導語
國內某核電廠安全噴淋泵外筒體與底板連接螺柱在安裝完成20h后斷裂。該螺柱材料為X6CrNiCu17-04時效硬化馬氏體鋼雙頭螺柱,規格為M36×110mm。該批螺柱按規定進行了固溶加時效處理,其中固溶溫度為1050℃,保溫時間為4h,油冷;時效硬化處理溫度為(610±5)℃,保溫時間為4h,空冷。固溶、時效硬化溫度曲線均符合規范要求。研究人員采用宏觀觀察、化學成分分析、力學性能測試、金相檢驗、掃描電鏡(SEM)和能譜分析等方法對該螺柱的斷裂原因進行分析,以防止該類問題再次發生。
01理化檢驗
1.1 宏觀觀察
斷裂螺柱整體及斷口宏觀形貌如圖1所示,該螺柱斷裂于螺紋位置,斷口潔凈且較平齊,無明顯的塑性變形,斷口表面呈結晶顆粒狀,由中心向周圍呈明顯的放射棱線特征,外側邊緣存在微小的剪切唇邊,中心區及放射區域的面積之和占斷口總面積的90%以上,該斷口為典型脆性斷口。
1.2 化學成分分析
采用ICP-AES型電感耦合等離子體原子發射光譜儀對斷裂螺柱進行化學成分分析,結果如表1所示。其中采用惰性氣體熔融熱導法測量氫元素,從螺栓上取約1g試樣,浸在四氯化碳溶液中,之后用超聲波清洗試樣,風干后將試樣放入經脫氣的石墨坩堝中,在質量分數為99.99%以上的氬氣保護下加熱熔融,釋放出的氫氣分子進入載流氣體中,經色譜柱與氣體分離后,在熱導池中進行檢測,根據熱導率的信號變化,計算出氫含量。由表1可知:該批螺柱的化學成分均符合RCC-MM5110《壓水堆核島機械設備設計和建造規則》的要求,尤其是S、P等有害雜質元素的含量均滿足標準要求,但氫含量較高,斷裂螺柱中H的質量分數達到了0.00046%,明顯偏高,也顯著高于未斷裂螺柱中氫的質量分數。
1.3 力學性能測試
對螺柱進行布氏硬度測試,在距螺紋末端1倍直徑處截取試樣,用砂紙磨光試樣表面,并拋光。測試設備為數顯布氏硬度計,試驗條件為:載荷為187.5kg,鋼球直徑為2.5mm,載荷保持時間為10s,壓痕直徑的測量精確到0.005mm。斷裂螺柱硬度實測值分別為376,376,395,388HB,平均值為383.7HB;同批次未斷裂螺柱硬度實測值分別為339,341,344,342HB,平均值為343.5HB。
布氏硬度測試結果表明,該批次螺柱的布氏硬度滿足RCC-MM5110標準對相應鋼種的要求(≥302HB),但都顯著高于標準規定的下限值,同時斷裂螺柱硬度明顯高于同批次未斷裂螺柱。
選取同批次未斷裂螺柱進行室溫拉伸試驗,加載位移速率為2mm/min,試驗精度為±0.5%。同批次試樣的室溫拉伸試驗結果如表2所示。由表2可知:同批次試樣室溫抗拉強度和屈服強度滿足RCC-MM5110標準對X6CrNiCu17-04鋼材料的要求,其中屈服強度和抗拉強度較高,分別達到了970MPa和1200MPa,斷后伸長率和斷面收縮率滿足標準要求,但裕度不大。
1.4 金相檢驗
依據GB/T13299—1991《鋼的顯微組織評定方法》及GB/T10561—2005《鋼中非金屬夾雜物含量的測定標準評級圖顯微檢驗法》在斷裂螺柱上分別取樣,將試樣置于光學顯微鏡下觀察,結果如圖2所示。
斷裂螺柱以及同批次未斷裂螺柱基體的顯微組織均為回火馬氏體+少量鐵素體,不存在異常硬脆組織,晶粒度為6~7級,非金屬夾雜等級也在設計范圍內。
