英國首先在80Ni-20Cr合金中加入少量鋁和鈦,形成γ'相(gamma prime)以進行強化,研制成第一種具有較高的高溫強度的鎳基合金。同一時期,美國為了適應活塞式航空發動機用渦輪增壓器發展的需要,開始用Vitallium鈷基合金制作葉片。 此外,美國還研制出Inconel鎳基合金,用以制作噴氣發動機的燃燒室。以后,冶金學家為進一步提高合金的高溫強度,在鎳基合金中加入鎢、鉬、鈷等元素,增加鋁、鈦含量,研制出一系列牌號的合金,如英國的"Nimonic",美國的"Mar-M"和"IN"等;在鈷基合金中,加入鎳、鎢等元素,發展出多種高溫合金,如X-45、HA-188、FSX-414等。由于鈷資源缺乏,鈷基高溫合金發展受到限制。 高溫合金材料的性能特征: Ø優秀的高溫強度及塑性 Ø良好的抗氧化性及抗熱腐蝕性 Ø優異的抗蠕變性能、抗裂變性能 Ø良好的組織穩定性 Ø變形加工困難 Ø具有較好的性能價格比 在高溫合金發展過程中,工藝對合金的發展起著極大的推進作用。 20世紀 40-50 年代初 20世紀 50年代 20世紀 60年代 高溫合金生產制備工藝較為復雜,熔煉、鑄造、熱處理為主要流程工藝。生產流程及工藝的穩定對高溫合金材料的力學性能產生直接影響。快速發展的經濟和科學技術為各種新型高溫合金材料的研發和推廣提供了較大的發展空間,在對合金性能要求越來越高的情況下,必須要對各種工藝進行不斷的完善和優化,保證各種工藝與高溫合金材料的變化相適應。工藝的不斷完善引入可實現性能的不斷提升,發展新型的高溫合金,進而推動相關產品與行業的發展。 高溫合金制備工藝 嚴格控制化學成分是保證高溫合金具備優異性能的基礎,熔煉工序能有效消除大于臨界尺寸的夾雜物,降低氧、氮、及硫的含量,從源頭上提高高溫合金的純凈度,因此熔煉工序在高溫合金的制備工藝中處于首要位置。 目前國際上高溫合金的熔煉方法主要有真空感應爐(VIM)、真空自耗爐(VAR)、電渣重熔爐(ESR)。近年以粉末高溫合金為代表的新型高溫合金應用領域愈加廣泛,粉末高溫合金的熔煉工藝成為前沿研究的技術,國際上俄羅斯粉末高溫合金采用VIM 或VIM+VAR 雙聯熔煉工藝,美國粉末高溫合金采用 VIM+ESR+VAR 三聯工藝,而國內粉末高溫合金基本采用 VIM 單煉工藝,導致我國粉末高溫合金材料純凈度低于國外先進水平。 高溫合金精密鑄造技術以熔模鑄造工藝為主,發展形成了等軸晶類型、定向柱晶與單晶類型的精密鑄造形式。目前高溫合金鑄件已經開始向著復雜化、大型化、高精確度化的方向發展,對鑄造工藝、流程形成一定的挑戰,也促使熔模精密鑄造技術不斷進步,從真空冶煉技術發展到無余量鑄造技術、定向凝固技術、單晶技術等方面。 定向合金組織 單晶 鑄造技術的提升與高溫合金原材料生產制造之間也存在直接的聯系,需要結合高溫合金材料特性、鑄件使用情況等,完善相應的工藝技術模式與機制,控制材料的性能,保證生產工藝穩定性。目前在生產的過程中,高溫合金的成分參數與凝固參數控制存在難點,很容易在定向凝固生產或是單晶生產期間出現雀斑、熱裂和疏松等缺陷,嚴重影響產品的高溫性能。美國在研究的過程中使用高梯度定向凝固技術進行航空發動機葉片的生產,有效降低了雀斑缺陷問題的發生率,嚴格控制各個零件尺寸條件下的溫度梯度參數,形成一定的生產優化、改良的作用。 