泄漏事故。統(tǒng)計顯示,在石油化工行業(yè)中,超過60%的管道故障是由CUI引發(fā)的。每年全球由于CUI引發(fā)設備和管道發(fā)生故障導致的危險產品泄漏、設備非正常停車甚至人員傷亡等一系列嚴重問題所造成的損失高達數(shù)十億美元。
2、CUI的發(fā)生機理
對于CUI的發(fā)生機理,Kane等和Norsworthy等認為水分是發(fā)生CUI的最根本原因。Frank等則認為保溫層與管道基體表面的溫差是CUI速率的決定因素,在熱循環(huán)下,隨著水分重復地聚集和蒸發(fā),使得保溫材料和基體金屬間的電解液濃度越來越大,腐蝕速率不斷提高。多數(shù)研究者認為,CUI發(fā)生的原因是由于水、水中的雜質以及溫度的共同作用。
系統(tǒng)泄漏或保溫層的破損等會導致水分滲入保溫層使其變潮濕,保溫層內外的溫差會使水汽冷凝在金屬基體表面,形成局部液體聚集。同時,雨水或保溫層中有害介質的溶解聚集會形成電解質溶液,特別是局部酸性環(huán)境的形成,會加速潮濕環(huán)境中設備管道的腐蝕和過早失效。而且此時保溫層導熱系數(shù)會增大,使保溫節(jié)能效果降低,也會加速CUI進程。CUI常見的腐蝕物以氯化物和硫酸鹽為主。大量工程案例和研究表明,碳鋼和低合金鋼在保溫層下的腐蝕常表現(xiàn)為均勻腐蝕和點蝕,而奧氏體不銹鋼則多發(fā)生外應力腐蝕開裂和點蝕。最容易發(fā)生CUI的溫度范圍是-4~175 ℃,在達到水的沸點之前,溫度每提高15~20 ℃,腐蝕速率就會加倍。而周期性的溫度變化,會使設備或管道長期處于干濕及冷熱交替的條件下,導致腐蝕介質的濃縮和聚積,增強該區(qū)域的腐蝕性,加快腐蝕速率,導致CUI頻繁發(fā)生。在堿性環(huán)境下,碳鋼和低合金鋼的腐蝕速率最低,但氯化物會引起點蝕的發(fā)生;而在酸性環(huán)境下,S和N的氧化物很容易引發(fā)外應力腐蝕開裂,導致安全事故的發(fā)生。
3、CUI的防護
CUI的高危害性引起了研究者的廣泛關注,1985年頒布了ASTM STP880;1998年NACE出版了NACE RP0198-1998 (2004年修訂);2007年ASTM頒布了G189-07;2008年歐洲腐蝕聯(lián)盟(EFC) 對CUI進行了全面介紹,同時也對近期的研究進展進行了總結說明,具有非常高的實用價值。
3.1 保溫材料外防護層
外防護層是包裹在保溫層外,防護CUI的第一道屏障,目的是保護保溫層系統(tǒng)免于受到機械或氣候傷害,阻止或減少外部水分或腐蝕介質的進入和駐留。對于外防護層的選擇需要考慮經濟成本、實用性、設備或管道的復雜程度以及基體的工況溫度等因素。外防護層常分為金屬和非金屬,常用的金屬材料有鍍鋁鋼、鍍鋁鋅鋼、鋁和不銹鋼,金屬防護層對外界的機械損傷抵抗力弱,因此常通過增加厚度來提高抵抗力,此時的抗腐蝕性能相對較高。常用的非金屬防護層有紫外線固化型的玻璃纖維增強塑料、熱塑性塑料和聚合物等,非金屬防護層具有更好的密封性能和更低的成本,但非金屬防護層由于較低的熔點且抗機械損傷能力弱等因素使其應用受到一定的限制。
