為解決粉末高溫合金渦輪盤中存在的夾雜物尺寸超標、超聲檢測不合格等關鍵問題,我國深入開展了“擠壓+等溫鍛造”工藝的研究,并取得了重要進展。近期,我國在北重集團3.6萬噸黑色金屬擠壓機上成功擠壓出用于航空發動機渦輪盤的粉末高溫合金棒坯。這一成果標志著我國在粉末高溫合金制造技術領域實現了重大突破。研究表明,在擠壓過程中,原始顆粒邊界(PPB)被有效消除,夾雜物沿擠壓方向得到充分破碎和延展。在隨后的等溫鍛造階段,這些夾雜物在垂直于鍛造方向的平面內進一步被細化和彌散分布,從而顯著改善了材料的均勻性和綜合性能。此外,我國在粉末高溫合金擠壓變形研究中也取得了積極進展,尤其是在有限元模擬技術方面。通過模擬包覆擠壓過程,可以系統分析模具結構參數、工藝條件等對擠壓過程的影響,為優化模具設計、實現最佳結構組合提供了科學依據。目前,“擠壓開坯+等溫鍛造”工藝已被確立為我國粉末高溫合金渦輪盤制造的核心發展方向之一。這一技術路線的突破為提高渦輪盤的性能和質量奠定了堅實的基礎,同時也為我國高端制造業提供了重要支撐。
高溫合金是指以第珊主族元素(鐵、鈷、鎳)為基,加入大量強化元素,能在 600℃以上的高溫及一定應力作用下長期工作的一類金屬材料。高溫合金具有較高的高溫強度以及良好的抗氧化、抗熱腐蝕、抗疲勞性能,在高溫下具有良好的組織穩定性和使用可靠性,因此,也被稱為熱強合金、耐熱合金或超合金。此前我們已經對高溫合金進行了詳細的講解,有需要了解的小伙伴可以點擊鏈接查看。 粉末高溫合金是一種基于粉末冶金技術制造的高性能材料,專為在高溫和極端環境下工作而設計。其主要特點是能夠在高溫條件下保持優異的機械性能、抗腐蝕性和抗氧化性。這類材料廣泛應用于航空航天、燃氣輪機、核電及化工等領域,是現代高科技產業不可或缺的重要支柱。 粉末高溫合金的制備通過將不同成分的金屬粉末混合并致密化,形成均勻微觀結構,從而克服了傳統鑄造和鍛造工藝的缺陷。這種方法能更精準地調控材料的微觀組織與成分分布,使其在高溫環境下的表現更加優越。與傳統鑄造材料相比,粉末高溫合金還表現出更高的組織穩定性和抗疲勞性能,這使其在苛刻工況下的壽命大幅延長。 粉末高溫合金的發展始于20世紀50年代。隨著航空工業的快速發展,傳統鑄造高溫合金逐漸暴露出晶粒粗大、成分偏析、缺陷難以控制等問題,難以滿足噴氣發動機和燃氣渦輪日益苛刻的使用要求。粉末冶金技術的出現,為解決這些問題提供了新的思路。粉末高溫合金經歷了三代發展,已在先進軍、民用航空發動機的渦輪盤等多種關鍵零件上廣泛應用,當前國際粉末高溫合金研發已經進入第四代。粉末高溫合金鑄錠內部無宏觀偏析、微觀組織均勻、晶粒細小,具有優異的力學性能和熱加工性能,可有效地保證發動機的可靠性和耐久性,而且可近凈成形,制造周期短,生產成本較低。 1950-1970年代: 粉末高溫合金技術初見雛形,研究重點集中于制備技術與性能表征。最早期的應用是航空發動機中的小型零部件。此階段的粉末高溫合金多基于傳統鑄造高溫合金的成分。 1980-1990年代: 隨著氣霧化技術和熱等靜壓(HIP)技術的發展,粉末高溫合金的制備工藝得到了顯著改進,合金強度和可靠性顯著提升。研究人員逐漸認識到微觀結構對高溫性能的重要性,推動了合金設計的精細化。 2000年代至今: 粉末高溫合金的性能不斷優化,微觀組織控制技術逐漸成熟。隨著增材制造技術(如激光熔化沉積、電子束熔化)的興起,粉末高溫合金的應用范圍進一步拓展。不僅在航空航天等傳統領域,其在能源、醫療和高端裝備制造中的應用也日益廣泛。 