精密鑄造分類:主要有熔模鑄造、陶瓷型鑄造、金屬型鑄造、壓力鑄造、消失模鑄造。 常用熔模鑄造基本流程: 固溶熱處理是指在高于高溫合金組織內析出相的全溶溫度,使合金中各種分布不均勻的析出相充分溶解至基體相中,從而實現強化固溶體并提高韌性及抗蝕性能,消除殘余應力的作用,以便繼續加工成型,并為后續時效處理析出均勻分布的強化相做準備。 時效熱處理是指在強化相析出的溫度區間內加熱并保溫一定時間,使高溫合金的強化相均勻地沉淀析出,碳化物等均勻分布,從而實現硬化合金和提高其強度的作用。 鑄造高溫合金是由合金錠重熔后直接澆注或定向凝固成零件的高溫合金 ,其發展始于20世紀40年代 。1943年美國首次在渦輪噴氣發動機 J-33上選用了 HS-21制作渦輪工作葉片,替代變形合金 Hastelloy-B的葉片,開創了航空發動機使用鑄造高溫合金的先例 。隨著航空發動機的發展,對高溫合金性能提出越來越高的要求 ,為 了提高熱強性能,在變形高溫合金中相繼加入了多種合金元素 ,導致變形加工 困難的問題,于是 ,航空和冶金工作者越來越重視鑄造合金的研究 。20世紀50年代 末 ,真空熔煉技術出現,合金中有害雜質和氣體去除,合金成分得到精確控制 ,高溫性能不斷提高,研制出 IN100,B1900,MAR-M200等多種性能優異的合金。20世紀60年代定向凝固技術的發展 ,促進了定向柱狀晶和單晶高溫合金的蓬勃發展 ,使航空發動機的使用溫度達到 1700℃ 以上 。 鑄造高溫合金不再考慮鍛造變形性能 ,可通過精密鑄造方法或定向凝固工藝鑄造出形狀復雜且有通暢內腔的無余量空心薄壁葉片。因此,鑄造高溫合金元素總量要顯著高于變形高溫合金 ,其中,固溶強化元素增添了 Re,Ru等元素,難熔金屬元素 w 的含量提高(有些 合金超過 10%)沉淀強化合金元素除 Al,Ti之外,還加入 Nb,Ta,Hf,V等元素。研究表明,鑄造高溫合金元素含量總和可達 50%,沉淀強化相 γ相含量達 60%-70%,此外,鑄造高溫合金粗大的晶粒和凝固偏析引起的枝晶骨架 以及 晶界和枝晶間形成的一次碳化物骨架,可有效地強化合金,因此,鑄造高溫合金持久強度、抗拉強度都明顯高于變形高溫合金。同成分的鑄造高溫合金要比變形高溫合金使用溫度提高 10-30℃,同時,加入更多的 合金元素也有利于開發新合金 。 鑄造高溫合金按凝固方法分類可分為等軸晶鑄造高溫合金、定向凝固柱晶高溫合金和單晶高溫合金三類。 1)等軸晶鑄造高溫合金 2)定向凝固柱狀晶高溫合金 定向凝固高溫合金是通過定向凝固技術制備出晶界平行于主應力軸從而消除有害橫向晶界的柱狀晶高溫合金。20世紀 60年代中期,美國PW公司發明了定向凝固工藝并用于生產鎳基合金柱狀晶渦輪葉片,可提高葉片工作溫度 500C。我國于20世紀 70年代開始定向凝固合金研究工作,到現在已研制出多種定向凝固柱狀晶高溫合金,并在多種型號的發動機上 使用,某些定向凝固合金葉片已開始批量生產。 定向凝固渦輪盤 3)單晶高溫合金 采用定向凝固工藝消除所有晶界的高溫合金稱為單晶高溫合金。20世紀80年代以來。