金屬磨損是機械工程和材料科學中的一個重要研究領域。金屬磨損是指金屬表面在摩擦或接觸過程中,由于機械或化學作用導致材料逐漸喪失的現象。磨損是影響金屬材料使用壽命和性能的關鍵因素之一。了解磨損的基礎知識對于材料選擇、設計和維護非常重要。本期內容主要是分享金屬磨損的基礎知識和影響因素,學習適當的控制措施提高金屬部件的使用壽命和性能。 金屬磨損概述 金屬摩擦表面相互接觸過程中,表面不斷發生損耗或產生塑性變形,使金屬表面狀態和尺寸發生改變的現象稱為磨損。磨損導致的材料損失可能以磨屑、碎片或顆粒的形式表現出來。在摩擦載荷作用下,金屬表面性質(金相組織、物理化學性能、力學性能)和形狀的(形貌和尺寸、粗糙度、表面層厚度)會發生變化。 通常磨損過程是一個漸進的過程,正常情況下磨損直接的結果也并非災難性的。金屬磨損研究在材料科學與工程、機械工程和表面工程等領域均有涉及,各個學科的交叉和合作在磨損研究中也顯得尤為重要,有助于全面理解和解決磨損問題。但從材料學科特別是從材料的工程應用來看,人們更重視研究材料的磨損。 圖1 磨損行為的學科交叉性 金屬磨損并非單一的力學過程。引起磨損的原因既有力學作用,也有物理和化學作用,因此,摩擦副材料、潤滑條件、加載方式和大小、相對運動特性(方式和速度)以及工作溫度等諸多因素均影響磨損量的大小,所以,磨損是一個復雜的系統過程。 磨損是材料五類失效模式之一,造成的損失也 是巨大的。據統計,在失效的零部件中,80%以上 是由各種形式的磨損或腐蝕引起的。就一個國家而言,每年因摩擦磨損造成的經濟損失一般占GDP的1%以上。 在機械的正常運轉中,磨損過程大致可分為三個階段,如圖2所示。 圖2 金屬磨損特性曲線 (1)跑合(磨合)磨損階段 特點:這一階段中,磨損速度由快變慢,而后逐漸減小到一穩定值。這是由于新加工的零件表面呈尖峰狀態,使運轉初期部件的實際接觸面積較小,單位接觸面積上的壓力較大,因而磨損速度較快,如圖1中磨損曲線的Oa段。跑合磨損到一定程度后,尖峰逐漸被磨平,磨損速度即逐漸減慢。 (2)穩定磨損階段 特點:在這一階段中磨損緩慢、磨損率穩定,零件以平穩而緩慢的磨損速度進入零件正常工作階段,如圖2中的ab段。這個階段的長短即代表零件使用壽命的長短,磨損曲線的斜率即為磨損率,斜率越小磨損率就越低,零件的使用壽命就越長。經此磨損階段后零件進入劇烈磨損階段。 機制: 磨粒磨損:硬質顆粒或突起在表面滑動或滾動,產生劃痕和切削作用。 腐蝕磨損:環境中的化學或電化學反應導致金屬表面生成腐蝕產物,這些產物在機械作用下被移除。 疲勞磨損:由于循環應力作用,表面或亞表面材料產生疲勞裂紋,導致材料剝落。 (3)劇烈磨損階段 特點:此階段的特征是磨損速度及磨損率都急劇增大。當工作表面的總磨損量超過機械正常運轉要求的某一允許值后,零件的磨損加劇,精度下降,潤滑狀態惡化,溫度升高,從而產生振動、沖擊和噪聲,導致零件迅速失效,如圖2中的bc段。 機制: 疲勞裂紋擴展:由于累積的疲勞損傷,裂紋繼續擴展并最終導致材料剝落。 磨損產物的堆積:磨損產生的顆粒堆積在接觸表面,增加磨粒磨損和粘著磨損的程度。 表面溫度升高:摩擦熱積累導致表面溫度升高,材料軟化和氧化加劇,加速磨損。 上述磨損過程中的三個階段,是一般機械設備運轉過程中都存在的。