第三章 全面腐蝕 ▲
3.4 全面腐蝕機理
全面腐蝕(均勻腐蝕)是由化學腐蝕或電化學腐蝕引起的。腐蝕介質能夠較均勻地抵達金屬表面的各部位,而且金屬的成分和組織比較均勻,使腐蝕在整個金屬表面以幾乎相同的速度進行。
全面腐蝕多發生在碳鋼和低合金鋼材料上。不銹鋼和其他依靠鈍化膜耐蝕的材料在低pH值的腐蝕環境中,也可以因鈍化膜溶解而活化,發生全面腐蝕;或者在高溫條件下,鈍化膜轉化為疏松多孔的氧化皮,附著性差易剝落,而失去保護作用。
無論是化學腐蝕,還是電化學腐蝕引起的全面腐蝕,其共同的特點是材料表面不能形成具有保護作用的鈍化膜,腐蝕產物可溶于介質中,或形成疏松多孔的氧化皮,使腐蝕得以持續進行。
Vol.3.4.1 化學腐蝕
化學腐蝕通常發生在一些干燥氣體和非電解質溶液環境中,工業中常見的化學腐蝕有金屬高溫氧化、高溫硫化、鹵素腐蝕等其它的氧化劑(H2O、CO2、SO2、SO3、H2S等)引起的化學腐蝕,在這些腐蝕條件下金屬表面會形成氧化膜(層、皮)、硫化膜(層、皮)、氮化膜(層、皮)、鹵化膜(層、皮)等;在滲碳、脫碳、氫腐蝕等還原性氣氛引起的腐蝕,會形成滲碳或脫碳層;在熔鹽中產生堿性或酸性熔融腐蝕導致金屬厚度減??;金屬在非電解質溶液中的腐蝕、某些金屬在某些有機溶劑中的腐蝕現象(如:Al在CCl4、Mg和Ti在甲醇中的腐蝕)等也屬于化學腐蝕。腐蝕反應熱力學和動力學見“化學腐蝕”。金屬被氧化的化學腐蝕表現為氧化膜(皮)或其他腐蝕產物形成的膜逐漸增厚,腐蝕能否持續進行和腐蝕速率,取決于所生產的氧化膜(皮)對基體金屬的保護作用。
01 氧化
在空氣或高溫含氧的工藝氣、煙氣、水氣等環境中,金屬被氧化,產生全面腐蝕。主要化學反應見式2-1~2-4。高溫氧化的典型過程為當金屬達到高溫氧化起始溫度時開始氧化,在金屬表面形成一層致密的金屬氧化膜阻止金屬發生進一步氧化,但隨著溫度上升,氧化膜成分發生變化,氧化膜逐漸增厚,失去對金屬的保護作用。金屬中的鉻含量的增高有助于提高氧化膜的穩定性,阻止氧化皮的剝落。
碳鋼的基體組成為Fe,因此它的氧化皮主要是由FeO、Fe3O4、Fe2O3組成,故它的抗氧化性和純Fe的差別并不大,即570℃以下碳鋼具有較好的抗氧化性,溫度高于700℃時碳鋼脫碳嚴重,它比純Fe的抗氧化性更差,這是因為脫碳時逸出氣態CO2使氧化皮中出現更多缺陷的緣故。
提高鋼鐵抗高溫氧化性能的主要合金元素,除Cr外還有Al和Si。雖然Al和Si的作用比Cr更強,但加入Al和Si對鋼鐵的力學性能和加工性能不利,而Cr能提高鋼材的常溫和高溫強度,所以Cr成為耐熱鋼必不可少的主要合金元素。Ni-Cr合金由于Cr的選擇性氧化,合金表面可形成致密的NiCr2O4及Cr2O3保護膜,使合金的抗氧化溫度達1100℃。Ni-Cr-Al合金由于Al2O3的熱穩定性比Cr2O3更高,所以Ni-Cr-Al合金可以在1300℃下使用。
02 高溫硫腐蝕
高溫硫腐蝕指金屬在高溫下與含活性硫介質作用,生成硫化物的過程,它是煉油石油化工、火力發電和工業中各種燃料爐的一種常見的失效方式。高溫環境中硫的存在形式不同, 硫腐蝕的類型也呈多樣性,可大致分為: 高溫硫化,高溫混合氣氛下的硫化-氧化所導致的熱腐蝕。