粉末高溫合金材料的性能特征: 粉末高溫合金的優異性能主要體現在以下幾個方面: 高溫強度 在高溫下仍能保持較高的抗拉強度和屈服強度,適用于渦輪葉片等高溫承載部件。其強度源自精細的晶粒和析出強化機制。 抗蠕變性能 在長期高溫工作條件下表現出優異的抗蠕變性能,能夠抵抗材料在應力作用下的永久變形。這主要得益于其均勻的晶粒和分布合理的第二相顆粒。 抗氧化性和耐腐蝕性 表面能夠形成穩定的保護膜,防止氧化和腐蝕,尤其適用于高溫氧化和化學腐蝕環境。特別是在含硫氣氛中,粉末高溫合金具有獨特優勢。 微觀組織均勻性 粉末冶金技術制備的材料具有均勻的組織結構,減少了傳統鑄造工藝中的偏析現象,提高了材料的可靠性。 疲勞抗性 粉末高溫合金的均勻組織和致密微觀結構賦予其極高的抗疲勞性能,尤其在循環載荷和熱循環條件下表現卓越。 根據合金的基體元素、性能特點和應用領域的需求,粉末高溫合金可以分為以下幾類: 鎳基粉末高溫合金 特點:鎳基合金是目前使用最廣泛的高溫合金,具有卓越的高溫強度、抗蠕變性和抗氧化性能。這些性能得益于其主要基體金屬鎳的高熔點及其對鋁和鈦等強化元素的優良兼容性。鎳基合金中常添加鉻以提高抗腐蝕性,同時通過鋁和鈦的析出強化形成γ′相(Ni3Al)。 應用:鎳基合金廣泛應用于航空發動機燃燒室、渦輪葉片及導向葉片等高溫部件,是燃氣渦輪核心部件的首選材料。 鈷基粉末高溫合金 特點:鈷基高溫合金以其在高溫氧化環境下的優異表現而著稱,特別適用于需要長時間承受高溫熱腐蝕的場合。鈷基合金因其良好的延展性和韌性,能夠更有效地抵抗熱疲勞和熱震。其基體結構通常含有碳化物和析出相強化,但與鎳基合金相比,其高溫強度稍低。 應用:鈷基合金主要用于航空航天燃燒室、渦輪殼體以及化工行業中抗腐蝕性要求高的部件。 鐵基粉末高溫合金 特點:鐵基合金是一種成本較低的高溫合金,適合在中高溫條件下工作。鐵基合金中常摻入鉻、鎳、鉬等元素以提高其抗氧化和抗腐蝕性能,但其高溫性能較鎳基和鈷基合金遜色。 應用:鐵基高溫合金適用于化工設備中的耐熱部件、鍋爐熱端組件及部分中溫燃氣渦輪組件。 復合型粉末高溫合金 特點:復合型合金通過組合多種金屬基體元素的優勢,實現了性能的協同優化。例如,基于鎳-鈷復合體系的高溫合金既具有鎳基合金的高溫強度,又兼備了鈷基合金的耐腐蝕性。此類合金在一些極端環境下具有不可替代的優勢。 應用:復合型粉末高溫合金主要用于特殊高溫環境中的關鍵部件,例如需要承受強熱流和復雜應力的核反應堆核心部件。 新型超高溫粉末合金 特點:新型超高溫合金是近年來發展的熱點領域,旨在滿足極端溫度(超過1200°C)的工作需求。通常采用高熔點元素如錸、鉭、錸-銥等材料制備,具有極高的熱穩定性和抗氧化能力。 應用:主要用于超高溫燃氣渦輪、尖端航空航天技術以及高溫核能裝置中的核心部件。 粉末高溫合金的生產工藝總體上是通過在惰性氣氛保護下制備和處理金屬粉末,然后利用熱成形技術實現粉末的固結與致密化。經過多年的技術發展,目前主要形成了兩種代表性工藝路線:以歐美國家為主的“氬氣霧化法 (AA) 制粉 + 熱擠壓 (HEX) + 等溫鍛造 (ITF)”工藝,以及以俄羅斯為主的“轉電極法 (PREP) 制粉 + 熱等靜壓 (HIP) 直接成形”工藝。 粉末高溫合金盤件制造的主要工藝流程 我國在粉末高溫合金制造領域取得了顯著進展,研發了一條“等離子旋轉電極法 (PREP) 制粉 + 熱等靜壓 (HIP) 成形 + 包套鍛造/熱處理”的工藝路線。