鋼件熱處理強化后的性能與淬火馬氏體的性能有密切的關系。其中最突出的問題是強度和韌性的配合。因此,需要從決定馬氏體強度和韌性的一般規律出發,找出設計或選用新的鋼種以及制訂合適的熱處理工藝的一些基本原則。
一、馬氏體的硬度和強度
鋼中馬氏體最主要的特性就是高硬度、高強度,其硬度隨碳含量的增加而升高。但當碳含量達0.6%時,淬火鋼的硬度接近最大值,如圖1 。
▲圖1 淬火鋼的最大硬度與碳含量的關系1-高于AC3淬火 2-高于AC1淬火 3-馬氏體硬度
碳含量進一步增加時,雖然馬氏體硬度會有所增高,但由于殘留奧氏體量增加,使鋼的硬度反而會下降。合金元素對馬氏體硬度影響不大。
近年來對馬氏體高強度的本質進行了大量的研究工作,認為引起馬氏體高強度的原因是多方面的,其中主要包括相變強化、碳原子的固溶強化和時效強化等。
1. 相變強化
馬氏體相變的切變特性造成在晶體內產生大量微觀缺陷(位錯、孿晶及層錯等),使得馬氏體強化,此即謂之相變強化。實驗證明,無碳馬氏體的屈服極限為284MPa。這個值與形變強化鐵素體的屈服極限很接近。而退火狀態鐵素體的屈服極限僅為98~137MPa。也就是說,相變強化使強度提高了147~186MPa。
2.固溶強化
為了嚴格區別C原子的固溶強化效應與時效強化效應,曾專門設計了一系列Ms 點極低且碳含量不同的Fe-Ni-C合金,以保證馬氏體相變能在C原子不可能發生時效析出的低溫下進行。淬火后即在低溫下測量馬氏體的強度以了解C原子的固溶強化效應,圖2 中曲線1為Fe-Ni-C合金淬火后在0°C測得的結果。
▲圖2 Fe-Ni-C合金馬氏體在0℃時的屈服強度σ0.6與碳含量的關系
由此曲線可見,馬氏體的屈服極限隨碳含量的增加而升高,但當碳含量達0.4%以上時,強度不再增加。根據這一曲線可得出馬氏體的屈服強度與碳含量的關系,在含C<0.4%時此關系近似為:
σs=284+1784× (%C)MPa (1)
為什么馬氏體中的間隙原子有如此強烈的固溶強化效應,而C溶解在奧氏體中的固溶強化效應則不大?
目前認為,奧氏體和馬氏體中的C原子均處于Fe原子組成的八面體中心,但奧氏體中的八面體為正八面體,間隙C原子溶入只能使奧氏體點陣對稱的膨脹。而馬氏體中的八面體為扁八面體,即有一個方向上的Fe原子間距較小,間隙原子溶入后力圖使其變成正八面體。結果使扁八面體短軸方向上的Fe原子間距增長了36%;而在另外兩個方向上則縮短了4%,從而使體心立方變成了體心正方。由間隙C原子所造成的這種不對稱畸變稱為畸變偶極,可視其為一個強烈的應力場,C原子就在這個應力場的中心,這個應力場與位錯產生強烈的交互作用,而使馬氏體的強度提高。按這個觀點計算所得的C的固溶強化效應與實驗數據基本符合。但碳含量超過0.4%以后,馬氏體進一步強化的效果減小,可能是因為C原子靠得太近,以至畸變偶極應力場之間因相互抵消而降低了應力。應當指出,上述用Ms點極低的Fe-Ni-C合金所得的為欒晶馬氏體,其中也包含欒晶對馬氏體的強化作用。對于位錯型馬氏體,就沒有這部分強化,故強度略低。形成置換式固溶體的合金元素對馬氏體的固溶強化效應相對于C來說要小得多,據估計,僅與合金元素對鐵素體的固溶強化作用大致相當。
3.時效強化