必須說明的是,在跑合階段結束后應清洗零件,更換潤滑油,這樣才能正常地進入穩定磨損階段。 耐磨性是材料抵抗外部磨損的性能,這是一個系統性質。迄今為止,還沒有一個統一的、意義明確的耐磨性指標,表征金屬的耐磨性需要綜合使用各種磨損測試方法和分析技術,包括磨損試驗、磨損量測量和表面分析等。 (1)磨損測試方法 可通過磨損試驗機、磨粒磨損試驗、腐蝕磨損試驗等評估材料的耐磨性能。 (2)磨損量 在規定條件下,經過規定時間的磨損后,樣品表面的損耗程度稱為磨損量(W)。磨損量可通過測量長度、體積或質量的變化而得到,并相應稱它們為線磨損量、體積磨損量和質量磨損量。 若測量單位摩擦距離、單位壓力下的磨損量等,則稱為比磨損量。磨損量越小,耐磨性越高。 (3)耐磨性 磨損量的倒數稱為耐磨性,即ε=1/W。ε值越大,材料的磨損抗力越大。 (4)相對耐磨性 指在同樣條件下,標準試樣(Pb-Sn合金)的磨損量與被測試樣磨損量的比值稱為相對耐磨性。相對耐磨性的倒數稱為磨損系數。 (5)磨損表面分析 可選擇光學顯微鏡、掃描電子顯微鏡、能譜分析、X射線衍射等儀器設備了解磨損過程中材料的變化和機理。 ASTM G99:銷-盤磨損試驗標準。 ASTM G65:干砂橡膠輪磨損試驗標準。 ASTM D4172:四球磨損試驗標準。 ISO 20808:陶瓷材料的球-盤磨損試驗標準。 金屬的磨損類型 通常,按照磨損機理和磨損系統中材料與磨料、材料與材料之間的作用方式劃分,磨損的主要類型可分為磨料磨損、粘著磨損、腐蝕磨損和疲勞磨損(接觸疲勞)四種基本類型。但磨損過程十分復雜,有許多實際表現出來的磨損現象不能簡單地歸為某一種基本磨損類型,而往往是基本類型的復合或派生,如氣蝕磨損、沖蝕磨損和微動磨損等。 一、粘著磨損 粘著磨損是指當兩個金屬表面在相對運動時,由于局部接觸區域的粘著作用,導致材料從一個表面轉移到另一個表面的磨損現象。這種磨損通常發生在金屬表面具有相似硬度和化學成分的情況下。 粘著磨損一般是在滑動摩擦條件下,當摩擦副相對滑動速度較小(鋼小于1m/s)時發生的,例如,內燃機中的活塞環和缸套襯這一運動的摩擦副,如不考慮燃氣介質的腐蝕性,主要表現為粘著磨損。 粘著磨損的過程主要包括以下幾個步驟: 接觸和粘著: 當兩個表面相互接觸時,由于局部壓力和摩擦熱的作用,接觸點的溫度升高,導致表面材料發生微觀的粘著和局部熔化。 在高壓力區域,原子間的相互作用力使表面材料發生粘著。 相對運動和剪切: 在外力的作用下,兩個表面發生相對運動,粘著點被拉伸和剪切。 由于相對運動,粘著點破裂,部分材料從一個表面轉移到另一個表面,形成磨屑。 磨屑的形成和脫落: 被剪切和拉伸的粘著點最終斷裂,形成微小的磨屑。 這些磨屑在進一步的相對運動中被帶走或殘留在表面,導致表面進一步磨損。 粘著磨損機理如圖2所示。粘著磨損的磨損表面形貌為錐刺、鱗尾、麻點等,如圖3所示。 圖2 粘著磨損機理示意圖 圖3 粘著磨損的失效形貌 粘著磨損按程度不同可分為五級:輕微磨損、涂抹、擦傷、撕脫、咬死。如氣缸套與活塞環、曲軸與軸瓦、輪齒嚙合表面等,皆可能出現不同粘著程度的磨損。涂抹、擦傷、撕脫又稱為膠合,往往發生于高速、重載的場合。 材料特性、法向力、滑動速度以及溫度等均對粘著磨損有明顯影響。 