利用該工藝成功生產出大尺寸的FGH4095粉末渦輪盤。此外,通過直接HIP成形工藝制備的粉末高溫合金渦輪擋板和小尺寸渦輪盤,已完成試車并實現批量生產能力。\n\n在第2代粉末高溫合金FGH4096的研發中,雙性能渦輪盤的研究工作取得了突破性進展。采用“PREP + 直接HIP + 等溫鍛造”工藝,攻克了粉末純凈度等關鍵技術難題,成功研制出用于某高推重比發動機的FGH4096合金渦輪盤。通過細晶鍛造與梯度熱處理工藝的結合,制備出具有雙顯微組織特性的盤坯,其輪緣晶粒度達5~6級,輪轂晶粒度達10~11級。這些成果標志著我國在高性能粉末高溫合金領域實現了重要技術突破。 粉末高溫合金在制備和加工過程中可能產生多種缺陷,這些缺陷直接影響材料的性能和可靠性,尤其是在高溫、高應力條件下的應用。夾雜物、PPB和熱誘導孔洞(TIP)是粉末高溫合金的3大缺陷,嚴重影響粉末高溫合金零件的性能。 缺陷描述:夾雜物是制備過程中外界雜質(如氧化物、硫化物、氮化物)或未充分反應的化合物顆粒,通常來源于制粉、混粉和燒結過程。 影響: 機械性能降低:夾雜物是潛在的裂紋源,導致材料的抗疲勞性能和高溫強度下降。 檢測不合格:夾雜物容易在超聲檢測中暴露,影響零部件質量評價。 使用壽命縮短:夾雜物的存在可能導致裂紋在高應力環境下快速擴展,降低構件的可靠性。 缺陷描述:原始顆粒邊界是制粉后顆粒間的結合弱區,其主要表現為未完全消除的界面化學雜質和結構缺陷。 影響: 抗蠕變性能減弱:在高溫高應力環境下,PPB容易成為蠕變變形的起始點。 延展性降低:PPB導致材料在受力時更易發生斷裂,降低了整體塑性。 疲勞壽命減少:PPB的存在容易引發局部應力集中,加速疲勞裂紋的萌生和擴展。 缺陷描述:孔隙和氣孔是粉末冶金過程中未完全致密化的結果,可能由氣體殘留、燒結不足或粉末分布不均引起。 影響: 強度損失:孔隙降低了材料的整體強度和密度。 疲勞裂紋萌生:孔隙是裂紋形成的核心部位,容易在循環載荷下擴展。 韌性降低:氣孔的存在削弱了材料的抗沖擊能力和延展性。 綜上所述,粉末高溫合金的缺陷主要集中在夾雜物、孔隙、PPB等方面,這些缺陷對材料的強度、疲勞壽命、高溫性能等核心指標有顯著負面影響。通過優化制粉工藝(如氣霧化或等離子旋轉電極法)、提高致密化技術(如熱等靜壓和等溫鍛造)以及加強質量檢測,可以有效減少缺陷,提高粉末高溫合金的性能和可靠性。這些改進措施對于滿足航空航天、燃氣渦輪等領域對高性能材料的嚴格要求具有重要意義。 金屬粉末的生產方法種類繁多,包括固體破碎法、球磨法、霧化法、電解法和化學法等。針對增材制造的需求,由于其對粉末的流動性和填充性要求較高,球形粉末成為首選材料。在眾多制備技術中,霧化法被廣泛認為是生產增材制造用金屬粉末的最理想方法。同時,旋轉電極法因其能夠制備出高純度、高球形度的粉末,近年來也逐漸在增材制造粉體材料的制備中得到應用。 這里說明:鎳基高溫合金球形粉末的制備基本工藝流程包括:母合金的冶煉與加工→制粉→粉末篩分→(電選分離雜質)→粉末性能檢測。其中,母合金熔煉、霧化制粉以及電選分離雜質是確保高品質粉末的重要關鍵環節。 母合金熔煉技術 高溫合金母合金的熔煉對高品質球形粉末的制備至關重要,但熔煉過程中可能引入夾雜物、縮孔、疏松等缺陷,影響粉末質量。為解決這些問題,通常采用真空感應熔煉(VIM)+電渣重熔(ESR)/真空電弧重熔(VAR)的多聯精煉工藝。