激光粉末床熔融(LPBF)產生的不規則大孔隙是一種固有缺陷,極大地限制了構件的力學性能。激光重熔是減少孔隙率和增加能量輸入的有效方法,而過多的熱量積累通常是以犧牲粉末飛濺為代價的。
Graphical abstract
近日,北京科技大學、上海交通大學研究團隊將激光重熔和五種掃描策略(三種往返和兩種棋盤策略)相結合, LPBF制備哈氏合金X合金,通過實驗和模擬研究了掃描策略對相關組織和力學性能的影響。相關研究成果以題為 “Tailoring the microstructure and mechanical properties for Hastelloy X alloy by laser powder bed fusion via scanning strategy” 發表在Materials & Design期刊上。
圖1(a)氣霧化制備的 HX合金粉末形態(b)粉末粒度分布(c)LPBF制備的HX合金成分。
在增材制造之前,對直徑在20-60μm范圍內的粉末進行干燥,隨后打印10×10×5mm的HX樣品。保護氣體為氮氣,基板為預熱80 ℃的45#鋼。在打印過程中采用了基于初步測試確定的一系列優化參數,并總結在表1中。
表1 LPBF工藝參數
為了了解制造工藝對HX樣品微觀結構的影響,為HX塊制備了五種掃描策略,如圖2(a-e)。三種往返策略(分別為M0、M67和M90)對應于粉末層之間0°、67°和90°的旋轉增量角。此外,還采用了兩種棋盤策略(分別為CB1和CB2)來研究島掃描的重熔效應。5×5mm的相鄰島區域的矢量彼此垂直,并且后續層的矢量與前一層保持正交關系。有趣的是,CB1策略的熱歷史更為復雜,它涉及到來自鄰近區域的巨大熱影響。與CB1相比,CB2策略每個單位面積簡單,因為激光束在打印過程中優先掃描各向同性區域。在這項研究中,所有樣本都是使用雙掃描制作的,包括在初始熔化后立即開始第二次掃描。有人建議,在單個粉末層的熔化過程中實施這種雙掃描方法可以提高冶金質量。制作室溫拉伸試樣,如圖2(f),加載方向垂直于建筑方向。
圖2(a-e)不同掃描策略的示意圖,分別為M0、M67、M90、CB1和CB2,以及(f)實際樣本的示意圖。
對LPBF工藝進行了模擬,揭示了各種掃描方式的凝固狀態和冷卻條件。本文中,冷卻速率(G×R)和熱梯度(G)是熔池凝固的關鍵輸出參數。此外,G/R的值代表組成過冷,并與晶體形成相關。為了模擬打印過程,使用Flow 3D軟件建立了多物理場模型,其中包括熔融金屬流動、相變、Marangoni效應、反沖壓力、表面張力和激光與材料的相互作用。詳細的計算方法和初始輸入顯示在補充信息中。
為了獲得粉末在基板上的分布,應用離散元法(DEM),并鋪下兩層粉末來模擬打印過程。每層都進行了兩次掃描,以檢測重熔效果。在本研究中,模擬域設置為800×800×260μm,并切片為1312000個單元。往返策略,設置了兩條軌道來了解整體凝固條件。棋盤策略,對四個島嶼的結合區域進行了建模,以獲得額外的邊界情況。與實際的增材制造工藝相對應,將單個激光束應用于熔融粉末,這導致島掃描的時間成本更高。此外,在激光轉向時關閉能量輸入,以減少局部熱量積聚對整體模擬的影響。HX的物理參數取自文獻,激光參數也與實驗數據一致。值得注意的是,密度和粘度隨溫度而變化,而不是固定值。