塑性材料比脆性材料易于粘著;互溶性大的材料(相同金屬或晶格類型、點陣常數、電子密度、電化學性質相近的金屬)組成的摩擦副粘著傾向大;單相金屬比多相合金粘著傾向大;化合物比固溶體粘著傾向小;金屬與非金屬組成的摩擦副比金屬與金屬的摩擦副不易粘著。 在摩擦速度一定時,粘著磨損量隨法向力增大而增加。試驗指出,當接觸壓應力超過材料布氏硬度的1/3時,粘著磨損量急劇增加,嚴重時甚至會產生咬死現象。因此,設計選材的許用壓應力必須低于材料布氏硬度值的1/3,以免產生嚴重的粘著磨損。 在法向力一定時,粘著磨損量隨滑動速度增加而增加。但達到某一極大值后又隨滑動速度增加而減小,如圖4所示。這可能是由于滑動速度增加時,接觸表面溫度升高,材料剪斷強度下降,使粘著磨損量增加,而滑動速度過大又使塑性變形不能充分進行而延緩了粘著點的長大,使磨損量減小。 圖4 磨損量與滑動速度的關系 防止或減少粘著磨損須從設計、選材、潤滑和加工工藝等方面來綜合采取措施。 首先,注意摩擦副配對材料的選擇。其基本原則是配對材料的粘著傾向應比較小,如選用互溶性小的材料配對;選用表面易形成化合物的材料配對;在受力較小時,選用金屬與高分子材料配對等。在滑動軸承中,選用淬火鋼軸與錫基或鋁基軸瓦配對。 其次,因為磨損發生在表層,所以最經濟有效的方法是提高零件表面的耐磨性,如采用表面熱處理、化學熱處理、電鍍、噴涂、堆焊、表面覆膜技術和離子注入技術等。 此外,控制摩擦滑動速度和接觸壓應力,可使粘著磨損大為減輕。降低摩擦副表面粗糙度和摩擦表面溫度,改善潤滑狀態等都可降低粘著磨損量。 二、磨料磨損 運動的硬顆粒使被摩擦的構件表面產生破損而 分離出磨屑或劃傷的磨損現象,稱為磨粒磨損,又稱磨料磨損。磨粒磨損很少是由一種單一的磨損機制引起的,常常是多種磨損機制的相互作用,并隨磨損條件的變化從一種磨損機制轉變為另一種磨損機制。 圖5 磨粒磨損的四種機制 磨料磨損是最常見的、同時也是危害最為嚴重的磨損形式。在各類磨損形式中,磨料磨損大約占總消耗的50%。 (1)磨料磨損機理 磨料磨損可能是磨粒對摩擦表面產生的切削作用、塑性變形和疲勞破壞作用或脆性斷裂的結果,還可能是它們綜合作用的反映,并以某一損壞方式為主。磨粒磨損的主要特征是摩擦面上有明顯犁皺形成的溝槽或磨屑,如圖6所示。 圖6 磨粒磨損表面的犁溝和磨屑(SEI) a)犁溝;b)磨屑 當磨料硬度較高且棱角尖銳時,磨料猶如刀具一樣,在切應力作用下,對金屬表面進行切削。這些切削一般較長而深度較淺。實際上,磨料形狀一般比較圓鈍,而且材料表面塑性較高,磨料在材料表面滑過后只能犁出一條溝槽來,使兩側金屬發生塑性變形而堆積起來,在隨后的摩擦過程中,這些被堆積部分又被壓平,如此反復地塑性變形,導致裂紋形成而引起剝落。因此,這種磨損實際上是疲勞破壞過程。硬而脆的材料遇到磨粒磨損時,由于磨料不易刺入材料使材料發生塑性變形,更不易被切削,這時材料常常是以脆性斷裂、微觀剝落的機制發生遷移,宏觀上便是發生了磨損。 圖7 三種不同形式的磨粒磨損形貌 (2)影響磨料磨損的因素 磨料磨損的影響因素很多,十分復雜,還包括了外部載荷、磨料硬度和顆粒大小、相對運動情況、環境介質以及材料組織和性能等。影響磨料磨損的因素有零件材料的內部因素和磨粒等的外部因素。 