真空感應熔煉可精確控制成分并制備自耗電極,電渣重熔可有效去除非金屬夾雜,真空電弧重熔進一步消除宏觀偏析,獲得組織均勻、純凈度高的母合金。電渣重熔因其卓越的夾雜物去除能力,是高溫合金母合金精煉的優選工藝,為高質量粉末的生產提供了保障。 俄羅斯自20世紀90年代起廣泛應用真空感應熔煉+電渣重熔工藝生產粉末高溫合金母合金錠,顯著提升了母合金的純凈度。2002年,鋼鐵研究總院設計并建造了首臺超小斷面真空/惰性氣體保護快速電渣爐,通過該工藝制備的FGH95母合金顯著降低了氧含量,減少了Al和Ti的燒損,同時減少了非金屬夾雜物的尺寸和數量。泡沫陶瓷過濾技術利用陶瓷板過濾器對金屬熔體進行過濾,同樣能夠有效去除夾雜物和有害元素,北京科技大學、中科院金屬所等單位已通過該技術取得了良好成果。此外,日本的旋轉鑄錠工藝、北京航材院的優質高溫合金錠生產技術,以及西北工業大學的電磁軟接觸成形凈化技術和復合熔鹽凈化技術等,也在合金凈化方面表現出顯著優勢。近年來,電磁凈化技術和超聲波處理技術等新型技術成為研究熱點,為提升母合金純凈度提供了新的思路。隨著航空發動機對粉末高溫合金性能和可靠性的要求不斷提高,研發高效率、低成本、高純凈的母合金熔煉與凈化技術成為未來發展的重要方向。 制粉 粉末制備是粉末高溫合金生產中至關重要的環節。通過制備出尺寸細小均勻、球形度高且氣體和夾雜物含量低的粉末,可以顯著減少甚至消除PPB和夾雜物等冶金缺陷,改善合金盤件的組織和性能,確保其質量。目前,先進的粉末制備技術是生產高品質高溫合金粉末的關鍵,主要工藝包括真空感應熔化氣霧化法(VIGA)、等離子旋轉電極制粉技術(PREP)、電極感應氣體霧化法(EIGA)以及等離子霧化法(PA)。這些技術為高溫合金的高性能化提供了重要保障。 1)真空感應熔化氣霧化法(VIGA) 真空感應熔化氣霧化法(VIGA)是一種在真空環境下制備金屬粉末的工藝。其過程包括利用感應加熱技術熔化爐料,并在達到一定溫度后向熔煉室和霧化室充入惰性霧化氣體。熔融金屬通過噴嘴流入霧化室后,利用高壓惰性氣體將金屬液流破碎成細小液滴,液滴在高速冷卻中凝固形成金屬粉末。該方法能夠高效制備尺寸細小、球形度高的粉末,適用于高品質金屬粉末的生產。 真空感應熔化氣霧化法(VIGA)示意圖 目前,真空感應熔化氣霧化制粉技術不僅廣泛應用于鎳基高溫合金粉末的制備,還可用于多種金屬材料的粉末化生產,包括不銹鋼(如316L、174PH)、鈷基合金(如CoCrMo、CoCrW、CoCrMoW)、鈦及鈦合金(如TC4、TC11、TA15、TiAl4822、Ti2AlNb)以及其他鎳基合金(如FGH95、FGH96、FGH97、GH4169)和稀有金屬粉末。這一技術因其高效性和適用性廣泛,被廣泛應用于高性能金屬粉末的生產領域。 2)等離子旋轉電極制粉技術(PREP法) 等離子旋轉電極制粉技術利用離心霧化原理,在惰性氣體環境下,通過等離子電弧快速熔化旋轉棒料,熔融金屬在離心力作用下形成液滴,并在濺射室內快速凝固成顆粒,最終收集于粉末罐中。該技術適用于制備高反應性金屬、耐熱鎳基和鈦合金粉末。據悉,國內制造等離子旋轉電極制粉設備的企業包括湖南頂立科技、湖南久泰、西安賽隆等,所生產的設備通過電機驅動棒料旋轉,轉速可達1000015000 r/min,制得粉末的粒度D50一般大于100 μm。相比之下,俄羅斯在PREP設備領域處于世界領先地位,其Granule 2000型設備設計先進,棒料轉速可達2000025000 r/min,制備的粉末粒度更小(D50約為60 μm),球形度高、氧氮含量低、無衛星粉,性能優異。