隨著合金設計理論水平的提高,成分不斷改進,熔煉工藝優化,鑄造技術進步,使其力學性能的提高一再獲得突破,如今 ,單晶高溫合金已經發展到第五代。 典型鎳單晶高溫合金 單晶高溫合金中加入了大量 W,Mo ,Ta,Re,Ru等難熔金屬元素 ,其含量比同代次定向凝固柱狀晶合金都高。難熔金屬產生固溶強化 ,提高固溶溫度 ,時效時大量析出沉淀強化相γ相。第一代單晶高溫合金不含稀土金屬元素 Re,隨后 ,發現添加元素 Re后 80%原子能進入γ固溶體,引起較大的晶格畸變,20%的元素 Re直接進入γ相,提 高γ相的溶解度,增加γ相體積分數,從而提高合金承溫能力,而且 Re原子的加入有助于減小單晶晶粒缺陷和表面再結晶傾向。從第二代 單晶合金開始添加元素 Re, 3%Re和 6%Re是第二代和第三代單晶高溫合金的標志 ,但 Re原子加入會促進有害的 TCP相生成和次生反應區(SRZ)生成 , 降低組織穩定性 。第四代 和第五代單晶合金以分別加入 3%和 6% 的元素 Ru,抑制TCP相析出,增加合金組織穩定性。 第一至第五代單晶高溫合金在 137MPa,1000h 條件下的承溫能力 等軸晶、定向凝固及單晶 M-M200的蠕變和持久性能 變形高溫合金是指將鑄錠進行冷 、熱加工制成各種型材或 零件毛坯 ,最后制成熱端零件 的高溫合金 ,其關鍵是合金錠具有成形能力。變形高溫合金是最先用于航空發動機的高溫合 金 ,1939年英國首先研制成功 Nimonic75,1944年 Nimonic80A 正式使用 ,1956年中國發展了第一種變形高溫合金 GH3030,之后又相繼研制了GH4033等合金,經過 60多年的發展,全世界目前生產的變形高溫合金超過 200種 ,中國生產的變形高溫合金超過 70種 。 與鑄造高溫合金相比,變形高溫合金合金化程度低,因此 ,熔點較高,熱加工溫度上限較高 ,合金再結晶溫度較低 ,降低熱加工溫度下限,因此 ,變形高溫合金熱加工范圍較鑄造高溫合金寬。此外,變形高溫合金偏析較輕,合金組織中的γ析出相數量較少,變形抗力低 ,加工變形性能良好 ,因而可以通過熱加工和冷加工工藝制備出不同形狀的型材和零件毛坯 。 按基體元素的不同,變形高溫合金可分為鐵基變形高溫合金 、鎳基變形高溫合金和鈷基 變形高溫合金。 1)鐵基變形高溫合金 鐵基變形高溫合金是從奧氏體不銹鋼發展起來的。鐵基變形高溫合金Fe含量在 18%~45%,為穩定奧氏體,通常要入 25%-45%的元素Ni,也可加入適量的元素 Mn,N,C。代替部分元素 Ni。為保證合金有充分的抗氧化腐 蝕能力,鐵基變形合金中還加入 11%~23%的元素 Cr,所以鐵基高溫合金實際上是以 Fe-Ni-Cr三元系為基,當Ni含量大于40%時一般也稱作鐵鎳基高溫合金。鐵基高溫合金的基體通常有 Fe-15Cr-25Ni型、Fe-15Cr-35Ni型、Fe-15Cr-45Ni型。 常見鐵基變形高溫合 金的牌號、化學成分及使用溫度 鐵基變形高溫合金按其強化方式可分為三類 :第一類是碳化物 、氮化物或復合碳氮化物強化合金,其使用溫度在 550-600℃,現已逐漸被其他合金取代;第二類是固溶強化合金, 在高溫下有良好的抗氧化和抗腐蝕能力 ,使用溫度在 800~ 950℃,主要用作板材 ,制造承力不大但工作溫度較高的零件;第三類是金屬間化合物強化合金,使用溫度在 600-750℃。 