外防護層由于很容易受到氣候、化學腐蝕以及機械的傷害,因此,需要經常性地進行維護。實踐證明,將鋁箔用作CUI的外防護層,不僅可以作為屏障阻止腐蝕介質接觸金屬表面,而且還能對金屬起陰極保護作用,其導熱性優(yōu)于一般不銹鋼材料,可以有效防止保溫層結構下奧氏體不銹鋼外應力腐蝕開裂。
3.2 正確選擇保溫材料
保溫材料是對容器和管道進行隔熱保溫的重要組成部分,是包裹在管道或設備外面的第二道屏障。合理地設計和安裝高質量的保溫材料以及正確的維護可以有效地提高對CUI的防護效率。
保溫材料分為疏水性和親水性,疏水性保溫材料按原理又分為自身疏水 (泡沫玻璃) 和加入化學添加劑疏水 (如WRG巖棉、Pyrogel XT等);而常用的親水性材料有巖棉、硅酸鈣等。CUI是金屬長期暴露于潮濕環(huán)境中的產物,因此,貯存水分最少并且干燥速率最快的保溫材料可以有效地減少CUI帶來的傷害。研究表明,在CUI的溫度范圍內 (-4~175℃),吸水性材料會加速CUI速率,而疏水性材料則可以抑制CUI速率,但疏水性材料的實際工程應用并不廣泛,一方面是由于其價格比親水性材料高很多,另一方面是缺少不同保溫材料間系統(tǒng)的對比數(shù)據(jù) (盡管已有工廠使用疏水性材料,并有效地減緩了CUI,但是鑒于各個工廠的保溫材料的數(shù)據(jù)多是與工廠的實際工況及設備緊密聯(lián)系在一起的,故不能隔離開來作為單獨的實驗數(shù)據(jù)),這使得高效的疏水性保溫材料沒有得到廣泛的推廣。
實踐表明,幾乎沒有保溫材料可以避免CUI。一方面保溫材料與金屬表面間的環(huán)形空隙以及設備和管道外表面本身的缺陷都可以收集水分和腐蝕性介質,從而使得其聚集和濃縮,增強腐蝕性,;另一方面保溫材料本身具有水溶性、滲透性和可濕性,材料內部和外界的腐蝕污染物 (氯化物、硅酸鹽等) 都會隨著水分的進入而溶解,加大腐蝕液濃度,加速腐蝕速率。因此,常要求保溫材料可浸出Cl-含量要小于10 mg/kg,有些保溫材料會在加工制造時期加入腐蝕抑制劑來預防CUI。但后來的工程實例表明,隨著腐蝕抑制劑循環(huán)性地溶入水中后再干燥,抑制劑會被水分帶走,因此,加入腐蝕抑制劑的保溫層跟不加腐蝕抑制劑的保溫層效果基本相同;加入疏水劑的保溫材料可以提高對CUI的防護,但是不同疏水材料對水分的貯存能力不同,其干燥速率也不相同,貯水能力更強的材料,干燥時間也更久,其發(fā)生CUI的風險也更大。
Mitechell等通過實驗證明了在150 ℃的熱油管表面,使用兩相的環(huán)氧樹脂復合泡沫30個月沒有出現(xiàn)任何明顯的粘連或腐蝕現(xiàn)象,并以此為根據(jù)提出在120 ℃以下的工況,可以利用兩相和三相環(huán)氧樹脂復合泡沫塑料來充當保溫層起到防腐絕緣的效果,但由于這種方法的成本較高,并且與硅酸鹽等常規(guī)保溫層相比,保溫效率較低而沒有大面積推廣。
CINI的研究者發(fā)明了一種新型的含有篩網(wǎng)的“不接觸保溫材料”,這種保溫材料因為空氣間隙的存在使基體材料保持相對干燥,并可直接方便地把檢測設備塞入保溫層下對基體表面進行損傷檢測。