① 高溫硫化腐蝕
高溫硫化是指高溫下金屬與硫反應而導致的腐蝕。通常是指含H2S、單質S蒸氣和有機硫化物在高溫下與金屬發生高溫硫腐蝕,形態為均勻減薄,可在金屬表面生成硫化物膜,硫化物膜厚度較大,可達幾十nm,甚至更高,某些硫化膜也可以對基體金屬產生保護作用。如在240℃以上的重油部位硫、硫化物和硫化氫形成的腐蝕環境,常減壓蒸餾裝置中的常壓塔減壓塔下部及塔底管線、常壓重油和減壓渣油的高溫換熱器,硫化催化裂化裝置分餾塔的下部、延遲焦化裝置分餾塔的下部等位置。加氫裝置、催化重整裝置、延遲焦化裝置的焦炭塔、分餾塔、硫磺回收裝置、硫磺尾氣脫硫裝置以及聚苯乙烯裝置的脫氫爐等都存在高溫硫的腐蝕。
Ni及Ni合金對H2S和含硫氣體在高溫下特別敏感,這種腐蝕往往帶有災難性。因為,液態硫化物迅速進入金屬晶界,從而使金屬碎裂。但鐵基合金、300系列不銹鋼在這種環境下耐蝕性較好。
金屬與硫反應的速度比氧化反應快得多,其主要原因為:
a.硫化物的擴散系數大于氧化物的擴散系數;
b.硫化物的熔點比氧化物的低,金屬可與這些硫化物形成低熔點的共晶物,進而導致加速硫化反應;
c.金屬硫化物的分子體積大于氧化物,硫化物產生的應力比氧化物產生的應力大許多, 易使硫化層破裂,從而加速金屬的硫化。
能與金屬起反應的硫稱為活性硫,主要有元素硫、硫化氫、硫醇硫、二硫化物、亞砜、硫醚,硫醚、噻吩、苯并噻吩、二苯并噻吩、砜為非活性硫。高溫硫腐蝕與溫度關系密切,不同溫度下各種硫化物的腐蝕性不同。所以,在含硫原油的加工過程中,由于非活性硫不斷向活性硫轉變,使硫腐蝕不僅存在于一次加工裝置,也存在于二次加工裝置,甚至延伸到下游化工裝置??梢哉f硫腐蝕貫穿于煉油的全過程。再加上硫腐蝕與氧化物、氯化物、氮化物、氰化物等腐蝕介質的共同作用,形成了錯綜復雜的腐蝕體系,對硫腐蝕的動力學和熱力學研究以及防護措施的制定帶來很多困難。主要機理為:
a.t≤120℃硫化物未分解,在無水情況下,對設備無腐蝕;但當含水時,則形成煉廠各裝置中輕油部位的各種H2S-H20型腐蝕;
b.≤240℃,原油中活性硫化物未分解故對設備腐蝕輕微;
c.240℃<t≤340℃,硫化物開始分解,生成H2S對設備腐蝕開始,并隨著溫度升高而腐蝕加重;
d. 340℃<t≤400℃,H2S開始分解為H2和S,H2S分解出來的硫為活性硫,腐蝕性很強。該溫度下,低級硫醇能直接與鐵反應而腐蝕。腐蝕反應式為:
H2S = H2 + S(3-1)
Fe + S = FeS(3-2)
RCH2CH2SH + Fe = FeS + RCH=CH2 + H2 (3-3)
煉油廠中高溫硫的腐蝕是以H2S為主的活性硫腐蝕,由于原油所含硫化物組成及性質不同,腐蝕性也可能不同。原油中不同有機硫化物有不同分解溫度,硫醚和二硫化物在130~160℃開始分解,其他有機物的分解反應在250℃左右開始。溫度升到375~425℃時未分解的H2S也能與鐵直接反應;
e.420℃<t≤430℃,高溫硫對設備腐蝕速率最快;