鐵基變形高溫合金高溫力學性能 2)鎳基變形高溫合金 鎳為面心立方結構 ,從室溫到高溫沒有同素異構轉變 ,是一種非常良好的基體金屬,而且鎳化學穩定性良好 ,在 500℃以下幾乎不氧化 ,常溫下不受濕氣 、水及鹽類水溶液的作用。鎳基變形高溫合金通常加入 10%-25%的Cr元素,以保證合金具有良好的抗氧化腐蝕性能,所以鎳基合金實際上 以 Ni-Cr為基體。此外 ,有些合金在 Ni-Cr固溶體中加入元素 Co(15Yo-20%),Mo(約 15%)或 w (約 11%),分別構成 以 Ni-Cr-Co,Ni-Cr-Mo,Ni-Cr-W 為基體的三元系變形高溫合金。 中國常用鎳基變形高溫合金的牌號、化學成分及使用溫度 鎳基變形高溫合金高溫力學性能 3)鈷基變形高溫合金 鈷在 400℃以下具有密排六方結構 ,在高溫時會發生同素異構轉變為面心立方結構 ,且這種轉變具有非熱特性 ,在溫度循環過程中具有可逆性 ,為使鈷基合金具有穩定面心立方 構的γ奧氏體 ,通常加入 5%-25%的鎳或 9%-20%的鐵 ,此外 ,還通常加入 20%左右的元素 Cr,以便在合金表面形成防護性能良好的 Cr203氧化膜來提高鈷基變形高溫合金的抗氧化性能和抗腐蝕性能。所以,鈷基變形高溫合金實質上是以Co-Ni-Cr三元系為基,另含 W,Mo,Nb,Ta等固溶強化元素和碳化物形成元素。 部分鈷基變形高溫合金的化學成分 (質量分數) 鈷基變形高溫合金與鎳基變形高溫合金相比,其加工硬化速率較大,零件成形后的表面質量較好 ,但在成形過程中,一般需要較多的熱加工加熱火次或冷變形中間退火次數 ,其加工成形設備的噸位也要求較大。鈷基變形高溫合金在高于 980℃時 ,其強度很高 ,抗熱疲勞、熱腐蝕和耐磨腐蝕性優異,但是,鈷基變形高溫合金以碳化物為主要強化相,缺少共格類的強化相,在較低和中等溫度范圍內持久強度比鎳基變形高溫合金低。 鈷基變形高溫合金高溫力學性能 隨著高溫合金工作溫度和強度的不斷提高以及綜合性能的改善,合金中強化元素含量不斷增加 ,成分越來越復雜,熱加工性能變得很差 ,不少高性能鎳基高溫合金已不能熱加工變形 ,只能以鑄態使用 。然而 ,由于鑄造組織偏析嚴重導致了顯微組織的不均勻和力學性能的波動,故而開始采用粉末冶金工藝生產高溫合金克服上述缺點 ,得到幾乎無偏析、組織均勻、熱加工性能良好的高溫合金材料。粉末高溫合金是先進航空發動機關鍵熱端部件的優選材料,主要用于制造渦輪盤、壓氣機盤、鼓筒軸、渦輪盤、高壓擋板等發動機熱端高溫承力轉動部件。目前,用粉末冶金法制得的高溫合金可分為普通粉末 (powdermetallurgy, PM)高溫合金和氧化物彌散強化 (oxidedispersionstrengthened,ODS)高溫合金兩類。目前,已經研制了四代粉末高溫合金,制備出的渦輪盤等多種粉末高溫合金關鍵零部件已成 功應用于先進航空發動機 。 1)普通粉末高溫合金 粉末高溫合金的工藝流程大致如下 :制備粉末~ 固實~熱加工變形 ~熱處理。粉末的質量嚴重影響著粉末高溫合金的性能 ,通常要求粉末的氣體含量及夾雜物含量低 ,粒度分布及形狀合適。