使用圖像分析軟件計算相鄰表面的平均孔隙率和每個試樣的頂面粗糙度。CB2試樣的相對密度最高(M0:98.13%、M67:97.28%、M90:97.34%、CB1:96.98%和CB2:99.60%)。與其他試樣相比,CB2的粗糙度最低。圖3(a,c)顯示了對應于LPBF掃描策略M90和CB2的拋光X-Y橫截面的光學顯微照片。通過往返策略制造的樣品獲得了LPBF工藝的三個典型缺陷,包括氣孔、未熔合和未熔化的粉末,如圖3中紅色箭頭所示。相反,CB2中出現了罕見的小孔和缺乏聚變粒子。圖右上角的高倍率SEM圖像顯示了不同樣品的未熔化粉末形態。由于存在球化缺陷,圖3(b)(對應于最高粗糙度為48.298μm的M90樣品)描繪了顯著的表面波動。從圖3中可以看出,島狀掃描實現了更平滑的打印質量,表面粗糙度也可能與內部孔隙含量有關。
圖3(a)(c)M90試樣和CB2試樣的OM圖像(b)(d)M90標本和CB2標本的粗糙度照片,M90(e)和CB2(g)試樣的缺陷分布圖像,以及M90(f)和CB1(h)試樣的孔隙放大率。
考慮到從橫截面圖像中獲得的體積孔隙率的不可靠性,從M90和CB2試樣中獲得的孔隙率分布如圖3(e,g)。球形直徑小于0.03mm的缺陷被清除為噪點。值得注意的是,CB2試樣的孔隙率小于M90試樣(分別為0.67%和7.94%),并且CB2試樣中的缺陷主要分布在島內含量較低的連接區。從中還可以看出,M90中的缺陷尺寸比CB2中的大,前者大多是大的不規則孔隙,后者主要是小孔,如放大圖像圖3(f,h)。M90塊中當量直徑大于100?m的孔隙數量高達23個,而CB2中只有3個。先前的研究已經確立了基于球度值來區分LPBF合金中孔隙類型的可行性,球度值源自缺陷的體積和面積:
其中V和A分別表示體積和表面。通常,球度值大于0.7被認為傾向于球化。根據統計分析,M90試樣缺陷中球形孔隙的比例(60.68%)遠高于CB2試樣的比例(26.28%),但幾乎沒有觀察到大于0.9的氣孔。用不同的掃描策略獲得的各種缺陷百分比可能與LPBF工藝中的冷卻條件密切相關。
通過不同掃描策略制造的蝕刻樣品的橫向光學顯微照片如圖4。與頂面圖像類似,所有曲流樣品中都存在不規則的大孔隙和未融合的顆粒。此外,M0和M90中捕獲了一些凝固裂紋,這已被確定為LPBF制造的HX合金的固有缺陷。一些沿著晶界分裂形成晶間裂紋,一些裂紋從孔中出現。這種差異是顯而易見的,因為棋盤樣品中幾乎沒有制造缺陷。如圖4(d,e)所示,兩個XZ表面圖像顯示了相鄰島嶼之間的良好組合。從這些照片中,島嶼策略獲得了平滑均勻的熔池地形。然而,由于冶金缺陷的存在,往返策略獲得了波動的熔池軌跡。
圖4(a-e)分別為M0、M67、M90、CB1和CB2試樣的OM圖像(a1-e1)和(a2-e2)相關試樣不同放大倍數的SEM形態。
蝕刻后試樣XZ表面的SEM圖像如圖4(a1-e1)??梢园l現,不同樣本的邊界間隔是不同的。因此,測量六個區域的線距離(D),然后計算平均值。隨著激光軌跡旋轉角度的增長,數值變得更加廣泛(DM0:4.824μm,DM67:5.101μm,DM90:5.739μm)。至于島狀印刷,由于激光路徑不垂直或平行于XZ平面,因此顯示出交替的熔融路徑圖案。此外,還拍攝了局部區域的高放大率圖像,如圖4(a2-e2)。柱狀晶粒是竣工樣品的主要微觀結構。柱狀晶??梢栽诙鄠€熔池中連續生長,并且在晶界中沒有發現碳化物分布,這與我們以前沒有逐層重熔工藝的工作不同。這可以另外表明合金在重熔過程之后實現了更多的均勻化。晶粒偏轉角是決定微觀織構取向的關鍵因素。從黃色箭頭可以看出,只有CB2試樣的晶粒生長方向嚴重偏離池邊界法線方向(20.04°),而其余晶粒的偏轉角小于10°(分別為M0:5.71°、M67:2.79°、M90:7.07°、CB1:4.17°)。