Williams等通過將保溫材料包裹在沒有涂層的水平碳鋼管外來模擬最惡劣的環(huán)境下暴露條件發(fā)現(xiàn),Cryogel Z材料是所有測試樣品中對碳鋼基體保護效果最好的,這是由于其內在的聚酯薄膜屏障可以有效地防止水分滲入;玻璃棉則致使碳鋼管發(fā)生最嚴重的CUI,這是由于材料本身的疏水性限制了水分氣相和液相的自然遷移,使進入的水分被困在了由管壁、疏水保溫層形成的楔形空間內,因此,在高溫區(qū)域使用玻璃棉需要充分做好密封工作;礦棉包覆下的碳鋼管,在頂部發(fā)生了少量腐蝕,且其表面風化嚴重,觸感潮濕,這主要與材料纖維自身的吸水性能有關;硅酸鈣保溫材料所導致的腐蝕主要集中在管道底部,吸水量為自身的157%,這與其多孔性所導致的水分自動向底部聚集有關。
3.3 保溫材料下金屬外表面防護涂層
金屬表面外防護涂層從物理上隔斷了潮濕腐蝕環(huán)境和污染物與金屬表面的直接接觸,能夠在一定程度上預防基體金屬發(fā)生腐蝕。CUI發(fā)生的環(huán)境條件決定了所采用的防護涂層要具有防腐蝕性、抗氧化性、耐熱性以及熱循環(huán)抗性;高溫條件下不降解、能承受熱膨脹和收縮引起的應力;能在較低的表面預處理要求下快捷高效地進行噴涂并與基體良好地結合;能夠為基底材料提供足夠的屏障來抵抗存在的腐蝕性污染物以及熱水和水蒸汽的腐蝕。不恰當?shù)倪x擇涂層或不合格的涂層很容易發(fā)生化學降解,使得水的滲透性增加,在這種情況下,即使涂層沒有發(fā)生破損,也會增加水的滲入,發(fā)生CUI。因此,保溫材料下防護涂層或保溫材料外防護層的完整性和破損程度都直接影響CUI的發(fā)生。
傳統(tǒng)有機涂層和熱噴鋁涂層被廣泛用于CUI的防護,但前者有時會出現(xiàn)涂層過早破裂所導致的嚴重CUI發(fā)生。文獻研究證實了熱噴鋁涂層能有效預防碳鋼的CUI,其性能比傳統(tǒng)有機涂層優(yōu)越。Fischer等研究了熱噴鋁涂層對碳鋼設備CUI問題的防護能力,實驗結果表明,熱噴鋁涂層性能較為出色,其防護壽命可達20~30 a。Halliday等開發(fā)了冷噴鋁涂層技術,并設計用于評價涂層性能的測試方法,經過實驗室模擬和現(xiàn)場試用的雙重測試,得出新型冷噴鋁涂層在大幅度溫度變化條件下,仍具有優(yōu)異的耐腐蝕性、耐高溫性和耐熱振性。Russell等利用礦物化涂層實驗論證其對管道和設備能進行有效防護,保溫層下的金屬表面壽命可達到20年。因此,對于金屬表面防護涂層,在實際應用時,應綜合考慮最高運行溫度、持續(xù)運行時間以及涂層推薦應用壽命來進行選擇。
4、涂層的種類與應用
4.1 有機涂層
有機涂層是最早用來防止CUI的涂層,防護機理主要是通過與基體間良好的粘結性能,作為阻擋層來減緩侵蝕性離子向金屬基體的擴散。涂層中的緩蝕性顏料可以在侵蝕性離子到達基體前抑制其腐蝕作用,其防腐性能主要取決于涂層與金屬基體的粘結強度和涂層對水及侵蝕性離子的抗?jié)B透能力。有機涂層在管道系統(tǒng)或者熱加工限制區(qū)域的維護方面的應用仍然非常廣泛,但是其薄膜涂層的天然脆性導致其在管道交接和安裝期間會產生劃痕,并且有機涂層的可滲透性也是它在CUI中應用的弱點。