f.t>480℃,硫化物近于完全分解,腐蝕率下降;
g.t>500℃,硫化物不穩定,腐蝕轉化為高溫氧化腐蝕。
不同硫化物的腐蝕性強弱不一樣,二硫化物腐蝕最強。含有活潑氫的硫化物在高溫下對金屬的腐蝕服從催化反應機理,無活潑氫的硫化物在高溫下對金屬的腐蝕服從硫自由基機理。單質硫在高溫下不需要離解或催化過程,可直接在金屬表面吸附發生反應腐蝕金屬,所以單質硫在這些硫化物中表現出了最強的腐蝕性。二硫化物官能團“-S-S-”化學性質十分活潑,受熱易分解,生成硫自由基,因此對金屬具有很強的腐蝕性。H2S在高溫下由于通過氫原子吸附在金屬表面,其吸附作用和硫自由基相比稍弱,因此其腐蝕性應弱于元素硫和二硫化物。硫醇在熱作用下可以形成·SH自由基,也可以在金屬表面催化腐蝕金屬,因此腐蝕性應比硫化氫弱,但強于其它非活性硫化物。硫醚中的官能團“-S-”化學性質較為穩定,只有分解或生成硫自由基才能腐蝕金屬。噻吩類硫化物由于其雙環作用,大大增強了其分子內的共軛作用,因此噻吩類化合物性質十分穩定,在熱作用下幾乎不分解,同時由于其強共軛作用,分散了硫的電子云密度,使硫具有一定的親電性,因此其可以在金屬表面具有一定的吸附量,因而在一定條件下,噻吩類化合物具有一定的緩蝕作用。
影響高溫硫腐蝕的主要因素有:
a.材料合金成分。增加材料中Cr元素含量可提高其抗高溫硫腐蝕性能,加工高含硫原油的高溫(288℃)以上部位,Cr5Mo的腐蝕速率較大,應選用更高等級材質,見SH/T 3096[1],300系列不銹鋼可耐硫腐蝕。工程設計上耐硫腐蝕金屬材料的選擇是根據腐蝕性評價數據或曲線和實踐經驗來確定,不片面追求合金化和不銹鋼化。McConomy曲線可以預測材料高溫硫的腐蝕程度,工程上用來確定選材,API RP 939C [2] 對McConomy曲線進行了修正和補充。該項推薦作法適用于操作溫度在230℃~540℃條件下,不論是否有氫存在的含硫化合物的烴類工藝流體。這里沒有規定含硫量的下限,因為在過去10多年中,一些加氫處理裝置的重沸器/分餾塔在硫或H2S含量低至1×10-6的情況下也出現了比較嚴重的腐蝕。API RP 939C的適用范圍不包括鎳基合金腐蝕和由于燃燒含硫燃料所導致的加熱管外壁腐蝕;
b.溫度和流速。介質流速和溫度的升高均能導致材料的腐蝕速率增加,溫度的影響大于流速的影響。流速超過30m·s-1腐蝕加劇,和環烷酸腐蝕一樣,在渦流高的位置保護性的硫化膜被沖刷,腐蝕加劇;
c.原油的硫含量與其腐蝕性沒有線性關系;同一種原油不同餾分油的硫含量決定油品的腐蝕性能,油品的腐蝕速率隨硫含量的升高而增加。
② 高溫混合氣氛下的硫化-氧化
高溫混合氣氛下的硫化-氧化腐蝕是指在含氧和硫的混合氣氛下,金屬受到氧化、硫化或硫化-氧化為主的腐蝕,主要形式有:
a.在氧分壓高于氧化物分壓時,反應主要是氧化,形成氧化物;
b.在硫分壓高于硫化物分壓時,反應主要是硫化,形成硫化物;
c.當環境氣氛的硫分壓、氧分壓正處在硫化物、氧化物的分壓時,同時發生硫化、氧化,硫化物和氧化物能平衡共存。
03 環烷酸腐蝕