材料的硬度是影響磨料磨損最大的因素。一般來說材料的硬度(正確地說是材料磨損后的表面硬度)越高,則耐磨性越高。對純金屬和退火鋼,耐磨性大致與硬度成正比。經熱處理的鋼,其耐磨性也隨著硬度的提高而提高,只是提高的程度稍低。對于像石英和陶瓷等硬度很高的材料,硬度過高后耐磨性反而下降,這是由于斷裂韌度下降,容易發生脆性碎裂使磨損增大。 外部因素中影響較大的是零件材料硬度Hm與磨粒硬度Ha的比值。當Hm/Ha>0.8時,零件材料的耐磨性迅速提高;當Hm/Ha<0.8時,零件材料的耐磨性低。前者稱為軟磨料磨損,后者稱為硬磨料磨損。因此,要提高材料的耐磨性,材料的硬度必須大于磨粒硬度80%,這是選擇材料的一個比較關鍵性問題。 此外,磨料的粒度、幾何形狀和組成等對磨損也有影響。 提高零件耐磨料磨損性能的方法,首先是選擇材料。對于以切削作用為主要機理的磨粒磨損應增加材料硬度,材料的硬度必須大于磨料硬度80%,可使磨損量減得很小,這是提高耐磨性的最有效措施。如選擇中、高碳鋼和含鉻、錳的合金鋼淬火獲得馬氏體組織,采用高錳鋼、普通白口鑄鐵、合金白口鐵、粉末冶金減摩和耐磨材料、金屬陶瓷、陶瓷等,都可得到高硬度和高耐磨性。但如果磨料磨損機理是塑性變形,或塑性變形后疲勞破壞(低周疲勞)、脆性斷裂,則提高材料韌性對改善耐磨性是有益的。 其次,采用表面熱處理和化學熱處理,或用硬合金表面堆焊、熱噴涂和其他表面涂覆方法,也能有效地提高磨料磨損耐磨性。另外,經常注意工件防塵和清洗,加裝防護密封裝置等,防止大于1μm磨粒進入接觸面也是有效的措施。 三、腐蝕磨損 腐蝕磨損是指摩擦副表面在相對滑動過程中,表面材料與周圍介質發生化學或電化學反應,并伴隨機械作用而引起的材料損失現象稱為腐蝕磨損。腐蝕磨損因常與摩擦面之間的機械磨損(粘著磨損或磨粒磨損)共存,故又稱腐蝕機械磨損。 腐蝕磨損通常是一種輕微磨損,但在一定條件下也可能轉變為嚴重磨損。常見的腐蝕磨損有氧化磨損、特殊介質腐蝕磨損、沖蝕磨損等。 除金、鉑等少數金屬外,大多數金屬表面都被氧化膜覆蓋著,純凈金屬瞬間即與空氣中的氧起反應而生成單分子層的氧化膜,且膜的厚度逐漸增長,增長的速度隨時間以指數規律減小,當形成的氧化膜被磨掉以后,又很快形成新的氧化膜,隨后又再被磨去。如此,氧化膜形成又被除去,工件表面逐漸被磨損,這就是氧化磨損,可見氧化磨損是由氧化和機械磨損兩個作用相繼進行的過程。 氧化磨損的磨損速率最小,其值僅為0.1~0.5μm/h,屬于正常類型的磨損。氧化磨損的宏觀特征是,在摩擦面上沿滑動方向呈勻細磨痕,鋼鐵氧化磨損產物或為紅褐色的Fe2O3,或為灰黑色Fe3O4。一般情況下氧化膜能使金屬表面免于粘著,氧化磨損一般要比粘著磨損緩慢,因而可以說氧化磨損能起到保護摩擦副的作用。 在金屬部件與酸、堿、鹽等特殊介質發生化學腐蝕的情況下而產生的磨損,稱為特殊介質腐蝕磨損。其磨損機理與氧化磨損相似,但磨損率較大,磨損痕跡較深。金屬表面也可能與某些特殊介質起作用而生成耐磨性較好的保護膜。 為了防止和減輕腐蝕磨損,可從表面處理工藝、潤滑材料及添加劑的選擇等方面采取措施。 沖刷磨損是指流體或固體以松散的小顆粒按一定的速度和角度對材料表面進行沖擊所造成的磨損。松散粒子尺寸一般小于100μm,沖擊速度在550m/s以內。