環(huán)氧涂層是有機涂層中很重要的一種類型,它以環(huán)氧樹脂為主要成膜物,通常能夠提供很好的涂層系統(tǒng),大部分有延展性,固化快速并且能夠很好地黏附在管道表面。多數(shù)環(huán)氧樹脂都耐化學腐蝕、耐磨而且應用廣泛。但是當溫度出現(xiàn)波動時,一些環(huán)氧樹脂會變得非常脆甚至產生裂紋。環(huán)氧樹脂的化學成分限制了其最高服役溫度為230 ℃,高于這個溫度就會使涂層中的C-C鍵斷裂,從而使聚合物碳化導致涂層失效。其最佳操作溫度為149 ℃ (300 F),通過高質量的控制程序應用的環(huán)氧涂層可以在常規(guī)檢查及維護前使用9~13年。
環(huán)氧酚醛涂料是另外一種常用的有機涂層,它易于維修,防腐蝕性能優(yōu)異,可用于150 ℃以下工況的熱作鋼設備;酚醛型環(huán)氧樹脂的服役溫度可到204 ℃,有良好的耐酸性、耐水性和抗?jié)B透性能,但涂層的厚度以及噴涂工藝要求嚴格,在熱循環(huán)和熱沖擊下抵抗力差。
4.2 熱噴鋁涂層
熱噴涂技術 (TSA) 是利用一種氧燃料或噴射電弧,將噴涂材料 ( 如金屬、合金等) 加熱至熔融或半熔融狀態(tài),通過氣流吹動使其霧化高速噴射到零件表面,以形成噴涂層的表面加工技術。
熱噴鋁技術是CUI保護涂層系統(tǒng)中非液體涂層的一種。工程實例表明,熱噴鋁涂層在絕緣層下設備表層可服役20~30年而不需要維修檢測。美國海軍從20世紀70年代開始研究TSA涂層,最初由于成本較高而發(fā)展緩慢,后來隨著新型噴涂設備的應用大大降低了其成本,這才促進了TSA涂層在市場上的發(fā)展和普及,尤其是在石化行業(yè)。TSA涂層要求SSPC-SP5/Sa3等級 (最徹底的處理級:基體表面呈均勻銀白色金屬光澤) 的表面預處理工藝,需要專門的噴涂工具來進行高效噴涂。如果涂層質量不合格,熱噴鋁涂層就會過早地失去附著力,引起氣泡和早期失效。
TSA涂層可以應用到多種材料表面起保護作用,如碳-錳鋼、低合金鋼、奧氏體和雙相不銹鋼等,其防護原理是陽極保護:在保溫層下溫和的酸性環(huán)境中,Al對鋼材基體來說是陽極,熱噴鋁涂層系統(tǒng)就是一個巨大的陽極,可以長期很好地起到犧牲保護的作用。但TSA不能自我修復污點,在建議膜厚上面有限制。TSA涂層的現(xiàn)場噴涂方法有火焰噴涂和雙絲電弧噴涂,火焰噴涂常用在僅有有限入口的現(xiàn)場管道和容器施工,而電弧噴涂則常用于空間范圍較廣的噴涂項目中。與傳統(tǒng)的涂層相比,TSA涂層具有耐化學腐蝕pH 4~9、可以在循環(huán)溫度工況下服役、連續(xù)服役溫度可達480 ℃、抗機械損傷等優(yōu)點。
鈦改性無極共聚物涂層 (TMIC) 對TSA來說是完美的互補產品,它可以單獨使用,也可以和TSA涂層一起使用。對于新設備來說,它可以有效地對TSA的孔隙度進行互補,把TSA的使用壽命延長到25~30年。而對于使用中的TSA涂層,當其接近失效時,TMIC涂層可以和TSA一起使用,作為一個維護涂層,重新填充孔隙度且增加額外的保護屏障,延長TSA涂層的使用壽命。因此,通過把TSA涂層和TMIC涂層結合在一個雙涂層系統(tǒng)中,生成一種優(yōu)質防護CUI的涂層方案。TMIC涂層不僅能夠很好地抵抗高溫,而且它延展性好,可以較好地承受熱循環(huán)。TMIC涂層的應用可以通過傳統(tǒng)噴涂、無氣噴涂、刷涂等方法,基體的表面預處理等級為SSPC-SP6,可以應用于新設施或現(xiàn)場維護等場所。
4.3 冷噴鋁涂層
