日前,由東北大學許云波教授團隊研發的高強塑積汽車鋼在河鋼唐鋼高強汽車板連退生產線成功下線,力學性能全部達到指標并獲得用戶訂單,標志著我國首次在以“較低冷卻速率和一步過時效處理”為特征的傳統連續退火生產線上成功研發具有優異力學性能的第三代汽車鋼,河鋼唐鋼也成為國際上首家掌握這項技術并投入工業化應用的企業。
隨著能源危機和環境惡化的日益加劇,安全、節能和環保已成為汽車制造業的發展潮流。在保證使用安全的前提下,汽車輕量化是汽車節能減排最有效的方法。因此,近年來全球各大鋼鐵企業紛紛加大了第三代汽車鋼的研發力度,力求通過車身減重實現汽車“更省油、更安全”的目標。作為第三代鋼典型代表之一的淬火配分(Q&P,Quenching and Partitioning)鋼,因其優異的強塑性能和適合工業化批量生產的技術特點而成為其中最為矚目的明星。
2003年,美國物理冶金學家Speer教授提出Q&P工藝的概念,之后短短十多年時間,中國寶鋼利用其先進的具有“高溫均熱、高速冷卻和淬火再提溫”功能的高強專用退火線把Q&P鋼從概念變成了商業化產品,鞍鋼也采用“快速冷卻+兩步配分”方法打通了高強Q&P鋼的工業化路徑,這使得中國在第三代高強鋼開發和應用方面走在世界前列。
然而,按照經典的淬火配分理論,為了獲得優異的強塑性能,傳統連續退火生產線必須擁有高速冷卻和淬火后快速提溫(“兩步配分”)等特殊功能。而配置如此豪華的一條高強鋼專用退火生產線投資動輒八、九個億,有的甚至高達十多億。國內已有和在建的四十余條大型連續退火產線中,僅有兩、三條具備這樣的條件。因此,大部分鋼企對于具有誘人性能的高強Q&P鋼只能望洋興嘆,這極大地限制了新一代高強塑積汽車鋼的推廣和應用。
在冷卻速率不高、不具備淬火再提溫功能的傳統連續退火生產線上開發第三代高強鋼,逐漸成為學界和業界共同追求的目標。為解決這一行業共性技術難題,東北大學軋制技術及連軋自動化國家重點實驗室許云波教授團隊深入開展淬火配分理論和關鍵工業化技術的研究,突破單獨依賴馬氏體向奧氏體碳配分的傳統框架,提出“鐵素體、貝氏體和馬氏體協同碳配分”新概念與新工藝,通過合金成分設計、奧氏體穩定化和多相微結構的精準調控,在國際上首次基于河鋼唐鋼傳統連續退火生產線的較低冷速與一步過時效處理,成功開發出QP980鋼。這一鋼種成品板屈服強度≥600MPa,抗拉強度≥980MPa,斷后延伸率達到21~28%,綜合性能表現優異,這使河鋼唐鋼成為繼中國寶鋼、鞍鋼之后國內又一家具備QP980供貨能力的汽車鋼制造商。
與同級別“兩步配分”商業化Q&P鋼相比,新技術溫控路徑簡單,配分窗口靈活,生產銜接順暢高效,工藝成本降低,僅取消“感應提溫”一項就可以節約電費50~100元/噸。而且,新產品典型組織和力學性能表現優異,通卷性能波動小,抗回火穩定性強,顯微組織中殘奧體積分數提高2%~6%,斷后延伸率增加2%~4%,強塑積可達27GPa?%以上。電阻點焊及成形性能與“兩步配分”產品典型值基本相當,其中折彎、回彈等性能更優,1.6mm板臨界相對彎曲半徑降至1.5mm左右,90°折彎回彈角可達到約14°。
此外,與同級別冷軋雙相鋼(DP)、相變誘發塑性鋼(TRIP)相比,不僅合金成本大幅度降低,而且鋼材韌塑性、成形性和延伸凸緣性等顯著提高,特別是延伸率達到了同級別DP鋼的兩倍以上。
新型Q&P鋼可用于橫梁、縱梁、車窗框架、保險杠及地板加強件等汽車結構件,通過減薄零件厚度,減少燃油損耗,有效實現節能降耗。例如,使用QP980替代DP600,工件厚度由1.2mm減薄至1.0mm,可為汽車減重10%~20%。同時,汽車安全性顯著提高,在正常碰撞下人員死亡率大幅度下降。新技術的成功開發與應用,將全面打通基于傳統連退線的第三代高強塑積汽車用鋼的設計、研發、生產與應用產業鏈,進一步推動我國汽車輕量化鋼鐵材料研發與應用達到國際領先水平。
— END —
更多關于材料方面、材料腐蝕控制、材料科普等方面的國內外最新動態,我們網站會不斷更新。希望大家一直關注中國腐蝕與防護網http://www.ecorr.org
責任編輯:王元
投稿聯系:編輯部
電話:010-62313558-806
中國腐蝕與防護網官方 QQ群:140808414
免責聲明:本網站所轉載的文字、圖片與視頻資料版權歸原創作者所有,如果涉及侵權,請第一時間聯系本網刪除。
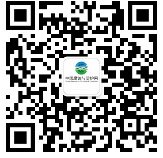
官方微信
《中國腐蝕與防護網電子期刊》征訂啟事
- 投稿聯系:編輯部
- 電話:010-62316606-806
- 郵箱:fsfhzy666@163.com
- 中國腐蝕與防護網官方QQ群:140808414