根據攜帶粒子的介質不同,沖刷磨損又分為氣固沖刷磨損、流體沖刷磨損、液滴沖刷磨損和氣蝕磨損,氣固沖刷磨損又稱噴砂型沖刷磨損,是最常見的沖刷磨損。 圖8 沖刷磨損機理 在沖刷磨損過程中,表面材料流失主要是機械力引起的。在高速粒子不斷沖擊下,塑性材料表面逐漸出現短程溝槽和魚鱗狀小凹坑(沖蝕坑),且變形層有微小裂紋。 圖9 典型韌性材料的沖刷磨損形貌 腐蝕磨損的破壞作用大大超過單純的腐蝕或磨損。一般金屬潔凈表面與空氣接觸后生成氧化膜,多數金屬表面氧化膜的厚度為0.01μm。當磨損速度低于氧化膜厚度的增長速度時,氧化和磨損尚不相互促進,膜層可起保護作用。當磨損速度超過氧化速度,腐蝕磨損便變得劇烈。但氧化膜又不宜過厚,否則易于脆性斷裂,形成硬的氧化物磨粒,使磨損加速。腐蝕磨損與環境、溫度、滑動速度、載荷和潤滑條件有關,相互關系極為復雜。如內燃機軸承在濕空氣中容易生銹,在潤滑劑中工作也常會出現腐蝕磨損。在特殊介質中工作的選礦機械和化工機械等的零件更常出現嚴重的腐蝕磨損。防止腐蝕磨損應從選材(如用不銹鋼和耐蝕合金等)、表面保護處理、降低表面工作溫度和選擇適當的潤滑劑等入手。 四、微動磨損 兩個接觸物體表面間沒有發生宏觀的相對運動, 但在載荷作用下產生小振幅相對振動(一般小于 100um), 接觸表面所產生的磨損稱為微動磨損。如圖10中的緊配合軸,在反復彎曲時,二配合面產生軸向相對滑動,滑動量從配合面內至邊緣逐漸增大,約為2~20μm,長期運行后發現配合處軸的表面被磨損,并出現細小粉末狀磨損產物。這種在相互壓緊的金屬表面間由于小振幅振動而產生的復合形式磨損稱為微動磨損,有氧化腐蝕現象的微動磨損也稱微動磨蝕,在交變應力下的微動磨損稱為微動疲勞磨損。 圖10 微動磨損的產生 在有振動的機械中,螺紋聯接、花鍵聯接和過盈配合聯接等都容易發生微動磨損。微動磨損的特征是摩擦副接觸區有大量紅色的Fe2O3磨損粉末,如果是鋁件,則磨損產物為黑色的。微動磨損時在摩擦面上還常常見到因接觸疲勞而形成的麻點或蝕坑。 一般認為,微動磨損的機理是,摩擦表面間的法向壓力使表面上的微凸體粘著。粘合點被小振幅振動剪斷成為磨屑,磨屑接著被氧化。被氧化的磨屑在磨損過程中起著磨粒的作用,使摩擦表面形成麻點或蟲紋形傷疤。這些麻點或傷疤是應力集中的根源,因而也是零件受動載失效的根源。根據被氧化磨屑的顏色,往往可以斷定是否發生微動磨損。如前所述,被氧化的鐵屑呈紅色,被氧化的鋁屑呈黑色,則振動時就會引起磨損。 從以上產生微動磨損的原因分析中可以看出,微動磨損不是單獨的磨損形式,而是粘著磨損、氧化磨損、磨料磨損,甚至還包含著腐蝕作用引起的腐蝕磨損和交變載荷作用引起的疲勞磨損,所以,微動磨損是幾種磨損形式的復合,究竟以哪一種形式的磨損為主,要視具體情況而定。 圖10 微動磨損的損傷過程 OA: 由于金屬轉移和初始磨損造成曲線迅速上升; AB: 從剪切到磨粒參與磨損, 使曲線第二次向上彎曲; BC: 磨粒作用下降,從而減緩材料損失; CD: 最后達到穩定的磨損率。 圖11 微動磨損不同階段的損傷過程 滾壓、噴丸和表面化學熱處理都能使表層產生壓應力,從而有效地提高微動磨損與疲勞的抗力。就材料來說,選擇抗粘著磨損能力大的,其抗微動磨損的能力也較強;硬度高的材料具有良好的抗微動磨損性能,但微動疲勞性能就較差。