熱噴涂由于使用高溫熱源的關系,通常使粉末顆粒被加熱到熔化狀態(tài),在噴涂過程中會不可避免地發(fā)生一定程度的氧化,影響涂層性能。而新型的冷噴涂技術 (CS) 是基于空氣動力學原理的一種新型的噴涂技術。鋁涂層是金屬基體腐蝕保護的常用原料,不僅可以犧牲陽極保護基體,而且鋁涂層表面容易鈍化,可以在金屬基體表面形成致密而穩(wěn)定的氧化膜。冷噴涂鋁涂層就是利用冷噴涂技術,通過高壓載氣 (常選用惰性氣體) 加速后,將涂層顆粒(直徑<50 μm的鋁粉末) 在溫度遠低于噴涂材料熔點下 (小于600 ℃),以超音速(300~1200 m/s)、完全固態(tài)的狀態(tài)與基體發(fā)生塑性碰撞,顆粒的速度決定了涂層的沉積效率和接合強度,粉末顆粒通過產生較大的塑性變形而沉積于基體表面并形成金屬鍵,實現(xiàn)涂層的沉積,生成致密的、無氧化物的金屬涂層。它不僅避免了材料的氧化及生成不需要的物相,保留了最初粒子的性質,而且制備的涂層熱影響殘余應力低,涂層的厚度、顯微硬度及孔隙率較TSA都有很大的提高。
Balani等通過用100%的He氣以及80%He與20%N的混合氣體將鋁粉噴射到1100鋁基體表面后,用透射電鏡分析發(fā)現(xiàn)純He比混合氣體能產生更致密更堅固的涂層系統(tǒng),且在pH值為0.9的強酸中腐蝕發(fā)現(xiàn),用純He氣噴射的涂層系統(tǒng)耐腐蝕性能更強。Choi等系統(tǒng)地研究了冷噴涂鋁的特征,包括微觀結構、抗腐蝕性能、以及殘余應力等,得出冷噴涂鋁涂層具有優(yōu)良的耐腐蝕性能,孔隙率低且涂層較厚等優(yōu)點。
國際油漆協(xié)會通過一系列循環(huán)模擬實驗表明:與傳統(tǒng)的酚醛環(huán)氧、有機硅鋁粉、無機硅氧烷油漆相比,冷噴鋁的耐高溫性能、耐熱振性能和熱循環(huán)防腐性能均十分優(yōu)異,經過高溫熱循環(huán)后,仍能在海洋大氣環(huán)境下保持十分優(yōu)異的防腐性能,是目前解決保溫層下腐蝕的最佳涂料方案之一。
4.4 納米涂層
納米涂層是通過使用納米技術,使材料在分子水平上收縮,來形成一種致密的涂層,由于納米材料所具有的特殊性能,可以在涂層聚合物中均勻分布,使得涂層的整體性質也發(fā)生相應的變化,因此,納米涂層可以實現(xiàn)許多功能的疊加,得到具有高強度、高柔韌性以及優(yōu)良光澤度的多功能涂層。
不同納米顆粒的加入,可以相應地提高涂層的性能,如ZrO,SiO和AlO等粒子,可以明顯提高材料的抗磨損性能;而TiO或ZnO顆粒則可以吸收并反射紫外線,降低光化學降解速率引發(fā)的氧化分解,延長使用壽命;Mg-Al層狀雙金屬氫氧化物 (LDH) 納米粒子可以在燃燒時吸收熱量并生成HO和CO,有效提高涂層的防火性能。
涂層的抗腐蝕性能主要受到顏料-樹脂比例 (P/B) 的影響,它決定腐蝕性有害電解質在涂層中的傳遞速率。由于納米材料具有更高的表面活性。相比于傳統(tǒng)顏料,它可以吸收更多樹脂,這就減少了顏料與樹脂之間的空隙,提高了涂層的密度和致密性,減少了腐蝕性介質的傳輸路徑,抗腐蝕性能也就得到了提高,但是只有最佳的顏料-樹脂比例才會有最好的效果,如Chen等研究發(fā)現(xiàn),對于Nano-ZinC納米涂層,最好的顏料-樹脂比例為0.3,而對于傳統(tǒng)的鋅涂層則為1.0,如果加入過多的納米粒子反而會形成不連續(xù)的膜層而產生缺陷。