圖5給出了不同試樣沿構建方向的反極圖(IPF)圖和極圖(PF)圖,因此可以從EBSD數據中討論晶體取向和晶粒尺寸。與水平方向相比,垂直方向的晶粒尺寸相當大,尤其是M0和M67樣品。IPF圖的顏色顯示M90的〈1.0〉取向更為明顯。有趣的是,從圖5(e2)中可以看出,CB2試樣表現出更明顯的〈111〉微觀織構,晶粒形態趨于等軸類晶體。圖中的白色虛線表示每層的劃分區域,相鄰晶粒以不同的方向發展,晶粒的高度與粉末層的厚度相似。如圖5(a1-e1)所示,CB2制造顯示出最高的微觀結構分布,最大指數為6.842,CB1樣品的最大極性密度略降至6.814左右。然而,所有往返構建的微觀結構都被削弱了,如下最大微觀結構指數所示(分別為M0的5.326、M67的4.091和M90的4.976)。
圖5(a-e)、(a1-e1)、(a2-e2)和(a3-e3)重建的EBSD、PF、IPF以及M0、M67、M90、CB1和CB2的KAM映射分別作為構建樣本。
圖5(a3-e3)描述了XZ縱向橫截面局部區域中往返策略試樣的更顯著的取向差關系(M0、M67和M90分別為1.375°、1.645°和1.437°)。與紋理密度的趨勢相反,島狀掃描獲得了較低的KAM值(CB1樣品:1.429°),CB2樣品的平均KAM角顯著降低到0.872°。由于KAM值可以表示殘余應力的水平,因此有理由證明,竣工CB2塊體中存在最低的內應力。幾何必要位錯(GNDs)可以反映鎳基合金的塑性變形能力。通過設置5°的最大方位角來計算五個試樣的平均GND密度(ρGNG),并對其進行計數以進行后續比較。CB2樣品獲得了最稀疏的位錯密度(1.370×1013 m?2),這意味著通過這種島掃描策略制造的金屬塊體的室溫變形能力可能比其他構建方法更好。
此外,棋盤制造的平均晶粒尺寸略低于往返策略(分別為M0:10.84μm、M67:11.16μm、M90:11.06μm,CB1:10.68μm、CB2:10.40μm)。不同樣品的縱橫比(晶粒的短軸與長軸的比率)也從SEM圖像中捕獲。由于CB2樣品中的優先晶粒生長趨勢被抑制,它表現出最高的縱橫比(0.46),而其余四個樣品更傾向于外延生長(分別為M0:0.43、M67:0.44、M90:0.44、CB1:0.39)。相似的晶粒長度和寬度表明,CB2策略可以降低LPBF合金的各向異性,少量等軸晶體的存在也可以削弱非均勻性趨勢,改善性能。
此外,凝固金屬的恢復或再結晶可能發生在多次熔融過程中,因為在CB2樣品中發現了一些等軸顆粒。因此,使用晶粒重建軟件測量了晶粒的內部再結晶分數,具體數據如圖所示。6。通過將2°設置為內部平均取向差角(IAMA)的臨界閾值,變形晶粒的值高于2°。亞結構區域被定義為IAMA<2°,但亞晶粒的取向差是大于2°的IAMA。除此之外,其他晶粒被標記為再結晶晶粒。CB2試樣的變形晶粒百分比最低(12.72%),回收晶粒百分比為69.46%。
圖6 不同樣品的再結晶圖,分別包括M0、M67、M90、CB1和CB2。
圖7(a)顯示了五個竣工試樣的代表性工程應力-應變曲線和斷裂試樣的宏觀形貌。不同程度的頸縮現象發生在斷裂區附近。通過CB2策略形成的樣品實現了拉伸強度和伸長率的最佳平衡,其中屈服強度(YS)、極限拉伸強度(UTS)和斷裂伸長率(El)分別達到579±38MPa、816±17MPa和29.2±4.8%。對于CB1樣品,三種力學性能的值都有所下降(YS:454±57 MPa,UTS:814±17 MPa,El:24.3±3.2%)。與之前的研究一致,M67試樣的結果優于M90(YS值分別為568± 54MPa和546±57MPa,UTS值分別為762± 44MPa和721±35MPa,El值分別為16.0± 3.3%和13.2± 4.9%)。