1.5 掃描電鏡和能譜分析
進一步對斷裂螺柱金相試樣進行掃描電鏡及能譜分析,斷裂螺柱存在較為明顯的成分偏析帶,結果如圖3所示。
對偏析帶和基體分別進行能譜分析,結果如圖4所示。由圖4可知:成分偏析區域除C元素含量明顯比基體高,其他主元素含量與基體相當。
將斷裂螺柱斷口試樣置于掃描電鏡下觀察,結果如圖5,6所示。由圖5可知:斷口整體較為平整,沒有明顯的塑性變形,整個斷口呈放射狀脆斷形貌特征,可明顯分為起裂區、裂紋擴展區和終斷區,斷口起裂位置為螺柱心部,并由心部向四周放射狀擴展,起裂區呈典型的沿晶特征,晶面伴有爪狀紋。
由圖6可知:斷口擴展區以沿晶斷裂為主,并有少量韌窩;終斷區呈韌窩個別撕裂特征,面積非常小,該斷口呈典型的脆性斷裂特征。
02綜合分析
斷裂螺柱材料為X6CrNiCu17-04沉淀硬化馬氏體不銹鋼,金相檢驗結果表明其組織主要為馬氏體,馬氏體中滑移系較少,相比于其他組織,其對氫脆更為敏感。該螺柱在安裝過程中并未發生斷裂,但放置一段時間后才出現斷裂現象,具備典型延時斷裂的特征。該批螺柱在制造階段要經過酸洗,從而引入大量氫,后期除氫不完全導致較多的氫滯留在螺柱內。化學成分分析結果表明:發生斷裂螺柱中氫元素的質量分數較高,達到0.00046%。大量氫原子會向缺陷多的應力集中部位擴散并聚集,使缺陷處氫元素含量增大,大量氫原子形成更為穩定的氫分子,而氫分子的比容很大,故體積膨脹造成巨大的內應力,材料的斷裂應力下降,應力集中部位形成裂紋,裂紋逐漸擴展,直至材料發生斷裂。
通常中強度鋼中氫元素質量分數達到0.00003%,高強度鋼中氫元素質量分數達到0.00001%就可以大大增加氫脆敏感性。力學性能分析也表明:該批螺柱強度普遍偏高,屈服強度和抗拉強度分別高達970MPa和1200MPa,屬于典型的高強度螺柱。斷裂螺柱硬度顯著高于未斷裂螺柱,螺柱硬度和強度越高,所受應力越大,則氫脆敏感性就越高。從斷裂螺柱宏觀形貌上看,該螺柱斷裂于螺紋位置,斷口潔凈且較平齊,無明顯的塑性變形,斷口表面呈結晶顆粒狀,由中心向周圍呈明顯的放射棱線特征,為典型脆性斷口。起裂區晶面上伴有爪狀紋,這是典型的氫脆斷口形貌,金相檢驗發現斷裂螺柱心部存在偏析缺陷,在服役條件下,螺柱處于較高應力狀態,在力的作用下氫元素向應力集中處或偏析缺陷處快速擴散和聚集,從而加速了螺柱的氫致延遲斷裂。
03結論及建議
斷裂螺柱發生的是典型的氫致延遲斷裂,該批螺柱的硬度、屈服強度和抗拉強度較高,增強了氫脆的敏感性。斷裂螺柱心部存在偏析缺陷,且斷裂螺柱中氫元素質量分數高達0.00046%,在應力作用下氫元素極易在偏析缺陷處擴展和聚集,從而加速了螺柱的斷裂。建議對該類馬氏體高強度外螺紋緊固件的加工和表面處理過程中,選用氫脆風險最小的生產工藝,并采取有效的方法和措施避免氫脆斷裂的發生。
免責聲明:本網站所轉載的文字、圖片與視頻資料版權歸原創作者所有,如果涉及侵權,請第一時間聯系本網刪除。
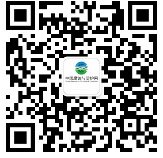
官方微信
《腐蝕與防護網電子期刊》征訂啟事
- 投稿聯系:編輯部
- 電話:010-62316606
- 郵箱:fsfhzy666@163.com
- 腐蝕與防護網官方QQ群:140808414