最新的Granule 2500型設備進一步優化了電極旋轉系統,轉速達到25000~30000 r/min,顯著提高了粉末細度和質量。PREP制粉法中,粉末粒度與棒料轉速成反比,轉速越高,粉末粒度越小,這使得高轉速設備在制備高品質金屬粉末方面具有明顯優勢。 3)等離子霧化法(PA法) 等離子霧化法(PA法)是一種通過等離子槍加熱金屬絲材,熔化并霧化生成球形粉末的技術。該方法由M.EntezaRian于1998年提出并申請專利,目前加拿大AP&C公司在該領域處于全球領先地位,掌握成套技術專利。PA法的原理是在惰性氣體保護下,利用等離子槍將合金絲材熔化成金屬蒸汽,通過氣淬冷卻使其快速團聚并形成超細合金粉末。該工藝制得的粉末粒徑分布窄(10~150μm),其中50μm以下粉末占比約40%,球形度高且雜質含量低,細粉收得率極高。然而,PA法的主要限制在于原料需為較細的絲材,制造成本較高且制粉效率較低。\n\n目前,加拿大AP&C公司的等離子霧化設備配備全自動監控系統和氣體回收裝置,確保粉末質量穩定性并降低生產成本。該技術已廣泛應用于大規模生產高品質球形金屬粉末,涵蓋純鈦及鈦合金、鎳基合金等材料領域。 4)電極感應氣體霧化法(EIGA法) 電極感應熔化氣霧化法(EIGA法)是一種不使用陶瓷坩堝的超潔凈氣體霧化制粉技術,具有生產效率高、產量大、粉末粒徑細小的特點。其原理是在惰性氣體保護下,將母合金棒料通過送料裝置送入錐形超高頻感應線圈,尖端逐漸熔化形成連續可控的金屬液流,在重力作用下流入霧化室。高壓惰性氣體將液流破碎成小液滴,小液滴在霧化室內迅速球化并凝固形成金屬粉末。EIGA法的關鍵優勢在于整個熔化過程不使用坩堝或導流嘴,顯著減少非金屬雜質的引入。與VIGA法相比,EIGA法制備的粉末粒度更小,Dv(50)一般控制在50~100 μm之間,粉末球形度高,幾乎沒有片狀物,且生產效率更高。德國ALD公司通過優化該技術,開發了多種型號的制粉設備,廣泛應用于鈦及鈦合金粉末材料的科研與生產。日本OSAKA鈦公司使用EIGA法制備的Ti6Al4V粉末粒徑Dv(50)約40 μm,球形度高,雜質含量少,并已在增材制造領域實現應用。 電選分離技術 電選分離技術是去除高溫合金粉末中非金屬夾雜物的關鍵方法,其利用金屬粉末和非金屬夾雜物電性能的差異,通過電暈放電使粉末顆粒帶電,從而實現分離。在靜電分離過程中,金屬粉末因電導率高快速釋放電荷,在重力和離心力作用下進入成品區,而非金屬夾雜物因電導率低被吸附到輥筒上并最終刷除。研究表明,電暈極電壓和輥筒轉速是影響分離效果的主要因素。以最佳工藝參數(電暈極電壓40kV,輥筒轉速50r/min)對50~100μm夾雜物處理時,去除率可達76.7%。此外,北京鋼鐵研究總院和北京航空材料研究院等單位已成功研發摩擦電選分離設備,其分離率超過85%,并可在高純惰性氣體保護下完成,避免粉末氧化。然而,當前電選技術分離范圍有限,僅能處理一定粒度范圍的夾雜物,分離效率和效果仍需進一步提升。未來的發展方向是擴大分離粒度范圍和提高去除效率,以更好滿足高溫合金粉末生產的需求。 粉末篩分 在金屬粉末生產中,霧化后的后處理過程對最終粉末特性至關重要,包括氧化鈍化、分級(篩分或空氣分級)和混合,以獲得均勻的粉末批次。粉末篩分用于去除雜質并獲得所需粒度的粉末,為避免篩分過程中粉末氧化,篩分機通常在真空或惰性氣體保護下運行。