時效強化也是一個重要的強化因素。理論計算得出,馬氏體在室溫下只需幾分甚至幾秒就可通過原子擴散而產生時效強化。電阻分析表明,C原子的擴散實際上比理論計算的結果快。在-60°C以上,時效就能進行,發生C原子偏聚現象(回火時碳原子析出以前的階段)。C原子偏聚是馬氏體自回火的一種表現。因此,對于在-60℃上形成的含碳馬氏體都有一個自回火問題,在強化的總效果中都包括了時效強化在內。圖2中曲線2表明,淬火后在0℃時效3小時,屈服極限就有了進一步提高,碳含量愈高,時效強化效果愈顯著。
4.動態應變時效
馬氏體的屈服強度與碳含量的關系如圖3 。
▲圖3 馬氏體的屈服強度與碳含量的關系
由圖可見,當永久變形很小時(ε=0.02%),其屈服強度σ0.2幾乎與碳含量無關,并且數值很小(約為196MPa)。可是σ0.2卻隨碳含量的增加而急劇增大。這個現象說明,馬氏體本來比較軟,在外力作用下因塑性變形而急劇加工硬化,即發生了動態應變時效。
二、馬氏體的機械性能與形態及亞結構的關系
淬火馬氏體和回火馬氏體的硬度與抗拉強度之間存在著線性關系。對屈強比為常數的合金,硬度和屈強比之間也存在類似關系。Fe-C和Fe-Ni合金中的研究資料匯總 見圖4 。
▲圖4 淬火馬氏體的硬度與屈服強度的關系
這些數據表明,Fe-C合金馬氏體的硬度與其屈服強度成良好的線性關系。因此,在研究馬氏體的性能時,常由鋼淬火后所測量的硬度來大致估計鋼中馬氏體的強度。
對于碳含量低于0.3%的Fe-C合金馬氏體,其組織基本上為位錯型馬氏體,主要靠C的固溶強化(C釘扎位錯)。碳含量大于0.3%的馬氏體,其亞結構中孿晶量增多,還附加孿晶對強度的貢獻。圖5 示出C對Fe-C合金馬氏體 硬度的影響。同時示意出亞結構對馬氏體硬度(強化)的貢獻與碳含量之間的關系。其中直線表示碳釘扎位錯的作用,橫線部分表示孿晶亞結構對硬度的影響。當碳含量大于0.8%時,硬度不再增高是由于殘留奧氏量增高所致。
▲圖5 C對Fe-C合金馬氏體硬度的影響(-196℃,7天)
圖6 表示未經時效的Fe-Ni-C合金位錯型馬氏體與孿晶馬氏體的抗壓強度。
▲圖6 未經時效的孿晶馬氏體與位錯馬氏體的抗壓強度(Fe-Ni-C合金)
由圖中可見,在低碳量范圍內兩者抗壓強度相差很小,而隨碳含量增加,欒晶馬氏體的抗壓強度增加較快,曲線的斜率較大。這說明碳含量增高欒晶亞結構對馬氏體的強度的貢獻增大。圖7 中表示的Fe-Cr-C鋼馬氏體中的情況亦類似。
▲圖7 Cr含量和碳含量對Fe-Ni-C鋼淬火馬氏體的影響(n代表Fe-4%Cr-0.17%C鋼α中的孿晶相對量)
當提高鉻含量使孿晶亞結構相對量增加時,在0.17%C鋼中屈服強度并不增加。由此可見,單純合金元素的固溶強化作用是比較小的,而在C含量為0.35%的鋼中,其孿晶相對量較高,當提高鋼中鉻含量而使孿晶相對量增加時,屈服強度顯著上升。
除成分及亞結構決定馬氏體的強度外,原始奧氏體晶粒大小和板條狀馬氏體群的大小對馬氏體的強度也有一些影響。見圖8。
▲圖8 0.2%C鋼馬氏體的屈服強度與晶粒大小的關系
由圖8 中可見,馬氏體的屈服強度(σ0.2)與奧氏體晶粒大小(dγ)及馬氏體群大小(dα)的平方根成線性關系,可列為:
(2)
(3)
因此,原始奧氏體晶粒愈細小,馬氏體群愈小,則馬氏體的強度愈高。但是對中碳低合金結構鋼,奧氏體晶粒從單晶細化至10級晶粒時,強度增加≤245MPa。因此在一般鋼中,以細化奧氏體晶粒的方法來提高馬氏體強度作用不大。尤其對硬度很高的鋼,奧氏體晶粒大小對馬氏體強度的影響更不明顯。只在一些特殊熱處理中,如形變熱處理或超細化處理中,將奧氏體晶粒細化到15級或更細時,才能期望使強度提高幅度達到490MPa。