由于打印缺陷的數量最大,M0樣品獲得了最差的強度(分別為YS:473±64MPa和UTS:580 ±65MPa)和伸長率(3.5±2.0%)。
圖7(a)工程應力-應變曲線和五個拉伸樣品的宏觀照片,(b)五個拉伸樣本的真實應力-應力曲線和應變硬化率曲線,(c)不同掃描策略的拉伸性能,分別代表M0、M67、M90、CB1和CB2,(d)激光重熔HX合金的UTS與伸長率和以前的文獻值。
真實應力-應變曲線和應變硬化率也繪制在圖7(b)。真實應力的分布趨勢與工程應力值相似,棋盤策略的應變硬化率優于往返策略。與拉伸強度相對應,CB2試樣的位錯硬化也略高于CB1試樣。選擇并分析先前的文獻,然后提取UTS和伸長率,得到圖7(d)。綠色點是從制造的HX中獲得的,而藍色數據是從這些鑄態合金中提取的,作為基準。在目前的研究中,使用紅球突出顯示了不同拉伸樣品的數據。與之前的研究相比,在不進行后熱處理的情況下,CB2樣品的重熔工藝可以獲得更好的效果。
為了進一步討論增強性能的性質,通過SEM觀察研究了五個拉伸部件的斷裂表面形貌,如圖7(a)。根據圖8(a-e)的形態信息,每個樣品的斷裂表面都存在裂紋和孔隙。M0、M67、M90和CB1的SEM圖像中明顯出現了許多殘留的未熔融顆粒,這與先前的OM結果相似。至于CB2本體,圖8(e)中捕捉到幾乎不存在球形粉末。圖8(a1-e1)和圖8(a2-e2)分別是拉伸斷裂的較高放大率。值得注意的是,凹坑是主要的微觀結構特征,這是這些建成塊中發生韌性斷裂的證據。此外,在M0樣品中,在孔附近也很少產生類似解理的區域。解理面的存在意味著準解理斷裂的開始。毫無疑問,M0的伸長率正在下降到CB2試樣的約12%。然而,解理狀表面可能不僅僅是解釋極弱延展性的原因,而且凹坑的大小也可以在解釋兩種制造之間的性能差距方面發揮作用。CB2樣品內部凹坑的平均尺寸略大于M0樣品(M0:0.410μm和CB2:0.646μm)。由于CB2斷裂中出現了韌窩和解理面的混合物(圖8(e1,e2)),韌性-脆性協同斷裂機制值得更多關注。此外,在補充信息中提供了與頸縮區域相鄰的拉伸樣品的詳細分析。更重要的是,CB2試樣的位錯密度升高率相對高于M0試樣,這也符合CB2拉伸試驗中更好的伸長率(分別為M0:16.7%和CB2:159.2%)。
圖8(a-e)M0、M67、M90、CB1和CB2樣品的SEM斷裂照片,分別為(a1-e1)和(a2-e2)局部區域的高放大率照片。
在不同的熔融區上進行了納米壓痕實驗,以評估顯微硬度。熔池被分為兩部分,一部分是非重熔區(NRZ),它是僅在單個粉末層中的兩條熔池線的中間區域,而另一個區域被命名為重熔區(RZ)。如圖9(a)所示,RZ通常比NRZ更硬,CB2樣品比其他樣品更硬(NRZ:4.946GPa和RZ:5.679GPa)。對于M0樣品的最高孔隙比,塊體表現出相對最差的硬度(分別為NRZ:4.350GPa和RZ:5.099GPa)。此外,還對棋盤掃描的過渡區域進行了測試。與其他區域相比,這些弱點獲得了較低的顯微硬度(分別為CB1:3.894GPa和CB2:3.970GPa)。CB2試樣的硬度明顯高于其他試樣。人工測量一次枝晶臂間距(PDAS)以區分微觀結構變化。測量每個區域的枝晶距離5次,并獲得平均值。圖9(b)描述了CB2試樣的PDAS值仍然處于最低水平,而與RZ(0.40μm)或NRZ(0.60μm)無關。此外,通過比較這兩個區域,RZ的值通常低于NRZ的值,顯示出與顯微硬度一致的趨勢。