篩分工藝的關鍵參數是振幅和振動頻率,VIGA法制備的原粉一般需通過100目預篩,以防較大異形物體損壞篩網。此外,改善鈍化后粉末流動性的方法多樣,目前已開發多種技術來量化粉末的流變性(流動性和鋪展性),但不同方法之間的相關性尚不明確。除了漏斗流速法外(ASTM B213/ISO 4490/ASTM B964),尚未有其他廣泛采用的標準方法。同時,增材制造對金屬粉末流動性的可接受值仍缺乏明確共識,未來需要進一步研究和量化以提高粉末的性能適配性。 應用背景: 材料與技術: 常用粉末高溫合金:FGH95、FGH96、FGH4096等鎳基合金。 制備工藝:采用真空感應熔煉氣霧化法(VIGA)制粉,結合“擠壓開坯+等溫鍛造”工藝制備高性能渦輪盤。 應用優勢: 細晶組織提高了抗蠕變性能和疲勞強度。 減少了冶金缺陷(如夾雜物、PPB),顯著提升部件壽命和可靠性。 應用背景: 材料與技術: 常用粉末高溫合金:IN738、Rene 95、GH4169等鎳基合金。 制備工藝:采用等離子旋轉電極制粉技術(PREP)生產高純度球形粉末,確保葉片性能的一致性。 應用優勢: 優異的高溫強度和抗氧化性能,延長部件使用壽命。 球形粉末使得增材制造(3D打印)技術可用于復雜結構部件的生產。 應用背景: 材料與技術: 常用粉末高溫合金:NiAl基、TiAl基合金(如TiAl4822、Ti2AlNb)。 制備工藝:使用EIGA法制粉,結合增材制造技術,生產輕量化、復雜形狀的熱屏蔽部件。 應用優勢: 提供優異的高溫抗氧化和抗腐蝕性能。 顯著減輕航天器重量,提高推進效率。 應用背景: 材料與技術: 常用粉末高溫合金:鈷基合金(CoCrMo)、鈦合金(Ti6Al4V)。 制備工藝:等離子霧化法(PA)生產的高球形粉末用于金屬增材制造技術。 應用優勢: 提供高度定制化的植入物,適配患者的解剖結構。 高純凈度和表面光潔度,減少生物排斥反應。 應用背景: 材料與技術: 常用粉末高溫合金:NiCr基和CoCr基合金。 制備工藝:真空熔融氣霧化技術(VIGA)生產高純粉末,結合熱等靜壓(HIP)成形技術。 應用優勢: 高溫抗氧化性和抗輻射性能,確保組件長期穩定運行。 微觀組織均勻,延長使用壽命。 結語
點此處跳轉查看:一文了解先進高溫合金材料
1. 夾雜物
2. 原始顆粒邊界(PPB)
3. 孔隙和氣孔
1. 航空發動機渦輪盤
粉末高溫合金廣泛應用于航空發動機的渦輪盤部件,這是發動機的核心部件之一,需要在高溫、高壓、高轉速下長時間運行。
2. 燃氣輪機熱端部件
燃氣輪機的燃燒室和渦輪葉片需要承受極高溫度和氧化環境,是關鍵的高溫部件。
3. 航天器熱屏蔽材料
航天器的熱屏蔽材料需要在高溫和極端輻射環境下保持穩定,粉末高溫合金為該領域提供了優質材料選擇。
4. 醫療植入物
粉末高溫合金也用于醫療植入物,如髖關節和膝關節的人工替代物,必須滿足高強度、耐腐蝕及生物相容性要求。
5. 核能反應堆組件
核反應堆中某些部件(如控制棒、燃料包殼)需要在高溫、高輻射和腐蝕環境下運行。
免責聲明:本網站所轉載的文字、圖片與視頻資料版權歸原創作者所有,如果涉及侵權,請第一時間聯系本網刪除。
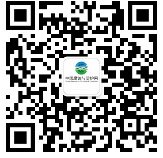
官方微信
《腐蝕與防護網電子期刊》征訂啟事
- 投稿聯系:編輯部
- 電話:010-62316606
- 郵箱:fsfhzy666@163.com
- 腐蝕與防護網官方QQ群:140808414