由上所述,低碳馬氏體的強化主要依靠其中C的固溶強化。在一般淬火過程中,伴隨自回火而產生的馬氏體時效強化也具有相當的強化效果。隨馬氏體中C和合金元素的含量增加,欒晶亞結構將有附加的強度。細化奧氏體晶粒大小及馬氏體群大小,也能提高一些馬氏體的強度。位錯馬氏體的亞晶界間距對馬氏體的強度也有一定的影響。
過去認為,馬氏體的韌性很差,幾乎沒有可塑性,這種認識是片面的。例如,位錯型馬氏體就具有良好的塑性和韌性。圖9表示低碳位錯型馬氏體(<0.4%C)具有較好的韌性。
▲圖9 不同碳含量Ni-Cr-Mo鋼的沖擊韌性
隨其碳含量的增加,韌性顯著下降。如對碳含量為0.6%的馬氏體即使經低溫回火,沖擊韌性還是很低,見圖9 b)。而圖7中表示,對于含C0.17%的馬氏體,當其中孿晶馬氏體量增加2倍以上時,斷裂韌性才顯著下降。而對含碳0.35%的馬氏體隨著孿晶馬氏體量增加,強度直線上升,斷裂韌直線下降。由此可見,馬氏體的韌性主要決定于它的亞結構。
圖10表示,在相同屈服條件下為脆性馬氏體的斷裂韌性比欒晶型馬氏體的斷裂韌性高得多。
▲圖10 含0.17%C及0.35%C的Fe-Cr-C鋼,淬火回火后的性能
圖11 表明鋼經回火后仍具有這種規律。
▲圖11 位錯型馬氏體與孿晶型馬氏體經不同回火后的沖擊韌性
大量實驗事實都證明,在強度相同的條件下,位錯馬氏體比孿晶馬氏體的韌性好得多,如表1 。
▼表1 馬氏體形態對鋼機械性能的影響
一般說來,低碳鋼淬火后往往得到位錯型馬氏體,但若認為低碳馬氏體就一定具有良好的韌性則是不夠確切的。因為在低碳鋼中若加入大量的能使Ms點降低的合金元素,淬火后也會得到大量的欒晶馬氏體,這時鋼的韌性亦將顯著變壞,見表2 。
▼表2 馬氏體形態與韌性的關系
所以,確切地說,應該是位錯型馬氏體具有良好的韌性,而不宜籠統地說低碳馬氏體具有良好的韌性。位錯型馬氏體不僅韌性優良,而且還具有脆性轉折溫度低、缺口敏感性低等優點。所以目前對結構鋼都力圖處理成位錯型馬氏體。
孿晶馬氏體之所以韌性差,除因其內部具有微裂紋而附加了脆性外,還可能與孿晶亞結構的存在及在回火時碳化物沿欒晶面析出呈不均勻分布有關。也有人認為可能與C原子在孿晶界偏聚有關。
綜上所述,馬氏體的強度主要決定于它的碳含量及其組織結構(包括自回火時的時效強化);而馬氏體的韌性主要決定于它的亞結構。低碳的位錯型馬氏體具有相當高的強度和良好的韌性。高碳的欒晶型馬氏體具有高的強度,但韌性很差。因此,以各種途徑來強化馬氏體,但使其亞結構仍保持位錯型,便可兼具強度和韌性。這是一條很重要的強韌化途徑。
三、馬氏體的相變塑性
金屬及合金在相變過程中塑性增長,往往在低于母相屈服極限的條件下即發生了塑性變形,這種現象即稱為相變塑性。鋼在馬氏體相變時也會產生相變塑性現象,稱為馬氏體的相變變塑性。
馬氏體相變誘發塑性的現象早就應用于生產,如高速鋼拉刀淬火時進行熱校直就是利用了馬氏體的相變塑性。圖12示出0.3%C-4%Ni-1.3%Cr鋼的馬氏體相變塑性。
▲圖12 0.3%C-4%Ni-1.3%Cr鋼在不同溫度下應力和總伸長率的關系