高溫合金粉末的制備方法主要有惰性氣體霧化法、旋轉電機法和真空霧化法三種。惰性氣體霧化法應用最廣泛 ,在整個真空及密閉的設備中,經真空熔煉的合金熔體經注口流下,在高壓高速的氣流中霧化成粉末。所用的氣體通常是氬氣,所得粉末中氣體含量約為40-200μg/g,粉末主要呈球狀,也有一些空心顆粒、串狀顆粒或片狀顆粒,粒度分布較寬 ,有粗大的也有特別細小的顆粒 ,需經篩分后再集取 。 粉末高溫合金的性能強烈地受制粉、固實化工藝的影響,不 同制粉工藝的粒度分布差異對合金的晶粒和性能有一定的影響 ,在熱等靜壓合金中能表現出來,但在熱擠壓合金中破碎完全,已顯示不出粒度分布的影響。 部分美國、歐洲的粉末冶金高溫合金的化學成分與性能 部分俄羅斯研發的粉末高溫合金成分及性能 部分中國的粉末冶金高溫合金化學成分與性能 中國研制的三種渦輪盤粉末冶金高溫合金性能 2)氧化物彌散強化高溫合金 氧化物彌散強化高溫合金(ODS)是將細小的氧化物顆粒 (一般選用 Y203)均勻地分散于高溫合金基體中,通過阻礙位錯運動而產生強化效果的一類合金。機械合金化工藝的發明是ODS高溫合金發展史上的一個里程碑 ,機械合金化是在高能 球磨機內完成的,常用的高能球磨機有攪拌式、振動式和滾筒式三種。 幾種典型的ODS鎳基高溫合金 ODS高溫合金力學性能最大的特點是高溫強度 。加入的氧化物顆粒 Y203具有很高的熔點 (2417℃),且不與基體發生反應,所以具有非常好的熱穩定性和化學穩定性,其強化作用可以維持到接近合金的熔點溫度,因此,ODS高溫合金的使用溫度可以達到 0.9Tm。 目前國內外已生產和研制的 ODS高溫合金主要有三類: 國際上高溫合金的研制始于上世紀二三十年代,主要在英美俄等國家展開。目前, 世界范圍內僅有不超過 50 家企業具備生產高性能高溫合金的能力,主要集中在美英法德等歐美國家,整個行業頭部效應明顯。 國際知名的高端高溫合金生產國家和企業主要有美國的通用電氣公司、普拉特-惠特尼公司、佳能-穆斯克貢公司、漢因斯·司泰特公司、國際因科合金公司等,以及英國的國際鎳公司、日本的 JFE 鋼鐵株式會社、新日鐵住金株式會社、神戶制鋼等。這些企業經過多年的技術積累,均已建立了完善的企業級的高溫合金工藝、性能體系、過程控制及選材標準,生產的高溫合金具有成本低、質量高且穩定性好等優勢。 國內高溫合金起步較晚,初期以仿制為主,目前已建立較為完備的產品體系。由于高溫合金主要運用于航空航天、核電等戰略核心領域,因此作為高精尖產品,國外廠商管控嚴格,很少出口銷售。國內高溫合金行業從 20 世紀 50 年代末仿制前蘇聯高溫合金體系開始,經過 60 余年的發展,經歷了由仿制到仿創結合再到獨創的發展歷程,形成了我國獨特、系統、完整的高溫合金體系,是國際上公認的四大較完整的高溫合金體系之一。 我們把國內從事高溫合金的廠家分為四類: 目前,國內規模較大的高溫合金生產企業有撫順特鋼和鋼研高納。此外,寶鋼特鋼、攀長鋼、中科院金屬所、北京航材院也具備一定的產能。 目前具備鑄造高溫合金精鑄件的廠家分為兩類,一類是鋼研高納、中科院金屬所和北京航材院三家公司;另一類是黎明、西航、南方、成發等專業發動機廠自行生產精鑄件。