為減少微動磨損和微動疲勞,在界面間加入非腐蝕性潤滑劑或采用墊襯改變接觸面的性質,如蒸汽錘錘桿和錘頭配合處插入軟銅片作墊襯,螺紋聯接加裝聚四氟乙烯墊圈也可減小微動磨損,都可收到良好的效果;對壓配合件可用卸載槽以減少應力集中;再如增大緊配合的過盈量,實際上過盈量超過25~30μm就可防止微動磨損的出現。 金屬的接觸疲勞 一、接觸疲勞現象 接觸疲勞又稱表面疲勞磨損或疲勞磨損,是工件(如齒輪、滾動軸承,鋼軌和輪箍,鑿巖機活塞和釬尾的打擊端部等)表面在接觸壓應力的長期反復作用下引起的一種表面疲勞破壞現象。 接觸疲勞的宏觀特征是接觸表面出現許多針狀或痘狀的凹坑,稱為麻點,也叫點蝕或麻點磨損。有的凹坑很深,呈“貝殼”狀,有疲勞裂紋發展線的痕跡存在,圖12是GCr15鋼接觸疲勞失效的表面形貌。 齒輪、軸承、鋼軌與輪箍的表面經常出現接觸疲勞破壞。在剛出現少數麻點時,一般仍能繼續工作,但隨著工作時間的延續,麻點剝落現象將不斷增多和擴大,例如齒輪,此時嚙合情況惡化,磨損加劇,發生較大的附加沖擊力,噪聲增大,甚至引起齒根折斷。由此可見,研究金屬的接觸疲勞問題對提高這些機械零件的使用壽命有著重大的意義。 圖12 接觸疲勞表面形貌(SEI) 二、影響接觸疲勞壽命的因素 接觸疲勞壽命首先取決于加載條件,特別是載荷大小。此外,還與許多其他因素有關,這里僅簡敘其中若干有代表性的因素。接觸疲勞是軸承和齒輪常見的失效形式,下面介紹的影響因素主要是針對這兩類工件的。 (1)非金屬夾雜物 鋼在冶煉時總存在非金屬夾雜物等缺陷,鋼中的這些夾雜物的種類、數量、形狀、尺寸和分類等都對疲勞壽命產生影響。軸承鋼中的塑性夾雜物(硫化物)對壽命的影響較小,球狀夾雜物(鈣硅酸鹽和鐵錳酸鹽等)次之,脆性夾雜物(氧化物Al2O3、氮化物、硅酸鹽等)呈棱角尖銳形分布時對接觸疲勞壽命危害最大。這是由于脆性夾雜物尖角處的應力集中及它們跟基體交界處的彈塑性變形不協調而引起應力集中,使脆性夾雜物的邊緣部分極易形成為裂紋,降低接觸疲勞壽命。 (2)馬氏體含碳量的影響 軸承鋼中馬氏體組織中含碳量對其壽命有較明顯的影響。圖13是軸承鋼中馬氏體含碳量與接觸疲勞壽命的關系圖。從圖看出,馬氏體中碳的質量分數在0.5%附近壽命最高,低于或高于這個量,壽命都急劇降低。因為鋼中馬氏體含碳量增加,脆性就增多,并使奧氏體含量相應增多,疲勞壽命降低。若含碳量過低,就降低鋼的基體強度和硬度,從而減弱了基體抗疲勞磨損的能力。 圖13 馬氏體中碳質量分數與接觸疲勞壽命的關系 (3)馬氏體及殘余奧氏體級別 因工藝不同,滲碳鋼淬火可以得到不同級別的馬氏體和殘留奧氏體。若殘留奧氏體越多,馬氏體針越粗大,則表層有益的殘余壓應力和滲碳層強度就越低,易產生裂紋,故降低接觸疲勞壽命。 (4)未溶碳化物和帶狀碳化物 軸承鋼中碳化物含量多少及其粒度、形狀和分布均對接觸疲勞壽命有很大影響。碳化物數量太多,顆粒粗大,形狀不規則,分布不均勻,都會引起組織和性能的不均勻和應力集中等,從而造成接觸疲勞壽命降低。通過適當的熱處理,使未溶碳化物顆粒趨于小、少、勻、圓,對于提高軸承鋼接觸疲勞壽命是有利的。 帶狀碳化物之間的馬氏體碳含量較高,故脆性較大且易成為接觸疲勞裂紋源,從而降低接觸疲勞壽命。 