該鋼經850℃奧氏體化后,其Ms 點為307℃。奧氏體的屈服強度為137MPa。由圖中可以看出,當鋼奧氏體化后在307°C及323°C下施加應力,所加應力低于鋼的屈服強度時,即產生塑性變形,且塑性隨應力的加大而增長。在307℃施加應力時,溫度已達鋼的Ms點,故有馬氏體相變發生。而馬氏體相變一旦發生,即貢獻出塑性,所以隨應力增長,馬氏體相變在應力誘發下不斷進行,因而相變塑性也就不斷增長。在323℃加應力時,雖然在Ms點以上,但因應力誘發形成馬氏體,所以,所呈現的高塑性也是由于馬氏體相變引起的。近年來的研究工作表明,馬氏體相變所誘發的塑性還可顯著提高鋼的韌性。例如,在圖13中,存在著兩個明顯的溫度區間,在100~200℃高溫區,因為在斷裂過程中沒有發生馬氏體相變,K1c很低;在20~-196℃的低溫區,在斷裂過程中伴有馬氏體相變,結果使K1c顯著升高。如將高溫區曲線外推至室溫,可以看到,在室溫下伴有馬氏體相變的K1c較不發生馬氏體相變的K1c(即奧氏體的K1c)提高了63.8MPam?。
▲圖13 0.6%C-9%Cr-8%Ni-2%Mn鋼經1200℃水淬再經過420℃變形75%后在不同溫度下的斷裂韌性
關于馬氏體相變誘發塑性,可從如下兩方面加以解釋:
1.由于塑性變形而引起的局部區域的應力集中,將由于馬氏體的形成而得到松弛,因而能夠防止微裂紋的形成。即使微裂紋已經產生,裂紋尖端的應力集中亦會因馬氏體的形成而得到松弛,故能抑制微裂紋的擴展,從而使塑性和斷裂韌性得到提高。
2.在發生塑性變形的區域,有形變馬氏體形成,隨形變馬氏體量增多,形變強化指數不斷提高,這比純奧氏體經大量變形后接近斷裂時的形變強化指數要大,從而使已發生塑性變形的區域繼續發生變形困難,故能抑制頸縮的形成。
馬氏體相變塑性的研究引起了材料和工藝的一系列變革。近年來應用馬氏體的相變塑性現已設計出相變誘發塑性鋼,這種鋼的Ms和Md點符合于Md>20°C>Ms,即鋼的馬氏體轉變開始點低于室溫,而形變馬氏體點高于室溫。這樣,當鋼在室溫變形時便會誘發形變馬氏體,而馬氏體轉變又誘發了塑性。因而使這類鋼具有很高的強度和塑性。相變塑性的研究也推動了熱處理工藝的變革,使人們努力探求如何通過相變誘發塑性,而擬定出各種各樣的現代強韌化熱處理工藝。為發掘材料潛力及研制新鋼種服務。
四、馬氏體的物理性能
1.比容
由圖14示出的奧氏體和馬氏體的點陣常數隨碳含量的變化,可計算出馬氏體形成時比容增大。
▲圖14 奧氏體與馬氏體點陣常數
和鋼中碳含量的關系
馬氏體碳含量對比容的影響如圖15 所示。
▲圖15 馬氏體形成時比容的變化
馬氏體形成時比容的增大,造成鋼淬火時產生組織應力,從而促進馬氏體的顯微裂紋擴展。利用馬氏體形成時比容增大的現象,可以用膨脹法來測定馬氏體的轉變量以研究馬氏體轉變過程。
馬氏體的膨脹系數比奧氏體約小1/3,約為12~14x10E-6 mm/(mm·℃);奧氏體的膨脹系數為18x10E-6 mm/(mm·℃)。
2.磁性
奧氏體沒有鐵磁性,馬氏體有鐵磁性。馬氏體的磁飽和強度因碳含量的增高而減小。由于馬氏體組織具有很高的內應力,因而它的磁矯頑力很高。因此,也可以用磁性法來測量馬氏體的轉變量和殘留奧氏體的含量。
3.電阻
馬氏體是C在α-Fe中的過飽和固溶體,其電阻比珠光體大得多,與奧氏體的電阻相近。馬氏體碳含量越高,電阻越大,如圖16 所示。
▲圖16 淬火鋼的電阻率
免責聲明:本網站所轉載的文字、圖片與視頻資料版權歸原創作者所有,如果涉及侵權,請第一時間聯系本網刪除。
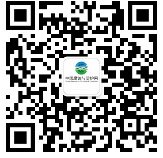
官方微信
《中國腐蝕與防護網電子期刊》征訂啟事
- 投稿聯系:編輯部
- 電話:010-62316606-806
- 郵箱:fsfhzy666@163.com
- 中國腐蝕與防護網官方QQ群:140808414