環烷酸在石油煉制過程中,隨原油一起被加熱、蒸餾,并與其沸點相同的油品冷凝,且溶于其中,從而造成該餾分對設備材料的腐蝕。
環烷酸是非電解質,與金屬的反應是化學腐蝕過程。腐蝕大多發生在液相,在220℃以下腐蝕很輕,在沸程為270~280℃,350~400℃時腐蝕最嚴重,氣相腐蝕很小。環烷酸腐蝕的反應為:
2RCOOH + Fe = Fe(RCOO)2 + H2↑ (3-4)
2RCOOH + FeS = Fe(RCOO)2 + H2S↑ (3-5)
可以看出,環烷酸除了與鐵直接作用產生腐蝕外,還能與腐蝕產物如FeS反應,生成可溶于油的環烷酸鐵,當環烷酸與腐蝕產物反應時,不但破壞了具有一定保護作用的FeS膜,同時游離出H2S又可進一步腐蝕金屬:
H2S + Fe = FeS+ H2↑ (3-6)
從動力學角度考慮,環烷酸與金屬反應通常經過環烷酸分子向金屬表面傳輸、在金屬表面吸附、與表面活性中心發生反應、腐蝕產物脫附4個步驟,上述步驟中最慢的步驟是整個腐蝕反應的控制步驟。因原油性質和設備材質不同, 反應溫度和流速流態等因素的差異, 環烷酸腐蝕的控制步驟也會發生變化。環烷酸腐蝕為吸熱反應,因此升高溫度,顯著加速碳鋼在高溫環烷酸介質中腐蝕速率。
影響環烷酸腐蝕的因素主要有油品的酸值、硫含量、溫度、流速和流態、材質、環烷酸的種類和分子量大小。介質的酸值、流速、流態和溫度是環烷酸腐蝕的重要參數,流速和酸值、溫度存在著一個臨界值,對環烷酸腐蝕的影響很復雜。在不同的流速流態下,環烷酸腐蝕形態和機理都可能發生改變。針對高溫環境下影響原油中環烷酸腐蝕的主要因素, 一般主要采用以下方法控制其腐蝕:
a.合理設計,改進煉油工藝,采用混煉或摻煉技術、注堿工藝以降低原油酸值或控制硫含量等方法,將高酸值和低酸值的原油混合到酸值低于環烷酸腐蝕發生的臨界值以下控制環烷酸腐蝕;
b.選材,在較高流速下,耐蝕性從低到高排列順序為碳鋼、低合金鋼和不銹鋼。Cr對耐蝕性起決定作用,主要是提高合金熱穩定性和產生鈍化作用,在鋼表面形成富氧的氧化膜,擴大鋼在酸中的鈍化范圍,提高鋼的抗氧化能力。有研究表明[3],在酸值小于4 mg KOH/g、流速大于73 m·s-1時,5Cr-0.5Mo 和12%Cr鋼有比碳鋼更好的耐蝕性能。
中國石化集團防腐蝕研究中心對S32168(321)、S31603(316L)、S41008(0Cr13)、Cr5Mo和20G在環烷酸腐蝕速率進行了試驗研究,結果見圖3-11、12。介質流速在25m·s-1時,不銹鋼明顯優于碳鋼和低合金鋼,在300℃以上S31603仍能維持鈍態,而S32168、S41008已活化,腐蝕速率明顯上升。
圖3-11S31603、0Cr13、Cr5Mo和20G腐蝕評價結果(25m·s-1)
圖3-12 S32168和S31603的腐蝕評價結果對比(25m·s-1)
c.注堿中和或原油脫羧。在原油進入蒸餾裝置之前,可注入苛性鈉中和環烷酸,然后分離;
d.控制流速流態。包括適當降低物料流速、在可能的情況下改變管長、擴大管徑以降低流速, 盡量在結構上平緩過渡, 減少急彎走向以控制流態等方法來控制環烷酸對設備的腐蝕。但是由于工藝的限制,對于流速、流態的改變受到很大的局限,因此對環烷酸腐蝕的抑制作用也有限;