Noveiri等在實際工程油氣管道表面施加30%丙烯酸類樹脂水和70%納米材料的涂層,通過掃描電鏡等手段對涂層進行分析,發(fā)現(xiàn)該涂層孔隙率非常低,耐腐蝕且難以滲透。Zand等在316L上施加硅烷的混合納米涂層并通過一系列實驗驗證得出,硅烷涂料中引入納米涂層技術,可以提供一層高效、致密、可靠且無污染的抗腐蝕涂層。Anwar等通過對比在環(huán)氧樹脂和氯乙烯涂層中加入或不加入多壁碳納米管 (MWCNT) 得到的不同涂層,通過電化學抗譜 (EIS) 分析并對比相同實驗條件下的結果,發(fā)現(xiàn)加有納米材料的涂層強度、粘附力和致密性明顯提高。
由于納米涂層的發(fā)展才剛剛起步,在實際應用中還有許多亟待解決的問題。首先,納米粒子的分散性和穩(wěn)定性,由于納米粒子較大的比表面積,使其具有較高的表面動能,可能會發(fā)生結痂現(xiàn)象;其次,作為顏料,納米粒子可能會因為尺寸過小失去顏色而變得透明;再次,要有穩(wěn)定的粘合劑來抑制納米材料如TiO的光催化活性以及有關超細粉末的硬化問題和特細微粒進入體內可能會引發(fā)化學反應產生的危險等。
沒有哪種單一的CUI涂層系統(tǒng)能夠適用于任何環(huán)境任何問題,在選擇涂層時要注意不同的系統(tǒng)選項。權衡涂層系統(tǒng)的性能表現(xiàn),綜合各方面的因素恰當?shù)剡x擇適合的涂層系統(tǒng),最大程度的達到環(huán)境效益和經濟效益的結合。
5、結論
包覆有保溫層管道和設備的使用壽命與CUI有很大的關系,CUI的隱蔽性和高危害性已經給工業(yè)生產帶來了嚴重的經濟問題和安全問題。隨著工業(yè)特別是石化工業(yè)的高速發(fā)展,有關CUI的問題越來越突出,由于CUI所導致的損失也越來越大,因此,研發(fā)新型高效防護涂層及保溫材料,最大程度地減少CUI的發(fā)生,在CUI問題上實現(xiàn)經濟效益、環(huán)境效益和安全效益的多項統(tǒng)一具有非常重要的意義。
更多關于材料方面、材料腐蝕控制、材料科普等方面的國內外最新動態(tài),我們網(wǎng)站會不斷更新。希望大家一直關注中國腐蝕與防護網(wǎng)http://www.ecorr.org
責任編輯:殷鵬飛
《中國腐蝕與防護網(wǎng)電子期刊》征訂啟事
投稿聯(lián)系:編輯部
電話:010-62313558-806
郵箱:fsfhzy666@163.com
中國腐蝕與防護網(wǎng)官方 QQ群:140808414
免責聲明:本網(wǎng)站所轉載的文字、圖片與視頻資料版權歸原創(chuàng)作者所有,如果涉及侵權,請第一時間聯(lián)系本網(wǎng)刪除。
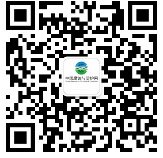
官方微信
《中國腐蝕與防護網(wǎng)電子期刊》征訂啟事
- 投稿聯(lián)系:編輯部
- 電話:010-62313558-806
- 郵箱:fsfhzy666@163.com
- 中國腐蝕與防護網(wǎng)官方QQ群:140808414