圖9(a)竣工樣品的納米硬度值(b)不同樣品的PDAS,分別代表M0、M67、M90、CB1和CB2(c)CB2試樣NRZ的PDAS測量圖(d)CB2試樣RZ的PDAS測量圖。
在本研究中,主要的制造缺陷被確定為大的不規則孔隙和氣孔。激光能量密度不足是形成不規則孔隙的主要原因。由于熔體蒸發引起的反沖壓力,氣孔可以容易地以更高的能量密度形成。在這種情況下,較低的激光輻射不能充分熔化金屬粉末,導致大尺寸孔隙內殘留顆粒。在LR加工過程中,第二能量輸入導致熔體飛濺,導致出現不規則的大開孔。除了能量密度外,屏蔽氮流入活性熔融金屬也可能是形成這些缺陷的一種可能解釋。氣孔主要歸因于施工室內的保護性氣體或粉末表面未干燥的水分。值得注意的是,原始顆粒干燥時間的延長導致HX制造中微孔含量較淺。這些發現有助于理解使用LR加工的金屬材料中缺陷形成的機制,并為開發改進的加工技術以實現無缺陷制造提供信息。
第一次掃描后的重熔過程在熔池中引發了嚴重的Marangoni對流和蒸汽羽流,導致一定程度的金屬飛濺。這種方法還加速了熔池內焊劑的蒸發,導致在下一次粉末堆積之前,球形顆粒聚集在熔化軌道周圍。此外,由于圖3(a)中殘余顆粒的存在支持了激光能量密度不足,以及某些區域的粉末層厚度相對較高,因此激光無法完全熔化金屬顆粒。這削弱了層間結合效應,并導致形成許多不規則的大孔,在頂面上產生明顯的波浪。此外,孔隙率可能與激光掃描路徑長度呈正相關。彎曲策略制造的較長激光軌跡允許由于延長的凍結間隔而在熔池中生長空穴。島策略的路徑長度幾乎是往返掃描的一半,這可能是第二次掃描期間較低余熱效應的原因。這些發現有助于更好地理解重熔和激光掃描策略對使用激光技術制造的金屬材料的質量和缺陷的影響。
與傳統的制造技術相比,LPBF方法由于更高的冷卻速率和溫度梯度而產生柱狀晶粒。圖中的顯微照片4(a-e)表明在第二次掃描過程中形成了重熔軌跡,與粉末相比,由于固體金屬具有優異的導熱性,因此其冷卻速度自然更高。LPBF的逐層熔化方法使熔池的頂部晶粒能夠重復熔化并沿著優選的方向生長,這進一步受到掃描策略的影響,導致不同的微觀結構,如圖5(e)。CB2樣品重熔過程中的熱發射導致晶粒傾斜,而不是向上生長,改變了柱狀晶粒的優先取向,轉變為〈111〉微觀織構分布。
CB2策略中相對較細的晶粒可歸因于第二次熔化期間較高的冷卻速率和較快的成核。據觀察,在第二次熔化過程中,積累的熱量會使少數變形晶粒重新熔化,這可能導致無序的形核和生長。此外,CB2具有最低的PDAS,這意味著它具有最小的亞晶粒尺寸。圍繞這些亞晶粒的位錯網絡限制了位錯的滑動,從而提高了機械強度。Hall-Petch方程表明,對于CB2試樣,更細的亞晶粒也產生更高的強度。此外,較高百分比的亞結構表現出較低的內部位錯密度和殘余應力,這也可以導致更好的伸長率效果。
在LPBF-ed HX合金中,位錯硬化是除晶界強化外的主要強化機制。在棋盤樣品中觀察到的較高應變硬化率表明,在拉伸試驗過程中,多個滑移系統同時運行,導致位錯在應力集中(如晶界、孔隙和微裂紋)中增殖和積累。圖8(a)可以作為支持這一觀點的確鑿證據。
Masahiro Kusano觀察到的PDAS的減少反映了LPBF過程中冷卻速率的快速增加。在第二次掃描期間,未完全冷卻到環境溫度的固體金屬被重新注入激光能量。熱擴散系數的差異將導致垂直熔體線方向上的點的不同冷卻速率和熱梯度,最終影響材料的硬度。除了殘余應力和位錯密度外,內部孔隙率在決定材料顯微硬度方面也起著重要作用。較低的硬度值表示較差的結合效果,如圖7(a)所示的鋸齒狀斷裂形態所示。XCT三維圖像顯示,島嶼邊界幾乎沒有孔隙,進一步支持了該地區較軟的特征。