e.添加緩蝕劑,常用的環烷酸緩蝕劑主要有磷系緩蝕劑以及非磷系緩蝕劑,磷系緩蝕劑主要有磷酸酯類、亞磷酸芳香酯類緩蝕劑,非磷系緩蝕劑是一些含氮、硫等元素的有機化合物。在緩蝕效果方面磷系緩蝕劑優于非磷系緩蝕劑,而將兩者混合使用緩蝕效果最佳。
f.涂鍍層表面保護。在基材表面噴涂耐高溫涂層或采用化學鍍層等。該方法實際上將環烷酸與鋼鐵界面變成環烷酸與耐高溫涂層間的界面。耐高溫涂層或化學鍍層難溶于環烷酸或原油,故可有效防止環烷酸腐蝕。
g.加強在線腐蝕監測,采用腐蝕掛片、旁路、餾分油鐵離子分析、超聲波測厚、安裝電阻或電感腐蝕探針等方法在線監測材料的腐蝕速率。
04 高溫氫腐蝕(HTHA)
HTHA是氫原子擴散到鋼中并與微觀組織中的碳化物發生反應的結果。在臨氫條件下,吸附在鋼表面的分子氫通過金屬晶格和晶界向鋼內擴散,使鋼嚴重脫碳產生沿晶腐蝕裂紋,力學性能下降。這種腐蝕速度取決于溫度、氫分壓、加熱時間、鋼的含碳量和合金元素等因素。有2種反應和HTHA相關,一個是氫分子(H2)分解成能在鋼中擴散的氫原子(H),第二個反應發生在原子氫和金屬碳化物之間,4H + MC = CH4 + M。對鋼材的破壞也有2種形式,一是因甲烷氣體在碳化物基體界面上積聚,形成了很高的局部應力,而產生內部脫碳和裂紋或鼓包,其力學性能發生顯著的劣化。二是原子氫和鋼材表面或臨近表面的碳化物發生反應產生的表面脫碳,在該表面甲烷氣體可溢出而不會形成裂縫。內部裂縫一般可在碳鋼、C-0.5Mo鋼和高氫分壓下的Cr-Mo鋼中觀察到,而表面脫碳在高溫和低的氫分壓下的Cr-Mo鋼中更普遍。增加鋼中合金的Cr、Mo元素,碳化物的穩定性提高,可減緩HTHA。
鋼的抗氫腐蝕性能與鋼的顯微組織也有密切關系。所以,壓力容器的制造和熱處理制度對設備的抗HTHA性能影響也很大,對于淬火狀態,只需經很短時間加熱就出現了氫腐蝕,但進行回火處理,且回火溫度越高,由于形成穩定了的碳化物,抗氫腐蝕性能也得到改善。另外,對于在臨氫環境下使用的鉻-鉬鋼設備,進行焊后熱處理同樣具有提高抗氫腐蝕能力的效果。試驗證明,2.25Cr-1Mo鋼焊縫若不進行焊后熱處理,則發生氫腐蝕的溫度將比納爾遜(Nelson)曲線表示的溫度低100℃以上。
在高溫氫腐蝕中,在高溫氫氣中材料的蠕變強度會下降。特別是由于二次應力(如熱應力或由冷作加工所引起的應力)的存在會加速高溫氫腐蝕。當沒有變形時,氫腐蝕具有較長的“孕育期”;隨著冷變形量的增大,“孕育期”逐漸縮短,當變形量達到一定程度時,則無論在任何試驗溫度下都無“孕育期”,只要暴露到此條件的氫氣中,裂紋立刻就發生。
