感應淬火后的回火方式有幾種?常見問題有哪些?
2025-01-08 11:07:30
作者:材子筆記 來源:材子筆記
分享至:
一般而言,我們都知道淬火以后肯定要有回火(注:回火也另稱為“配火”)這個工序才行。可有的時候我們在現場觀察到,為什么有的工件感應淬火后好像沒有進行回火呢?
事實上這類工件真的沒有進行回火嗎?
答案肯定是否定的。
具體采用哪種方式的回火,且看下文所述。
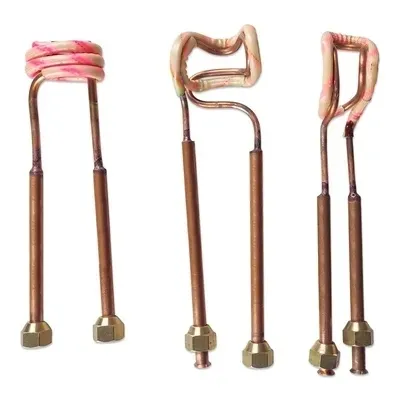
感應加熱淬火后一般只進行低溫回火。
其目的是為了降低殘余應力和脆性,而又不致降低硬度,但應盡量保持高硬度和高的表面殘余壓應力。
一般采用的回火方式有爐中回火、自回火和感應加熱回火。
感應淬火冷透的工件、浸淬火連續淬火后的工件以及薄壁和形狀復雜的工件,通常在空氣爐或油浴爐中回火;
為了在高頻表面淬火后使工件表面保留著較高的殘余壓應力,回火溫度比普通加熱淬火的要低,一般不高于200℃。
自回火就是利用感應淬火冷卻殘留下來的熱量而實現的短時間回火。
自回火不僅簡化了工藝,而且對防止高碳鋼及某些高合金鋼產生淬火裂紋也很有效。自回火的主要缺點是工藝不易掌握,消除淬火應力不如爐中回火。
采用自回火時,應嚴格控制冷卻介質的溫度、噴冷時間和噴射壓力。具體的操作規范應通過具體工件的試驗來確定。
表1列出了45鋼達到相同硬度的自回火溫度與爐中回火溫度的比較。
表1 達到相同硬度的自回火溫度與爐中回火溫度的比較
注:淬火后硬度63.5-65HRC,爐中回火1.5h。
連續感應淬火的長軸或其他零件,有時采用感應加熱回火比較方便。
這種回火方法,可以緊接在淬火后進行。由于回火溫度低于磁性轉變溫度,電流的透入深度較小。另一方面,為降低表面淬火件過渡層中的殘留拉應力,回火的感應加熱層深度應比淬火層深才能達到回火目的。
因此,感應加熱回火應采用很低的頻率或很小的比功率,延長加熱時間,利用熱傳導使加熱層增厚。采用同時加熱法時,可利用繼續加熱法使加熱層增厚。
感應加熱回火的最大特點是回火時間短。因此要達到與爐中回火相同的硬度及其他性能時,回火溫度應相應提高。
此外,采用感應加熱回火,由于加熱時間短,所得到的顯微組織有極大的彌散度,回火后的耐磨性和沖擊韌度比爐中回火高,而且容易安排在流水線上。感應回火要求加熱速度小于15-20℃/s。
感應加熱熱處理常見的質量問題有開裂、硬度過高或過低、硬度不均、硬化層過深或過淺等。
產生原因:
加熱溫度過高、溫度不均;冷卻過急且不均;淬火介質及溫度選擇不當;回火不及時且回火不足;材料淬透性偏高、成分偏析、有缺陷、含過量夾雜物、零件設計不合理、技術要求不當等。
產生原因:
加熱功率過大或過小、電流頻率過低或過高、加熱時間過長或過短、材料淬透性過低或過高、淬火介質溫度/壓力/成分不當等。
產生原因:
材料碳含量偏高或偏低、表面脫碳、加熱溫度低、回火溫度或保溫時間不當、淬火介質成分/壓力/成分不當等。
產生原因:
感應器結構不合理、加熱不均、冷卻不均、材料組織不良(帶狀組織偏析、局部脫碳)等。
產生原因:
感應器結構不合理、零件有尖角、孔、槽等、加熱時間過長、材料表面有裂紋等。
感應加熱熱處理零件有下列情況時允許返修處理。
硬度低或有大片軟點、硬化區范圍和硬化層深度不符合技術要求、加熱溫度不足造成金相組織不合格等,返修件的處理方法可按下述兩種辦法進行:
返修件經感應加熱到700-750℃后在空氣中冷卻透,然后按該零件淬火規范進行第二次淬火。
返修零件經爐中加熱到550-600℃,保溫60-90min。然后在水中或空氣中冷卻,再按原淬火規范進行第二次淬火。
免責聲明:本網站所轉載的文字、圖片與視頻資料版權歸原創作者所有,如果涉及侵權,請第一時間聯系本網刪除。