圖10顯示了兩個粉末層的兩次掃描的溫度-速度場分布。熔融金屬的蒸發在一定程度上發生在與粉末的激光接觸區的前部,這是由于在小區域內積累了大量的熱量,導致溫度高于蒸發點。盡管如此,較厚的光斑直徑和中等的激光能量密度導致了氣泡的不存在。如黑色輪廓線所示,由于熔池尾部的流速較弱,激光束的移動和蒸發產生的反沖壓力在熔池內部引起了顯著的逆時針Marangoni對流。此外,由于固體的傳熱系數大于氮氣的傳熱系數,由重熔掃描產生的熔池體積小于由第一次掃描產生的熔融池體積,通過比較圖10(b,d)和圖10(a,c)可以明顯看出。
圖10 同一截面在不同狀態下的溫度場和速度場(a)第一層和第一次掃描,(b)第一層與第二次掃描。
圖11(a)顯示了五種不同策略下粉末床中心點溫度隨時間變化的各種曲線,包括單層粉末的第二次掃描。除M67樣品外,第一次掃描導致熔池溫度高于重熔樣品。此外,由于激光掃描速度均勻,構建相同尺寸的島狀樣品所需的時間更長,這從圖11(a)中也很明顯。由于激光移動路徑的差異,與長線掃描相比,島狀策略經歷了多次熱循環,CB1樣品多次達到峰值溫度,并且CB1的CB2峰值溫度略低。此外,圖11(b)展示了粉末層模型的平均溫度曲線。值得注意的是,棋盤策略的最終平均溫度遠高于曲流策略,其中CB2達到880.88 K。這表明掃描后熔體的流動時間更長,可能會填充一部分孔隙,這可能是密度更高的原因。
圖11 不同掃描時間和不同樣品的溫度-時間曲線分別表示M0、M67、M90、CB1和CB2(a)模型中心點的瞬態溫度曲線(b)模型的平均溫度曲線和(c)模型的每單位體積的累積蒸發質量。
根據liu的研究,打印引起的缺陷受到熔池蒸發的影響。具體而言,當溫度超過材料的熔點時,金屬顆粒蒸發并離開熔池,產生向下的反沖壓力,促進熔池內的內部流動和孔隙成核。此外,強烈的蒸發會導致蒸發羽流,周圍粉末的無序流動可能會加速大的不規則孔隙的形成。為了進一步解釋密度差異,研究人員計算了每單位體積的累積蒸發質量,如圖11(c)。雖然由于路徑長度不同,最終蒸發值不同,但討論的重點是不同模型在同一時期的蒸發。局部放大顯示棋盤策略的蒸發比往返策略的蒸發弱得多。因此,可以假設CB2在制造相同尺寸的塊時將損失最低的質量。質量損失越大,蒸發越劇烈,進一步破壞熔池的穩定狀態。因此,棋盤制造的高密度可歸因于較低的蒸發質量損失。
圖12顯示了各種型號的冷卻速率圖,所有這些都是從掃描軌跡的中心拍攝的。由于在這些模擬中激光束運動的軌跡不同,只選擇了四個部分來檢查橫截面附近的冷卻速率變化。熔池內部的冷卻速率明顯高于邊緣,如圖12(b4,c2)。此外,在相鄰軌道掃描之后的熱效應導致更深的區域經歷冷卻。此外,圖12(d1,d4)和(e1,e4)表明,島狀掃描的冷卻速率高于往返掃描。除M67外,在其他策略中,未重熔區的凍結率顯著低于重熔區。這歸因于第一次掃描后固化流的傳熱系數更顯著,這導致更快的熱擴散、相對較小的熔池體積以及重熔過程中更高的冷卻速率。由于重熔區的凝固速度更快,最終結果將是局部區域的硬度相對較高,與納米壓痕測試結果一致。然而,應該注意的是,由于兩個軌道的中心被選擇在固液界面,所獲得的數據將略高于LPBF實驗中測量的冷卻速率(105–106 K/s)。此外,除了冷卻速率外,本研究還檢查了溫度梯度和溫度梯度與生長速率的比率(G/R),如補充信息所示。觀察到,與其他模型相比,CB2策略具有更高的平均G/R值(圖S3),這意味著成分過冷不太明顯,隨機晶粒形成的可能性較小,從而導致更明顯的微觀織構。