高溫高壓氫環境下的設備選材是按照“納爾遜(Nelson)曲線”來選擇的,該曲線最初是在1949年由G·A·Nelson收集到的使用經驗數據繪制而成,并由API提出,于1970年作為API出版物941(第一版)公開發行。從1949年至今,根據實驗室的許多試驗數據和實際生產中所發生的一些氫腐蝕破壞的事例,相繼對曲線進行過多次修訂,API RP 941一直是最有用的抗高溫氫腐蝕選材的一個指導性文件,該準則提供了煉油廠和石油化工廠加工高溫高壓氫氣或含氫流體設備用鋼的安全范圍,相關國家標準正在制定中。該曲線是本推薦準則中所列的臨氫作業用鋼防止脫碳和開裂的操作極限,在溫度和氫分壓范圍,這些鋼已經得到成功應用而沒有因HTHA造成的破壞。材料默認為退火狀態,不能用于含As、Sb、Sn和P等高含量混入元素的鋼,如懷疑高含量混入元素,則臨界Pv系數應降低,對于高含量的混入元素的鋼的熔煉爐次,臨界Pv系數可低至0.25。
05 滲碳
在高溫及含碳的環境氣氛(如CO和烴類)中,環境中的碳化物在與鋼接觸時發生分解并生成游離碳,使鋼表面的氧化膜破損,并滲入鋼中生成碳化物的現象。一般在表面發生,碳的濃度在表面最大。滲碳危害有:
a.滲碳裂紋;
b.蠕變斷裂;
c.650℃以下的脆性斷裂;
d.滲碳引起的金屬粉化;
c.承載壁厚減薄。
06 脫碳
鋼的脫碳是由于鋼中的滲碳體Fe3C在高溫下與介質作用被還原成鐵發生脫碳反應,使得鋼表面滲碳體減少。由于Fe3C含量的減少將使鋼表面的碳含量降低,致使鋼鐵表面硬度減小,疲勞極限降低,此現象稱為碳鋼的脫碳。主要化學反應有:
07 氮化(滲氮)
某些合金暴露在含氮化合物(氨、氰化物)很高的高溫工藝環境中時,尤其是在還原條件下,形成一個硬脆的氮化表面層。受影響的合金主要有碳鋼,低合金鋼、300系列和400系列不銹鋼。會導致高溫蠕變強度、室溫力學性能(尤其是強度/韌性)、焊接性能和耐蝕性能的降低,嚴重降低材料的耐蝕性。
滲氮是一個擴散控制過程,由溫度、時間、氮的分壓和金屬成分決定。溫度必須足夠高,以使氮從氨或其它化合物中熱分解出來,并使氮向金屬內部擴散。滲氮在溫度高于316℃時開始發生,在高于482℃時加重。高氣相氮活性(高的氮分壓)促進滲氮。
滲氮通常發生在部件的表面,形成一個暗灰色的外觀。但是,在滲氮的初始階段,只能通過金相來發現。在更嚴重的階段,金屬會顯示出很高的表面硬度。在多數情況下,容器或設備表面硬度的輕微增加不會影響設備的整體力學性能。但是,在滲氮層內潛在的裂紋擴展可能會穿透整個基體金屬。12% Cr(mass)以下的低合金鋼的滲氮伴隨著體積的增加,滲氮層會開裂和破碎。高于410℃,優先的晶界滲氮可能會導致微裂紋和脆斷。不銹鋼會形成一個薄的脆性層,在熱循環或外加應力的作用下發生開裂和破碎。
防護措施,需要采用更耐蝕的含有30%到80%的鎳的合金,而不采用改變工藝條件來降低氮分壓或降低溫度。
Vol.3.4.2 電化學腐蝕
造成壓力容器全面腐蝕的電化學腐蝕過程,主要取決于腐蝕微電池的作用。腐蝕原電池由微觀腐蝕電池組成,其單個陰、陽極的面積非常小,甚至用微觀方法也無法辨認,而且微陽極和微陰極的位置隨機變化;整個金屬表面在電解質溶液中處于活化狀態,只是各點隨時間(或地點)有能量起伏,能量高時(處)呈陽極,能量低時(處)呈陰極,從而使整個金屬表面遭受均勻的腐蝕。
金屬與溶液的界面特性―雙電層,金屬浸入電解質溶液內,其表面的原子與溶液中的極性水分子、電解質離子相互作用,使界面的金屬和溶液側分別形成帶有異性電荷的雙電層。雙電層的模式隨金屬、電解質溶液的性質而異,一般有以下3種類型,圖3-13。