三家單位主要承接航天航空發動機廠對外委托的精鑄件業務。目前三家單位在鑄造高溫合金的材料制備、生產技術上均有各自特點,其中鋼研高納產能大于其余兩家。 高溫合金全球市場持續成長,中國成為主要增量市場。我國高溫合金市場中,變形高溫合金和鎳基高溫合金占比最大,根據制造工藝,變形高溫合金約占整個高溫合金市場 70%左右,其次是鑄造高溫合金(20%)和粉末高溫合金(10%);根據合金基體元素,鎳基高溫合金占比達 80%左右,鎳-鐵高溫合金和鈷基高溫合金 占比分別約為 14%和 6%。 高溫合金第一大應用場景是航空航天領域,需求份額占比為 55%。高溫合金材料是航天航空發動機的重要制造原材料,主要應用于發動機的燃燒室、導向器、渦輪葉片、渦輪盤、尾噴口及機匣等部件。其次,高溫合金具備耐高溫、耐腐蝕等優良性能,也被廣泛應用于燃氣輪機、石油化工、工業和汽車領域等場景。 1)航空發動機 高溫合金從誕生起就應用于航空發動機,在現代航空發動機中,高溫合金材料主要用于四大熱端部件:燃燒室、導向室、渦輪葉片和渦輪盤,此外還用于機匣、環件、加力燃燒室和尾噴口等部件。 2)汽車渦輪增壓器 汽車廢氣增壓器渦輪也是高溫合金材料的重要應用領域。目前,我國渦輪增壓器生產廠家所采用的渦輪葉輪多為鎳基高溫合金渦輪葉輪,它和渦輪軸、壓氣機葉輪共同組成一個轉子。根據每萬輛汽車渦輪增壓器高溫合金用量約為 3.5 噸,2021 年汽車生產行業需要高溫合金材料約 9128.7 噸,市場規模約為 18.3 億元。考慮到未來汽車數量和我國裝配率的提高,假設未來年均增長率為 5%,預計到 2030 年我國汽車市場對高溫合金材料的需求總計約為 10.6 萬噸。 3)核電領域 核電用高溫合金包括:燃料元件包殼材料、結構材料和燃料棒定位格架,高溫氣體爐熱交換器等,均是其他材料難以代替的。 世界核能協會發布的核燃料報告預測, 全球核電裝機容量預計將以每年 2.6%的速度增長,到 2040 年全球核電裝機容量將達到 61500 萬千瓦,且裝機容量增長將主要來自中國、俄羅斯等國家。2022 年 1 月,隨著福清核電站 6 號機組并網發電,我國大陸并網核電機組達到 53 臺,總裝機容量 5463.695 萬千瓦,僅次于美國與法國,位居世界第三位。國家能源局預計,我國核電裝機規模將在 2030 年達到 1.2 億~1.5 億千瓦,因此估計截至 2030 年 我國還將新建設完成約 8000 萬千瓦的核電機組。每座 60 萬千瓦核電站約需高溫合金材料 600 噸,以此計算,共需高溫合金材料約為 80000 噸,考慮到核電站建設國產率約為 80%,預計未來平均每年高溫合金國內需求量約 為 7111 噸。 4)其他領域 高溫合金材料在玻璃制造、冶金、醫療器械等領域也有著廣泛的用途。
免責聲明:本網站所轉載的文字、圖片與視頻資料版權歸原創作者所有,如果涉及侵權,請第一時間聯系本網刪除。
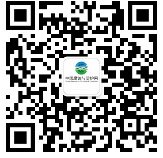
官方微信
《腐蝕與防護網電子期刊》征訂啟事
- 投稿聯系:編輯部
- 電話:010-62316606-806
- 郵箱:fsfhzy666@163.com
- 腐蝕與防護網官方QQ群:140808414