圖12 激光軌跡(a1-a4)M0、(b1-b4)M67、(c1-c4)M90、(d1-d4)CB1和(e1-e4)CB2樣品之間XZ截面的冷卻速率分布的比較。
總之,棋盤掃描策略的獨特熱流方向和重熔的第二次能量輸入導致CB2試樣內的晶粒偏轉角更加突出,從而產生更加突出的〈111〉微觀織構。棋盤策略中,蒸發引起的粉末飛濺不太可能發生,增強的流動性可以關閉一些不規則的孔隙。此外,在流動過程中,金屬與未熔化的粉末結合,這提高了隨后激光掃描的燒結效率。相反,對于彎曲樣品,在兩次焊道中使用相同的激光能量密度會增強熔池中的Marangoni對流,導致飛濺和羽流,從而降低密度。盡管對于相同數量的印刷層,島狀策略可能需要更多的時間,但由于較高的冷卻速率可能導致合金在第二次掃描激活之前固化,因此它可能導致類似于傳統工藝的后處理效果。因此,重熔允許合金內部恢復,甚至再次熔化凝固的金屬以產生新的晶粒。最終,通過重熔和棋盤掃描制備的HX合金的強度和延展性得到了協同增強,超過了LPBF ed HX合金既定的性能。此外,重熔(一次和四次)和掃描策略(層間旋轉角度的90°和67°)的組合可以產生更致密的合金。應進行進一步的研究,重點關注熔化時間和旋轉角度的組合,以獲得較低缺陷密度的較窄窗口。
本文設計了五種LPBF掃描策略,并分析了不同HX合金重熔后的密度、微觀結構和室溫力學性能。CFD模型用于模擬熔體流動,并進一步解釋了凝固機理。具體研究結果總結如下:
1)與往返掃描相比,棋盤掃描重熔HX的表面更光滑。棋盤2策略的內部密度(99.33%)明顯優于往返90°策略(92.06%),這是由于其優異的流動性和較輕的熔融金屬蒸發。通過彎曲策略獲得的合金內部的大量孔隙缺陷嚴重削弱了力學性能。
2)所有試樣的微觀結構主要由柱狀晶粒結構組成。最短的平均樹枝壁間距證明棋盤2試樣具有最快的冷卻速率。棋盤2試樣的主要特征也是微觀織構強度最強和位錯密度最低,由于晶粒偏轉角最大(20.04°),表現出明顯的〈111〉取向。
3)在室溫拉伸試驗中,棋盤2試樣獲得了最佳的力學性能,其斷裂機制主要為韌性-脆性協同斷裂。根據GND的較高百分比上升,棋盤2樣本在拉伸過程中驅動了大量的滑移系統。由于晶界強化和位錯硬化,具有較小亞晶粒的棋盤2試樣比其他試樣更硬,盡管弱點大多分布在島狀連接處。
4)通過流體模擬分析,短線性棋盤策略導致了優越的冷卻速率,粉末模型的平均溫度更高,從而使掃描后的熔體流動性更好。重熔處理可以產生部分恢復的晶粒,進一步提高伸長率。較高G/R值的較寬區域也表明棋盤2試樣晶粒不再傾向于垂直于熔池底部生長,但重熔可以形成一定量的等軸晶體。
對于棋盤掃描,第一次熔化可以產生更快的冷卻速度和更好的熔體流動性,進一步填充孔隙缺陷。與重熔工藝相結合,凝固晶粒內發生回復,從而釋放殘余應力、稀疏位錯和優異的機械性能。棋盤2策略與激光重熔相結合,實現了其他策略的最佳性能。重熔工藝與棋盤策略相結合,產生了良好的結合效果和力學性能,可為工程應用提供指導。
論文鏈接: https://doi.org/10.1016/j.matdes.2023.112386
免責聲明:本網站所轉載的文字、圖片與視頻資料版權歸原創作者所有,如果涉及侵權,請第一時間聯系本網刪除。
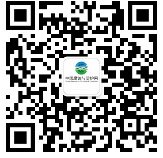
官方微信
《腐蝕與防護網電子期刊》征訂啟事
- 投稿聯系:編輯部
- 電話:010-62316606
- 郵箱:fsfhzy666@163.com
- 腐蝕與防護網官方QQ群:140808414