圖3-13 金屬在電解質溶液中的雙電層模型
a.離子的水化能超過了晶格上的鍵能,金屬側荷負電、溶液側荷正電的相對穩定的雙電層,電負性強的金屬,如鋅、鎘、鎂、鐵等浸入水、酸、堿、鹽溶液中形成這種雙電層;
b.離子的水化能小于金屬上晶格的鍵能,金屬側荷正電、溶液側荷負電,通常比較不活潑的金屬浸在含有濃度較高的正電性較強的金屬離子的溶液中,如鉑浸在鉑鹽溶液中、銅浸在銅鹽溶液中等形成這種雙電層;
c.離子的水化能等于金屬上晶格的鍵能,形成金屬側荷正電、溶液側荷負電,如鉑浸在溶有氧的中性溶液中,氧分子被吸附在鉑表面,并離解為原子,再奪得鉑表面的電子而成為荷負電的負離子。
雙電層如同平板電容,由于兩側之間的距離非常?。ㄒ话慵s為5×10-10 m左右),所以雙電層中的電場強度特別高,達到109 ~ 1010 V·m-1。雙電層兩層“極板”分處于不同的兩相—金屬相(電子導體相)和電解質溶液(離子導體相)中,雙電層的內層有過剩的電子或陽離子,當系統形成回路時,電子即可沿導體流入或流出電極,形成腐蝕電流,使腐蝕反應得以進行。金屬的電化學腐蝕歷程包含著兩個同時進行而又相對獨立的過程,即陽極的氧化反應和陰極的還原反應,當電極反應正逆過程的電荷輸送速度和物質遷移速度相等時,反應達到動態平衡狀態。
金屬的熱腐蝕是高溫腐蝕的一種重要形式,在工業上,典型的熱腐蝕環境主要有燃燒動力系統和燃料電池等。這兩種環境的沉積巖類型分別為硫酸鹽和碳酸鹽。
a.硫酸鹽體系。硫酸鹽沉淀熱腐蝕是指金屬材料由于高溫環境因素,在其表面沉積物形成熔融鹽層而加速腐蝕的現象。堿金屬等硫酸鹽的熔點低,在高溫下呈熔融狀態。若在灰渣附著層中存在焦硫酸鹽時會形成反應速度更快的熔巖型腐蝕。當溫度在680℃左右時,熔融硫酸鹽的腐蝕速度約為氣態時的4 倍。并隨壁溫度增高而加劇。
如,在各種燃油和燃煤的動力裝置中,由于燃料中含有S、K、C、Na、V等雜質,在燃燒時形成SO2、CO2、SO3、V2O5等雜質,與含O2和NaCI再作用形成硫酸鹽沉積在材料表面。純Na2SO4熔點為844℃,如果混合其他鹽,混合鹽的熔點會降低。
b.碳酸鹽體系。碳酸鹽體系背景主要是第二代燃料電池-熔融碳酸鹽燃料電池。
由于表面沉積一層熔融鹽而引起的金屬熱腐蝕與常規的金屬在水溶液中腐蝕有相似之處。已明確,如果介質是離子導體,那么金屬腐蝕過程總是按電化學腐蝕的途徑進行。與水溶液相似,熱腐蝕的電化學機制模型認為,在熔鹽體中至少存在兩個電化學反應,金屬陽極溶解和氧化劑的陰極還原。
免責聲明:本網站所轉載的文字、圖片與視頻資料版權歸原創作者所有,如果涉及侵權,請第一時間聯系本網刪除。
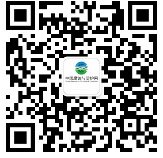
官方微信
《中國腐蝕與防護網電子期刊》征訂啟事
- 投稿聯系:編輯部
- 電話:010-62316606-806
- 郵箱:fsfhzy666@163.com
- 中國腐蝕與防護網官方QQ群:140808414