對于軸承研究表明,在一定硬度范圍內,接觸疲勞壽命隨表層硬度的提高而延長,當表面硬度超過一定值后,再提高硬度,接觸疲勞壽命反而會降低。如圖14所示,硬度在62HRC左右壽命最高,低于或高于這個硬度范圍,其壽命均有較大的降低。 圖14 表面硬度與接觸疲勞壽命的關系 對于滲碳件而言,如果心部硬度太低,則表面硬度梯度太陡,易在過渡區內形成裂紋而產生深層剝落。因此,適當提高心部硬度,才能充分發揮材料強度潛力,有效提高接觸疲勞壽命。實踐表明,滲碳齒輪心部硬度值以35~40HRC為宜。 為防止表層產生早期麻點或深層剝落,滲碳的齒輪需要有一定的硬化層深度。最佳硬化層深度t推薦值為 式中 m—模數 B—接觸面半寬 (1)表面粗糙度與接觸精度 減少表面冷、熱加工缺陷,降低表面粗糙度,提高接觸精度,可以有效地增加接觸疲勞壽命。接觸應力大小不同,對表面粗糙度要求也不同。接觸應力低時,表面粗糙度對接觸疲勞壽命影響較大;接觸應力高時,表面粗糙度影響較小。 (2)硬度匹配 兩個接觸滾動體的硬度匹配恰當與否,會直接影響接觸疲勞壽命。例如,ZQ-400型減速器小齒輪與大齒輪的硬度比保持1.4~1.7的匹配關系,可使承載能力提高30%~50%。 此外,兩個接觸滾動件的裝配質量及它們之間的潤滑情況也影響接觸疲勞壽命。 預防金屬腐蝕措施 預防金屬腐蝕可以從多個方面入手,涵蓋了材料選擇、表面處理、設計優化、潤滑管理和環境控制等方面。以下是幾個主要的預防措施: 耐蝕性能:選擇具有良好耐蝕性的金屬材料,如不銹鋼、銅合金、鋁合金等,根據具體環境條件選擇合適的材料。 抗氧化能力:考慮材料的抗氧化能力,特別是在高溫或氧化性環境中的應用,選擇耐高溫合金或抗氧化表面涂層材料。 防腐涂層:在金屬表面涂覆具有防腐性能的涂層,如環氧樹脂涂層、聚氨酯涂層、熱浸鍍鋅等,形成有效的防護層。 陽極保護:對于某些金屬,如鋁合金,在其表面形成氧化層可以提供一定程度的防腐保護。 減少潮濕環境接觸:優化設備和結構設計,盡量減少金屬表面暴露在潮濕或腐蝕介質中的時間和條件。 減少應力集中:設計時避免尖銳邊角和應力集中區域,以減少腐蝕的發生和擴展。 合適的潤滑劑:選擇適合的潤滑劑,形成有效的潤滑膜,減少金屬表面的直接接觸和磨損,同時防止腐蝕介質侵蝕。 定期維護:定期檢查和更換潤滑劑,保持潤滑系統的清潔和潤滑效果。 控制濕度和溫度:控制環境中的濕度和溫度,尤其是在暴露在潮濕或高溫環境中的金屬部件。 防止腐蝕介質:采取隔離措施或使用防護罩、涂層等方法,避免腐蝕介質直接接觸金屬表面。 定期檢測和維護:定期進行腐蝕檢測和監測,及時發現和處理潛在的腐蝕問題。 教育和培訓:對工作人員進行腐蝕防護的培訓,提高其對腐蝕防護工作的重視和能力。
(6)磨損測試標準
1. 材料選擇
2. 表面處理
3. 設計優化
4. 潤滑管理
5. 環境控制
6. 其他措施
免責聲明:本網站所轉載的文字、圖片與視頻資料版權歸原創作者所有,如果涉及侵權,請第一時間聯系本網刪除。
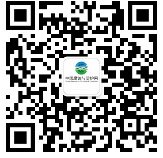
官方微信
《腐蝕與防護網電子期刊》征訂啟事
- 投稿聯系:編輯部
- 電話:010-62316606
- 郵箱:fsfhzy666@163.com
- 腐蝕與防護網官方QQ群:140808414